Response to Flammable Liquid Emergency Incidents, Second Edition PDF
Document Details
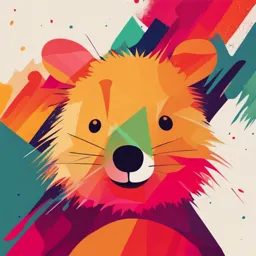
Uploaded by ValiantSunstone
Tags
Summary
This document is a guide for responding to flammable liquid emergencies, specifically incidents involving petroleum products. It provides definitions of key terms, descriptions of different response units, and details on various aspects of facility fire protection. The document appears to be from an educational or training program.
Full Transcript
Response to Flammable Liquid Emergency Incidents, Second Edition Final Version – April 2014 DEFINITIONS The following definitions shall be used throughout this manual and in any pre-incident plans. Additives: Products found at bulk petroleum storage facilities that are stored in smaller...
Response to Flammable Liquid Emergency Incidents, Second Edition Final Version – April 2014 DEFINITIONS The following definitions shall be used throughout this manual and in any pre-incident plans. Additives: Products found at bulk petroleum storage facilities that are stored in smaller tanks and are added to gasoline or diesel fuel in very small quantities. Additives are typically similar to diesel fuel in combustibility, but may present greater health hazards. Aqueous Film Forming Foam (AFFF) and Alcohol Resistant Aqueous Film Forming Foam (AR-AFFF): AFFF and AR-AFFF are the most commonly used foams available today, with the AR version making it the most versatile foam as well. AFFF is synthetic foam with the basic elements being fluorochemical surfactants, hydrocarbon surfactants, and solvents. Just as in AR- FFFP, the addition of a polymer gives AR-AFFF its alcohol resistant properties. These versatile foams have excellent knockdown ability, good heat resistance, good fuel tolerance, good vapor suppression and in the AR version, excellent alcohol tolerance. AFFF is available in a wide range of percentages from 1% to 6%. AR Foam Unit: A self-contained fire engine that has been specifically designed to respond to flammable liquids incidents within the NOVA region. Units carry AR-AFFF foam and may have pump-and-roll capability. ARFF Unit: This is a self-contained unit specifically designed to have a pump-and-roll capability and a minimum of 100 gallons of foam concentrate; may have duel agent application ability and duel agent application. The minimum ARFF vehicle requirements are established by Title 14 Code of Federal Regulations Part 139 – Certification of Airports, NFPA 414: Standard for Aircraft Rescue and Fire-fighting Vehicles, and NFPA 1901: Standard for Automotive Fire Apparatus. Auto-Ignition Temperature: The lowest temperature where a substance will auto-ignite and combust without any other sources of ignition. Barrel: Petroleum products handled by pipelines and in bulk storage are measured in barrels. A barrel (abbreviated bbl) contains 42 U.S. gallons. Combustible Liquid: Liquid having a flash point above 100 degrees Fahrenheit (37.78 Celsius) and below 200 degrees Fahrenheit (93.33 Celsius). Fixed Facility Containment: Primary containment: Includes tanks and piping where product is contained under normal circumstances. Secondary containment: Diked area around tanks where product will be contained in the initial stages of an incident. Secondary containment also includes controlled drainage areas at loading racks and other areas where spills are likely to occur. Product may be diverted to secondary containment from other areas, or may be diverted from secondary containment to remote impounding areas. 2 Response to Flammable Liquid Emergency Incidents, Second Edition Final Version – April 2014 Tertiary containment: Additional area where product can be contained in the event of a catastrophic incident. Product may also be diverted to this area for remote impounding. Fixed Facility Fire Protection Features: Fixed Foam System: Complete foam delivery system that can provide finished foam to a specific area without intervention. This type of system includes a water supply and a foam supply for a set duration to control an anticipated incident. These systems may be equipped for automatic operation or may require manual initiation. Portable Protection: Foam delivery system that can be carried or wheeled. Semi-Fixed Foam System: A foam delivery system that is similar in concept to a dry standpipe. This system consists of piping and foam discharge outlets that are installed to protect hazard areas but have no supply of foam or water connected to them. These systems require action by the fire department. Topside Foam System: A system of fixed foam chambers (a device where foam solution is combined with air to produce finished foam) and piping designed to deliver finished foam from above the surface of the contents of the tank. This may be a fixed or semi- fixed system. Subsurface Foam System: A system in which foam solution is injected at the bottom of the tank and rises to the surface of the product. This may be a fixed or semi-fixed system. Rim Protection: A system used on some floating roof tanks where protection is provided to the rim of the roof only by use of a foam dam. Flammable Liquid: Any liquid having a flash point below 100 degrees Fahrenheit (37.78 degrees Celsius) and having a vapor pressure not exceeding 40 psi absolute. Flexible Fuel Vehicle (FFV): An alternative fuel vehicle with an internal combustion engine designed to run on more than one fuel, usually gasoline blended with either ethanol or methanol fuel. Fluoro-Protein Foam (FPF): Fluoroprotein foam is much like protein foam, but with a fluorocarbon surfactant added to the ingredients. This foam provides good knockdown ability, excellent heat resistance, excellent fuel tolerance, excellent vapor suppression, and no alcohol tolerance. FPF is available in 3% and 6% versions. Foam Application Methods (Fixed Facility): Type I: Obsolete method no longer used in the NOVA region. This type of application was intended to deliver finished foam to burning surface gently and with minimal agitation. Type II: Fixed foam outlet, either subsurface or topside, designed to deliver finished foam to surface of burning liquid with restricted agitation. 