Human Factors Review PDF
Document Details
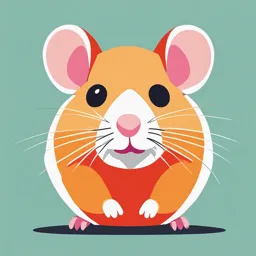
Uploaded by WondrousPeridot
Tags
Summary
This document discusses human factors in aircraft design, covering topics such as the PEAR model, the Dirty Dozen, and aircraft airframe systems. It delves into various aspects of aircraft structures and loads.
Full Transcript
**HUMAN FACTORS** - **PEAR MODEL** - **P-PEOPLE** -- people who perform the work and it focus on physical, physiological, psychological, and psychosocial factors - **E**-**ENVIRONMENT** -- physical workplace on the ramp, in the hangar or shop - **A**-**ACTIONS...
**HUMAN FACTORS** - **PEAR MODEL** - **P-PEOPLE** -- people who perform the work and it focus on physical, physiological, psychological, and psychosocial factors - **E**-**ENVIRONMENT** -- physical workplace on the ramp, in the hangar or shop - **A**-**ACTIONS** - **R**-**RESOURCES --** collective asset that can be tangible or intangible II. **THE DIRTY DOZEN** 1. **LACK OF COMMUNCATION --** failure to provide and receive information for the maintenance task 2. **COMPLACENCY --** overconfidence from a repeated experience in performing a task 3. **LACK OF KNOWLEDGE --** shortage of the training, information of ability to successfully perform 4. **DISTRACTION --** anything that draws your attention away from the task at hand 5. **LACK OF TEAMWORK --** failure to work together to complete a shared goal 6. **FATIGUE --** physical or mental exhaustion threatening work performance 7. **LACK OF RESOURCES --** not having enough people, equipment, documentation, time, parts to finish the task 8. **PRESSURE --** real or perceived forces demanding high-level job performance 9. **LACK OF ASSERTIVENESS --** failure to speak up or document concerns about instructions, orders, or the actions of others 10. **STRESS --** physical, chemical, or emotional factor that causes physical or mental tension 11. **LACK OF AWARENESS --** failure to recognize a situation, understand what it is, and predict the possible results 12. **NORMS --** one of the expected, yet unwritten rules of behavior III. **AIRCRAFT AIRFRAME SYSTEMS** - **LOAD APPLIED TO AIRCRAFT STRUCTURES** - **TENSIONS --** tensile load is one of which tends to stretch a structural member (ties) - **COMPRESSION --** opposite of tensile loads and tend to shorten structural members (struts) - **SHEAR --** force which tends to slide one face of the material over adjacent face (riveted joints) - **BENDING --** tension as the outer edge stretches, compression as inner, shear across the structures as the forces try to split it - **TORSION --** twisting forces produces tension at the outer edge compression in the center and shear across the structure - **STRESS --** internal force per unit area inside a structural part because of external loads and therefore a tensile load or force will set up a tensile tress, compression loads will set up compressive stress - **STRAIN --** external force of a sufficient magnitude acts on a structure, the structural dimensions change (deformation) - **BUCKLING --** occurs to thin sheet materials when they are subjected to end loads and to ties if subjected to compressive forces - **DYNAMIC LOADS --** tend to build up quickly due to changes in flight conditions - **STATIC LOADS --** constant and build slowly, aircraft on the ground will experience static loads - **FORCES ACTING ON THE AIRCRAFT STRUCTURE** - **AIRCRAFT STRUCTURES** - **FUSELAGE --** main structure or body of the aircraft **FUSELAGE CONSTRUCTION:** - **TRUSS OR FRAMEWORK --** used for light, non-pressurized aircraft **-** consists of light gauge steel tubes welded together **-** covered by a lightweight aluminum alloy or fabric skin - **MONOCOQUE --** used for light aircraft **-** all the loads are taken by the skin with just light internal frames or formers to give the required shape - **SEMI-**MONOCOQUE -- stressed skins **-** additional structural members known as stringers and longeron were added to run lengthwise along the fuselage joining the frames together - **LONGERONS --** beams in the fuselage that are fitted longitudinally from nose to tail **-** often placed below the floor and take the main bending loads - **FRAMES --** vertical structures that are open in their center **-** designed to take the major loads and give the aircraft its shape - **BULKHEADS --** similar to frames but are usually solid but may have access doors **-** designed to give the fuselage its shape and take some of the main loads - **FIREWALLS --** separating the flight deck and cabin from the engine **-** required