Industrial Pharmacy Lec 4 PDF
Document Details
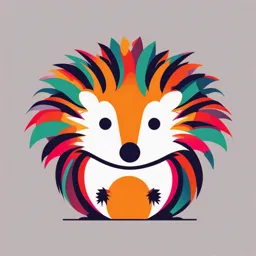
Uploaded by EntrancedAstronomy
College of Pharmacy
2023
Mohammed A Albarki, PhD
Tags
Summary
This document covers the topic of tablet coating in industrial pharmacy. It discusses the principles, processes, and evaluations related to the subject. The document was created by Mohammed A Albarki, PhD and is for a 4th stage course at a department of pharmacy.
Full Transcript
Lec 4:Tablet Coating MUC- Pharmacy Department- Industrial Pharmacy I- 4th stage. – Spring 2023 Mohammed A Albarki, PhD 1 Tablet Coating Tablet coating is adapted from the food preservation process. The first air suspension coater...
Lec 4:Tablet Coating MUC- Pharmacy Department- Industrial Pharmacy I- 4th stage. – Spring 2023 Mohammed A Albarki, PhD 1 Tablet Coating Tablet coating is adapted from the food preservation process. The first air suspension coater was created by Dr. Dale Wurster in 1950. He introduced airflow in the tablet coating machine and the perforated coating pans. His work resulted in the first reproducible and uniform tablet coating. 2 College of Pharmacy- Industrial Pharmacy II- 5th stage- First Semester Tablet Coating Tablet Coating Principles Tablet coating is an additional step that increases cost; therefore, the decision to coat a tablet is usually based on one or more of the following reasons: 1. To minimize undesirable taste, odor, or color of the drug. 2. To provide physical and chemical protection for the drug. 3. To control the release of the drug from the tablet. 4. To protect the drug from the gastric environment of the stomach with an acid- resistant enteric coating. 5. To improve the pharmaceutical elegance by use of special colors and contrasting printing. 6. To assist tablet movement and mobility, especially for patients with dysphagia while swallowing. 3 College of Pharmacy- Industrial Pharmacy II- 5th stage- First Semester Tablet Coating Tablet Coating Process 4 College of Pharmacy- Industrial Pharmacy II- 5th stage- First Semester Tablet Coating Tablet Coating Three main parts in studying tablet coating: Tablet Properties Coating compositions Coating Process Ideal Tablet Shape for Non-Enteric Coating Coating Equipment coating Materials Tablet physical properties Enteric Coating Coating Process Materials Solvents Sugar Coating Plasticizers Film Coating Colorants Evaluation of Film and Film defects Opaquants 5 College of Pharmacy- Industrial Pharmacy II- 5th stage- First Semester Tablet Coating Preferred Tablet Properties for Coating 1. Tablets must possess the proper physical characteristics: To withstand the intense mechanical stress that results from striking other tablets and the walls of the coating machine, the tablet must be strong enough to resist abrasion and chipping. 2. Tablet shape should be intact and free of imperfections: 3. Tablet surfaces that are brittle, soften in the presence of heat, or affected by the coating compositions tend to become rough in the early phase of the coating process and are unacceptable for film coating. 6 College of Pharmacy- Industrial Pharmacy II- 5th stage- First Semester Tablet Coating Preferred Tablet Properties for Coating 4. The physical shape of the tablet is important. The coating includes covering the tablet with a tacky polymeric material that before becoming completely dry will form tacky semisolid and eventually to a nontacky dry surface. So, tablets need constant movement inside the coating machine, or tablet agglomeration can occur. The ideal tablet shape for coating is the sphere which allows the tablet to roll freely in the coating pan with minimal tablet-to-tablet contact. 7 College of Pharmacy- Industrial Pharmacy II- 5th stage- First Semester Tablet Coating Preferred Tablet Properties for Coating The worst shape is a square flat-faced tablet in which coating materials would collet between the surfaces to glue them together. That’s why coated tablets usually have round surfaces. 5. Tablet surface hydrophobicity/hydrophilicity should match that of the coating materials. Coating materials must wet the tablet surface. For this reason, surfactant may be added to the coating solution. 8 College of Pharmacy- Industrial Pharmacy II- 5th stage- First Semester Tablet Coating Coating Compositions Coating material can form a physical deposition on the surface of the tablet such as sugar and wax coating. Coating materials should have the following properties: 1. Soluble in solvent for coating preparation. 2. Able to produce elegant-looking products. 3. Stability in the presence of heat, light, moisture, air, and the substrate being coated. Film properties should not change with aging. 9 College of Pharmacy- Industrial Pharmacy II- 5th stage- First Semester Tablet Coating Coating Compositions 4. Essentially no taste, odor, or color. 5. Compatibility with common coating solution additives. 