QFD (1).pptx
Document Details
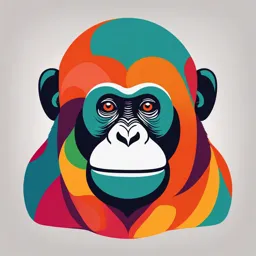
Uploaded by SafeDiscernment
University of Strathclyde
Full Transcript
QFD Vicky Hamilton e: [email protected] This session… So we identify a problem area, then what do we do? Must look good Must not be heavier than a bag of sugar Needs to be multifunctional Etc. Quality Function Deployment (QFD) What is QFD? Continuous Improvement method Provides focus to...
QFD Vicky Hamilton e: [email protected] This session… So we identify a problem area, then what do we do? Must look good Must not be heavier than a bag of sugar Needs to be multifunctional Etc. Quality Function Deployment (QFD) What is QFD? Continuous Improvement method Provides focus to the development cycle Strong customer focus ↓ overall time to market Supports the implementation of Concurrent Engineering Could be used throughout the whole design process. In this lecture we will look at QFD from a Product Specification perspective only QFD a brief history Pioneered by Dr. Yoji Akao (Japan) 1966 First large application in Kobe Mitsubishi Heavy Industries in 1972 Introduced in the Western hemisphere in 1980’s Early adopters include Xerox, Ford, Procter & Gamble, 3M Who uses/has used QFD? 3M, AT&T, Boeing, Chevron, Continental Rehabilitation Hospital, DaimlerChrysler, EDS, Ford Motor Co., General Motors, General Dynamics, Gillette, Hayes Brake, Hewlett-Packard, Hughes Aircraft, Hyundai Motor Company, IBM, Jet Propulsion Laboratory, Kawasaki Heavy Industry, Kodak, Lockheed-Martin, Motorola, NASA, NATO, NEC, Nissan Motors, Nokia, Pratt & Whitney, Poland Ministry of Finance, Proctor & Gamble, Raytheon, Samsung, Seagate Technology, Sun Microsystems, Texas Instruments, Toshiba, U.S. Department of Defense, Visteon, Volvo, Xerox Attributes & benefits Customer driven Reduces implementation time Promotes teamwork “Increased competitiveness” Provides documentation Improved products & services Introduces ‘Voice of the Customer’ to product design Requirements prioritised in line with customer opinion Voice of the Customer (VoC) Input of the customer in their terms good quality Nice looking cool educational fun modern geeky Quality of customers feedback Solicited/unsolicited, quantitative/qualitative, structured/random How it works? Translates VoC into quantifiable design/engineering requirements. VoC Translation Mouse trap that is good at luring mice Mouse trap has a lure radius of 20 feet Quantify the relationships between different customer requirements Focuses the development process by setting a direction for the design. Helps to identify design trade offs. E.g. customer wants more springiness, but doesn’t want extra height QFD & the House of Quality (HoQ) Graphic tool used in QFD for defining the relationship between customer needs and product/service capabilities Matrix based tool – Paper based (e.g. wall chart) – Computer based (e.g. MS Excel, QFD Capture) Uses indicators to define the interactions – Strong (positive) Value 9 – Medium (neutral) Value 3 – Weak (negative) Value 1 House of Quality (HoQ) 7 1. Customer requirements (what) 3 2. Ranked requirements by customer 3. Design requirements (how) 4. Relationships between customer and design requirements 1 2 4 6 5. Technical competitive comparison/target values 6. Competitor assessments 5 7. Relationships between design requirements Example What is important to you in the design of a phone? Connects to the car Won’t smash easily Lots of memory Fits in my pocket easily Charges quickly Good storage Good camera 1 7 3 1 2 4 5 6 2 7 3 1 2 4 5 6 3 Direction of improveme nt 7 x Weight 3 1 Has to have a good Needs to camera connect to my car Have to be able to video call 2 4 5 6 Relationships Strong Moderate ○ ▽ 9pts 4 3pts Weak 7 1pt 3 Weight x 1 2 4 5 6 Relationships Strong Moderate ○ ▽ 9pts 5 3pts Weak 1pt Weight 7 3 1 2 4 5 51 31 70 39 27 23% 14 % 32% 18% 12% (4x9)+(5x3) =51 6 Advanced Workshop 7 16GB Camera 16MP Camera 5 3 51 31 70 39 27 23% 14 % 32% 18% 12% 1 2 4 5 6 6 7 3 1 2 4 5 6 7 7 3 - 1 2 4 5 6 The design process and QFD Design Activitie s Market Benchmarki ng PDS Parametric Analysis Concept Creative methods Detail Controlled Convergenc e Manufacture FMEA Sell Design Method s DFMA Taguchi etc… QFD Cascade QFD 1 QFD 2 QFD 3 QFD 4 The translation process Requirements Matrix Design Requirements Design Matrix Engineering Design Customer Requiremen ts Design Requiremen ts Product Characteristics matrix Product Characteristics Manufacturing Purchasing Matrix Manufacturing Purchasing Operations Engineering Design Product Characterist ics Control verification Matrix Production quality control Manufacturing Purchasing Translation process e.g. Customer requirements Design requirements Engineering requirements Parts characteristics Requirement for body work to last a long time Years of durability for body part No visible exterior rust in 3 years Paint weight 2 - 2.2g/sq. Process planning Dip part in tank three times Operation requirements Time: 2min, Acid level:5-8 QFD & Industry QFD implementation issues CE implementation issues Perception of being overly complex What the customer really wants? Victims of their own success Lose contact with customers Push to shorten commercial cycle Lack of documented Case Studies Confidentiality issues Strategic competitive advantage