Materiali Legno PDF
Document Details
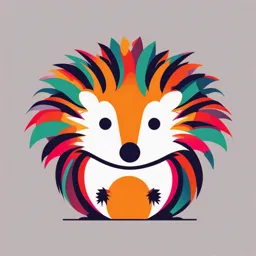
Uploaded by HearteningVariable9037
Tags
Summary
This document provides information about wood materials, including different types of wood, their properties, and characteristics. It covers topics like the structure of wood cells, physical and mechanical properties, moisture content, and various defects that can occur in wood.
Full Transcript
delle essenze legnose da cui ricava il legno utilizzato industrialmente: tavole travi, ecc. E' costituito da cellule dure e compatte, è l'alburno invecchiato, nel quale non scorre più la linfa e dal quale si estrae il cosiddetto legno massello. Legno costituito da piccole cellule cave che si svilupp...
delle essenze legnose da cui ricava il legno utilizzato industrialmente: tavole travi, ecc. E' costituito da cellule dure e compatte, è l'alburno invecchiato, nel quale non scorre più la linfa e dal quale si estrae il cosiddetto legno massello. Legno costituito da piccole cellule cave che si sviluppano nella direzione del tronco. Il vuoto all'interno delle cellule (LUME) favorisce lo scorrimento dei fluidi essenziali per la vita dell'albero mentre la parte della cellula è responsabile della resistenza meccanica del legno Le foreste di alberi che producono legno si dividono in: ANGIOSPERME producono legni duri temperati e tropicali come QUERCIA, FAGGIO, TEAK GIMNOSPERME producono legni dolci come ABETE, PINO questa suddivisione si riflette sulla struttura delle cellule ma non sulle proprietà meccaniche del legno. Le cellule sono composte da sostanze naturali: - Emicellulosa - Cellulosa - Limina lignina Legno dolce: è quello delle conifere Legno duro: è quello delle latifoglie caduche PRINCIPALI PROPRIETA' FISICHE E MECCANICHE DEL LEGNO dipendono dalla struttura delle pareti delle cellule La parate della cellula è costituita da microfibrille allineate nella direzione del tronco dell'albero. La principale differenza tra legni consiste nello spessore delle pareti delle cellule e quindi nella densità Rigidità , Il legno è un materiale rigido e leggero. La durezza del legno varia a seconda del rapporto tra la lignina e la cellulosa. Lavorabilità , Il legno è un materiale da costruzione molto versatile e facilmente lavorabile. Consente di realizzare strutture in grado di sostenere carichi e sollecitazioni anche elevate. UMIDITA' Le cellule dell'albero che contengono i fluidi necessari alla vita dell'albero, mantengono la presenza di acqua anche dopo il taglio UMIDITA' del legno è la % in peso dell'acqua rispetto al legno essiccato UMIDITA' % = peso umido - peso a secco x 100 peso a secco Con Legno verde si indica la condizione di umidità presente al momento del taglio (in genere varia dal 60% al 200% in funzione del tipo di legno (dolce o duro, alburno o durame o in relazione alle stagioni). legno tende a cedere acqua e a raggiungere un valore di equilibrio con l'umidità dell'ambiente. Si assume come riferimento un’umidità 12% che rappresenta il valore a cui si porta il legno in ambienti il cui non viene bagnato dalla pioggia L'acqua viene assorbita in parte nelle pareti delle cellule mentre la restante è libera bel vuoto interno alla cellula Stagionatura: una volta tagliato, il legno perde velocemente circa il 30% di acqua presente nelle cavità cellulari. Successivamente il legno continuerà , ma più lentamente a perdere acqua, fino a raggiungere l'equilibrio con l'ambiente circa il 12% - 23% di umidità . Per ottenere questo, le assi devono essere stagionate o essiccate. Il metodo naturale è quello che garantisce in futuro una maggiore stabilità . La stagionatura naturale la si ottiene accatastando le assi una sull'altra frapponendo dei listelli al fine di permettere la circolazione dell'aria. Poiché per raggiungere i risultati voluti sarebbe necessario molto tempo ( non inferiore all'anno con climi favorevoli), si fa ricorso a essiccazioni artificiali in appositi ambienti (essiccatoi) che sono veri e propri forni con umidità e calore controllati. Bisogna tener presente che il legno regolerà continuamente la sua umidità con quella dell'aria circostante; se viene portato in un ambiente chiuso e dotato di riscaldamento centrale, il suo contenuto di umidità diminuirà lentamente fino a circa il 10%, provocando ovviamente un maggior restringimento, accompagnato da aumento densità e resistenza meccanica. Nb. l'umidità del legno anche dopo la stagionatura non è costante varia in funzione delle condizioni ambientali Le variazioni dimensionali possono avere luogo anche dopo la posa in opera del legno. DIFETTI vedi file pdf Anomalie nella struttura del legno riguardano: - Accrescimento eccentrico del midollo - Agenti atmosferici, insetti e funghi - Crescita a spirale L'albero è materia organica vivente e, il suo legno può presentare numerosi difetti che spesso ne pregiudicano l'utilizzo tecnologico. Il tronco viene facilmente aggredito da insetti, muffe e parassiti che intaccano la corteccia e penetrano all'interno, producendo carie, infradiciamento e altri inconvenienti. Un altro difetto frequente è la cipollatura, cioè il distacco parziale tra due anelli di accrescimento. Inevitabili poi sono i nodi, che indicano la posizione di rami che non si sono mai sviluppati; i nodi, dopo l'essiccamento, tendono a staccarsi dal resto, provocando dei fori nelle tavole. Molti difetti sono dovuti all'azione del gelo: ad esempio le fenditure, spaccature radiali più o meno profonde e le lunature, che consistono nella presenza, all'interno del durame, di porzioni tenere, della consistenza dell'alburno. Un altro difetto frequente è l'eccentricità del midollo cioè la sua posizione spostata rispetto al centro del tronco, verso l'esterno, tipica di alberi che crescono su pendii molto ripidi. Un altro grave difetto è il cosiddetto imbarcamento per cui l'asse, originariamente lineare, assume conformazione curva, deformandosi irrimediabilmente. Le cause sono da ricondursi alla insufficiente stagionatura del legname prima della lavorazione, con il conseguente ritiro delle fibre. Lavorazioni del legno Le principali fasi di produzione del legname grezzo sono le seguenti: ABBATTIMENTO SRAMATURA taglio dei rami di una pianta. Questa operazione può essere effettuata prima e dopo l'abbattimento dell’albero SCORTECCIATURA è una fase del processo di lavorazione del legno nell'industria della cellulosa. Viene effettuata sul fusto dell'albero dopo l'abbattimento e la sramatura tramite macchine scortecciatrici oppure