U.S. Air Force Facilities Management Playbook 2022 PDF
Document Details
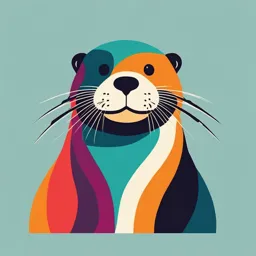
Uploaded by PanoramicCharacterization
2022
Tags
Summary
The 2022 U.S. Air Force Facilities Management Playbook is a guide for managing facilities within the Air Force. It details roles and responsibilities, procedures, and services for facility management.
Full Transcript
Air Force Civil Engineer Facility Management Playbook 2022 U. S. A I R F O R C E Facilities Management Playbook 1|Page ...
Air Force Civil Engineer Facility Management Playbook 2022 U. S. A I R F O R C E Facilities Management Playbook 1|Page Air Force Civil Engineer Facility Management Playbook Table of Contents Document Change Log................................................................................................................. 4 Chapter 1 Introduction........................................................................................................... 5 1.1 Playbook Scope.......................................................................................................................6 Chapter 2 Facility Manager Appointment............................................................................... 7 2.1 Roles and Responsibilities.......................................................................................................7 2.2 FM Positions............................................................................................................................7 2.3 FM Appointment Qualifications..............................................................................................7 2.4 FM System Authorization Access Request (SAAR)..................................................................8 2.5 FM Training.............................................................................................................................8 Chapter 3 Facility Manager Duties........................................................................................ 10 3.1 Roles and Responsibilities.....................................................................................................10 3.2 FM Duties..............................................................................................................................10 3.3 CE Services............................................................................................................................11 3.3.1 Facility Inspections........................................................................................................11 3.3.2 CE Service Request Criteria...........................................................................................11 3.3.3 Minor Maintenance......................................................................................................12 3.3.4 CE Service Requests......................................................................................................12 3.4 Maintenance of Surrounding Areas......................................................................................13 3.5 Contract Surveillance............................................................................................................13 3.6 Key Control and High Security Locks.....................................................................................14 3.7 Fire/Safety.............................................................................................................................15 3.8 Mold......................................................................................................................................16 3.8.1.1 Occupants...................................................................................................................17 3.8.1.2 FMs.............................................................................................................................17 3.09 Energy Conservation and Awareness...................................................................................18 3.10 Reserved Parking...................................................................................................................18 3.11 Continuity Book.....................................................................................................................19 3.12 Real Property........................................................................................................................20 3.13 Emergency Management (EM).............................................................................................20 3.14 Generators............................................................................................................................21 3.15 Fuel Tanks.............................................................................................................................21 Chapter 4 Unaccompanied Housing Facility Management..................................................... 22 4.1 Inspections............................................................................................................................22 4.2 Change of Occupancy Maintenance (COM)..........................................................................23 4.3 Locks and Keys......................................................................................................................24 4.4 Inventory Change Requests (ICRs)........................................................................................24 Chapter 5 Facility Management (FM) Program Management................................................. 26 5.1 Roles and Responsibilities.....................................................................................................26 5.2 FM Appointment Process......................................................................................................27 5.3 FM Training...........................................................................................................................28 5.4 Information Repositories......................................................................................................29 5.5 FM Handbooks and Local Policies...........................................................................................30 5.6 Energy Conservation and Usage............................................................................................30 2|Page Air Force Civil Engineer Facility Management Playbook 5.7 Facility Visits..........................................................................................................................30 5.8 Environmental Considerations...............................................................................................30 5.9 Emergency Management.......................................................................................................31 5.10 Generator Maintenance........................................................................................................31 5.11 Key Performance Indicators..................................................................................................31 Appendix A - Acronyms and Definitions..................................................................................... 32 Appendix B - Master List of Links................................................................................................ 34 Appendix C - Attachments......................................................................................................... 36 Attachment A - AF Cleanup and Mold Prevention Policy Following Water Damage.......................36 Attachment B - Remediation of Mold-Contaminated Building Materials........................................37 Table of Figures Figure 1: CE Portal NexGen IT Homepage............................................................................................... 5 Figure 2: NAF DCPDS............................................................................................................................... 8 Figure 3: Core Competencies.................................................................................................................. 9 Figure 5: CE Portal Homepage............................................................................................................... 26 Figure 6: VLC Welcome Page................................................................................................................. 28 Table of Tables Table 1: FM Program OPR and Responsibilities...................................................................................... 7 Table 2: FM Program OPR and Responsibilities.................................................................................... 10 Table 3: FM Roles and Responsibilities................................................................................................. 26 Table 4: AF Cleanup and Mold Prevention Policy Following Water Damage....................................... 36 Table 5: AF Policy for Remediating Building Materials with Mold Growth Caused by Clean Water.... 39 Table 6: Cleanup Methods.................................................................................................................... 