Inhalation Dosage Form PDF 2019-2020
Document Details
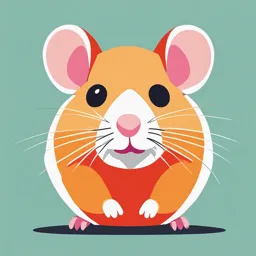
Uploaded by FineTimpani830
Baghdad College of Pharmacy
2020
Tags
Summary
This document discusses inhalation dosage forms, including nebulizers, metered-dose inhalers (MDIs), and dry powder inhalers (DPIs). It covers the design of these devices, their components, and the principles behind their functioning. The document also mentions the role of propellants and surfactants in different types of inhalers.
Full Transcript
## INDUSTRIAL PHARMACY ### Lec. 8 ### 2019-2020 ## INHALATION DOSAGE FORM A wide variety of agents has been administered to the lung via inhalation, for the treatment of many diseases. The most frequent use of inhalation therapy is for the treatment of asthma using drugs such as 𝛽-agonist, corti...
## INDUSTRIAL PHARMACY ### Lec. 8 ### 2019-2020 ## INHALATION DOSAGE FORM A wide variety of agents has been administered to the lung via inhalation, for the treatment of many diseases. The most frequent use of inhalation therapy is for the treatment of asthma using drugs such as 𝛽-agonist, corticosteroids and anticholinergic agents. However, the respiratory route has been receiving increased attention recently as a route for systemic drug delivery, most notably for the delivery of inhaled insulin. For all inhalation dosage forms, the particles size of a therapeutic agent should be 5 µm or less. There are 3 basic types of commercially available inhalation delivery systems: 1. **Nebulizers**: Used for the acute care of patients. Solutions or suspensions can be nebulized by ultrasonic or an air jet and administered via a ventilation mask. 2. **Metered-dose inhalers**: A versatile multi-dose inhaler where the drug is formulated in a propellant mixture under pressure. The drug is expelled out (by a valve) in a metered volume. 3. **Dry powder inhalers**: instead of formulating the drug in liquid form, these inhalers deliver the drug as powder to be inspired by the patient. ### The design of nebulizer There are two general types of nebulizers: the ultrasonic and air jet. In ultrasonic nebulizers, ultrasound waves are formed in nebulizer chamber by a ceramic crystal that vibrates when electrically is switched on. The ceramic crystal produces high-energy waves in the solution (within the chamber) that generates an aerosol cloud at the solution surface. **Schematic representation of ultrasonic nebulizer** - Therapeutic mist - Piezo electric crystal - High frequency source The aerosol produced by an air-jet nebulizer is generated by a completely different principle. When compressed air is forced through an orifice, an area of low pressure is formed. A liquid may be withdrawn from a nozzle to mix with the air jet to form droplets. A baffle within the nebulizer is often used to facilitate the formation of the aerosol cloud. Compressors are usually used to generate the airstream. **Schematic of an air-jet nebulizer** - Therapeutic mist - Pressurized gas - Area of negative pressure - Jet - Baffle - Solution Nebulizers are designed primarily for using aqueous solutions or suspensions. Typically the suspensions use particles up to 5 microns. ### The design of metered-dose inhalers The main components of all metered-dose inhalers (MDIs) are: - Active ingredient - Propellant (a liquefied gas) - Metering valve - Canister - Actuator with a mouthpiece. **Schematic of metered-dose inhalers** - Canister - Actuator - Metering valve - Mouthpiece - Actuator seat - Actuator orifice - Drug suspension or solution in propellant The active ingredient may be suspended in the propellant or dissolved directly in the propellant (or dissolved by the aid of a cosolvent then mixed with the propellant). The metering valve is the key for measuring an accurate dose to the patient. The valve is fixed onto a canister, which is made of aluminum. Finally, there is the actuator (made from plastic) which holds the canister and through which the patient inhales the dose. Hydrofluroalkane (HFC) propellants are novel excipients developed for long-term use in MDIs. Because the propellants in MDIs comprise the large majority of the formulation (more than 98%), extensive testing studies show that these materials are safe. MDIs typically contain a surfactant or dispersing agent (because they are either solution or suspension). These materials generally need to have some solubility in the propellant. These agents are required both to maintain the disperse nature of the drug (in suspension formulations) and also to provide lubrication for the metering valves. However, these surfactants have poor solubility in the HFC propellants, so alternate formulation strategies, such as using cosolvents, have been developed. The fundamental requirement of a MDI formulation is that the drug dose be delivered accurately and reproducibly. Regarding a suspension MDI, this requirement can be met only if the drug can be homogeneously distributed in a deaggregated state. The extent and rate of drug sedimentation can be reduced to some extent by manipulating the physicochemical properties of