Electronics Manufacturing, 21WS610META PDF
Document Details
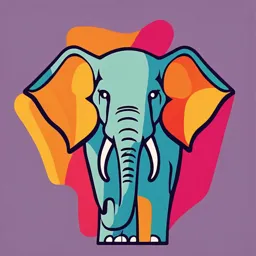
Uploaded by MagicCongas4169
Loughborough University
Patrick Webb
Tags
Summary
This document is lecture notes on electronics manufacturing. It covers a range of topics including component packaging and PCB assembly methods. It also describes the related manufacturing processes.
Full Transcript
21WS610META – Manufacturing Technology Electronics Manufacturing Patrick Webb [email protected] T2.28b Topics Outline 1. Introduction: – Technology trends – What is special about electronics manufac...
21WS610META – Manufacturing Technology Electronics Manufacturing Patrick Webb [email protected] T2.28b Topics Outline 1. Introduction: – Technology trends – What is special about electronics manufacturing? 2. Interconnection requirements/hierarchies 3. Component types and their manufacture 4. PCB manufacturing processes: – Photolithography, drilling, etching, etc. 5. PCB assembly – Soldering processes 6. Contamination control / yield / testing 21WS610META – Manufacturing Technology – Electronics Manufacturing Topic 3: Component packaging and PCB assembly methods Through Hole / Pin Through Hole (TH/PTH) Technology The traditional PCB assembly technology Through Hole / Pin Through Hole (TH/PTH) Technology The traditional PCB assembly technology Dual In Line (DIL) TH ICs DIL 14 0.1” pitch (~2.5 mm) 0.3” width (1” = 1 inch = 25.4 mm) Dual In Line (DIL) TH ICs DIL 14 0.1” pitch 0.3” width (1” = 1 inch = 25.4 mm) Dual In Line (DIL) leadframe Dual In Line (DIL) TH ICs DIL 20 0.1” pitch 0.3” width Dual In Line (DIL) TH ICs DIL 24 0.1” pitch 0.6” width Dual In Line (DIL) TH ICs DIL 40 0.1” pitch 0.6” width Dual In Line (DIL) leadframe Dual In Line (DIL) TH ICs DIL 64 0.1” pitch 0.9” width The solution? The solution? No! The Solution? Surface Mount Technology (SMT) Smaller Cheaper Allows higher pin counts (number of IOs or leads) The Solution? Surface Mount Technology (SMT) SMT IC packages JLCC 68 0.05” pitch (~1.3 mm) SMT IC packages SMT IC packages QFP 208 (Quad Flat Pack) 0.5 mm pitch SMT IC packages QFP 256 0.4mm pitch The Solution: Area Array Packages BGA – Ball Grid Array BGA 225 1.5 mm pitch Area Array Packages BGA 304 1.25 mm pitch Rent’s rule revisited Nleads = 2.4 x Ntransistors0.3 For microprocessors: Increasing Ntransistors by 10 implies doubling Nleads (number of pins) (because 100.3=2) Components and PCB assembly Electrically components can be divided into two main categories: – Passive Resistors (Rs) Capacitors (Cs) Inductors (Ls) – Active Diodes (Ds) Transistors (Ts or Qs) Integrated circuits (ICs) In this module we don’t care about these distinctions!! Physical form depends on whether for through hole or surface mount assembly System size and weight are usually dominated by packaging and interconnection Typical PC motherboard 30cm×25cm = 750cm2 Si content ≈ 10cm2 SMT Pick and Place Machine https://youtu.be/UPgrKp3DyqU Components are packaged to be presented to machines like this Speeds of 12,000 + components per hour Component Presentation https://youtu.be/epXwwy7hfQs Axial through hole components Two wire connections on same axis Typically Rs and Ds + some Cs and Ls Usually supplied in bandolier Radial through hole components Two or more parallel wires Typically Cs and Ts + LEDs Typically taped with sprocket holes Through hole ICs Four or more connections usually in two rows 0.1” (2.54mm) pitch Typically delivered in tubes/sticks SMT components “Chip” components most numerous Rs and Cs Delivered in bulk or taped Evolution of chip component size ~5mm2 ~2.5mm2 ~1.25mm2 The 12 in 1206 indicates 0.12” i.e. 3.2mm Evolution of chip component size https://industrial.panasonic.com/ww/ss/technical/r1 Other SMT components Metal electrode leadless face (MELF) – Rs and Ds Wide variety of IC package styles – SO, J-lead, QFP, etc, etc – Can be supplied in tubes, tape or trays Gantry PCB Conveyor Components in tape and reel packaging Pick and place head Local fiducials Often used for vision systems to accurately identify placement position for fine pitch components XY co-ordinates from e.g. PCB corner not sufficient Local fiducials Often used for vision systems to accurately identify placement position for fine pitch components XY co-ordinates from e.g. PCB corner not sufficient Next: Printed Circuit Board (PCB) manufacturing processes WS610META – Manufacturing Technology Electronics Manufacturing Patrick Webb [email protected] T2.28b WS610META – Electronics Manufacturing Topic 1. Introduction to Electronics Manufacturing With thanks to David Whalley Topics Outline 1. Introduction: – What are electronic products? – Technology trends – What is special about electronics manufacturing? 2. Interconnection requirements/hierarchies 3. Component types and their manufacture 4. PCB manufacturing processes: – Photolithography, drilling, etching, etc. 5. PCB assembly – Soldering processes 6. Contamination control / yield / testing WHAT ARE ELECTRONIC PRODUCTS? Electronics Market Sectors Consumer Transport Medical Military Telecomms Industrial Consumer Electronics Consumer Electronics? https://en.wikipedia.org/wiki/Cam_timer Transport Telecomms Google data centre, St Ghislain, Belgium IOT – Internet of Things Rahman et al, Mathematical Biosciences and Engineering. 19. 7586-7605. 