6. Nontoxic and pharmacologically inert. 7. Should not tend to bridge/fill the debossed tablet surfaces. 8. Resistance to cracking. Note: No coating material fulfills all requirements of an ideal coating material. 10 College of Pharmacy- Industrial Pharmacy II- 5th stage- First Semester Tablet Coating Coating Compositions: Film Forming Materials Polymers are used to form the film around the tablet. Can be classified into non-enteric and enteric materials. Examples: Non-enteric Materials: these materials tend to solubilize inside the GI tract and release the drug. a. Hydroxypropyl methylcellulose (HPMC). b. Ethyl Cellulose (EC). Enteric materials: these materials tend to solubilize depending on the pH of the GI tract. a. Hydroxypropyl Methyl Cellulose Phthalate (HPMCP). b. Cellulose Acetate Phthalate. c. Acrylate Polymers. 11 College of Pharmacy- Industrial Pharmacy II- 5th stage- First Semester Tablet Coating Non enteric Materials (Non Functional FC) Hydroxypropyl methylcellulose (HPMC): Available in different viscosity grades. This polymer is the material of choice for air suspension and pan-spray coating systems. It is close to be an ideal coating polymer for film coating. The reasons for that are: 1. Solubility of the polymer in organic and aqueous solvents. 2. Noninterference with tablet disintegration and drug availability. 3. Flexibility (chip resistance) and absence of taste and odor. 4. Stability in the presence of heat, light, air and moisture. 5. Ability to incorporate color and other additives into the film without difficulty. 12 College of Pharmacy- Industrial Pharmacy II- 5th stage- First Semester Tablet Coating Hydroxypropyl methylcellulose (HPMC): Non Ideal properties: When used alone it tend to bridge and fill debossed tablet surfaces. That is why its usually incorporated in a mixture with other polymer or plasticizers to eliminate bridging or filling problem. 13 College of Pharmacy- Industrial Pharmacy II- 5th stage- First Semester Tablet Coating Non enteric Materials (Non Functional FC) Ethyl Cellulose (EC): This material is completely insoluble in water and gastrointestinal fluids and thus cannot be used alone for tablet coating. It is usually combined with water-soluble polymers, e.g., HPMC, to prepare films with reduced water solubility. Advantages: The polymer is soluble in various organic solvents and is nontoxic, colorless, odorless, tasteless, and quite stable to most environmental conditions. Disadvantages: EC without plasticizers tend to be brittle. 14 College of Pharmacy- Industrial Pharmacy II- 5th stage- First Semester Tablet Coating Enteric Materials The most important reasons for enteric coating are: 1. To protect the drug from the stomach, e.g., enzymes and certain antibiotics. 2. To protect the stomach from the drug, e.g., salicylates. 3. To deliver drugs optimally absorbed in the small intestine to their primary absorption site in their most concentrated form. 4. To provide a delayed-release component for repeat- action tablets. 15 College of Pharmacy- Industrial Pharmacy II- 5th stage- First Semester Tablet Coating Enteric Materials Ideal enteric coating material should have the following properties: 1. Resistance to gastric fluids. 2. Ready susceptibility or permeability to intestinal fluids. 3. Compatibility with the most coating solution component and the drug substrates. 4. Stability alone and in coating solutions. 5. Formation of a continuous (uninterrupted) film. 6. No toxicity. 7. Reasonable cost. 8. Ease of application without specialized equipment. 16 College of Pharmacy- Industrial Pharmacy II- 5th stage- First Semester Tablet Coating Enteric Materials (mechanism) The pH of the stomach varies from 1-5. Enteric materials are either (mechanism of action): 1. water-resistance è digested or emulsified by intestinal juices. 2. pH-sensitive materials. slowly swell and fall apart when solvated or become permeable near and above pH 5. Usually, the enteric formulation is a combination of the enteric technique above to achieve the desired action. Because all available enteric material falls short in some aspects. 17 College of Pharmacy- Industrial Pharmacy II- 5th stage- First Semester Tablet Coating Challenges for Enteric Coated Tablet All enteric-coated tablets must pass the USP disintegration test where the tablet has to stay intact for at least 1 hour and disintegrate within 2 hours (for most tablets). Passing the test does not mean guaranteeing optimal bioavailability. Several other challenges will face enteric coated tablets inside the body: 1. The pH of the stomach varies from 1-5. Some patients are having achlorhydria or hypochlorhydria. 2. The amount of gastric fluids may vary between individuals; and for the same individual from time to time. 18 College of Pharmacy- Industrial Pharmacy II- 5th stage- First Semester Tablet Coating Challenges for Enteric coated tablet 3. USP test does not require testing the drug amount in solution during the disintegration test. In some cases, the drug can escape before tablet breakage so the tablet will pass the USP test but may fail to protect the GI tract. 