Fuel Oil System GM PDF
Document Details
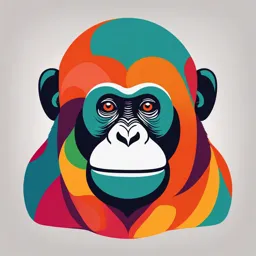
Uploaded by ImaginativePeachTree
STC/JHS
N.L.SAH
Tags
Summary
This presentation describes the fuel oil system of a General Motors (GM) locomotive. It covers various components such as pumps, filters, and pre-heaters, and discusses the operation and function of each. Diagrams aid in the understanding of the fuel system.
Full Transcript
Fuel oil system of GM Locomotive N.L.SAH U Starting of system Fuel is drawn from the storage tank through a fuel suction strainer by a motor driven positive displacement gear type pump. Positive displacement type pump Gear pumps are positive...
Fuel oil system of GM Locomotive N.L.SAH U Starting of system Fuel is drawn from the storage tank through a fuel suction strainer by a motor driven positive displacement gear type pump. Positive displacement type pump Gear pumps are positive displacement type of pumps. Gear pumps are generally used in system where the operating pressure is up to 3600 PSI. Gear pumps are classified as :- External Gear Pump Teeth are on the outside of the gears. Internal Gear Pump The Internal gear pump has similar characteristics to the external gear pump. The pump has improved suction and delivery characteristics & is smoother in operation. The Internal gear pump is however more complicated and expensive to manufacture & maintain. Teeth of an external gear mesh with the teeth on the inside of a larger gear. Pumping chambers are formed between the gear teeth. A crescent seal separates the inlet & outlet. This seal is machined in to the valve body where clearance between the teeth is maximum. The crescent seal provides a positive seal between the inlet & outlet and reduces internal leakage. FUEL OIL PUMP The motor driven fuel pump is mounted on the equipment rack. It is an Internal gear pump driven by battery power during system priming and by power from the Auxiliary Generator during operation. Working of fuel oil pump Fuel is drawn into the inlet portion to fill a space created by the gear teeth coming out of mesh. The fuel is then trapped in the space between the gear teeth and carried to the out side of the pump where the gear mesh, forcing the fuel from between the gear teeth out through the outlet. Pre-Heater Some of fuel is pumped through a pre-heater, And some is directed through an AMOT mixing valve. Warm fuel from the pre- heater goes to the Amot valve where it is mixed with fuel from pump. 350c FUEL PRE-HEATER The water flows through a tube inside the cooler. The fuel flows in the shell around the heated tube. The coolant and fuel flow through the cooler in opposite directions to produce the maximum cooling effect. Fuel existing the pre heater goes to the mixing valve. Primary filter Fuel, which exits the mixing valve, flows through the primary fuel filter. A canister type primary fuel filter assembly is mounted on the equipment rack under the lube oil cooler assembly. Primary Filter-- Primary filter is a simple sediment filter. Fine wire gauze is not used because the possibility of blocking tendency. The purpose of sediment filter is to remove the larger droplets of water and abrasive matter that may be present in the fuel oil. System diagram – Primary Fuel Filter To engine mounted Primary fuel filterfilter FUEL PUMP 30 psi fuel by pass valve & gauge From fuel straine r Primary fuel filter bypass and gauge A bypass valve and gauge is connected across the primary filters. If the primary filters become plugged, fuel will bypass. As the filter element becomes plugged, the indicator will read higher until it reaches the red change filter zone at approximately 30 psi pressure differential. At this point, the bye pass valve will begin to open, allowing the fuel oil to bye pass the primary fuel filter. Renew primary fuel filter elements when the indicator reaches the change filter zone. Engine mounted fuel filter assembly Fuel after passing through primary fuel filter, it flows through the engine mounted fuel filters. A relief valve is connected on engine mounted fuel assembly. Main Filters The working of this filter is based on agglomerate flow. When the fuel oil containing any fine Water droplets is passed through a porous filter element, the drops join together or agglomerate into large drops. Relief valve As the engine mounted fuel filter elements become plugged, fuel flow to the injectors is limited. A relief valve will open at a preset high pressure (70 psi) to return fuel to the tank, bypassing the fuel injectors. After passing through the engine mounted duel - element filter, the fuel flows through manifolds that extend along both banks of the engine. These manifolds supply fuel to the injectors. The fuel pump delivers more fuel oil to the injectors than is injected into the cylinders. The excess fuel is used to cool and lubricate the close tolerance injector parts. Injector FUEL INJECTORS Fuel Injector is mounted on the combustion chamber. Function of the fuel Injector is to atomize the fuel. i.e. to break it in the form of a fine spray and distribute it into the cylinder. Returning of fuel Fuel returning from the injectors passes through the “return fuel” sight glass and back to the fuel tank. Fuel Injector 1)EUI (electronic unit injector) 2)MUI (Mechanical unit injector) The Injector consists of two parts – Nozzle unit and Nozzle holder. The nozzle body is attached to the body by a nozzle cap nut. Nozzle holder has a flange, cap and two opening inlet for fuel and for leak off. MUI MUI Injectors have an adjustable calibrating slide mounted on the side of the injector body, adjacent to the rack. This slide is incorporated solely as a means of adjusting injector output on the calibrating stand. Filters at the fuel inlet and outlet connections protect the working parts of the injectors. Fuel back pressure A relief valve at the inlet to the fuel “ return fuel” sight glass establishes a fuel back pressure (15PSI), thus maintaining a positive supply of fuel for the injectors. Sight Return glass Bypass valve & sight (Normall 30 PSI Condition gauge (normally y empty) full) 15PSI 7 Primary 0 Primary filter P filter Secondary S 13 filter I micron Thermostati 5 micron c Mixing valve Pre- Filling EFCOS Heater cap Vent pipe Strainer FPM 600 micron Positive FUEL TANK Glow Displacement CAPACITY= 6000 Liters rod Gear gauge 7.5 gal./min. Drain