Management Accounting - Lesson 4 - Calculation Methods - PDF
Document Details
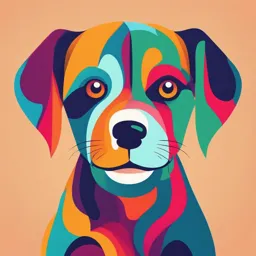
Uploaded by PeerlessSpring5691
Universidad de Málaga
Mariano Soler Porta
Tags
Summary
This document is a lesson on management accounting, specifically on the calculation methods and cost carriers. It discusses the different types of production - simple, alternative, parallel, and joint - that a company may have. It also outlines the basic methods, including splitting, supplement, and distribution, applicable to these different production types.
Full Transcript
MANAGEMENT ACCOUNTING Grado en Economía y Administración y Dirección de Empresas LESSON 4: THE COST CARRIES: CALCULATION METHODS PART 1: CONCEPT AND CLASSES Departamento de Contabilidad y Gestión UNIVERSIDAD D...
MANAGEMENT ACCOUNTING Grado en Economía y Administración y Dirección de Empresas LESSON 4: THE COST CARRIES: CALCULATION METHODS PART 1: CONCEPT AND CLASSES Departamento de Contabilidad y Gestión UNIVERSIDAD DE MÁLAGA LESSON 4: THE COST CARRIES: CALCULATION METHODS Versión 2.0 Septiembre de 2021 © Mariano Soler Porta MANAGEMENT ACCOUNTING Grado en Economía y Administración y Dirección de Empresas © Mariano Soler Porta - Dpto. Contabilidad y Gestión - Universidad de Málaga 2 LESSON 4: THE COST CARRIES: CALCULATION METHODS 1 COST CARRIERS: CONCEPT AND CLASSES 1.1. CONCEPT OF COST CARRIER The previous lessons, we have dealt with the two first basic concepts of the process of generating the cost in the company "Elements or factors of cost" and "Cost Centers”. This lesson we will refer to the third of these concepts, the Cost carrier or Cost Object. This concept responds to the idea of affectation of cost and it fulfils the cumulative function of the value of the total consumption of material and intangible goods generated during the production process and which, therefore, integrate the product or service, either from the centers (organic system), or from the factors (inorganic system). However, depending on the cost allocation approach to be used, and because the production does not incorporate all of the costs in all of them, we can find other kinds of carriers: ✓ In the Full-Costing: There is only one carrier: the production valued at total cost o full cost carrier, ✓ In the Direct-Costing: There are different carriers: The production Valued at variable cost or variable cost carrier The carrier of the fixed cost. ✓ In the FullCosting Evolved Also There are different carriers: The production Valued at intrinsic or production cost or Production cost carrier The cost carrier to reintegrate 1.2. CLASSES OF COST CARRIER In all cases we refer to production as an effect, and in all its manifestations: Finished production, comprises the products manufactured by the company and whose sale constitutes the main activity of the company. In a company that manufactures furniture, the different models of furniture. MANAGEMENT ACCOUNTING Grado en Economía y Administración y Dirección de Empresas © Mariano Soler Porta - Dpto. Contabilidad y Gestión - Universidad de Málaga 3 LESSON 4: THE COST CARRIES: CALCULATION METHODS Semifinished production, it covers the products manufactured by the company, but which are still pending elaboration to achieve the desired products. Usually these are not intended for sale, but this may happen Circumstance. Examples of this category of inventories would be: wood planks and furniture skeletons. Production in progress, it includes those products that are in the training or transformation phase in a specific activity centre. There is no possibility of selling them. It could be noted: Wood being sawn, unfinished wood planks or furniture skeletons being varnished. Subproducts (coincides with the concepts of Residue and recovered material of the PGC), those obtained inevitably and at the same time as the products if they have intrinsic value and can be used by the company or sold. Sawdust obtained in the manufacture of furniture, if used by the company to make Wood agglomerate, would be a byproduct that recovers. Molasses in the manufacture of sugar (they constitute the raw material of the industrial alcohol), the residues of fish (they become oils and fertilizers) or the whey of milk in the manufacture of cheese, would be by-products to be sold. Waste: Those obtained inevitably and at the same time as the products or by-products, but they do not have value of realization and therefore they cannot be sold (even sometimes for the company it has a cost its elimination). The definition of carrier that we are considering is that of Final cost carrier, but the concept of carrier or Cost Object, as a cost accumulator in its broadest sense, it also refers to intermediate stages of aggregation of costs such as an activity, a department, etc. MANAGEMENT ACCOUNTING Grado en Economía y Administración y Dirección de Empresas © Mariano Soler Porta - Dpto. Contabilidad y Gestión - Universidad de Málaga 4 LESSON 4: THE COST CARRIES: CALCULATION METHODS 2 THE COST OF THE COMPANY OR ITS OWN COST PRICE The cost of the company is defined as the integral set of all the costs that are generated in the company (it comes to coincide with the concept of full cost of full-cost method), and will depend