Supply Chain Management Overview PDF
Document Details
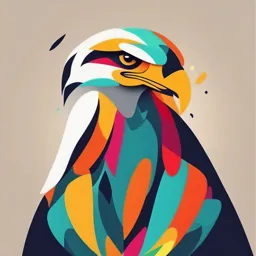
Uploaded by TopNotchBallad
Rutgers University
Tags
Summary
This document provides an overview of supply chain management, detailing the key processes from sourcing to delivery. It covers topics like logistics, warehousing, transportation, the SCOR model, and discusses forecasting techniques within the context of supply chain planning and operations. The content is aimed at explaining the fundamental aspects of managing materials, information, and finances within a supply chain.
Full Transcript
What is supply chain Any organization offering a product or a service has a supply chain.\ Products and Services are created from materials, equipment,\ labor, time, money, and other resources. Products and services need suppliers, manufacturers, and customers; all of\ which make up a supply chain...
What is supply chain Any organization offering a product or a service has a supply chain.\ Products and Services are created from materials, equipment,\ labor, time, money, and other resources. Products and services need suppliers, manufacturers, and customers; all of\ which make up a supply chain. A supply chain can be very simple or it may be very complex.\ Supply chains exist in organizations that are:\ -- Large or Small\ -- Public or Private\ -- For-Profit or Not-for-Profit A diagram of manufacturing products AI-generated content may be incorrect. - Logistics is part of supply chain management that plans, implement and controls the flow of storage of goods, from point of origin to point of consumptions. - Warehouse is a facility that allows a company to store materials and finished products. - Warehousing is the function that allows a company to receive, store, withdraw, package, and ship items to a manufacturing location or finished products to a customer. - 5 ways: Truck, Rail (most capable), Air (most expensive), Pipeline(cheapest), Water (the longest) (ocean/deepwater, intercoastal, inland waterways) - Intermodal is using a combination of any other transportation modes for a single shipment. Rolling a truck transport into a ship transport without unloading the truck. Everyone benefits from the supply chain Public, private, small, and big Corp companies with lots of inventory benefit the most. Benefits of Supply Chain Management\ ♣ Improved customer service\ ♣ Increased revenue\ ♣ Lower costs\ ♣ Better asset utilization\ ♣ Adds customer value / retain customers\ ♣ Minimize delays / shorter lead-times\ ♣ Elimination of rush (unplanned) activities\ ♣ Reduced uncertainty throughout the supply chain\ ♣ Lower inventory levels throughout the supply chain\ ♣ Ability to effectively respond to disruptions and conflicts\ \ \ Who benefits the most from supply chain management?\ Firms with:\  Large inventories\  Large number of suppliers\  Complex products and/or large number of products\  Large purchasing budgets / expenditures *The goal of Supply Chain Management is to:\ - Increase Customer Service\ \*\* while simultaneously \*\*\ -Reducing both:\ -- Inventory Investment and\ -- Operating Expenses (i.e., costs)\ * *In line with this goal, the two main reasons that firms\ implement Supply Chain ManagementSupply Chain Management are to:\ 1. achieve cost savings\ 2. better coordinate resources*  Supply chains are generally described as spanning from end-to-end, i.e., from your\ suppliers-suppliers on one end, through your internal operations, and out to your\ customers-customers on the other end Basic supply chain model: plan, source,make,deliver,enable Most supply chains are enabled through various types of processes and technologies Enabling flows continuously through the supply chain. **Scor Model: Plan** - Planning establishes the parameters within which the supply chain will operate - Planning includes the determination of: \- Marketing and distributive channels \- Promotion \- Quantities \- Timing -Inventory and replenishment policies \- Production policies **Scor Model: Source** - Sourcing is the process of identifying the suppliers that provide the materials and services needed for supply chain to deliver the finished products desired by customers. - This phase helps identify reliable suppliers but also build strong relationships with those suppliers. - Supply chain managers must also develop pricing, shipping, delivery and payment process with suppliers and create metrics for monitoring and improving the performance. **Scor Model: Make** - Make or Manufacturing is the series of operations performed to convert materials into a finished product - Finished product is manufactured, tested, packaged and scheduled for delivery. - Quality management is an important aspect of manufacturing process. - This is the most metric-intensive portion of supply chain, where companies are able to measure quality levels, production output, and worker productivity. **Scor Model: Deliver** - Logistic Phase is part of supply chain management that oversees the planning and execution of the forward flow of goods and related information between various points in the supply chain to meet customer requirements. - Where companies coordinate the receipt of orders from customers, develop a network of warehouses, pick carriers to transport products to customers, and set up an invoicing system to receive payments, among other aspects. **Scor Model: Return** - Reverse Logistics this is the part of supply chain management that deals with planning and controlling the process of moving goods from Point of consumption back to point of origin for repair, reclamation, remanufacture, recycling, or disposal - As