Introduction to Process Dynamics and Control PDF
Document Details
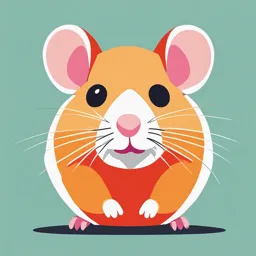
Uploaded by EasyToUseElPaso
Mapúa University
Engr. Louise Grace Avena-Ardeta
Tags
Summary
This document provides an introduction to process dynamics and control, covering various aspects such as process control, distributed control systems (DCS) compared to programmable logic controllers (PLCs), objectives of control, design methodology for process control, and illustrating relevant examples. The material includes discussions on maintaining operational conditions and set points in water tank simulations, and examines factors impacting process controls, such as safety and environmental considerations.
Full Transcript
Internal Use Introduction to Process Dynamics and Control CH158-2P Process Dynamics and Control Engr. Louise Grace Avena-Ardeta Internal Use...
Internal Use Introduction to Process Dynamics and Control CH158-2P Process Dynamics and Control Engr. Louise Grace Avena-Ardeta Internal Use 2 Process control is a mixture between combination of the statistics and engineering discipline that deals with the mechanism, architectures, and algorithms for controlling a process. ▪ Controlling the temperature of a water stream. Process Control ▪ Operating a jacketed reactor isothermally. ▪ Maintaining a set ratio of reactants to be added to a reactor. ▪ Ensuring that the tank does not overflow. Engr. Louise Grace Avena-Ardeta Internal Use 3 ▪ Safety ▪ Minimize environmental impact Process Control ▪ Optimize processes by maintaining process variable near the desired values Engr. Louise Grace Avena-Ardeta Internal Use 4 Today many chemical plants have gone to full automation, which means that engineers and operators are helped by DCS that communicates with the instruments in the field. Distributed Control System (DCS) Engr. Louise Grace Avena-Ardeta Internal Use 5 ▪ PLC – one machine ▪ DCS – entire plant/interconnected processes DCS vs PLC PLC DCS Engr. Louise Grace Avena-Ardeta Internal Use 6 1. Maintain the process at the operational conditions and set points A water tank in Objectives of a heating or cooling The water level in the Control process without tank will continue to HOW TO CONTROL? drainage and rise and is constantly eventually being filled overflow with water Engr. Louise Grace Avena-Ardeta Internal Use 7 1. Maintain the process at the operational conditions and set points A water tank in ADD control Objectives of a heating or cooling The water level in the valves and level sensors Control process without tank will continue to in the tank that can tell the drainage and rise and engineer or is constantly eventually technician the being filled overflow level of water with water in the tank Engr. Louise Grace Avena-Ardeta Internal Use 8 TALKS ABOUT INTERNAL FACTORS AFFECTING THE PROCESS 1. Maintain the process at the operational conditions and set points ADD control A water tank in valves and a heating or The water level level sensors in cooling process in the tank will the tank that can without continue to rise tell the drainage and is and eventually engineer or constantly overflow technician the being filled with level of water in water Objectives of the tank Control Engr. Louise Grace Avena-Ardeta Internal Use 9 TALKS ABOUT EXTERNAL FACTORS AFFECTING THE PROCESS 2. Transition the process from one operational condition to another Examples of why a process may be moved from one operational set point to another: 1. Economics Objectives of 2. Product specifications Control 3. Operational constraints 4. Environmental regulations 5. Consumer/Customer specifications 6. Environmental regulations 7. Safety precautions Engr. Louise Grace Avena-Ardeta Internal Use 10 ▪ Input Variable - shows the effect of the surroundings on the process ▪ Manipulated output - variable in the surroundings can be Definitions and control by an operator or the control system in place Terminologies ▪ Disturbances - inputs that can not be controlled by an operator or control system. There exist both measurable and immeasurable disturbances. Engr. Louise Grace Avena-Ardeta Internal Use 11 ▪ Output variable - variables that are process outputs that affect the surroundings ▪ Single input – Single output (SISO) - for one Definitions and control(output) variable there exist one manipulate (input) variable that is used to affect the process Terminologies ▪ Multiple input – Multiple output (MIMO) - several control (output) variable that are affected by several manipulated (input) variables used in a given process Engr. Louise Grace Avena-Ardeta Internal Use 12 ▪ Cascade: A control system with 2 or more controllers, a "Master" and "Slave" loop. The output of the "Master" controller is the setpoint for the "Slave" controller. ▪ Dead Time: The amount of time it takes for a process to Definitions and start changing after a disturbance in the system. ▪ Derivative Control: The "D" part of a PID controller. With Terminologies derivative action the controller output is proportional to the rate of change of the process variable or error. ▪ Error: In process controls, error is defined as: Error = setpoint - process variable. Engr. Louise Grace Avena-Ardeta Internal Use 13 ▪ Integral Control: The "I" part of a PID controller. With integral action the controller output is proportional to the amount and duration of the error signal. ▪ PID Controller: designed to eliminate the need for continuous operator attention. They are used to automatically adjust system variables to hold a process Definitions and variable at a setpoint. Terminologies ▪ Proportional Control: The "P" part of a PID controller. With proportional action the controller output is proportional to the amount of the error signal. ▪ Setpoint: The setpoint is where you would like a controlled process variable to be. Engr. Louise Grace Avena-Ardeta Internal Use (days-months) 5. Planning and Scheduling 14 (hours-days) 4. Real-Time Optimization 3b. Multiv ariable (minutes-hours) and Constraint Control Hierarchy of (seconds-minutes) 3a. Regulatory Process Control Control Activities (< 1 second) 2. Saf ety , Env ironment and Equipment Protection (< 1 second) 1. Measurement and Actuation Process Engr. Louise Grace Avena-Ardeta Internal Use 15 ▪ Understand the process Design ▪ Identify the operating parameters Methodology for ▪ Identify the hazardous conditions Process Control Engr. Louise Grace Avena-Ardeta Internal Use 16 ▪ Identify the measurables ▪ Temperature Pressure Flow rate pH Humidity Level Concentration Viscosity Conductivity Turbidity Redox/potential Electrical behavior Flammability ▪ Identify the points of measurement Design ▪ Select measurement methods Methodology for ▪ Electric Pneumatic Light Radiowaves Infrared (IR) Process Control Nuclear ▪ Select control method ▪ Select control system Engr. Louise Grace Avena-Ardeta Internal Use 17 ▪ Set control limits ▪ Define the control logic ▪ Create redundancy system Design ▪ Define fail-safe Methodology for ▪ Set lead/lag criteria Process Control ▪ Investigate effects of changes before/after ▪ Integrate and test with other systems Engr. Louise Grace Avena-Ardeta Internal Use 18 Failures in Process Control Engr. Louise Grace Avena-Ardeta Internal Use 19 Failures in Process Control Engr. Louise Grace Avena-Ardeta Internal Use 20 ▪ https://forms.office.com/r/LcdS4Zy6gX ChEATDUDE Engr. Louise Grace Avena-Ardeta