10.3934/mbe.2022357. TECHNOLOGY TRENDS Comparing electronics to other technologies Vincent Black Shadow 1948 American Speed Record1948 https://en.wikipedia.org/wiki/Rollie_Free Ducatti 996 1998 50 years of superbike evolution Manufacturer & Vincent Ducati Model Black Shadow 996SPS Year of 1948 1998 introduction Engine 4 stroke 4 stroke type V twin V twin Capacity 998cc 996cc Max. power 55bhp 123bhp Tubular steel Tubular steel Frame with engine as with engine as construction stressed stressed member member Weight 208kg 190kg Top speed 200km/hour 270km/hour “First” Stored Programme Computer 1948: The Manchester “Baby” 1k bit storage 500×109 bits At a manufacturing rate of 1/s ….. ….17,000 years! 1965: Moore’s Law Moore’s Law (Intel co-founder) can be stated as: “the number of transistors on a chip will double about every two years” http://www.intel.com/ 1971: Intel i4004 – first microprocessor 4 mm Min feature size: 10 micrometers =10,000 nm What if We Shrank an i4004? Minimum feature sizes (node) UV Light Q. What made all of this Mask possible? A. Lithography Target An enabling technology for rapid and accurate Expose, manufacture of develop and etch complex / repetitive components Patterned target Not just digital ICs Volume reduction by factor of 20 in 7 years Microelectromechanical Systems- MEMS Lithography also used for MEMS e.g. low cost sensors: – Pressure – Acceleration – Gyros MEMS in Your Smartphone The Price of Progress “The Chips Are Down: The Semiconductor Industry and the Power of Globalisation,” The Economist, December 1, 2018. Page 8 Global Chip Shortage https://www.spglobal.com/marketintelligence/en/news-insights/blog/chip-shortages-stick-around-while-the-world-waits-for-more-capacity ICs need Interconnection So what is special about electronics manufacturing? Electronics is a large, complex and rapidly evolving industry Lithography is a key process allowing parallel manufacturing of very complex products Form doesn’t follow function Manufacture of the latest chips requires huge investment But – these chips must be connected to many other components to be able to work Therefore interconnection technology is critical to exploiting advances in semiconductor technology This is where the lecture programme will focus over the coming weeks WS610META – Manufacturing Technology Electronics Manufacturing Patrick Webb [email protected] T2.28b WS610META – Electronics Manufacturing Topic 4 PCB Manufacturing With thanks to David Whalley Topics Outline 1. Introduction: – Technology trends – What is special about electronics manufacturing? 2. Interconnection requirements/hierarchies 3. Component types and their manufacture 4. PCB manufacturing processes: – Photolithography, drilling, etching, etc. 5. PCB assembly – Soldering processes 6. Contamination control / yield / testing 2 Making a double sided plated through hole PCB - overview Start with a double sided copper clad laminate board Making a double sided plated through hole PCB - overview copper laminate Making a double sided plated through hole PCB - overview photoresist Making a double sided plated through hole PCB - overview Electroless copper Making a double sided plated through hole PCB - overview Plated copper Making a double sided plated through hole PCB - overview Plated solder Making a double sided plated through hole PCB - overview Final steps Apply surface finish for areas to be soldered Apply solder mask PCB Manufacturing Materials and Processes Materials Drilling Lithography – Imaging – Etching – Plating Single sided PCB manufacture Double sided plated through hole (PTH) PCB manufacture Some other types of PCB PCB Manufacturing Materials and Processes Materials Drilling Lithography – Imaging – Etching – Plating Single sided PCB manufacture Double sided plated through hole (PTH) PCB manufacture Some other types of PCB PCB Materials: Substrate Substrate = material supporting conductive tracks and components Provides mechanical support of circuit Also contributes to electrical performance Need a balance of – Cost – Dielectric properties – Stability – Temperature resistance Dielectric properties refers to – Good insulator – Resistance to high voltage breakdown – Low dielectric constant for high frequency currents – determines propagation speed of signals – Low loss = absorbs little energy from changing electric fields – Stable dielectric properties – so electrical performance is stable PCB Materials: Substrate Typically glass reinforced epoxy “FR4” Various lower cost materials e.g: – Glass reinforced polyester – Glass reinforced phenolic – Paper reinforced phenolic Specialised (i.e. more expensive) materials available e.g: – Glass reinforced polyimide high temps / high reliability – PTFE for very high frequencies – Non-reinforced materials for flexible PCBs (e.g. polyimide/polyester films) Typical thickness 1.6mm (1/16”) But can be multilayer and thicker Or thinner e.g. smartphones Woven Glass Fibre Tightly woven gives well controlled mechanical properties Substrate Materials: Conductor Conductor material almost always copper foil / film – Adhered to substrate – 1oz (per square foot) is a typical thickness (~35μm) – Thicker for power electronics 2 – 3 oz or more – Thinner for fine pitch e.g.: ¼ to ½ oz PCB Manufacturing Materials and Processes Materials Drilling Lithography – Imaging – Etching – Plating Single sided PCB manufacture Double sided plated through hole (PTH) PCB manufacture Some other types of PCB Drilling Many holes are required in printed circuit boards The more complex the circuit the more holes are required The holes mainly provide electrical connectivity between top and bottom conductor layers For more complex circuits there are also conductor layers inside the PCB Holes are also required for any through hole components, e.g.: connectors Drilling: PCB Drill bits Solid tungsten carbide with standard length