Unit V: Energy Resources PDF
Document Details
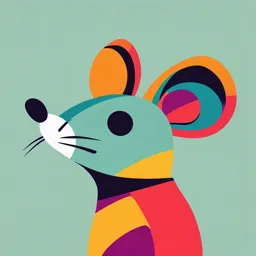
Uploaded by SublimePrairie2494
Tags
Summary
This document provides an overview of energy resources, including the definition and units of calorific value, different types of fuels (solid, liquid, gaseous), and biodiesel. It also covers the concepts of HCV/LCV and proximate analysis of coal.
Full Transcript
Unit V: Energy Resources (8 Lectures) Introduction, Calorific value of fuel – HCV, LCV- Dulong's formula. Classification- solid fuels: Coal – analysis of coal – proximate and ultimate analysis and their significance. Liquid fuels – Petroleum a...
Unit V: Energy Resources (8 Lectures) Introduction, Calorific value of fuel – HCV, LCV- Dulong's formula. Classification- solid fuels: Coal – analysis of coal – proximate and ultimate analysis and their significance. Liquid fuels – Petroleum and its refining, cracking types – moving bed catalytic cracking. Knocking – octane and cetane rating, synthetic petrol - Fischer-Tropsch’s process; Gaseous fuels – composition and uses of natural gas, LPG and CNG, Biodiesel – Transesterification, advantages. Define Calorific value of a fuel and write its units. The total quantity of heat liberated when a unit mass of fuel is burnt completely is called calorific value of a fuel. Units:- Calorie is the amount of heat required to raise the temperature of one gram of water through one degree centigrade Kilocalorie is defined as the quantity of heat required to raise the temperature of one kilogram of water through one degree centigrade. 1 kilocalorie = 1000 calories British thermal unit is defined as the quantity of heat required to raise the temperature of one pound of water through one degree Fahrenheit. 1 B.Th.U = 252 cal =0.252 K.Cal 1 K.Cal = 3.968 B.Th.U Centigrade heat unit is defied as the quantity of heat required to raise the temperature of one pound of water through one degree centigrade. 1 K.Cal = 3.968 B.Th.U = 2.2 C.H.U Define HCV/GCV and NCV/LCV. Higher or gross calorific value(HCV or GCV) is defined as the total amount of heat produced when unit mass or volume of the fuel is burnt completely and the products of combustion have been cooled to room temperature. HCV can be calculated by Dulong's formula as follows : HCV or GCV = 1/100[ 8080C+34500(H-O/8)+2240S] Where, C, H, O, S are the percentages of carbon, hydrogen, oxygen and sulphur. The calorific values of the components of fuels are outlined below: Constituent Calorific value(K.cal/Kg) Hydrogen 34,500 Carbon 8080 Sulphur 2240 Lower or net calorific value is defined as the net heat produced when unit mass or volume of the fuel is burnt completely and the products are permitted to escape.(LCV) LCV = HCV – latent heat of water vapour formed = HCV – mass of hydrogen X 9 X latent heat of steam Because 1 part by mass of hydrogen produces 9 parts by mass of water. The latent heat of steam is 587 K.Cal/Kg or 1060 B.Th.U/lb of water vapour formed at room temperature. SOLID FUELS The main solid fuels are wood, peat, lignite, coal and char coal. Certain agricultural and industrial wastes like rice husk, coconut and nut shells etc. are also employed as fuels. COAL: Coal is a highly carbonaceous matter that is formed as a result of alteration of vegetable matter under certain favorable conditions. It is mainly composed of carbon, hydrogen, nitrogen and oxygen besides non-combustible organic matter. Selection of coal: The following factors are considered for the selection of coal for different uses. The calorific value of a fuel should be high, so that large quantities of heat can be obtained from a small quantity of coal. It should have low moisture content. It should have low ash content since the presence of ash reduces the heating value of coal. Coal should have high calorific intensity. The size of coal should be uniform to facilitate handling and regulation of combustion. Analysis of coal:- The coal should be analysed to assess its quality. It is done by the following two methods. Proximate analysis: - This analysis records moisture, volatile matter, ash and fixed carbon as percentages of original weight of coal sample. This analysis is of significant in commercial classification and industrial utilization of coal. It is a quantitative analysis of following determinations. (i)Moisture content:- About 1g of finely powdered air dried coal sample is weighed in a crucible and is placed inside an