Paint Technology 1 (PDF)
Document Details
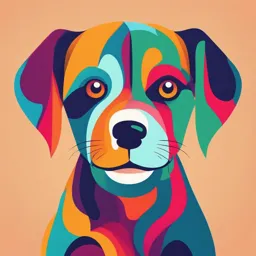
Uploaded by AwestruckRadiance2351
Tags
Summary
These notes cover paint technology, specifically focusing on the properties of various polymers used in paints. They detail the synthesis of polyamides, polyesters, and epoxies, their applications, and the properties of coatings. The notes contain homework assignments related to the topics.
Full Transcript
# PAINT TECHNOLOGY - I ## Classmate Notes ### Page 1 * Polyamide = Diacid + Diamine #### Homework * **HW Revise:** If you are developing a polyesterpolyol by choosing 4-5 raw materials, calculate the final MW of polyester, its hydroxyl value, etc. * **HW:** In epoxy resin, there is no way to th...
# PAINT TECHNOLOGY - I ## Classmate Notes ### Page 1 * Polyamide = Diacid + Diamine #### Homework * **HW Revise:** If you are developing a polyesterpolyol by choosing 4-5 raw materials, calculate the final MW of polyester, its hydroxyl value, etc. * **HW:** In epoxy resin, there is no way to theoretically calculate EEW, unlike in polyester polyol. * **HW:** Find out how polyamides are synthesized? RM, RM ratios, type of rxn (Condensation), types of polyamides, applications * **HW:** With a particular epoxy value & amine value of hardener, what amount of raw materials should one select for a particular mole ratio? * **HW:** Why dimer fatty acids are read in Polyamides? They give good flexibility. * **Benefit of alkyds over polyester is that due to the presence of oil/long chain fatty acid additional prop. are obtained such as:** * Gloss * Barrier properties * Hydrophobicity #### Properties of Coatings are Classified as: 1. **Optical Properties:** Give you sheen, gloss, flexibility, impact resistance, adhesion 2. **Mechanical Properties:** Hardness, thickness (DFT), abrasion resistance. #### Homework * **HW Revise:** Dependency of Tg, Crystallinity on * _MW_ * _Chainlength_ * **Suppose we have 1,6-Hexanediol and ethylene glycol. We react both of them w/ adipic acid and get a polyester-polyol each time. Which The polyester-polyol with 1,6-Hexanediol will be more flexible. It will also be less crystalline.** * **Generally long chain amides are rarely available. So we prefer dimer acid which gives good flexibility, to polyamides.** ### Page 2 * Polyamides are used for curing of epoxy? * Comparing Structure of epoxy polymer, we have a rigid aromatic structure of BPA which will ↓ flexibility and ↑ the crystallinity of our given polymer. As crystallinity ↑ flexibility ↓. * Anticorrossive properties are lost if the film becomes brittle (..if film is brittle, mechanical properties such as adhesion to substrate are lost). * Hardener thus has to be more flexible to neutralize rigidity of the epoxy. #### Homework * **HW:** Find temp @ which water, xylene comes out from reaction of synthesis of polyester resin (Saturated) * **HW:** Get literature on polyurea. * **HW:** What are the reactions which an isocyanate compound can undergo? (Get from polyurethane books) Reaction of NCO + H2O? Biurets, aliphonates? Polyisocyanates? NCO Adducts? Reactivity of various functional groups w/ NCO's? Reaction w/ alcohols, amines, Carboxylic groups? Types of isocyanates. * **Glycidyl Methacrylate has an epoxy ring. So if you want to modify any compound having carboxyl group, you can open up the carboxyl with this and incorporate the unsaturation in your polymer.** ### Page 3 * **Pigment Volume Conch:** * For any paint formulation basic ingredients are * Pigments * Extenders * Binders * Additives * Solvents. * Once film is cured, Solvents are no longer a part of system. * Also Extenders has hardly any concentration as compared to Pigments, Extenders and Binders. * PVC is calculated, therefore, ignoring Additives and Solvents, and also, taking into account the %NVM of the binder. * **Sap valve oxn in gets completed within 45min only (Saponification) but to ensure 100% rxn we keep for 2hrs (NO AIR CONDENSOR to binder conch, NO NEED to add water for reflux. IN THE FIRST PLACE)** * **Any paint recipe is formulated on the basis of what application it is to be used for. Eg Primer Coat requires higher conch of pigment. Usually it is a 4 coat system:** * Primer Coat (Highest Pigment Loading) * Base Coat * Intermediate Coat * Top Coat (Lowest Pigment Loading) * In automobile sector, it is but natural that