and shank diameter 50m to 3.15mm diameter Multi-spindle PCB Drilling Machine https://youtu.be/W130X0kSzYI?t=19 PCB drilling Multi-spindle CNC machines Small holes mean high spindle speeds: – 100,000+ rpm common – 250,000+ rpm spindles available allowing sub 100m holes Entrance and exit materials used to minimise burring and improve accuracy Layers stacked to improve throughput – Hole aspect ratio limits stack height – Entrance / exit material between layers in stack Routing (cutting out) of PCBs Other hole formation processes Alternatives not suitable for typical traditional PCB manufacture Punching: high volume (high tooling costs), low quality, low complexity (non- PTH) product Moulding: high volume (high tooling costs), low complexity, but can be 3D product Photolithography (additive processes) Laser drilling Routed PCB PCB Manufacturing Materials and Processes Materials Drilling Lithography – Imaging – Etching – Plating Single sided PCB manufacture Double sided plated through hole (PTH) PCB manufacture Some other types of PCB Exposure Methods n.b. 1 mil = 1 thou’ = 0.001” = 0.0254 mm Contrast Photographic film response Photoresist response Tone Tone Exposure Exposure Contrast Lithography Steps White areas let the UV light throught Positive Resist Lithography Steps Black areas are exposed resist Positive Resist Lithography Steps Positive Resist Resist remaining after developing Lithography Steps Positive Resist Copper etched where there is no resist Lithography Steps Black areas are exposed resist Resist remaining Negative after developing Resist Copper etched where there is no resist Exposure Time Sensitivity measured in J/m2 Exposure unit will create surface flux with an intensity of W/m2 W = J/s Therefore: exposure time = sensitivity / intensity Alignment Alignment marks Alignment tolerances PCB Manufacturing Materials and Processes Materials Drilling Lithography – Imaging – Etching – Plating Single sided PCB manufacture Double sided plated through hole (PTH) PCB manufacture Some other types of PCB Etching Etching Anisotropic etching wet etching of single crystal materials e.g. silicon dry etching processes (gas / plasma) Plating Electroless plating can add metal onto other metals or onto insulators, but is slow Electrolytic plating (electroplating) only works on conductive substrates, but can build a thick layer much more quickly Single sided PCB manufacture Single sided PCB manufacture Faster and cheaper process Single sided PCB manufacture Double sided PCB manufacture Double sided PCB manufacture Double sided PCB manufacture Multilayer PCBs Provide more track per unit area Some other types of PCB Multilayer – Diminishing returns unless buried vias – Or sequential build for maximum area utilisation Flexible PCBs Provides wiring between parts of system Allows PCB to fold into limited spaces in product Allow for movement e.g. printer heads, disk drives Flexible PCBs Can be rigidised or combined with rigid boards 2 WS610META – Manufacturing Technology Electronics Manufacturing Patrick Webb [email protected] T2.28b WS610META – Electronics Manufacturing Revision Lecture Topics Outline 1. Introduction: – Technology trends – What is special about electronics manufacturing? 2. Interconnection requirements/hierarchies 3. Component types and their manufacture 4. PCB manufacturing processes: – Photolithography, drilling, etching, etc. 5. PCB assembly – Soldering processes 6. Contamination control / yield / testing Interconnection hierarchies 1 2 3 4 5 Level One Interconnection Typical IC package cross section polymer encapsulant wirebond Die leadframe Flip-Chip Assembly Under Bump Solder Metallisation (UBM) Die Joint Underfill Copper Track PCB Smallest possible package, lightweight Full array interconnection is possible Short electrical path leads to best electrical performance Solder based flip-chip assembly is the most compatible with standard PCB assembly processes Underfill often necessary for reliability (thermal expansion mismatch) Level Two Interconnection Surface Mount Technology (SMT) Through Hole Technology (THT) Surface Mount Technology (SMT) The majority used PCB assembly technology Through Hole / Pin Through Hole (TH/PTH) Technology The traditional PCB assembly technology SMT IC packages: J Lead 20 pin 36 pin 44 pin 52 pin 68 pin SMT IC packages: Quad Flat Pack (QFP) QFP 256 0.4mm pitch SMT IC packages: Ball Grid Array (BGA) BGA 225 THT IC Packages: Dual In Line (DIL) DIL 14 0.1” pitch Passive Component Packages Electrically components can be divided into two main categories: – Passive Resistors (Rs) Capacitors (Cs) Inductors (Ls) – Active Diodes (Ds) Transistors (Ts or Qs) Integrated circuits (ICs) SMT Passive Components “Chip” components Rs and Cs Presentation of SMT Components for Assembly Tape and reel Trays/ waffle packs THT Components Axial components Radial components Typically supplied on a tape PCB Manufacturing PCB Manufacturing Materials and Processes Materials Drilling Lithography – Imaging – Etching – Plating Single sided PCB manufacture Double sided plated through hole (PTH) PCB manufacture Flexible PCBs Making a double sided plated through hole PCB - overview Solder Mask Solder mask prevents solder from flowing where it should not go during soldering Through Holes and Vias Through holes provide holes to insert THT components Through holes and vias also electrically interconnect different layers of a double sided or multilayer PCB Flexible PCBs Provides wiring between parts of system Allows PCB to fold into limited spaces in product Allow for movement e.g. printer heads, disk drives Soldering