Material Exam 3 PDF
Document Details
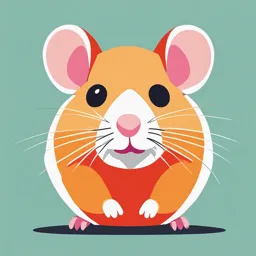
Uploaded by NoteworthyCoralReef
Tags
Summary
This document contains short questions and answers related to construction materials, focusing on topics such as different types of piles, formwork, pumps, and concrete properties. The material covers aspects of construction project management, including construction methods and considerations for a top-down approach.
Full Transcript
## Short Questions **Two kinds of different pile:** - Displacement Pile: Steel H Pile - Replacement Pile: Barrettes **What are the advantages using Tremie pipes technique?** Answer: to prevent concrete contamination **Suppose we have three formworks here, including column, slab and beams. Which f...
## Short Questions **Two kinds of different pile:** - Displacement Pile: Steel H Pile - Replacement Pile: Barrettes **What are the advantages using Tremie pipes technique?** Answer: to prevent concrete contamination **Suppose we have three formworks here, including column, slab and beams. Which formwork could be removed first/earlier?** Answer: Wall and Columns (because it can stand on his own) The strength of beams and slab are too low (horizontal formwork) **Time: Remove the formwork of beam and slab needs around 2 weeks. Time: Remove the formwork of wall needs around 24 hours** **What kind of pump can be used in dewatering?** - Submerged Pump - Suction Pump **What is the self-compacting concrete?** (Highly workable and even pumpable?) **What materials is added into the concrete so that it could become self-compacting?** Answer: superplasticizer (pumpable and flowable?) **Suppose you got a super tall building; what kind of formwork apply in there for the slab construction, that could speed up the construction?** Answer: Fly Form/Table Form **What are the main steels for the Continuous Beam?** Answer: Top Steel (cantilever) and Bottom Steel (Span): RC beam RC Column: Top Steel (Over Column) Also, over several span **What are the main steels for the Simply Supported Beam?** Answer: one span only, main steel will be bottom steel **As there will be joint problem (water leakage problem) surrounding with precast, which joint is better for improving the water tightness by joining the precast together?** - Dry Joint: by sealant and gasket - Wet Joint: Monolithic Joint Answer: Wet Joint. (1. Place in-situ concrete topping 2. Give you Monolithic Joint) so better to prevent water leakage. In-situ concrete will cover all the gaps, should not rely on the gasket or the sealing, coz is totally unreliable. **Which construction equipment is more silence?** Answer: Hydraulic Vibrator Machine **Suppose this room catches fire, and we check damage of structure. What is the critical temperature of structure will lose half strength?** Answer: 600°C (whether the steel and concrete structure) **Suppose in construction site, I want to move the wall tile of sinks from ground elevation to fifth floor. What construction machines or plant we should use to pick up this wall tiles?** Answer: Material Hoist (pick up the materials only, not for human) **We got two kinds of materials, epoxy and silicone. Which one is suitable for water tightness jointing.** Answer: Silicone (for water tightness joint) Epoxy (for concrete spalling) (structural repair) **What materials should be used in the cover spaces?** Answer: Plastic - wall formwork - Cover - Spacer - RC steel bar **There are three types of system in curtain wall, which one is the most famous one?** - Stick System - Unitised System - Semi-Unitised System Answer: Unitised System, as it is more effective and economical **Which one is the most popular displacement pile in HK?** Answer: Steel H Pile **What is the machine for bored pile installation?** - Temporary steel casing - Hydraulic oscillator - Chisel - RCD with roller bit - Underway mark - Install the steel reinforcement cage - Tremie pipe and hoper **What are Common Pile Tests?** - Dynamic load test - Static load test - Sonic load test - Sonic logging test - Standard Penetration test - Core Drilling - Vibration test - Lateral Load test - Tension test **What are the advantages of the top-down method?** - Excavation takes up a lot of time - The top-down construction method can reduce the construction time for the project. - basement and the superstructure can be constructed at the same time. - more advantage weathertight working condition (not affected by inclement weather) **Deep Basement:** - For the depth more than 20 meters (more than 4 levels) we should use diaphragm wall + top-down method - For the depth less than 10 to 20 meters (less than 3 levels) we should use Steel Sheet Piling and Cofferdams (Bottom Up method) Depending on depth and levels of the basement **What is the potential Risk for building basement?