to protect the flight crew and passengers in the event of an engine fire - **WINGS --** support the weight of the aircraft in the air and so must have sufficient strength and stiffness **WINGS CONSCTRUCTION:** - **BIPLANE --** wing spars, interplane struts and bracing wires form a lattice girder of great rigidity which is highly resistant to bending and twisting - **BRACED MONOPLANE --** used on low-speed aircraft - **CANTILEVER MONOPLANE --** one or more strong beams, called spars, run along the span of the wing - **SPARS --** single spar twin spar or multi-spar - **SKIN --** takes the loads due to differences in air pressure and the mass and inertia of the fuel in the wing tanks - **STRINGERS --** spanwise members giving the wing rigidity by stiffening the skin in compression - **RIBS --** maintain the aero foil shape of the wings, support the spars, stringers and skin against buckling - **STABILIZING SURFACES (EMPENNAGE)** - **TAILPLANE OR HORIZONTAL STABILIZER --** provide longitudinal stability by generating upwards or downwards forces as required (controlled by elevator) - **FIN OR VERTICAL STABILIZER --** generate sideways forces (directional control provided by the rudder) **MATERIALS USED** - **ALUMINUM --** and its alloys are the most widely used metals for structural use due to a good strength to weight ratio with duralumin type alloys predominating due to their good fatigue resistance - **STEEL --** and its alloys are only used where strength is vital and weight penalties can be ignored - **TITANIUM --** much lighter than steel and can be used where fire protection is required - **MAGNESIUM ALLOY --**principal advantage being their weight **COMPOSITE MATERIALS --** made of at least two elements to produce a material with properties that are different to those of the original elements - **SANDWICH CONSTRUCTION --** used typically for flight control surfaces, flooring, fuselage panels, empennage skin and sound proofing for engines **-** laminar construction that uses honeycomb core with skins of composite material or aluminum alloy **ATTACHMENT METHODS:** - **RIVETING** - **WELDING** - **BOLTING --** employed where high shear or tensile loads are experienced (locking wire, split pins, nuts) - **PINNING --** use of pins - **BONDING --** sheet of adhesive is placed between the two materials **AIRCRAFT HYDRAULIC SYSTEM --** complex system essential for operating various a/c components - It is commonly used for controlling flight surfaces, managing landing gear, operating thrust reversers, controlling brakes **HYDRAULIC SYSTEM SCHEMATIC --** Reservoir has a Hydrostatic pressure (low pressure) but it is pre pressurized to convert the hydrostatic pressure to hydrodynamic pressure and helped by additional pressure given by the Ambient Conditions (temp).= \"High pressure\" is necessary to satisfy the demands of the users. Excess pressure will circulate back to the storage (reservoir) - FUNCTION OF **HYDRAULIC SYSTEM** IN AN AIRCRAFT \- The **hydraulic system** in an aircraft provides the necessary force to operate key components such as: 1. **FLIGHT CONTROLS**: Powers ailerons, elevators, rudders, and flaps for smooth control. 2. **LANDING GEAR**: Extends and retracts the landing gear during takeoff and landing. 3. **BRAKING**: Enables strong, reliable braking and anti-skid functions after landing. 4. **THRUST REVERSERS**: Assists in slowing the aircraft by redirecting engine thrust. 5. **NOSE WHEEL STEERING**: Controls ground maneuvering during taxiing. 6. **SPOILERS AND SPEED BRAKES**: Manages drag and lift to aid in slowing the aircraft. - **FUNCTION OF ELECTRICAL SYSTEM IN AN AIRCRAFT** **-** The **electrical system** in an aircraft is critical for powering various systems and components. Its primary functions include: 1. **POWERING AVIONICS**: Supplies electricity to navigation, communication, and flight control instruments. 2. **LIGHTING**: Provides power to interior and exterior lights, including cockpit, cabin, and landing lights. 3. **ENGINE STARTING**: Powers the starter motor to initiate engine operation. 4. **FUEL PUMPS**: Operates pumps that transfer and pressurize fuel for the engines. 5. **ENVIRONMENTAL SYSTEMS**: Powers air conditioning, heating, and pressurization systems. 6. **LANDING GEAR AND FLAP SYSTEMS**: Powers electrical components involved in controlling landing gear and flaps (in some aircraft). 7. **AUXILIARY POWER UNIT (APU)**: Provides backup electrical power when the main engines are off. - **FUNCTION OF PNEUMATIC SYSTEM IN AN AIRCRAFT** 1. **ENGINE STARTING**: Provides the air pressure needed to start the engines, especially in turbine-powered aircraft. 