3 Response to Flammable Liquid Emergency Incidents, Second Edition Final Version – April 2014 Type III: Use of master streams and hand line nozzles to deliver finished foam to the burning surface in a manner resulting in some agitation of the surface. Foam Task Force: Response consisting of two AR foam units, one pump-and-roll unit, two engines, one battalion chief, and one hazardous materials asset (if not already dispatched). Hydrocarbon: Organic compound found in petroleum products, containing primarily hydrogen and carbon. Most hydrocarbons are refined from crude oil or have been extracted from vegetable fiber. Typical hydrocarbon fuels include gasoline and diesel fuel. Hydrophilic: A substance having a strong affinity for water. Leak: Release of product from primary containment, such as a tank, pipe, valve, etc. Leaks may be controlled or uncontrolled. In a controlled leak, the flow of product has been stopped by some action, such as closing a valve. In an uncontrolled leak product is still actively flowing. Loading Rack (Fixed Facility): Area where tank vehicles are loaded with product for delivery outside the facility. Operating Modes: Operating modes indicate the type of action that is currently being taken. The mode can be changed to a more or less aggressive attack as the situation dictates or as additional resources become available. It is important that all personnel operating at the incident understand the implications of the current mode and are made aware of any change. Offensive Attack Mode: A commitment of resources to aggressive leak, spill, and fire control objectives; used where additional risk is justified because rescue operations can be quickly achieved, the spill or leak can be quickly contained, or the fire can be quickly extinguished. Defensive Attack Mode: Uses resources to achieve less aggressive objectives, such as limiting the overall size or spread of the problem. Used where the benefit of offensive attack is not worth the risk involved, but where other actions can be taken to mitigate the hazard or protect exposures. Non-Intervention Mode: Taking no immediate action other than isolating the area until the risk of intervention is reduced to an acceptable level, as operations may transition between offensive and defensive strategies. This operating mode may be used while assembling resources to commence an offensive attack. Petroleum Distillate: Combustible liquids, including diesel fuel, heating oil, and jet fuel. Pipeline: DOT-regulated carrier of product. The Northern Virginia region is served by two petroleum pipeline companies, Colonial Pipeline and Plantation Pipeline. These pipelines are underground for most of their route. Pipeline Manifold (Fixed Facility): Piping that incorporates control valves to deliver product from the pipeline to storage tanks. 4 Response to Flammable Liquid Emergency Incidents, Second Edition Final Version – April 2014 Polar Solvent: Flammable liquids that mix readily with water. Examples include alcohols, ketones, and lacquers. Product: Generic term for petroleum fuels. Product Pumps (Fixed Facility): Pumps, usually located within secondary containment, which deliver product. Pump-and-roll Unit: A self-contained unit that is specifically designed to respond to flammable liquid incidents with in the NOVA region. Units may carry AFFF or AR-AFFF foam. These units are typically found at airports. Reformulated Gasoline (RFG): Gasoline in which the composition has been changed to reduce automotive emissions. RFG has lower levels of volatile compounds and benzene and contains oxygenates such as ether or ethanol. RFG with greater than 10% oxygenate additives reacts more like a polar solvent and should be treated as such. Spill: Product that is outside primary containment as a result of a leak. Spills may be further defined as contained or uncontained. A contained spill is a situation where the spilled product is within a defined area, such as secondary or tertiary containment, and there is little risk of further spread. As per the Emergency Response Guide: Small Spill: A spill occurring from a container or package approximately 55 gallons or less, a small cylinder, or a small leak from a large container with a minimum flow. Passenger vehicles with leaking tanks are considered small spill responses. Large Spill: A large spill exceeding 55 gallons or multiple spills from multiple small packages or containers. Large spill responses include any incident at or involving pipelines, horizontal tanks, tank farms, or flammable liquid tanker trucks or rail cars. Tank Construction Features (Fixed Facility): Cathodic Protection: A system of corrosion protection that uses a small electrical current. Cone Roof: A large tank with a fixed steel roof and an exposed product surface within the tank. Covered Floating Roof: A large tank that has an external steel roof and an internal floating roof. Double Bottom: A feature of large tanks designed to prevent environmental contamination from a leak at the bottom of the tank. Leak detection equipment is typically provided within the space between the double tank bottoms. Foam Dam: Fire protection feature installed on some floating roofs to limit foam application to the rim area of the roof. 5 Response to Flammable Liquid Emergency Incidents, Second Edition Final Version – April 2014 Eye Brow Vent: A hooded metal structure attached to the exterior top edge of a fixed roof tank, which provides weather protection over the vent ports for an internal floating roof tank. Geodesic Dome Roof: A lightweight roof type of characteristic design. Horizontal Tank: An aboveground tank of smaller capacity, typically not more than 30,000 gallons, oriented with the cylinder in a horizontal position. These tanks may be of single or double wall construction. Tanks with single wall construction should be provided with secondary containment. Open Floating Roof: A large tank that is open at the top but has a roof that floats on top of the product within the tank. Weak Roof to Shell Seam: A weld that is less strong allowing the roof to blow away in an explosion, exposing the surface of the interior of the tank. Vapor Recovery/Combustor Systems (Fixed Facility): Systems designed to recover or burn petroleum vapors for environmental reasons. Vapors are collected by tank vehicles at the point of delivery and are returned to the bulk petroleum storage facility complex for disposal. Vapor recovery systems return the vapors to liquid state by a process of compression and/or cooling. Vapor Density: The weight of a vapor compared to the weight of dry air. Substances lighter than air are said to have vapor densities less than 1.0 and those heavier than air have a vapor density greater than 1.0. Specific Gravity: The ratio of the density of a liquid to the density of water. 