** - Soil Collapse - Worker's Safety - Disruption of underground utilities (settlement and services) - Neighboring buildings foundations settlement / structures / MTR - Ground Water / Flooding **What are the advantages of precast concrete:** - **Demand on Skilled Labour** - Semi-skilled labour required on site for installation of precast elements - Lower labour cost (wage gap: HK Vs. China) - Aging skilled labour force in HK - **Reliable Quality Control** - QC in factory - accurate, reliable - Substandard quality to discard the products before installation - RFID tag embedded in building products (e.g. precast units) - **Consistent s Higher Quality** - Indoor working environment (shielded from heat and rain) - Use of robot / machinery (consistent workmAnswerhip) e.g. troweling - Vertical elements cast horizontally (e.g. façade) to better compaction - Vibration table (e.g. slab) – compaction - Curing chamber - controlled environment: temperature, humidity, pressure - Window frame cast BEFORE concreting to lower risk of water leakage - Waterproofing layer applied to floor slab in precast toilet to lower risk of water leakage - External finishes (e.g. tiles) fixed on the ground level (rather than working at height on a scaffold!) - **Reduce No. of Separate Operations** - Some elements (e.g. façade, toilet) involve a lot of trades/sub- contractors - Different companies to conflicts - E.g. Trades involved in toilet: plastering, painting, waterproofing, stonework, joiners, suspended ceiling, plumbing/drainage, electricity, gas - Precast factory: under same management; well-planned - **Better Continuity of Operation** - Production line to smooth operation, not affected by weather, not affected by delay of a particular trade - Must guarantee steady supply of precast components/elements (logistic) - **Faster Construction** - No need to erect and strike formwork on site - No need to wait for the concrete to develop strength - Progress not affected by weather - Avoid labour shortage affecting progress - **Environmentally Friendly** - Factory production Vs. Site production: reduce wastage on materials - Good quality to minimum defective works to lower demand on future repair and maintenance works - Noise and air pollution- away from domestic area - Replace timber formwork - Recycling (e.g. reinforcement, formwork) - Accurate ordering of material – avoid over ordering causing wastage - Smooth concrete surface to reduce / eliminate finishes (direct painting or tiling without plastering) - Hollow units to save materials - Hollow units to reduce dead load to saving in structural components - e.g. foundation, columns - **Prestressed Concrete** - Fully utilize the strength of materials (concrete and steel rebar) - Pre-tensioning to be carried out in the factory (more difficult in site) - Thinner slab, no/shallow beam design to save materials and save foundation cost, reduce building height (thus less wind load) - E.g. Cambridge House in Quarry Bay used U-shape pre-tension beam - **Safer** - Minimize work at height - tidier site - housekeeping - More machine/robot to substitute workers - Minimize weather exposure (heat, rain) - **Higher Productivity** - Use of machinery, e.g. vibration table for compaction - Reduce demand on tower crane (lifting reinforcement, concrete, formwork) **Question: Once the site had adopted prefabrication, if you a site agent, what are the important considerations for prefabrication on site plan?** - Make sure the tower crane can pick up the material - tower crane capacity in relation to working radius. - The area in storing the prefabricated material – consider the construction speed, how many item you can pick up in a day. So, need to choose suitable working area to store the prefabricated materials in relation to how fast you consume to pick up all the materials and arrivals of the materials. - The internal access - whether the internal road to allow the car to turn around on site. **Methods of constructions:** **Installation Procedure of Machine Dug Piles:** - The location of the pile is set out to predrilling A. Predrilling is necessary for piles founded on rock B. the process is like soil investigation C. purpose is to identify the founding rock level before actual pile construction work commences - Position the boring rig (with the rotary auger) to bore the initial hole for the insertion of the temporary steel casing - The casing is pushed into the ground using a vibratory hammer or oscillator. The casing serves to align the drilling process and prevent the collapse of the soil (underground) during drilling - The boring is proceeded with the rotary auger (or other types of drilling bits). The rotary auger