39 3|Page Air Force Civil Engineer Facility Management Playbook Document Change Log The table provided below lists significant changes found in this Playbook. SECTION # SECTION NAME CHANGE DESCRIPTION DATE Facility Manager Moved from Chapter 3 to Chapter 2, 08/11/2021 Chapter 3 Appointment Moved Chapter 4 to Chapter 3 Facility Manager Created 2.1-2.5 08/11/2021 Chapter 2 Appointment Chapter 3 Facility Manager Duties Created 3.1 -3.8, updates to 3.16 08/11/2021 Facility Management Changed Chapter name from 08/11/2021 Chapter 5 (FM) Program Manager to Management management Added section 4.1.3 “Inspection 04/27/2022 Simulation.” An immersive Chapter 4 Inspection Simulation Unaccompanied Housing Facility Inspection Added below statement to 1st 07/1/2022 sentence: “…and subsequent condensation from a broken Facility Manager building envelope (both from facility Chapter 3 Duties, 3.8 Mold deficiencies and from building occupants opening windows/doors),…” Sec. 3.6 Key Control and Updated AFI 31-101 to DAFI 31-101 08/31/2022 Chapter 3 High Security Locks Updated AFI 31-101 to DAFI 31-101; 08/31/2022 Appendix B Master List of Links updated hyperlink; added Restricted Use note Title Page Date Updated to 2022 08/31/2022 Added the word “does” in front of 11/17/2022 Chapter 3 Section 3.3.1 “not” in second para., second sentence. Removed 0 from 3.09 to just read 11/17/2022 Chapter 3 Section 3.9 3.9 to be consistent with other sections. Added table header to second page 11/17/2022 Appendix A Acronym List of acronym list 4|Page Air Force Civil Engineer Facility Management Playbook Chapter 1 Introduction Air Force (AF) policy and doctrine dictate that Civil Engineer (CE) forces establish, operate, sustain, and protect installations as power projection platforms that enable AF and other supported commander’s core capabilities through engineering and emergency response across the full mission spectrum. At the installation level, CE forces sustain and maintain the installation, however customers are responsible for letting CE know what is needed in their facility so that CE can in-turn enable that power platform and mission. Facility Managers (FM) are the focal point for customer needs in a facility. They ensure customer needs are met while looking at a whole building’s needs, prioritizing and coordinating within the facility to ensure that the needs are met in the most cost- effective manner possible with the resources available. In accordance with (IAW) Air Force Instruction (AFI) 32-1001, this playbook provides standard business processes for the management of the installation Facility Management Program and helps ensure continuity of installation programs. Refer to the Operations Engineering Playbook for additional information on overarching Requirements and Optimization guidance. Air Force Civil Engineer Center (AFCEC) provides additional support to Operations (CEO) through the AFCEC/COOM SharePoint Site. The site contains checklists, guides, links, lessons learned, and additional guidance. For the best experience, post questions to the Discussion Board and setup alerts to receive notifications for new posts, questions, and answers. Utilize the AFCEC/COOM, Ops Business Process Library (BPL) as well for detailed information on related business processes outlined in AFI 32-1001 and/or this playbook. For additional information on the NexGen Information Technology (IT) initiative, go to the CE Portal NexGen IT homepage. Figure 1: CE Portal NexGen IT Homepage 5|Page Air Force Civil Engineer Facility Management Playbook 1.1 Playbook Scope Limitations: This playbook does not replace, supersede, or circumvent existing Department of Defense (DoD) or AF policy. Applicability: This playbook is intended for Operations Flight personnel to support the management of the Facility Management Program IAW AFI 32-1001 and AFI 32-6000, as discussed in Chapter 4. It is every Operations Flight’s responsibility to ensure it does not degrade the ability of senior leaders to perform executive level advocacy for our future budgetary needs. While no single exception may seem significant, at the enterprise level, the hundreds of exceptions made each year have significant impact on budget planning and reporting. Ensuring the scarce funds are used and accounted for when executing these requirements provides critical integrity to the overall resource advocacy and execution. This requires Operations Flights to improve stewardship in funds accountability. 6|Page Air Force Civil Engineer Facility Management Playbook Chapter 2 Facility Manager Appointment Several of the forms and documents referenced in this Playbook are located in the Reference Section to the right of the Playbook narrative on the CE Portal or located within the BPL associated with this section. 2.1 Roles and Responsibilities Roles Responsibilities Appoints FMs Unit Commander Notifies R&O Requirements Section Provides assistance to FMs Facility Manager Program Manager Trains FMs (FMPM) Documents FMs when appointed Suspends FM user rights when training is not completed Manages facilities assigned FM Completes training Table 1: FM Program OPR and Responsibilities 2.2 FM Positions FMs are responsible for numerous infrastructure related tasks within a facility. Primary FMs are the sole CE focal point within a facility. Primary FMs receive requests from all users in the facility, vet them, and submit them if they meet service task submission criteria (See the Work Management Playbook for more information on this criteria). Primary FMs must know about all infrastructure related requests in a facility, future uses of the facility, future missions moving in and out of the facility, and be included by CE in the planning of Facility Projects. Alternate FMs serve as a backup to the Primary FM for when the Primary FM cannot complete their assigned roles due to leave, Temporary Duty (TDY), etc. Alternate FMs do not serve as Primary FMs for their unit’s footprint and do submit work tasks unless primary responsibilities have been delegated to them by the Primary FM. Alternate FMs coordinate all FM SRs with the primary FM for submittal. 2.3 FM Appointment Qualifications The Federal Buildings Personnel Training Act (FBPTA), passed in 2010, requires all federal personnel providing building operations and maintenance services to demonstrate competencies necessary to effectively operate government facilities. With this act in mind, the following criteria are required for AF Additional Duty FMs. Note: Personnel hired directly as FMs may have additional requirements, training, and certifications required. Only an E-5 or above or civilian equivalent (not excluding certain contractors) may be appointed as a primary or alternate FM. Facilities that do not have personnel residing in the facility that hold the required rank or qualifications, may have a qualified FM manage several facilities instead. FMs are required to utilize NexGen IT when available for non-emergency work. This requires the position have a Common Access Card/Personal Identity Verification (CAC/PIV). 7|Page Air Force Civil Engineer Facility Management Playbook Unit Leadership assigning an employee without a CAC/PIV, who requires access to NexGen IT, must initiate contact with their local Trusted Agent Security Manager (TASM)*, who were appointed by the Service or Agency Point of Contact (SPOC), in order to have them start the application of a CAC/PIV. The CE Unit will annotate in local guidance that until the FM (appointee) obtains a CAC/PIV, the FM will only be able to call in Emergencies, and a current FM for the unit covers in their place until the appointee obtains a CAC/PIV and submits their NexGen IT access paperwork to CE through the NexGen IT System Authorization Access Request (SAAR) process. Be able to lift, push, pull and carry 50 lbs., climb ladders and maneuver over moderate distances or be able to delegate these responsibilities to another individual with local leadership direction. In facilities that have a classified mission, it may be beneficial to appoint an FM that has the appropriate clearance. This can help the FM advocate for that mission and their needs to CE. *AAFES pushes records through Non-appropriated Funds (NAF) Defense Civilian Personnel Data System (DCPDS) vs. TAs inputting an application in the Trusted Associate Sponsorship System (TASS); and do not process Foreign Affiliates** (military and civilian) in TASS as of July 2020. Contact local SPOC or TASM for more information. Figure 2: NAF DCPDS 2.4 FM System Authorization Access Request (SAAR) The FM submits a SAAR to request access to NexGen IT (if fielded at the installation), selects the FM role, and submits non-emergency requirements through NexGen IT (when available). Refer to the BPL page – Facility Manager SAAR for guides on the SAAR request process. 2.5 FM Training FMs are often responsible for multimillion-dollar facilities and the safety and well-being of all personnel within the facility. These responsibilities require FMs to attend initial FM training prior to being appointed as an FM so there is no lapse in coverage. See section 5.3 on types of FM training. Failure to complete the prescribed training may result in the FMPM suspending the FM from being able to submit non-emergency requests and a notice to the FM’s Unit Commander. 8|Page Air Force Civil Engineer Facility Management Playbook In addition to basic FM training and in accordance with the FBPTA, FM’s also pursue more professional training opportunities to polish the core competencies involved with their position. These competencies were developed by the General Services Administration (GSA) and are shown below. FMs review the BPL page – FM Training, for a list and links to specific training opportunities. Figure 3: Core Competencies 9|Page Air Force Civil Engineer Facility Management Playbook Chapter 3 Facility Manager Duties Several of the forms and documents referenced in this Playbook are located in the Reference Section to the right of the Playbook narrative on the CE Portal or located within the BPL associated with this section. 3.1 Roles and Responsibilities Roles Responsibilities Supports FMs Unit Commander Provides program guidance FMPM Supports FMs Manages facilities assigned FM Maintains continuity book Two-way communication with facility users and CE as they relate to facility Ensures all FM duties are completed (when available) Table 2: FM Program OPR and Responsibilities Note: Refer to the BPL page – Facility Manager SAAR, for guides on the SAAR request process. 