6 Response to Flammable Liquid Emergency Incidents, Second Edition Final Version – April 2014 GENERAL CONSIDERATIONS FOR SPILLS AND FIRES INVOLVING CLASS B FUELS Fires involving petroleum products and chemicals pose significant problems for firefighters. The Northern Virginia region has significant potential for events involving these substances. There are also significant resources in the area to deal with these types of incidents. This chapter will deal with general considerations involving all petrochemical incidents. The most common types of petrochemical events will be covered in greater detail later in this manual. Some or all of the following hazards will be present during events involving flammable liquids:  Fire or explosion;  Ignition by heat, sparks, or flame;  Vapors that may explode;  Vapors that may travel;  Containers that may explode when heated or punctured;  Health hazards;  Vapors or liquid that may be toxic if inhaled, ingested, or absorbed;  Vapors and liquid that may produce burns or irritate skin and eyes;  Inhalation of vapors that may cause dizziness or nausea; and/or  Environmental hazards that potentially endanger wildlife, streams, and rivers (which may influence the operations of critical systems such as water distribution and waste water treatment facilities). Recommended Response Actions Incidents involving Class B fuels (spills and/or fires) must be carefully managed. Upon the arrival of the initial unit officer, command procedures must begin. The Incident Command System (ICS) provides the needed management tools to coordinate the resources assigned to the incident. The ICS organization has the capability to expand and contract to meet the needs of the incident. Operating modes indicate the type of action that is currently being taken on the scene of an emergency incident. The mode can be changed to a more or less aggressive attack as the situation dictates or as additional resources become available. It is important that all personnel operating at the incident understand the implications of the current mode and are made aware of any change. The initial units arriving on the scene of a flammable liquids incident should declare the operating mode. There are three operating modes typically used at an incident involving a flammable liquid: offensive attack mode, defensive attack mode, and non-intervention mode.  Offensive attack mode is a commitment of resources to aggressive leak, spill, and fire control objectives. This operating mode is used where additional risk is justified because rescue operations can be quickly achieved, the spill or leak can be quickly contained, or the fire can be quickly extinguished. 7 Response to Flammable Liquid Emergency Incidents, Second Edition Final Version – April 2014  The defensive attack mode uses available resources to achieve less aggressive objectives, such as limiting the overall size or spread of the problem. This operating mode is used where the benefit of offensive attack is not worth the risk involved, but where other actions can be taken to mitigate the hazard or protect exposures.  Non-intervention mode means taking no immediate action other than isolating the area until the risk of intervention is reduced to an acceptable level so that operations may transition to offensive or defensive strategies. This operating mode may be used while assembling resources to commence an offensive attack. Consideration must be given to the use of the non-intervention mode particularly when dealing with ethanol fires or large-scale incidents, such as a rail car fire, until appropriate resources are available. First Engine Company Actions The first engine company shall perform the initial size-up and identify any obvious life hazards. During the size-up, note any visual indicators of hazards, such as smoke, vapor clouds, active leaks, or odors. The first engine should initiate hazard protection for life safety and rescue measures if deemed necessary. The first engine company should make contact with the responsible party or the facility representative, determine the current situation, and ask about any actions taken prior to arrival of fire department personnel. When delivering the on-scene report, the first engine company officer (initial Incident Commander) must confirm staging area and make initial assignments to units arriving on the scene. The first engine company should perform reconnaissance (recon) of the suspected hazard area for leak/spill/fire. Recon teams should be equipped with appropriate personal protective equipment (PPE), detection equipment, binoculars, and thermal imager. The recon team must comply with the two-in/two-out rule. The reconnaissance report should answer the following questions:  Is there any life hazard?  What is the product type? Is it flammable or combustible? Is it a hydrocarbon or polar solvent? Refer to Emergency Response Guidebook.  Is the product still leaking? If so, what is the flow rate of the leak?  Can the leak be controlled?  How much has been spilled?  What is the approximate surface area of the spill or fire?  What is the total potential spill?  Is the spill or fire contained?  Where is the product going?  For a spill, are any potential ignitions sources present?  