Drilling Final Notes (1) PDF
Document Details
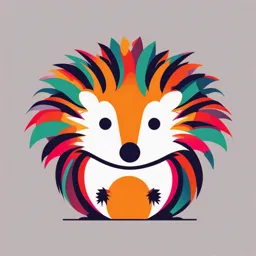
Uploaded by ResponsiveBanshee8241
Tags
Summary
This document contains notes on drilling operations, focusing on hole problems including pipe sticking, differential pipe sticking, lost circulation, and borehole instability. It also discusses survey methods, prevention, and solutions for these issues.
Full Transcript
Chapter 2: Hole Problems (a) Pipe Sticking Identification ❖ Drill string cannot be rotated ❖ Drill string cannot be pulled out Definition Occurs when the drill pipe is motionless and get (b) Differential...
Chapter 2: Hole Problems (a) Pipe Sticking Identification ❖ Drill string cannot be rotated ❖ Drill string cannot be pulled out Definition Occurs when the drill pipe is motionless and get (b) Differential pushed against mud cake because of too much Pipe Sticking pressure differences Prevention Minimize pressure differences between borehole and formation Maintain efficient mud properties control (density, fluid loss) Minimize friction factor using - Oil based mud - Low water loss mud Minimize contact area between drill string and borehole using - stabilizers on drill collar - non-circular drill collar Solutions 1. Hydrostatic Pressure Reduction - Pump low density fluid into drill string 2. Spotting Organic Fluid - Use mixture of diesel oil and surfactant 3. Back-off Operations - Fish remaining parts Identification ❖ Uncontrolled mud flow into formation (c) Lost ❖ Can be total loss (no mud return) or partial loss Circulation (some return with decreasing mud pit volume) Causes Induced fracture from: Hydrostatic mud pressure exceeding rock breaking strength Excessive wellbore pressure due to: - High flowrate (high annular friction pressure loss) - Fast tripping (high surge pressure) Survey 1. Spinner Survey Methods 2. Temperature Survey 3. Radioactive Tracer Survey 4. Pressure Transducer Survey Prevention Use of proper mud systems - Utilize low density mud Control rate of penetration Solution Lost Circulating Materials (LCM) - Use granular, fibrous or flaky materials Cement plugging - Apply squeeze cementing to seal severe loss zone 1 Holes ❖ Time dependent borehole narrowing (d) Borehole Closure ❖ Occurs in plastic flowing shale and salt Instability formation ❖ Problems: - Pipe sticking risks - Increased torque and drag Hole ❖ Hole becomes larger than intended Enlargement ❖ Caused by hydraulic erosion in shale (Washout) ❖ Problems: - Difficult cementing - Logging operations issue Fracturing ❖ Occurs when wellbore drilling fluid pressure more than formation fracture pressure ❖ Results in lost circulation Collapse ❖ Occurs when drilling fluid pressure too low ❖ Results in pipe sticking Prevention 1. Proper mud weight selection and maintenance 2. Proper hydraulics for ECD control 3. Adequate annular velocity for hole cleaning Solution 1. Proper mud weight selection - Not too heavy - Not too light 2. Good hole cleaning practices - Ensure cuttings are removed efficiently - Prevent cuttings accumulation 2 Chapter 3: Well Control (a) Concepts Well Control Preventing uncontrolled flow of fluids from formation into borehole and surface Kick Intrusion of formation fluids into wellbore when Pformation > Pmud Blowouts Uncontrolled flow of fluids to surface 9surface blowouts) or into fractured zone (underground blowouts) (b) Kick Causes Unexpected high-pressure zone - Rapid sedimentation deposition - Improper cement jobs Decrease wellbore fluid pressure - Lost circulation - Inadequate drilling mud weight Reduced mud column height due to - Swabbing Indicators Primary indicators: - improper hole fill up during tripping - increased flowrate and pit volume Secondary indicators: - sudden increase in penetration rate - changes in pump pressure (c) Well Control Primary Maintaining overbalance using drilling mud Methods Preventive measure Secondary Uses Blowout Preventer (BOP) Aims to stop fluid flow Tertiary Uses substances like cement to stop formation fluid influx (d) BOP System Annular Ring-shaped equipment at BOP top Component Preventer Uses hydraulic piston to push bladder and seal annulus Ram Types Pipe Ram: Seals around specific pipe sizes Blind Ram: Closes wellbore when no pipe present Shear Ram: Cuts through drillpipe for emergency shut-in Blind Shear Ram: Combines shearing and sealing capabilities (e) Shut in During Drilling 1. Stop rotation Procedures 2. Raise Kelly above rotary table 3. Stop mud pumps 4. Close annular preventer. Record pressures and pit gain 3 During 1. Set tool joint on slips Tripping 2. Install and close safety valve 