Cours Procédés de Production Mécanique PDF
Document Details
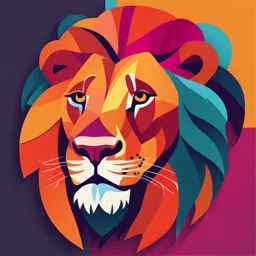
Uploaded by CommodiousLagrange7573
École Nationale d'Ingénieurs de Tunis ENIT
Sirine Chtourou
Tags
Summary
This document provides an overview of mechanical production processes, covering topics such as material classifications, transformation methods, and technologies used. It also includes information on different types of manufacturing processes and their applications.
Full Transcript
Cours : Procédés de Production Mécanique 2AGI ECOLE NATIONALE D’INGENIEURS DE TUNIS ENIT Cours : Procédés de Production Mécanique 2ème année Cycle d’Ingénieurs en Génie Industrielle Enseigné par :...
Cours : Procédés de Production Mécanique 2AGI ECOLE NATIONALE D’INGENIEURS DE TUNIS ENIT Cours : Procédés de Production Mécanique 2ème année Cycle d’Ingénieurs en Génie Industrielle Enseigné par : Sirine CHTOUROU CHTOUROU S ENIT Cours : Procédés de production mécanique 2AGI Introduction aux procédés de production mécanique CHTOUROU S ENIT 1/60 Cours : Procédés de production mécanique 2AGI Introduction aux procédés de production mécanique 1. Définition : Les procédés de production mécanique sont l'ensemble des méthodes employées pour convertir des matières premières en pièces ou produits finis (comme l’indique la figure 1), en respectant des spécifications. Ces méthodes sont essentielles dans pratiquement tous les domaines industriels : automobile, aéronautique, énergie, construction, etc. Figure 1 Exemples des produits finis 2. Classification des procédés de fabrication Les procédés de production mécanique peuvent être classifiés selon plusieurs critères tels que: 2.1. Nature du matériau: Métalliques: Comprend les procédés adaptés aux métaux, comme le soudage, le forgeage, et le moulage. Non métalliques: Englobe les plastiques, céramiques et composites, avec des techniques comme l'injection pour les plastiques et le frittage pour les céramiques. 2.2.État du matériau: Un exemple de classification des procédés de fabrication mécaniques selon l’état du matériau est illustré dans la figure 2. Solides: Utilisation de matériaux sous forme solide (poudres, filaments, plaques). Liquides: Techniques impliquant des matériaux liquides, comme le moulage par injection ou la coulée. CHTOUROU S ENIT 2/60 Cours : Procédés de production mécanique 2AGI Gazeux: Moins courant, mais inclut des procédés comme la pulvérisation. Figure 2 Classification des procédés de production mécanique selon l’état du matériau 2.3.Méthodes de transformation: Enlèvement de matière: Procédés où la matière est retirée pour obtenir la forme désirée (usinage, perçage). Déformation plastique: Transformation du matériau par déformation sans enlever de matière (forgeage, emboutissage). Fusion: Implique la fusion des matériaux pour les mouler (moulage, fonderie). Assemblage: Techniques qui unissent plusieurs pièces (soudage, collage). 2.4.Technologie utilisée: Procédés conventionnels : Techniques établies depuis longtemps comme le tournage et le fraisage. Procédés non conventionnels: assisté par ordinateur FAO. Fabrication additive: Techniques modernes qui construisent des objets couche par couche (impression 3D). 2.5.Cadence de production: Pièces unitaires: Fabrication d'objets uniques ou prototypes. Production en série: Techniques adaptées à la fabrication en grande quantité. CHTOUROU S ENIT 3/60 Cours : Procédés de production mécanique 2AGI Les procédés de production mécanique se classifient en deux grandes catégories : ceux avec enlèvement de matière et ceux sans enlèvement de matière. Cette classification permet de choisir la méthode adaptée selon les exigences de fabrication et les propriétés du matériau. a) Procédés sans enlèvement de matière : Ces procédés transforment la matière sans retirer de matériau. Ils utilisent la déformation, l’assemblage ou la fusion pour donner forme aux pièces. Mise en forme : Forge (à chaud, à froid) Emboutissage Extrusion Laminage Fabrication additive : Dépôt de matière fondue (FDM) Frittage laser sélectif (SLS) Stéréolithographie (SLA) Fonderie : Moulage en sable Moulage en moules métalliques Assemblage : Soudage (TIG, MIG, laser) Collage Rivetage b) Procédés avec enlèvement de matière : Ces procédés consistent à retirer une partie de la matière pour obtenir la forme souhaitée. Usinage conventionnel : CHTOUROU S ENIT 4/60 Cours : Procédés de production mécanique 2AGI Tournage Fraisage Perçage Alésage Usinage non conventionnel : Usinage par électroérosion (EDM) Découpe laser Découpe par jet d’eau Centre d’usinage CNC (tour, fraise) Abrasion : Rectification Polissage Ponçage 3. Propriétés des matériaux et essais de caractérisation : 3.1.Propriétés des matériaux : Les matériaux se classent en 4 catégories selon leur nature, leurs propriétés et leurs liaisons chimiques : Matériaux métalliques : Métaux purs ou alliages avec liaisons métalliques. Matériaux organiques : Polymères, élastomères et matériaux biologiques avec liaisons covalentes et faibles. Matériaux minéraux : Roches, oxydes, verres, céramiques avec liaisons ioniques ou covalentes. Matériaux composites : Association structurée de matériaux différents, issus des classes précédentes. Les propriétés des matériaux, qu'elles soient physico-chimiques ou d'usage, dépendent de la nature des atomes et des liaisons chimiques (masse volumique, stabilité mécanique et CHTOUROU S ENIT 5/60 Cours : Procédés de production mécanique 2AGI thermique, conductivité, etc.) ainsi que de la structure atomique (dureté, ductilité, ténacité, rigidité plastique). Ils sont classifiés comme suit ; a) Propriétés mécaniques : Résistance mécanique : capacité à supporter des charges (traction, compression). Dureté : résistance à la pénétration ou à l’usure (tests Brinell, Rockwell, Vickers). Résilience : capacité à absorber l’énergie avant la rupture. Ductilité : aptitude à se déformer sans se rompre (étirement, pliage). Ténacité : résistance à la propagation des fissures. b) Propriétés physiques Densité : masse par unité de volume. Conductivité thermique : capacité à transmettre la chaleur. Conductivité électrique : aptitude à conduire l’électricité. Expansion thermique : changement de volume avec la température. Point de fusion : température à laquelle un matériau fond. c) Propriétés technologiques Usinabilité : facilité avec laquelle un matériau peut être usiné. Forgeabilité : aptitude à la déformation plastique. Soudabilité : capacité à être assemblé par soudage. Coulabilité : aptitude à remplir un moule (fonderie). d) Propriétés chimiques Résistance à la corrosion : aptitude à résister à l’environnement (oxydation, humidité). Réactivité chimique : interactions avec d’autres substances. CHTOUROU S ENIT 6/60 Cours : Procédés de production mécanique 2AGI 3.2. Essais mécaniques de caractérisation des matériaux : Les essais mécaniques de caractérisation (figure 3) permettent d’évaluer le comportement des matériaux soumis à différentes contraintes. Ils fournissent des données essentielles sur des propriétés comme la résistance, la dureté, l’élasticité ou la ductilité. Méthodes de caractérisation des propriétés ESSAI DE ESSAI DE CHOC TRACTION CHARPY ESSAI DE ESSAI DE DURETE FATIGUE Figure 3 Essais mécaniques de caractérisation des matériaux a) Essai de traction : Une poutre est soumise à une traction simple si, elle est exposée à deux forces F directement opposées appliquées au centre de la surface des sections extrêmes. Ces forces ont pour effet de tirer la poutre dans des directions opposées, entraînant ainsi une tendance à l'allongement de la poutre (figure 4). F (N) Mors mobile Acquisition des données avec Δl (mm) ordinateur et un logiciel ‘Wintest F ( MPa) analysis’ S0 Mors fixe Machine de traction de type: M350-10CT l 100 % l0 Figure 4 Description d’essai de traction L’essai de traction permet de ; Etudier le comportement élastique, plastique d’un matériau et sa résistance à la rupture. CHTOUROU S ENIT 7/60 Cours : Procédés de production mécanique 2AGI Identifier la corrélation entre l'effort appliqué et l'allongement résultant pour établir la loi de Hooke ; Évaluer le module