2. **CABIN PRESSURIZATION**: Supplies compressed air to maintain proper cabin pressure at high altitudes. 3. **AIR CONDITIONING**: Powers the environmental control system to regulate cabin temperature and ventilation. 4. **ANTI-ICE AND DE-ICING**: Delivers hot compressed air to prevent or remove ice buildup on critical surfaces such as wings and engine inlets. 5. **HYDRAULIC SYSTEM PRESSURIZATION**: In some aircraft, the pneumatic system helps pressurize the hydraulic system by providing air to hydraulic reservoirs. - **FUNCTION OF FUEL SYSTEM IN AN AIRCRAFT** 1. **FUEL STORAGE**: Safely stores fuel in multiple tanks, typically located in the wings and fuselage. 2. **FUEL DELIVERY**: Pumps and controls fuel flow from the tanks to the engines, ensuring a steady and regulated supply. 3. **FUEL DISTRIBUTION**: Balances fuel between tanks to maintain the aircraft\'s weight and balance during flight. 4. **FUEL MONITORING**: Provides information on fuel quantity, temperature, and pressure to the pilot through cockpit gauges. 5. **CROSSFEED AND TRANSFER**: Allows fuel to be transferred between tanks to manage the fuel load and ensure even consumption. 6. **EMERGENCY SHUTOFF**: Includes safety mechanisms to stop fuel flow in the event of a fire or system malfunction. - **TYPES OF LANDING GEAR** 1. **Tricycle Landing Gear** - Description: Consists of two main wheels and a smaller nose wheel. - Advantages: Provides stability during takeoff and landing, allows better forward visibility, and reduces the risk of tipping forward. - Usage: Common in most modern aircraft, including commercial airliners and general aviation aircraft. 2. **Tailwheel (Conventional) Landing Gear** - Description: Two main wheels are located ahead of the center of gravity, with a smaller tailwheel at the rear. - Advantages: Suitable for rough terrain, allows for shorter and simpler landing gear designs. - Usage: Often used in older aircraft, bush planes, and aerobatic aircraft. 3. **Tandem Landing Gear** - Description: Consists of two sets of main wheels arranged in a straight line along the fuselage. - Advantages: Reduces the need for wing-mounted gear and allows for more flexible wing designs. - Usage: Found in certain military aircraft and gliders. 4. **Multi-Bogie Landing Gear** - Description: Uses multiple wheels on each main landing gear strut, often arranged in bogies (multi-wheel assemblies). - Advantages: Distributes weight more evenly, allows for heavy aircraft to operate on soft or rough surfaces. - Usage: Common on large commercial aircraft and heavy cargo planes. **5. Fixed Landing Gear** - Description: Landing gear that remains extended and exposed during flight. - Advantages: Simple, lightweight, and low-maintenance, typically more affordable. - Usage: Found on small general aviation aircraft and ultralights. **6. Retractable Landing Gear** - Description: Can be retracted into the fuselage or wings during flight to reduce drag. - Advantages: Improves aerodynamics, reduces drag, and allows for higher speeds. - Usage: Common on commercial, military, and high-performance aircraft. **7. Floats, Skis, and Amphibious Landing Gear** - Floats: Used for water landings; replaces wheels with floats. - Skis: Allow landing on snow or ice surfaces. - Amphibious Gear: Combines floats with retractable wheels, enabling operation on both water and land. - Usage: Found on seaplanes, bush planes, and specialized aircraft for winter operations. **8. Skid Landing Gear** - Description: Skids are used instead of wheels, common in helicopters. - Advantages: Provides stability for takeoff and landing in rugged or uneven terrain. - Usage: Mostly used on helicopters, particularly small and utility models. **MOMENTS AROUND THE AXES** **LONGITUDINAL AXIS** -- Rotation around the longitudinal axis is ***rolling and is controlled by the ailerons***, or for some aircraft, spoilers, or by a combination of the two. **LATERAL AXIS** -- Rotation around the lateral axis is ***pitching and is controlled by the elevators***, or by a moving tailplane. **NORMAL AXIS** -- Rotation around the normal axis is ***yawing and is controlled by the rudder.