this process goes against the normal outbound flow of products to marker, the supply chain managers have to crease a responsive and flexible network for receiving defective and excess products back from their customers and supporting customers who have questions or problems. - Enable processes facilitate a companys ability to manage supply chain and are spead through out every stage. - This stage DOES NOT occur sequentially like others. - Enabling processes include elements such as: - Supply Chain systems and network operations - Supply configuration control - Interfaces - Gateways - Database administration - Electronic data interchange (EDI) - Telecom. services - Performance measurement - Contract management - Business rules - Standards - Training and education Just-in-TimeJust-in-Time is a philosophy of manufacturing based on the\ planned elimination of all waste and continuous productivity\ improvement. Push or Make-to-Stock: Producing stock on the basis of anticipated demand.\ Demand forecasting can be done via a variety of sophisticated techniques. Push Business Model (anticipatory business model)(used by 95% of companies)  Advantages: If the manufacturer creates a good forecast and supply plan, the\ product is immediately available to ship to the customer on demand from the\ existing finished product inventory in the warehouse.\ Manufacturers also have the opportunity to plan resources better or with more\ flexibility, and can maximize the utilization of resources at the lowest cost. Disadvantages: High inventories (and capital tied up in inventory), dependency\ on forecasting, forecasting error creates non-value adding time, inefficiencies,\ obsolescence, shortages, and additional cost. Push business model (responsive model) (used by 5% of companies) -Advantages: High levels of customer service through responsiveness and\ flexibility to meet uncertain customer demand.\ Pull models have short lead times, reduce dependency on forecasting, use short and\ flexible production runs, store very low inventories, reduce waste, provide\ opportunities for customization, and improve cash flow. -Disadvantages: Every order is basically a rush order, and any problems will lead to\ customer dissatisfaction.\ Pull models are highly dependent on customer relationships. They have a reduced\ ability to take advantage of economies of scale. Fast, responsive, flexible, robust and\ integrated systems and processes are a must for this model to work. Resource issues\ will have a significant and immediate impact on throughput and customer satisfaction.  Chapter 2 -Independent Demand is demand for an item that is unrelated to the\ demand for other items, such as a finished product, a spare part, or\ a service part. \[Demand for these items is Forecasted\] \[Demand for these items is Forecasted\] -Dependent Demand is demand for an item that is directly related to\ other items or finished products, such as a component or material\ used in making a finished product. \[Demand for these items is calculated) Finished product= bicycle (independent demand items) Component parks= frame, seat, handlebar, wheels, tires (dependent demand items) Forecasting and Demand Planning What is forcasting? - Are the key building blocks from which all supply chain planning activities are derived. Step 1. - Is forecasting where the forecast is developed through data analysis and judgment. -organizations need to have a formal forecasting process to develop an agreed-upon set of numbers that becomes the driver for demand planning What is Demand Planning Step 2. - Is Demand planning, where management and other experts within the company review the forecast to ensure that it\'s aligned with the company\'s strategy, business policies, and business knowledge, and make necessary adjustments. Forecasting techniques -Qualitative forecasting which is based on opinion and intuition (no data) -Quantitative forecasting uses mathematical models and historical data to make a forecasts. The five qualitative models used are:\ 1. Personal Insight\ 2. Jury of Executive Opinion- people who know most about the product and market place would likely form a jury\ 3. Delphi Method\ 4. Sales Force Estimation\ 5. Customer Survey Quantitative forecast techniques 1. Time series- based on the assumption that the future is an extension of the past. Historical data used to predict future demand (frequently used) 2. Cause and effect- assumes that one or more factors predict future demand.(seasonally used) A combination of both qualitative and quantitative techniques is recommended to be used. Bullwhip effect -- is a phenomenon describing how small fluctuations in the market, demand can get larger fluctuations as it goes to the retailer, wholesalers, distributor and manufacturer. To mitigate any disruptions, companies often carry an inventory buffer called safety stock. Second-guessing what is happening with ordering patterns and potentially overreacting creates the bullwhip effect. Starts from customer to supplier. Bullwhip and its effects Leads to discrepancies between inventory and demand. This often leads to an increase in production, which increases storage and labor costs, unmet customer demand, and product spoilage and obsolescence. Can be fixed by collaborative planning. Remember there is no single remedy. Naïve forecasting- sets the demand for the next time period to be exactly the same as the demand in the last period Naïve forecasting advantage: works well for mature products and is very easy to determine. Naïve forecasting disadvantage: works for mature products only. Any variations in demand will create inventory issues. Collaborative planning, forecasting,replenishment (CPFR)- Is a business practice that combines the intelligence of multiple trading partners who share their plans, forecasts, and delivery schedules with one another in a effort to ensure a smooth flow of goods across a supply chain. CPFR can significantly reduce the bullwhip effect (its safety stock and associated cost) by providing a plethora of benefits including better customer service, lower inventory cost, improved quality, reduce cycle time, better production methods. 