electric hot air oven maintained at 105-110oc.It is kept for one hour and then taken out. It is cooled in a desiccator and weighed. The loss in weight is reported as the moisture content on percentage basis. Loss in weight due to loss in moisture % of moisture = ------------------------------------------ X 100 Weight of coal sample taken (ii) volatile matter:- The moisture free coal is taken in a silica crucible and heated for 7 minutes in a muffle furnace at 925oC+-20oC.The crucible is taken out and cooled first in air and then in desiccators. The loss in weight is reported as volatile matter on percentage basis. Loss in weight due to removal of volatile matter % of volatile matter =------------------------------------------------------------------------ X 100 Weight of coal sample taken (iii)Ash content:-It is the weight of residue obtained after burning a weighed amount of dry coal in an open crucible at 700-750oC for half an hour in a muffle furnace. The weight of residue remaining in the crucible is reported as ash content on percentage basis. Weight of the ash formed % of ash =------------------------------------------ X 100 Weight of dry coal taken (iv) Fixed carbon: - It is the quantity of carbon in coal that can be burnt by a primary current of air drawn through the hot bed of fuel. The sum total of the percentages of moisture, volatile matter and ash subtracted from 100 gives percentage of fixed carbon. % of fixed carbon =100-% of (moisture+ volatile matter +ash) Significance of proximate analysis:- It provides the following valuable information in assessing the quality of coal. (i) Moisture content:-Moisture lowers the effective calorific value because considerable amount of heat is wasted in evaporating the moisture during combustion. Hence lesser the moisture content, better the quality of coal as a fuel. (ii)Volatile matter:- It may be combustible gases (H2,CO,CH4 etc.) or non-combustible gases (CO2,N2).The presence of non-combustible gases is undesirable since they do not add to the heat value. The volatile matter content of coal influences the furnace design. Higher the content, larger is the combustion space required. The % of volatile matter in coal denotes the proportion of coal which will be converted into gas and tar products by heat. Hence high volatile matter content is preferable in coal gas manufacture and carbonization plants. Low volatile matter and high fixed carbon is preferred for manufacture of metallurgical coke. (iii)Ash: - It is the non-combustible, useless matter that is left behind when all the combustible matter s burnt off from coal. Hence lesser the ash content better is the quality of coal. (iv)Fixed carbon: - Higher the percentage of fixed carbon, greater is its calorific value and better the quality of coal. Ultimate analysis: - This is the elemental analysis. It involves the determination of carbon and hydrogen, nitrogen, sulphur and oxygen. (i) Carbon and hydrogen: - About 1-2g of accurately weighed coal sample is burnt in a current of oxygen in a combustion apparatus. The carbon and hydrogen of the sample are converted into CO2 and H2O.These is absorbed by KOH and CaCl2 tubes of known weights. The weights of CaCl2 and KOH in the bulbs are determined. C +O2 CO2 H2 +1/2O2 H2O 2KOH +CO2 K2CO3 +H2O CaCl2 +7H2O CaCl2.7H2O The increase in weight of CaCl2 gives the weight of H2O formed and increase in weight of KOH gives the weight of CO2 formed. Increase in weight of KOH X 12 % of carbon = ---------------------------------------------------------X100 Weight of coal sample taken X 44 Where 12 represent the atomic weight of carbon and 44 represents the mol.wt. of CO2. Increase in weight of CaCl2 X 2 % of hydrogen = ----------------------------------------------------- X 100 Weight of coal sample X18 Where 2 is the mol.wt. of H2 and 18 is the mol.wt. of H2O. (ii) Nitrogen: - The nitrogen in coal is determined by kjeldahl’s method. About 1g of accurately weighed powdered coal is heated with conc.H2SO4 along with K2SO4 and CuSO4 in a long necked flask called kjeldahl’s flask. After the solution becomes clear i.e., when whole nitrogen is converted into ammonium sulphate, it is treated with excess of NaOH to liberate NH3. The liberated ammonia is distilled into a measured amount of standard acid solution. The unused acid is then determined by titrating with standard NaOH solution. Thus the amount of acid neutralized by liberated NH3 is