one should ↑ the pigment conch and ↑ binder to improve gloss) #### Properties that depend solely on pigments are: * Porosity (As porosity ↑ Chemical Resistance ↓) * Film density * Hiding lopacity * Tensile Strength #### Optical properties are mostly dependent on binder (also on pigment to a limited extent) #### Other properties depending on binder are: * Impact resistance. * Flexibility. * Adhesion. * Chemical Properties (Also depend to little extent on pigment) * Most binders have density 1-1.1g/cm³ * Pigments have density range 2.2-8.0g/cm³ #### Homework * **HW:** Find out all pigments, extenders used in paints along w/ their density, R.I and Oil Absorption Value. * **HW:** Find out derivation for acid valve, sap value formula. * **In case of sap value we use 56.1, "Acid value" 56100, for both cases units are same, then why there is change informula? Why we use water condensor for sapvalue? Why we add water after 1hr for reflux?** ### Page 4 * **Air Condensor must be used for Hydroxyl Value only.** #### Homework * **HW:** Reaction of Sap Value? Why (0.5M) Alc-KOH and not Aq. KOH? Defn of Normality? * **Water condensor gives better efficiency of condensation because we have external supply of water to give condensation of vapors. Air condensors work on heat convection principle (Its hot at the bottom). When you go up, the temperature gets cooler and thus by self-temperature difference the vapor condenses.** * **Its used only when 'normality' is not a matter.** * **In case of Hydroxyl value, Acetic Anhydride/Pyridine Mixture is used. Acetic Anhydride is the main Raw Material which attacks the -OH group, and is not that volatile (Pyridine is solvents/catalyst)** * **HW:** Why carry out blank reading in Sap Value, not in Acid value? * **HW:** Reaction involved & Procedure of Iodine Value, Red Wij's Soln? * **Procedure:- (To dissolve sample) ** * **Sample + CCl4/CHCl3** * **Add Wij's Soln (25mL)** * **Put cork on flask, put in dark for 20min (max 0.5hrs)** * **After taking out from dark, add 10-15% KI Solution and trap.** * **Titrate Against Ma₂S2O4, every thing using Cork & titrate immediately.** * **HW:** Difference blw Iodimetric and Iodometric titration ### Page 5 * **PVC and its effects are studied strictly for paint film properties and not for liquid paint.** * It is the **ratio of the volume of pigment in paint film to the volume of pigment and binder solids (completely dried cured film). For metallic look (in say automobiles):** * PVC will be almost '0' (or maybe 5-10%) for the topcoat. * Varnish and enamels are visually clear coats. (Contain no pigments) * **How to calculate Bulk Density? (Practically):** * Say we fill a 100mL container w/ Pigments, and say wt of pigment is 50g * There are voids present throughout the volume, and thus if we tap the container lightly, the pigment particles try to fill up the empty spaces, and volume ↓ (Say free from 100mL to 90-95mL). #### As we keep tapping, after a particular point there will be no change in the volume because the voids biw the pigment particles are occupied by the pigments itself, to the highest possible extent (The pigments are not uniformly sized particles considering that volume for the given mass, the density obtained is called 'Tapped Density' and the Volume is called 'Tapped Volume'. (Density before tapping → Bulk Density')). * After the pigment particles have tried their best to occupy the interspace voids, there could still be small voids present in which the pigmentary particles couldn't fit in. * There is air occupied in these small voids. * In this condition, the maximum solvent quantity that can fit into the voids, without changing the volume of pigment occupied (is now the 'Tapped Volume') is measured and from this the 'Critical Pigment Volume Concentration' is calculated. * The CPVC is a state at which the pigments and binders are exactly in appropriate proportion, wherein there are no voids present at all. * This is a desirable cond", since if voids are present then chemical properties, density and optical properties are affected since we get porosities in the paint film. ### Page 6 * **Practically, the CPVC is calculated by knowing the oil absorption value of the pigment.