For fires and spills, what are the primary and secondary exposures?  Is the area secure from unauthorized entry? 8 Response to Flammable Liquid Emergency Incidents, Second Edition Final Version – April 2014 When the recon is complete, the first engine should report the findings to the Incident Commander (IC) and make recommendations concerning the initial operating mode and the initial isolation zone. When resources are not readily available or delayed, strong emphasis must be given toward identification and protection of exposures. Refer to Appendix A: Quick Response Guides. First-arriving Battalion Chief The first-arriving battalion chief should obtain the situation report from the initial IC and assume command of the incident. He or she should then assemble essential staff and facility assistance to support unified command. A key role of the first battalion chief is to perform the risk assessment for fire department personnel and review life safety considerations and potential exposures for civilian personnel on site. Based on the initial size-up, the following items should be considered:  The need for greater alarms,  Establishing an operating mode for the incident and the creation of a plan for continued operations,  Ensure specialized needs and resources for the incident are enroute, to include apparatus with portable folding tanks for remote foam fill/draft sites,  EMS support,  Deployment of units from the staging area, and  Scene security and safety. The battalion chief should also confirm with facility representatives the level to which emergency plans have been initiated. Refer to Appendix A: Quick Response Guides. Water Supply In addition to all of the considerations that the initial company officer and or IC must be aware of, water supply should be a high-priority consideration during any flammable liquids emergency. Even prior to arrival on the scene the company officer should be considering how companies will get the volume of water necessary to control the incident. For flammable liquids emergency incidents involving fixed facilities such as distribution centers, storage facilities, and other commercial manufacturing or storage facilities, municipal water supplies or onsite commercial water supplies should be used. These systems were engineered so that potential releases and or fires could be controlled and or contained within the facility boundaries. Each of these facilities should be preplanned with the water supply information readily available to include primary and secondary water supply considerations. Additionally, specialty extinguishing devices such as fire pumps, foam systems, and remote distribution 9 Response to Flammable Liquid Emergency Incidents, Second Edition Final Version – April 2014 systems should be identified along with any special operational instructions. A copy of this preplan should also be kept in an identified location on the premises so that in case the first due units are not available for response, the initial company officer can locate them for quick reference. The location should be entered into the CAD system for identification. In non-fixed facilities, response knowledge of area water supplies should again be known to the first engine officer as well as the IC. In areas that are served with municipal water systems this should include the location of the largest main systems in the first due area as well as off-loop water supplies for secondary and tertiary units depending on the location and type of incident you are responding to. The rule of thumb when developing your water supply plan is that the supply should be able to flow at least 1000 GPM of finished product per unit flowing product. The company officer and/or IC need to factor in all of the exposures or potential exposures in their final water supply calculations. The IC should establish a water supply group or officer in the initial stages of the incident. This responsibility should be given to the third due engine officer or to the second due battalion chief. Other resources available to the IC are the availability of large-diameter hose (LDH) trailers. Dulles International Airport has a trailer which carries 3000 feet of 7-inch LDH and the City of Fairfax carries 900 feet of 5-inch LDH on the foam nozzle trailer and 1000 feet on the foam pump trailer. When an incident occurs on a limited-access highway or in a rural area, water supply must take a higher priority. During these incidents the strategies and tactics described in the Water Supply for Suburban and Rural Firefighting manual should be used. Early activation of a tanker task force, even during the initial dispatch would be beneficial and is encouraged as it allows for sufficient water to arrive faster in case a quick knock down or life safety issue is present. Depending on the size and dynamics of the incident several drop sites might be needed. The water supply group leader will need to use 1000 GPM of finished product per unit as the goal for each of the drop sites. As stated earlier, use of LDH resources should be taken into consideration for limited access areas such as railways access roads and or limited access highways. It is strongly encouraged that rural and limited access areas, such as highways, be preplanned for flammable liquids incidents. 