on each economic unit, the dimension of the organization and the technology applied in the management process. This company cost will have different structure and composition, depends of the applying in the capture of the magnitudes of the internal scope an organic or inorganic system. in the case of the application of an Inorganic System, that neglects the existence of the centers in the company and considers that the formation of the cost of the carrier is carried out directly, with the classes of cost, we can define different levels of cost until arriving at the cost of company, as the following chart shows. Figure 4.1: Composition of the cost of the company in a system of inorganic costs. Source: Requena Rodríguez, J.M. y Vera Ríos, S. (2008) MANAGEMENT ACCOUNTING Grado en Economía y Administración y Dirección de Empresas © Mariano Soler Porta - Dpto. Contabilidad y Gestión - Universidad de Málaga 5 LESSON 4: THE COST CARRIES: CALCULATION METHODS The process begins with the treatment of the direct labor over the direct materials. The valuation of both consumptions is called BASIC COST, direct cost or primary cost. In addition to the direct factors, the production involved other indirect factors (amortizations, telephone, electricity, repairs, etc.). We call them Indirect Production Cost. The sum of these Indirect costs with previous direct costs, determine the INDUSTRIAL COST. For the realization of the production process has been necessary a background and contemporary financing that generates costs, the Financial Costs Related with production. Adding it with the industrial cost we have the PRODUCTION COST. Once the production is obtained, it goes to the warehouse until it is sold. In this period the costs are denominated Sales costs or product placement on the market, which added to the operating cost determines the COMMERCIAL COST. All the previous processes are developed by means of an adequate economic direction of the company (management, organization of the company, planning of the business management), which also originates a cost, called Management and administration Costs (General insurance, costs of maintenance of the administration, direction, organization, planning, accounting, etc.). By adding them to the commercial cost, we finally get the COMPANY COST. In the case of the Organic System, the composition of the company cost will be the following: MANAGEMENT ACCOUNTING Grado en Economía y Administración y Dirección de Empresas © Mariano Soler Porta - Dpto. Contabilidad y Gestión - Universidad de Málaga 6 LESSON 4: THE COST CARRIES: CALCULATION METHODS Figure 4.2: Composition of the cost of the company in a system of organic costs. Source: Requena Rodríguez, J.M. y Vera Ríos, S. (2008) The elaboration of the product takes place from the cost of the direct materials. At first, the tasks carried out in the Procurement or Purchase Section will be carried out, which increase the cost of it. The sum of both costs is called the ASSIGNMENT COST OF DIRECT MATERIALS, which will be the amount by which the purchasing section transfers the direct materials to the transformation section to carry out its consumption and processing. These materials will then undergo a series of processes in the Transformation section that will generate the Maintenance costs of the transformation section. Added to the cost of the transfer of the materials will result in the cost of production or THE INTRINSIC COST of production. Once the production is finished, it goes to the sales section where its storage, conservation, distribution, etc. will take place, in short, all the actions aimed at placing it on the market, which would cause a new increase in the cost, determining what is known as COMMERCIAL COST. MANAGEMENT ACCOUNTING Grado en Economía y Administración y Dirección de Empresas © Mariano Soler Porta - Dpto. Contabilidad y Gestión - Universidad de Málaga 7 LESSON 4: THE COST CARRIES: CALCULATION METHODS Finally, in order for everything to be possible, the appropriate management and administration has been carried out, which generates the costs of the Administration section, which together with the commercial cost determines the COMPANY COST. The cost of maintaining the commercial and administrative sections is the so-called "Cost to be return". Both esqueare translated into the company in A form of composition of the cost to be taken for each product, to know the composition of the same. 3 METHODS OF CALCULATION: FUNDAMENTAL PRINCIPLES The incorporation of the cost to the cost carriers, either from the Classes in an Inorganic system, either from the Centers, in an Organic system, is carried out through those of "Calculation Methods", which are defined as the "Set of operations aimed at carrying out the computation of the costs to be imputed to the product ". The way of acting will be conditioned by the structure that owns the cost (inorganic or organic), the technological and economic characteristics of the production (if production is simple, composite, etc.) and by the behavior of the factors that intervene in the process. 