** * The point at which there is just enough binder to fill all the void spaces in the pigment in a compact combination where there are only 2 phases in exact proportion. * The PVC @ the above point is referred to as CPVC? * After CPVC there is not enough binder to hold all the pigmentary particles within itself, leading to formation of porosities. * **CPVC = (Tapped Volume of Pigment) - (Volume of Solvent Used) x100 / (Tapped volume of Pigment)** * We have the flexibility of formulating a paint 30% intended CPVC paint to 25-26% PVC or even 32-33% PVC due to reasons such as cost, provided that the properties are not affected to a great extent. * **eg Say paint at CPVC gives 3000g Scratch hardness but our particular application requires only 2500g scratch hardness then we can decide to formulate the paint at PVC other than CPVC.** ### Page 7 * **EFFECT OF PVC ON FACTORS AFFECTING PAINT PERFORMANCE:** * **PHYSICAL PROPERTIES:** #### A] Density of Paint Film: * **Say density of paint film is 1glce at CPVC which is say 30% for the given formulation.** * **From 0 to 30% PVC, as quantity of pigment ↑ wrt quantity of binder.** * There will not be any porosities as there is more than enough binder to fill the voids blw pigments. * **Density of pigments > Density of binders (Usually).** * Thus, Density ↑ as PVC ↑ till CPVC. * b/w pigment particles * **Above CPVC, there is not enough binder to fill up the voids, there will be porosities generated.** * **Since air gets entrapped in the pores, and Density of Air << Density of binders < Density of pigments.) Density ↓ as PVC↑ after CPVC. Decrease in density depends on the conch of the air entrapped and thus it ↓ v. fast much above CPVC.** #### B] Tensile strength: (vertical tensile strength) * **For testing tensile strength paint film is cut in a particular size as per ASTM Standards.** * It is fixed blw 2 Jaws and a particular load is applied. * The machine pulls the film at both ends, acc." to the load. * When the film is unable to bear the strain it will break. * **Strength of the film depends on the binder content.** * Pigments/fillers added to the paint formulation give enhanced reinforcement but only to a certain level of addition (Upto CPVC). * After CPVC when the entire pigment surface is not completely wetted by the resin, deterioration starts and the film can't hold itself together due to less binder. * The film becomes weak at the points where there are pores generated and the strength thus falls off. #### B] Dry Film Thickness: * **As you go on adding pigmentation, the film thickness will increase.** * Whatever dispersion you get for your pigment, you will not be able to get that thick paint with only clear coat. * Above CPVC, pigmentation is more, and there will be even more thickness of paint film. * At very high PVC, there will be a thin layer of pigment coming out (Defect of 'Chalking') ### Page 8 * **Hess's Paint Film Defects** * **"'Distempers' are acrylic emulsion paints w/ very high PVC (containing mostly fillers like CaCO3). Rubbing fingers on the surface of film leaves chalk on the surface of your hand.** * **DFT depends on extent of pigment dispersion, which depends on bow many pigmentary particles we are able to get in their primary particle size.** * **Binder solids, PVC , total paint formulation solids, Viscosity, NVM of paint all these factors decide DFT.** * **If extent of grinding is not upto the mark, then DFT will be affected.** * **If viscosity of paint is too less, then to achieve your desired thickness you have to apply a number of coats.** * **DFT is the major factor which decides all paint properties. If DFT is too high, adhesion of paint may fail, leading to poor performance properties.** * **Emulsion paint which sometimes comes out in the form of big flakes (like a 'dorito') is a result of too high DFT.** * **If DFT is too low, then we get good mechanical properties but poor chemical properties.** * **Distance blw substrate and nozzle of spray gun, fan width affect DFT** * **Adhesion: Adhesion is a property of binder as there is more than enough binder to hold all the pigmentary particles together (even at CPVC) below CPVC there will be good adhesion. If you add further pigmentation above CPVC, adhesion ↓ since there is not enough binder to hold the pigment together.** * **Flexibility: Conical and Cylindrical Mandrel tests are used to check flexibility of coatings.** ### Page 9 * **Similar to testing for tensile strength. If there is a good elasticity to your film you'll get good elongation strength. Done on UTM (Universal Tensile Tester).