Introduction To Maintenance PDF
Document Details
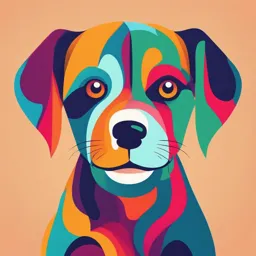
Uploaded by AdvantageousArlington7241
Tags
Summary
This document provides an introduction to maintenance, covering various aspects such as different types of maintenance, problems and objectives. It also explores the importance of maintenance and different aspects of scheduled maintenance.
Full Transcript
INTRODUCTION TO MAINTENANCE INTRODUCTION Plant maintenance is an Important service function of an efficient production system. It helpsin maintaining and increasing the operational efficiency of plant facilities. Maintenance is the procedure of finding...
INTRODUCTION TO MAINTENANCE INTRODUCTION Plant maintenance is an Important service function of an efficient production system. It helpsin maintaining and increasing the operational efficiency of plant facilities. Maintenance is the procedure of finding the faults in any equipment/Machine and also removal of fault. I t may be before the breakdown or after the breakdown. Plant maintenance usually refers to the methods, strategies, and practices used to keep an industrial factory running efficiently. This can include anything from regular checks of equipment to make sure they are functioning properly. The general aim of plant maintenance is to create a productive working environment that is also safe for workers. FAILURE Failure – inability to produce work in appropriate manner Equipment / machine failure on production floor – worn out bearing, pump, pressure leaks, broken shaft, overheated machine etc. Equipment failure in office – failure of power supply, air-conditioned system, computer network, photocopy machine Vehicle failure – brake, transmission, engine, cooling system MAINTENANCE IN SERVICE INDUSTRY Hospital Restaurants Transport companies Banks Hotels and resorts Shopping malls / retail Gas station MAINTENANCE IN MANUFACTURING COMPANIES Electronic Automotive Petrochemicals Refinery Furniture Ceramics Food and beverages OBJECTIVES Minimize loss of productive time Minimize repair time & cost Keep productive assets in working condition Minimize accidents Minimize total maintenance cost Improve quality of products IMPORTANCE Dependability of service Assured quality Prevent equipment failure Cost control Huge investment in equipment PROBLEMS IN MAINTENANCE Lack of management attention to maintenance Little participation by accounting in analyzing and reporting costs Difficulties in applying quantitative analysis Difficulties in obtaining time and cost estimates for maintenance works Difficulties in measuring performance PROBLEMS EXIST DUE TO Failure to develop written objectives and policy Inadequate budgetary control Inadequate control procedures for work order, service requests etc. Infrequent use of standards To control maintenance work Absence of cost reports to aid maintenance planning and control system MAINTENANCE OBJECTIVES Must be consistent with the goals of production (cost, quality, delivery, safety) Must be comprehensive and include specific responsibilities MAINTENANCE COSTS Cost to replace or repair Losses of output Delayed shipment Scrap and rework AREAS OF MAINTENANCE 1. Civil maintenance- Building construction and maintenance, maintaining service facilities 2. Mechanical Maintenance- Maintaining machines and equipments, transport vehicles, compressors and furnaces. 3. Electrical Maintenance- Maintaining electrical equipments such as generators, transformer, motors, telephone systems, lighting, fans, etc. NATURE OF MAINTENANCE PROBLEM GENERAL CLASSIFICATION MAINTENANCE PROBLEM Mechanical Failure Worn out bushes and bearings and other moving parts. Fatigue of machine members Creep of material at high temp Excessive forced vibration, misalignments etc. Thermal Failure Overheating of the component Lack of lubrication Inadequate of cooling Electrical insulation failure Chemical Failure Highly corrosive fluids containing abrasive particles Failure of protective linings like glass , rubber etc. CLASSIFICATION MAINTENANCE PROBLEM BASED ON TIME SPAN Short run production problem Maintenance problem which are carried out in a sort period of time are known as short run production system. It may be hourly, daily ,weekly and monthly. Example:- Hourly- inspection of correct lubricant, level of coolant, sharpness of cutting tool. Daily- cleaning of m/c, tightening of nuts, correct cooling, inspection of various indicators, minor adjustment of parts. Weekly- Major adjustment, lubrication, tightening of parts. Monthly- checking for insulation, corrosion, safety