manualmente. Consiste nell’asportazione della corteccia dal tronco che viene caricato su un nastro trasportatore all'interno di rulli ruotanti contrapposti e muniti di punzoni. La scortecciatura consente di standardizzare le dimensioni del tronco dell'albero, di agevolare l'essiccazione e il trasporto del legno in segheria. Le dimensioni standard del legno permettono la movimentazione della materia prima tramite processi automatici o semiautomatici che aumentano la velocità della produzione e riducono il costo unitario. Non è comunque una fase di lavorazione obbligata. Alcune segherie sono attrezzate con macchinari appositi per eliminare l'eventuale presenza di residui sul tronco dell'albero. In alcuni casi la corteccia viene lasciata sul per rallentare l'essiccazione o per proteggere ll legno dall'attacco di parassiti, funghi e muffe. ACCATASTAMENTO è un'operazione del processo di lavorazione del legno. Dopo il taglio i tronchi sono accatastati in uno spazio aperto della segheria mediante un braccio meccanico in attesa di essere utilizzati corre input del processo produttivo. La fase di accatastamento svolge anche una funzione di prima essiccazione e di prima stagionatura del legno. Nel processo di lavorazione del legno la fase di accatastamento è generalmente collocata tra l'operazione di scortecciatura e quella di vaporizzazione del tronco. VAPORIZZAZIONE è un processo della lavorazione del legno. Dopo lo scortecciamento i tronchi sono investiti da un getto di vapore alla temperatura di 100°C per pulire il materiale dalla presenza di eventuali parassiti. Il vapore consente, inoltre , di preparare il legno alle successive operazioni di taglia. La vaporizzazione ha anche l'effetto di modificare la colorazione naturale del legno. I processi di vaporizzazione Ti processo di autovaporizzazione Si utilizzano delle apposite camere di vaporizzazione per creare un ambiente di vapore e per una gestione più efficiente del processo di vaporizzazione del legno. Il legno viene accatatato all’interno della camera. Il vapore acqueo viene generato da una fonte esterna e introdotto nella cella per investire il tronco scortecciato. Il processo di autovalorizzazione Alcune tecnologie utilizzano anche un processo di auto-vaporizzazione a camera stagna che permette di generare vapore sfruttando l'acqua contenuta nel legno stesso. Anche in questo caso il legno viene accatastato all'interno della camera. In questo caso, però, non è necessario disporre di un generatore di vapore da una fonte esterna. TRONCATURA è una operazione di lavorazione dell'albero dopo l'abbattimento che consiste nel taglio del fusto dell'albero o dei rami allo scopo di ottenere pezzi di forma circolare o tronchi più piccoli della dimensione voluta a seconda dell'uso. La troncatura viene effettuata a terra dopo l'abbattimento dell’ albero tramite l'ausilio di motoseghe. Le dimensioni dei tronchi dopo l'operazione di troncatura sono determinate dalle esigenze di trasporto o da quelle delle successive fasi di lavorazione del legno in segheria. LISCIVIAZIONE del legno è una operazione nel processo di lavorazione del legno che permette di eliminare dal legno le sostanze organiche imputridite e i parassiti, La lisciviazione può essere effettuata tramite il lavaggio del legno con acqua corrente oppure tramite lil procedimento di vaporizzazione. La lisciviazione re il legno dalle sostanze organiche che potrebbero favorire la nascita di parassiti, funghi e colonie di insetti sul legno. L'operazione di lisciviazione rende anche il legno più morbido al fine di agevolare le operazioni di taglio, tranciatura, piegatura e sfogliatura durante le successive lavorazioni. In alcuni casi la lisciviazione è utilizzata anche per scurire la tinta naturale del legno. La lisciviazione del legno rientra nelle operazioni di lisciviazione. SEZIONATURA del legno è una operazione del processo di lavorazione del tronco di un albero che consiste nel taglio del tronco in sezioni regolari per agevolare le successive operazioni di lavorazione. La sezionatura è una operazione effettuata in segheria, La tipologia della sezionatura dipende dalla forma dall'utilizzo finale del legno. Esistono diversi tipi di sezionature: Sezionatura tradizionale. La sezionatura tradizionale può avvenire mediante un taglio radiale o un taglio parallelo. SEZIONATURA A TAGLIO TRADIZIONALE Sezionatura a quartieri. La sezionatura a quartieri consiste nella suddivisione del tronco in due o più zone (quartieri) con successivo taglio delle singole zone in modo parallelo, alternativo o radiale. PRINCIPALI PROPRIETA' FISICO CHIMICHE DEL LEGNO A causa della complessa struttura del leano Il titiro è diverso lungo | 3 assi principali. Durante la stagionatura è circa del 0,1 % in direzione longitudinale mentre può variare da 1 a 10% in direzione tangenziale ed è inferiore nella radiale circa 5 %. PROPRIETA' DEL LEGNO - Materiale ANISOTROPO (presenta proprietà differenti a seconda di come viene. sollecitato) - Densità in genere inferiore a quella dell'acqua (nb. generalmente Il legno galleggia) - Ottimo isolante termico acustico ed elettrico. - Soggetto a degrado chimico e fisico (brucia) biologico RESISTENZA MECCANICA determinata da: DIFETTI DENSITÀ UMIDITÀ DIREZIONE DI SOLLECITAZIONE Densità e resistenza meccanica sono in relazione (dipende da spessore parete) cellulare) Resistenza a compressione aumenta con aumento densità . L'effetto dell'umidità si manifesta solo al di sotto del punto di saturazione delle fibre La resistenza a trazione è influenzata dall'umidità è minore di quella a compressione PROPRIETA' CHIMICHE E FISICHE: degrado + frequente è quello biologico (insetti, funghi, batteri..) Agenti aggressivi fisici (agenti atmosferici) o chimicie termochimici (fuoco) DEGRADO: agenti biologici provocano decomposizione del legno. Insetti mangiano il legno, la resistenza a questo tipo di attacco dipende da ambiente, tipo legno, e periodo di taglio Il legno si conserva bene in ambiente secco. Criticità è l'umidità che favorisce sviluppo insetti e funghi in grado di decomporlo: variazioni cicliche di umidità danno luogo a variazioni dimensionali e a fessurazioni dove gli insetti penetrano facilmente. Il principale fattore che contribuisce alla resistenza all'attacco biologico è la presenza di estratti ad es. I tannini nel legno di quercia, impediscono sviluppo agenti decomposizione. Spesso per controllare attacco biologico si sceglie la stagione del taglio, si evita il periodo di crescita durante il