** * For air drying paint, as per ASTM standards you have to allow paint to cure in the atmosphere for at least 7 days. * For stoving system, akeep substrate as it is for 24 hrs after removing from oven. Don't do testing before that. * When you keep the panel at the acute angle of the conical mandrel shape, and paint it,, the panel will bend along with that. * Cylindrical Mandrel is used for coil coating applications, where too much flexibility is required. (even more so above CPVC, as PVC ↑ flexibility ↓) * **Clear Coatings > Coatings containing pigments) (flexibility)** * **Impact Resistance: There is a metal rod called 'Indenter', which has a conical shape at the bottom. That gives intense mechanical force on the substrate. There is a fixed weight put on top of the indenter. Grades of the indenter can vary based on the height of the rod and weight on it. When you put the indenter on coated substrate, Impact on painted side of panel → Direct Impact, " " Non-painted " " → Inverse/Reverse Impact Indenter falls from a height onto substrate and thus carries some energy along with it. The coating must be able to absorb the energy and dissipate it uniformly all over the surface. Not doing so will lead to development of cracks where the indenter makes impact on the panel. Units: Pound -cm (weight of indenter, height from which it is dropped) Binder is responsible to dissipate the energy, Thus below CPVC we have good impact resistance properties. As no. of Catoms ↑ flexibility ↑ Impact resistance ↑, If pigmentation ↑ Impact resistance ↓, & as comp. to lower PVC Paint.** ### Page 10 * **Erichsen Cupping Test: Scratch hardness depends more on DFT than PVC but, it ↓ after CPVC. Abrasion Resistance after CPVC (Pigments loosely, held above eprc cause weightloss) For paint w/ PVC > CPVC, the pores containing air will be impacted first and they won't be able to dissipate the energy uniformly, causing cracking. If binder is too thick, here also film will become brittle and we get similar trend. Even if we use good quality resins, if the DFT is more than the expected one, you will not get good properties. Erichsen Cupping Test is the best test for impact resistance.** * **CHEMICAL PROPERTIES: ** * **A] Acid Resistance:** We have **5% soln of aq HCl/H2SO4, in which you dip the painted substrate/panel, after sealing all the edges of the panel**, (If you don't seal the edges the acid component can start eat penetrating from the sides of the panel) **Dip for 6 hrs** * If there is no damage to the film in the first 6 hrs , continue till 18 more hrs to complete 624 hrs test. * When we are studying the effect of Acid Resistance in relation with PVC we are assuming that the binder has good acid resistance. * We are also assuming that the pigmentary material itself has good acid resistance. * We are also assuming we have optimum DFT (50-80μ). * Suppose the acid goes through the pores to the substrate. When the acid attacks the substrate it can start going inner layer (blw Substrate and first layer of paint film. * In this process , it can make the film lose adhesion to the substrate. * **Two types of porosities can be generated in the film:** * _Direct / Continuous Porosity_ * _Discrete Porosity._ ### Page 11 * **Stain resistance is tested only for decorative coatings and wood coatings.. Also for wall paints. This is dependent on porosity.** * **HW:** Reaction of corrosion [Anode/ Cathode) * **Suppose paint thickness is 50μ. If pore depath < 50μ → Continuous porosity, pore depth >50μ → Discrete porosity. Any PVC > CPVC will generate porosities. Here we can actually see the substrate. Chemical can attack the substrate directly.** * **Suppose Hydrogen is involved as a side product of corrosion reaction.** * **Suppose there is a painted panel and there are blister formed. They are formed due to entrapment of gases. Bursting of blister will lead to rupture of film causing ↓ chemical resistance.** * **Above CPVC there are lot of pores. Thus chances of gas entrapment are few. Thus blistering resistance will ↑ after CPVC if there is a discrete porosity, then the chances of gas going out of the film are less, and thus there is an increase in blister formation (blistering resistance ↓).