*** IV. **AIRCRAFT AVIONICS SYSTEM** **AVIONICS --** aviation electronics - **NAVIGATION --** field of study that focuses on the process of monitoring and controlling the movement of a craft or vehicle from one place to another - **COMMUNICATION --** act of conveying meanings from one entity or group to another using mutually understood signs, symbols, and semiotic rules - **SURVEILLANCE --** monitoring or close observation of behavior, activities, or information for the purpose of influencing, managing, or directing - **NDB --** non-directional beacons - **VOR --** Very High Frequency (VFR) Omni-Directional Range - **DME --** Distance Measuring Equipment - **TACAN --** Tactical Air Navigation System - **LORAN-**C - **ILS** - **MLS** - **GPS** - **AUTOPILOT** - **GYROSCOPE** - **ALTIMETER RADAR** - **DOPPLER** - **VFR -- VISUAL FLIGHT RULE --** based on flying by visually looking out of the cockpit **-** visually navigate with reference to ground landmarks \- aircraft altitude control may be based solely on the natural horizon visible through the windscreen of the aircraft \- looking out to avoid collisions with another a/c \- VFR flights usually involve small aircraft operated for personal purpose - **IFR -- INTRUMENT FLIGHT RULE --** based on flying using airborne instruments **-** must be equipped with gyroscope, navigational equipment, radio communications, transponder **-** operators are fully controlled by ATC system **-** ATC operators on the ground gives directions for each aircraft's flight plan **AIRCRAFT INSTRUMENT** +-----------------------------------------------------------------------+ | 12. **AIRSPEED INDICATOR --** uses the pressure differential in the | | pitot-static system to measure and display the aircraft's speed | | | | - ASI displays speed in knots or miles per hour | | | | - Device for measuring the forward speed of the aircraft | +=======================================================================+ | 1. **ATTITUDE INDICATOR --** aka artificial horizon | | | | - Uses a rigidly-mounted internal gyro to display the | | aircraft's attitude relative to the horizon | | | | - Display consists of a miniature a/c aligned to the horizon in | | straight-and-level flight, with a blue sky above and brown | | ground below | | | | - Pitch and roll | +-----------------------------------------------------------------------+ | 2. **ALTIMETER --** uses barometric pressure obtained from the | | static port to display the a/c approximate altitude or height | | above mean sea level (MSL) in feet | | | | - Measures the height of an aircraft above a fixed level | | | | - Measures the altitude of the aircraft | +-----------------------------------------------------------------------+ | 3. **TURN COORDINATOR --** uses a canted internal gyro to display | | both initial roll rate and stabilized rate of turn | | | | - Around the longitudinal (roll) axis | | | | - Rate of turn | +-----------------------------------------------------------------------+ | 4. **HEADING INDICATOR --** uses a rotating gyro to display the | | current compass rose direction (heading) that the a/c is flying | +-----------------------------------------------------------------------+ | 5. **VERTICAL SPEED INDICATOR --** uses an internal pressure | | differential to provide a visual indication of how fast the a/c | | is climbing or descending | +-----------------------------------------------------------------------+ | **ENGINE INSTRUMENT** | | | | 6. **TACHOMETER --** device for counting | | | | - Used to show the number of revolutions per minute (RPM) of | | the engine | +-----------------------------------------------------------------------+ | 7. **OIL PRESSURE GAUGE --** tells the pilot that the oil pressure | | is within operating limits, ensuring the engine is getting the | | lubrication it needs | +-----------------------------------------------------------------------+ | 8. **OIL TEMPERATURE GAUGE --** measures the temperature of oil | | | | - Green area shows the normal operating range | | | | - Red line indicates the maximum and allowable temperature | +-----------------------------------------------------------------------+ | 9. **FUEL GAUGE --** accurately monitors and measures the quantity | | of on-aircraft fuel, which is a critical function necessary for | | the safe and efficient operation of any aircraft | +-----------------------------------------------------------------------+ | 10. **FUEL FLOW METER --** shows the rate of fuel consumption, | | helping pilots manage fuel efficiency and reserves | +-----------------------------------------------------------------------+ | 11. **EXHAUST GAS TEMPERATURE (EGT) --** measures the temperature of | | the exhaust gases, which can indicate engine performance and | | efficiency | +-----------------------------------------------------------------------+ V. **AERODYANMICS** a. **THEORY OF FLIGHT** - **AIRFOIL --** a structure curved to produce lift - **LEADING EDGE --** front of airfoil - **TRAILING EDGE --** end of the airfoil - **CHORD LINE --** imaginary line between the leading edge and the trailing edge of the wing - **CAMBER --** curvature of an airfoil - **WING SPAN --** distance measured from wing tip to wing tip - **WING AREA --** average length X width - **PLANFORM --** shape of the wing from above - **ASPECT RATIO --** ratio of wing span: wing chord - **ANGLE OF INCIDENCE --** angle between chord line and longitudinal axis - **RELATIVE AIRFLOW --** airflow with respect to wing; opposite of aircraft motion - **ANGLE OF ATTACK --** angle between chord line and relative airflow - **PRINCIPLES OF LIFT** - **BERNOULLI'S PRINCIPLE** -- Faster airflow over the curved upper surface of the wing creates lower pressure, while slower airflow under the wing creates higher pressure. This pressure difference generates lift. - **NEWTON'S THIRD LAW** -- The wing deflects air downward, and the reactive force pushes the wing upward, contributing to lift. b. **FOUR FORCES OF FLIGHT** 1. **LIFT --** wing is shaped like an airfoil. In normal forward flight wind passing over the wing called relative wind is what helps the airfoil generate lift **-** when air is moving across the airfoil it is forced to move faster across the top than it is along the bottom \- the slower moving air across the bottom puts more pressure upwards on the wing than the faster moving air across the top, this in turn creates lift (***Bernoulli's principle)*** \- while the wings are creating the force of lift which is pulling the aircraft up, we also have the force thrust pulling the aircraft forward **THRUST -** we also have the force thrust pulling the aircraft forward, created by the propeller 2. **WEIGHT --** counteracts the two forces above **-** gross weight along with gravity all act as weight pulling down on the aircraft **-** in order for an airplane to fly, the lift generated by the wings must be equal to or greater than the weight of the aircraft 3. **DRAG --** opposite of life **-** created simply by the aircraft's existence **-** object's natural desire to resist moving through a fluid such as air or water **-** thrust must be equal or greater than drag VI. **POWERPLANT -- JET TURBINE** - Internal combustion engine that uses air as its working fluid - Extracts chemical energy from fuel and converts it into mechanical energy by utilizing the gaseous energy of the working fluid (air) to drive the engine and propeller, propelling the airplane - **TYPES OF JET ENGINE** 1. **TURBO JET --** jet engine which produces all its thrust by ejecting a high energy gas stream from the engine exhaust nozzle 2. **TURBO FAN --** modern variation of the basic gas turbine engine - Consists of a core engine surrounded by a fan at the front and an additional turbine at the rear - The fan and fan turbine, like the core compressor and core turbine, have many blades and are connected to an additional shaft 3. **TURBO PROP --** optimized to drive an aircraft propeller through reduction gearing - Aircraft equipped with turboprop engines are highly efficient at lower flight speeds, consuming less fuel per seat mile and requiring shorter runways for takeoff and landing 4. **TURBO SHAFT --** variant of gas turbine engine optimized to produce shaft power to drive machinery instead of generating thrust - **INTAKE SECTION --** designed to guide incoming air to the compressor with minimal energy loss due to drag or ram pressure - This ensures that the airflow into the compressor is free of turbulence, maximizing operating efficiency - Intake sits upstream of the compressor, and its main parts include the inlet cowl and fan cowl doors - **COMPRESSOR SECTION --** responsible for providing enough compressed air to meet the needs of combustion - It increases the pressure of the incoming air mass received at the inlet and supplies it to the combustion section at the required pressure - It supplies bleed air for various purposes in the engine and aircraft - Located between the air inlet duct and the combustion chamber - Mainly composed of rotor and stator blades - **COMBUSTION SECTION --** houses the combustion process, which elevates the temperature of the air passing through the engine - Primary function is to burn the fuel/air mixture efficiently - Located between the compressor and turbine section - Consists of parts such as the case, diffuser, liner, snout, dome/swirler, fuel injector, and igniter - **Types: can, annular, can-annular** - **TURBINE SECTION --** converts a portion of the kinetic energy from the exhaust gasses into mechanical energy