will cut through the soil and will be raised to the surface to depose the excavated soil to the side of the borehole. - The temporary steel casing can be extended by connecting to another casing. The connection is usually a mechanical lock on the ends of both casings. The boring will continue until the desired depth of the pile is reached. - If the pile founding level is in a rock stratum, a reversed circulation drill, RCD, may be used to bore into the rock to form the rock socket - A bellout at the base is usually formed. The minimum depth of penetration of the bellout is usually 300 mm - the borehole (base) will be cleaned using "air lifting" method - The steel reinforcement cage will then be lowered to the borehole. To maintain an adequate concrete cover, spacers must be provided to the reinforcement. Also, to reduce the bearing pressure on the bedrock, a bellout may be formed at the base of the pile to increase the bearing area. - concrete is poured using tremie pipes (prevent segregation). The tremie pipe will be lowered to the bottom of the borehole and concrete will then flow through the pipe. The tip of tremie pipe should be placed at a depth of between 2 m to 3 m below the concrete surface (to prevent concrete contamination). - Extract the temporary steel casing and tremie pipe during concreting. - After concrete acquires adequate strength, excavate to the cut-off level of the pile and remove the excess contaminated concrete to expose the reinforcement. Pile cap may then be formed by embedding the exposed reinforcement **Construction Procedures of Diaphragm Wall:** - construct a pair of guide walls - these walls act as guide for the clamshell/grab (excavation machinery) to excavate the trench. - Hydrofraise/hydromill cutters will be used to cut through rocks or other obstructions. - Bentonite slurry mixing plant and storage silos are set up for circulation. - Excavation is carried out within the bentonite slurry. The bentonite serves to support the excavation by exerting hydrostatic pressure onto the trench wall to prevent the collapse of soil and ground water infiltration. - The excavation of the trench is usually done in alternate panels between the guide walls - panel width of 4 – 6 m is quite usual for stable soil. - the bentonite used in the excavation is treated (desanded) and will be recirculated continuously during excavation by pumping from the trench to an elevated tank from which it returns to the trench. - After excavation to a panel is completed, vertical tubes (stop-end) are placed at each end to form a semicircular recess at the end of panel. [waterstops may be used at the stop-end recess to improve the watertightness of the wall]. - This recess will provide a joint to the adjacent panel (to be cast later). - Reinforcement cage will then be lowered into the trench (with bentonite). - Since the diaphragm wall will also act as the permanent basement wall, therefore, box-outs will be attached to the reinforcement cage to form the junctions of floors and walls. - The panel will then be concreted using tremie pipes (tip of tremie pipe should be immersed about 1 metre below concrete level to prevent concrete contamination) - The denser concrete will displace the bentonite which will then be pumped to the de-sanding plant (remove soil particles) before it is reused - Once the concrete is hardened, the stop-end will be removed and to be ready to bond to adjacent panels - the next panel will be excavated, and the procedure is continued until the continuous diaphragm wall (e.g. a box shaped wall enclosed the whole basement) is constructed. **Construction procedures for top-down method:** - Construct diaphragm walls - Bored holes are formed with bored piles at the bottom - Steel stanchions are punched through the concrete at bored piles' head (before set) - bored holes are then backfilled with soil. - upper portion of stanchions is exposed to allow the construction of the superstructure. - Ground floor slab is cast - Excavation for the first level of basement will then proceed along with the construction of the superstructure. - When the first level of basement is reached, beam and slab will be constructed (connected to the starter bars and the steel couplers in the exposed diaphragm wall and the steel stanchions, respectively). - The beam and slab system will act as the lateral support to the diaphragm wall. - Temporary openings made in slabs to allow further excavation downward. These openings provide access for the excavating machinery and allow the removal of soil. - ramps may be built to allow dump trucks to access the basement for soil removal - Repeat excavation until the formation level of the basement slab is reached. Construct foundation slab and ground beams