Asphalt Plant (MENG5383) Chapter 7 PDF
Document Details
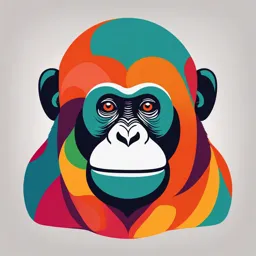
Uploaded by ResoundingCarnelian684
Ambo University
Tags
Summary
This document provides a detailed overview of asphalt plants, including their different types (batch and drum), components (cold feed system, dryer, mixer, etc.), and working principles. It also discusses reclaimed asphalt pavement (RAP) and addresses dust collection. The document appears to be lecture notes for a course on heavy duty and construction equipment.
Full Transcript
Ambo University 1 Department of Mechanical engineering HEAVY DUTY AND CONSTRUCTION EQUIPMENT MENG5383 Chapter 7 Asphalt Plant 2 Introduction Th...
Ambo University 1 Department of Mechanical engineering HEAVY DUTY AND CONSTRUCTION EQUIPMENT MENG5383 Chapter 7 Asphalt Plant 2 Introduction The purpose of an ashalt plant is to blend aggregate and asphalt cement together at an elevated temperature to produce a homogeneous asphalt paving mixture. The primary functions of an asphalt mixing plant are to: dry and heat the aggregate combine the aggregates, filler and binder in the correct proportions mix binder and aggregates discharge the mix in good condition for transport, placing and compaction 3 Types of asphalt plant There are two main types of asphalt mixing plants: 1. Batch 2. Drum i. parallel-flow drum mix, ii. counter-flow drum-mix 4 BATCH PLANT In the batch-type mixing plant, hot aggregate and asphalt are withdrawn in desired amounts to make up one batch for mixing. After thoroughly mixing, the material is discharged from the pugmill in one batch. The major components of a batch plant are the cold feed system, asphalt cement supply system, aggregate dryer, mixing tower, and emission-control system. 5 figure.: Major components of a batch plant. 6 7 COLD FEED SUPPLY Cold aggregate feed is the first major component of the batch- type asphalt concrete plant. usually fed by a crane with a clamshell bucket or a front-end loader. Figure: typical three bin cold feed System 8 There are several different types of cold feeders. Among the most common are: A. Continuous belt type B. Vibratory type 9 DRYER The dryer is a large rotating metal drum mounted at an angle and equipped with a gas or oil-heating unit at the lower end. Hot gases from the burner pass from the lower end of the rotating drum and out the upper end. Cold aggregate is feed into the upper end of the dryer and is picked up by steel angles or flights mounted on the inside of the unit. As the drum rotates, the aggregate is lifted up and dumped through hot gases. Figure - Typical Asphalt Plant Dryer 10 DUST COLLECTOR 11 Dried aggregates are generally transported from the dryer by a hot elevator and deposited onto a screening unit that is mounted over the plant bins. The function of hot screens is to accurately separate the aggregate into the specified sizes and deposits in to a hot bins. 12 Hot bins Hot bins are used to temporarily store heated and screened aggregate in the various size fractions required. Each bin should be large enough to prevent depletion of the material when the mixer is operating at full capacity. 13 Pug mill mixer A batch plant mixer consists of a mixing chamber, which is lined to reduce wear and two shafts with paddles. Asphalt is pumped into the mixer and sprayed over the aggregate through a spray bar. When the mixing is completed, a gate at the bottom of the mixer is opened and the completed mix drops into a truck. 14 Reclaimed asphalt pavement (RAP) If RAP is incorporated into the mix, it is placed in a separate cold-feed bin from which it is delivered to the plant. The RAP can be added to the new aggregate in one of three locations: the bottom of the hot elevator; the hot bins; or, most commonly, the weigh hopper 15 Working principle of batch plant The aggregate used in the mix is removed from stockpiles and placed in individual cold-feed bins. Aggregates of different sizes are proportioned out of their bins by a combination of the size of the opening of the gate at the bottom of each bin and the speed of the conveyor belt under the bin. Generally, a feeder belt beneath each bin deposits the aggregate on a gathering conveyor located under all of the cold- feed bins. 16 Working principle of batch plant The aggregate is transported by the gathering conveyor and transferred to a charging conveyor. The material on the charging conveyor is then carried up to the aggregate dryer. The aggregate is introduced into the dryer at the upper end and is moved down the drum by both the drum rotation (gravity flow) and the flight configuration inside the rotating dryer. 