3. Close annular preventer 4. Make up Kelly 5. Record pressures and pit gain 4 Chapter 4: Special Drilling Operations PART A (a) Coring System Conventional Coring Definition Core cutting from bottom of hole during drilling You need Uses inner core barrel with core catcher comprehensive suspended inside outer core barrel formation evaluation Attached to drill string with core bit Working with thick, Types 1. Standard Conventional Core Barrel uniform, - for consolidated formation consolidated - length: 1.5 ft to 400 ft formations 2. Heavy Duty Conventional Core Barrel Large, continuous - for harder formation core samples are - has higher torque required 3. Core Barrel Liners Detailed reservoir - supports core material during handling analysis is planned - act as preservation system Budget allows for higher costs 4. Disposable Inner Core Barrels -available in aluminium, fibre glass - low friction coefficient Advantages ❖ Good for thick formations ❖ Obtain large, continuous core sample ❖ Provides undisturbed sample Disadvantages ❖ Expensive diamond bits and core barrels ❖ High rig time and tool cost ❖ Must decide to core before drilling Special Coring Definition Specialized coring system for specific coring needs Working with Focus on maintaining reservoir unconsolidated conditions formations Types 1. Pressure-Retained Coring Need to maintain - maintains reservoir pressure reservoir pressure - length: 10-20 ft conditions - max. pressure: 10,000 psi Accurate oil 2. Sponge-Lined Coring saturation data is - traps expelled oil crucial - length: 30ft - temperature stable up to 350F Working with high- pressure reservoirs 3. Full-Closure Coring - for unconsolidated formation - length: 30ft max 5 Advantages ❖ Better preservation of reservoir properties ❖ Improved oil saturation data ❖ Better recovery in unconsolidated formations Disadvantages ❖ More complex equipment ❖ Temperature limitations ❖ Some systems have length restrictions ❖ Higher costs than conventional coring Wireline Sidewall Definition Cores obtained after drilling and logging Coring Samples taken from wellbore wall Need to target Types 1. Percussion Sidewall Coring specific zones - Uses hollow bullets shot into formation identified after - Up to 65 samples logging 2. Rotary Sidewall Drilling Working with limited - Uses diamond-tipped drill budget - Max. 30 samples Time is a critical Advantages ❖ Can target specific zones after logging factor ❖ Quick operation Need samples from ❖ Reduces unnecessary coring ❖ Can obtain samples after well is drilled multiple depths Disadvantages Percussion Type: ❖ Alters formation properties ❖ Poor for hard rock Rotary Type: ❖ More expensive than percussion ❖ Smaller sample size than conventional coring ❖ Limited number of samples per run Conclusion: conventional coring for comprehensive formation evaluation special coring for specific reservoir conditions or formation types sidewall coring for targeted sampling after drilling The "best" choice depends on: 1. Formation type 2. Budget constraints 3. Time considerations 4. Well conditions 5. Sample size needs 6 Chapter 4: Special Drilling Operations PART B (b) Coiled Tube Drilling Definition A continuous, jointless hollow steel pipe that (CTD) can be coiled/uncoiled on a reel Key Features Uses downhole mud motors to turn the bit Faster than conventional drilling rigs More economical than conventional drilling Applications 1. Re-entry drilling from existing wellbores o Often performed through existing production tubing (selalu onshore) 2. Special drilling operations: o Underbalanced drilling (UBD) o Managed pressure drilling (MPD) o Low BHP drilling 3. Service operations: o Fishing o Logging 4. Hybrid operations: o Combined with conventional rotary drilling rigs o Rotary rig drills initial wellbore o CTD used for precise zone penetration Advantages ❖ Continuous operation (no connections needed) ❖ Faster tripping times ❖ Better well control ❖ More environmentally friendly Disadvantages ❖ Limited weight on bit ❖ Limited hole size ❖ Higher maintenance requirements ❖ Lower penetration rates (c) Fish Hook Drilling Definition A specialized form of directional drilling where the wellbore is angled beyond horizontal Typically involves a 110º-140º tangent section Application 1. Accessing reservoirs that are difficult to reach with conventional directional or horizontal wells 2. Demonstrated success in fields like Shell Brunei's Seria Field (2007) 7 (d) Extended Reach Drilling Definition Horizontal displacement exceeds 16,400 (ERD) ft from surface location High inclination angles (typically >75- 80°) Advantages ❖ Allows access to deposits far from the drilling rig ❖ Reduces number of platforms needed ❖ Enables production from environmentally sensitive areas Disadvantages Mechanical Limitations: ❖ High drag and torque forces ❖ Pipe buckling risks ❖ Pipe/casing breakage potential Operational Challenges: ❖ Cutting accumulation in high-angle sections ❖ Pipe sticking ❖ Strict rig specification requirements (e) Multilateral Drilling Definition Multiple horizontal lateral wells drilled from a single mainbore All laterals connect back to the same mainbore Key Laterals: Wellbores drilled from main Components wellbore Branches: Wellbores drilled from horizontal lateral into horizontal plane Splays: Wellbores drilled from horizontal lateral into vertical plane Junctions: Intersections between laterals and main wellbore Advantages ❖ Enhanced reservoir access ❖ Improved production performance ❖ Lower overall cost Disadvantages ❖ Increased wellbore instability risks ❖ Challenges in cement placement ❖ Specialized equipment required 8 Technology Advancement of Multi Laterals (TAML) Complexity Level Pros Cons Application Example Level 1 Pros Lowest cost option Competent A mature carbonate field Simple completion carbonate in the Middle East needs design reservoirs cost-effective production Quick to execute Naturally fractured enhancement. The No specialized tools formations formation is naturally required Short-term fractured but stable, and No cement required production wells the operator wants to at junction Exploration wells access multiple reservoir Low-pressure compartments with Cons formations minimal investment. Open-hole lateral from open-hole No selective control Stable sandstone mother bore of laterals formations No hydraulic isolation No mechanical/ Limited mechanical hydraulic junction support Higher risk of Used in consolidated collapse formations Difficult re-entry operations Level 2 Pros Mixed formation Better main bore types An offshore field has integrity Primary wellbore competent reservoir rock Selective production stability concerns but unstable overburden. possible Pressure-depleted The operator needs to Relatively simple reservoirs maintain main bore completion Multiple zone integrity while accessing Lower cost compared production multiple reservoir to higher levels Enhanced oil compartments cost- Good main bore recovery projects effectively. Cased and accessibility Water/gas injection cemented Open lateral bore wells Cons Allows selective Lateral still vulnerable production to collapse No hydraulic isolation Partial mechanical support only 9 Level 3 Pros Unconsolidated Mechanical support for formations A heavy oil field in both bores Multiple reservoir Canada requires multiple Better lateral pressures laterals in accessibility Long-term unconsolidated sand. Enhanced well control production wells The operator needs Improved production Fields requiring mechanical support for flexibility frequent both main bore and workovers laterals but doesn't Cons Heavy oil require pressure isolation Cased/cemented No hydraulic isolation production between zones. main bore but Higher completion Thermal recovery uncemented laterals costs projects More complex completion equipment Mechanical anchor to More complex main bore installation Level 4 Pros High-pressure Better cement isolation formations A North Sea Enhanced wellbore Long-life field development requires stability developments multiple laterals in high- Good for long-term Complex pressure zones. The production reservoir operator needs good management mechanical support and Cons Water/gas some degree of zonal Higher completion injection wells isolation for proper Both main bore and costs Production wells reservoir management. laterals Complex cement job requiring isolation cased/cemented required Multi-zone Provides mechanical Challenging installation completion junction integrity Risk of cement failure requirements No hydraulic isolation Level 5 Pros High- High-pressure pressure/high- A deepwater Gulf of capability temperature Mexico project requires Selective wells accessing multiple production/injection Multiple pressure pressure zones with Enhanced safety regime reservoirs different fluid types. The features Environmentally operator needs full Cons sensitive areas pressure isolation Very high costs Complex between laterals for Sealed junctions Complex installation reservoir safety and production Full hydraulic and Specialized management optimization. mechanical equipment required Fields with Installation risks varying fluid types 10 Level 6 Pros Critical wells Highest integrity