determined. From this, the nitrogen present in the sample is calculated. Volume of acid used X normality of acid X 14 % of nitrogen = ----------------------------------------------------------------------------X100 Weight of coal sample taken X 1000 (iii) Sulphur: - It is determined from the washings obtained from the known mass of coal used in a bomb calorimeter for determination of calorific value. During this, sulphur is converted into sulphate. The washings are treated with barium chloride solution and thus barium sulphate is precipitated. The precipitate is filtered, washed and heated to constant weight. O2 BaCl2 S ------------------> SO4-2 ------------------------> BaSO4 Weight of BaSO4 obtained X 32 % of sulphur = ------------------------------------------------------- X 100 Weight of coal sample taken X 233 Where 32 is the atomic weight of sulphur and 233 is the molecular weight of BaSO4. (iv) Oxygen: - It is determined indirectly by deducting the combined % of carbon, hydrogen, nitrogen and sulphur from 100. % of oxygen = 100 - % of (C +H +N+ S) Significance of ultimate analysis: - It gives the following information. (i) Carbon &hydrogen: - Greater the percentage of carbon and hydrogen better is the coal in quality and calorific value. The hydrogen is combustible and present in combination with oxygen in water. On heating, it changes into steam. The calorific value of any fuel containing hydrogen is only due to hydrogen present in free state and not in combined form as water. So lesser the percentage of hydrogen better is the quality of coal. (ii) Nitrogen: - It has no calorific value and hence its presence is not desirable. (iii) Sulphur: - Sulphur adds to the calorific value of coal since the oxidation of sulphur is an exothermic process. S + O2 SO2 + heat But SO2 is harmful. Because it gets oxidized to SO3, which forms H2SO4 leading to corrosion. 2 SO2 + O2 2SO3 SO3 + H2O H2SO4 (iv) Oxygen:-The oxygen content in coal decreases the calorific value. Hence a good quality coal should have low percentage of oxygen. REFINING OF PETROLEUM:- Refining is defined as “the process by which petroleum is made free of impurities, division of petroleum into different fractions having different boiling points and their further treatment to impart specific properties.” In refining of petroleum, the crude oil is separated into various useful fractions by fractional distillation and finally converted into desired specific products. The plants used for refining of petroleum are called oil refineries. The process of refining involves the following steps. (i)Removal of solid impurities: - The crude oil is a mixture of solid, liquid and gaseous substances. This is allowed to stand for some time so that the heavy solid particles settle down and the gases evaporate. The supernatant liquid is then centrifuged and all the solids get removed. (ii)Removal of water (Cottrell’s process):- The crude oil from the oil well is a stable emulsion of oil and salt water. This mixture is passed between two highly charged electrodes so that emulsion films are destroyed and the colloidal water droplets combine into bigger drops and separates out from the oil. (iii)Removal of harmful sulphur impurities: - It involves in treating in oil with copper oxide. The sulphur compounds get converted into insoluble copper sulphide and are removed by filtration. (iv)Fractional distillation: - The crude oil is then heated to about 400o C in an iron retort in which all the volatile constituents are evaporated. The hot vapors are then passed into a fractionating column. It is a tall, cylindrical tower containing a number of horizontal stainless steel trays at short distances. Each tray is provided with a small chimney covered with a loose cap. As the vapors go up, they become cool and fractional condensation takes place at different heights of column. Higher boiling fractions condense first and the lower boiling fractions later. The following are the various principal fractionation products obtained from crude. (i) Uncondensed gases: - They are lower hydrocarbons and obtained below 30oC. They are highly combustible. They are used as domestic fuel. (ii)Gasoline or petrol: - It is obtained between 40-120oc and is a mixture of hydro- Carbons like pentane to octane. Its calorific value is 11,250 k.cal/kg. It is highly volatile and inflammable. It is used as a fuel for internal combustion engines of automobiles and