3.2 FM Duties FMs accomplish a wide variety of functions within a facility. This can be seen by the number of directives that specifically mention FMs as having responsibility or roles. This includes duties in the realms of security, fire, energy, environmental, safety, bio-environmental, emergency management, contracting, and CE. Duties performed by FMs include but are not limited to: Being the central POC for facility occupants requesting CE services and for CE Performing walkthroughs of their facility to find safety, fire, security, or repair requirements. Ensure SR’s, Contract By Requester (CBR), and U-Fix-It requests are submitted verbally, online, or written in accordance with AFI 32‐1001, and supporting playbooks. Being responsible for maintenance of areas surrounding their assigned facilities IAW local guidance. Establishes a key control program and procedures for the security of all basic and master keys that service their facility. Ensure proper surveillance and customer complaint procedures are adhered to IAW the requirements in the contracts for refuse collection, grounds maintenance, and custodial services. Ensure the facility is safe from fires and other mishaps. Maintain an aggressive energy and water conservation program. Manage reserved parking within their facility. Maintain a facility folder for a chronological history of the building (electronic file suggested to minimize resource consumption). 10 | P a g e Air Force Civil Engineer Facility Management Playbook Help create and maintain the facility Emergency Action Plans (EAPs). Other duties as assigned. Delegating duties, as appropriate, with unit leadership approval Depending on the facility, some FM’s may also have duties in regard to generators, emergency management (EM), and/or hazardous waste. 3.3 CE Services As the central POC for facility occupants, the task that typically takes the most time from a FM is requesting CE services. Primary FMs receive all service requests in a facility, validate the requests, submit the requests, and track the requests to completion. Many installations have found the FM so vital to their mission that, signs are posted at facility entrances notifying occupants who their FM is and how to contact them. 3.3.1 Facility Inspections FMs are required to conduct full walkthroughs of their facilities at least monthly to identify the following: Repair requirements. Fire, safety, and environmental concerns. Unapproved work that may be in the process of being accomplished or has been completed. Damage from neglect or willful abuse. Ways to improve energy usage. This includes mechanical rooms, offices, common areas (to include bathrooms and hallways), and the outside of the facility. This walkthrough does not include areas that are not safe, such as roofs or confined spaces within a facility. FMs use this time to also check on service requests that have already been submitted to CE. Occasionally problems resolve themselves or get worse, or an FM may want to provide feedback to CE on a service request that was complete. The FM are required to report unapproved work or damage that seems to have been from neglect found during the walkthrough to CE. Unapproved work is considered Facility Abuse and requires a Report of Survey (RoS) be completed per DoD 7000.14- R, Vol 12 Chap 7. RoS procedures vary from installation to installation, so FMs are to contact their FMPM for specific guidance for their installation. 3.3.2 CE Service Request Criteria In addition to requirements found during walkthroughs, FMs also receive repair and enhancement requests directly from occupants. Any request that affects the infrastructure of a facility has to be requested to CE prior to being implemented or purchased to ensure the infrastructure can handle the request. This includes new mission equipment and appliances. When this happens, FMs are required to validate the request, ensuring it is a CE responsibility, by physically looking at the request to get a full scope of the requirement and to prevent being a “middle-man”. An FM 11 | P a g e Air Force Civil Engineer Facility Management Playbook gathers support documentation and ensure all needed and detailed information is present. FMs for tenant units have to review the support agreements in place for their unit to ensure that the work requested is fully supported by the local CE unit and to see what stipulations for that work may apply (e.g.,., reimbursements, no support, contract work, etc.). Tenant units follow the same work priorities as other units on base. 3.3.3 Minor Maintenance Some facility repairs has to be completed by the FM as a part of their duties. These duties are typically quick and simple fixes that can be accomplished with minimal tools on hand and supplies from the installation U-Fix-It store. FM’s will need to follow local procedure to request U-Fix-It supplies from CE. Local requirements will dictate the specific responsibilities and all requirements are to be followed within the confines of AF Manual (AFMAN) 91-203; however, some common tasks include: Plunging Toilets. Turning off emergency shut off valves to plumbing fixtures in case of a major leak. Placing approved ice-melt products on sidewalks. Replacing light bulbs under 10 ft (if not deemed a safety concern or CE responsibility). Replacing ceiling tiles under 10 ft. Tightening hinges or other simple mechanisms. Replacing light switch or outlet covers. Replacing toilet seats. Basic pest management practices (emptying mouse traps, spraying for bugs/weeds, etc.). In addition to the above, local units are responsible for maintaining non-real property equipment. Items such as furniture, electronics, or light bulbs for such items are some examples of non-real property equipment that would need to be funded and maintained by the owning unit. 3.3.4 CE Service Requests Once verified, the Primary FM submits the service request to CE using NexGen IT (if available) or by other locally developed submission processes. See local guidance, the Work Management Playbook, NexGen IT Reference Guides, or BPL page – FM CE Service Requests, for more detailed information on how to submit a service request to CE and things to look for when determining if a request is valid. Sustainment (priority 3A-3C) work requests are completed as manpower is available. These types of requests repair and sustain the installation and mission “as is”. Enhancement requests (priority 4A and 4B) are requests to upgrade or change something in the facility. These types of requests may not be completed depending on available CE manpower and may instead need to be funded with the using the requesting unit’s funds depending on local CE guidance. If funded using the requesting unit funds, these requests are called “contract by requester”, or CBRs. 12 | P a g e Air Force Civil Engineer Facility Management Playbook CBRs still need to be approved by CE prior to the government entering into any contract. Approval is needed for anything that connects to or modifies the infrastructure such as bottle filling water fountains, painting, hanging large televisions or displays, modular furniture, or other large appliances. These can draw significant infrastructure resources and CE is required to ensure the current infrastructure can support what the unit wants while also meeting fire, safety, design, and environmental codes. Failure to gain approval prior is considered facility abuse and may result in the unit’s funds being spent with no work, additional funds to ensure the work was completed to code, or the unit paying another contract to restore the facility to its prior function. CE will also usually only fund the replacement or broken pieces of facility infrastructure unless advantageous to the government due to maintenance costs, etc. If a building requires signs within it, a service request is required to be submitted to CE. Interior signs have to comply with United Facilities Criteria (UFC) 3-120-01 and certain signs are required to be Americans with Disabilities Act (ADA) compliant. CE will verify that the signs meet the UFC requirements and that the designs match base architectural designs. Annually, the FM works with the local CE unit to validate all open requirements for their facility that have been open for over a year. With the turnover of various positions, this validation helps to ensure that work orders are not in a backlog or using resources when it may no longer be needed. FMs contact their local CE R&O section to determine the local process to accomplish the annual facility project validation. 3.4 Maintenance of Surrounding Areas FMs are also responsible for the maintenance of areas directly surrounding their facility. This distance is usually 50 ft but may be different based on local requirements. Within this area, FMs are responsible for ensuring that trash is picked up, landscaping is kept neat and clean, weeds are controlled in sidewalks, flower beds, rock beds, etc., snow is removed from sidewalks, and designated tobacco areas are kept neat and clean. As mentioned previously, FMs do not have to accomplish these tasks themselves and are to work with the First Sergeant(s) and building leadership to receive personnel to accomplish these tasks. FMs do not accomplish any duties that are accomplished via service contract at their installation. 