quale il legno è ricco di linfa nutrimento per i parassiti. Si applicano trattamenti impregnanati con funzione Idrorepellente, fungicida e anche ritardante di fiamma in caso di incendio (soluzioni chimiche applicate a spruzzo, per Immersione o sotto pressione) che aumentano la resistenza a questo tipo di degrado DEGRADO fisico: dovuto ad agenti atmosferici: radiazioni solari, pioggia, vento in genere si tratta di degrado superficiale COMBUSTIONE: attacco termochimico Legno materiale combustibile e facilmente incendiabile Il comportamento del legno sottoposto a combustione conserva per tempi lunghi le sue caratteristiche meccaniche Zona esterna carbonizzata Zona intermedia pirolisi (dove arrivando ossigeno avviene la combustione) Zona interna inalterata ancora in grado di resistere meccanicamente LAVORAZIONI DEL LEGNO Le principali fasi di produzione del legname grezzo sono: - ABBATTIMENTO - SRAMATURA taglio dei rami di una pianta. Questa operazione può essere effettuata prima e dopo l'abbattimento dell'albero - TRONCATURA è una operazione di lavorazione dell'albero dopo l'abbattimento che consiste nel taglio del fusto o dei rami allo scopo di ottenere pezzi di forma circolare o tronchi più piccoli della dimensione voluta a seconda dell'uso. La troncatura viene effettuata a terra dopo l'abbattimento dell'albero tramite l'ausilio di motoseghe. Le dimensioni dei tronchi dopo l'operazione di troncatura sono determinate dalle esigenze di trasporto o da quelle delle successive fasi di lavorazione del legno in segheria. - SCORTECCIATURA processo di lavorazione del legno nell'industria della cellulosa. Viene effettuata sul fusto dell'albero dopo abbattimento e sramatura tramite macchine scortecciatrici o manualmente. Consiste nell'asportazione della corteccia dal tronco che viene caricato su un nastro trasportatore all'interno di rulli ruotanti contrapposti e muniti di punzoni. Consente di standardizzare le dimensioni del tronco dell'albero, agevolare l'essiccazione e il trasporto in segheria. Le dimensioni standard del legno permettono la movimentazione della materia prima tramite processi automatici o semi-automatici che aumentano la velocità della produzione e riducono il costo unitario. Non è comunque una fase di lavorazione obbligata. Alcune segherie sono attrezzate con macchinari appositi per eliminare l'eventuale presenza di residui sul tronco dell'albero, In alcuni casi la corteccia viene lasciata sul tronco per rallentare l'essiccazione e proteggere il legno dall'attacco di parassiti, funghi e muffe. - STAGIONATURA Illegno regolerà continuamente la sua umidità con quella dell'aria circostante; se viene portato in un ambiente chiuso e dotato di riscaldamento centrale, Il suo contenuto di umidità diminuirà lentamente fino a circa il 10%, provocando ovviamente un maggior restringimento, accompagnato da aumento densità e resistenza meccanica. Nb. l'umidità del legno anche dopo la stagionatura non è costante varia in funzione delle condizioni ambientali. Le variazioni dimensionali possono avere luogo anche dopo la posa in opera del legno - VAPORIZZAZIONE dopo lo scortecciamento i tronchi sono investiti da un getto di vapore alla temperatura di 100°C per pulire il materiale dalla presenza di eventuali parassiti. Il getto di vapore consente, Inoltre, di preparare il legno alle successive operazioni di taglio. La vaporizzazione ha anche l'effetto di modificare la colorazione naturale del legno. - processo di vaporizzazione Si utilizzano delle apposite camere di vaporizzazione per creare un ambiente di vapore saturo e per una gestione più efficiente del processo di con acqua corrente o tramite il procedimento di vaporizzazione del legno, Il legno viene accatastato all'interno della camera. Il vapore acqueo viene generato da una fonte esterna e introdotto nella cella per investire il tronco scortecciato. - processi di auto vaporizzazione processo di auto-vaporizzazione a camera stagna che permette di generare vapore sfruttando l'acqua contenuta nel legno stesso, Il legno stesso. Il legno viene accatastato all'interno della camera e non è necessario disporre di un generatore di vapore da una fonte esterna. - LISCIVIAZIONE permette di eliminare dal legno sostanze organiche imputridite e parassiti. Puo essere effettuata tramite il lavaggio del legno vaporizzazione. L'operazione di lisciviazione rende anche il legno più morbido al fine di agevolare le successive operazioni di taglio, tranciatura,piegatura e sfogliatura. In alcuni casi la lisciviazione è utilizzata anche per scurire la tinta naturale del legno. PREPARAZIONE - SEZIONATURA è una operazione del processo di lavorazione dell'albero e consiste nel taglio del tronco in sezioni regolari per agevolare le successive avorazioni. La sezionatura si effettua in segheria. La tipologia della sezionatura dipende dalla forma dall'utilizzo finale del legno. Esistono diversi tipi di sezionature: SEZIONATURA TRADIZIONALE avviene mediante un taglio radiale o un taglio parallelo SEZIONATURA A TAGLIO TRADIZIONALE sezionatura a quartieri. La sezionatura a quartieri consiste nella suddivisione del tronco in due o più zone (quartieri) con successivo taglio delle singole zone in modo parallelo, alternativo o radiale. La sezionatura del legno viene effettuata sul tronco in segheria mediante una macchina detta sezionatrice. Le sezionatrici possono essere verticali o orizzontali in base al tipo di appoggio del tronco. Nella sezionatrice verticale la struttura di appoggio è verticale con un braccio mobile in cui è collocata la sega circolare. Nella sezionatrice orizzontale la struttura di appoggio è un banco di lavoro orizzontale con una sega collocata in un ponte superiore. Prima di arrivare all'industria del mobile il legname è lavorato nelle segherie o nella industria del compensato a seconda della tipologia e della qualità del legname. SEGHERIA Il legname è sottoposto alle operazioni di lisciviazione, taglio, stagionatura ed essiccazione (naturale o artificiale) prima di essere consegnato all'industria del mobile ed utilizzato per la produzione di prodotti in legno (es. mobili in legno). DERIVATI DEL LEGNO - APPLICAZIONI Il taglio viene eseguito prima della stagionatura per ottenere travi, assi, travetti... ELEMENTI DI LEGNO MASSELLO: Limiti nel, comportamento anisotropo, instabilità dimensionale in presenza di variazioni di umidità , presenza difetti e disponibilità limitata per questo SEMILAVORATI pezzi legno incollati si ottengono: DERIVATI DEL LEGNO: - Legno