Industrial Engineering PDF
Document Details
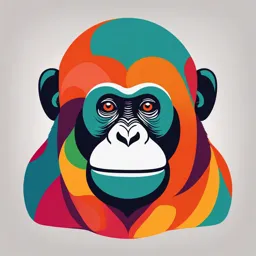
Uploaded by AdjustableUnakite4577
University of Kirkuk
Mahmud H. Ali
Tags
Summary
This document is an overview of industrial engineering. It covers topics like assignment problems, quality control, and optimization methods in engineering contexts.
Full Transcript
Industrial Engineering By Mahmud H. Ali __________________________________________________________________________________________________ Industrial Engineering...
Industrial Engineering By Mahmud H. Ali __________________________________________________________________________________________________ Industrial Engineering By Mahmud H. Ali __________________________________________________________________________________________________ Industrial Engineering By Mahmud H. Ali __________________________________________________________________________________________________ Industrial Engineering By Mahmud H. Ali __________________________________________________________________________________________________ Industrial Engineering By Mahmud H. Ali __________________________________________________________________________________________________ Industrial Engineering By Mahmud H. Ali __________________________________________________________________________________________________ Industrial Engineering By Mahmud H. Ali __________________________________________________________________________________________________ Industrial Engineering By Mahmud H. Ali __________________________________________________________________________________________________ Industrial Engineering By Mahmud H. Ali __________________________________________________________________________________________________ Industrial Engineering By Mahmud H. Ali __________________________________________________________________________________________________ Industrial Engineering By Mahmud H. Ali __________________________________________________________________________________________________ Industrial Engineering By Mahmud H. Ali __________________________________________________________________________________________________ Industrial Engineering By Mahmud H. Ali __________________________________________________________________________________________________ Industrial Engineering By Mahmud H. Ali __________________________________________________________________________________________________ Industrial Engineering By Mahmud H. Ali __________________________________________________________________________________________________ Industrial Engineering By Mahmud H. Ali __________________________________________________________________________________________________ Industrial Engineering By Mahmud H. Ali __________________________________________________________________________________________________ Industrial Engineering By Mahmud H. Ali __________________________________________________________________________________________________ Industrial Engineering By Mahmud H. Ali __________________________________________________________________________________________________ Industrial Engineering By Mahmud H. Ali __________________________________________________________________________________________________ University of Kirkuk Collage of Engineering Mechanical Department 7.4.3 Assignment problem The objective of assignment problem is to assign number of resources (men, machines, etc) to equal number of jobs at a minimum cost or maximum profit. The assignment is to be made in one to one basis. In the balanced assignment problem there are n jobs to be processed on m available machines (n=m). While in unbalanced problem when the number of jobs not equal to number of machines the problem is equalized by adding row or column with zero elements to get a square matrix and the problem is solved as normal assignment problem. The method of solving assignment problem is called Hungarian method and its steps are as follows: 1- Row operation: subtract the minimum cost of each row from other elements in the row to get zero in each row. 2- Column operation: subtract the minimum cost of each column from other elements in the column to get zero in each row. 3- Draw minimum number of horizontal and vertical lines to cover all zeros in the matrix. If number of lines equal to number of jobs in the square matrix then the solution is obtained and go to step5, else continue with the following steps. 4- Determine the smallest element in the matrix not covered by lines subtract it from other elements and add it to the elements in the intersection of the lines until number of lines equal to number of jobs. 5- Assign the jobs to the machines that correspond to the zero element location. The assignments of machines are started by assigning the machines to the rows with minimum number of zeros and cancel the column from the matrix. This process is continued until the jobs assigned to the machines. 