Duties of the Control Technician - Training Material PDF
Document Details
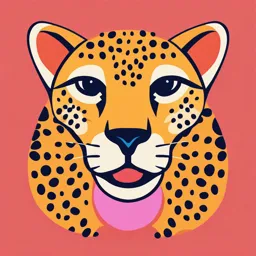
Uploaded by UncomplicatedTennessine1728
Nanyang Polytechnic
Tags
Summary
This document provides training material on the duties of a control technician. It covers topics such as process operations, handling emergency situations, process monitoring, troubleshooting. The document includes examples and illustrations using the Distributed Control System (DCS) and also includes the importance of coordination with field technicians and maintenance staff.
Full Transcript
Topic 3: Duties of the Control Technician TOPIC 3A: PROCESS OPERATIONS 1 Official (Closed) and Sensitive-Normal Control Technician: “Brain” behind the Chemical Plant Field technicia...
Topic 3: Duties of the Control Technician TOPIC 3A: PROCESS OPERATIONS 1 Official (Closed) and Sensitive-Normal Control Technician: “Brain” behind the Chemical Plant Field technicians Control technicians 2 Official (Closed) and Sensitive-Normal Control Technician: aka “Panel-man” or “Boardman” 3 Official (Closed) and Sensitive-Normal Meanwhile in a peaceful control room… Source: https://www.youtube.com/watch?v=gd_AKIkIod8&t=26s Watch how the control technician manages the chemical plant with ease via the e-lecture! 4 Official (Closed) and Sensitive-Normal Learning outcomes 1. Describe the roles and responsibilities of a control technician. 2. Identify the operating limits of key process parameters 3. Execute startup procedures using the ENVISION simulator and approved SOP Official (Closed) and Sensitive-Normal Key Responsibilities of A Control Technician 1. Topic 3a: Process Operations 2. Topic 3b: Handling Emergency Situations 3. Topic 3c: Process Monitoring and Troubleshooting 4. Topic 3d: Others (Quality Control, Coordination) 6 Official (Closed) and Sensitive-Normal Distributed Control System (DCS) A DCS uses a computer screen to interface with the process plant. All controlling is done from a keyboard and bank of computer monitors. Each DCS has a series of screens schematically displaying major equipment, piping or trends. Technician can adjust the setpoints of parameter and then return to the area screen to view how the system respond to the change. All actions executed by the technician and responses of the parameters are recorded in the database for trending and troubleshooting purposes. 7 Official (Closed) and Sensitive-Normal So what can be done from the control room? Communicate with other Start/ stop chemical Change process parameters process technicians equipment by changing setpoints Monitor the process Be alerted by alarms if Initiate plant shutdown parameters real time there is abnormality using emergency button 8 Official (Closed) and Sensitive-Normal Watch the full and detailed explanation via the e-lecture! Operating a “Live” Plant! 9 Official (Closed) and Sensitive-Normal DCS Screen #1: Process parameters which are out of range are highlighted in different colour. Technician must know how to respond e.g. change setpoint? Lower Process unit production? Cut steam? Watch the full and detailed explanation via the e-lecture! Interlock alarms also flash on the screen. Technician has to acknowledge and determine the cause for the alarms. Beside each piece of equipment, Colour coded operating parameters of pipelines, valves and temperature, pressure, flow equipment 10 rate, level etc are displayed. Official (Closed) and Sensitive-Normal DCS Screen #2: Timestamp facilitates Process Trends troubleshooting e.g. technician can observe that as the reactor temperature rises, the reactor pressure rises at the same time Watch the full and detailed explanation via the e-lecture! Historic trending makes it easier for monitoring parameters during process upset 11 Official (Closed) and Sensitive-Normal DCS Screen #3: Technicians can choose to acknowledge or silent the low Alarm Summary priority alarms so that he/she can focus on the critical alarms Alarms are arranged in chronological order and helps in incident investigation and understanding sequence of events 12 Topic 3: Duties of the Control Technician TOPIC 3B: HANDLING EMERGENCY SITUATIONS 1 Official (Closed) and Sensitive-Normal Learning outcomes 1. Analyze how safety shutdown interlocks/ system works 2. Analyze process parameters using historical trends and alarm summary. 3. Perform emergency shutdown in the control room.. Official (Closed) and Sensitive-Normal DCS Screen #4: Shutdown and Interlock Systems Watch the full and detailed explanation via the e-lecture! Emergency shutdown button which can be activated in the event of fire, major leakage etc Technician must know what the critical process parameters which will cause the unit to trip or cause a runaway reaction. 