compensato - Truciolato - Pannelli di fibre - Legno lamellare - Sughero I Tipi di pannelli differiscono per densità e struttura e trovano impiego nel settore dell'arredamento e altri ambiti APPLICAZIONI INDUSTRIA DEL COMPENSATO Nell'industria del compensato Il legname, viene sottoposto alle operazioni di tranciatura, sfogliatura, essiccazione, taglio e incollaggio. Al termine del processo produttivo il legname viene trasportato presso le industrie che lo utilizzano come materia semilavorata del processi produttivi. Le principali industrie di sbocco del legname come materia semilavorata sono l'industria del mobile, le segherie e l'industria della carta. Al termine del processo di lavorazione si ottiene Il compensato. Il compensato viene, infine, spedito all'industria del mobile che lo utilizza nel processo di produzione dei mobili. COMPENSATO è un semilavorato Strati sottili di legno (sp. 3 mm. ognuno) ricavati tagliando a spirale il tronco e sovrapposti con diverso orientamento della fibre e incollati. Appartiene alla grande classe del pannelli stratificati o multistrati, dal quall si distingue per l'orientamento Incrociato del vari strati. Il procedimento per ottenere pannelli di legno compensato consiste infattl nello "sfogliare" il tronco d'albero con un apposito tornio in grado di tagliare uno strato molto sottile di legno (1-3 mm), incollando pol I fogli fra loro in modo da "incrociare le venature". Questo Incrocio fa sì che la resistenza del materiale sia uniforme in tutte le direzioni, perché la resistenza del legno lungo le venature non si manifesta ugualmente in tutte le direzioni. L'incrocio delle venature fa sì che le caratteristiche meccaniche del legno, tipicamente unidirezionali, vengano "compensate" in una direzione ortogonale, da cui il nome. COMPENSATO E MULTISTRATO I legni più utilizzati per la produzione di pannelli sono legni dolci: abete, betulla o pioppo, ma si realizzano anche con essenze più pregiate: faggio, teak, okoume etc. Vi sono inoltre compensati in cui i soli strati esterni sono realizzati con fogli più o meno sottili di essenze pregiate come quelle appena citati o anche noce, rovere, palissandro, ecc., mentre gli strati interni, che costituiscono la gran parte del pannello, sono legni dolci. In questi ultimi casi il compensato viene detto compensato impiallacciato. Per incollare i fogli tra loro serve si usa colla fenolica (resistente all'acqua) si ha un compensato adatto all'esterno e al trasporto via mare (es compensato "canadese marino"). I pannelli che hanno più di 3 strati, con spessore superiore a 8 mm, prendono il nome di MULTISTRATO COMPENSATO E MULTISTRATO Spesso i due termini "compensato" e "multistrato" vengono confusi tra loro e ritenuti erroneamente sinonimi: soprattutto a livello commerciale. Il termine "compensato" viene utilizzato (Impropriamente) per indicare pannelli con strati sottili e fino ad un certo spessore, mentre il termine"multistrato" viene impiegato per indicare pannelli di altri spessori e con strati più grossi. Propriamente per pannello in "compensato" si intende un pannello composto da un numero di tre strati, di cui quello centrale di maggiore spessore; un pannello in "multistrato" è composto da 5 o più strati. In entrambi i casi le venature sono orientate ortogonalmente. TRUCIOLATO semilavorato - In origine la categoria del pannelli truciolari era composta esclusivamente da pannelli definiti "pannelli di particelle", cioè composti di segatura ovvero trucioli di granulometria fine. In seguito, si sono aggiunti altri tipi di pannello. Ne esistono diverse varianti classificate per lo più in base alla granulometria del trucioli impiegati. Un elenco provvisorio potrebbe essere il seguente: PANNELLI DI PARTICELLE composti da trucioli di granulometria fine e molto fine, legati con colle. Caratterizzati da una struttura a più strati. In genere, mediante procedimenti industriali, i trucioli più fini sono disposti preferibilmente nella parte esterna del pannello mentre quelli più grossi nella parte interna, senza un orientamento preciso anche in virtù delle loro dimensioni ridotte. Vengono fabbricati tramite pressatura a caldo in processi continui fino ad ottenere un pannello. Il semilavorato serve da base per essere rivestito con laminato plastico o Impiallacciatura per conferire al pannello qualità estetiche e migliori proprietà meccaniche, fisiche o chimiche come: resistenza e Impermeabilità all'acqua (nel caso di pannelli prodotti con incollaggi non fenolici o "marini") e ad alcuni agenti chimici, migliore resistenza al graffio e agli urti, migliore rigidità . PANNELLO DI PARTICELLE OSB (Oriented Strand Board, Pannello di scaglie orientate): costituiti da più strati non ben definiti (come invece avviene nel compensati), di "scaglie di legno", ovvero trucioli lunghi e stretti detti strand, pressati e tenuti assieme da un legante. La struttura del pannello è pensata per renderlo più resistente in una direzione. Per questo, negli strati esterni le scaglie hanno una disposizione prevalentemente parallela ad uno dei due lati del pannello. Particolare attenzione è dedicata al rapporto dimensionale delle scaglie. Questo migliora la resistenza alla flessione in una direzione. All'interno del pannello le scaglie sono spesso orientate perpendicolarmente a quelle degli strati esterni, ma possono anche avere orientamento casuale. PANNELLO DI FIBRE MDF Il Medium-density fibreboard (sigla MDF), traducibile come "pannello di fibra a media densità ", è un derivato del legno. E il più famoso e diffuso della famiglia del pannelli di fibra, comprendente tre categorie distinte in base al processo impiegato e alla densità : bassa (LDF), media (MDF) e alta (HDF) I pannelli di fibra sono costituiti da legno che è stato ridotto nei suoi elementi fibrosi di base, ed è stato ricostruito in un materiale stabile. ed omogeneo. Si producono pannelli di varia densità , in relazione alla pressione applicata durante la fabbricazione, ed al collante usato. MDF, o Medium Density Fiberboard I pannelli artificiali denominati Medium Density Fiberboards sono dotati di superfici lisce su entrambe le facce, fabbricati con un procedimento a secco. Le fibre sono legate tra loro con una resina collante sintetica. Hanno una struttura uniforme ed una trama fine che permette lavorazioni con la macchina sia del bordo sia delle facce. Questo fa sì che i pannelli MDF possono essere lavorati come legno naturale, ed addirittura vi si possono sostituire in certi usi. Sono