3.1. FUNDAMENTAL PRINCIPLES To ensure the correction of the Methods of calculation, professor Schneider believes that meet two principles: ✓ Principle of proportionality ✓ Principle of differentiation. According to the Principle of proportionality, known a magnitude of cost and elements to which it should be affected, that cost should be allocated proportionately to the consumption of factors that these elements include (for MANAGEMENT ACCOUNTING Grado en Economía y Administración y Dirección de Empresas © Mariano Soler Porta - Dpto. Contabilidad y Gestión - Universidad de Málaga 8 LESSON 4: THE COST CARRIES: CALCULATION METHODS example, if a product incorporates double quantity of raw material that another must correspond double cost). With regard to the Principle of differentiation, the incorporation of the cost to the carriers must be done in a way, that analyzing its value we can know the different strata that compose it, and so, we get information about the process of obtaining this product. 3.2. CLASSES OF PRODUCTION To carry out the application of the different methods of calculation it will be necessary to know the type of production, defined as a cause1, that the company develops. Can be distinguished fundamentally between two Classes of production (considered as a cause): Simple and composed. Is understood as Simple production, the one under which you get a single product type (Cement, wheat, Etc). The Composite production will be the one by which two or more kinds of products are obtained (a land with wheat and barley). In turn, this can be of three classes: Alternative, cumulative and parallel. a. Alternative: That in which increases in the obtaining of one of the products implies decreases in the production of the others, because they are excluding (in a same land dedicated to wheat and barley, if more wheat is cultivated, it is less barley, or in a cattle farm, the increase in the production of milk produces a decrease in the meat). b. Cumulative: The one in which the obtaining of a type of product and its increase imply the obtaining of another or others, because they are obtained simultaneously. It also receives the name of Joint production. (milk and wool production, refinery ofl oil that gives place to different derivatives...). There is a particular case of joint production called Coupled production, when the proportion in which the different types of 1It is necessary to interpret the term production in a double sense, as a cause and as an effect, according to which we relate it with the productive process itself or with the product resulting from that process. MANAGEMENT ACCOUNTING Grado en Economía y Administración y Dirección de Empresas © Mariano Soler Porta - Dpto. Contabilidad y Gestión - Universidad de Málaga 9 LESSON 4: THE COST CARRIES: CALCULATION METHODS products are obtained is constant (it is very common in the chemical Industry). c. Parallel: the one where you get two or more types of products but independently, without interference, it is, therefore, of the conjunction of several simple productions. Different methods of calculation are applicable for different types of production, which we will analyse in the following sections. Figure 4.3: Main calculation methods MANAGEMENT ACCOUNTING Grado en Economía y Administración y Dirección de Empresas © Mariano Soler Porta - Dpto. Contabilidad y Gestión - Universidad de Málaga 10 MANAGEMENT ACCOUNTING Grado en Economía y Administración y Dirección de Empresas LESSON 4: THE COST CARRIES: CALCULATION METHODS PART 2: METHODS OF CALCULATING: DIVISION AND SUPPLEMENTS Departamento de Contabilidad y Gestión UNIVERSIDAD DE MÁLAGA LESSON 4: THE COST CARRIES: CALCULATION METHODS Versión 2.0 Septiembre de 2021 © Mariano Soler Porta MANAGEMENT ACCOUNTING Grado en Economía y Administración y Dirección de Empresas © Mariano Soler Porta - Dpto. Contabilidad y Gestión - Universidad de Málaga 2 LESSON 4: THE COST CARRIES: CALCULATION METHODS 4 METHODS OF CALCULATING: DIVISION AND SUPPLEMENTS First of all, we will refer to the Splitting method, which consists of calculating a quotient between a Total Cost and the Number of units corresponding to calculate a Unit Cost. Within it, we can find two types: ✓ 1. Pure ✓ 2. By Equivalences 4.1. PURE SPLITTING METHOD Its application can be made of two Ways: Globalized and differentiated. Application Globalized, is used in production systems in the that is obtained only one type of product (as long as there is no production in progress in the period under calculation). Total Cost (𝐾) Unit Cost (𝑘) = Produc. units (𝑥) Application Differential is used in the systems of Organic costs, in those phases of the production or centers in which only the treatment of one product is performed, or several, but with uniform treatment. Total Cost of the Main place "i" (KLP𝒊 ) 𝒌𝒊 = Units process in place "i" (N𝒊 ) In this case, the unit cost of the product will be formed by the sum of the k i of each one of the Centers Main company. MANAGEMENT ACCOUNTING Grado en Economía y Administración y Dirección de Empresas © Mariano Soler Porta - Dpto. Contabilidad y Gestión - Universidad de Málaga 3 LESSON 4: THE COST CARRIES: CALCULATION METHODS 4.2. SPLITTING METHOD BY EQUIVALENCES Its applies in most cases, since it is not too common to find companies that obtain a single type of product. This Method is based on the existence of different types of