10 Response to Flammable Liquid Emergency Incidents, Second Edition Final Version – April 2014 CHARACTERISTICS OF CLASS B FUELS For many years, the fire service only had to be concerned with two categories of petroleum products, flammable and combustible liquids. Technological advances have led to the creation of many additional categories of these liquids. Most of these products fit into more than one clinical definition of a flammable liquid. The two main types of product that may be dealt with are hydrocarbons and polar solvents. Hydrocarbons are organic compounds containing only hydrogen and carbon and are found primarily in petroleum products and coal. Most hydrocarbons are a byproduct of crude oil or have been extracted from vegetable fiber. Typical hydrocarbon fuels include gasoline and diesel fuel. Polar solvents are products of distillation that are water soluble. As a result, polar solvents have an attraction to water and controlling spills and fires of this product necessitate the use of special types of foams. Examples or polar solvents include alcohols (such as ethanol), ketones, and lacquers. Hydrocarbons and polar solvents may be further classified as flammable or combustible. Flammable liquids are those having a flash point below 100 degrees Fahrenheit (37.78 degrees C) and having a vapor pressure not exceeding 40 psi absolute. Combustible liquids have a flash point above 100 degrees Fahrenheit (37.78 degrees C) and below 200 degrees Fahrenheit (93.33 Celsius). Reformulated gasoline (RFG) is gasoline in which the composition has been changed to reduce automotive emissions. RFG has lower levels of volatile compounds and benzene, and contains oxygenates such as ether, methanol or ethanol. RFG with greater than 10% oxygenate additives reacts more like a polar solvent and should be treated as such. Ethanol1 The addition of ethanol to gasoline presents some unique firefighting challenges. Traditional methods of firefighting against hydrocarbon (gasoline) fires have been found to be ineffective against these polar solvent-type (ethanol-blended) fuels. While gasoline will tend to float on top of water, ethanol fuels are water soluble and will tend to blend with the water. For this reason, the use of Alcohol-Resistant (AR) foam as a means of extinguishing an ethanol fire is recommended. Common Ethanol Fuel Mixtures Ethanol-blended fuels may include blends of gasoline and ethanol in any ratio, but presently there are three common ethanol-blended fuels. Most common is E-10 (10 percent ethanol and 90 percent gasoline) which may be labeled as RFG or oxygenated gasoline. Also common is E-95 1 Information for this section of the manual obtained from the Ethanol Emergency Response Coalition’s Complete Training Guide to Ethanol Emergency Response, http://www.ethanolresponse.com/pages/resources. 11 Response to Flammable Liquid Emergency Incidents, Second Edition Final Version – April 2014 ethanol that has been denatured with 5 percent unleaded gasoline, finally, E-85 (85 percent ethanol and 15 percent gasoline) is sold into a developing market as a retail blend for Flexible- Fuel Vehicles (FFV) only. While ethanol has been consistently blended at the 5.7 percent and 7.7 percent level in California, it is more frequently blended at the 10 percent level by volume across the United States. With a requirement to replace the octane improvement lost by state bans on Methyl Tertiary Butyl Ether (MTBE), the demand for ethanol has increased dramatically. The EPA has recently approved a new fuel blend that will be appearing in the marketplace for consumer use. Emergency responders should be aware of the introduction and distribution of E- 15 (15 percent ethanol and 85 percent gasoline). This blend is an increase from the most common gasoline: E-10 (10 percent ethanol and 90 percent gasoline). Chemical and Physical Characteristics of Ethanol Emergency responders are generally not going to encounter pure ethanol unless they respond to an event at an ethanol production facility or a rail trans-loading facility. Ethanol for use in motor fuel blends will generally be denatured with up to 5% gasoline or a similar hydrocarbon (E-95) for any style of transport. Nevertheless, the following discussion of the characteristics of ethanol will be based on pure rather than denatured product since the denaturant will have minimal effects on product characteristics. Pure ethanol is a polar solvent that is water-soluble and has a 55°F flash point. Ethanol has a vapor density of 1.59, which indicates that it is heavier than air. Consequently, ethanol vapors do not rise, similar to vapors from gasoline, which seek lower altitudes. Ethanol’s specific gravity is 0.79, which indicates it is lighter than water but since it is water-soluble (hydrophilic) it will thoroughly mix with water. Ethanol has an auto-ignition temperature of 793°F and a boiling point of 173°F. Ethanol is less toxic than gasoline or methanol. Carcinogenic compounds are not present in pure ethanol. Like gasoline, ethanol’s greatest hazard as a motor fuel component is its flammability. It has a wider flammable range than gasoline: the lower explosive limit (LEL) is 3.3 percent and the upper explosive limit (UEL) is 19 percent. In a pure form, ethanol does not produce visible smoke and has a hard-to-see blue flame. In a denatured form there is little to no smoke, but a slight orange flame may be visible, Figure 1. Figure 1: Slight orange flame may be visible in denatured ethanol.2 2 http://www.fsi.illinois.edu/content/courses/programs/ethanol/ 12 Response to Flammable Liquid Emergency Incidents, Second Edition Final Version – April 2014 Interestingly, ethanol and some ethanol blends can conduct electricity while gasoline does not and is considered an electrical insulator. The most striking difference between these two fuels is that, unlike gasoline, ethanol mixes easily with water. While it is possible to dilute ethanol to a condition where it no longer supports combustion, this is not practical in the field as it requires copious amounts of water. Even at 5 parts water to 1 part ethanol, it will still burn. One of the noticeable differences in the blended fuel versus unblended gasoline is the visual difference of the smoke and flame characteristics. Higher concentrations of ethanol produce less black smoke and decreased visible flame color. Another noticeable difference of ethanol-blended fuels under fire conditions is that when foam or water has been flowed on the burning product, the gasoline will tend to burn off first, eventually leaving the less volatile ethanol/water solution which may have no visible flame or smoke. Transportation and Transfer of Ethanol and Blend Fuels The majority of the fuel ethanol (E-95) is transported from the production facilities to the storage depots by rail. Storage depots that do not have rail access receive E-95 by road tankers. There is some