d'élasticité longitudinale (module d'Young E) de différents matériaux testés…. L’essai de traction permet d’étudier le comportement élastique, plastique et la résistance à la rupture d’un matériau sous forme d’une courbe obtenue f . Ainsi, les propriétés mécaniques qui en découlent lors d’un essai de traction (illustrées dans la figure 5) sont ; l l l0 Déformation ou l'allongement relatif noté ε (%) : 100 100 l0 l0 F Contrainte σ (MPa) : S0 Limite d’élasticité ou la résistance élastique à la traction Re (MPa) : la contrainte en Fe point A : e Re S0 Contrainte maximale ou la résistance maximale à la rupture Rm (MPa) : la contrainte au Fm point C m Rm S0 Allongement de rupture A%. Module de Young E : dans la zone élastique OA, l’évolution de la contrainte en fonction de déformation est linéaire. La pente de cette droite est définie comme le module de Young ou le module d’élasticité ou le coefficient d’élasticité longitudinal. C’est la loi F L0 de Hoocke : E S0 L Striction Z (%) : c’est la réduction de la section maximale de l’éprouvette rompue. Elle S 0 Su est définie comme l’aptitude à la déformation : Z 100 avec S0 est la section S0 sollicitée initiale (avant l’essai) et Su est la section sollicitée après la rupture. CHTOUROU S ENIT 8/60 Cours : Procédés de production mécanique 2AGI F ( MPa) S0 Rr l 100 % l0 Allongement à la rupture Ar% Figure 5 Courbe contrainte en fonction de déformation lors de l’essai de traction b) Essai de dureté : La dureté d’un matériau (symbole H) caractérise la capacité d’un matériau à résister au marquage (empreinte…), à l’usure et à l’érosion. Les méthodes de mesure de la dureté, telles que Brinell, Rockwell et Vickers, représentent des approches distinctes mais complémentaires pour évaluer la résistance d'un matériau à la déformation plastique, chacune offrant des avantages spécifiques en fonction des propriétés du matériau et des conditions de test (tableau 1). Tableau 1 Comparaison entre les méthodes du mesure de la dureté Type d’essai Brinell Vickers Rockwell Symbole HB (Hardness Brinell) HV (Hardness HR (Hardness Rockwell) Vickers) Pénétrateur: Nature Acier trempé ou carbure du Diamant Diamant Acier tungstène trempé Forme Sphère Pyramide à base Cône Sphère carré CHTOUROU S ENIT 9/60 Cours : Procédés de production mécanique 2AGI Mode Chargement progressif Comme HB Pré-charge F0 puis charge d’application pendant 15s, maintien 15s supplémentaire, et retour à F0 de la charge puis décharge Valeur Moyenne de 2 diamètres Moyenne des 2 Profondeur de pénétration e mesurée perpendiculaires d1 et d2 de diagonales d1 et d2 l’empreinte Mesure pour P/surface de la calotte P/surface de Complément de la profondeur H sphérique l’empreinte de pénétration HB 2F pyramidale HRC 100 e2 e0 gD D D 2 d 2 HV 0,189 F HRB 130 e2 e0 d2 d1 d 2 d 2 Application Aciers non trempés. Fontes, Aciers trempés. Aciers trempés principale soudures, métaux non- Aciers à outils ferreux Avantages Etant relativement marge Pratiquement Mesure plus simple. La lecture HB convient pour les indépendant de la directe permet une acquisition matériaux hétérogènes charge. Il convient des données bien pour les pièces minces Inconvénients HB est fonction de la Ne convient pas pour Dispersion importante des charge. Formation de les matériaux mesures bourrelets au bord de hétérogènes (petites l’empreinte empreintes) CHTOUROU S ENIT 10/60 Cours : Procédés de production mécanique 2AGI c) Essai de choc Charpy : La résilience est une caractéristique mécanique du matériau noté K. elle est définie comme la capacité d’un matériau à absorber les chocs mécaniques sans rompre Elle est mesurée à partir de l’énergie nécessaire pour un pendule pesant briser une éprouvette entaillée. C’est l’énergie consommée par la rupture de l’éprouvette. Cette énergie dissipée est mesurée avec l’essai de choc Charpy. Essai de choc Charpy ou essai de résilience consiste à rompre par un choc une éprouvette parallélépipédique entaillée reposant sur deux appuis (figure 6). La résilience est influencée par la forme de l’entaille de l’éprouvette, la