aeroplanes. (iii)Kerosene oil: - It is obtained between 180oc-250oc and consists of paraffin’s, Naphthalene and aromatic compounds. Its calorific value is 11,000 k.cal/kg. Kerosene oil is used as domestic fuel in stoves, tractor fuel, and illuminant, as jet engine fuel and for making oil gas. (iv) Gas oil or diesel oil:- It is obtained between 250oC-320oC. Its calorific value is 11,000k.cal/kg It is used as diesel engine fuel. (v)Residual oil: - It is the heaviest fraction of distillation On cooling, it gives paraffin wax which is used in the manufacture of candle, polishes, paper etc. It also gives greases and lubricating oil which are used as lubricants. The asphalt is used as preservative for wood water proofing and laying down the roads. CRACKING:- During distillation of crude oil, the gasoline obtained is of very important in automobile industry. The yield and quality of gasoline is improved by cracking. It involves thermal decomposition of heavier fractions. Cracking is defined as the process by which the higher hydrocarbons are decomposed into lower hydrocarbons by the application of heat. C10H22 ---------- C5H12+ C5H10 C9H20 ---------- C5H12+ C4H8 Moving bed catalytic cracking: The solid catalyst (Al O or Al (SiO ) ) is finely powdered and charged into catalytic chamber. The catalyst particles move freely in the chamber like a fluid. Hence the process is called fluid bed or moving bed catalytic cracking. The preheated vapors of cracking stock (gas oil, heavy oil) are passed into the chamber along with fluidized catalyst in which cracking of heavier into lighter molecules occurs. Then the vapors are passed into fractionating column. The catalyst particles settle to the bottom of catalytic chamber due to deposition of carbon on the surface of catalyst The catalyst powder is forced into regenerator by an air blast. In the regenerator, carbon is burnt and the regenerated catalyst is charged into catalytic chamber for mixing with fresh batch of incoming cracking oil. Knocking: -The rate of oxidation is so great that the last portion of fuel-air mixture gets ignited instantaneously and produces sound in the engine called as knock. This rattling noise produced in the internal combustion engine is called knocking. This defect is due to the faulty design of engine, which results in loss of efficiency. It is also due to unfavourable conditions due to defective ignition of fuel-air mixture. The tendency of fuel constituents to knock is in the following order Straight chain paraffins>branched chain paraffins>olefins>cycloparaffins>aromatics Thus olefins possess better anti-knock properties than the corresponding paraffins and so on. Hence the fuel with least knocking is a good fuel. The knocking is decreased by adding a little of tetra ethyl lead (TEL).It is a colourless, sweet smelling and highly poisonous liquid. Octane number:- The performance of gasoline in an internal combustion engine is rated based on octane number. Higher the octane number of fuel better is its performance and lower is the knocking engines. The octane number of gasoline is defined as the percentage of iso- octane present in a mixture of iso-octane and n-heptane. Eg:-The octane number of a motor fuel is 80.It means that the gasoline will produce knocking by the mixture of 80 parts of iso-octane and 20 parts of heptane. n-heptane knocks very badly and its anti-knock value is arbitrarily fixed as zero and iso- octane has the highest anti-knocking value i.e., 100. So the octane number shows the anti-knocking property of any fuel. Improvement of anti-knock characteristic of a fuel:- The octane number of fuels can be raised by the addition of certain compounds like tetra ethyl lead [(C2H5) 4Pb or TEL], diethyl telluride [(C2H5) 2Te]. Such compounds are called anti- knock compounds and the process is called doping. Synthetic Petrol:- The important methods commonly used for synthesis of petrol are:- Fischer-Tropsch’s method and Bergius process (i)Fischer-Tropsch’s method:- In this method, the raw material is the hard coke. The red hot coke is converted into water gas by passing steam over it. C + H2O → CO + H2 (Water gas) The water gas is then mixed with hydrogen. The gas is purified by passing through Fe2O3 to remove H2S and then into mixture of Fe2O3 and Na2CO3 to remove organic sulphur compounds. The purified gas is then compressed to 5-25 atm and then led through a convertor containing the catalyst consisting of