3 Official (Closed) and Sensitive-Normal Handling emergency situations The control room technician must be ready to respond to a variety of different emergency situations such as: 1. For emergency within unit (gas leak, hydrocarbon spillage): Shut the unit down immediately and isolate the area where the leak/spillage/incident has occurred 2. Loss of a major utility (electrical power, cooling water, instrument air, steam): Shut down the unit safely by quickly putting emergency back-up systems such as emergency power generators in service. 3. Catastrophic situation (major fire or toxic explosions): Keep personnel on his or her unit informed about the situation by radio. He may be needed to help direct emergency response teams while maintaining the process unit under control. 4 Official (Closed) and Sensitive-Normal Handling emergency situations The control room technician must be ready to respond to a variety of different emergency situations such as: 1. For emergency within unit (gas leak, hydrocarbon spillage): Shut the unit down immediately and isolate the area where the leak/spillage/incident has occurred 2. Loss of a major utility (electrical power, cooling water, instrument air, steam): Shut down the unit safely by quickly putting emergency back-up systems such as emergency power generators in service. 3. Catastrophic situation (major fire or toxic explosions): Keep personnel on his or her unit informed about the situation by radio. He may be needed to help direct emergency response teams while maintaining the process unit under control. 5 Official (Closed) and Sensitive-Normal Emergency Shutdown Systems (ESD) Emergency Shutdown System (ESD) is designed to minimize consequences of emergency situations related to off-spec products, equipment damage, excessive temperature/pressure, loss of containment, fire etc. The ESD for a process control system includes an ESD controller which provides output signals to the ESD solenoid valve which will then respond in a fail safe state. Examples of common ESD: - Stopping all feed flow to reactor when there is loss of cooling water, excessive reactor temperature/ pressure, detection of catalyst poison in feed - Stopping all fuel to fired heater when burner flame is extinguished - Tripping large rotating equipment such as compressors or turbine when there is excessive bearing temperature or motor vibration readings - Tripping of pumps when tank level is too low Official (Closed) and Sensitive-Normal Emergency Shutdown Systems (ESD) Typically, each ESD is configured in a triplicated format ( "2 out of 3 logic"). Shutdown action is initiated when any two of the three process parameters exceed the maximum tolerable limits. The “2 out of 3 logic” has the following advantages: - Online testing and maintenance of individual channels is possible. - The unit is not shut down due to a single spurious trip signal. Official (Closed) and Sensitive-Normal Emergency Shutdown Systems (ESD) Typically, each ESD is configured in a triplicated format ( "2 out of 3 logic"). Shutdown action is initiated when any two of the three process parameters exceed the maximum tolerable limits. The “2 out of 3 logic” has the following advantages: - Online testing and maintenance of individual sensors is possible. - The unit is not shut down due to a single spurious trip signal. Official (Closed) and Sensitive-Normal Process Interlocks An interlock is a process condition (s) that must be met to allow a process or equipment to start/continue operation: 1. Flow interlock – reactor cannot be started up unless the coolant flow is meets a minimum value 2. Pressure interlock –control valve which controls flow to a tank cannot open if the water pressure is too low 3. Level interlocks - centrifugal pump cannot start if the tank level is too low. Official (Closed) and Sensitive-Normal Topic 3: Duties of the Control Technician Topic 3c: Process Monitoring and Troubleshooting 1 Official (Closed) and Sensitive-Normal Learning outcomes 1. Describe the common process deviations associated with plant operations 2. Describe the rules of thumb for monitoring process variables 3. Collect and analyze process data associated with the process deviations. 2. Identify possible causes of the process deviation. 