level High-risk An Arctic development Factory-tested environments requires maximum components Deepwater reliability in a hostile Maximum reliability developments environment. The Best pressure isolation Arctic operations operator needs factory- Excellent quality Complex reservoir tested components and control situations the highest level of Cons Multiple pressure mechanical and pressure Highest cost option zones integrity for safe, long- Junction integral to Most complex term production. main bore casing installation Highest complexity Limited availability and capability Chapter 4: Special Drillings Operations PART D Workover Operation Definition process of performing major maintenance on an oil or gas well after it has been completed and has been in operation for some time Reasons for workover Declining Well The well is not producing at expected rates due to Performance various factors. Mechanical Failures Failures in cementing, tubulars, packers, safety valves, or artificial lift equipment. Reservoir Data Collection Gathering pressure, fluid samples, and zonal productivity tests. Well Abandonment Temporarily or permanently shutting down a well. Types of workover Tubing Replacement Replacing worn-out or damaged tubing to restore operations production. Wellbore Cleanup Removing sand, paraffin, or scale that blocks fluid flow. Artificial Lift Maintenance Repairing or replacing ESPs (Electric Submersible Pumps) or gas lift valves Fishing Retrieving lost tools or equipment from the wellbore Workover Equipment Conventional Rigs Like drilling rigs but smaller, used for full workover operations. Wireline Units Used for running tools inside the wellbore without removing tubing. 11 Chapter 5: Well Completion and Components 1. Surface X-Mass Tree Primary Function Controls fluids produced from or Components injected into well Provides valve control system Enables vertical access for wireline operations Key Components Pressure gauges - Monitor well pressure Gauge flange/tree cap - Provides top seal Swab valve - Uppermost valve for intervention access Production wing valve - First valve on production wing Kill wing valve - Enables pumping equipment connection Master valves (Upper and Lower) - Main isolation valves Well Head Components A-section: Casing head B-section: Casing spool C-section: Tubing head Function Suspends casing and tubulars Provides surface closure Supports blowout preventer stack Bases for X-mas tree installation 2. Subsurface Subsurface Purpose Emergency well shut-in Equipment Safety Valve Prevents uncontrolled flow (SSV) Protects against blowouts Types Surface Controlled (SC-SSV) Remotely controlled from surface More reliable and widely used Subsurface Controlled (SSC-SSV) Actuated by well flow characteristics Installed via wireline Side Pocket Application Gas lift operations Mandrel Chemical injection (SPM) Circulation purposes Permanent downhole gauge installation 12 Sliding Side Function Enables tubing-annulus communication Door (SSD) Pressure equalization Fluid circulation Packers Function Provides annular seal Improves flow stability Protects outer containment system Enables zone isolation Type Retrievable packers Permanent packers Hydraulically-set packers Mechanically-set packers Additional Landing Nipple Purpose: Secure wireline/coiled tubing Component plugs Features: Internal machined profile Applications: Flow control equipment installation Perforated Joint Alternative fluid entry path Positioned below packer Backup if shoe becomes blocked Blast Joint Protects tubing from abrasive flow Made from high-quality alloy steel Used in multiple completions 3. Well Definitions The assembly of downhole tubular and equipment that Completion enables safe and efficient production from an oil/gas well Allows controlled flow of the well Objectives Provide communication between reservoir and well Optimize production/injection performance Ensure safety (e.g., sand control) 4. Types of well Open Hole Characteristics Production casing set above zone of completion Completion interest Simplest and cheapest completion Best for consolidated formations Advantages No perforation expenses Easy to deepen well Disadvantages Difficult to control water/gas production May require frequent cleanout Not suitable for unconsolidated formations Screen or Characteristic Uses wire-wrapped screen or slotted Pre-slotted steel pipe Liner Controls sand production Common in inclined/high angle wells Cemented Characteristic Most common type and Uses casing string or liner Cemented in place 13 Perforated Provides effective zonal isolation Casing 14