4. Some enteric-coated techniques use retardant polymer which depends on hydrophobicity and is not pH dependent. In this case, the polymer needs time to solubilize and allow the drug to release so if the tablet travels so fast in the GI tract it may not have enough time to solubilize and the tablet will fail to release its contents. 19 College of Pharmacy- Industrial Pharmacy II- 5th stage- First Semester Tablet Coating Coating Compositions: Enteric Materials Cellulose Acetate Phthalate (CAP): It has been used widely in the industry. Disadvantage Dissolving only above pH 6 and possibly delaying the absorption of drugs. It is also hygroscopic and relatively permeable to moisture and gastric fluids. There may be a premature release of some drugs. CAP films are brittle and require some adjuvants to achieve better film. 20 College of Pharmacy- Industrial Pharmacy II- 5th stage- First Semester Tablet Coating Enteric Materials Acrylate polymers (Eudragit): These polymers produce films that are resistant to gastric fluid and are soluble in GIT fluid at pH 6-7. Hydroxy Propyl Methyl Cellulose Phthalate (HPMCP): These polymers dissolve at a lower pH (pH 5-5.5) and this solubility may result in higher bioavailability of some drugs. 21 College of Pharmacy- Industrial Pharmacy II- 5th stage- First Semester Tablet Coating Coating Compositions: Solvents To dissolve or disperse polymer and other additives. Ideal solvent: 1. It Should dissolve or disperse the polymer system. 2. It should easily disperse other coating solution components into the solvent system. 3. Small concentrations of polymers (2 to 10 %) should not result in an extremely viscous solution, which will create coating problems. 4. It should be colorless, tasteless, odorless, inexpensive, non-toxic, inert, and nonflammable. 5. It should have a rapid drying rate. 6. It should have no environmental impact. 22 College of Pharmacy- Industrial Pharmacy II- 5th stage- First Semester Tablet Coating Solvents The most widely used solvents (either alone or in combination) are water, ethanol, chloroform, and acetone. Because of environmental and economic considerations, water is the solvent of choice; however, several polymers cannot be applied as aqueous solutions. 23 College of Pharmacy- Industrial Pharmacy II- 5th stage- First Semester Tablet Coating Coating Compositions: Plasticizers A plasticizer is a non-volatile material that when incorporated with the film former, improves the flexibility and adhesion properties of the resulting film. Without a plasticizer, most of the polymers tend to pack together in a rigid three-dimensional honeycomb arrangement. When used in the correct proportion, the plasticizers impart flexibility to the polymer by decreasing their molecular rigidity. A combination of plasticizers may be needed to achieve the desired effect. The concentration of the plasticizer(s) depends on many factors including the polymer type method of application, and the manufacture’s recommendation. 24 College of Pharmacy- Industrial Pharmacy II- 5th stage- First Semester Tablet Coating Coating Compositions: Plasticizers Recommended levels of plasticizers can range from 1-50% w/w of the film former. Some of the commonly used plasticizers are castor oil, glycerin, low molecular weight polyethylene glycol (PEG) (200-400 series), Tweens, and Spans. In aqueous coating, water-soluble plasticizers, e.g., PEG are used. Conversely, castor oil and Spans are used primarily for organic coating solutions. 25 College of Pharmacy- Industrial Pharmacy II- 5th stage- First Semester Tablet Coating Coating Compositions: Colorants They may be soluble in the solvent or suspended as insoluble powders. Lakes pigments have become the colorants of choice for sugar or film coating systems, as more reproducible colors are achieved. Lakes pigments will produce a more evenly distributed color every time. 26 College of Pharmacy- Industrial Pharmacy II- 5th stage- First Semester Tablet Coating Coating Compositions: Opaquants These are very fine inorganic powders used in the coating solutions to provide more pastel colors and increase film coverage. These opaquants can provide a white coating or mask the color of the tablet core. Colorants are much more expensive than opaquants and less colorant is required when opaquants are used. The most commonly used material for this purpose is titanium dioxide. 27 College of Pharmacy- Industrial Pharmacy II- 5th stage- First Semester Tablet Coating Coating Process Tablet coating is the application of coating materials to moving tablets with the concurrent use of heated air to facilitate the evaporation of the solvent. 