Fe, Ni or Co. The product formed depends upon the catalyst. A Cobalt catalyst gives more olefins. Iron oxide with K2CO3 as promoter gives heavier hydrocarbons. Mixed catalysts like Cobalt, Magnesia are used to produce high grade diesel fuel from the enriched water gas. n CO + 2n H2 → CnH2n + n H2O n CO + (2n+1) H2 → CnH2n +2 + n H2O The reactions are exothermic. So the outgoing hot gaseous mixture is led to a cooler, where crude oil is obtained. The crude oil is then passed into a fractionating column and separated into different fractions like heavy oil, kerosene oil and gasoline. Then heavy oil is reused for cracking to get more gasoline. GASEOUS FUELS:- The gaseous fuels are the most preferred fuels because of their ease of storage, transport, handling and ignition. Advantages of gaseous fuels:- They can be distributed over a wide area through pipe lines, so that manual labour can be eliminated. They are ash less and smokeless and very clean to operate. The feed of the gas to the burner can be easily controlled and can be lighted very easily. Gases are miscible with air and hence the excess air needed is very less. These are quite efficient as the losses due to errors like smoke, convection etc., are minimum Disadvantages:- Even they are more advantageous, Great care should be taken due to their high inflammability. More space is required for the storage of gaseous fuels since they occupy large volumes. Natural gas:- Natural gas is obtained from the wells dug in the earth during mining of petroleum. It is mostly composed of methane and small quantities of ethane along with other hydrocarbons. If lower hydrocarbons are present in the gas or when the gas is associated with crude oil, it is called dry gas. If the hydrocarbons with high molecular weights are present or when the gas occurs along with petroleum, it is called wet gas. The average composition of natural gas is CH4 = 70-90% , C2H6 =5-10%, H2 =3% , CO+CO2 = rest The calorific value of natural gas is 8000-14000 k.cal/m3. For e.g. If natural gas contains H2S, it can be removed by scrubbing with monoethanolamine. 2 HO.CH2.CH2.NH2 + H2S -------------->(OH.CH2.CH2.NH2)2 H2S On heating, H2S can be liberated. Uses of natural gas:- It is an excellent domestic fuel which can be carried to long distances through pipe lines. It is used in the manufacture of chemicals like carbon black, methane, formaldehyde etc. Synthetic proteins used as animal feed is obtained by microbiological fermentation of methane. It is also used for the generation of electricity in fuel cells. Natural gas is also used as a source of H2. Hence ammonia can be made by reacting N2 with H2 obtained from natural gas. LPG:-liquefied petroleum gas or bottled gas or refinery gas 1. It is obtained as a by-product during the cracking of heavy oils or from natural gas. 2. LPG is dehydrated, desulphurised and traces of odourous organic sulphides are added to give warning of gas leak. 3. LPG is supplied under pressure in containers under the trade name like Indane, Bharat gas etc. 4. Its calorific value is about 27,800 K.Cal/m3 5. LPG consists of hydrocarbons of volatility that they can exist as gas under atmosphere pressure, but can be readily liquefied under pressure. 6. The main constituents of LPG are n-butane, isobutane, butylene and propane with little or no propylene and ethane. Uses:-The largest use of LPG is as domestic fuel and industrial fuel. It is widely used as motor fuel. Advantages of LPG over gaseous fuel:- High efficiency and heating rate. The calorific value is 3 times that of natural gas and 7 times that of coal gas. Use of well-designed, durable and neatly constructed burners ensure complete combustion with no smoke. Needs little care for maintenance purpose. Cleanliness in storage, handling and use. Flexibility and easy control. Easy to manipulate. Portability in steel cylinders make its use possible in remote or isolated places. Comparatively less of health hazard, even in case of leakage since it contains no CO Advantages of LPG over gasoline as a motor fuel:- It is cheaper than gasoline. It gives better distribution and mixes easily with air. It is highly knock-resistant. Residue and oil contamination is small, as it burns cleanly. Disadvantages of LPG over gasoline as a motor fuel:- Due to its faint odour, leakage cannot be easily detected. Handling has to be done under pressure. LPG is advantageous only in engines working under high