Soldering Solder alloys Intermetallics Wetting and fluxes Forms of solder and flux Soldering processes Eutectic Composition Eutectic composition Solder Alloys Historically eutectic or near eutectic tin lead solder was used – composition around Sn63Pb37 Concerns over use of lead have led to a ban on its use in several regions for most applications: – Industry now favours high tin alloys e.g: SnCu0.7 (MP 227ºC) SnAg3.8Cu0.7 (MP 217ºC) Wetting & Fluxes Two requirements must be met in order for the molten solder to wet the work-pieces : – The surfaces must be clean and oxide free so that the solder may come into intimate contact with the materials – The process must be thermodynamically possible Fluxes help both these requirements to be met Intermetallics Intermetallics are crystalline compounds of metals formed at the interfaces of a solder joint They must be present in a good solder joint But they are brittle – so should not be too thick Forms of solder: wire Used primarily for hand soldering Usually flux cored Solder Flux core Forms of solder: paste Used primarily for reflow soldering Dense suspension of solder particles in a mixture of flux and solvents (vehicle) Solder Flux etc. Forms of solder: bulk Used primarily for mass soldering processes such as wave soldering Cast ingots/bars/sticks (typically 0.5 to 5kg) or pellets Soldering Processes - SMT The Stencil Printing Process SMT Pick and Place Machine https://youtu.be/UPgrKp3DyqU Components are packaged to be presented to machines like this Speeds of 12,000 + components per hour Reflow Temperature Profile Spike Thermal (reflow) Preheat soak Cooling Soldering Processes - THT A wave soldering machine Wave Soldering https://youtu.be/VWH58QrprVc Yield, Test and Inspection Yield calculation If yield per process step is known then overall yield is calculated by multiplying yield of each step Because there are so many steps in electronics manufacturing, individual step yields need to be very high Overall yield(n steps) = yield(step1) x yield(step2)x …yield(stepn) There are also multiple inspection and test procedures carried out at different phases of electronics manufacturing – E.g. 20 steps with a yield of 99% = 0.9920 = 82% Examples of Inspection and Test Multiple stages Die testing of inspection and test are carried out Test probe marks through all phases of Solder paste inspection electronics manufacturing Assembled PCB “bed of nails” testing WS610META – Manufacturing Technology Electronics Manufacturing Patrick Webb [email protected] T2.28b Topics Outline 1. Introduction: – Technology trends – What is special about electronics manufacturing? 2. Interconnection requirements/hierarchies 3. Component types and their manufacture 4. PCB manufacturing processes: – Photolithography, drilling, etching, etc. 5. PCB assembly – Soldering processes 6. Contamination control / yield / testing 22WS610META – Electronics Manufacturing Topic 5 Soldering With thanks to David Whalley 2 Soldering - subtopics Introduction to soldering Solder alloys Intermetallics Wetting and fluxes Forms of solder and flux Soldering processes Soldering - subtopics Introduction to soldering Solder alloys Intermetallics Wetting and fluxes Forms of solder and flux Soldering processes Introduction to soldering What is soldering? – Soldering and brazing are the joining of two materials using a molten metallic filler material having a lower melting point than either of the materials being joined – This is different to welding where the parent materials melt – Soldering is taken to include those processes using a filler which melts below 400ºC, whilst in brazing a filler melting at over 400ºC is used Introduction to soldering What is soldering? – Soldering and brazing are the joining of two materials using a molten metallic filler material having a lower melting point than either of the materials being joined – This is different to welding where the parent materials melt – Soldering is taken to include those processes using a filler which melts below 400ºC, whilst in brazing a filler melting at over 400ºC is used Introduction to soldering Where is soldering used? – Principally in electronics assembly – There are >1012 electronic components sold annually - almost all of which are soldered to PCB’s – Many electronic components also contain internal solder joints making the total even higher – Traditionally used for e.g. automotive radiator manufacture and other heat exchangers – Other principal applications outside the electrical/electronic industries are plumbing and light metal fabrications Introduction to soldering Where is soldering used? – Principally in electronics assembly – There are >1012 electronic components sold annually - almost all of which are soldered to PCB’s – Many electronic components also contain internal solder joints making the total even higher – Traditionally used for e.g. automotive radiator manufacture and other heat exchangers – Other principal applications outside the electrical/electronic industries are plumbing and light metal fabrications Introduction to soldering Where is soldering used? – Principally in electronics assembly – There are >1012 electronic components sold annually - almost all of which are soldered to PCB’s – Many electronic components also contain internal solder joints making the total even higher – Traditionally used for e.g. automotive radiator manufacture and other heat exchangers – Other principal applications outside the electrical/electronic industries are plumbing and light metal fabrications Ball Grid Array cross-section Soldering - subtopics Introduction