guards, TYPES OF MAINTENANCE Breakdown maintenance or corrective maintenance Preventive maintenance Predictive maintenance Routine maintenance Planned/Scheduled maintenance BREAKDOWN MAINTENANCE Occurs when there is a work stoppage due to machine breakdown Maintenance becomes repair work Seeks to get the equipment back into operation as quickly as possible To control the investment in replacement spare machines. DISADVANTAGES OF CORRECTIVE MAINTENANCE Breakdown generally occurs inappropriate times leading to poor and hurried maintenance Excessive delay in production & reduces output Faster plant deterioration Increases chances of accidents and less safety for both workers and machines More spoilt materials Direct loss of profit Can not be employed for equipments regulated by statutory provisions e.g. cranes, lift and hoists etc PREVENTIVE MAINTENANCE (PM) Principle – “Prevention is better than cure” Procedure - Stitch-in-time It locates weak spots of machinery and equipments provides them periodic/scheduled inspections and minor repairs to reduce the danger of unanticipated breakdowns Preventive management It is undertaken before the need arises and aims to minimize the possibility of un -anticipated production interruption or major breakdowns ADVANTAGES OF PM Advantages: Reduces break down and thereby down time Lass odd-time repair and reduces over time of crews Greater safety of workers Lower maintenance and repair costs Less stand-by equipments and spare parts Better product quality and fewer reworks and scraps Increases plant life Increases chances to get production incentive bonus PREDICTIVE (CONDITION-BASED) MAINTENANCE In predictive maintenance, machinery conditions are periodically monitored and this enables the maintenance crews to take timely actions, such as machine adjustment, repair or overhaul It makes use of human sense and other sensitive instruments, such as audio gauge, vibration analyzer, amplitude meter, pressure, temperature and resistance strain gauges etc. PREDICTIVE MAINTENANCE (CONTD.) Unusual sounds coming out of a rotating equipment predicts a trouble An excessively hot electric cable predicts a trouble Simple hand touch can point out many unusual equipment conditions and thus predicts a trouble ROUTINE MAINTENANCE this includes activities such as periodic inspection, cleaning, lubrication and repair of production equipments after their service life. SCHEDULED MAINTENANCE Scheduled maintenance is a stitch-in-time procedure and incorporates inspection lubrication repair and overhaul of equipments If neglected can result in breakdown Generally followed for: overhauling of machines changing of heavy equipment oils cleaning of water and other tanks etc. CONTROL OF MAINTENANCE 1. Authorized by an official 2. Maintenance schedule 3. Issue materials against proper authorization 4. Maintenance budgets 5. Equipment records MAINTENANCE SCHEDULING: Scheduling refers to timing and sequences of operations. It is an important segment of the production planning & control activity as well as the service operations like plant maintenance IMPORTANCE OF SCHEDULING: Facilitates optimum use of highly paid maintenance staff Equipments can be utilized effectively Eliminates undue interruptions in the production flow Eliminates chances of sudden breakdown Facilitates proper sequence in maintenance service TOTAL PRODUCTIVE MAINTENANCE (TPM) Tot a l productive maintenance (TPM) originated in Japan in 1971 as a method for improved machine availability through better utilization of maintenance and production resources I t can be considered as the medical science of machines. Tot a l Productive Maintenance (TPM) is a maintenance program which involves a newly defined concept for maintaining plants and equipment. T h e goal of the TPM program is to markedly increase production while, at the same time, increasing employee morale and job satisfaction. TPM brings maintenance into focus as a necessary and vitally important part of the business. It is no longer regarded as a non- profit activity. Down time for maintenance is scheduled as a part of the manufacturing day and, in some cases, as an integral part of the manufacturing process. The goal is to hold emergency and unscheduled maintenance to a WHY TPM T P M was introduced to achieve the following objectives. Avoid wastage in a quickly changing economic environment. Producing goods without reducing product quality. Reduce cost. Produce a low batch quantity at the earliest possible time. Goods send to the customers must be non defective.