transfer of fuel ethanol from rail tanks directly to road tankers called trans-loading. An example of this is the trans-loading facility in the City of Alexandria located at 1000 S. Van Dorn Street. This is considered to be an interim process until permanent transfer facilities can be provided. Trans-loading has the greatest potential for transfer problems due to a lack of permanent fixtures or safety equipment. Emergency responders should be aware of this process occurring in their areas. There is some fuel ethanol transported by waterway on board barges or freighter ships. At this time very small amounts of ethanol-blended fuels are being experimentally transported by pipeline to evaluate the feasibility of larger-scale pipeline transfers. Ethanol transportation incidents with fire put firefighters in a position of greater hazard than hydrocarbon transportation incidents. The chemical properties of ethanol as well as the physical and mechanical properties of rail cars and tanker trucks with structural damage can increase the risk of catastrophic failures similar to a BLEVE. Factors influencing this change in fire behavior include:  Gasoline tends to burn off first (higher vapor pressure).  Less heat produced from ethanol fires compared to hydrocarbons.  Ethanol burns more efficiently than hydrocarbons.  Ethanol is 100% miscible in water.  20% ethanol solution is flammable.  The presence of water separates gasoline from mixture.  Ethanol has a higher flash point.  Greater percentage of gasoline in the mix produces greater heat and possibility of soot production in tank. 13 Response to Flammable Liquid Emergency Incidents, Second Edition Final Version – April 2014 Note: Due to catastrophic failure occurring in past incidents, it cannot be emphasized enough that in an incident involving an ethanol carrier and fire, the declaration and use of the non-intervention mode while maintaining maximum safe distances is imperative. Assembling appropriate resources and protecting exposures must become the main objectives. Ethanol Foam Firefighting Various foams have been around for over fifty years and have proven to be very effective on hydrocarbon fuels. However, these foams that were not developed for application on alcohol- or ethanol-blended fuels are simply ineffective on fuels containing alcohols or ethanol. This is because the alcohol or ethanol content of the blended fuel literally attacks the foam solution, absorbing the foam solution into the ethanol-blended fuel. Foam that is designed to be alcohol resistant forms a tough membrane between the foam blanket and the alcohol-type fuel. It is crucial that these AR foams are used in combating ethanol-blended fuel fires, including E-10. This is an important point. Additionally, to be effective, these foams must be applied gently to the surface of the alcohol- or ethanol-blended fuels. Otherwise, the foam is absorbed into the fuel and will not resurface to form an encapsulating blanket. Extensive testing done at the Ansul Fire Technology Center indicated that even at low-level blends of ethanol with gasoline, as low as E-10, there is a major effect on foam performance. The testing also indicated that with high-level blends of ethanol with gasoline, even AR foams required careful application methodology and techniques to controls fires. AR-type foams must be applied to ethanol fires using Type II (fixed foam chambers) gentle application techniques. For responding emergency services, this will mean directing the foam stream onto a vertical surface and allowing it to run down onto the fuel. Direct application to the fuel surface will likely be ineffective unless the fuel depth is very shallow (i.e., 0.25 inches or less). Type III application (fixed and handline nozzle application) is prone to failure in ethanol-blended fuels of any substantial depth. The only time it is effective is when it is deflected off surfaces, such as tank walls, to create a gentle style application. It has also been found that even with indirect application off surfaces, it may require substantial increases in flow rate to accomplish extinguishments. Therefore, in situations where AR foam cannot be applied indirectly by deflection of the foam off tank walls or other surfaces or there is no built-in application device to provide gentle application, the best option may be to protect surrounding exposures. Another property of alcohol- or ethanol-type fuel fires is that they require a higher flow rate (application rate) of foam to extinguish fires. AFFF-type foams require approximately 1 gallon per minute (gpm) foam solution flow for every 10 square feet of burning surface on a hydrocarbon-type fuel. Ethanol-blended fuels require approximately double that flow (2 gpm/10 square feet) of an AR-type foam solution for products not in depth. For ethanol-blended fuels in depth the required foam flow will be 3 gpm/10 square feet. As with all types of foam, mixing percentage is dependent upon the type and design of the foam concentrate. Departments that are subject to incidents involving the various blends of fuels found on highway incidents or at storage facilities should strongly consider converting to AR foam concentrates or develop a means of having a cache of AR foam readily available. If a department has a specific hazard that only involves non-alcohol or non-ethanol blended fuels, they may want to consider 14 Response to Flammable Liquid Emergency Incidents, Second Edition Final Version – April 2014 non-AR foam for that specific hazard. However, for over-the-road incidents they should have AR foam readily available. Keep in mind that AR foams are effective on both alcohol fires and hydrocarbon fires. As a matter of fact, some of the AR foams have quicker knockdown abilities and longer foam retention times than some of the traditional protein-based hydrocarbon foams. It is also recommended that a thermal imaging camera be used to more accurately determine if a fire is completely extinguished, especially during sunlight hours. Since AR foams are universally effective on both ethanol-blended fuels and