3.5 Contract Surveillance Numerous facility upkeep and maintenance activities are accomplished by contractors instead of CE or facility personnel. For contracts managed by CE, Contracting Officer Representatives (CORs) are assigned to oversee and provide surveillance to these contracts. Due to the sheer size of these contracts however, CORs cannot be everywhere and have to view samples of the tasks to ensure compliance with the Statement of Work (SoW) or Performance Work Statement (PWS). FMs provide an essential service and fill in the gap for contract surveillance. The FMPM works with the CORs to provide a simple checklist to FMs based on the SoW/PWS so that FM 13 | P a g e Air Force Civil Engineer Facility Management Playbook understands the scope of the work being completed and the quality requirements in place that the contractors are responsible for completing. While FMs and building occupants cannot direct a contractor to accomplish or redo a task, FMs notify the appropriate COR when they feel the contractor did not accomplish the task appropriately. Typical CE Service contracts include but are not limited to: Refuse (trash) collection Custodial services Grounds maintenance 3.6 Key Control and High Security Locks Per DAFI 31-101, Integrated Defense, many FMs are required to maintain key control for their facilities. CE takes that a step further and requires all FMs maintain positive key control of their facilities. Facilities contain many items required to keep Department of the AF missions ongoing and include expensive, sensitive, or classified information. Ensuring facilities cannot be accessed by unauthorized personnel is therefore vital to protecting the mission. FMs is required to have all occupants sign for all issued keys/electronic key cards and maintain a log showing the key numbers and who the keys are assigned to. FMs record key issuances on an AF Form 2432, Key Issue Log or other locally developed form approved by the FMPM. FMs overseeing Arms, Ammunition, and Explosives (AA&E) facilities reference UG-2045-SHR and AFMAN16-1404, Information Security Program, for additional guidance on key control and storage procedures in their facilities. At some locations, CE unit issues and log all key to individual occupants instead of FMs. When this occurs, FM’s are waived from this requirement. Due to the risks involved with master keys, they are created and issued to only a small number of personnel that have a need for them. This list usually includes the FMs and Unit Commanders. When an FM requests a new master key, a memorandum has to be signed by the using organizations Commander or equivalent (on G-series orders) and submitted to CE by the Primary FM via service request. CE will review the request and will determine whether to create the key based on the totality of the circumstances. In the event of lost, misplaced or stolen keys, the FM notifies CE immediately. CE will review the request and based on the totality of the circumstances and risk posed (such as mission, security, hours of occupation, key loss reason and location, etc.), will determine what, if anything, is to be done. Possible solutions include but are not limited to rekeying the entire facility or rooms affected, having the facility guarded by the FM/occupants, notification to the Base Defense Operations Center (BDOC) for inclusion into the blotter, or nothing. Some of these solutions may require affected unit pay for the costs. GSA certified locks are used on doors throughout facilities that contain classified information. CE maintains these locks as they are considered real property. CE typically does not maintain or repair other types of locks that are not considered real property. These include GSA locks on safes, padlocks, or standard locks on furniture. CE may not maintain mechanical push- button locks (sometimes incorrectly referred to as cipher locks). These locks are usually installed for convenience and not for security. Contact the FMPM to determine what locks 14 | P a g e Air Force Civil Engineer Facility Management Playbook the CE unit maintains. If locks are not maintained by CE, then the using unit is responsible for the maintenance and repair of these locks. Refer to the BPL page – FM Facility Security, for additional information in regard to the lock and key control. 3.7 Fire/Safety Air Force Occupational Safety, Fire and Health Standards (AFMAN 91-203) and Fire and the Emergency Services (F&ES) (AFI 32-2001) provide guidance to FMs on facility safety. It is vital the FMs know and understand their roles when it comes to these directives and regularly read through these publications to ensure compliance. FMs have to work closely with the unit Safety Manager and the Fire Prevention Office to ensure the facility is safe for occupants within. In compliance with these publications, FMs is required to accompany the Fire Inspector during annual fire inspections within their facilities. It is advised that in addition to the annual checks, FMs also check for fire and safety issues during their monthly walk-throughs of their facility. See the BPL page – FM Maintenance, for more information and checklists to assist with facility inspections. Some facilities have fire extinguishers located within them. For these facilities, FMs will need to check the pressure on them as well as for any damage (missing pins, broken mounting brackets, etc.) and the date of manufacture, then annotate the inspection date and their initials on the fire extinguisher inspection tag located on or near the extinguisher. The life expectancy of fire extinguishers varies by the type of extinguisher, usually between 5 and 12 years. After these intervals, extinguishers require hydrostatic testing. Typically, AF fire departments do not perform this testing or provide replacement extinguishers. FMs are required to work with their unit to budget for purchasing and maintaining fire extinguishers, per AFMAN91-203, as these items are not considered real property (RP) or real property installed equipment (RPIE). Facilities with fire extinguishers are required to also have FMs or supervisors document when work center personnel have completed fire extinguisher training and understand their responsibilities when it comes to fire prevention. FMs are responsible for training new personnel to their facilities on evacuation procedures as well as identifying a pre-determined area for personnel to gather after an evacuation. In addition to training, FMs ensure evacuation signs are posted throughout their facilities so that occupants understand the primary and secondary means of evacuation in case of emergency. FMs can work with their local Fire Prevention Flight for help with these requirements. In addition, they can schedule evacuation drills for their facilities to ensure occupants are prepared and developed plans work as intended. FMs also ensure a process is in place for closing the facility at the end of the day if not in 24- hour occupation. End of day inspections involve the facility being checked for fire hazards, such as appliances left on, space heaters left on, extension cords still in use, decorations in compliance, etc. See the BPL page – FM Maintenance, for a sample end of day fire inspection checklist. End of day fire safe inspections has to be documented. Space heaters are generally not allowed in facilities; however, they can be approved on a case-by-case basis. In cases where heat may not be functioning properly, the local CE unit will submit and route a request for a space heater in the affected areas, if it cannot be 15 | P a g e Air Force Civil Engineer Facility Management Playbook mitigated in another way. In medical cases where a space heater is required, a memorandum from the member’s medical provider must be submitted to the local CE unit for approval. Information on the memorandum must not violate the Health Insurance Portability and Accountability Act (HIPPA) standards, but must include, at a minimum, the length of time the heater is required, the building/room number/office and/or cubicle it will be in, why the normal building HVAC system is inadequate to meet the member’s needs, and a brand/model number that the member is wanting so that it the safety features and electrical load can be calculated and approved or disapproved. A sample waiver memo can be found on the AFCEC/COOM BPL page – FM Fire, Safety, and Health. FMs must ensure occupants understand regulations in regard to decorations, especially around holidays when decorations are more commonplace. Decorations are often flammable and are displayed in manners that run afoul of fire codes. When social or other unusual events happen in a facility, FMs must check with their local fire prevention office to see what guidelines may apply. FMs must ensure: Decorations are unplugged when the occupant is not in the immediate vicinity. Lit candles and other decorations with open flames are never allowed in a facility. Decorations do not block, partially block or hinder egress routes. Wires for decorations do not present tripping hazards. Decorations do not pull more AMP’s than what the circuit is designed to handle. Live trees are not used. Wiring is free from defects (no cuts, frays, splices, etc.). Wiring is not tacked, pinned, or stapled. 3.8 Mold Molds can be found almost everywhere. Mold grows rapidly (biomagnification) indoors when the spores come in contact with building materials, that have sufficient moisture to support active fungal growth. It is impossible to get rid of all mold and mold spores indoors, as mold spores will be found floating through the air and in-house dust. The mold spores will not grow if moisture is not present. Indoor mold growth can and will be prevented or controlled by controlling moisture levels indoors. The typical conditions leading to mold growth in buildings include inadequate moisture control and subsequent condensation from a broken building envelope (both from facility deficiencies and from building occupants opening windows/doors), deficient ventilation systems, poor housekeeping, chronic water intrusion, and/or isolated floods, such as from a burst water pipe. Once growth begins, fungal spores and bacteria amplify quickly. The microorganisms produce new spores that are introduced into the airstream either because the mold grows on the wet building material or during other building material disturbances (e.g., renovations, repair work, etc.). Such growth also can lead to the release of volatile compounds and odors characteristic of fungal/microbial growth. Preventing and remediating water damage is necessary to protect the health and well-being of AF communities and our investment in AF infrastructure. In most cases, mold-related contamination is associated with water--the key to an effective mold program is controlling moisture in the facility. However, moisture control must be combined with adequate 16 | P a g e Air Force Civil Engineer Facility Management Playbook housekeeping and active participation of facility occupants in inspecting and responding promptly to initial signs of mold. By promoting timely facility moisture control, effective housekeeping, and active occupant participation, installations can successfully control mold growth and prevent potential subsequent medical concerns. 