1. Resource requirement panning- A long-range capacity planning schedule used to check whether aggregate resources are capable of satisfying aggregate production. You have to find the capacity. 2. Rough-cut planning- not long-term nor short-term planning; this is for case planning. So, in case something happens, they use this rough cut to check the feasibility of MPS. 3. Capacity Requirements Planning (CRP)- is a short-range capacity planning module used to check the feasibility of the material requirements plan. All these plans require all managers, workers, and the company to be monitored. In case things happen. Simple regression-attempts to model the relationship between a single independent variable and a dependent variable (demand) by fitting a linear equation to the observed data ex. If company invest in marketing they have to increase forecast. vs. multiple regressions- attempts to model the relationship between two or more independent variables and a dependent variable (demand) by fitting a linear equation to the observed data. Ex. If advertising is increased and price lowered then the demand will go up, if advertising is increased and the price also increased, the impact on demand is not as obvious. But the mathematics of multiple regressions can help predict demand. Aggregated production plan- hierarchical planning process that translates annual business marketing plans, and demand forecast into a production plan for a product family\* in a plant or facility. (one year plan) Aggregation plan difference from daily operations Cause and effects model Simple regression and Multiple regression \#major ERP providers are 1. Sap 2. Oracle, 3. Microsoft implementing ERP systems 1. Best of breeds- pick the best application for each individual function (disadvantage- software may not integrate well but may not be a major issue in future) Single integrator solution- pick all the desired applications from a single vendor Productions strategies (MTS,MTO,ATO,ETO): - Level production strategy- constant output rate - Chase production strategy- adjusts capacity to match demand - Mixed production strategy- maintains stable core workforce while using short term help. Level production vs chase production-Level maintains a constant level of production despite the demand variations, unlike chase who's production varies by demand. Cyclical variation- a wave like pattern that can extend multiple years and therefore cannot be easily predicted (business cycle, china growth, GDP) Tiers of suppliers. 1. Tier 1 suppliers are those who directly supply products and services to the primary company. 2. Tier 2 suppliers provide materials or components 3. Tier 3 suppliers are the suppliers of tier 2 Rough cut planning (RCCP)- used to double check MPS 1. Rough-cut planning- not long-term nor short-term planning; this is for case planning. So, in case something happens, they use this rough cut to check the feasibility of MPS. Mean absolute deviation (MAD)- measured the size of the forecast error in units. It\'s calculated as the average of unassigned Ie. Absolute errors over period of time. (no negative numbers) MAD = ∑(\|A -- F\|) / n\ Where:\ A = Actual demand\ F = Forecast demand\ n = Number of time periods Mean absolute percent error (MAPE)- measured the size of the error in percent terms. It\'s calculated by the average of the assigned percentage; people usually understand this forecast error better. MAPE = ∑ ((\|A -- F\|)/ A) / n\ (expressed as a percentage)\ Where:\ A = Actual demand\ F = Forecast demand\ n = Number of time periods Measured of forecasting accuracy (MSE)- magnifies the errors by squaring each one before adding them up and dividing by the number of forecast periods. MSE = ∑ (A-F) ² / n\ Where:\ A = Actual demand\ F = Forecast demand\ n = Number of time periods Chapter 1: Introduction to Supply Chain Management B. Lowering costs while improving customer satisfaction 2\. Which of the following best describes the flow within a supply chain? B. The interconnected movement of materials, information, and finances 3\. What distinguishes a service supply chain from a traditional supply chain? A. It does not involve the movement of tangible goods 4\. Which of the following are the components of the SCOR model? C. Plan, Source, Make, Deliver, Return 5\. What is a key characteristic of a pull-based supply chain model? C. Manufacturing occurs only when customer demand is confirmed Chapter 2: Forecasting and Demand Planning 6\. What is the main purpose of demand forecasting? B. To predict future demand and align resources accordingly 7\. Which of the following correctly differentiates qualitative and quantitative forecasting methods? C. Qualitative forecasting is preferred when historical data is unavailable or insufficient 8\. What is the Bullwhip Effect in supply chain management? B. The tendency for small demand fluctuations to cause larger shifts upstream in the supply chain 9\. Which metric is commonly used to measure forecast accuracy? C. Mean Absolute Deviation (MAD) 10\. Collaborative Planning, Forecasting, and Replenishment (CPFR) is