** * **As process of corrosion goes on, more and more Hydrogen gas will be liberated and that will start at the substrate. That gas will exert a pressure on the film from inside. In case of corrosion, the moisture and oxygen will go from film to the substrate. But the gas which is formed, will come from the substrate to the top of the film.** * **b] Alkali Resistance:** * Testing process is same, except we use 5% soln of aq. NaOH. * **c] Solvent Resistance:** * If you put painted film in oven, and solvent gets trapped within the painted film during curing, then if there are pores formed already, then solvent can easily escape the and there are no blisters formed due to the solvent. * If there is porosity and you do not give enough flash-off time for your substrate (ie after applying on substrate you immediately keep it in oven) then there will be sudden temp change, ie, after Room Temp., you are keeping it directly @ 120°C, then the solvent will immediately try to go out off the film at such high temp. During this process, if there is a continuous porosity existing, then the solvent will go off easily. * However if there is a discrete porosity then the solvent will put pressure on the film, while going out of the film. (when it is a pinhole on the film. This will not depend much on the PVC because usually the solvent leaves the film during flash off time and doesn't remain in the paint film. * If it is a storing paint which you are applying on a substrate, you usually don't allow the substrate to be put in oven immediately. We give around 10-15min flash off time. * In the industry, there are is a conveyor belt which passes thru different temperature zones so that the solvent goes on its owngradually. ### Page 12 * **d] Blocking Resistance: Related to the porousity** * In the industrial prodh set up, you have targets for painting at least (say) x no. of articles within a given shift. When you paint the article, and stack them on top of each other, it can happen that the binder from one article can easily penetrate in the coating of the next article. * This can happen if the binder is too much. * Thus there is a porosity generated on the bottom or top article. * If there is continuous porosity then binder can easily transfer from one particle to another. ### Page 13 * **Note that there will NOT be a transfer of pigment (This can only happen if PVC is >>> CPVC). Since the binder comes from one object to the other, the properties will not be upto the mark if the binder is lost.** * **e] Enamel Holdout:- Also related to porosity of film. Usually when paint film is applied, you scrape one layer and then apply the paint. If scraping of wall is not properly done, and you apply one paint coat, and on top of that you apply another coat having high gloss.** * **Suppose the earlier coat has a higher PVC than CPVC then there are already porosities generated. (Primer Coat w/ high pigmentation). We are wanting good gloss (which is property of binder), and thus we apply 2nd coat with low PVC. When you apply it on the primer paint and there is a porosity in the primer paint, the binder from the 2nd coat can easily migrate into the 1st coat. Thus there will be redn of gloss of the top coat (Which you intended to have higher gloss). If the 1st coat is not allowing the 2nd coat to develop full gloss, this situation is termed as 'Enamel Holdout'. If the 1st coat has discrete porosity, then the binder will not be lost from the 2nd coat to the 1st coat on a major extent. However if its a continuous porosity, then the binder is lost on a major extent.** ### Page 14 * **HW: Lacquer, enamel, latex. Density of air = 1.225kg/m³. [Difference Usually in R. I- of binder-pigment > Binder Air]* * **LEC4: No Syllabus Related Info.** * **LEC5:** * **④ OPTICAL PROPERTIES:** #### Gloss and Hiding: * **Gloss is property of binder.** * Thus even as you start adding pigment (even below CPVC), gloss starts ↓. * **When you go on adding pigment, the interparticle distance blw pigments ↓.** * Thus surface becomes more or less irregular and more scattering occurs than reflection. * **Above CPVC there are too many pigmentary particles in a given area. And here porosities are also generated, leading to greater scattering.** * **Here the RJ's of pigment, binder also plays a role. More the difference blw the R.I. of binder, pigment, then better will be your hiding. Also, Regularity of reflection of incident light ↓.