anche un eccellente substrato per piallacci, e prendono bene la pittura. I pannelli MDF sono disponibili in spessori dai 6 al 32 mm, in una gran varietà di dimensioni. LEGNO LAMELLARE materiale strutturale solido e resistente prodotto incollando delle tavole di legno a loro volta già classificate per uso strutturale. E un materiale composito, costituito essenzialmente di legno naturale, di cui mantiene i pregi (tra i principali l'elevato rapporto tra resistenza meccanica e peso ed un buon comportamento in caso di incendio), ma è anche un prodotto nuovo, realizzato su scala industriale, che attraverso un procedimento tecnologico di Incollaggio a pressione riduce I difetti propri del legno massiccio. Formato da più strati di lamelle - generalmente di larghezza non superiore al 20 cm e sp. di qualche cm. giuntate tra loro (per prevenire eccessive deformazioni causate dal fenomeno del ritiro) e nella loro ricomposizione tramite incollaggio a caldo e sotto pressione, le lamelle sono posizionate tra loro con venatura contrapposta così da garantire una maggior uniformità nella resistenza della trave. È possibile produrre elementi di forma e dimensione volute, senza i limiti derivanti dalla dimensione dell'albero, ottimizzando in questo modo le prestazioni meccaniche della trave. Il LIMITE IN LUNGHEZZA di una trave in legno lamellare è dato principalmente dalla possibilità di trasporto e messa in opera della stessa. LEGNO LAMELLARE Pur essendo realizzate con un materiale combustibile, le strutture in legno lamellare possono avere una resistenza al fuoco pari o superiore a quella di strutture in acciaio o in calcestruzzo armato. Nel legno lamellare la combustione avviene lentamente grazie al buon isolamento termico realizzato dallo strato superficiale carbonizzato. Ad un aumento molto lento della temperatura corrisponde una variazione quasi trascurabile della resistenza meccanica delle fibre di legno della sezione non carbonizzata e la struttura cede o crolla solo quando la parte della sezione non ancora carbonizzata è talmente diminuita da non riuscire più ad assolvere alla sua funzione portante. La resistenza al fuoco di un elemento strutturale in legno lamellare dipende dalla velocità di carbonizzazione che è possibile calcolare sperimentalmente o analiticamente per diverse specie legnose. TRANCIATI Il tranciato di legno consiste in fogli estremamente sottili risultato della tranciatura delle assi di massello. Sono detti anche Impiallacciature, piallacci o rimessi. Nella tecnica della fabbricazione e lavorazione del legno vengono definiti tranciati del fogli di legno estremamente sottili (fino ad un massimo di 30 decimi di millimetro) ottenuti dal taglio orizzontale dei tronchi. Vengono utilizzati per essere applicati a supporti di vario tipo come compensato, lamellare, mdi, listellare, tamburato o masselli in legno meno nobile per produrre componenti per la fabbricazione a oggetti finiti es mobili o arredi che abbiano un aspetto simile al massello, ma con minori costi, maggiore resistenza al tarli, maggiore leggerezza e anche in un certo senso una maggiore stabilità se ben costruiti. Il massello tende nel tempo a muoversi ed imbarcarsi di più. Una differenza particolarmente utile nella fabbricazione delle porte. IMPIALLACCIATURA L'impiallacciatura è un'operazione che viene eseguita in falegnameria e consiste nel ricoprire un legname non pregiato od un pannello con un sottilissimo tranciato di legno detto piallaccio. Il termine "Impiallacciatura" viene comunemente utilizzato, in modo improprio, per Indicare qualsiasi rivestimento di un legno non pregiato, includendo anche quelli effettuati, ad esempio, con resine melamminiche (pannelli nobilitati) o tranciato di legno. Il nobilitato è un pannello di legno truciolare rivestito su di un lato, o su tutti e due i lati, con carta melamminica, che è un materiale sintetico costituito da fogli di carta sottilissima (attorno al decimo di mm) impregnata di resina melamminica. L'uso di tale carta fa sì che il pannello nobilitato venga spesso anche chiamato pannello melamminico (o melaminico). Il pannello può essere costituito oltre che di truciolare (anche da legni riciclati), anche da faesite, da compensato, da legno stampato, OSB o da MDF. E considerato un prodotto piuttosto economico; tuttavia lo sviluppo di carte sempre pia realistiche, unito a doti notevoli di durezza e resistenza al graffio e al solventi della superficie, rende questo prodotto usatissimo nel mondo dell'arredamento. Il LAMINATO Invece è un materiale molto simile al melaminico ma la sua composizione è diversa. E principalmente un materiale composto da tre strati: un pannello di fibra ad alta densità (3), una carta stampata che ne costituisce il decoro (2), e uno strato finale impregnato di resine melaminiche (1). SUGHERO E 100% naturale, si produce dalle piante e i suoi usi sono molteplici: Un materiale naturale di origine vegetale che si ricava dalla quercia da sughero o sughera, una pianta diffusa nel Mediterraneo occidentale. Questo tessuto vegetale (un insieme di cellule con funzioni specifiche) è formato da cellule vegetali e aria e cresce tutt'intorno al tronco dell'albero per proteggerlo; lo si può estrarre senza danneggiare la pianta e il suo utilizzo ricopre numerosi campi applicativi. E' impermeabile a gas e liquidi, ottimo Isolante calore, elettricità e suono. Elastico può essere compresso e deformato facilmente riprendendo, dopo sollecitazioni, dimensioni originali PRINCIPALI CLASSI DI MATERIALI - CERAMICI CERAMICI: materiali costituiti da composti inorganici caratterizzati da struttura fragile. Sono solidi inorganici: in genere OSSIDI DI METALLO altri sono combinati con carbonio, azoto, zolfo La loro struttura è spesso CRISTALLINA anche se alcuni presentano la struttura in parte cristallina e in parte amorfa CARATTERISTICHE GENERALI - CARATTERE REFRATTARIO (elevato punto di fusione quindi elevate temperature di esercizio) - BUONA RESISTENZA CHIMICA A SOLVENTI E ACQUA - BASSISSIMA CONDUCIBILITÀ TERMICA ottimi isolanti - ALTA RESISTIVITÀ ELETTRICA - BASSO COSTO DI MATERIE PRIME E FABBRICAZIONE (solo per i ceramici tradizionali) - POSSIBILITA' DI MANIPOLARE L'ASPETTO ATTRAVERSO TRATTAMENTI SUPERFICIALI - ELEVATA DUREZZA - FRAGILITA' - DENSITA' MEDIO BASSA - BUONA RESISTENZA A COMPRESSIONE - SCARSA RESISTENZA A TRAZIONE NB: il diamante presenta invece CONDUCIBILITA' TERMICA SUPERIORE al rame CERAMICI TRADIZIONALI costituiti da 3 componenti ARGILLA, SILICE, FELDSPATO Come si