used primarily to: C. Improve forecast accuracy and reduce inefficiencies in the supply chain Chapter 3: Supply Chain Planning 11\. What is the primary focus of long-range supply chain planning? C. Decisions related to facility locations and major investments 12\. Which production strategy adjusts production rates to match demand while maintaining minimal inventory? A. Chase Production Strategy 13\. In supply chain planning, what does Material Requirements Planning (MRP) primarily focus on? C. Scheduling and managing material procurement for production 14\. What is a key advantage of Enterprise Resource Planning (ERP) systems? B. They integrate various business functions into a unified system 15\. The Master Production Schedule (MPS) serves as: B. A detailed plan for production scheduling based on forecasts and orders **799:301 Introduction to Supply Chain Management** **Quiz Questions Q1** **Chapter 01** 1. Supply chain management starts with understanding the flow. A. True 2. The following diagram depicts the anticipatory business model (or push business model). A. False 3. It was intense global competition that led manufactures to adopt Supply Chain Management (SCM) and other practices such as Just-in-Time (JIT). A. True 4. The goal of Supply Chain Management is to increase customer service by increasing inventory and reducing costs. A. True 5. Service firms offer intangible products (meaning products that cannot be physically touched), therefore, they do not have a supply chain. A. False 6. Which of the following statements is TRUE? A. Strategic partnerships are seen as one of the foundations of supply chain management 7. Which one of the following is NOT a common mode of transportation in the supply chain? A. Bus 8. Successful modern supply chain management typically includes the practice of? A. Collaborating and sharing information between supply chain partners 9. Which one of the following is NOT one of the four Foundations of Supply Chain Management? A. Plan B. Source C. Forecast D. Make E. Deliver 10. Based on the diagram, which of the following correctly identifies the Manufacturer\'s Tier 1 supply chain partner(s)? A. Supplier C and Customer C **Chapter 02** 1. 11. The Qualitative forecasting method is based on opinion & intuition. A. True 12. Forecasts are more accurate the farther out into the future that you forecast. A. False 13. Cause-and-Effect Models can have multiple independent variables. A. True 14. Independent Demand is demand for an item that is directly related to other items or finished products, such as a component or material used in making a finished product. A. False 15. Collaborative Planning, Forecasting, and Replenishment is the process of combining statistical forecasting techniques and judgment to construct demand estimates for products or services. A. False 16. Which one of the following is [NOT] a type of qualitative forecasting? A. Naïve method 17. What does the acronym CPFR represent? A. Collaborative Planning, Forecasting, & Replenishment 18. In the absence of any other information or visibility, individual supply chain participants can begin second-guessing what is happening with ordering patterns, and potentially start over-reacting. This is known as? A. The Bullwhip Effect 19. When creating a quantitative forecast, data should be evaluated to detect for a repeating pattern of demand from year to year, or over some other time interval, with some periods of considerably higher demand than others. This is known as a? A. Seasonal Variation 20. \_\_\_\_\_\_\_\_\_\_\_\_\_\_\_\_\_\_\_\_\_\_\_ measures the size of the forecast error in units. It is calculated as the average of the unsigned errors over a specified period of time. A. Mean Absolute Deviation **Chapter 03** 2. 21. The goal of supply chain planning is to balance supply and demand in a way that realizes the financial and service objectives of the company. A. True 22. Material Requirement Planning is the system intended to develop long-range plans (more than a year away) concerning product families manufactured by the organization. A. False 23. The three basic production strategies for addressing the aggregate planning problem are the chase production strategy, the level production strategy, and the mixed production strategy. A. True ( find the difference between this for test) 24. The Chase Production Strategy relies on a constant output rate and capacity while varying inventory and backlog levels to handle the fluctuating demand pattern. A. False 25. Master Production Scheduling is a process that brings all the demand and supply plans for the business (sales, marketing, development, production, sourcing, and finance) together to provide management with the ability to strategically direct the business to achieve a competitive advantage A. False 26. Which of the following is an engineering document that shows an inclusive listing of all the component parts and assemblies making up the final product? A. Bill of Materials (there is multilevels you have to know for test) 27. The medium-range capacity planning technique used to check the feasibility of the Master Production Schedule (MPS) is called? A. Rough-cut Capacity Planning (RCCP) 28. Which of the following MRP terms represents a committed order awaiting delivery for a specific period? A. Scheduled receipt 29. Organizations that choose to implement one single system with all of the desired applications from a single vendor is said to have chosen a? A. Single integrator solution 30. The process of converting a parent item's planned order releases into component gross requirements is called? A. MRP Explosion