to soldering Solder alloys Intermetallics Wetting and fluxes Forms of solder and flux Soldering processes Solder alloys 1 Limited choice of metallic elements with useful melting point for soldering: – Hg -39ºC – Ga 30ºC – Na 98ºC – In 156ºC – Sn 232ºC – Bi 270ºC – Cd 321ºC – Pb 328ºC Alloys are therefore almost always used There are literally hundreds of commercially available solder alloys: – http://www.indium.com/products/alloy_sorted_by_temperature.pdf Sn is a major constituent of most electronic solders A binary phase diagram A binary phase diagram Pasty phases A binary phase diagram Eutectic composition Solder alloys 2 Traditionally the principal alloys used in electronics manufacture were of tin and lead, often with other minor additions: – usually eutectic or near eutectic alloys – eutectic composition for tin-lead alloys is 63%Sn/37%Pb by weight (SnPb37) – melting point (MP) of 183ºC – ‘60/40’ was also commonly used in through hole Slightly lower cost – Addition of 2% Ag (SnPb36Ag2) common for SMT Lower MP of 179ºC Slightly stronger Less dissolution on Ag containing terminations Solder alloys 2 Traditionally the principal alloys used in electronics manufacture were of tin and lead, often with other minor additions: – usually eutectic or near eutectic alloys – eutectic composition for tin-lead alloys is 63%Sn/37%Pb by weight (SnPb37) – melting point (MP) of 183ºC – ‘60/40’ was also commonly used in through hole Slightly lower cost – Addition of 2% Ag (SnPb36Ag2) common for SMT Lower MP of 179ºC Slightly stronger Less dissolution on Ag containing terminations Solder alloys 3 Concerns over use of lead have led to a ban on its use in several regions for most applications: – RoHS directive within EU – from 2006 – Exceptions e.g. for high reliability – Industry favouring high tin alloys e.g: SnCu0.7 (MP 227ºC) SnAg3.8Cu0.7 (MP 217ºC) – negative impacts as well as positive Introduction to soldering Solder alloys Intermetallics Wetting and fluxes Forms of Solder Soldering Processes Intermetallic formation Reactive wetting takes place in most soldering processes Chemical reaction between at least one element of solder alloy and one element of metal being soldered to Most common situation is a tin containing solder on a copper termination – Cu3Sn formed near to copper – Cu6Sn5 formed near to solder Soldering - subtopics Introduction to soldering Solder alloys Intermetallics Wetting and fluxes Forms of solder and flux Soldering processes Wetting and Fluxes Surface tension and wetting Liquid drop Solid surface Non-wetting: Ө tending to 180° Poor wetting Good wetting: Ө tending to 0° Surface tension and wetting angle γ = surface energy (also called surface tension) – it is the energy per unit area associated with an interface We have three interfaces solid to air (subscript s) liquid to air (subscript l) liquid to solid (subscript ls) Why is it called surface tension? Surface energy has units of: J/m2 But: J = N.m So surface energy is also a tension i.e: J/m2 ≡ N/m => We have forces trying to move the air/solid/liquid interface Why is it called surface tension? Surface energy has units of: J/m2 But: J = N.m So surface energy is also a tension i.e: J/m2 ≡ N/m => We have forces trying to move the air/solid/liquid interface Why is it called surface tension? Surface energy has units of: J/m2 But: J = N.m So surface energy is also a tension i.e: J/m2 ≡ N/m => We have forces trying to move the air/solid/liquid interface Why is it called surface tension? Surface energy has units of: J/m2 But: J = N.m So surface energy is also a tension i.e: J/m2 ≡ N/m => We have forces trying to move the air/solid/liquid interface Spreading of liquids on a surface What if wetting angle very small? Spreading occurs if: γs > γl + γls Wetting & Fluxes Two requirements must be met in order for the molten solder to wet the work-pieces : – The surfaces must be clean and oxide free so that the solder may come into intimate contact with the materials – The process must be thermodynamically possible Fluxes help both these requirements to be met Wetting & Fluxes Flux coats surface – changing the surface energies Fluxes Traditionally fluxes have been primarily rosin (also known as colophony) which is extracted from pine trees Usually also contain activators such as halides or organic acids The rosin melts at about 172-175ºC, coating the surface to be soldered, cleaning it and reducing any oxide film Because the activators make the flux corrosive traditional fluxes must be cleaned after soldering to remove the residues – Rosin fluxes are difficult to clean without using organic solvents – In the past this was a major use of CFC’s Alternatives: – Synthetic resin based flux systems – Water washable systems – Low residue/no clean systems De-wetting De-wetting is the process where solder that has already wetted a surface pulls back from the surface either completely or only partially e.g. leaving a ‘blobby’ solder joint. De-wetting occurs when the requirements for wetting are no longer satisfied e.g. – Flux activity is spent changing the surface energies – Solder has dissolved the wetted surface and is now in contact with an underlying layer which is less wettable than the original De-wetting De-wetting is the process where solder that has already wetted a surface pulls back from the surface either completely or only partially e.g. leaving a ‘blobby’ solder joint. De-wetting occurs when the requirements for wetting are no longer satisfied e.g. – Flux activity is spent changing the surface energies – Solder has dissolved the wetted surface and is now in