** * **In industrial coatings, topcoat can be of 10-12% PVC also but in automobile " " is clear coat (More expensive).** * **Abore CPVC it will be a matte finish (Irregular Scattering).** * As pores are generated air will be filled up and * * **Scattering happens in an haphazard manner and gives an effect like hiding (pseudo-effect) and is called as dry hiding?. Gloss is measured using gonioscope.** ### Page 15 * **SOLVENTS** * **Suppose you don't use any solvent in the processing of your paint and your binder has high viscosity, then it will not have proper grinding of pigment and thus efficiency of the first stage (grinding stage) itself will be less. So you need to maintain a particular NVM even during the grinding stage. (Ease of processing).** * **Further reasons for using solvents in paint in addition to pigment, binder and additives are: Ease of packaging, Ease of application, Ease of handling (Transfer of material from application equipment to the substrate), To have a proper levelling of film: Suppose the viscosity is high and you are not putting any solvent. If you apply on a panel, you will get a thick paint film. Normally a mixture of solvents and not just a single solvent is added in the paint application. One should select a 'True Solvent' for your paint, and that solvent should remain in the paint film for the longest amount of time.** #### **eg if we want to make a solution of epoxy resin, GY250 (EEW 180-190) we will choose a non-** * **HW: Find out the polarity of all alcohol solvents, ketonic solvents, ester solvents, ether solvents, halogenated solvents and all aromatic solvents** ### Page 16 * **LEC 6: Molar wt = Equivalent Wt/ Charge = MW*Moles, Functionality < 1 (Pger < 1 implies that the gelation pt will reach before the reaction reaches 100%, WH2O=Removable moles of Water * 18 * Moles of Sample, Polyester Calculations Table: Assume OH value = 140, Target MW=2000, WH20** | RM | EW | Moles | Charge | CA | COH | WH2O | |---|---|---|---|---|---|---| | AA | 146 | 73 | 0.8 | 116.8 | 1.6 | 28.8 | | PA | 148 | 74 | 0.2 | 29.6 | 0.4 | 23.6 | | NPG | 1014 | 52 | x | 104x | 208x | - | | Gly | 92 | 30.6 | y | 92y | - | 34 | | **Total** | **1+x+y** | **104x+92y** | **146.4+** <br/> **104x + 92y + 114** | **2.0** | **2x+3y** | **32.4** | * **Yield @zero Acid Valve (Complete Rxn) = Yo = Total Charge - Water of condensation. 104x+92y + 114** * **Theoritical Hydroxyl Value (COH-CA). 56100 / Yo** * **140=(2x+3y-2).56100** * **104x+92y+114** * **128160 = 97640 x + 155420 y** * **2000 = 104x+92y+114** * **1+x+y-2** * **1896x+ 19084 = 2114** * **Solve Simultaneously ↓⇓ x=0.775 y=0-337** * **Average functionality F= 2CA / mi = 4 / 1+0.775 +0.33 = 1.89** * **Pgel = 2 / F = 2 / 1.89 = 1.05** #### Back calculating charges: * **Total Charge = 258.004** * **WNPG = 80.6** * **WGAY = 31.004** #### Back Calculate Yield: * **Yo = 225.604** * **COH = 2.561** ### Page 17 * **In actual practice OAV is not possible, usually we get around SAV. The yield'y 'A & MW M₂ at the point at which We stop the rxn (ie @ Acid Valve 'A') can also be calculated.** * **LEC7: Yield at a particular acid value 'A'.** * **YA = 56100** * **56100-18A** * **X yo** * **Corresponds to total water coming out of the 'rxn @Acid Value 'A'.** * **Theoritical MW @ Acid Value 'A'.** * **MA = YA** * **(Mi-CA)** * **56100** * **Acid valve @ to (When all reactants are added initially) = CA X56100.** * **Total Charge 2×56100 = 258.004 = 434-88** * **Say we are to calculate yield @ Acid Valve '50' and the corresponding MW: Y A = 56100 X 225.604 (56100-18×50) = 229.28 MA= 229-28 (2.105-2.0) + 229.28x50 / 56100 = 741.168** * **We are calculating mass of the reaction product@ a particular Acid Valve, where in that stage there is unreacted alcohol which is in excess, and also unreacted acid. This is the reason YA> Yo** #### Homework * **HW:** Structure, properties of Etergonic Acid. * **Find all dicarboxylic acids having unsaturations in it so that it can be used for unsaturated polyesters.** * **Structure of TMA (Trimelletic Anhydride), the major diacid used to make water reducible polyesters.