3. Recommend and execute investigative and corrective actions to stabilize the process. Official (Closed) and Sensitive-Normal Process Monitoring Without instruments revealing important process information, it would be impossible to control or monitor a process. A technician’s knowledge of what is happening in their process is revealed to them by the instruments Technicians must understand how their instruments work and how to tell when the instruments are not working correctly. Use pressure, temperature, flow, and level to determine if the equipment is operating and running in the most efficient manner. Accuracy of instruments is worthless if not wisely acted upon by alert, well trained technicians. Official (Closed) and Sensitive-Normal Case study: Why process monitoring and troubleshooting is crucial Watch what may happen if effective process monitoring and troubleshooting is done properly via the e-lecture! Note: This process plant was built in the 1970s. Therefore, it was not equipped with several important control systems, cooling water mechanisms and automatic shutdown systems that modern plants have. Abnormal situations were handled manually which are the key reasons why the incident happened. 4 Official (Closed) and Sensitive-Normal Monitoring Temperatures Temperature instruments tend to have a lag time when responding to temperature changes Temperature will not rise instantaneously Animations to illustrate the concepts can be viewed in e-lecture! Official (Closed) and Sensitive-Normal Monitoring Temperatures Even a slight change in temperature in a unit can lead to undesirable consequences. Generally, an increase in the temperature will increase: This temperature chart is showing normal operation. The temperature is monitored at the inlet and at the outlet of the unit. 1. Rate of evaporation/boiling (or drop in temperature increase rate of condensation and solidification) 2. Gas volume/vapour pressure 3. Amount of dissolved material in solution 4. Rate of reaction (or reduced crystallisation) Changes in feed temperature must be recognised quickly so that adjustments can be made before there is a loss of control in the unit. An alert operator should be able to notice the upward temperature trend between t1 and t2. If left uncontrolled, excessive temperatures in the unit can lead to the production of off-spec product, dangerously high pressures, equipment damage, shutdown and costly equipment downtime for repairs. Official (Closed) and Sensitive-Normal Monitoring pressure Differences in pressure causes fluids to flow and determine the direction of fluid flow. The degree of pressure difference impacts the volume of flow (or leak). An increase in pressure in a vessel also causes an increase in boiling points of the substances in the vessel Animations to illustrate the concepts can be viewed in e-lecture! Official (Closed) and Sensitive-Normal Monitoring Pressures High pressure (e.g. in a vessel or pump discharge) generally means that there is a blockage in the outlet. Blockage can be caused by a closed valve, choked filters, or solidification of fluid in the pipe (for highly viscous materials such as polymers or waxes). Excessively high pressure may damage pipes or rupture vessels. Bursting discs and pressure safety valves (PSVs) are designed to relieve the pressure safely before the vessel is damaged. However, the activation of PSVs in the process plant is a major event because this means enormous loss of product and it often leads to major upset. Abnormally low pressure in the unit normally means that there is a leak or unknown loss of the fluid. This often result in a drop in production rate, environmental or safety issues. Official (Closed) and Sensitive-Normal Monitoring Flow Rates Changing Flow Rates can affect other variables e.g. Increasing fuel to furnace can raise the furnace temperature or releasing gases from process vessel can lower the pressure in the vessel Animations to illustrate the concepts can be viewed in e-lecture! Official (Closed) and Sensitive-Normal Monitoring Levels Most level detectors have a fast response to changes. Maintaining level may be required to protect equipment such as exchanger or pumps. Generally, level does not go to zero abruptly. A sudden drop in level may be due to loss of electricity or signal to the instrument. Animations to illustrate the concepts can be viewed in e-lecture! Official (Closed) and Sensitive-Normal Topic 3: Duties of the Control Technician Topic 3c: Process Monitoring and Troubleshooting 1 Official (Closed) and Sensitive-Normal Learning outcomes 1. Describe the common process deviations associated with plant operations 2. Describe the rules of thumb for monitoring process variables 3. Collect and analyze process data associated with the process deviations. 4. Identify possible causes of the process deviation. 