IE 324 Sales & Operations Planning Lecture Notes PDF
Document Details
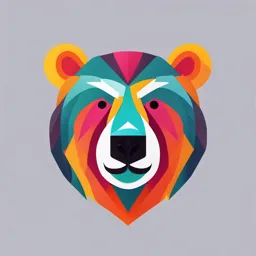
Uploaded by IntegratedBugle263
Tags
Summary
These are lecture notes for IE 324, week 5, focusing on Sales & Operations Planning (S&OP). Topics covered include an introduction to sales and operations planning, the S&OP process, the role of S&OP in a supply chain, and aggregate planning approaches.
Full Transcript
IE 324 Lecture Notes – Week 5 Sales & Operations Planning (S&OP) 1 Outline Introduction to Sales & Operations Planning The S&OP Process The Role of S&OP in a Supply Chain Aggregate Planning in S&OP Aggregate Planning Approaches...
IE 324 Lecture Notes – Week 5 Sales & Operations Planning (S&OP) 1 Outline Introduction to Sales & Operations Planning The S&OP Process The Role of S&OP in a Supply Chain Aggregate Planning in S&OP Aggregate Planning Approaches 2 Sales & Operations Planning (S&OP) We make both micro and macro decisions through life: for example, “what to eat for lunch” is a micro decision; “where to live”, “what to study” are macro decisions (i.e., Macro decisions are the kind that change the course of one’s life) A company must also make both micro and macro decisions everyday. Some macro decisions are strategic as technology selection, market entry; Some macro decisions are more tactical as planning company-wide workforce and production levels, setting sales target. 3 Sales & Operations Planning (S&OP) S&OP: also called Macro Planning at the tactical level, since purpose of the S&OP process is to develop the top-down sales and operations plans: for the entire firm, or for some subset of the firm such as a product line or a particular plant. S&OP process begins with demand forecasts and turns them into targets for both sales and operations plans. 4 Sales & Operations Planning (S&OP) Goals of S&OP: to make aggregate level plans that all divisions as well as suppliers, and others in the supply chain can work to, (The output of S&OP is an aggregate plan.) to resolve the inherent tension between sales division and operations division in an organization or to satisfy demand while maximizing profit Sales divisions are measured on revenue, Operations divisions measured on cost. 5 Sales & Operations Planning (S&OP) S&OP should not be determined by the operations people alone; rather it should be agreed on by all the functions of the company (operations, human resources, marketing and finance) and also its supply chain: → S&OP is a structured, collaborative and cross-functional decision-making process that align the competing objectives and constraints. Since each functional part of a firm and the supply chain has its own limitations and constraints, coordination can be difficult. This coordinated planning effort has evolved into a process known as sales and operations planning (S&OP). 6 Targeted market S&OP share, quality, service, profit levels loans, cash turnover, working Process -No Firing -Inventory < Imax capital -Service level > α -Plant capacity -Outsourcing -pricing policy capacity -promotions -Suppliers’ capacity -Warehousing capacity 7 S&OP Process Inputs to the S&OP process: Company policies like “avoid firing personnel”, “limit inventory levels”, “maintain a certain customer service level” Strategic objectives such as “capturing a certain market share”, “achieving targeted levels of quality or profit or service” Capacity constraints (from operations and the other parties in the supply chain) such as the plant capacity, outsourcing capacity, suppliers’ capacity, etc. Financial constraints loans, cash turnover, working capital Demand constraints (from sales) pricing policy, promotions 8 S&OP Process Sales Planning in the S&OP process: Preliminary demand figures are obtained using a forecasting model and then adjusted based on opinions from key customers and sales personnel in the field. These forecasts are further adjusted for planned promotions, product introductions, special offers. → demand management Customer service level is set. → % demand to be satisfied on time; i.e., not backordered. 9 S&OP Process Operations (production) Planning in the S&OP process: The sales plan is then shared with operations function and it is converted to a production plan (operations plan or aggregate plan) as economically as possible. The production plan (monthly by product/service line or family) includes: Workforce level needed Other resources’ levels needed (like machinery, logistics) Quantity and mix of products Overtime and outsourcing levels if any needed Anticipated inventory levels, backlogs, backorders, lost sales. 10 S&OP Process Then the two plans, sales plan and operations plan, must be reconciled → we end up with an annual S&OP that must be updated monthly. Operations plan, production plan and aggregate plan are used interchangeably. 11 The Role of S&OP in a Supply Chain S&OP is an important supply chain issue. For S&OP to be effective, it requires input from both upstream and downstream stages in the chain; and its results have a significant impact on supply chain performance. Good demand forecasts require collaboration with downstream supply chain stages. → “collaborative forecasting” Several constraints in S&OP are from supply chain partners (mainly upstream - like suppliers) outside the company. Production plan for a company defines demand for her suppliers and establishes supply constraints for her customers. 