température et les traitements thermiques. Ce test consiste à appliquer à l’aide d’une pendule pesant un choc mécanique sur une éprouvette entaillée. L’énergie cinétique du pesant est convertie en une énergie mécanique. Une partie de cette énergie est absorbée par l’éprouvette provoquant sa rupture ou sa déformation. La résilience, ainsi est calculée comme le rapport entre l’énergie dissipée et la section sollicitée. é𝑛𝑒𝑟𝑔𝑖𝑒 𝑑𝑖𝑠𝑠𝑖𝑝é𝑒 (𝐽) résilience K (J/cm2)= résilience ' K ' résilience ' K ' 𝑠𝑒𝑐𝑡𝑖𝑜𝑛 𝑠𝑜𝑙𝑙𝑖𝑐𝑖𝑡é𝑒 (𝑐𝑚2) Pupitre de Pendule pesant commande Figure 6 Description d’essai de choc Charpy CHTOUROU S ENIT 11/60 Cours : Procédés de production mécanique 2AGI 3.3.Traitement thermiques : Les traitements thermiques des métaux et alliages visent à altérer leurs propriétés uniquement en ajustant la température. Voici les principales catégories de traitement thermique : Trempe Revenu Recuit En général, ces traitements n'altèrent pas la composition chimique des matériaux ou alliages, mais peuvent influencer leur constitution (état du carbone et forme du fer), leur structure (taille et distribution des grains) et leur état mécanique. Ils sont définis comme un ensemble des opérations : un chauffage suivi d’un refroidissement contrôlé. a) Trempe : C'est un processus où un matériau, généralement en acier, est chauffé à une température élevée puis rapidement refroidi dans un milieu tel que l'eau, l'huile ou l'air. Ce refroidissement rapide permet de figer la structure cristalline du matériau, ce qui entraîne une augmentation de sa dureté. La trempe est réalisée pour durcir l'acier en le rendant plus dur mais souvent moins ductile. Son cycle thermique est basé sur (figure 7) : a) Chauffage à une température d’austénitisation Ta : Les constituants ferrite et perlite se transforment en austénite. b) Maintenir à la température constante pour une durée spécifique afin d’assurer l’homogénéisation de la température dans toute la pièce (de la surface jusqu’au cœur de la pièce formation de l’austénite). c) Refroidissement rapide : avec l’eau afin que l’austénite se transforme en martensite. L’objectif de ce traitement thermique est ; Re↑ HB↑ Rr↑ A%↓ K↓ CHTOUROU S ENIT 12/60 Cours : Procédés de production mécanique 2AGI Figure 7 Principe de traitement thermique Trempe b) Revenu : C'est un processus qui suit généralement la trempe. Après avoir durci l'acier par trempe, il est chauffé à une température inférieure à celle utilisée pour la trempe, puis refroidi lentement. Ce processus de chauffage et de refroidissement contrôlés vise à réduire les contraintes internes créées par la trempe, tout en ajustant les propriétés mécaniques de l'acier. Le revenu réduit la dureté excessive résultant de la trempe, améliore la ténacité et la résistance à la rupture, et réduit la fragilité de l'acier tout en maintenant une certaine dureté. L’objectif de ce traitement thermique est ; Re ↓ HB↓ Rr↓ A%↑ K↑ Figure 8 Principe de traitement thermique Revenu CHTOUROU S ENIT 13/60 Cours : Procédés de production mécanique 2AGI c) Recuit : Le processus de recuit, contrairement à la trempe, vise à optimiser la ductilité et la résilience du métal, atteignant ainsi des niveaux maximaux des A% et K, tout en minimisant les valeurs de Rr et H. La structure résultante, composée de perlite et de ferrite, améliore significativement l'usinabilité du matériau (figure 3). Le processus implique d'abord le chauffage du matériau au-delà de sa température d'Austénisation, suivi d'une période de maintien à cette température pour assurer une uniformité structurelle, puis d'un refroidissement progressif. Les traitements surfaciques permettent d’obtenir des propriétés spécifiques à la surface d’une pièce tout en préservant les caractéristiques internes. Selon leur principe, ils améliorent principalement : La dureté en surface La résistance à l’usure La résistance à la corrosion Le comportement au frottement Par exemple, pour un pignon, on recherche une grande dureté en surface (résistance au frottement) et une bonne résilience au cœur (résistance aux contraintes