1. The distribution of the coating materials is done by the continuous movement of the tablets in the coating pan. During the coating process, the tablets move through an application zone (in front of the nozzle) in which a portion of the tablets receive some of the coating materials. 2. With the help of hot air, the tablets are mostly in the drying phase and are recycled repeatedly through the application zone until the desired coat is achieved. 28 College of Pharmacy- Industrial Pharmacy II- 5th stage- First Semester Tablet Coating Coating Equipment 1- Conventional Pan System It consists of a spherical pan mounted angularly on a stand. The pan is rotated by a motor. Heated air is directed into the tablet bed and is exhausted by means of ducts. The coating materials (solution) are applied to the tablets by either ladling or spraying on the rotating tablets. Using spraying is preferred because: a) It is faster. b) Distributes the coating materials more evenly. c) Reduces the drying time. 30 College of Pharmacy- Industrial Pharmacy II- 5th stage- First Semester Tablet Coating 2- Perforated Pan System It is the most widely used machine in tablet coating. It consists of a perforated drum that rotates in a closed chamber. Drying air is passed through the tablets and is exhausted through perforations in the drum. Perforated pan coaters are efficient with high coating capacity and can be automated completely for both the sugar and film coating processes. The coating solution is applied to the surface of the rotating bed of tablets through spraying nozzles that are positioned inside the drum. https://youtu.be/SXEduweiViw 31 College of Pharmacy- Industrial Pharmacy II- 5th stage- First Semester Tablet Coating Types of Coating & Processing Sugar Coating It was commonly used in the past, although it may be used nowadays due to the excellent appearance it gives to tablets. The sugar coating involves several steps, the duration of which ranges from a few hours to several days. è needs time A successful product greatly depends on the skill of the operator. This is especially true in the pan-ladling method in which the coating solution is poured over the tablets. 33 College of Pharmacy- Industrial Pharmacy II- 5th stage- First Semester Tablet Coating Sugar Coating The sugar-coating process involves the following steps: sealing, sub-coating, syruping (smoothing), finishing and polishing. Sealing (Seal Coating): To prevent moisture penetration into the tablet core, a sealing coat is applied. Without a sealing coat, the overwetted tablets would absorb excess moisture, leading to tablet softening or disintegration and affecting the physical and chemical stability of the finished product. 34 College of Pharmacy- Industrial Pharmacy II- 5th stage- First Semester Tablet Coating Sugar Coating Process: Seal Coating Shellac is an effective sealing agent, but tablet disintegration and dissolution times may prolong upon aging because of the polymerization of the shellac. Original Tablet Zein is another material that has been used as an effective sealing agent. Prolongation of dissolution times has not been reported for zein on aging. Sealed Tablet 35 College of Pharmacy- Industrial Pharmacy II- 5th stage- First Semester Tablet Coating Sugar Coating Process: Subcoating The subcoating is applied to round the edges and build up the tablet size. Sugar coating can increase the tablet weight by 50- 100%. The subcoating step consists of applying a sticky binder solution (e.g. gelatin or sugar solution) to the tablets followed by a dusting of a subcoating powder (e.g. talc powder) and then drying. Subsequent sub-coats are applied in the same manner until the desired thickness is achieved. Note: any coat should not be applied unless the previous one is completely dry. 36 College of Pharmacy- Industrial Pharmacy II- 5th stage- First Semester Tablet Coating Sugar Coating Process: Syrup (smoothing/coloring) Coating The purpose of this step is: 1. To hide the imperfections in the tablet surface caused by the sub-coating step and 2. To impart the desired color to the tablet. This step perhaps requires the most skill. The first syrup coats usually contain some suspended powders and are called “grossing syrups”. In general, no color is added until the tablets are quite smooth because premature application to rough tablets can produce a mottled appearance in the final tablets. In the subsequent syruping steps, syrup solutions containing the dye are applied until the final size and color are achieved. 37 College of Pharmacy- Industrial Pharmacy II- 5th stage- First Semester Tablet Coating Sugar Coating Process: Finishing and Polishing Finishing: in the finishing step, a few clear coats of syrup may be applied. Polishing: the desired luster (gloss) is obtained in this step. The tablets can be polished in clean coating pans by using certain wax (e.g. beeswax, carnauba wax). 