12 The Role of S&OP in a Supply Chain Ideally, all stages of the supply chain should work together on S&OP that optimizes supply chain performance. → “collaborative planning” If each stage develops its own aggregate plan independently, it is unlikely that all the plans will be aligned This lack of coordination results in shortages or oversupply in the supply chain. 13 The Role of S&OP in a Supply Chain e.g. (operations in the factory) (warehouses) 14 The Role of S&OP in a Supply Chain S&OP: a business process to manage the balance and trade-off between the conflicting preferences of the supply and demand side of the supply chain and that offers many value- creation opportunities. S&OP is increasingly being viewed as essential to synchronize the entire supply chain in order to improve its efficiency. S&OP appears to be driving the supply chain benefits such as better meeting customer demand, while at the same time resulting in reduced inventories and minimized supply chain operating costs. S&OP has also been described as a set of decision-making processes to balance demand and supply, to integrate marketing, financial planning and operations planning, and to link high-level strategic plans with day-to-day operations. 15 Aggregate Planning in S&OP Aggregate planning is an important part and actually output of S&OP - core of operations component of S&OP - also called macro production planning Since capacity has a cost (hence it is limited and scarce) and lead times are often long, companies make these decisions long before actual demand is known. Aggregate planning is not limited to manufacturing firms; service organizations must determine their staffing needs as well (e.g., hospitals must plan staffing levels for nurses). 16 Aggregate Planning in S&OP Through aggregate planning a company determines ideal levels of capacity, production, outsourcing, inventory, stockouts, and even pricing and promotions to meet known but dynamic demand over a medium range planning horizon of 3 to 18 months. → tactical level decisions. In this time frame (planning horizon), it is too early to determine production levels by SKU (rather by product lines or families), but it is also generally too late to arrange for additional capacity. Therefore, aggregate planning answers the question: “How should a firm best utilize the facilities that it currently has?” 17 Aggregate Planning in S&OP – Planning Horizon Planning horizon (T): specified in advance (3 to 18 months). Its choice is critical. Too short T: production duration not well reflected. Too long T: inaccuracy in forecasts. Plan frequency and planning horizon depend on the specifics of the industry. End-of-horizon effect: “IT=0” is a poor strategy (Q: Why?) Rather take IT>0 18 Aggregate Planning in S&OP – Planning Horizon A company must also specify the duration of each period within the planning horizon (e.g., weeks, months, or quarters). In general, aggregate planning takes place over months or quarters as the periods. The longer the periods considered in a production model (e.g., days, weeks, or months), the higher the level of aggregation of time. → time aggregation (temporal aggregation) One could use a fine time grid in the earlier part of the model’s planning horizon (e.g., weeks or days) and a coarser time grid (e.g., months or quarters) in the later part of the time horizon, as data regarding this part is very uncertain anyway. 19 Aggregate Planning in S&OP – Planning Horizon Rolling horizon: New forecasts are appended and old forecasts are updated. Rolling horizon (and plans) are almost always used in practice. April May June July-Aug. Sept.-Oct. ….. Now: April Action Plan Plan Plan Plan Plan May June July Aug.-Sept. Oct.-Nov. ….. Now: May Action Plan Plan Plan Plan Plan The action period above is fixed only. Usually time fences are used to show when the level of certainty changes and referred to as frozen (fixed), slushy (somewhat fixed), and liquid (highly flexible) time periods. 20 Aggregate Planning in S&OP – Aggregation Issues In tactical/strategic models, it is often necessary to aggregate certain entities (e.g., products, resources as workforce and machines) of the production system. Instead of dealing with individual machines → machine group or department or entire production line. 21 Aggregate Planning in S&OP – Aggregation Issues Product aggregation: One important reason for aggregation: demand forecasts in medium- or long-term models on the level of individual products could involve too much uncertainty, whereas forecasts on the level of groups of products will presumably have smaller errors. Also, detailed and accurate data on products might not be available and expensive to obtain, especially in large companies with complex product portfolios and manufacturing systems. Grouping (or aggregating) the products under a business area starts with family level in product hierarchy, which is developed by Kotler and Keller in 2006. 