3.8.1 Responsibilities 3.8.1.1 Occupants Areas that are often or always damp can be hard to maintain completely free of mold. If there is mold in the shower or elsewhere in the bathroom that seems to reappear, increase the air circulation by leaving the shower door/curtain open along with the door to the bathroom. Also, clean the area more frequently and this will usually prevent mold from recurring, or at least keep the mold to a minimum. Practice sound housekeeping: vacuum floors, remove trash frequently, prevent excessive dust accumulation, and use typical household cleaning products to control mold and mildew. When water leaks or spills occur indoors – ACT QUICKLY. If wet or damp materials or areas are dried 24-48 hours after a leak or spill happens, in most cases mold will not grow. Report all plumbing/building leaks and moisture problems immediately to housing or FM. When cooking, always operate the stove exhaust hood or when bathing, use the bathroom exhaust fan. Make sure the laundry clothes dryer vent is connected properly and exhausting outdoors. If condensation or moisture is seen collecting on windows, walls or pipes - ACT QUICKLY to dry the wet surface and reduce the moisture/water source. Condensation can be a sign of high humidity. Report all moisture or potential mold findings to the FM. 3.8.1.2 FMs Inspect and report moisture problems before mold and related microbial contamination becomes problematic. Since molds depend on the availability of nutrients (e.g., dirt, cellulose, and other substrates) as well as moisture, ensure a clean and dry environment is maintained within the facility. As part of routine building inspections required by the FM Playbook, conduct periodic evaluations of all portions of the facility that the FM has reasonable access to. Roofs, mechanical rooms, inside of walls, above ceilings and below floors are not the responsibility of the FM to inspect. Conduct inspections of facilities immediately following (24 hours) unusual events such as natural disasters (hurricanes, heavy rain, deep freezes where pipes have a history of breaking). FMs must clean and correct any small mold problems or water damage promptly (within 48 hours) following the guidelines in Attachment A. If mold 17 | P a g e Air Force Civil Engineer Facility Management Playbook contamination or water damage is extensive, the FM will submit a service request to CE for remediation. FMs or other occupants cleaning mold must wear appropriate PPE and containment options as annotated in Attachment A and Attachment B and consult an occupational health professional or BE, as needed. A facility that has a history of water damage or HVAC problems may initially be placed on a 30-day evaluation cycle and later, as maintenance requirements subside, the cycle may be extended. FMs must perform the following actions: Monitor the facility for signs of water damage (e.g., spotted ceiling tiles, water marks near windows/doors/damp floors, etc.) Check for signs of condensation and/or suspected mold growth around diffusers or HVAC vents. Keep air-conditioning drip pans clean and the drain lines unobstructed and flowing properly. Before a mold or water damage remediation project begins, the FM, in coordination with the Bioenvironmental Engineering (BE), and CE, shall notify the building occupants and the building’s organizational commander in the affected area(s). The notification must include a description of the planned remedial measures and an estimated completion date, along with list of points of contact for any occupant health concerns. If a FM receives occupant health complaints, they will refer the potentially affected personnel to their medical provider for evaluation and care. Conduct building surveys following rain events to document condensation and wet spots. Submit a service request to repair moisture problems (See procedure described in Attachment A). Attachment C addresses response activities for wet building materials. 3.9 Energy Conservation and Awareness FMs must promote sound energy conservation practices within their facility. FMs know their facility and users the best and are often in the best position to identify ways to improve energy usage based on their unique situations. FMs work with the installation Energy Manager for ways to improve energy conservation in their facility. See the BPL page – FM Energy Management, for more energy conservation ideas from around the AF. 3.10 Reserved Parking FMs are usually the POC for the installation when it comes to reserved parking at their facilities. There are regulations that cover reserved parking that FMs will be aware of. Army 18 | P a g e Air Force Civil Engineer Facility Management Playbook Regulation (AR) 190-5 (AF I31-218), UFC 3-120-01, and the Americans with Disability Act (ADA) are the primary regulations that cover reserved parking. Reserved parking are kept to a minimum on an installation. Reserved parking with names, ranks, or titles are avoided for Operations Security (OPSEC) purposes. Generic names (such as “visitor” or simply “reserved”) or office symbols are used as much as possible. Stand-alone signs or wall-mounted signs are discouraged. Curb markings and pavement markings being the preferred method. When requesting signs for personnel that are not regularly at the location (such as Wing/Commander (Wg/CC), signs that have a slide with removable tags are the preferred option to reduce the number of reserved spots and maximize flexibility of the reserved spots so that perhaps the sign can be used for a host of Distinguished Visitors (DVs), or not reserved at all when a DV is not expected. The ADA regulates handicapped parking spots. How many spots required, and the design of handicapped parking spots depends on the total number of parking spaces at the facility. FMs can consult the ADA Standards for Accessible Design (28 CFR Part 36) for additional information and the table showing the number of required accessible parking spots and submit a service request to CE if their parking lot is out of compliance. In addition to requesting and managing the reserved parking at a facility, FMs are sometimes also appointed as parking wardens. If assigned as a parking warden, a FM can issue parking tickets and call Security Forces (SFS) to request a boot be placed on vehicles that are in violation of parking requirements IAW AR 190-5. Check with the FMPM and/or Security Forces to see if this is a responsibility at the installation and to receive additional training as needed. 3.11 Continuity Book FMs serve as the focal point of their facility and are often balancing and juggling multiple things at once. Add in periods of absences such as PCS, leave, and TDY and it can be easy to see why continuity books are a necessity as an FM. Having a continuity book allows FMs to have a central place to store their information so their tasks can be picked up in case of an absence or transition to another person. FMs must have and maintain a continuity book. The local CE unit will dictate the exact method of this continuity book, but typically the following items are stored within: Most recent FM Appointment Letter. FM training slides. FM Handbook. Key Log. Log of service requests (manual or export from NexGen IT if used). List of upcoming Facility Projects. Results from FM periodic spot inspections. Fire Prevention/Safety paperwork (Fire Prevention Inspections, Safety Writeups/Inspections, Hazard ID forms). Known hazards (Asbestos Containing Material (ACM), Lead Based Paint (LBP), Radon, etc.). Emergency Management and Force Protection checklists (as appropriate). 19 | P a g e Air Force Civil Engineer Facility Management Playbook 3.12 Real Property FMs serve as the POC for real property issues in their facility as well. They must ensure that the facility is being used for its intended use. This means that the FM needs to be familiar with some real property terms and procedures. Facilities are categorized for their use by the Real Property Categorization System (RPCS). The RPCS is determined by the DoD and is assigned to a facility by the Real Property Officer (RPO) via the use of Category Codes (CATCODES). These CATCODES are a 6-digit number, and they determine a lot about a facility to include funding levels, funding types, importance of the facility to the mission, what fire and electrical codes to use, etc. It is very important that these CATCODES are accurate and current to ensure that the facilities are funded and given the resources needed to keep that facility operational. As an FM, it is important that one gets approval before initiating any changes in a facility. This is usually done via a space request, but the FMPM or RPO can explain how to change the space use within the facility. Note: In addition to space requests, some facilities on AF installations hold a historical building title. There are many rules when it comes to what can and cannot be done and how tasks can be done in historical buildings. Often these historical buildings are on state historical registries which means that each state has specific rules when it comes to these types of buildings. FMs in historical buildings need to know the local rules that govern their facilities so that they can plan accordingly. 