38 College of Pharmacy- Industrial Pharmacy II- 5th stage- First Semester Tablet Coating Film Coating Process It is preferred over sugar coating because: 1. It is faster. 2. More economic. 3. The versatility of film-forming polymers that can be used 4. It slightly increases the final tablet weight (only 2-5%). Film coating involves the same equipment and methods as in sugar coating, as follows: 39 College of Pharmacy- Industrial Pharmacy II- 5th stage- First Semester Tablet Coating Pan Spray Method for Film Coating The introduction of spraying equipment was an evolution in the film coating process. Spraying allows an important advantage which is automatic control of the liquid application. 40 College of Pharmacy- Industrial Pharmacy II- 5th stage- First Semester Tablet Coating Pan Spray Method: Control Variables Whatever the coating is carried out in, a conventional or perforated pan, certain process variables should be controlled to ensure good product quality. 1. Pan variables: the pan shape, load, and rotational speed all affect the mixing of the tablets. Uniform mixing is essential for depositing the same quantity of the film on each tablet. Speeds that are too slow may cause localized overwetting, resulting in tablets sticking. Speeds that are too high may not allow enough time for drying before the same tablets are reintroduced under the spray; which results in rough tablets. 41 College of Pharmacy- Industrial Pharmacy II- 5th stage- First Semester Tablet Coating Pan Spray Method Control Variables 2. Spray variables: the spray variables to be controlled: a) The rate of liquid application. Correct Distance b) The degree (size and size distribution) of atomization. Atomization that is too fine leads to some droplets drying before reaching the surface è rough tablet or excess dust in the pan. Too large an atomization will lead to overwetting. Too Far Distance c) Nozzle to bed distance (affects the amount of coating solution applied to a tablet each time it passes in front of it). 42 College of Pharmacy- Industrial Pharmacy II- 5th stage- First Semester Tablet Coating Pan Spray Method: Control Variables 3. Drying air variables: The temperature, volume, and rate are parameters of the process air that need to be controlled to obtain an optimum drying environment. The heat sensitivity of the film-forming material and tablet core largely determines the upper temperature that can be applied. The temperature applied is between 50-90 ℃ (for most drugs). 43 College of Pharmacy- Industrial Pharmacy II- 5th stage- First Semester Tablet Coating Evaluations of Coated Tablets Will involve: Evaluation of the general appearance such as color (hue and continuity), size, and physical defects on the coating Performance of the tablet: drug release characteristics, long-term stability of coated product. In general, visual inspection is sufficient to define relative coated tablet quality. A practical qualitative measure of the resistance of a coated tablet to abrasion can be obtained by merely rubbing the coated tablet on a white sheet of paper. Strong films remain intact and no color is transferred to the paper; very soft coats are readily "erased" from the tablet surface to the paper. 44 College of Pharmacy- Industrial Pharmacy II- 5th stage- First Semester Tablet Coating Film Defects Variations in formulation and processing may result in unacceptable quality defects in the film coating. 1. Sticking and picking: overwetting or excessive film tackiness causes the tablets to stick to each other or the coating pan. On drying, the point of contact of the film may remain adhered to the pan or another tablet. 2. Roughness: a rough or gritty surface is a defect often observed when the coating is applied by a spray. Some of the droplets may dry too rapidly before reaching the tablet bed resulting in a deposit on a tablet surface. 45 College of Pharmacy- Industrial Pharmacy II- 5th stage- First Semester Tablet Coating Film Defects 3. Orange peel effects: inadequate spreading of the coating solution before drying caused a bumpy or “orange peel” effect on the coating. This indicates spreading is impeded by: 1- too rapid drying or 2- high solution viscosity. 4. Bridging and filling: during drying, the film may shrink and pull away from the sharp corners resulting in a “bridging” of the surface depression. This problem results from inadequate plasticizers. à Adjusting the amount of plasticizer or using another one will solve the problem. 46 College of Pharmacy- Industrial Pharmacy II- 5th stage- First Semester Tablet Coating Film Defects Blistering: When coated tablets require further drying in ovens, the solvent from the core is too rapidly evaporated, and the effect of high temperature on the strength, elasticity, and adhesion of the film may result in blistering. è solution: Milder drying will solve this problem. 47 College of Pharmacy- Industrial Pharmacy II- 5th stage- First Semester Tablet Coating