Case Packing Procedure Guide PDF
Document Details
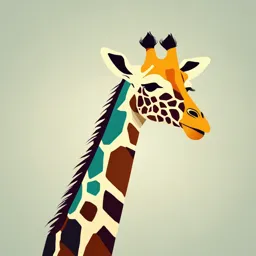
Uploaded by MagicalPeach2454
Xavier University – Ateneo de Cagayan
Tags
Summary
This document provides a detailed standard operating procedure for case packing operations, covering pre-operation setup, monitoring during operation, and machine shutdown procedures. It emphasizes quality control, machine maintenance, and safety protocols to ensure efficient and safe operations.
Full Transcript
**Before Operation** 1. Follow Good Manufacturing Practices (GMP) in the work area. 2. Preparation of the required forms and materials 1. Case Packing Machine Checklist (QMS-PRN-B-F-1013) 2. Packaging Materials Monitoring Form (QMS-PRN-B-F-8004) 3. Case Packing / Checkweigher M...
**Before Operation** 1. Follow Good Manufacturing Practices (GMP) in the work area. 2. Preparation of the required forms and materials 1. Case Packing Machine Checklist (QMS-PRN-B-F-1013) 2. Packaging Materials Monitoring Form (QMS-PRN-B-F-8004) 3. Case Packing / Checkweigher Monitoring Form (QMS-PRN-B-F-1002) 3. Check the product name and size of the product-to-run 4. Check the availability of raw materials (WAC and Hotmelt glue) 5. Coordinate with production supervisor regarding the availability of the said materials. 6. Turn on the main switch of the power supply for the machine 7. Pull and turn the knob of the air supply valve in clockwise direction to open. Push to lock 8. Check the pressure gauge of supplied compressed air if within standard requirement (6-7 bars) 9. Turn on the gluing device (Robatech). If already turned on, check the temperature if within standard specification (160-170 ℃) and also check if the hotmelt tank is filled, refill if necessary 10. Load wrap-around cartons into the tray magazine 11. Set the machine to automatic on the hand-machine interface (HMI) 12. Press the green button to start the machine. **During Operation** 1. Record the starting time of the production operation at the downtime tab. 2. Conduct hourly monitoring of the required parameters from the Case Packing Machine Checklist (QMS-PRN-B-F-1013) 1. Case Weighing (functioning) 2. Carton Code (correct and clear) 3. Glue Application (acceptable) 4. Area Cleaned 5. Appearance (acceptable) 6. Glass breakage (zero) 3. Observe proper Standard Operating Procedure and GMP inside production area. 4. Conduct regular visual monitoring on the supply of wrap around cartons in the blank magazine, and glue level in the gluing device tank. Load the WAC and glue if necessary. 5. During receiving of WAC: 7. Check the if the materials receiving tag is present in the supplied WAC. 8. Gather the details indicated on the tag and record it on the Packaging Materials Monitoring Form (QMS-PRN-B-F-8004). 5.2.1 Box Number 5.2.2 Quantity 5.2.3 Reference / P.O. Number 5.2.4 Production Date 5.2.5 Shift 5.2.6 Time 5.2.7 Supplier 6. Any deviations observed and machine trouble during operations: 9. Stop the machine. 10. Log the starting time of the machine downtime. Case Packing Machine Checklist (QMS-PRN-B-F-1013) 11. Assess the downtime if within the operator's capacity to repair. 12. Call out the attention of maintenance personnel for repair and inform the line supervisor. 13. Refer to Casepacking 4 (ROBOPACK) Operational Downtime Analysis (QMS-PRN-B-K-1100) for dealing with common operational downtime. 1. Toppled bottles inside the case packer 2. Misaligned carton in the wrap 3. Wrong lane 4. Open flap carton 5. Carton not picked by suction arm 6. Clogging of carton in discharge conveyor 7. Lying bottles in divider 14. Follow the Glass Breakage Policy for any glass breakages encountered. 15. Before the end of the shift 8. Receive the Materials Issuing Monitoring Form (QMS-PRN-B-F-8000) from the auxiliary personnel, verify and acknowledge if coinciding with Packaging Materials Monitoring Form 9. Fill-out the Case Packing / Checkweigher Monitoring Form 10. Relay information with regards to machine trouble or any deviations observed to incoming operator. Turnover accomplished report to the incoming shift operator. Turnover accomplished report to the incoming shift, the last shift should submit the accomplished report to the Supervisor. +-----------------------------------------------------------------------+ | **After Operation** | +=======================================================================+ | 1. Machine Shut Down | | | | 1. Stop the packing operation and turn off the machine including | | the gluing device. Make sure that the packer has discharged | | all the products inside before stopping. | | | | 1. Press the stop button to stop the case packing machine | | | | 2. Press the off button to turn off the gluing device | | | | 3. Close the valve for air supply | | | | 2. Stop the checkweigher by pressing the stop button | | | | 3. Tally the remaining leftover materials and record to the | | Packaging Materials Monitoring Form | | | | 4. Wrap with stretch film the leftover packaging materials and | | return to auxiliary storage | | | | 5. Accomplish all required forms and submit to Production Unit | | Head for review and signing | | | | 6. Clean and clear the work area | | | | 7. Report to Production Unit Head / Department Head any issues | | and concerns observed during production | +-----------------------------------------------------------------------+ +-----------------------------------------------------------------------+ | **Cleaning Procedure** | +=======================================================================+ | 1. Prepare all cleaning materials needed such as rags, plastic pail | | with water, soap, plastic broom, dustpan, hose for air supply, | | mop and trash bin. | +-----------------------------------------------------------------------+ | 2. Open the safety guards and set the machine in Manual mode. | +-----------------------------------------------------------------------+ | 3. Ensure that there are no bottles and cartons left in the machine | +-----------------------------------------------------------------------+ | 4. Check if there are missing/damaged parts of the machine and | | report to Line Supervisor for any unusual observation subject for | | necessary action. | +-----------------------------------------------------------------------+ | 5. Clean and clear the machine from dirt, glass bits, and fragments | | using broom and air hose. | +-----------------------------------------------------------------------+ | 6. Use the metal hook to remove broken glass from unreachable areas. | +-----------------------------------------------------------------------+ | 7. Remove the hardened glue using metal spatula in the machine. | +-----------------------------------------------------------------------+ | 8. Soak the rag in the plastic pail with clean water and soap, then | | wipe the base of the machine and the parts that are sticky and | | has oil or grease. | +-----------------------------------------------------------------------+ | 9. Wipe also the machine covers and the safety guards. | +-----------------------------------------------------------------------+ | 10. Clean also the catchment pans under the machine using broom and | | dustpan. | +-----------------------------------------------------------------------+ | 11. Wipe the sensors, reflectors and the other parts of the machine | | using dry rags with caution. | +-----------------------------------------------------------------------+ | 12. Clean and mop the entire work area of the machine. | +-----------------------------------------------------------------------+ | 13. After cleaning, close the air supply of the machine. | +-----------------------------------------------------------------------+ | 14. Place all the cleaning materials used in the designated area. | +-----------------------------------------------------------------------+ | 15. Report to Line Supervisor any issues and concerns observed during | | the production machine cleaning run. | +-----------------------------------------------------------------------+