3.13 Emergency Management (EM) The FMs and the unit EM representative(s), are responsible for creating their facility’s EAP and ensuring the plan can be enacted during an emergency. Items in the plan include: Shelter In Place (SIP) locations Evacuation locations and accountability procedures Egress routes HVAC shutoff procedures Force Protection Condition (FPCON) requirements SIP kits Procedures for reporting a fire or other emergency Procedures for employees that are required to stay behind and not evacuate FMs and EM reps review their installation’s IEMP 10-2 when developing their EAP procedures to ensure all logical risks are included in the plan. FMs, EM reps, and supervisors will need to train facility occupants on emergency procedures and conduct drills to ensure everyone knows what to do during an emergency. It may be advantageous for FMs to be a member of the Wing Inspection Team (WIT) or work with their unit to be excused from the initial stages of an exercise that tests EAPs so they can instead see first-hand what does and does not work with their EAP and modify it accordingly. 20 | P a g e Air Force Civil Engineer Facility Management Playbook 3.14 Generators If a facility has a generator, the generator must be tested at least semi-annually. When the generator is tested, the FM must verify that all circuits powered by the generator have been switched over from commercial power within the facility. This usually involves walking the facility and testing key items and systems within the circuits to ensure that they have power. When it is time for a generator test, CE will contact the FM and provide them the date and time in advance so that scheduling conflicts can be worked out. If a conflict cannot be worked out, FMs must route a waiver for the semi-annual test to the appropriate authority, usually the Major Command/Deputy Commander (MAJCOM/CD). If a unit in the facility requests that their personnel be trained on how to operate the generator, they will contact the FMPM to schedule the training for all personnel that the unit designates. FMs must maintain a list of all personnel trained on the generator. 3.15 Fuel Tanks Facilities that have fuel tanks are required to appoint a fuel tank custodian. Examples include facilities with generators and gas stations. While Fuel tank custodians are not required to be Facility Managers, per AFMAN32-1067, Water and Fuel Systems, FMs must report suspected fuel releases and follow-up if there are two consecutive months of excessive inventory variances. 21 | P a g e Air Force Civil Engineer Facility Management Playbook Chapter 4 Unaccompanied Housing Facility Management In addition to the tasks above, Unaccompanied Housing Managers (UHMs) and Airman Dorm Leaders (ADLs) have additional Facility Management tasks levied upon them due to the unique aspects of dormitories and their impact to Quality of Life (QoL) for the force. This chapter discusses those tasks and provides guidance on how to meet the tasks outlined in AFI 32-6000. Work Orders: As with normal facilities, ADLs, as FMs, will submit all requester driven work requests to CE via the methods in place at the installation. There are several methods that ADL’s have created to obtain work requests from dorm occupants. See the BPL page – FM Unaccompanied Housing, for some of these methods and the steps to implement them. 4.1 Inspections When conducting monthly walk-throughs of the facilities as mentioned in chapter 4, UHM’s must conduct an inspection of at least 10% of the total rooms. This would mean that each room needs to be inspected at least once a year. When determining what rooms to inspect, UHM’s prioritize personnel that are on extended TDY’s, such as deployments, to ensure that any issues that in these rooms are noticed and addressed before becoming a major issue. After that, UHM’s divide the remainder of their rooms by 12 and inspect these rooms on a recurring basis. All rooms in the UHM inventory must be inspected and UHM staff must work with the occupants to conduct the inspections. Facility Maintenance Inspections are specifically conducted to spot any health, life or safety concerns for the facility itself and must not be used as a shield for other purposes. Items to inspect and look for are covered in AFI 32-6000 and in the checklist found in the AFCEC COOM BPL page – FM Unaccompanied Housing. These inspections require prior notice to the occupant and must not be invasive to the occupant. Facility Maintenance Inspections only look at the facility itself and must not go into Airman’s personal belongings (unless needed to check on the facility). Examples: It would be OK to enter into an Airman’s closet or move items in a closet in order to visually inspect all walls for mold, but it would be inappropriate for a UHM to open drawers of furniture, wardrobes, or desks as this would not be needed to check the condition of the facility itself. If, during the course of a Facility Maintenance Inspection, unauthorized or illegal items are found in plain sight, UHMs must contact the appropriate authorities (usually the First Sergeant and/or Security Forces) to handle the situation. Due to the personal nature of private rooms and the legalities of entering private quarters, facility room inspections must occur by the UHM staff and not with Bay Orderlies or other augmentees. Recordings of room inspections may be permitted to ensure a burden of proof or records of inspections, but these recordings must be secured and personnel outside of the direct UIHM staff must not be allowed access to the recordings unless for legal or disciplinary reasons. 4.1.2 Inspection Criteria AFI 32-6000 lists several items that UHM staff must inspect in their facilities. The AFCEC/COOM BPL page – Unaccompanied Housing, has a standardized checklist that UHMs modify to meet their specific needs. 22 | P a g e Air Force Civil Engineer Facility Management Playbook 4.1.3 Inspection Simulation Click below to launch the inspection simulation. This is an opportunity to apply the knowledge gained from the playbook. A certificate of completion will be awarded once the proficiency minimum of 190 points is achieved. 4.2 Change of Occupancy Maintenance (COM) IAW AFI 32-6000, when a resident terminates their quarters, Unaccompanied Manager (UM) staff must accomplish a pre-final inspection with the resident (or Commander/First Sergeant in rare cases). During this time, UHM staff compare the current room condition with the room condition when the occupant checked into the room. The goal is to annotate all problems with the room and to submit repair/maintenance requirements to the local CE unit so that the room can be readied before a new member occupies the room. UHM staff annotate the room in the enterprise Military Housing (eMH) program as down for maintenance until the repairs are made so that occupants are not moved in prior to the repairs being made. When damages are noted, UHM staff take the appropriate action as noted below. Note: This playbook only details facility maintenance type of work and does not cover non- real property related items (such as shower rods, furnishings, appliances, etc.) Normal wear and tear facility maintenance: For normal wear and tear, UHM staff visit the local CE unit’s U-Fix-It store to obtain the materiel needed to bring the room to ready state. Normal wear and tear facility maintenance COM will take no more than 4 hours’ worth of repair/maintenance with the room being down for no more than 72 hours. Normal wear and tear facility maintenance usually consists of nail holes, oiling of hinges/lock mechanisms, small chips in plaster, or loose grouting. 23 | P a g e Air Force Civil Engineer Facility Management Playbook Life-cycle maintenance: All facility components have a life-cycle, with varying degrees of years needed before the component needs to be replaced. Most are taken care of during facility renovations, however some, such as paint or carpet, may need to occur in between renovations. UHM staff work with their CE R&O section to determine when these types of maintenance need to occur and schedule with them as occupants leave to minimize occupant disruption and move costs and maximize Inventory and Utilization (I&U) rates. For life-cycle maintenance, local CE units will usually not have the manpower to be able to accomplish the work in a timely manner. In these cases, UHM staff and the R&O section work together to set up an Indefinite Delivery, Indefinite Quantity (IDIQ) or Blanket Purchase Agreement (BPA) type of contract to have an outside contractor perform these actions. See the BPL page – Unaccompanied Housing, for sample contracts that can be used for these purposes. Damages: When the UHM staff notices damages outside of normal wear and tear, they must take immediate action before the member departs (especially if the member is separating). UHM staff must contact the CE R&O section to obtain a cost estimate for the repairs and utilize the cash collection processes in AFI 32-6000 to obtain the funds necessary to return the room to a functional condition. The cash collection voucher must only cover damages outside of the normal wear and tear and life-cycle maintenance. Life-cycle maintenance costs will not be charged to the individual if the component is already scheduled for replacement. 4.3 Locks and Keys Dorms are complex facilities with many locks and keys that must be managed by the UHM office. Many UH offices have switched locks from traditional mechanical key locks to other types of locks to include card swipes, key fobs, or digital combinations. Traditional key locks are the preferred in dorm facilities however, due to ease of maintenance and repair and lower overall maintenance costs. If a dorm facility switches to one of these types of specialized lock systems, it is usually no longer maintained by the local CE unit as it becomes specialized equipment and not real property. One of the better methods of key control in dorm facilities include the use of digital key vaults. These combine physical keys with a digital method to allow remote access to occupants without the need of the UHM staff. If utilized, only the vault itself would be considered specialized equipment, with the actual door locks and keys still being a traditional CE real property asset. See the BPL page – FM Unaccompanied Housing, for different product options for these types of systems. 