** * **For the above formulation, find out how much TMA should be added if we want a final polyester of 100 mg KOH/g sample. (Later neutralize loong AV using amines, addition of which will give water solubility to the polyester by forming salt @ the -C001 (Triethylamine is preferred). Since TMA is added MW of final product will be different) ** ### Page 18 * **First say @ 'to AV = 434.88. We continue rxn till Av drops to around 50-60. Then we add TMA to make Av'100'. Then continue the ren till water of condensation stops coming out. At the pt when we add TMA, we have a carboxylexcess (The system becomes rich in Carboxyl) and the conch of OH as compared to the carboxyl equivalents goes down. So your polyester will NOT have hydroxyls. Only w/ those -OH which are free will the carboxyls continue reacting, and water of condensation will start coming out of the ran mony Once the water of rxn stops, you can ensure all the hydroxyls have been consumed. In this case we will get -OH Valve ~ 10-15mg KOH/gsample (It will be theoritically o but practically not possible. After neutralizing the hydroxyls , whatever carbonyls arestill present, those will contribute to a certain AV.** * **LEC8:** ### Page 19 ### Page 20 * **& Design an Alkyd Resin having 70% Oil Length using DCO, Assume that Imol of Phthalic Anhydride is used 2A 148gm. Pentaerythritol and Phthalic Anhydride ← To react this completely, assume 0.5mol be req=2B0% 689m We want excess hydroxyl We assume 10% hydroxyl on basis of equivalents. Thus we will take 0.5 +10% = 0.55mol Pentaerythritol Gm's of oil reqd = Oil length [Qty PA + Qty Penta - H₂O] excess = 6.8gm and Total Penta Reqd = 68+6.8 = 74.88gm 100-Oil length Water of rxn from Imol PA will be Imol H2O = 189 Gm's of oil req = 70 [148+748-18) = 477-866 30** * **For We** | MW | EQ | Raw Material | Charge | Moles | CA | eOH | WH 20 | |---|---|---|---|---|---|---|---| | 878 | 292.67 | DCO | 477.866 | 0.54 | 1.62 | 1.62 | - | | 148 | 74 | PA | 148 | 1 | 2 | 2 | 18 | | 136 | 34 | PE | 700.66 | 2.09 | 3.62 | 3.82 | 18 | | **** | **** | **Structure of DCO:-** | **** | **** | **** | **** | **** | | **** | **** | _CH2-O-C-(CH2) 7-CH=CH-CH=CH-(CH2)5-CH₃_ | **** | **** | **** | **** | **** | | **** | **** | _CH-0--(CH2)7-CH=CH-CH=CH-(CH2)5-CH₃_ | **** | **** | **** | **** | **** | | **** | **** | _CH2-0-C-(CH2)7-CH=CH-CH=CH-(CH2) 5 - CH₃_ | **** | **** | **** | **** | **** | | **** | **** | _→57'C' + 6'0''+ 98 'H'_ | **** | **** | **** | **** | **** | | **** | **** | _MW=878 = 878_ | **** | **** | **** | **** | **** | ### Page 21 * **LOFA, PE,PA Assume sxgm of LOFA →Path PA neutralizn →LOFA exccess once you cake,calc. quantity of PE reg to For I mol oil we get 3 equivalents of each (3ex and зеон) We have used 0.54 mol of Oil** * **Replace 20%, Or of penta by EG, thor by gayeer of yo ** ### Page 22 * **N-methylpyrrolidone, polar BP also SOLVENTS (Contd.): Classes of solvents: ix Alcohols > Esters v> Halogenated (mostly banned toxic) vi> Hydrocarbon Solvents vii> (q Solvents & (subsect) DMF, THF iv> Ketones vüⅲ> Oxygenated solvents (eg Dioxane) In case of true solvent polarity diff. b/w solrent and polymer is hardly 2-3 units. (polarity index) polarity of solvent must highes For every polymer , there is a true solvent existing. The true solvent allows the polymer to extend its chains further once the polymer is dissolved in that solvent. Initially the viscosity goes on ↑ to a certain extent when you dissolve the polymer in its true solvent eg PVC + Cyclohexanone + Toluene solute True solvent Latent solvent (To↓ viscosity) ↳ Polymer'swells' In some of the solvents the polymer gives a swollen mass, without actually dissolving and giveng a homogenous soln. To that viscosity again we can add diluent Suppose we have 2 polymers, a polyester-polyol and an acrylic polyol mixed in a coating system and we are curing the entire system using isocyanate In this case, all the binders must be having a common true solvent. Diluent will then have to be added, which gives a clear homogenous solution when the dryer is added in the true solvent. If the true solvent evaporates fast, then the painted film will not have proper levelling of the substrate. Non-solvents are NOT used in coating applications (when they are added to a polymer solution, the polymer precipitates out.)** ### Page 23 * **Solubilility parameter of polymer mainly depends on its structure. We can check purity of solvent using HPLC IR, UV-Visible, GC. For comparing Craporation rates we either use PET ether or butyl acetate (High BP/ Louweraporating solvent, Low BP).