5. Recommend and execute investigative and corrective actions to stabilize the process. This concepts illustrated in this topic is best understood via e-lecture as many key process parameters are visually referenced in e-lecture. Official (Closed) and Sensitive-Normal Process A: Tank Farm Operations Official (Closed) and Sensitive-Normal Normal operating conditions of TK-1 Official (Closed) and Sensitive-Normal Scenario #1: What did the oil go? The Oil Movements control technician has been moving material from TK-2 into TK-1 for the last two hours. While the level reading for TK-2 has been dropping at 5% per hour, you notice that TK-1’s level reading has only increased by 1% since the transfer started. Troubleshoot the situation, list the probable causes and investigative actions. No change in pressure Oil being transferred Level increased by only 1% Official (Closed) and Sensitive-Normal Scenario #1: What did the oil go? The Oil Movements control technician has been moving material from TK-2 into TK-1 for the last two hours. While the level reading for TK-2 has been dropping at 5% per hour, you notice that TK-1’s level reading has only increased by 1% since the transfer started and some abnormal pressure. Troubleshoot the situation, list the probable causes and investigative actions. Improper line-up – Problems with TK1 or TK2 A leak in the system product going to another level indicators tank Have both level Check that no product Confirm valve line-ups indicators checked lines are leaking are correct Manually check local Perform material Check other tanks for level gauges in both TK-2 balance calculation, unexpected level and TK-1 based on results of increase manual gauging Check that TK-2 pump is running Official (Closed) and Sensitive-Normal Scenario #2: Pressure surge alert It is a Thursday evening, and the shift has been relatively quiet. In the control room, you are monitoring oil transfer into TK-1, and no flow is currently leaving TK-1. A field technician is making an area round of the tank farm when you then notice the abnormal pressure at TK-1 and it is increasing. Troubleshoot the situation, list the probable causes and investigative actions. N2 supply fully closed 100% opened to flare Increased from 41 to 55 kPa Oil being transferred Increasing from 25% to 28% Official (Closed) and Sensitive-Normal Scenario #2: Pressure surge alert It is a Thursday evening, and the shift has been relatively quiet. In the control room, you are monitoring oil transfer into TK-1, and no flow is currently leaving TK-1. A field technician is making an area round of the tank farm when you then notice the abnormal pressure at TK-1 and it is increasing. Troubleshoot the situation, list the probable causes and investigative actions. Closed block valve along N2 bypass valve is opened PIC-100 is faulty flare line or leaking PCV-100A Check the local pressure Physically check the line Check bypass valve on gauge at the tank to up along flare line PCV-100A to confirm that confirm PIC-100 reading it is closed If all else fails, PCV-100A may be leaking (passing) Bypass valve Local PG Official (Closed) and Sensitive-Normal Scenario #3: Pressure drop detected The weather has been warm during the day, but cool at night, with ambient temperature at ~24 deg. You came on for the night shift, observed the following abnormal parameters. Troubleshoot the situation, list the probable causes and investigative actions. 100% opened for N2 entry Dropping from 41 to 27.5 kPa Dropped slightly from 25% to 21% Official (Closed) and Sensitive-Normal Scenario #2: Pressure drop detected The weather has been warm during the day, but cool at night, with ambient temperature at ~24 deg. You came on for the night shift, observed the following abnormal parameters. Troubleshoot the situation, list the probable causes and investigative actions. PCV-100A fails N2 block valve is PIC-100 is faulty closed, or PCV- closed or N2 line Leakage in N2 line 100B fails open is blocked Check the local Check the Visually inspect Visually inspect pressure gauge position of the the valve line-ups for leaks or use at the tank to valves at PVC- at the nitrogen soap solution confirm the 100A & B lines pressure Stroke PCV-100B Crack open instrument to verify that it is bypass valve of reading functioning PCV-100A to see properly if tank pressure responds. Bypass valve Official (Closed) and Sensitive-Normal Scenario #3: Pressure drop detected The weather has been warm during the day, but cool at night, with ambient temperature at ~24 deg. You came on for the night shift, observed the following abnormal parameters. Troubleshoot the situation, list the probable causes and investigative actions. 