22 Aggregate Planning in S&OP – Product Aggregation Use aggregate product by lumping products/services that share a common process to form a group. For similar items → an “average” item (TV sets, sedans, printing; but not custom furniture, castings, contract construction); an “average” request from a call center For dissimilar items but commonalities → aggregate by weight, volume, service classification, amount of worker hours, monetary value; e.g., castings in tons, glass in m2. All in all, appropriate aggregating scheme is not always obvious; but depends on the context of the particular production planning problem and the level of aggregation required. 23 Aggregate Planning in S&OP – Product Aggregation Example: Products A, B & C requires 5, 2.5 and 0.75 hours to produce, respectively. Monthly demands are: 200, 100 and 1,000 units for A, B and C, respectively. An equivalent monthly demand for an aggregate product in production hours = (5 200 ) + (2.5 100) + (0.75 1,000) = 2,000 hours. Similarly, an aggregate product in monetary terms is computed using production costs instead of production time. 24 Aggregate Planning in S&OP – Costs Costs (not all are out-of-pocket, some are opportunity costs; all costs are incremental): Aggregate plans are made with the help of a cost-sensitive performance measure. Costs affecting the aggregate plan: Regular time cost Overtime and undertime (idle time) costs Subcontracting/outsourcing costs Inventory holding costs Shortage costs (backorder cost or lost profit from lost sales) Smoothing cost (production rate-change cost) - usually hiring and firing costs 25 Aggregate Planning in S&OP - Costs Regular Time Costs: Costs of producing one unit of output during regular working hours. Includes payroll of regular employees, material costs, and other manufacturing expenses. Regular payroll costs become a sunk cost, when all production is carried out on regular time; since # produced= # demanded over any planning -horizon of sufficient length. If there is no overtime or worker idle time, not to be included in the total cost. Overtime and Outsourcing Costs: Cost of production of units not produced in regular working hours Overtime: Production by regular-time employees beyond the normal work day. Outsourcing: Production of items by an outside supplier 26 Aggregate Planning in S&OP - Costs Holding & Shortage (Backorder) Costs Holding Costs: Costs arise as a result of having capital tied up in inventory. Expressed in terms of money per unit held per planning period Assumed to be linear in the number of units being held at a particular point in time Include: costs for capital tied up in inventory (opportunity cost), insurance, taxes, breakage, spoilage, pilferage, costs of storage (equipment and people to handle inventory and physical space) 27 Aggregate Planning in S&OP - Costs Holding & Shortage (Backorder) Costs Shortage Costs: Costs arise as a result of negative inventory level. Expressed in terms of money per unit short per planning period. Shortages can occur when forecasted demand exceeds the system capacity or when demands are higher than anticipated. A unit that is ordered and not delivered on time, but later on, due to shortage is called a backorder Generally assumed that excess demand is backordered. But in highly competitive situations, excess demand is lost. Assumed to be linear. Include special record-keeping and handling of backordered items, and loss of revenue and goodwill. 28 Aggregate Planning in S&OP - Costs Smoothing Costs Arise as a result of changing the production levels from one period to the next. Most salient smoothing cost in aggregate planning: cost of changing size of workforce, include hiring and firing Hiring Costs: advertise, interview & train new hires Firing (laying off) Costs: severance pay, morale decline & loss of goodwill. (labor agreements restrict the management to freely alter workforce levels) Both costs are assumed to be linear functions of the number of employees hired or fired. 29 Aggregate Planning in S&OP - Costs Idle Time Cost Underutilization of equipment capacity/workforce or idle time Ignored unless an extra expense is incurred during idleness or in start- up after idling. But accounted for in cases like the examples below: Additives to preserve the status of a tank carrying concrete to the construction sites if the tank is left unused Retraining and reorganizing service personnel after lengthy idle periods Underutilized carrier capacity 30 Aggregate Planning in S&OP – Demand Options Operations managers can meet aggregate plans by adjusting capacity (supply) and/or demand. S&OP involve proactive demand management. Through demand options, firms try to smooth out changes in the demand pattern over the planning period. Many manufacturers assume that the use of the demand options has been fully explored by the marketing department and those reasonable options incorporated into the demand forecast. The operations manager then builds the aggregate plan based on that forecast. 