contact with an underlying layer which is less wettable than the original Soldering - subtopics Introduction to soldering Solder alloys Intermetallics Wetting and fluxes Forms of solder and flux Soldering processes Forms of solder: wire Used primarily for hand soldering Usually flux cored Solder Flux core Forms of solder: paste Used primarily for reflow soldering Dense suspension of solder particles in a mixture of flux and solvents (vehicle) Solder Flux etc. Forms of solder: bulk Used primarily for mass soldering processes such as wave soldering Cast ingots/bars/sticks (typically 0.5 to 5kg) or pellets Soldering - subtopics Introduction to soldering Solder alloys Intermetallics Wetting and fluxes Forms of solder and flux Soldering processes Soldering processes 3 main types of soldering process: – Single point e.g. hand, laser – Reflow soldering Solder and heat applied separately e.g. IR / convection or vapour phase – Mass soldering Molten solder applied directly to product Molten solder provides (most of) the heat e.g. wave soldering Hand soldering Used for prototyping, very low volume production, rework and repair Usually uses a cored solder wire and an electrically heated hand held soldering iron Variable quality – depends on training Can be roboticised – improves speed and consistency Hand soldering Hand soldering Hand soldering Component leg Solder wire Hand soldering Soldering iron Hand soldering Soldering iron - heat the component not the solder! Hand soldering Flux residue – potentially corrosive Reflow soldering Primarily used for SMT components Typical process steps: – Apply solder paste: e.g. stencil print or dispense – Place components – Apply heat: Dries any solvents in the paste Melts and activates the flux Melts solder particles Particles coalesce and wet to terminations – Cooling to solidify solder Slide on Solder Paste Printable Sticky Doesn’t dry out in a short time Swolvent can be driven off in reflow etc Solder Paste Stencil Printing A Solder Paste Stencil The Stencil Printing Process Example fine pitch print Reflow soldering Primarily used for SMT components Typical process steps: – Apply solder paste: e.g. stencil print or dispense – Place components – Apply heat: Dries any solvents in the paste Melts and activates the flux Melts solder particles Particles coalesce and wet to terminations – Cooling to solidify solder SMT Pick and Place Machine https://youtu.be/UPgrKp3DyqU Components are packaged to be presented to machines like this Speeds of 12,000 + components per hour Reflow soldering Primarily used for SMT components Typical process steps: – Apply solder paste: e.g. stencil print or dispense – Place components – Apply heat: Dries any solvents in the paste Melts and activates the flux Melts solder particles Particles coalesce and wet to terminations – Cooling to solidify solder The reflow process: Convection/IR soldering Most common process for SMT components Usually uses a multi-zone belt furnace In early machines infra-red (IR) was the dominant heat transfer process Progressively greater proportion of convection (hot air): – Less surface selective heat transfer – Faster heat transfer – Results in better control of profile and more uniform product temperature A typical reflow oven/furnace Temperature Profile Temperature Profile Spike Thermal (reflow) Preheat soak Cooling Mass soldering Primarily used for through hole components In mass soldering a pot of molten solder is maintained at typically 240-260ºC for SnPb or 260-270ºC for lead free At this temperature the solder will oxidise rapidly so oxide and dross must be removed regularly. Drossing can be reduced by: – Covering solder in layer of oil – Operation in an inert gas environment (nitrogen) Mass soldering processes: – Dip – Drag – Wave A wave soldering machine Wave soldering pot Wave Soldering https://youtu.be/VWH58QrprVc The safe operating area In all soldering processes there is a process window or safe operating area in terms of time/temperature which the process must fall inside The main criteria are: – i) The solder melting point must be exceeded – ii) The heating must not be so fast as to cause thermal shock or solder balling in reflow processes – iii) The PCB and component time temperature rating must not be exceeded – iv) Heating must not be so slow that the flux activity is used up Soldering health and safety In addition to observing normal safety and hygiene practices there are some additional points to observe regarding soldering processes: – Almost all soldering processes give off flux fumes which may be respiratory sensitizers (asthma trigger) – Flux systems often also give off solvent vapours – Fume extraction is therefore vital in production environments – Dross removal from solder pots may generate lead containing dust so a mask should be worn during this operation – Water or other liquids must not be allowed near molten solder pots since accidental spillage into the solder pot may result in a steam explosion WS610META – Manufacturing Technology Electronics Manufacturing Patrick Webb [email protected] T2.28b WS610META – Electronics Manufacturing Topic 6 Yield in Electronics Manufacturing With thanks to David Whalley Topics Outline 1. Introduction: – Technology trends – What is special about electronics manufacturing? 2. Interconnection requirements/hierarchies 3. Component types and their manufacture 4. PCB manufacturing processes: – Photolithography, drilling, etching, etc. 5. PCB assembly – Soldering processes 6. Contamination control / yield / testing Topics Outline 1. Introduction: – Technology trends – What is special about electronics manufacturing? 