17 Working principle of batch plant The burner is located at the lower end of the dryer, and the exhaust gases from the combustion and drying process move toward the upper end of the dryer, against (counter to) the flow of the aggregate. As the aggregate is tumbled through the exhaust gases, the material is heated and dried. Moisture is removed and carried out of the dryer as part of the exhaust gas stream. The hot, dry aggregate is then discharged from the dryer at the lower end. 18 Working principle of batch plant The hot aggregate is usually transported to the top of the plant mixing tower by a bucket elevator. The heated, dried, and resized aggregate is held in the hot bins until being discharged from a gate at the bottom of each bin into a weigh hopper. The asphalt cement is pumped from its storage tank to a separate heated weigh bucket located on the tower just above the pugmill. 19 Working principle of batch plant When mixing has been completed, the gates on the bottom of the pugmill are opened, and the mix is discharged into the haul vehicle or into a conveying device that carries the mix to a silo from which trucks will be loaded. 20 Drum mix plant A drum mix plant It is simpler in design or operation than a batch plant. The mixing drum looks like the familiar dryer. The difference is that the aggregate is not only dried and heated within the drum, but also mixed with the asphalt cement. A drum mix plant has no screening unit or hot bins. Figure: Major components of a parallel-flow drum-mix plant. 21 22 The major components of a drum mix plant are: Cold Feed Asphalt supply system Drum mixer (which serves as both a dryer and a mixer) Surge or storage bin Dust control system 23 Cold feed bins The cold-feed bins are used to proportion the material to the plant. A variable-speed feeder belt is used under each bin. The amount of aggregate drawn from each bin can thus be controlled by both the size of the gate opening and the speed of the feeder belt to provide accurate delivery of the different-sized materials. The aggregate on each feeder belt is deposited onto a gathering conveyor that runs beneath all of the cold-feed bins. The combined material is normally passed through a scalping screen and then transferred to a charging conveyor for transport to the drum mixer. 24 Dryer - mixer The dryer-mixer looks very much like the dryer on a batch or continuous plant, but it has a dual purpose. It both dries the aggregate and mixes the asphalt with the aggregate Asphalt delivery system The asphalt metering system controls the rate at which the asphalt is added. The control system monitors the mass of the aggregate on the belt and the speed of the belt. 25 Reclaimed asphalt pavement (RAP) Reclaimed material may contain large amounts of pavement, so there is usually a crusher somewhere in the system. Reclaimed material could be fed into the plant with the new aggregate, but to avoid problems such as smoke, fire, and asphalt sticking to the bin walls, it is added elsewhere, usually at either the midpoint or the far end of the dryer. This allows the reclaimed material to be heated without coming into direct contact with the dryer flame 26 Dust collector The same type of emission-control equipment is used on the drum-mix plant as on the batch plant. A primary dry collector and either a wet scrubber system or a baghouse secondary collector can be used. Surge silo A storage silo is used to store a bituminous mixture before it is loaded on to the trucks. 27 Working principle of drum mix plant T he aggregate has entered the drum mixer from the cold feed bins. In the early heating phase, surface and free moisture begin to leave the aggregate as temperature rises. As mix temperature reaches between at the maximum mixing temperature asphalt is introduced to the mix. The aggregate has been coated, and mix temperatures will continue to rise until desired temperature is reached. After the mix temperature has been achieved, the mix is discharged into a hot incline elevator that carries the mix to either a surge silo or storage tank