products, which incorporate different consumptions of Materials and Labor, so it will be necessary homogenize their differences as if they were a single type of product, and then be able to apply Pure Division method and thus get the unit cost. This homogenization will require to know the equivalence (Equivalence figure) of products with others with respect to the amount of material they incorporate, or with respect to the time of treatment in a given place. From this equivalence figure the Amount of equivalence or equivalent amount that are units with respect to the cost incorporating, although they are not actual units, only are units for the calculation. This multiplies the Number of units of each product (or Product project) by the Equivalence coefficient of products compared to others, (ie, a table incorporates two planks of wood and another four, so the second incorporates double quantity of materials that the first, and therefore, it must incorporate double cost of materials, and therefore the coefficient of equivalence would be 2 to 1 (or 4 to 2)). This coefficient can be established according to consumption of materials or depending on the consumption of labour, and multiplied by the number of Q. (quantity units) of products or materials in question, will lead to the Equivalence quantity or equivalent quantities, which are homogeneous units with respect to the cost incorporating. Q of product x Equivalence coefficient = Equivalence quantity The quotient between the Total Cost and these Units Equivalent will be the Unit cost of each of those equivalent units, and Multiplied by the equivalence figure will result in unit cost per product. MANAGEMENT ACCOUNTING Grado en Economía y Administración y Dirección de Empresas © Mariano Soler Porta - Dpto. Contabilidad y Gestión - Universidad de Málaga 4 LESSON 4: THE COST CARRIES: CALCULATION METHODS Example: A Company manufactures two-size handbags, being the difference between them amount of skin incorporating: The Large bag incorporates double amount of skin than Small one. The total cost of the sewn for Bags ascended to 10,800€. Asked: Calculate the cost of Sewn that incorporates each bag. 𝑇𝑜𝑡𝑎𝑙 𝑆𝑒𝑤𝑛 𝐶𝑜𝑠𝑡 10.800€ 𝑈𝑛𝑖𝑡 𝐶𝑜𝑠𝑡 = = =?? 𝑇𝑜𝑡𝑎𝑙 𝑢𝑛𝑖𝑡𝑠 𝑝𝑟𝑜𝑑𝑢𝑐𝑒 600 + 600 Can be calculate with a Pure Division metohd? As they are not equal, we cannot add 600 large bags with 600 small bags. Therefore, we cannot apply the pure division method, tendWe will apply equivalences according to the following table: Equivalence Equivalence Equivalence Q Unit Cost coefficient quantity Cost Big Bag 600 2 1.200 6 12 €/q Small Bag 600 1 600 6 6 €/q 1.800 𝟏𝟎. 𝟖𝟎𝟎 𝑼𝒏𝒊𝒕 𝑬𝒒𝒖𝒊𝒗𝒂𝒍𝒆𝒏𝒄𝒆 𝑪𝒐𝒔𝒕 = = 𝟔 𝒆𝒖𝒓𝒐𝒔/𝑞 𝟏. 𝟖𝟎𝟎 If the difference between the bags does not reside in the incorporation of raw material (they are the same size) but in the processing time, that is, a bag carries the skin smooth and the other one carries silk-screened, therefore, each smooth bag takes to do it 40 minutes and each bag Printed 1 hour. In this case the equivalences would be: Equivalence Equivalence Equivalence Q Unit Cost coefficient quantity Cost 3 Printed Bag 600 1,800 3.60 10.80 (60 minutes) 2 Smooth Bag 600 1,200 3.60 7.20 (40 minutes) 3,000 MANAGEMENT ACCOUNTING Grado en Economía y Administración y Dirección de Empresas © Mariano Soler Porta - Dpto. Contabilidad y Gestión - Universidad de Málaga 5 LESSON 4: THE COST CARRIES: CALCULATION METHODS 𝟏𝟎. 𝟖𝟎𝟎 𝑼𝒏𝒊𝒕 𝑬𝒒𝒖𝒊𝒗𝒂𝒍𝒆𝒏𝒄𝒆 𝑪𝒐𝒔𝒕 = = 3.6 𝒆𝒖𝒓𝒐𝒔/𝑞 𝟑. 𝟎𝟎𝟎 If the difference between the bags does not lie in the incorporation of raw material (they are the same size) but in the processing time, that is, a bag carries the skin smooth and the other one carries silk-screened, also the information can be presented in another way : In every hour of production are made 1.5 plain bags and 1 silkscreened bag Equivalence Equivalence Equivalence Q Unit Cost coefficient quantity Cost Printed Bag 600 1.5 900 7.20 10.80 Smooth Bag 600 1 600 7.20 7.20 1.500 𝟏𝟎. 𝟖𝟎𝟎 𝑼𝒏𝒊𝒕 𝑬𝒒𝒖𝒊𝒗𝒂𝒍𝒆𝒏𝒄𝒆 𝑪𝒐𝒔𝒕 = = 7,20 𝒆𝒖𝒓𝒐𝒔/𝑞 𝟏. 𝟓𝟎𝟎 These calculations can also be applied when the treatment of each cost place is different, and then a method of equivalence by sections will be applied, applying equivalences for the distribution of the cost of each place. 4.3. SUPPLEMENT METHOD On the other hand, Supplement method Is Applicable to companies that obtain different products, obtained with uniform or not treatments, for which it is not possible to establish equivalences1 To apply this method it will be necessary, first of all, to separate the direct costs of the indirect ones. ✓ The direct costs are divided proportionately to the quantity of product obtained, through the method of division, obtaining the 1 The methods of division and equivalence are compatible with both organic and inorganic systems, however, they are often linked to the division, preferably to the organic and the supplements, to the inorganic. MANAGEMENT ACCOUNTING Grado en Economía y Administración y Dirección de Empresas © Mariano Soler Porta - Dpto. Contabilidad y Gestión - Universidad de Málaga 6 LESSON 4: THE COST CARRIES: CALCULATION METHODS direct cost by Q of product. They are directly incorporated into the carrier. ✓ Indirect costs are added to the unit direct cost through Supplement Method, which will be