31 Aggregate Planning in S&OP – Demand Options Demand management entails modifying or influencing demand in several ways, called as demand options: Demand options: Advertising : to promote demand during slack periods and shift demand from peak periods to slack periods (i.e., to smooth out demand). Dynamic and/or differential pricing: used for reducing peak demand or for building up demand in off-peak periods by means of incentives, sales promotions. Some examples: winter coat specials in May cheaper seats in midnight flights electricity rates (TL/kwh) cheaper at night sales rebates (“buy 1 - get 1 free”) off-peak specials or happy hours at restaurants, cafes airlines and hotels offering weekend discounts and off-season rates 32 Aggregate Planning in S&OP – Demand Options Development of complementary offerings: firms with highly seasonal demands develop products that have countercyclic seasonal trends. Involves examining the idleness of resources and creating demand for idle resources. Some examples: Ice cream manufacturer offers cakes in winter months; hotels in the Mediterranean region offer attractive packages for conference organizations during off-season months; manufacturing both lawn mowers and snowblowers. Offering breakfast in restaurants to utilize idle capacity in the morning Cross selling: practice of selling an additional product or service to an existing customer. Selling two-way ticket like Ank-İst and İst-Ank, one of the ways being free. 33 Aggregate Planning in S&OP – Supply Options AP evaluates options in adjusting capacity to find an economic strategy to satisfy demand. These options in capacity adjustment are defined as supply (capacity) options, because they do not try to change demand but attempt to absorb demand fluctuations: Changing inventory levels Produces a constant amount each period → more even use of capacity throughout time. Variation in demand is accounted for by holding inventory. Large buildups of inventory during the periods of low demand Cost of this option: inventory holding cost Not an available option for service operations. 34 Aggregate Planning in S&OP – Supply Options Changing inventory levels Varying production rates through overtime and undertime Competent staff is maintained. Hiring/firing costs are avoided. A common option when demand fluctuations are not extreme and only temporary. Undertime is planned underutilization of the workforce: working fewer hours/day, working fewer days/week, furloughs (unpaid leave), vacation during months of slow demand. Varying workforce size by hiring or firing (layoffs) Cost of hiring and firing workers. May be restricted by union contracts and/or company policies. Not appropriate if worker skills are scarce or competition for labor is intense. Outsourcing (or subcontracting) A feasible option if a supplier can reliably meet quality and time requirements. Common for components, subassemblies, service operations. Requires strong relations with the supplier including contracts. 35 Aggregate Planning in S&OP – Supply Options Cooperative arrangements Similar to subcontracting. Involve partner firms that are typically competitors. The firms choose to share their capacity, thus preventing either firm from building capacity for occasional peak-demand periods only. e.g. Hotels or airlines that shift customers among one another when they are fully booked. Part-time or temporary workers Feasible option for unskilled jobs or in areas with large temporary labor pools. Less costly than full-time workers and more flexible. Used extensively in many service operations like restaurants, hotels, hospitals; and in agriculture-related industries. Disadvantages: high turnover, accelerated training requirements, less commitment, scheduling difficulties 36 Aggregate Planning in S&OP – Supply Options Backlogs, backordering and lost sales For customized products/services: orders are accepted but met at a later date, to benefit from economies-of-scale, etc. The accumulation of these orders create a backlog (orders to be fulfilled). For make-to-stock companies: customers that require a product which is temporarily out-of-stock may have the option of backordering the product. If backordering is allowed, then it can be planned. If the customer is unwilling to wait for the backordered product, the sale is lost. Lost sales can also be planned for, if allowed. 37 Strategies for Aggregate Planning Changing inventory levels → level production Demand Production Production Units Inventory Time 38 Strategies for Aggregate Planning Chase demand strategy (Zero inventory strategy) Matches the production rate with the demand rate → produces exactly the amount demanded by varying machine capacity (production rate, if production is machine-paced) and/or workforce level (by hiring and firing employees), overtime/undertime, subcontracting, etc. as the demand rate varies. Results in low levels of inventory in the supply chain. Cost of this strategy: cost of varying the machinery capacity and/or workforce level, cost of overtime,... A variation of this strategy is chase supply strategy. 39 Strategies for Aggregate Planning Chase Demand Strategy (Zero Inventory Strategy) Demand Production Units Time 40 Strategies for Aggregate Planning Pure vs. Mixed Strategies One strategy for adjusting capacity is not always preferable to another. The most effective strategy depends on the demand pattern, competitive position and cost structure of a firm or product line. Pure strategy: using only one of the strategies above in developing the aggregate production plan. e.g., Chase strategy or level strategy (two extreme strategies) Mixed strategies: using the two extreme strategies above together in developing the aggregate production plan. Neither pure nor mixed strategies guarantee an optimal plan. 41 Aggregate Planning Approaches Spreadsheet Methods Linear Programming (LP) Models Transportation Model Multi-objective Linear Programming (MOLP) Goal Programming (GP) 42