OM107 Facilities Management Lecture Notes PDF
Document Details
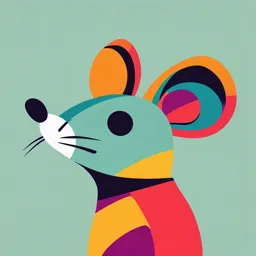
Uploaded by VeritableMoose8225
AGCortez
Tags
Summary
These notes cover OM107 Facilities Management, Lecture 2, focusing on product, process, and schedule design. The document details the relationship between these elements and how they relate to facilities planning, including considerations and examples.
Full Transcript
OM107- Facilities Management Lecture No.2 Product, Process, and Schedule Design Prepared by: AGCortez Introduction Product, process, schedule, and facilities design decisions are crafted related and sequential to each other. In this chapter, we focus on the produ...
OM107- Facilities Management Lecture No.2 Product, Process, and Schedule Design Prepared by: AGCortez Introduction Product, process, schedule, and facilities design decisions are crafted related and sequential to each other. In this chapter, we focus on the product, process, and schedule (PP&S) design functions as they relate to facilities planning. Product Design Involves both: the determination of which product are to be manufactured the comprehensive design of individual products The design of a product is influenced by aesthetics, function, materials, and manufacturing considerations. Marketing, purchasing, industrial engineering, manufacturing engineering, product engineering, and quality control, among other factors, will likewise influence the design of the product. In the final analysis, the product must meet the needs of the customer. Product Design (continued) The challenge of meeting customer needs can be accomplished through the use of quality function deployment QFD is an organized planning approach to identify customer needs and to decode the needs to product characteristics, process design, and tolerance requirements. Benchmarking is used to identify what the competition is doing to satisfy the needs of customers or to exceed customer expectations. It can also be used to identify best practices from the most successful organizations. Comprehensive operational specifications, pictorial representations, and prototypes of the product could also be utilized by facilities planner as essential inputs. Photographs and drawing can also be used to show how the products is assembled. Process Design Determination of how the product is to be produced. Who should do the processing? (Which part of the products should be made?, should product be subassembly, or part be produced in-house or subcontracted to an outside supplier or contractor? The “make-or-buy” decision?.) How the part will be produced? Which equipment will be used? (for the parts which will be made in-house) How long will it take to perform the operation? Production methods are the most fundamental factor affecting the physical layout. Process Design (continued) Within the process design, we need to consider following issues; 1. Process identification Make-or-buy analysis Parts identification 2. Process selection How the product will be made (operations, equipment, raw material, etc.) 3. Process sequencing How components are put together Process Design – Process Identification Make-or-buy analysis How are the make-or-buy decisions made? Can the item be purchased? Should we go for subcontracting? Can we make the item? Is it cheaper for us to make than to buy? Is the capital available so that we can make it? Managerial decisions requiring input from finance, industrial engineering, marketing, process engineering, purchasing, human resources, etc. Process Design – Process Identification The input to the facility planner is a listing of the items to be made/purchased. Parts list – component parts of a product: part numbers part name number of parts per product drawing references Bill of materials - structured parts list: contains hierarchy referring to the level of product assembly In a manufacturing, process identification consists of (a) a parts list indicating what is to be manufactured, (b) component part drawings describing each component, and (c) the quantities to be produced. Process Design – Process Identification Process Design – Process Identification Process Design – Process Selection How the product will be made (operations, equipment, raw material, etc.) 6 steps; Identify fundamental operations Define substitute process for each operations (manual, mechanized or automated) Analyze substitute processes (unit production time, equipment utilization, alternative equipment types) Standardize the process (utilization of inputs) Evaluate substitute process (economic evaluation) Select processes (flexibility, versatility, reliability, maintainability, and safety) Process Design – Process Selection Computer aided process planning (CAPP) can be used to automate the manual planning process. There are two types of CAPP systems: Variant CAPP, standard process plans for each part family are stored within the computer and called up whenever required. Generative CAPP, process plans are generated automatically for new components without requiring the existing plans. Selection of these systems basically depends on product structure and cost considerations. Typically, variant process planning is less expensive and easier to implement. Process Design – Process Sequencing Route sheet provides information on production methods, It identifies processes, equipment and raw materials Process Design – Process Sequencing Assembly chart determines how components are put together. Process Design – Process Sequencing Operation process chart – gives an overview of the flow within the facility A combination of route sheets and assembly charts Schedule Design How much to produce and when to produce? Production quantity decisions (lot size decisions); determining when to produce is referred to as production scheduling. In addition to how much and when to produce, it is important to know how long production will continue. Such a determination is obtained from market forecasts. Schedule design decisions are influenced by machine choice, number of machines, number of shifts, number of employees, space necessities, storage equipment, material handling equipment, personnel requirements, storage policies, unit load design, building size, and so on Facility Layout and Design Facility layouts refer to how workers, machines, equipment, and products are organized in a facility. The basic objective of layout is to ensure a smooth flow of work, materials, and information throughout the system. The key to good facility layout and design is the integration of the needs of people, materials, and machines in such a way that they create a single and well functioning system. Two distinct types of layout: product layout, and process layout. Factors in Determining Layout and Design 1) Ease of future expansion or change 2) Flow of movement 3) Materials handling Output needs Space utilization Shipping and receiving 4) Ease of communication and support 5) Impact on employee moral and job satisfaction 6) Promotional values 7) Safety Credits Camilar-Serrano, Angelita O., Facilities Planning and Management (2016), Unlimited Books Library Services and Publishing, Philippines Lapides, Paul D., Facility Management (2006), Wiley and Sons Inc. Roper, Kathy & Payant, Richard, Facilities Management Handbook (2014), AMACOM Varied online sources Getty Images from Google fppt.com