Cumulative or elective According to which indirect costs behave equally in relation to the same cost figure (raw material cost, direct labor cost or the sum of both, basic cost), or not. 4.3.1. CUMULATIVE SUPPLEMENT METHOD The Cumulative Supplements method is to calculate a Comprehensive supplement that integrates all indirect costs. This analyzes the proportion of the CI with respect to the total CD figure, with respect to the cost of materials or the figure of the labour cost and Adds a CI absorption supplement on the base of the proportion obtained over any of the three figures, and so shall be applied from one to other periods although they can change the proportions. Figure 4.4: Cumulative Supplements method Example: In a COM-SA that gets products A and B in the period X with the following cost figures: Budget Direct materials (M.D.) 10.000,00 € Direct Labour (M.O.D.) 5.000,00 € Indirect manufacturing costs (C.I.F.) 7.500,00 € Direct costs per unit for each type of product corresponding to the period are shown in the following table: MANAGEMENT ACCOUNTING Grado en Economía y Administración y Dirección de Empresas © Mariano Soler Porta - Dpto. Contabilidad y Gestión - Universidad de Málaga 7 LESSON 4: THE COST CARRIES: CALCULATION METHODS Unit costs Products M.D. M.O.D. A 100,00 € 50,00 € B 80,00 € 70,00 € Asked: Production unit cost calculation for products A and B, by aplying the method of cumulative supplements. In an inorganic cost system, it is necessary to distinguish between direct costs and indirect costs. The direct ones are incorporated at the cost of the products by "the Division method" and Indirect costs of manufacturing are incorporated to the product through the "Supplement method". In this case, we already give the unit costs of M.D. and M.O.D for each unit of each of the three products manufactured by the company, therefore, apply the method of supplements for absortion of C.I.F. To do this, in first, we'll calculate the supplements of The M.D., the M.O.D. and the total direct costs, on the C.I.F. figure, i.e. the percentage of each of these cost figures (M.D., M.O.D. and Total C.D.), on the figure of indirect costs. 7.500,00 Supplement C.I.F. over MD = = 0,75 = 75% 10.000,00 This Is, of each € of MD that incorporates the product, will be added 0.75€ of CIF 7.500,00 Supplement C.I.F. over MOD = = 1,5 = 150% 5.000,00 This Is, of each € of MOD that incorporates the product, will be added CIF 1.5€ 7.500,00 Supplement C.I.F. over CD = = 0,5 = 50% 15.000,00 This Is, of every € of CD incorporating the product, will be added CIF 0.5€ MANAGEMENT ACCOUNTING Grado en Economía y Administración y Dirección de Empresas © Mariano Soler Porta - Dpto. Contabilidad y Gestión - Universidad de Málaga 8 LESSON 4: THE COST CARRIES: CALCULATION METHODS Once we have calculated the three supplements that can be applied on unit costs of each one of the products, as shown in the following table: Product A B Direct Material Direct Labor Direct Costs Direct Material Direct Labor Direct Costs Supplement Supplement Supplement Supplement Supplement Supplement MD/q 100,00 100,00 100,00 80,00 80,00 80,00 MOD/q 50,00 50,00 50,00 70,00 70,00 70,00 75% MD = 150% MOD = 50% CD = 75% MD = 150% MOD = 50% CD = CIF/q 0,75x100 = 1,5x50 = 0,5x150 = 0,75x80 = 1,5x70 = 0,5x150 = 75,00 75,00 75,00 60,00 105,00 75,00 Unit Cost of 225,00 225,00 225,00 210,00 255,00 225,00 production In the event that, for all products the result of applying the different supplements to the direct unit costs would give the same unit cost of production (or cost of production/Q), as in the case of product A, the cumulative supplements method could be applied, and any of the three, on MD, on MOD or on the sum of all CDs could be taken, as the result would be the same. This occurs when the proportional behavior of all CIF on the different figures of MD, MOD and CD is the same. However, when this coincidence of results does not result, it is revealed the different proportional behavior of the different CIF figures (i.e. cost of repairs, amortization cost, electric energy cost, etc.). In this case be to apply the method of supplements Elective. 4.3.2. ELECTIVE SUPPLEMENT METHOD In the method of elective supplements exists different behaviors within CIF therefore, a single supplement is not calculated for the absorption of all CIF, but it will have to be independent between different classes according to their proportional behavior. To do this, it will be necessary to analyze these behaviors over several periods. In this way the problems of alteration of the proportions are avoided, however, it is usually used more the method of the cumulative supplements. MANAGEMENT ACCOUNTING Grado en Economía y Administración y Dirección de Empresas © Mariano Soler Porta - Dpto. Contabilidad y Gestión - Universidad de Málaga 9 LESSON 4: THE COST CARRIES: CALCULATION METHODS Figure 4.5: Elective Supplements method Example: The Company "S" is dedicated to obtaining the product X. In the present period “3”, has obtained 1.000 Q of product X and have been in the process of manufacturing 250 Q. The cost figures corresponding to the last three periods have been the following: Periods 1 2 3 Direct Materials 4,200,00 3.692.00 2,500.00 Direct