non-ethanol-blended fuels, they would be the foam of choice. When uncertain as to whether the fire encountered is an alcohol- or ethanol-blended fuel, fire departments may want to consider doubling their application rate (gpm) ability since ethanol-blended fuels require a higher rate of flow, keeping in mind that increasing the flow rate also increases water requirements. Ethanol Emergency Response Coalition (EERC) testing provides information regarding foam application and ethanol/ethanol blend fuel fires. Overall, AR-AFFF proved to be the most effective and most versatile agent tested. It was the only agent that was successful in all fire test scenarios. For detailed testing data please visit www.ethanolresponse.com. 15 Response to Flammable Liquid Emergency Incidents, Second Edition Final Version – April 2014 FUEL SPILLS AND FIRES Small Spills A small spill, as defined earlier in this manual, is a spill occurring from a container or package approximately 55 gallons or less, a small cylinder, or a small leak from a large container with a minimum flow. Passenger vehicles with leaking tanks are considered small spill responses. Small spills occurring inside a structure should be managed by a structure fire assignment for the type of building in which the spill is located, as well as a hazardous materials response (per jurisdictional guidelines). The resources required for the management of a small spill not occurring inside a structure include the following:  One engine company with atmospheric monitoring capabilities.  The engine company officer should consider a hazardous materials response (per jurisdictional guidelines).  If spill ignites, a Foam Task Force (FTF) (two AR foam units, one pump-and-roll unit, two engines, one battalion chief, and one hazardous materials asset if not already dispatched) should be requested. Large Spills A large spill, as defined earlier in this manual, is a spill exceeding 55 gallons or multiple spills from multiple small packages or containers. Large spill responses include any incident at or involving pipelines, horizontal tanks, tank farms, or flammable liquid tanker trucks or rail cars. The resources required for the management of a large spill with or without fire include the following:  4 engines  2 specialty units – one must be an aerial device  2 EMS units  1 battalion chief  1 command aide  1 EMS supervisor  1 Foam Task Force (FTF) (two AR foam units, one pump-and-roll unit, two engines, one battalion chief, and one hazardous materials asset if not already dispatched)  A hazardous material response (based on jurisdictional requirements) Incident Commanders should request a tanker task force response in non-hydrant areas. 16 Response to Flammable Liquid Emergency Incidents, Second Edition Final Version – April 2014 TANKER TRUCK INCIDENTS There are four tactical approaches to tanker truck incidents. 1. First, assemble the resources and extinguish the fire with Class B foam. Be sure an adequate foam and water supply is available before initiating the attack. Blended alcohol fuels will require an AR foam concentrate. 2. Second, for combustible liquids, extinguish the fire with water fog when it can be done without creating environmental problems with the runoff. Large, hot fires of combustible liquids (such as tank trucks) will require foam application for timely extinguishments. 3. Third, protect adjacent exposures, and allow the fuel to burn itself out. If the incident occurs in a rural area, obtaining sufficient water can be a problem. Develop plans for sustaining water supplies with fire department vehicles or large-diameter hose relays along major roads and expressways. 4. And lastly, un-ignited leaks and spills should be diked immediately at a safe location and the liquid covered with foam to suppress and control the flammable vapors. Remove all ignition sources. Figure 2: Tanker truck at loading facility. Before or during response, units should obtain initial information concerning weather conditions, especially wind direction and speed, and, if available, the name of the product involved in the incident. Also, find out if the product is still leaking, pooled in a spill, or burning. Are there fumes or vapors adjacent to the site? What is the location of the product and/or vapors? Are they on the road, in a ditch, or in the sewers? Are they blocking access of emergency vehicles? Are they blocking access to people or property? While en route, responders should plan to approach only from the uphill/upwind direction if possible. Review the product (if known) in your reference materials, including exposure 17 Response to Flammable Liquid Emergency Incidents, Second Edition Final Version – April 2014 symptoms, reactions with extinguishing or diking agents, health effects, and initial actions recommended. There is a great likelihood that an over the road transport vehicle will carry an ethanol-based product. Since both gasoline and ethanol-blended fuels have very similar physical and chemical characteristics, they will be transported in the same general types of containers and tanks. The most prevalent style of transport of the blended fuels that emergency responders will encounter will be by MC-306 and Department of Transportation (DOT)-406 style road tankers, Figure 3. These tankers are non-pressurized and have a capacity up to 9,000 gallons. Depending on the types of product being carried, the tanker is divided into compartments. Figure 3: Example of a MC-306/DOT406. The MC306/DOT406 has outlets on the underside of the trailer for on- and off-loading the product. In addition to the outlets on the bottom, pressure and vacuum relief devices will be the same as those that are currently found on gasoline-style transport takers. The valve is internal to the tanks with breakaway piping, remote shut-off controls, and vapor recovery systems. Vents and caps can fail or leak as a result of rollover accidents. Properly marked 10¾-inch placards should be visible on all four sides making identification of the product easier. Tankers carrying ethanol and ethanol-fuel blends will