internes). Les principales méthodes de durcissement de surface incluent : La cémentation La nitruration La trempe superficielle CHTOUROU S ENIT 14/60 Cours : Procédés de production mécanique 2AGI Procédés de fabrication avec enlèvement de matière CHTOUROU S ENIT 15/60 Cours : Procédés de production mécanique 2AGI Partie 1: Procédés avec enlèvement de matière : Procédé de tournage 1. Définition du tournage : Le tournage est un processus de fabrication de pièces métalliques par l'enlèvement de matière sous forme de copeaux. Il est principalement utilisé pour donner forme (mise en forme) aux surfaces extérieures et intérieures de pièces de révolution (figure 9). Il peut également être utilisé pour créer des formes internes, telles que des trous, des alésages, ou des filetages, etc. Lors du tournage, la pièce à usiner est généralement fixée dans un dispositif appelé mandrin, et elle est mise en rotation de manière uniforme. C’est le mouvement de coupe. En même temps, un outil muni d'une seule arête de coupe se déplace de manière linéaire, soit en parallèle, soit en oblique par rapport à l'axe de rotation de la pièce. C’est le mouvement d'avance. Figure 9 Principe du tournage L'équipement employé pour effectuer ce processus est appelé un tour (voir Figure 10). La pièce est mise en rotation par la broche à l'aide d'un mandrin ou d'un dispositif spécial. La vitesse de rotation de la broche peut être modifiée grâce à une boîte de vitesses (exprimée en N [tr/min.]). Le mouvement de translation du traînard est contrôlé soit par la barre de chariotage soit par la vis-mère. Une boîte d'avances permet de réguler la vitesse du traînard, ce qui détermine le déplacement de l'outil par rapport à un tour complet de la pièce (exprimé en f [mm/tr]). CHTOUROU S ENIT 16/60 Cours : Procédés de production mécanique 2AGI Figure 10 Tour parallèle 2. Opérations de tournage : Les opérations d’usinage se divisent en deux familles : usinage externe et interne (figures 11, 12 et 13). a) Usinage externe : Figure 11 : Usinage externe b) Usinage interne : Figure 12 : Usinage interne CHTOUROU S ENIT 17/60 Cours : Procédés de production mécanique 2AGI Figure 13 Opérations d’usinage 3. Outils de coupe en tournage : Outil de coupe en tournage peut être classifié selon l’opération d’usinage ou le type de plaquette (sa forme, matériau), comme indique la figure 14. Il existe divers matériaux pour la plaquette de l’outil comme indique la figure 15. Un matériau de coupe idéal doit posséder les caractéristiques suivantes : Dureté : Résister à l’usure en dépouille et à la déformation. Ténacité : Supporter les risques de rupture. Inertie chimique : Ne pas réagir avec la matière usinée. Stabilité chimique : Résister à l’oxydation et à la diffusion. Résistance thermique : Supporter les variations thermiques brusques. CHTOUROU S ENIT 18/60 Cours : Procédés de production mécanique 2AGI Figure 14 Types d’outil d’usinage Figure 15 Résistance à l’usure en fonction de la ténacité pour différents matériaux de coupe L'affûtage de l'outil prendra en compte trois angles principaux, comme les montre la figure 16: Angle de dépouille (a) : empêche le talonnage et facilite la pénétration de l'outil dans la pièce. Angle tranchant (b) : permet à l'outil de pénétrer dans la matière et assure la séparation ainsi que le cisaillement du copeau. Angle d'attaque (c) : facilite l'évacuation du copeau. CHTOUROU S ENIT 19/60 Cours : Procédés de production mécanique 2AGI Figure 16 Elément de la partie active de l’outil et les angles de coupe Après le maintien de l’outil dans le porte outil (tourelle), il est recommandé de faire le centrage de l’outil avec l’axe de la pièce à usiner. Réglage correct de l'outil L'outil est positionné à la bonne hauteur à l'aide d'une ou plusieurs cales. Une cale de protection doit également être utilisée. Outil mal réglé Si l'outil est placé trop haut par rapport au centre, réduire le nombre de cales. Toutes les cales doivent être alignées sur un même plan. Outil mal réglé Si l'outil est placé trop bas par rapport au centre, ajouter