Labor 10,170.00 6,190.00 9,200.00 CIF A 2.100.00 1.846.00 1,250.00 CIF B 2,034.00 1,238.00 1,840.00 CIF C 508.50 309.50 460.00 It is also known that a Q of product X is made from 4 units of materials and 2 times of treatment, however, a Q of product in progress X incorporates the same units of material that the product Finished X, but only half the time of transformation of this one. Asked: Calculate for the current period “3” the cost production unit for the finished product and the product that has been in progress, applying the method of elective supplements. This method applies to companies that use inorganic cost systems, in which we saw in the point 4.2, the unit production cost will be: 𝐏𝐫𝐨𝐝𝐮𝐜𝐭𝐢𝐨𝐧 𝐜𝐨𝐬𝐭 𝐃𝐢𝐫𝐞𝐜𝐭 𝐌𝐚𝐭𝐞𝐫𝐢𝐚𝐥 𝐂𝐨𝐬𝐭 𝐃𝐢𝐫𝐞𝐜𝐭 𝐋𝐚𝐛𝐨𝐫 𝐂𝐨𝐬𝐭 𝐂𝐈𝐅 = + + 𝐏𝐫𝐨𝐝𝐮𝐜𝐞𝐝 𝐔𝐧𝐢𝐭 (𝐐) 𝐏𝐫𝐨𝐝𝐮𝐜𝐞𝐝 𝐔𝐧𝐢𝐭 (𝐐) 𝐏𝐫𝐨𝐝𝐮𝐜𝐞𝐝 𝐔𝐧𝐢𝐭 (𝐐) 𝐏𝐫𝐨𝐝𝐮𝐜𝐞𝐝 𝐔𝐧𝐢𝐭 (𝐐) MANAGEMENT ACCOUNTING Grado en Economía y Administración y Dirección de Empresas © Mariano Soler Porta - Dpto. Contabilidad y Gestión - Universidad de Málaga 10 LESSON 4: THE COST CARRIES: CALCULATION METHODS In this case, first, we'll split the DirectCost / Q by the Division method, and then we'll apply elective supplements for the distribution of the CIF. To calculate the cost of the Direct materials by Q for the current period, we have to distribute it between the product X and the product in Course X'. For this, in the first place we will have to calculate the total amount of direct materials incorporated in the finished products and the products in progress: Products Q M.U./Q M.U. X 1.000 4 4.000 X’ 250 4 1.000 5.000 Once you have known the total units of Direct Materials incorporated in the production of the period, we will calculate the unit cost of the same: 2.500 Unit material Cost = 5.000 = 0,50€/𝑢𝑐𝑚 And then from the cost of MD/Q, and taking into account the number of MD units that incorporates each finished product X and each product in course X', we will obtain the unit cost of MD for each one of them: Products € / UM UM / Q €/Q X 0,50 4 2,00 X’ 0,50 4 2,00 Now we will have to calculate the cost of MOD for X and X', and is operated in the same way as with the MD's. First of all will have to calculate the total hours of treatment applied to all finished and ongoing production: Products Q hour / Q Hours X 1.000 2 2.000 X’ 250 1 250 2.250 Once we have known the total hours of MOD incorporated to the production of the period, we will calculate the unit cost of the same: MANAGEMENT ACCOUNTING Grado en Economía y Administración y Dirección de Empresas © Mariano Soler Porta - Dpto. Contabilidad y Gestión - Universidad de Málaga 11 LESSON 4: THE COST CARRIES: CALCULATION METHODS 9.200 Unit material Cost = = = 4,089€/ℎ 2.250 A Then, from the cost of MOD/hour and considering the number of hours of treatment that incorporates each finished product X and each product in Course X', we will obtain the unit cost of MOD for each one of them: Products €/hour hour / Q €/Q X 4,089 2 8,178 X’ 4,089 1 4,089 Once the direct costs have been distributed, we'll apply supplements Electives uipplement for the distribution of indirect costs. To do this, we will have to analyze the proportional behavior of each type of CIF with respect to the different figures of CD, over several periods of time, in this case 3. For CIF A: Period 1 Period 2 Period 3 Supplement 2.100 1.846 1.250 % over MD = 0,5 = 0,5 = 0,5 50 s/MD 4.200 3.692 2.500 For CIF B: Period 1 Period 2 Period 3 Supplement 2.034 1.238 1.840 is not proportional % over MD = 0,4842 = 0,3353 = 0,736 4.200 3.692 2.500 over MD 2.034 1.238 1.840 % over MOD = 0,20 = 0,20 = 0,20 20% s/ Mod 10.170 6.190 9.200 For CIF C: Period 1 Period 2 Period 3 Supplement 508,0 309,50 --- is not proportional % over MD = 0,1209 = 0,0838 4.200 3.692 over MD 508,50 309,50 460 % over MOD = 0,05 = 0,05 = 0,05 5 SMod 10.170 6.190 9.200 MANAGEMENT ACCOUNTING Grado en Economía y Administración y Dirección de Empresas © Mariano Soler Porta - Dpto. Contabilidad y Gestión - Universidad de Málaga 12 LESSON 4: THE COST CARRIES: CALCULATION METHODS Therefore, the production cost for the product X And the product in Course X': Concept Product X Product in Progress X’ Cost Md/Q 2,00 2,00 Cost MOD/Q 8,178 4,089 CIF A/Q (Supplement 50% s/MD) 50% of 2,00 = 1,00 50% of 2,00 = 1,00 CIF B/Q (Supplement 20% s/MOD) 20% of 8,178 = 1,636 20% of 4,089 = 0,818 CIF C/Q (Supplement 5% s/MOD) 5% of 8,178 = 0,409 5% of 4,089 = 0,204 Production cost/Q 13,223 8,111 MANAGEMENT ACCOUNTING Grado en Economía y Administración y Dirección de Empresas © Mariano Soler Porta - Dpto. Contabilidad y Gestión - Universidad de Málaga 13 MANAGEMENT ACCOUNTING Grado en Economía y Administración y Dirección de Empresas LESSON 4: THE COST CARRIES: CALCULATION METHODS PART 3: METHODS OF CALCULATING: JOINT PRODUCTION Departamento de Contabilidad y Gestión UNIVERSIDAD DE MÁLAGA LESSON 4: THE COST CARRIES: CALCULATION METHODS Versión 2.0 Septiembre de 2021 © Mariano Soler Porta MANAGEMENT ACCOUNTING Grado en Economía y Administración y Dirección de Empresas © Mariano Soler Porta - Dpto. Contabilidad y Gestión - Universidad de Málaga 2 LESSON 4: THE COST CARRIES: CALCULATION METHODS 5 CALCULATION METHODS FOR JOINT PRODUCTION Let's focus below in joint production because, unlike the other