generally be placarded with a flammable placard or a United Nations (UN) 1203 flammable placard when transporting lower ethanol concentrations up to and including E-10 blended fuels. The E-85 ethanol blend will carry a new designation for ethanol-blended fuels: UN 3475, Figure 4. The E-95 (denatured or Fuel Ethanol) ethanol-blended fuel will be placarded with a UN or North American (NA) 1987 flammable placard. E-100 (pure ethanol) will be placarded as UN 1170. Note: Due to catastrophic failure occurring in past incidents, it cannot be emphasized enough that in the instance of an incident involving an ethanol carrier and fire that the declaration and use of the non-intervention mode while maintaining maximum safe distances is imperative. Assembling appropriate resources and protecting exposures must become the objectives if there are no immediate life safety hazards. Rescues must be performed only after a risk vs. benefit analysis has been performed. Since there is a good chance that an MC306/DOT406 style road tanker will carry an ethanol- based product, the suggested primary attack is with an AR-AFFF finished foam. The preferred method of attack would be the use of an AR-AFFF unit. The AFFF pump-and-roll unit would remain as RIT or back up to the AR-AFFF. If life rescue is necessary, the pump-and-roll unit is capable and can function as the attack unit in a limited role. Initial actions include rescuing occupants of vehicles (body recovery can wait) and protecting exposures. 18 Response to Flammable Liquid Emergency Incidents, Second Edition Final Version – April 2014 Figure 4: An E-85 placard.3 Initial Operations It may take time to assemble the proper resources for a tanker truck on fire or leaking. Focus on your size-up and scene management skills to begin to bring order to what may be a complicated incident involving multiple vehicles and people. It might be helpful to remember the five steps of managing a multiple casualty incident and adjust accordingly depending upon your particular circumstances. Refer to Appendix A Quick Response Guides. Safety  The first arriving unit’s priority is scene safety.  Stay back and check out the situation slowly and carefully before doing anything.  Position apparatus uphill and upwind.  Stay away from wet areas or spills.  If vapors are suspected, maintain a safe distance-the invisible cloud is usually much larger than the visible cloud.  If no release is detected, look for people who are ill or unconscious. If people are down, maintain a safe distance until the situation and product is identified.  Some flammable/combustible liquids and vapors are toxic and can be absorbed through the skin and standard protective clothing and have no odor.  Do not approach unless product is identified. Treat unidentified products as a highly toxic, violently reactive, or explosive substance.  Mitigate IDLH if appropriate. 3 Photo by John Sachen. Source: http://firegeezer.com/2009/09/23/placarding-update/. 19 Response to Flammable Liquid Emergency Incidents, Second Edition Final Version – April 2014 Size-up  Ascertain type of incident: fire, spill, fire with spill.  From a distance (500 feet) use binoculars to look for placards or other warnings and the product name or number on the tractor or trailer.  Get information from people on the scene (driver, eyewitnesses, shipping papers or other identifying paperwork).  Determine scope of incident: number of involved vehicles and/or people affected.  Determine best scene access.  Determine water supply.  Pay extra concern to exposures. Allow the tanker truck to burn and assign units cool/protect the exposures.  Remember that the tractor or uninvolved portion of a multi-unit (tractor trailer or multiple trailers with a single tractor) is an important exposure. It may be necessary to disconnect the tractor or unhitch a trailer and remove it from exposure. Diking around the vehicle or damming a drainage ditch may be required to limit a running-spill fire.  Use master streams or other unmanned heavy caliber streams to keep suppression resources remote.  Attack from high ground with the wind at your back, checking for any overhead wires and coordinating streams so they do not oppose each other. Flush the fire away from exposures and into less hazardous areas. If agent is limited, use it to protect exposures. Agent that runs off is wasted. Do not wash away foam blankets with water streams. Send  Give a situation report to communications.  Request additional resources as needed (such as hazardous material, foam).  Initiate evacuations as needed; request law enforcement to assist.  Warn any incoming units of hazards. Set Up  Establish and maintain command until relieved.  Declare an operational mode: offensive, defensive, non-intervention.  Establish a staging area.  Set up scene access and egress.  Set up a perimeter using fire line tape or other means.  Establish an isolated holding area for personnel or victims who become contaminated. Patient Triage  Consider both the patients for triage as well as vehicles and any other problems which may be occurring or have occurred.  Assign units to triage people or problems – you may have to step back from the incident and send in a reconnaissance team in appropriate PPE to check the situation. The team 20 Response to Flammable Liquid Emergency Incidents, Second Edition Final Version – April 2014 should go in slowly and use combustible gas indicators and explosion proof lights and radios – and stay out of observed spills. Appendix A contains a guide to use as a helpful resource in tanker truck incidents. RAIL INCIDENTS The resources required for the management of rail car incidents are the same as those resources required for a large spill (as outlined earlier in the manual). This section provides information on dealing with a rail incident involving cargo, specifically rail tank cars. Though some of this info may also be pertinent to passenger trains, the main intent is in dealing with rail tank cars containing flammable liquids. Flammable liquids will be found most often in general service rail cars (