ottengono: le polveri di partenza sono materie prime che si trovano in natura queste vengono sottoposte ad un processo di cottura vetrificate GRANDI VOLUMI DI PRODUZIONE PRODUZIONE A BASSO COSTO IMPIEGHI mattoni, tegole, porcellana, vasellame, piastrelle, refrattari per Isolare termicamente, abrasivi. cementir CERAMICI AVANZATI costituiti costituiti da elementi metallici combinati con CARBONIO AZOTO ZOLFO Come si ottengono: le polveri di partenza sono quasi sempre ottenute per sintesi attraverso processi sonsticati processi produttivi. Le polveri vengono sinterizzate. Il difetto di questi ceramici è la fragilità che alpende dalla natura del loro legami chimici BASSI VOLUMI DI PRODUZIONE PRODUZIONE ALTO COSTO IMPIEGHI applicazioni elettroniche o magnetiche, applicazioni ottiche nucleari e biologiche ARGILLA combinata con acqua Caratteristica importante la sua plasticità cioè la capacità di deformarsi sotto l'azione di una pressione esterna e di conservare la forma. La plasticità aumenta con la aggiunta di acqua e viene gradualmente persa durante l'essiccamento (se eccessivo porta a deformazioni) SILICE e FELDSPATI (minerali) sono gli altri costituenti dei ceramici tradizionali. La SILICE è uno del maggiori ingredienti del refrattari e delle ceramiche bianche. Viene aggiunta sotto forma di sabbia di quarzo. E' una sorta di riempitivo inerte e utilizzato per impartire al verde (cioè il manufatto non ancora cotto) maggiore RESISTENZA necessaria per sagomare l'oggetto e mantenere la forma durante la cottura. FELDSPATI riducono la temperatura di fusione degli alluminosilicati LAVORAZIONI - preparazione dell'impasto - formatura dipende dalle esigenze produttive le principali sono PRESSATURA - COLATA A IMPASTO UMIDO - ESTRUSIONE PRESSATURA applicazione di una pressione per eliminare i vuoti (le porosità ) e ottenere una specifica forma. Il materiale presenta basso contenuto di acqua. COLATA A IMPASTO UMIDO una barbottina molto fluida (la barbottina è una sospensione molto fluida composta da acqua e argilla) viene versata in uno stampo di gesso poroso. Il materiale a contatto con il gesso diminuisce il suo contenuto d'acqua per effetto della forza capillare che risucchia l'acqua producendo uno strato di argilla solida il cui spessore aumenta nel tempo. L'impasto fluido in eccesso si elimina e si procede all'apertura dello stampo. Si possono realizzare anche forme complesse es, sanitari ESTRUSIONE permette una produzione continua ed efficiente. Una vite forza In modo continuo il materiale attraverso la matrice. Si producono tubi, barre piene e cave inoltre queste forme possono essere tagliate subito dopo l'uscita dall'estrusore. ESSICCAMENTO E COTTURA il pezzo crudo viene essiccato lentamente per eliminare l'acqua in eccesso segue un processo di riscaldamento graduale per rimuovere l'acqua strutturale e per decomporre e bruciare i leganti organici utilizzati nella formatura. FORNI DI COTTURA CONTINUI costituiti da un nastro trasportatore in cui vengono appoggiati i pezzi che attraversano il forno. I pezzi vengono scaldati in maniera graduale con un flusso di aria riscaldata. La temperatura massima viene raggiunta da metà forno, in corrispondenza dei bruciatori, nella seconda parte del forno i pezzi ceramici vengono riportati gradualmente a temperatura ambiente. La cottura favorisce la coesione tra le particelle (resistenza) e la riduzione FINITURA il prodotto ceramico cotto risulta poroso può essere impermeabilizzato o avere una migliore finitura superficiale e può essere smaltato SMALTATURA avviene a spruzzo o per immersione NB, per prodotti smaltati è necessario un doppia cottura (bicottura) CERAMICI TRADIZIONALI PRODOTTI - ceramiche bianche - prodotti strutturali (mattoni, piastrelle) - refrattari - abrasivi - cemento CERAMICHE BIANCHE Il tipo di argilla impiegato è il CAOLINO che conferisce al materiale un aspetto bianco, traslucido e vitreo. Proprietà : - impervietà ai fluidi | - bassa conducibilità elettrica - inerzia chimica - possibilità di essere prodotta in forme complesse Impieghi: stoviglie di porcellana bianca, impianti dentali, sanitari, lavandini, isolanti per le candele di accensione nei motori delle auto I prodotti a base di ceramiche bianche si suddividono in tre classi a seconda del grado di vetrificazione: - vetrosi - semi vetrato - porosi PORCELLANE sono ceramiche bianche completamente vetrose per questo motivo possono non essere smaltate. Hanno elevata RESISTENZA e TENACITÀ (resistenza a impatto) e basso assorbimento di acqua. PRODOTTI STRUTTURALI A BASE DI ARGILLA Prodotti da materie prime naturali a base di argilla quarzo e feldspato vengono mescolate con acqua, formati nella forma desiderata e infine cotti in forno Lavorazioni: ESTRUSIONE o PRESSATURA Proprietà : - resistenza ai carichi - resistenza agli agenti chimici Impieghi: utilizzati in edilizia: mattoni, pavimentazioni, tegole, tubi di scarico REFRATTARI materiali che hanno un punto di fusione molto alto e che mantengono le proprietà strutturali a temperature molto elevate. Proprietà : - inerzia chimica - resistenza alla temperatura - resistenza a corrosione - resistenza a usura, abrasione e shock termici Impieghi: vengono utilizzati nelle industrie metallurgiche e della fabbricazione del vetro in qunato utilizzano apparecchiature che lavorano a temperatura elevate. PRODOTTI STRUTTURALI A BASE DI ARGILLA ABRASIVI materiali costituiti da particelle con spigoli appuntiti Proprietà : - durezza Impieghi: utilizzati per raschiare e spianare superfici di materiali più teneri. Le polveri abrasive vengono compatatte per formare utensili (mole e nastri), in sospensione come lubrificanti per impregnare panni o spazzole o anche essere usati per la sabbiatura la lattatura. abrasivi naturali includono il diamante, il corindone e smeriglio e si trovano nei depositi naturali abrasivi sintetici sono prodotti di lavorazioni sofisticate a partire da materie prime includono il carburo del silicio, il diamante sintetico e allumina CERAMICI AVANZATI rappresentano uno sviluppo tecnico di proprietà , sono progettati per offrire variazioni rispetto alle proprietà tradizionalmente attribute alla loro classe. Proprietà : - materiale Inorganico - conducono elettricità - buona resistenza a usura - resistenza chimica - resistenza meccanica (vibrazioni e urti) PRODUZIONE sono ottenuti per miscelazione e successiva calcinazione delle polveri. Raramente vengono utilizzate polveri naturali come materia prima ma si utilizzano elementi sintetici