cases of composite production, it is not possible to apply, for certain stages of this type of production, the methods of calculation already studied. Within the joint production we can distinguish between: a. Joint production with by-products: The one where you get Main products and secondary products, as in the furniture industry that in addition to the different furniture you get sawdust, or manufacture of wheat flours, you get the bran. b. Joint production with co-products: The one in which several major products are obtained, such as the oil industry, or a livestock farm that obtains meat and leather, or, milk and wool. 5.1. BY-PRODUCT SOLD ON MARKET: SUBTRACTION METHOD The by-product sold on the market is understood as by-product as the concept of CMP residue. In this case the "Subtraction Method", which bases its reasoning that the profitability of the company can only be due to the main product, since the by-products do not constitute the object of the activity of the company, that is, the method of calculation tends to attribute all the profitability of the company to the main product in such a way that the profitability of the by- product is null. Two cases can be considered: 5.1.1. BY-PRODUCT SOLD ON MARKET AS OBTAINED Being “A” the main product and “S” The By-product: MANAGEMENT ACCOUNTING Grado en Economía y Administración y Dirección de Empresas © Mariano Soler Porta - Dpto. Contabilidad y Gestión - Universidad de Málaga 3 LESSON 4: THE COST CARRIES: CALCULATION METHODS K joint = KMD + KCC1 We have to spread this joint cost between A and S and we don't know how much corresponds to each one, then it has to be fulfilled: K joint = KA + KS = NA kA + NS kS As we are applying the " subtraction method", to cancel the profitability of the by- product we assign a value equivalent to your selling price ks= Psells by therefore, for the Total production of the by-product (Ns), we'll have to the By-Product production cost: KS = NS kS = NS PsellS is subtracted from the Production set Cost To get the Production cost of the main product: KA = Kjoint – KS and being KA = NA kA NA kA = Kjoint – KS 𝑲𝒋𝒐𝒊𝒏𝒕 – 𝑲𝑺 Clearing: kA = 𝑵𝑨 5.1.2. BY-PRODUCT SOLD ON MARKET WITH TREATMENT PRIOR TO SALE In this case, A is the main product And S the by-product that is sold in the market, but after the point of separation is obtained the main product A and Z, which is the semi-finished product S that, after the point of separation will be transformed into CC2, And you will get the by-product S, ready to sell. MANAGEMENT ACCOUNTING Grado en Economía y Administración y Dirección de Empresas © Mariano Soler Porta - Dpto. Contabilidad y Gestión - Universidad de Málaga 4 LESSON 4: THE COST CARRIES: CALCULATION METHODS Of Main product we get a quantity NA, Of By-Product Z, NZ, and the By-Product S, you get Ns, considering that not all the production of Z serves to obtain, only N’Z. So, in this case, the joint cost will be: Kjoint = KMD + KCC1 Being the separation point after the CC1, you must spread this joint cost between A and Z, Kjoint = KA + KZ = NA kA + NZ kZ The case of a by-product that is sold in the market, we must apply the “Method of Subtraction”, by means of which the cost of the by-product is equated to its selling price, however what is sold in the market (and therefore will have its selling price) is the by-product S and not the semi-finished Z which is not sold and therefore, it has no selling price to match its production cost. Therefore, kz can't be matched the selling price, because it is not sold, however, we may apply such equality with the S-product, kS= PsellS KS = NS kS = NS PventaS Have an equation with two unknowns, kA and kZ: Kjoint = NA kA + NZ kZ If we consider another equation that links the cost of the by-product S with the semi-finished Z: NS kS = N'Z kZ + KCC2 Replacing kS= PsellS 𝑵𝑺 𝑷𝑺𝒆𝒍𝒍𝒔 – 𝑲𝑪𝑪𝟐 Clearing: kZ = 𝑵𝒁 Once obtained kZ is replaced in Kjoint = NA kA + NZ kZ 𝑲𝒋𝒐𝒊𝒏𝒕 – 𝑵𝒁 𝒌𝒁 Clearing: kA = 𝑵𝑨 MANAGEMENT ACCOUNTING Grado en Economía y Administración y Dirección de Empresas © Mariano Soler Porta - Dpto. Contabilidad y Gestión - Universidad de Málaga 5 LESSON 4: THE COST CARRIES: CALCULATION METHODS 5.2. BY-PRODUCT USED AS FACTOR: RECOVERY METHOD The by-product used as a production FACTOR is understood by-product as the recoverable material. In this case the "Recovery Method", based on the principle that the use of the by-product implies a savings of factors, thus having to evaluate that by-product assigning the amount equivalent to the factor saved. E.g. The dowels or slats that come out of cutting the wood are used for drawers, ornaments, etc. of the furniture. We can distinguish two cases: 5.2.1. BY-PRODUCT USED AS FACTOR AS OBTAINED Being A The main product and S by-product: Kjoint = KMD + KCC1 We have to spread this joint cost between a and S and we do not know how much it corresponds to each one, then it has to be fulfilled: Kjoint = KA + KS= NA kA + NS kS As we are applying the "recovery method", the unit cost of the by-product is equal to the purchase price of the saved material. ks= PPurchase Material, therefore, for the Total production of the by-product (Ns), we'll have to the By-Product production cost: KS = NS kS = NS PPurchaseM is subtracted from