100% opened for N2 entry Dropping from 41 to 27.5 kPa Dropped slightly from 25% to 21% Official (Closed) and Sensitive-Normal Process B: Heat Exchanger Operations Official (Closed) and Sensitive-Normal Normal operating conditions of EX-101 Official (Closed) and Sensitive-Normal Scenario #1: Dwindling steam A control room operator (CRO) calls you on the radio to say that the steam low flow alarm (FAL-102) to the EX-101 heater has sounded. Troubleshoot the situation, list the probable causes and investigative actions. Low flow alarm Official (Closed) and Sensitive-Normal Scenario #1: Dwindling steam A control room operator (CRO) calls you on the radio to say that the steam low flow alarm (FAL-102) to the EX-101 heater has sounded. Troubleshoot the situation, list the probable causes and investigative actions. Loss of steam from FCV-102 fails close or FIC-102 reading is faulty source or leaking steam steam line plug Check the outlet Physically check the line Stroke FCV-102 to 100% pressure gauges to see if for any steam leaks and see if steam flow they are within normal Contact technician from increase. parameters. the steam unit to learn if there is any issues Low flow alarm Official (Closed) and Sensitive-Normal Scenario #2: Dipping water pressure While making rounds, you notice that the inlet water pressure gauge (PI-100) reads 55 PSI instead of the normal 92 PSI. Troubleshoot the situation, list the probable causes and investigative actions. Normal parameters Scenario #1 parameters Dropped from 92 to 55 PSI Official (Closed) and Sensitive-Normal Scenario #2: Dipping water pressure While making rounds, you notice that the inlet water pressure gauge (PI-100) reads 55 PSI instead of the normal 92 PSI. Troubleshoot the situation, list the probable causes and investigative actions. Faulty reading or faulty FIC-101 failed close or Pipe or exchanger leak pump plugged?? Check the PI-101 outlet Check exchanger for If there is a restriction in gauge to see if that is water leaks at the tube the valve or pipe, pump also reading low. If it is, side or exchanger flow will be low, and that may indicate a pump flanges. pump pressure will be problem. high. (Hence, unlikely) Check the pump suction /discharge valves to ensure they are fully opened. Check for abnormal sounds Official (Closed) and Sensitive-Normal Scenario #3: Foaming steam The operating shift is halfway through the night. Readings on the exit of both the shell and tube side of the exchanger have changed but none are in alarm state. Downstream users of the condensate stream notice some foaming of the water. Troubleshoot the situation, list the probable causes and investigative actions. Dropped from Dropped from 150 to 100 GPM 90 to 83 PSI Dropped from 150 to 139 degC Foaming (pH increased from 7 to 9) Dropped from 260 to 240 degC Official (Closed) and Sensitive-Normal Scenario #3: Foaming steam The operating shift is halfway through the night. Readings on the exit of both the shell and tube side of the exchanger have changed but none are in alarm state. Downstream users of the condensate stream notice some foaming of the water. Troubleshoot the situation, list the probable causes and investigative actions. FIC-100 failed close or Exchanger internal tube Faulty pump? plugged? leak Check the PI-100 outlet If there is a restriction in Run a physical pH gauge to see if that is the valve or pipe, pump sample to ensure the also reading low. If it is, flow will be low, and meter is operating that may indicate a pump pump pressure will be properly. problem. high. (Hence, unlikely) Check the pump suction and discharge valves to ensure they are fully opened. However, the first 2 causes are VERY unlikely. If there is a drop in water flow, steam outlet temperature should be rising and not dropping. Official (Closed) and Sensitive-Normal Scenario #3: Foaming steam The operating shift is halfway through the night. Readings on the exit of both the shell and tube side of the exchanger have changed but none are in alarm state. Downstream users of the condensate stream notice some foaming of the water. Troubleshoot the situation, list the probable causes and investigative actions. FIC-100 failed close or Exchanger internal tube Faulty pump? plugged? leak Check the PI-100 outlet If there is a restriction in Run a physical pH gauge to see if that is the valve or pipe, pump sample to ensure the also reading low. If it is, flow will be low, and meter is operating that may indicate a pump pump pressure will be properly. problem. high. (Hence, unlikely) Check the pump suction and discharge valves to ensure they are fully opened. However, the first 2 causes are VERY unlikely. If there is a drop in water flow, steam outlet temperature should be rising and not dropping. Topic 3: Duties of the Control Technician TOPIC 3D: OTHER RESPONSIBILITIES 1 Official (Closed) and Sensitive-Normal Learning outcomes 1. Describe the responsibilities of a control technician with regards to product quality control, coordinating tasks with field technicians and maintenance workers. Official (Closed) and Sensitive-Normal Example: Controlling the Methanol Plant Product composition Feed composition 3 Official (Closed) and Sensitive-Normal Controlling product quality Control room technician must be familiar with the specifications of all unit streams, especially the final products. 