to power the compressor and accessories - Primary function is to absorb about 60-70% of the total pressure energy from the exhaust gasses - Located downstream of the combustion chamber - Main parts include inlet guide vanes, turbine blades, turbine case, and turbine shaft - **Types of turbine blades: impulse, reaction, and impulse-reaction turbine blades** - **EXHAUST SECTION --** comprises several components with distinct purposes - Located directly behind the turbine section, the exhaust section extends until the gasses are ejected at the rear as high-velocity exhaust gasses - Main parts include exhaust cone, tailpipe, and exhaust nozzle - **ACCESSORY SECTION --** provide space for mounting accessories necessary for engine operation and control - Secondary functions include serving as an oil reservoir or sump and housing accessory drive gears and reduction gears - **TURBINE ENGINE PROPULSION PRINCIPLE** - To summarize, the principle used by a gas turbine engine to propel an airplane is based on Newton's third law of motion, which states that for every action, there is an equal and opposite reaction 1. **INLET --** air enters through the inlet 2. **COMPRESSOR --** the compressor increases the air pressure before it enters the combustion chamber 3. **COMBUSTION CHAMBER --** in the combustion chamber, the compressed air mixes with fuel and is ignited, creating expanding hot gasses 4. **TURBINE --** these hot gasses drive the turbine 5. **EXHAUST --** the gasses exit through the exit - Therefore, when the engine accelerates a mass of air (action), it applies a force to the aircraft (reaction) VII. **PHILIPPINE CIVIL AVIATION REGULATIONS** - **PCAR PART 1 -- GENERAL POLICIES, PROCEDURES, AND DEFINITIONS** \- Establishes the foundational rules, general procedures, and definitions that apply to Philippine civil aviation. \- Provides guidelines for regulatory enforcement and interpretation of key terms used in aviation. - **PCAR PART 2 -- PERSONNEL LICENSING** \- Defines the requirements for licensing aviation personnel (pilots, maintenance engineers, etc.). \- Covers qualifications, training, experience, and medical fitness necessary for obtaining and renewing licenses - **PCAR PART 3 -- APPROVED TRAINING ORGANIZATIONS (ATO)** \- Regulates the certification and oversight of training institutions for aviation professionals. \- Ensures compliance with standards for instructors, facilities, courses, and safety practices. - **PCAR PART 4 -- AIRCRAFT REGISTRATION AND MARKING** \- Details the procedures for aircraft registration and issuance of registration certificates. \- Establishes rules for displaying aircraft identification and marking requirements for Philippine-registered aircraft. - **PCAR PART 5 -- AIRWORTHINESS** **-** Outlines standards for maintaining aircraft airworthiness, including inspections and certification. \- Governs aircraft maintenance, modification, and mandatory checks to ensure safe operations. - **PCAR PART 6 -- APPROVED MAINTENANCE ORGANIZATIONS (AMO)** **-** Regulates maintenance organizations, requiring certification and oversight. **-** Specifies staffing, facility, and documentation requirements for performing aircraft maintenance and repairs. - **PCAR PART 7 -- INSTRUMENTS AND EQUIPMENT** \- Lists mandatory instruments and equipment for aircraft to ensure safe flight, including communication, navigation, and emergency gear. \- Ensures compliance with equipment standards for operational and safety purposes. - **PCAR PART 8 -- OPERATIONS OF AIRCRAFT** **-** Governs rules for flight operations, including commercial, private, and general aviation. \- Specifies responsibilities of pilots, flight crew, operational planning, and air traffic regulations for safe **aircraft operation.** - **PART 9 - AIR OPERATOR CERTIFICATION AND ADMINISTRATION:** **-** Sets requirements for obtaining an AOC, including an operations manual, safety management system, and necessary resources, with compliance overseen through audits and inspections. - **PART 10 - COMMERCIAL AIR TRANSPORT BY FOREIGN AIR CARRIERS:** \- Regulates foreign carriers in Philippine airspace, requiring operational permission, safety documentation, and adherence to operational guidelines. - **PART 11 - AERIAL WORK:** **-** Regulates specialized operations (e.g., aerial survey, crop dusting), requiring specific training, certification, and tailored safety protocols. - **PART 13 - ACCIDENT AND INCIDENT REPORTING:** **-** Requires timely reporting of accidents/incidents to CAAP, outlines investigation protocols, and mandates record-keeping and cooperation. - **PART 