the Production joint Cost to get the Production cost of the main product: KA = Kjoint - KS = Kjoint - NS PPurchaseM and being KA = NA kA NA kA = Kjoint - NS PPurchaseM MANAGEMENT ACCOUNTING Grado en Economía y Administración y Dirección de Empresas © Mariano Soler Porta - Dpto. Contabilidad y Gestión - Universidad de Málaga 6 LESSON 4: THE COST CARRIES: CALCULATION METHODS 𝑲𝒋𝒐𝒊𝒏𝒕 – 𝑵𝑺 𝑷𝒑𝒖𝒓𝒄𝒉𝒂𝒔𝒆𝑴 Clearing: kA = 𝑵𝑨 5.2.2. BY-PRODUCT USED AS FACTOR WITH TREATMENT PRIOR TO SALE In this case, A is the main product And S the By-product Reuse as a productive factor, but after the point of separation is obtained the main product A and Z, which is the semi-finished product S that, after the point of separation will be transformed into CC2, And you will get the by-product S, ready for reuse. Of Main product A get a quantity NA, of By-Product Z, NZ, and the By-Product S, get Ns, bearing in mind that not all the production of Z serves to get only NZ. So, in this case, the joint cost will be: Kjoint = KMD + KCC1 Being the separation point after the CC1, you have to spread this joint cost between A and Z, Kjoint = KA + KZ = NA kA + NZ kZ As it is the case of a by-product that is reused as raw material, we must apply the "Recovery method", which consists of Replace kByproduct with the price of purchase of the material, however what is re-used is the by-product S and not the semi-finished Z which does not recover directly, but after its transform in the S by-product, it has no price for acquisition to match their production cost. So, kz can't be matched with the price of acquisition, because it cannot be purchased on the market, however, we may apply such equality with S-product, kS= Q purchase of the material: KS = NS kS = NS PPurchase Material Have an equation with two unknowns, kA and kZ: MANAGEMENT ACCOUNTING Grado en Economía y Administración y Dirección de Empresas © Mariano Soler Porta - Dpto. Contabilidad y Gestión - Universidad de Málaga 7 LESSON 4: THE COST CARRIES: CALCULATION METHODS Kjoint = NA kA + NZ kZ If we consider another equation that links the cost of the by-product S with the semi-finished Z: NS kS = N'Z kZ + KCC2 Replacing kS= PPurchaseM 𝑵𝑺 𝑷𝑷𝒖𝒓𝒄𝒉𝒂𝒔𝒆𝑴 – 𝑲𝑪𝑪𝟐 Clearing: kZ = 𝑵𝒁 Once obtained kZ is replaced in Kjoint = NA kA + NZ kZ 𝑲𝒋𝒐𝒊𝒏𝒕 – 𝑵𝒁 𝒌𝒁 Clearing: kA = 𝑵𝑨 5.3. PRODUCTION CO-PRODUCTS: DISTRIBUTION METHOD The Joint production with co-products is solved by applying the "Distribution Method", that part of the basis of the equality of the profitability of the different products, therefore, to calculate the costs of the principal products will be made a proportion or equivalence. There are two cases: 5.3.1. CO-PRODUCTS SALES AS OBTAINED The coproducts are sold in the same state as they are obtained. A MD Cc1 B are obtained NA of A and NB of B. It is a question of sharing the cost as a function of the sale price, considering that the profitability of both major products will have to be equalized. Kjoint = KMD + KCC1 MANAGEMENT ACCOUNTING Grado en Economía y Administración y Dirección de Empresas © Mariano Soler Porta - Dpto. Contabilidad y Gestión - Universidad de Málaga 8 LESSON 4: THE COST CARRIES: CALCULATION METHODS It is solved by making a rule of three that relate the production costs and the corresponding revenues: Kjoint ----------------------- NA PvA + NB PvB X ----------------------- NA PvA Being the unknown the cost of production of a, in such a way that: 𝑲𝒋𝒐𝒊𝒏𝒕 ∗ 𝑵𝑨 𝑷𝒗𝑨 KA = 𝑵𝑨 𝑷𝒗𝑨 + 𝑵𝑩 𝑷𝒗𝑩 Knowing, on the other hand that: KA = NA kA, substituting in the previous expression, and clearing kA: 𝑲𝒋𝒐𝒊𝒏𝒕 ∗ 𝑵𝑨 𝑷𝒗𝑨 KA = NA kA = 𝑵𝑨 𝑷𝒗𝑨 + 𝑵𝑩 𝑷𝒗𝑩 𝑲𝒋𝒐𝒊𝒏𝒕 ∗ 𝑵𝑨 𝑷𝒗𝑨 𝑲𝒋𝒐𝒊𝒏𝒕 ∗ 𝑷𝒗𝑨 kA = = (𝑵𝑨 𝑷𝒗𝑨 + 𝑵𝑩 𝑷𝒗𝑩 ) 𝑵𝑨 𝑵𝑨 𝑷𝒗𝑨 + 𝑵𝑩 𝑷𝒗𝑩 And it would be the same for B. 5.3.2. CO-PRODUCTS WITH TREATMENT PRIOR TO SALE Coproductions requiring post-harvest treatment prior to sale. In this case, it is a question of sharing the cost of joint production between the semi-SA and semi-SB, but because the company does not sell them as such semi- processed, but transforms them into finished products A and B, we cannot use their selling price to make the proportion as in the previous case. We'll have to Predetermine A magnitude that makes the price of semi-finished. At this magnitude we're going to call it "Virtual Price", understanding the hypothetical price at which the company is indifferent to sell the semi-finished product or continue with its treatment until the finished product is obtained. MANAGEMENT ACCOUNTING Grado en Economía y Administración y Dirección de Empresas © Mariano Soler Porta - Dpto. Contabilidad y Gestión - Universidad de Málaga 9 LESSON 4: THE COST CARRIES: CALCULATION METHODS This is, bearing in mind that the profitability of the Semi-Product is the same, it should be fulfilled that: NSa PvirtualSa + KCC2 = NA PsellA NSb PvirtualSb + KCC3 = NB PsellB and clearing the virtual prices will serve to carry out the A in the previous case, instead of sales prices. B BIBLIOGRAPHY REFERENCES - REQUENA RODRÍGUEZ, J. M. Y VERA RÍOS, S. (2008). Contabilidad interna. Contabilidad de costes y de gestión. Barcelona: Ariel S.A. MANAGEMENT ACCOUNTING Grado en Economía y Administración y Dirección de Empresas © Mariano Soler Porta - Dpto. Contabilidad y Gestión - Universidad de Málaga 10