ed elevata purezza. La cottura avviene mediante sinterizzazione allo stato solido. CERAMICI AVANZATI STRUTTURALI sono materiali con particolari proprietà meccaniche oltre che adatti all'utilizzo in ambienti corrosivi APPLICAZIONI DEI CERAMICI STRUTTURALI Ceramici avanzati vengono utilizzati dove richiesta resistenza agli agenti corrosivi, proprietà di Isolamento, durezza e resistenza Impieghi: ambito automobilistico, veicoli aerospaziali, generatori di potenza, valvole del rubinetteria altre applicazioni sono le scarpe sportive chiodate o le sfere della penna a sfera ELETTROCERAMICI possiedono proprietà elettriche sono utilizzati per produrre I circuiti integrati e condensatori, guarnizioni frigoriferi, microfoni, guarnizioni altoparlanti CERAMICI OTTICI ceramici ottici alcuni ceramici avanzati presentano proprietà ottiche, uniscono una forte trasparenza a un notevole resistenza all'attrito e ad elevate temperature Impieghi: finestre dei lettori dei codice a barre, lo zaffiro o i contenitori per le lampade ai vapori di sodio. L'applicazione del ceramici può avvenire anche nell'industria del colore sotto forma di pigmenti. I pigmenti in polvere vengono incorporati nel pezzi ceramici per determinare il colore durante la cottura. MATERIALI POLIMERICI I materiali polimerici sono sostanze organiche costituite da molecole di elevato peso molecolare, dette macromolecole. Ogni singola molecola è formata da numerosi monomeri (molecola semplice dotata di gruppi funzionali tali da renderla in grado di combinarsi ricorsivamente con altre molecole) legati tra loro da legami di tipo covalente (legame chimico in cui due atomi mettono in comune delle coppie di elettroni). Fra le varie macromolecole sì instaurano legami intermolecolari. E' la compresenza di legami intermolecolari deboli e forti che determina le proprietà dei materiali polimerici. La maggior parte dei materiali polimerici contiene: C carbonio come elemento costitutivo principale! altri elementi importanti H idrogeno, azoto N, ossigeno O, fluoro F. I siliconi contengono come elemento costituente il Silicio SI. Quasi tutte le materie plastiche commerciali contengono svariati ADDITIVI aggiunti per modificarne le proprietà (plastificanti, stabilizzanti, antiossidanti, pigmenti, etc...) Per questo motivo il termine materiale polimerico non è necessariamente sinonimo di polimero anche se spesso i 2 termini vengono usati indifferentemente. I polimeri costituiscono cma la base delle materie plastiche e gomme, possono essere ottenute mediante isolamento chimico di sostanze polimeriche naturali o + frequentemente con processo interamente sintetico. MATERIALI PLASTICI La maggior parte dei materiali plastici è di origine sintetica - sono materiali che si ottengono per mezzo di procedimenti chimici sempre però partendo da prodotti naturali. I polimeri sono normalmente ottenuti per sintesi chimica a partire dal petrolio. Di tutto il petrolio consumato nel mondo solo circa il 4% viene utilizzato per produrre polimeri sintetici Tramite REAZIONI CHIMICHE le molecole semplici degli elementi di base (CARBONIO, OSSIGENO, AZOTO, IDROGENO, ZOLFO etc...) si combinano in complessi MACROMOLECOLARI disposti in 'catene' più o meno lunghe. Le MACROMOLECOLE possono essere ottenute con 2 procedimenti BASICI: - CONDENSAZIONE: molecole semplici, anche di specie diversa, si combinano tra loro liberando acqua, alcool, ammoniaca o altri prodotti. Una ulteriore reazione detta POLICONDENSAZIONE interessa gruppi molecolari formatisi nella prima fase - POLIMERIZZAZIONE: più molecole semplici anche di specie diverse, si combinano tra loro in presenza di un agente catalizzatore (calore, sostanza chimica, luce ultravioletta...). I prodotti si chiamano POLIMERI. MATERIE PLASTICHE possono essere suddivise in: - TERMOPLASTICHE - TERMOINDURENTI - ELASTOMERI (o GOMME) - TERMOPLASTICHE Possono essere riscaldate e formate innumerevoli volte, purchè la temperatura di riscaldamento sia inferiore a quella di decomposizione del materiale - TERMOINDURENTI Una volta raffreddate e indurite non possono essere più riscaldate e formate L'azione del calore provocherebbe reazioni chimiche tali da causare l'indurimento permanente del materiale - ELASTOMERI (o GOMME) Possono essere di origine naturale (es. caucciù) o sintetica Sono caratterizzate da grande elasticità che li rende adatti ad assorbire, deformandosi, le sollecitazioni meccaniche PROPRIETA' MATERIE PLASTICHE - Leggerezza. I polimeri hanno una densità pari a circa 1g/cm3 significativamente inferiore a quella ad es di vetro o acciaio. La minore densità si traduce in riduzione di peso - Ottime capacità di ISOLAMENTO termico ed elettrico - Ottima resistenza agli urti e deformabilità - Facilità di lavorazione STATO AMORFO e STATO CRISTALLINO La conformazione delle macromolecole di un polimero può essere - tipo amorfo cioè disposizione priva di ordine e regolarità nello spazio - tipo cristallino cioè reticolo regolare LAVORAZIONE DELLE MATERIE PLASTICHE Tutti i materiali polimerici presentano particolari proprietà di scorrimento ad un certo stadio del loro processo di trasformazione, ossia sono molto deformabili (+ dei materiali metallici) e facilmente lavorabili. I processi in uso per trasformare i granuli di polimero in prodotti finiti come fogli, barre, oggetti estrusi, tubi o parti stampate. CICLO DI VITA DI UN MATERIALE POLIMERICO Prima fase - ottenimento dei Monomeri - sostanze a basso peso molecolare che si trovano normalmente allo stato gassoso o liquido, a partire dal petrolio greggio Seconda fase - sintesi del polimero (polimerizzazione), avviene in impianti chimici Il polimero non sempre è utilizzabile allo stato puro, vengono stabilizzati (compounding) rispetto a sollecitazioni ambientali temperatura ,raggi ultravioletti etc...) ciò avviene con miscelazione di sostanza additivi che modificano proprietà Il polimero modificato prende il nome di MATERIALE POLIMERICO sotto forma di granuli o polvere Terza fase - trasformazione. Quarta fase - dismissione S VANTAGGI Attaccabilità da parte dei solventi (soprattutto le termoplastiche) e dagli acidi (soprattutto le termoindurenti) Scarsa resistenza a temperature elevate Meno rigidità e quindi deformabilità del manufatto Sensibilità ai raggi UV - esposizione prolungata può provocare reazioni chimiche che alterano aspetto estetico es ingÃallimento e proprietà meccaniche - Nb. Le proprietà meccaniche, elettriche, chimiche e termiche delle materie plastiche possono essere valutate con numerose