6- The maximization assignment problem is solved by converting the problem to minimization problem by subtracting the elements from the largest value in the matrix then using steps 1 to 5 to solve the problem CH7-1 University of Kirkuk Collage of Engineering Mechanical Department Example 7.5: Four different jobs are to be processed on 4 different machines. The following matrix gives the cost of producing the jobs on the machines. Assign the jobs on the machines for minimum cost. Machines Jobs A B C D J1 10 5 6 10 5 J2 6 2 4 6 2 J3 7 6 5 6 5 J4 9 5 4 10 4 Machines Jobs A B C D J1 10-5 5-5 6-5 10-5 J2 6-2 2-2 4-2 6-2 J3 7-5 6-5 5-5 6-5 J4 9-4 5-4 4-4 10-4 Machines Jobs A B C D J1 5 0 1 5 J2 4 0 2 4 J3 2 1 0 1 J4 5 1 0 6 2 0 0 1 CH7-2 University of Kirkuk Collage of Engineering Mechanical Department Machines Jobs A B C D J1 5-2 0 1 5-1 J2 4-2 0 2 4-1 J3 2-2 1 0 1-1 J4 5-2 1 0 6-1 Machines Jobs A B C D J1 3 0 1 4 J2 2 0 2 3 J3 0 1 0 0 J4 3 1 0 5 Min=2 Machines Jobs A B C D J1 3-2=1 0 1 4-2=2 J2 2-2=0 0 2 3-2=1 J3 0 1+2 0+2 0 J4 3-2=1 1 0 5-2=3 CH7-3 University of Kirkuk Collage of Engineering Mechanical Department Machines Jobs A B C D J1 1 0 1 2 J2 0 0 2 1 J3 0 3 2 0 J4 1 1 0 3 Jobs Machines Cost J1 B 5 J2 A 6 J3 D 6 J4 C 4 The total cost is: 5 + 6 + 6 + 4 = 21 CH7-4 University of Kirkuk Collage of Engineering Mechanical Department Example 7.5:A company wishes to assign 4 jobs on 4 machines to gain maximum profit. Find the best assignment of the machines. Machines Jobs A B C D J1 250 300 420 400 J2 350 400 200 250 J3 500 375 400 350 J4 400 350 420 300 Max. value is 500 so that the minimization matrix becomes: Machines Jobs A B C D J1 500-250 500-300 500-420 500-400 J2 500-350 500-400 500-200 500-250 J3 500-500 500-375 500-400 500-350 J4 500-400 500-350 500-420 500-300 The final result is 1720 Example 7.6: There are three jobs are to be assigned to three out of four machines. Determine the optimal assignment. Machines Jobs A B C D J1 13 8 17 19 J2 18 24 28 32 J3 19 15 22 10 Machines Jobs A B C D J1 13 8 17 19 J2 18 24 28 32 J3 19 15 22 10 J4 0 0 0 0 CH7-5 University of Kirkuk Collage of Engineering Mechanical Department 7. 5 Quality control Quality control is concerned with all those functions in an organization which affect quality and ensure that the products attain increasingly high level of quality demanded by the customers. As the quality improves we get better products and fewer rejects. Better products results in an increase in the market share and higher price of the products and hence increase of profit and productivity. Fewer defects results in improved productivity and lower costs. 10.5.1 Statistical quality control Statistical control has been a tool used to control the quality of end products based on inspection. It is assumed that the defects are normally distributed. In recent years the emphasis has been shifted to preventing defects from occurring during the production cycle, the quality is controlled at all critical work stations during the production process using control charts. Control charts is a graphical representation recording the characteristic of a sample of the products used to analyze the process trend to enable the management committees to take an action before the process goes out-of the limits that set by the quality standards. If the quality of the end products can be stated in term of a single variable like diameter, length, thickness, …etc control charts are mainly in form of Mean Chart (X-chart), Range Chart (R-chart) or Standard deviation chart (-chart). On the other hand if the quality of a product is dependent on number of defects in the product and is classified as good or bad the control charts are, Fraction Defective Charts (p Charts) and Number of Defects Chart (C-Charts) 10.5.2 Control limits The control limits of sampling variation as indicated by control charts. The quality of a product falling within the control limits indicate that all assignable causes have been removed and the products may be accepted. The control limits are indicated as upper control limit (UCL) and lower CH7-6 University of Kirkuk Collage of Engineering Mechanical Department control limit (LCL), the variation of property within these limits is accepted and outside of these limits is rejected. Engineering tolerance limit: It is the maximum and minimum limits of tolerance of the product allowed by the designer for gainful utilization of the product. Statistical tolerance limit: It is the limit of variation in which at least a specified property of the product should lie within. 