18 - DANGEROUS GOODS:** **-** Governs safe handling and transport of hazardous materials per ICAO standards, with strict rules on personnel training, passenger restrictions, and cargo safety. VIII. **AIRCRAFT MAINTENANCE PUBILICATIONS AND ATA 100 SPECIFICATIONS** 1. **AIRCRAFT MAINTENANCE MANUAL --** formal document which details the way in which all maintenance tasks carried out on an aircraft shall be accomplished. - Lubrication system functional checks - Servicing excluding structural repairs and modifications 2. **ILLUSTRATED PARTS CATALOG** -- specific to a/c type -- published by manufacturers - Comprehensive detail - Illustrations - Part numbers - Use for identifying parts and illustrating assembly 3. **STRUCTURAL REPAIR MANUAL --** descriptive information for identification and repair of a/c primary and secondary structure - how to assess the damage - classify the damage - how to repair the damage 4. **WIRING DIAGRAM MANUAL --** how the a/c wires are connected and where they should be located 5. **SYSTEM SCHEMATIC MANUAL --** simple diagrams that illustrate the major components and function of a system such as hydraulic or fuel - Detailed information that will help the mechanic to diagnose a problem or repair 6. **COMPONENT MAINTENANCE MANUAL --** details how to accomplish off-a/c maintenance tasks on an a/c component 1. Information required to check, repair, adjust and test units or assemblies 2. Contain enough detail to return the component to a serviceable condition 7. **MATERIAL SAFETY DATA SHEET --** provides information on the hazards of working with a chemical and procedures that should be used to ensure safety and proper storage 8. **FAULT ISOLATION MANUAL --** series of steps to be used when troubleshooting a problem - Replacing parts, one after another, until a faulty part is found and replaced 9. **MASTER MINIMUM EQUIPMENT LIST --** document prepared by the a/c manufacturer during a/c certification - lists items in an a/c that be deferred with little to no effect on the safety of the operation 10. **MINIMUM EQUIPMENT LIST --** prepared by an operator or an airline based on the MMEL - MEL is approved by the airline's national aviation authority - More restrictive than MMEL 11. **CONFIGURATION DEVIATION LIST --** listing of approved non-structural external parts that may be missing but the airplane remains airworthy 12. **SERVICE BULLETIN --** communicate details of modifications which can be embodied in a/c - Used to inform owners and operators about critical and useful information on a/c safety, maintenance or product improvement 13. **AIRWORTHINESS DIRECTIVES --** notification to owners and operators of certified a/c that a known safety deficiency/hazard with a particular model of a/c, engine, avionics or other system exists and must be corrected - **MANDATORY** 14. **ADVISORY CIRCULAR --** information and guidance by describing an acceptable means, but not the only means, of demonstrating compliance with aviation regulations and standards 15. **SUPPLEMENTAL TYPE CERTIFICATE --** certifies that a modification or improvement to an a/c, engine, or propeller has been approved and complies with the existing type certification standards\\ 16. **TYPE CERTIFICATE DATA SHEET (TCDS) --** provides vital information about the design, specifications, and the operational limitations of a specific a/c or engine model 17. **TASK CARD --** tailored description of a maintenance task prepared from original documentation by a technical support office to facilitate the correct completion of that task by those assigned to complete it 18. **SERVICE INFORMATION LETTER (SIL) --** information on part, product improvement or maintenance information designed to enhance the longevity of a part 19. **SERVICE INSTRUCTION --** describes modification, process, and other information pertinent to the maintenance, repair and overhaul 20. **ENGINEERING ORDER --** used to manage and plan maintenance to comply with the requirements that are identified by technical publications - Can either be date-based, meter-based or maintenance event-based IX. **ATA CHAPTER LIST** - **ATA 08 LEVELING AND WEIGHING. ** - **ATA 12 SERVICING - ROUTINE MAINTENANCE ** - **ATA 24 ELECTRICAL POWER ** - **ATA 27 FLIGHT CONTROLS ** - **ATA 28 FUEL ** - **ATA 29 HYDRAULIC POWER ** - **ATA 32 LANDING GEAR ** - **ATA 36 PNEUMATIC ** - **ATA 39 ELECTRICAL - ELECTRONIC PANELS AND MULTIPURPOSE COMPONENTS ** - **ATA 61 PROPELLERS ** - **ATA 71 POWER PLANT ** - **ATA 74 IGNITION ** - **ATA 79 OIL ** - **ATA 80 STARTING ** - **ATA 81 TURBINES (RECIPROCATING ENGINES) **