Inventory Management Basics PDF
Document Details
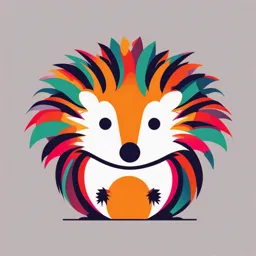
Uploaded by SelfSufficiencyLandArt334
Anju Mathew
Tags
Summary
This document provides a comprehensive overview of inventory management, covering key concepts such as Economic Order Quantity (EOQ), safety stock, and reorder points. It also covers various types of inventory, challenges, and techniques. The document is aimed to provide a basic understanding of these inventory management concepts.
Full Transcript
INVENTORY MANAGEMENT BASICS ANJU MATHEW ASSISTANT PROFESSOR We are exploring………. 1. Inventory: Meaning 2. Types of inventory 3. Economic Order Quantity (EOQ) 4. EOQ formula and calculations 5. Safety stock: Meaning, importance 6. Factors affecting safety stock 7....
INVENTORY MANAGEMENT BASICS ANJU MATHEW ASSISTANT PROFESSOR We are exploring………. 1. Inventory: Meaning 2. Types of inventory 3. Economic Order Quantity (EOQ) 4. EOQ formula and calculations 5. Safety stock: Meaning, importance 6. Factors affecting safety stock 7. Reorder point: Meaning, importance. What we expect………. Understand the concept of Inventory management, including types, EOQ, safety stock, and reorder points. They will be able to apply these concepts to optimize inventory levels, minimize costs, and improve business efficiency. INVENTORY can be defined as the tangible assets a company holds for the purpose of sale or use in production. It encompasses raw materials, work-in- progress goods, and finished goods ready for distribution. TYPES OF INVENTORY Raw materials Work-in-progress Finished goods Maintenance, repair, and operating (MRO) supplies Obsolete Inventory Example Raw materials Wood for furniture manufacturing Cotton for textile production Steel for automobile manufacturing Flour for a bakery Work-in-progress A partially assembled car on an assembly line A loaf of bread halfway through baking A dress with the fabric cut but not yet sewn Finished goods Cars in a dealership's showroom Loaves of bread on a bakery shelf Dresses hanging in a clothing store Maintenance, repair, and operating (MRO) supplies Obsolete Inventory Last year's fashion items Products replaced by newer models Inventory damaged or expired INVENTORY MANAGEMENT Inventory management is the process of efficiently overseeing and controlling a company's inventory of goods or products. It involves every stage in the product lifecycle, from procurement to storage and eventual sale. GOALS OF INVENTORY MANAGEMENT Minimize costs (Holding, Ordering and Stockout cost) Improving order fulfilment Improving inventory turnover Reduce wastage and obsolescence CHALLENGES IN INVENTORY MANAGEMENT Forecasting Demand Lead Time Variability Hidden Cost Product Obsolescence Space Constrains Inventory Management Techniques 1. Economic Order Quantity (EOQ) 2. Safety Stock 3. Reorder Point Economic Order Quantity (EOQ) It refers to the ideal order quantity that minimizes the total cost of inventory, which includes both ordering costs and holding costs. ORDERING COSTS HOLDING COSTS These are the costs associated These are the costs associated with placing an order with storing inventory Order processing fees Storage space costs (rent, utilities) Shipping and handling charges Insurance and taxes on inventory Administrative costs ASSUMPTIONS OF EOQ METHOD 1. Constant Demand 2. Constant Ordering Costs 3. Constant Holding Costs 4. Instantaneous Replenishment 5. No Quantity Discounts 6. Independent Demand 2𝐴𝐵 EOQ = 𝐶∗𝑆 A = Annual Consumption B = Buying cost per order C = Cost per unit S = Storage and Carrying cost (if it is given in % apply on cost of the material) 1. Calculate EOQ Annual usage = 90000 units Buying cost per order = Rs. 10 Cost of carrying inventory = 10% of cost Cost per unit = Rs. 50 2𝐴𝐵 Answer EOQ = 𝐶∗𝑆 A = 90000 units B = Rs. 10 C = R. 50 S = 10% EOQ = √2*90000*10 / 50* 10% 1800000 = 5 =√360000 = 600 Units Practice 1. From the following information, calculate Economic Order Quantity and the number of orders to be placed in one quarter of the year. Quarterly consumption of materials = 2000 Kg Cost of placing one order = Rs. 50 Cost per unit = Rs. 40 Storage and carrying cost = 8% of average inventory Answer 2𝐴𝐵 EOQ = 𝐶∗𝑆 A = 2000 * 4 = 8000 EOQ = √2*8000*50 / 40* 8% 800000 = 3.2 =√250000 = 500 Kgs 2. A Company manufactured 5000 units of a product per month. Cost of placing an order is Rs.100. The purchase price of raw material is Rs. 10 per kg. The re-order period is 4 to 8 weeks. The consumption of raw materials varies from 100 kg to 450 kg per week, the average consumption being 275 kg; the carrying cost of inventory is 20% per annum. Calculate EOQ Answer 2𝐴𝐵 EOQ = 𝐶∗𝑆 A= 275 * 52 = 14300 EOQ = √2*14300*100 / 10* 20% 2860000 = 2 =√1430000 = 1195.82 3. A Company uses 2500 units of a material per month. Cost of placing an order is Rs. 150. The cost per unit is Rs. 20. The re- order period is 4 to 8 weeks. The minimum consumption of raw material is 100 units whereas the average consumption is 275 units. The carrying cost of inventory is 20% per annum. Answer 2𝐴𝐵 EOQ = 𝐶∗𝑆 A = 2500 * 12 = 30000 EOQ = √2*30000*150 / 20* 20% 9000000 = 4 =√2250000 = 1500 Kgs Safety stock is the extra inventory a business keeps on hand to protect itself from unexpected fluctuations in demand or supply. It acts as a buffer, ensuring that you can meet customer needs even when things don't go exactly as planned. 1. Protection against demand spikes 2. Buffer stock for longer lead times 3. Prevention against price fluctuations Factors affecting safety stock Demand Variability Lead Time Variability Service Level How to maintain safety stock Accurate Demand Forecasting Lead Time Forecasting Regular Inventory Review Use Inventory Management Tools Build Strong Supplier Relationship Identify Potential Risk (economic, supply chain, natural disaster) Identify the possibility of Implementing JIT (Just In Time) method Service Level Agreement Regular Audit Cross Functional Collaboration (marketing, sales, procurement) Inaccuracy in demand Unpredictable Lead time forecasting Safety Stock - Challenges Excessive Holding cost Supply chain disruption Data collection Outdated technology challenges Safety Stock - Challenges Incorrect calculation Poor decision making The Reorder Point (ROP) is an inventory management metric that signifies the inventory level at which a new order for a specific product should be placed to ensure continuous supply and prevent stockouts. Activity – Find out how local shops are maintaining safety stock.