2. Interconnection requirements/hierarchies 3. Component types and their manufacture 4. PCB manufacturing processes: – Photolithography, drilling, etching, etc. 5. PCB assembly – Soldering processes 6. Contamination control / yield / testing Content Cleanliness in electronics manufacture Moore’s Law – what he really said Yield Inspection and test (briefly) Yield in electronics Many electronics manufacturing processes are yield based Rework opportunities may be limited Testing therefore critical to achieve success Manufacturing faults in PCBs and semiconductors are often “point” defects – e.g. localised short circuit or open circuit Cleanliness is critical to achieving high yield – Contamination by particles >≈10% of feature size may cause failure Cleanrooms Designed to reduce probability of particulate contamination landing on products or tools Also widely used in precision mechanical, medical device, pharmaceutical, etc. industries 3 key elements: – Clean materials for construction – Clean supply of air – Avoid introduction of contaminants Clean room apparel for staff Clean process materials and machinery Over pressure / airlocks / tack mats A simple mixed flow clean room HEPA (high efficiency Particulate air) filters Total vertical laminar flow cleanroom Cleanliness and clean room standards The traditional clean room standard is Fed. Std. 209D Unsuitable for state of art semiconductor manufacture Still appropriate for other processes Microprocessors What did Gordon Moore really say in 1965? Yield Heavily influenced by defect density Improvements in device yield are a major driver for Moore’s law Moore’s law is really about minimum cost Relative Manufacturing Cost per Component Number of components per integrated circuit Yield Heavily influenced by defect density Improvements in device yield are a major driver for Moore’s law Moore’s law is really about minimum cost Relative Manufacturing Cost per Component Yield driven by size of die Number of components per integrated circuit Yield Heavily influenced by defect density Improvements in device yield are a major driver for Moore’s law Moore’s law is really about minimum cost Relative Manufacturing Cost per Component Yield driven by Yield driven by size of die processing limitations Number of components per integrated circuit Yield calculation 1 If all defects are independently randomly distributed then the exponential distribution can be applied: Yield = e-AD where A = device area and D = defect density Effect of device size on yield 144 possible dice 34 possible dice 30 point defects 30 point defects 116 good dice = 81% yield 12 good dice = 35% yield Multiple steps in electronics manufacturing Multiple steps in electronics manufacturing Yield calculation 2 If yield per process step is known then overall yield is calculated by multiplying yield of each step Because there are so many steps in electronics manufacturing, individual step yields need to be very high Overall yield(n steps) = yield(step1) x yield(step2)x …yield(stepn) – E.g. 20 steps with a yield of 99% = 0.9920 = 82% – Or 100 steps with a yield of 99% = 0.99100 = 37% Yield calculation 2 If yield per process step is known then overall yield is calculated by multiplying yield of each step Because there are so many steps in electronics manufacturing, individual step yields need to be very high Overall yield(n steps) = yield(step1) x yield(step2)x …yield(stepn) – E.g. 20 steps with a yield of 99% = 0.9920 = 82% – Or 100 steps with a yield of 99% = 0.99100 = 37% Yield calculation 2 If yield per process step is known then overall yield is calculated by multiplying yield of each step Because there are so many steps in electronics manufacturing, individual step yields need to be very high Overall yield(n steps) = yield(step1) x yield(step2)x …yield(stepn) – E.g. 20 steps with a yield of 99% = 0.9920 = 82% – Or 100 steps with a yield of 99% = 0.99100 = 37% Examples of Inspection and Test Multiple stages Die testing of inspection and test are carried out Test probe marks through all phases of Solder paste inspection electronics manufacturing Assembled PCB “bed of nails” testing WS610META – Manufacturing Technology Electronics Manufacturing Patrick Webb [email protected] T2.28b Topics Outline 1. Introduction: – Technology trends – What is special about electronics manufacturing? 2. Interconnection requirements/hierarchies 3. Component types and their manufacture 4. PCB manufacturing processes: – Photolithography, drilling, etching, etc. 5. PCB assembly – Soldering processes 6. Contamination control / yield / testing WS610META – Electronics Manufacturing Topic 2. Interconnection requirements/hierarchies With thanks to David Whalley Interconnection hierarchies 1 2 3 4 5 Functions and requirements of the packaging and interconnection system The packaging / interconnection system must provide: – Connections for signal lines – Connections for electrical power – A physical structure to support and protect the circuit – Mechanisms for heat removal http://www.calce.umd.edu/whats_new/2012/Presentations/Avram Bar-Cohen.pdf System size and weight are usually dominated by packaging and interconnection Typical PC motherboard 30cm×25cm = 750cm2 Si content ≈ 10cm2 QUESTIONS? Interconnection hierarchies 1 Moore’s Law (Intel co-founder) can be stated as: “the number of transistors on a chip will double about every two years” http://www.intel.com/ Microprocessor pin count trend 1000 Number of pins 100 4 bit 8 bit 16 bit 32 bit 64bit Trend Series6 10 1000 10000 100000 1000000 10000000 Number of