compression ratios. Its octane number is quite low and the load sensitivity is very high. Due to this, the use of LPG is limited only to vehicles like trucks and tractors. LPG leaded with tetra methyl lead can be used as main constituent of diesel fuel for railway diesel locomotives. CNG: - Compressed natural gas It is a natural gas compressed to a high pressure of about 1000 atmospheres. A steel cylinder containing 15 kg of CNG contains about 2x104L or 20 m3of natural gas at 1 atmosphere pressure. CNG is used as a substitute for petrol and diesel. Because it is less pollution causing fuel. During its combustion, no sulphur and nitrogen gases are evolved. No it is better fuel than petrol or diesel for automobiles. The initial cost of engine designed to use CNG as a fuel is higher than that of engine designed to use petrol or diesel. In Delhi , it is mandatory for all buses, taxis and auto to use CNG as a fuel. CNG is preferred over LPG CNG is much safer fuel, since it ignites at a higher temperature than gasoline and diesel. The conversion of gasoline operated automobiles into CNG operated vehicle is easy. The operating cost of CNG fuel is much lower compared to gasoline operation. Combustion of CNG leads to lesser carbon monoxide emissions than gasoline. CNG mixes better with air than liquid fuels. Emission from CNG operated vehicle contains no pollutants like smoke SO2, SO3, C6H6, HCHO etc. CNG LPG Constituents Methane Propane and Butane Automatically generated from Obtained from natural gas and gas fields when natural gas is Source condensate wells, oil wells, coal extracted from the reservoir. By- bed methane wells. product of cracking process during crude-oil refining. Substitute for gasoline in Heating and cooking in homes, refrigeration, industrial, Uses automobiles. agricultural, catering and automobile fuel. Releases CO2 which is Environmental Releases lesser greenhouse gas. Greenhouse gas but is cleaner effects when compared to gasoline. It is lighter than air and hence Highly inflammable. It is heavier than air and on leakage will settle disperses quickly in the event of Properties to ground and accumulate in low spillage. lying areas. Easily disperses, hence risk of Since it is difficult to disperse risk Safety ignition is minimized. of fire is more. BIODIESEL. Biodiesel invented by Sa parente refers to a vegetable oil- or animal fat-based diesel fuel consisting of long-chain alkyl (methyl, propyl or ethyl) esters. Biodiesel is typically made by chemically reacting lipids (e.g., vegetable oil, animal fat (tallow) with an alcohol. Biodiesel is meant to be used in standard diesel engines and is thus distinct from the vegetable and waste oils used to fuel converted diesel engines. Biodiesel can be used alone, or blended with petro-diesel. Biodiesel can also be used as a low carbon alternative to heating oil. Blends of biodiesel and conventional hydrocarbon-based diesel are products most commonly distributed for use in the retail diesel fuel marketplace. Production Biodiesel is commonly produced by the transesterification of the vegetable oil or animal fat feedstock. Chemically, trans-esterified biodiesel comprises a mix of mono-alkyl esters of long chain fatty acids. The most common form uses methanol (converted to sodium methoxide) to produce methyl esters (commonly referred to as Fatty Acid Methyl Ester - FAME) as it is the cheapest alcohol available, though ethanol can be used to produce an ethyl ester (commonly referred to as Fatty Acid Ethyl Ester - FAEE) biodiesel and higher alcohols such as isopropanol and butanol have also been used. Using alcohols of higher molecular weights improves the cold flow properties of the resulting ester, at the cost of a less efficient transesterification reaction. A lipid transesterification production process is used to convert the base oil to the desired esters. Any free fatty acids (FFAs) in the base oil are either they are esterified (yielding more biodiesel) using an acidic catalyst or converted to soap and removed from the process.. A by-product of the trans esterification process is the production of glycerol. For every 1 tonne of biodiesel that is manufactured, 100 kg of glycerol are produced. Advantages: 1. Produced From Renewable Resources. 2. Can be Used in Existing Diesel Engines 3. Less Greenhouse Gas Emissions (e.g., B20 reduces CO2 by 15%) 4. Biodegradable and Non-Toxic 5. Grown, Produced, and Distributed Locally