prove unificate - Materie plastiche sono impiegate in tutti i settori industriali: industria chimica, meccanica, elettrica (componentistica, materiali isolanti), automobilistica (pneumatici, allestimenti interni, carrozzeria), industria imballaggio, edilizia, settore tessile (dalle materie plastiche si ricavano le fibre sintetiche) RESINE TERMOPLASTICHE ABS Acrilonitrile - butadiene - stirene caratteristiche: rigidità , robustezza, resistenza agli urti, bassa carica elettrostatica Es. componenti di carrozzeria, caschi, giocattoli, mobili RESINE TERMOPLASTICHE - CA Acetato di cellulosa caratteristiche: resistenza agli urti, a oli minerali e benzine, trasparenza, resistenza all'usura, facilità di colorazione Es. pellicole cinematografiche, oggetti decorativi, componenti meccanici di carrozzeria, fibre tessili RESINE TERMOPLASTICHE POLICARBONATO (PC) caratteristiche: buona trasparenza, buona resistenza alla fiamma, tende a ingiallire se posto a raggi Uva e possiede modesta resistenza alla fiamma. Es. CD-rom, componenti elettrici elettronici, lastre etc.. RESINE TERMOPLASTICHE - PA Poliammide caratteristiche: ottime capacità meccaniche, chimiche, termiche, variabili a seconda della varietà del prodotto, Es. tessili es nylon, tubazioni (nylon), componenti meccanici, funi, guarnizioni, scatole RESINE TERMOPLASTICHE Polimetacrilato di metile (PMMA) caratteristiche: trasparenza, infrangibilità , durezza, resistenza ad abrasione, lavorabilità , identificato anche con varie denominazioni commerciali (PLEXIGLASS, PERSPEX, etc...). Impiegabile in ambiente esterno (es. lampioni, lucernari, fanali, insegne luminose...). Es. lenti, vetri di sicurezza, contenitori trasparenti, apparecchi ottici RESINE TERMOPLASTICHE - Polietilene (PE) caratteristiche: resistenza ad agenti chimici, impermeabilità , resistenza ad urti, alta resistività elettrica Es. guaine isolanti per cavi elettrici, film trasparenti, imballaggi per alimenti, rivestimenti RESINE TERMOPLASTICHE - Polipropilene (PP) caratteristiche: ottime proprietà meccaniche, resistenza al calore all'abrasione, elasticità , sensibilità ad agenti chimici, lavorabilità , colorabilità è noto anche come MOPLEN Es. recipienti, elettrodomestici, fibre tessili, tubazioni per edilizia e impiantistica, componenti meccaniche, oggetti uso domestico, rivestimenti RESINE TERMOPLASTICHE Polistirene (PS) o polistirolo caratteristiche: resistenza agli urti, leggerezza, sensibilità ai solventi, infiammabilità Es. imballaggi, contenitori, protezioni antiurto, pannelli isolanti, elettrodomestici, oggetti arredo Il polistirene è usato come materia plastica di uso generale. Per il basso costo, è indicato per oggetti grandi di valore relativamente basso, come involucri esterni di apparecchiature, mobili, piatti e stoviglie usa-e-getta. Discrete proprietà meccaniche, le superfici sono lisce e lucide. I principali difetti sono la fragilità , dovuta allo stato vetroso, e la tendenza a scurire nel tempo per degradazione chimica. Massimo impiego per questione costi è il settore dell'imballaggio. Una variante molto interessante è il polistirene espanso, un materiale leggerissimo ottenuto facendo sviluppare bolle di gas prima che il polistirene liquido solidifica. Il materiale è costituito in massima parte da cavità vuote e chiuse, separate da sottili pareti di polistirolo. Il polistirene espanso è prodotto in gran quantità come trucioli per il riempimento di imballaggi, che assicurano il riempimento in volume e la resistenza agli urti, con un peso trascurabile. Come materiale continuo, può formare pannelli, scatole, pezzi sagomati di qualsiasi forma, adattata al contenuto da imballare. Questi oggetti di polistirene espanso sono ottimi isolanti: isolano dagli urti e dall'elettricità ; dall'umidità , dal rumore e dal calore. Sono quindi ottimi, ad esempio, come intercapedini per pareti, per il rivestimento di frigoriferi e per scatole per trasportare i gelati. RESINE TERMOPLASTICHE Polivinilcloruro (PVC) caratteristiche: isolamento elettrico, resistenza al calore e corrosione. Ignifugo, buona resistenza alla fiamma. Buona resistenza chimica ma bassa termica (difficoltà di lavorazione) e bassa resistenza a raggi UV per questo si aggiungono additivi. E' tenace. Es. tubazioni, serbatoi, recipienti per acidi, rivestimenti per mobili e auto, fibre tessili e isolanti Rappresenta il 70% del mercato - costo basso RESINE TERMOINDURENTI I polimeri termoindurenti appartengono a quella categoria di materie plastiche che possono essere lavorati e modellati una sola volta, se sottoposti nuovamente a riscaldamento si decompongono carbonizzando RESINE FENOLICHE Si ottengono per reazione tra fenolo e formaldeide. Un es è la bachelite, prima materia plastica sintetica comparsa al mondo. Queste resine hanno caratteristiche liquide e vischiose e vengono usate come vernici, mastici, e altri prodotti che induriscono essiccando RESINE POLIURETANICHE Poliuretani espansi flessibili sono schiume usate per i materassi e imbottiture. Lavorabili per stampaggio o iniezione Poliuretani espansi rigidi sono schiume rigide e leggere usate per produzione di lastre di materiale termoisolante (iniettate in frigoriferi, pannelli isolanti in edilizia etc) Poliuretani rigidi compatti utilizzati per pezzi rigidi di diverse consistenze Poliuretani elastici compatti sono i più diffusi, sono i comuni elastomeri utilizzati per produrre elastici, guarnizioni, tubi flessibili RESINE MELAMMINICHE - Sono resine termoindurenti prodotte dalla condensazione di formaldeide e melammina. Inodore, incolore, resistente a acqua e agenti chimici, all'abrasione e al calore utilizzata per la-produzione di arredi, formica, colle e vernici RESINE EPOSSIDICHE Sono resine termoindurenti che possiedono eccellente adesività , resistenza al calore, e agenti chimici. Ottime proprietà meccaniche e isolanti elettrici. Usate per vernici, rivestimenti ELASTOMERI o GOMME Sostanze naturali o sintetiche che hanno la proprietà chimica e fisica della gomma (caucciù) cioè di subire grandi deformazioni elastiche (possono essere allungate per poi ritornare a loro conformazione iniziale). Si lavorano per estrusione o stampaggio GOMME NATURALI - derivano dalla coagulazione del lattice di alcune piante tropicali GOMME SINTETICHE - i ottengono dalla polimerizzazione di idrocarburi semplici Fanno parte dei polimeri e si suddividono in 2 classi principali: ELASTOMERI TERMOPLASTICI possono essere rimodellati ELASTOMERI TERMOINDURENTI non possono essere rimodellati