4.4 Inventory Change Requests (ICRs) When submitting an ICR for dormitory facilities, documentation will need to be provided in the enterprise military housing (eMH) system. What documentation is needed will depend on the ICR submitted. When bringing a dorm out of eMH for a major renovation, attach a screenshot of the project from NexGen IT on bases that utilize NexGen IT (see below figure), or an AF332 for installations that utilize ACES-OPS Interim Work Information Management System (IWIMS) or other systems. For more information on ICRs, please visit the eMH support module, or the AFCEC Housing website. 24 | P a g e Air Force Civil Engineer Facility Management Playbook Figure 4: NexGen IT Project Page Note: When bringing a dorm back from a major renovation, attach a fully signed DD1354 from the renovation project, along with a new floor plan of the facility. ADL’s check with their CE Flight for an updated floor plan from the project. 25 | P a g e Air Force Civil Engineer Facility Management Playbook Chapter 5 Facility Management (FM) Program Management Several of the forms and documents referenced in this playbook are located in the Reference Section to the right of the Playbook narrative on the CE Portal or located within the BPL associated with this section. The references are separated by section on the CE Portal. If the document is referenced in Section 1, then Section 1 must be visible in the narrative screen to show the applicable references. Figure 4: CE Portal Homepage 5.1 Roles and Responsibilities Roles Responsibilities CE Commander Provides the FM program support. Facility Manager Manages and updates FM database. Program Manager Trains primary and alternate FMs. (FMPM) Manages the FM appointment process. Manages the unit online FM information repository. Disseminates information to FMs as necessary. Reports Key Performance Indicators (KPIs) on the program to leadership. Manages the FM Handbook and local FM policies. Table 3: FM Roles and Responsibilities FM Program Management: The CE FMPM, normally a 3E6X1 (E-5 or above or civilian equivalent) within Requirements and Optimization (R&O), manages the installation Facility Management Program. The FM program at an installation works with and provides CE guidance to military FMs of every rank and armed service, contractors, and civilians. They help successfully manage every facility on an installation and ensure numerous laws and regulations are followed in regard to real property, work management, fire, safety, and environmental concerns. It is vital that the FMPM can clearly communicate CE goals and strategic communication with all total service customers. The FMPM is responsible for the successful implementation of the FM program at the installation/unit to which they are assigned to. Successful FM programs incorporate the following plans of actions: Appointment Process Training 26 | P a g e Air Force Civil Engineer Facility Management Playbook Online Repositories of Information FM Handbooks and Local Policies Energy Conservation and Usage Facility Visits Environmental Considerations KPIs 5.2 FM Appointment Process While Unit Commanders are responsible for their unit’s FMs, the FMPM is responsible for the overall appointment process to include the submittal process, updating the FM listing, notifying the appropriate installation agencies, filing records, and removing previous FM’s from NexGen IT and FM databases. The FM appointment submittal process includes a central email inbox accessible for multiple people to receive appointment letters. This email address is well broadcasted to FM’s. Once a letter is received, the letter is validated based on the required information listed below: Date Facility Number Majority and minority unit(s) of the facility First, middle initial, last name of FMs Official email address DSN phone Home phone Privacy Act Statement Commander’s signature (required on G-Series orders) Other suggested field information includes: Certification of initial FM training Acceptance of FM job responsibilities Once the letter is validated and accepted, the FMPM must update the FM database. The current process recommendation is to manage the FM Database outside of NexGen IT. This is done within 7 days of receiving the letter. See the BPL page – FMPM FM Management, for FM database solutions. The FM database is sent to the Fire Department, BDOC, and Command Post on a weekly basis to ensure FM’s can be contacted during off-duty hours if necessary. The letter is then filed in accordance with local records management policy as a matter of official record. FM letters contain Personal Identifiable Information (PII) and must not be placed in locations that may jeopardize that information. Review AFI 33-332, Air Force Privacy and Civil Liberties Program or the unit’s record custodian for more information on appropriate filing locations. 27 | P a g e Air Force Civil Engineer Facility Management Playbook The FMPM is a person records manager within NexGen IT, as applicable. Prior to disposing of previous FM appointment letters, the FMPM must suspend old FM’s from NexGen IT. The member’s account is automatically locked after 30 days of not logging into NexGen IT. Do not rely on the 30-day rule; a user with an FM role could receive a Permanent Change of Station (PCS) to another installation and login to NexGen IT within the 30-day window. Each year, on the anniversary date of the FM’s appointment, the FMPM sends a revalidation letter (see example on the BPL page – FMPM FM Management) to the FM to update their contact information and ensure the FM processes the SAAR revalidation request. 5.3 FM Training The FMPM is responsible to ensure a robust training program exists for FM’s. Successful FM programs incorporate several tiers of training based on the experience of the FM: Initial training, local procedures, and annual revalidation. FM’s must not be given access to NexGen IT without successfully completing a training tier. Initial training typically consists of the FM completing the FM computer-based training (CBT) located on the AFCEC Virtual Learning Center (VLC). Initial training must be completed prior to the prospective FM being assigned as a FM. Figure 5: VLC Welcome Page The second tier of training (local FM training) is usually conducted by the FMPM with the assistance of local program management experts in areas such as the fire department, safety, and environmental. This is held within 45 days of an FM being assigned. Face-to-face methods are typically best for this training to allow question and answer sessions and to better engage with the FM. See the BPL page – FMPM FM Training, for other methods to conduct this training. The third tier of training is an annual revalidation. This is often in the form of a slideshow that just shows changes made to the program or CE policies over the last year. This slideshow is updated as changes occur, with changes over a year old being removed. This ensures the training is always relevant to the FM. 28 | P a g e Air Force Civil Engineer Facility Management Playbook Note: FM’s that do not attend their required training will have their NexGen IT account suspended and have non-emergency service requests rejected until training is completed. The FM submits a SAAR to request access to NexGen IT (if fielded at the installation), selects the FM role, and submits non-emergency requirements, called Service Requests (SRs) through NexGen IT (when available). The FM will call Emergency SR’s into the appropriate supporting unit and not solely rely on submitting the request through applicable IT systems or external electronic processes. Refer to the BPL page – Facility Manager SAAR, for guides on the SAAR request process. 5.4 Information Repositories As prescribed by the Secretary of the AF, Office of Business Transformation (SAF/MG), all AF CE units with FM program management responsibilities create and maintain an online repository (e.g., SharePoint) of FM program information, related training materials, and any other FM information and advertise the location to FMs. Where there is no capability to provide a SharePoint location, use an alternative method, such as an e-mail distribution list to provide weekly status updates. FMPM’s are responsible for maintaining their unit’s FM information repositories. Care is given to ensure that this site remains updated with relevant information for FMs. Examples of information that is included in the repository include: Contact Information. Calendars - include utility outages, training dates, down days, minimum manning days, Fire Prevention Visits, etc. Document Library(s) – include local policies, snow control, how to guides, forms, sample appointment letters, training, etc. U-Fix-It Inventories. Service Contract POCs. Process for AF103 Base Civil Engineer Work Clearance Request. Announcements. Feedback Mechanism. Maps. Sanitized FM Listing. Digital Facility Files/FM Continuity Books. Environmental Information (facilities with Asbestos, Lead Installation Paint, guides on disposal of hazardous waste, etc.). Fire Prevention Information. Emergency Management. 