transistors 1971: Intel i4004 – first microprocessor 4 mm Bond pads Min feature size: 10 micrometers =10,000 nm Microprocessor pin count trend 1000 Number of pins 100 4 bit 8 bit 16 bit 32 bit 64bit Trend Series6 10 1000 10000 100000 1000000 10000000 Number of transistors Rent’s Rule In general the number of inputs/outputs (IOs) or pins, I, that a circuit needs will increase with complexity The measure of complexity is the number of circuits, C, e.g. logic gates or transistors These can be related by Rent’s rule: I = bCp where b and p are empirical constants What is Behind Rent’s Rule? Consider this very simplified representation of a circuit Each blue circle is a circuit element Circuit Circuit elements What is Behind Rent’s Rule II Consider connections to a square of 16 nodes How many connections needed? Each side has four connections – square root of number of nodes There are four sides So I = 4C1/2 Rent’s Rule for Real Circuits I = 4C1/2 is not true for real circuits Rent determined b and p to be 2 and 2/3 for real circuits In later studies b and p were 6.54 and 0.44 For processors b and p are 2.3 and 0.3 Microprocessor pin count trend 1000 Gate Number of pins arrays 100 4 bit 8 bit 16 bit 32 bit 64bit Memory Series6 10 1000 10000 100000 1000000 10000000 Number of transistors QUESTIONS? To here first lecture 07/10/24 Level 1 interconnections 1 How can we connect silicon chips to the outside world? Bond pad area of an IC Sawn edge of IC Al bondpads Active circuitry Al track A Typical IC Package Polymer encapsulating material Metal legs – known as ”Pins” – connect to bond pads Typical IC package cross section polymer encapsulant Remember: die = IC = chip! wirebond Die leadframe Leadframe Wire bonding Wire bonding https://youtu.be/3YkGrhvrWxA?t=11 Slowed down https://youtu.be/SVuOWwL410U?t=6 Normal speed Decapped Package polymer encapsulant wirebonds IC leadframe www.nisene.com Encapsulant can be removed to see inside an IC package– the process uses acid and is called “decapping” Next Step – Connect to Level 2 Die Cu track solder PCB Level 2 Interconnection – Printed Circuit Board QUESTIONS? Alternatives to Wire Bonding Wire bonding is relatively slow because it is a sequential process There are two alternatives for level one interconnection – Flip Chip – fairly recent - the “minimum packaging” option – TAB bonding – older and less used now Flip-Chip Assembly Under Bump Solder Metallisation (UBM) Die Joint Underfill Copper Track PCB Smallest possible package, lightweight Full array interconnection is possible Short electrical path leads to best electrical performance Solder based flip-chip assembly is the most compatible with standard PCB assembly processes Underfill often necessary for reliability (thermal expansion mismatch) Customised Flip Chip Package Flip chip Underfill PCB https://www.linkedin.com/products/amkor-technology-fcbga/ Underfill and CTE Mismatch CTE = Coefficient of Thermal Expansion Solder joint CTE ~ 3x106 K-1 under stress CTE ~ 14x106 K-1 PCB expanded Room temperature High temperature CTE mismatches in electronic packaging materials cause mechanical stress during temperature cycles If not compensated for this reduces the lifetime of electronic components Underfill compensates CTE mismatch for flip chip packages Process Steps 1: Wafer Bumping 1. Apply solder wettable layer (under bump metallisation (UBM)) Al bondpads Under bump metallisation Passivation Si Chip 2. Apply solder to form bumps solder bumps Solder Bumped Die Solder bumps ready for connection to PCB Bump diameter approximately 100m (0.1mm) Process Steps 2: Flip-Chip Assembly 1. Align bumped die with circuit board and reflow REFLOW Flux PCB PCB 2. Apply underfill Underfill PCB TAB bonding Tape Automated Bonding (TAB) relies on a flexible tape instead of a lead-frame Reel to reel process – very fast Used for high volume products, e.g. smart cards Need to change tooling if chip/ PCB design changes Steps: IC bond pads gold bumped by plating IC bonded to tape in one go Process Steps 1 1. Apply (gold) chip bumps – note scale is exaggerated Al bondpads Passivation Chip bump (Au) Si Chip 2. Bond chip to copper on plastic tape – note all bonds made in one go Heat and pressure Thermode Copper lead Plastic tape Chip bump (Au) Process Steps 2 3. Cut and shape copper leads 4. Bond to PCB – again all bonds made in one go Heat and pressure Heated Bar Cu pad Solder layer PCB TAB bonding https://youtu.be/X104jJNTvuc TAB bonding TAB bonding Some Considerations of Level 1 Methods Tooling costs – is dedicated tooling needed for a given chip/PCB design? Electrical performance – how long are signal paths? – how consistent are they? Can die be tested before packaging (see known good die slide)? Similar to tooling costs consideration – what happens if the IC manufacturer changes the die size (referred to as “die shrink”) Known Good Die A proportion of die on a wafer are faulty (90% to 98% are good die) The problem is how to test them to find out which die are acceptable, preferably before packaging them This is referred to as “known good die” Probe Marks Bondpads Comparison of Level 1 methods Wire bond TAB Flip chip Add UBM e.g. Ni + Bond pads Standard (Al) Add bumps e.g. Au bumps e.g. solder Speed (process) Slow (sequential) Fast Fast Very high Very low Medium Tooling/set-up costs (tape + bond tool + (data driven) (bumping) bumping) Electrical OK Better The best performance Size OK OK The best Yield (testability / Poor Good Poor known good die) PCB compatible Needs Au on PCB Good Excellent Re-spin of substrate Die shrink impact Minimal Re-tool required design