the formulation. According to Stokes' law, ($V = \frac{D^2(d_1-d_2)g}{18\eta}$), one can change some of the variables in order to get an effective formulations (V is the settling velocity of solid, D is the diameter of the solid, d₁ and d₂ is the density of the solid and liquid respectively and η is the viscosity of the liquid). ### Metering valves The metering valve in an MDI is the critical component in the design of an effective delivery system. The main function of the metering valve is to reproducibly deliver a portion of the liquid phase of the formulation in which the medication is either dissolved or suspended. These valves are essentially designed to work in the inverted position. Inversion of the valve stem allows the contents of the MDI to fill the metering chamber to be dispensed through the orifice in the valve stem. After actuation, the metering chamber refills from the bulk liquid formulation and is ready to dispense the next dose. ### Filling metered-dose inhaler canisters Canisters are filled by liquefying the propellant at reduced temperature or elevated pressure. In cold filling, active compound, excipients and propellant are chilled and filled at about -30°C. Additional propellant is then added at the same temperature and the canister sealed with the valve. In pressure filling, a drug/propellant concentrate is produced and filled at effectively room temperature and pressure. The valve is crimped on to the canister and additional propellant is filled at elevated pressure through the valve, in a process known as gassing. Pressure filling is most frequently employed for inhalation aerosols. Once filled, the canisters are leak tested by placing them in a water bath at elevated temperature, usually 50-60°C. Following storage to allow equilibration of the formulation and valve components, the containers are weighed to check for further leakage, prior to spray testing and insertion into actuators. ### Advantages and disadvantages of metered-dose inhalers The major advantages of MDIs are their portability, low cost and disposability. Many doses (up to 200) are stored in the small canister and dose delivery is reproducible. The sealed container protects drugs from oxidative degradation and microbiological contamination. However, MDIs have disadvantages. In some cases they are inefficient at drug delivery to the desired site of action (drug disposition on respiratory walls). Minimized volatility characteristics of some types of propellants. An additional problem with MDIs, which is beyond the control of the formulator and manufacturer, is their incorrect use by patients. ### Design of dry powder inhalers In dry powder inhaler (DPI) systems, the drug is inhaled as cloud of fine particles. The drug is either preloaded in an inhalation device or filled into hard gelatin capsules or foil blister discs which are loaded into a device prior to use. There are two types of DPIs: those that use drug filled into discrete individual doses, e.g., gelatin capsule (Unit-dose inhalers) and those that use a reservoir of drug that meters out doses when required (Multi-dose inhalers). Both are now widely available and are gaining broad acceptance. There is clearly considerable interest in these devices because they do not require propellants to disperse the drug. Also DPIs can deliver larger drug doses than MDIs. On the other hand, they have a disadvantage; some DPIs require inspiration flow rates of 60 L/min to effectively deaggregate the powder. This certainly cannot always be achieved by all asthmatic patients. Also, they are more exposed to atmospheric conditions than MDIs, which may reduce formulation stability. Finally, DPIs are generally less efficient at drug delivery than MDIs. Unit-dose inhalers are devices in which a powder-containing capsule is placed in a holder. The capsule is opened within the device and the powder is inhaled. The capsule residue must be discarded after use and a new capsule inserted for the next dose. Example on this type is sodium cromoglycate. Briefly, the drug and diluents are prefilled in a hard gelatin capsule and loaded into the device. After activation of the device (which presses on the capsule), the patient inhales the dose which is dispensed from the broken capsule by means of inspired air. Regarding multi-dose inhaler, the drug is contained within a storage reservoir and can be dispensed into the dosing chamber by a simple back and forth twisting action on the base of the unit. **Figure: Components of the Turbuhaler, a multi-dose dry powder inhaler.** - (1) mouthpiece with insert - (2) bypass air inlet - (3) inhalation channel - (4) air inlet - (5) desiccant store - (6) window for dose indicator - (7) dose indicator - (8) storage unit for drug compound - (9) dosing unit - (10) operating unit - (11) turning grip. **Note:** The image in the document is of a schematic representation of the Turbuhaler, a multi-dose, dry powder inhaler. While the image shows the mechanism of the inhaler, the image cannot be converted into a markdown table as the image does not show a structured table layout.