29 | P a g e Air Force Civil Engineer Facility Management Playbook 5.5 FM Handbooks and Local Policies CE Units must create local FM handbooks and local policies that serve as a quick reminder and/or reference to FMs on the installation. The FMPM is usually the focal point for the review and dissemination processes to ensure continuity between policies and to gain feedback from FMs prior to publication. In addition, the FMPM is included in the review process of all support agreements on the installation to ensure local policy is taken into consideration. Local handbooks and policies are compiled in one location that is accessible to FMs on the installation. When updating FM training or handbooks, local single policy letters are incorporated into the revision to allow one document that contains all unit/installation policy instead of having numerous policy letters for FMs to review. See the BPL page – FMPM FM Handbook, for examples and templates for FM Handbooks as well as examples of local policies. As a part of the review process, FM Handbooks and policies must be reviewed by respective local program managers and local unit leadership. This ensures CE is speaking on one page in regard to policies and procedures and will also help to provide top cover for the section that created the policy or procedure. 5.6 Energy Conservation and Usage Air Force Manual (AFMAN) 32-1061 requires that FMs aid in compliance with energy policy directives and guidance. FMPM’s must disseminate information to the installation FM’s with the assistance of the Installation Energy Manager. Information considered includes energy tips, planned utility outage notices, and updates on current utility outages. Consider adding a calendar to the repository for easy access for planned outages and energy usage tips. 5.7 Facility Visits While not every unit has the manpower, having a facility visit team (sometimes also known as a “1219 team” or “SMART” team) can help AF facilities stay well maintained and in good repair. Facility visit teams can proactively find problems before they occur, keep emergency calls down, save time by completing several work tasks at once, and bring positive customer feedback to the CE unit. If not possible for the entire installation, consider focusing on high- maintenance facilities such as dormitories. FMPM’s work with their Operations Flight leadership to evaluate whether this type of team would be beneficial, and whether their units can support this type of team. 5.8 Environmental Considerations Serving as the facility focal point, FMs play a key role in the environmental protection and awareness to occupants within the facility. A successful FM Program will provide information on hazards associated within their facility. These hazards include ACM, Radon, LBP, Universal Waste (UW), disposal of hazardous waste, and mold. FMPM’s must include these topics in their program as applicable. FM training includes the above topics to include locations commonly found, hazards associated with them, and what to do if unknown hazards are suspected. In addition, FM’s must be informed if asbestos locations are known in their facilities. FM information repositories contain known listings of ACM, LBP, and Radon in addition to policies regarding mold remediation and universal waste 30 | P a g e Air Force Civil Engineer Facility Management Playbook storage. FMPMs, along with unit leadership, must coordinate with the local CE Environmental Element (CEIE), BE Flight, and safety offices when determining policy to ensure the safety of all installation personnel. 5.9 Emergency Management FMs must also be trained on Emergency Management (EM) procedures. AFI 10-2501 states that FMs, along with their EM representative, must work together to create EAPs for their facility. This could include tasks such as creating and stocking Shelter-In-Place rooms, creating checklists for facility occupants and Unit Control Centers (UCCs), Force Protection Condition (FPCON) procedures, or other Installation Emergency Management Plan (IEMP) 10- 2 tasks. FMPMs must work with their local EM flight to determine the exact processes for their installation and brief FMs appropriately. 5.10 Generator Maintenance Generator maintenance itself is performed by CE, however FMs may schedule hands-on- training for building occupants on associated generators and what their responsibilities include (See AFMAN 32-1062). FMPMs have a list of facilities that have generators and work with the CE power production shop and FMs to have this training when FMS and/or their units request it. FMs must also be trained on procedures to waive semi-annual generator tests when mission needs dictate. 5.11 Key Performance Indicators Successful FM programs are guided by several Key Performance Indicators (KPIs). These KPI’s help gauge areas in an FM program that may be strong, weak, or outstanding. Below are some useful KPI’s to gauge an FM Program. % FM’s trained. % FM trained (by unit). % Trained within 45 days of assignment. # FM’s with overdue training. # Facilities with no FM’s. # of phone calls received by R&O (if using NexGen IT) vs. Emergency Work Tasks. Program Elements implemented, as described throughout this chapter. Visit the BPL page – FMPM Key Performance Indicators, for how-to-guides to retrieve these KPI’s, information on how to understand and use the KPI’s, and sample slides to show the FM KPIs for various meetings. 31 | P a g e Air Force Civil Engineer Facility Management Playbook Appendix A - Acronyms and Definitions Acronym Definition AA&E ARMS, Ammunition and Explosives ADA Americans with Disabilities ADLs Airman Dorm Leaders ACM Asbestos Containing Material AF Air Force AFCEC Air Force Civil Engineer Center AFI Air Force Instruction AFMAN Air Force Manual BE Bioenvironmental Engineering BDOC Base Defense Operations Center BPA Blanket Purchase Agreement BPL Business Process Library CAC/PIV Common Access Card/Personal Identity Verification CATCODEs Category Codes CBR Contract by Requester CBT Computer-based training CC Commander CD Deputy Commander CE Civil Engineering CEO Operations COM Change of Occupancy Maintenance COR Contracting Officer’s Representative DCPDS Defense Civilian Personnel Data System DoD Department of Defense DV Distinguished Visitor EAP Emergency Action Plan EM Emergency Management eMH Enterprise Military Housing FBPTA Federal Buildings Personnel Training Act FM Facility Manager FMPM Facility Manager Program Manager FPCON Force Protection Condition GSA General Services Administration HIPPA Health Insurance Portability and Accountability Act IAW In Accordance With I&U Inventory and Utilization ICR Inventory Change Request IDIQ Indefinite Delivery, Indefinite Quantity IT Information Technology IWIMS Interim Work Information Management System KPIs Key Performance Indicators LBP Lead Based Paint MAJCOM Major Command NAF Non-appropriated Funds OPSEC Operations Security PCS Permanent Change Station PII Personal Identifiable Information 32 | P a g e Air Force Civil Engineer Facility Management Playbook Acronym Definition POC Point of Contact PWS Performance Work Statement QoL Quality of Life R&O Requirements and Optimization RoS Report of Survey RPCS Real Property Categorization System RP Real Property RPO Real Property Officer RPIE Real Property Installed Equipment SAAR System Authorization Access Request SAF/US(M) Secretary of the AF, Office of Business Transformation SME Subject Matter Expert SFS Security Forces SIP Shelter in Place SOW Statement of Work SPOC Service or Agency Point of Contact SRs Service Requests TASM Trusted Associate Security Manager TASS Trusted Associate Sponsorship System TDY Temporary Duty UCC Unit Control Center UFC United Facilities Criteria UHMs Unaccompanied Housing Managers UM Unaccompanied Managers UW Universal Waste VLC Virtual Learning Center WIT Wing Inspection Team 33 | P a g e Air Force Civil Engineer Facility Management Playbook Appendix B - Master List of Links Location Content Web Address Chapter 1 https://static.e-publishing.af.mil/production/1/af_a4/publication/afi32- Chapter 1, Sec. 1.1 AFI 32-1001 1001/afi32-1001.pdf Chapter 3, Sec. 3.2 Chapter 1 https://usaf.dps.mil/teams/10041/CEPlaybooks/OE/Documents/CEOE% Operations 20Playbook_Final.pdf; Engineering https://s3.console.aws.amazon.com/s3/buckets/afce-operations- Playbook engineering?region=us-east-1&tab=objects Chapter 1 https://usaf.dps.mil/sites/11252/24048/CO%20Support%20TRIRIGA%2 Ops BPL 0Deploy/TRIRIGA%20Ops%20Wiki/Work%20Management%20Business %20Process%20Library.aspx Chapter 1 CE Portal NexGen https://nexgenit.csd.disa.mil/vdesk/hangup.php3 IT Chapter 1, Sec. 1.1 Chapter 4 Chapter 4, Sec 4.1 https://static.e-publishing.af.mil/production/1/af_a4/publication/afi32- AFI 32-6000 Chapter 4, Sec 4.1.2 6000/afi32-6000.pdf Chapter 4, Sec 4.2 Chapter 5, Sec. 5.1 Chapter 2, Sec. 2.2 https://usaf.dps.mil/teams/10041/CEPlaybooks/WM/Pages/Overview.a Work spx; Management https://s3.console.aws.amazon.com/s3/buckets/afce-work- Playbook management?region=us-east-1&tab=objects Chapter 3, Sec. 3.3 DoD 7000.14-R https://comptroller.defense.gov/FMR/vol12_chapters/ Vol 12 Chap 7 Chapter 3, Sec. 3.3 https://www.wbdg.org/ffc/dod/unified-facilities-criteria-ufc/ufc-3-120- UFC 3-120-01 Chapter 3, Sec. 3.11 01 Chapter 3, Sec. 3.6 https://static.e- publishing.af.mil/production/1/af_a4/publication/dafi31- 101/restricted_access.pdf DAFI 31-101 Note: The OPR has restricted access to this product, it is either served from our Warehouse Management System (WMS) or stocked and issued by the OPR. Check WMS for availability first, if not found, then contact the OPR to request a copy. Chapter 3, Sec. 3.6 https://www.e-publishing.af.mil/Product- AF Form 2432, Index/#/?view=form&orgID=10141&catID=8&low=2400&high=2499&m Key Issue Log odID=449&tabID=131 Chapter 3, Sec. 3.6 https://www.navfac.navy.mil/content/dam/navfac/Specialty%20Center UG-2045-SHR s/Engineering%20and%20Expeditionary%20Warfare%20Center/DoD_Lo ck_Program/PDFs/UG-2045-SHR.pdf Chapter 3, Sec. 3.7 https://static.e- AFMAN 91-203 publishing.af.mil/production/1/af_se/publication/afman91- 203/afman91-203.pdf Chapter 3, Sec. 3.7 http://static.e-publishing.af.mil/production/1/8fw/publication/8fwi32- AFI 32-2001 2001/8fwi32-2001.pdf Chapter 3, Sec. 3.10