7.5.3 Types of control charts a) Charts for measurable variables - Average and Range 𝑋̅-Chart, UCL=𝑋̅+A2 R, LCL=𝑋̅-A2 R R-Chart, UCL=D4 R, LCL=D3 R -Average and Standard deviation UCL=𝑋̅+A1, LCL=𝑋̅-A1 b) Charts for attributes -Proportion of defectives (p-chart) 𝑃(1−𝑃) ̅ ̅ 𝑃(1−𝑃) ̅ ̅ UCL=𝑃̅ + 3√ +3, LCL=𝑃̅ − 3√ 𝑛 𝑛 𝑑 𝑃= , 𝑑: 𝑛𝑢𝑚𝑏𝑒𝑟 𝑜𝑓 𝑑𝑒𝑓𝑒𝑐𝑡𝑠 𝑖𝑛 𝑒𝑎𝑐ℎ 𝑠𝑎𝑚𝑝𝑙𝑒, 𝑛: 𝑠𝑎𝑚𝑝𝑙𝑒 𝑠𝑖𝑧𝑒 𝑛 ∑𝑃 𝑃̅ = 𝑁𝑜. 𝑜𝑓 𝑠𝑎𝑚𝑝𝑙𝑒𝑠 -Number of defects (c-chart) UCL= 𝐶 + 3√C, LCL= 𝐶 − 3√C 𝑡𝑜𝑡𝑎𝑙 𝑛𝑢𝑚𝑏𝑒𝑟 𝑜𝑓 𝑑𝑒𝑓𝑒𝑐𝑡𝑠 𝐶= 𝑡𝑜𝑡𝑎𝑙 𝑛𝑢𝑚𝑏𝑒𝑟 𝑜𝑓 𝑎𝑟𝑡𝑖𝑐𝑙𝑒𝑠 𝑖𝑛𝑠𝑝𝑒𝑐𝑡𝑒𝑑 CH7-7 University of Kirkuk Collage of Engineering Mechanical Department Table 7.1 Constants used with the charts Sample size A1 A2 D3 D4 2 3.76 1.88 0 3.27 3 2.40 1.02 0 2.58 4 1.88 0.73 0 2.28 5 1.60 0.58 0 2.12 6 1.41 0.48 0 2.00 7 1.28 0.42 0.08 1.92 8 1.18 0.37 0.14 1.86 9 1.09 0.34 0.18 1.82 10 1.03 0.31 0.22 1.78 CH7-8 University of Kirkuk Collage of Engineering Mechanical Department Example 7.7: Draw the 𝑥̅ and 𝑅̅ charts for the following data if sample size (n=7) Sample 1 2 3 4 5 6 7 8 9 10 No. Sample 37 33 41 32 35 34 33 34 35 33 Mean Sample 16 18 16 12 13 11 15 15 19 20 Range 42 40 38 36 X 34 32 30 28 0 1 2 3 4 5 6 7 8 9 10 30 25 20 15 R 10 5 0 0 2 4 6 8 10 CH7-9 University of Kirkuk Collage of Engineering Mechanical Department Example 7.8: Draw a control chart for the following data, if each sample contains 100 items Sample 1 2 3 4 5 6 7 8 9 10 No. No. of 10 12 7 7 9 8 8 10 11 8 defects pi 0.1 0.12 0.07 0.07 0.09 0.08 0.08 0.10 0.11 0.08 0.2 0.18 0.16 0.14 0.12 0.1 p 0.08 0.06 0.04 0.02 0 0 1 2 3 4 5 6 7 8 9 10 CH7-10 University of Kirkuk Collage of Engineering Mechanical Department Example 7.9: The product of a firm is inspected and the following results are obtained: Product 1 2 3 4 5 6 7 8 No. No. of 1 0 1 0 0 4 0 1 defects 𝑇𝑜𝑡𝑎𝑙 𝑛𝑢𝑚𝑏𝑒𝑟 𝑜𝑓 𝑑𝑒𝑓𝑒𝑐𝑡𝑠 𝐶= 𝑡𝑜𝑡𝑎𝑙 𝑛𝑢𝑚𝑏𝑒𝑟 𝑜𝑓 𝑝𝑟𝑜𝑑𝑢𝑐𝑡𝑠 1+0+1+0+0+4+0+1 = = 0.875 8 4.5 4 3.5 3 2.5 n 2 1.5 1 0.5 0 0 1 2 3 4 5 6 7 8 9 10 CH7-11 University of Kirkuk Collage of Engineering Mechanical Department 7.6 Optimization Optimization is a decision making process of arriving at the most favorable solution to a problem. As for example a manufacture may want to develop his product in a most favorable way so that he can derive maximum profit from the sale of the product without exceeding at the same time the tolerance limit, quality or the available resource. To optimize a system, it is necessary to study at first very closely the physical characteristic of the system and then formulate a mathematical model of the objective function with the variables along with their constrains. Then this mathematical model must be solved to obtain the desired solution. 7.6.1 Methods of optimization 1) Search Method 2) Dynamic Programming 3) Geometric Programming 4) Linear Programming 5) Calculus Method 7.6.2 Mathematical modeling Mathematical modeling mean representation of the physical problem in term of equations then the solution of these equations is applied to the physical situation to archive the desired object. As example, A carpentry shop produces chairs and tables subject to the following conditions 1) Each chair takes 3 hours of carpentry work and 1.5 hours of polishing. 2) Each table takes 2 hours of carpentry work and 3 hours of polishing 3) Painter time available per week is 24 hours. CH7-12 University of Kirkuk Collage of Engineering Mechanical Department 4) Carpenter time available per week is 27 hours 5) Profit earned on selling each chair is 4$. 6) Profit earned on selling each table is 5$. Find out the number of chairs and tables should be manufacture each week to maximize the profit? Mathematical modeling of the problem Let: X1: number of chairs to be produced per week. X2: number of tables to be produced per week. Z: Profit earned. Then the problem is modeled mathematically as in the following: The profit is: Z=4X1+5X2 Total carpentry time: 3X1+2X2≤27 Total polishing time: 1.5X1+3X2≤24 The production must be not negative so that: X1≥0 and X2≥0 7.6.3 Linear Programming The technique of Linear Programming can be applied when optimization is achieved in problem situation where the objective function as well as their constraints can be expressed in linear equation. The equations involving constraints can be either equalities or inequalities. Then the solution of the linear programming is maximization for the profit and minimization for cost and time consumption. CH7-13 University of Kirkuk Collage of Engineering Mechanical Department 7.6.3.1 Solution by graphical method The solution of the problem is the region bounded by constrains equations. The object variable is attains its extreme value, maximum or minimum at its vertices only. As example for data in section 7.6.2 the graphical representation of the problem is in the following sketch: The solution is the maximum value of Z among its values at points A, B, and C. The maximum profit (Z) is Max {ZA(X1.X2), ZB(X1.X2), ZC(X1.X2)} Example 7.10: Find the solution of following optimization problem if the objective function is profit. Z=20X1+25X2 3X1+2X2≤27 2X1+3X2≤23 X1≥0 and X2≥0 CH7-14