1. When the analysis results of the samples are uploaded into a database, control room technician can access and check 2. Check process variables according to standard operating parameters and discuss with field technician on any abnormalities observed in the field 3. If required, field technician may need to take another sample to verify the results 4. Make Necessary Adjustments to maintain product quality 4 Official (Closed) and Sensitive-Normal Making Necessary Adjustment to control methanol quality (by adjusting column reflux flow) Animations to illustrate the concepts can be viewed in e-lecture! 5 Official (Closed) and Sensitive-Normal Coordination with Field Technician DCS cannot do everything. Sometimes controllers or instruments fail and those functions have to be taken over manually. The field technician and control technician must work closely together and stay in contact via two- way radio. Calling Field Technician Sophia! Location please? Hey Jay! I am nearby the utility JAY area. How can I help you? SOPHIA 6 Official (Closed) and Sensitive-Normal Coordination with Field Technician (Swinging pumps) Animations to illustrate the concepts can be viewed in e-lecture! 7 Official (Closed) and Sensitive-Normal Coordination with Field Technician (Swinging pumps) Hey buddy! I need your help to swing P-12A to P-12B. It is time to do routine maintenance for P-12A Np! Let me go out to confirm suction to P-12B is lined up and discharge is closed. I will also prime P-12B first. When you are done with priming P-12B, radio me. P-12B primed and ready to roll. SOPHIA Got it. I am going to start P-12B now. Monitor for abnormal sounds before opening the discharge valve slowly Discharge valve full open. No abnormal JAY sounds. How is the flow looking? Flow is steady. I am going to shut down P-12A now. Standby. 8 Official (Closed) and Sensitive-Normal Coordination with Field Technician (Switching control valve to bypass) Animations to illustrate the concepts can be viewed in e-lecture! 9 Official (Closed) and Sensitive-Normal Coordination with Field Technician (Switching control valve to bypass) Hey buddy! We need to switch FC-11 at the column to it bypass valve. Are you available now? Ready when you are! I am doing my Area Rounds near the distillation unit You can crack open the bypass valve of FC-11 now Bypass of FC-11 cracked opened SOPHIA to 10%. How it is the flow? Controlling well. Pls continue to open the bypass by another 2 turns Opening the valve now. Will do it slowly. JAY Radio me if you need me to stop opening. FC-11 is almost fully close now. You can stop opening bypass. Can you get ready for ECP? Got it. Will radio Maintenance crew to for line breaking, after I complete ECP 10 Official (Closed) and Sensitive-Normal Coordination with Field Technician The control technician is monitoring and controlling the entire process may radio the field technicians to 1. Make manual adjustment to a specific piece of equipment (e.g. manual valves) to keep the entire process under control. 2. Check a piece of equipment that is not responding correctly (eg. pump does not start) 3. Monitor the status of equipment such as fired heaters, reactors via sight glasses for the purpose of troubleshooting The field technician then inspect and troubleshoot pieces of equipment and keep the control technician informed so that they can plan operations around the equipment. 11 Official (Closed) and Sensitive-Normal Coordination with Maintenance The two key occasions where maintenance of equipment will take place are: 1. Routine preventive maintenance of equipment: Based on the planned schedule, control room technician arrange for the field technician to shut the equipment down, while keeping the process under control, and clear it for the scheduled maintenance work. Maintenance group needs to plan the work, bring in the necessary equipment, tools, and manpower to do the repair 2. Non-routine: When an equipment critical to operations fails suddenly, the control room technician, maintenance personnel, lead technician and process engineer must come together to plan how to get the job done with minimum downtime. 12