une ou plusieurs cales. a) Outils à charioter : Les outils de chariotage, qu'ils soient positionnés à gauche ou à droite, permettent d'effectuer le travail dans une seule direction pour créer des cylindres ou des cônes sur la surface extérieure de la pièce (figure 17). Lorsqu'une pièce présente un épaulement, le résultat CHTOUROU S ENIT 20/60 Cours : Procédés de production mécanique 2AGI est une surface externe qui suit la forme de la pièce (travail d'enveloppe) et une autre surface qui suit la forme de l'outil lui-même (travail de forme). Figure 17 Chariotage : outil à charioter b) Outils à dresser : Lorsqu'il s'agit de créer des surfaces planes extérieures sur une pièce, le travail se fait dans une seule direction perpendiculaire à l'axe de la pièce (figure 18). En cas de présence d'un épaulement sur la pièce, cela entraîne la formation d'une surface qui suit la forme de la pièce (travail d'enveloppe) et une autre surface qui suit la forme de l'outil lui-même (travail de forme). Figure 18 Dressage : outil à dresser c) Les outils à charioter–dresser : Les outils de chariotage-dressage offrent au moins deux directions de travail possibles, ce qui leur permet d'accomplir des opérations de chariotage et de dressage pour créer des surfaces extérieures en suivant la forme de la pièce (travail d'enveloppe) comme montre la figure 19. CHTOUROU S ENIT 21/60 Cours : Procédés de production mécanique 2AGI Figure 19 Outil à charioter dresser 4. Paramètres de coupe : Pour obtenir des résultats satisfaisants lors de l'usinage, tels qu'un bon état de surface, une vitesse d'usinage optimale, et une usure modérée de l'outil, il est essentiel de choisir judicieusement les paramètres de coupe. Vitesse de rotation de la broche (N) (tr/min) : 1000 Vc N (1) D Avec D est le diamètre à usiner (mm) Vitesse de Coupe (Vc) [m/min] : Cela fait référence à la vitesse linéaire de déplacement de l'outil dans le sens du mouvement de coupe. La vitesse de rotation (N) [tr/min] est également importante, et elle représente le nombre de tours par minute que réalise la pièce en cours d'usinage. Ces deux paramètres sont liés par la formule : D N Vc (2) 1000 Où D représente le diamètre d'usinage de la pièce en millimètres. Avance par Tour (f) [mm/tr] : Il s'agit du déplacement de l'outil lors du mouvement d'avance, équivalent à un tour complet de la pièce. Cette valeur influe sur la quantité de matière enlevée à chaque passe (figure 20). CHTOUROU S ENIT 22/60 Cours : Procédés de production mécanique 2AGI Figure 20 Description des paramètres de coupe Vitesse d’avance (Vf) (mm/min) : la vitesse de déplacement d’un point considéré de l’outil ou de la pièce qui se déplace pendant l’usinage (qui possède le mouvement d’avance Mf) Vf f N (3) Profondeur de Passe (ap) [mm] : La profondeur de passe désigne l'épaisseur de la couche de matière retirée de la pièce lors de chaque passe de l'outil. Le choix de cette valeur peut influencer la durée de vie de l'outil et la qualité de la surface usinée. Le réglage approprié de ces paramètres est crucial pour obtenir des résultats optimaux tout en évitant des problèmes tels que la surchauffe de l'outil, des vibrations excessives, ou une usure prématurée de la pièce. La sélection des paramètres de coupe doit tenir compte de divers facteurs, y compris la matière de la pièce à usiner, la géométrie de la pièce, et les performances de la machine d'usinage (figure 21). Figure 21 Paramètres de coupe 5. Montages d’usinage (tour) : a) Montage en air : Pour maintenir la pièce en position, elle est fixée sur le porte-pièce par une seule de ses extrémités. Ce type de fixation est couramment employé pour des pièces de dimensions CHTOUROU S ENIT 23/60 Cours : Procédés de production mécanique 2AGI relativement courtes, où la longueur (L) de la pièce est significativement plus petite que son diamètre (D), soit L/D < 2. Dans ce contexte, le dispositif de fixation couramment utilisé est un mandrin (figure 22). Figure 22 Montage en air b) Montage mixte : La fixation de la pièce est réalisée d'un côté à l'aide d'un mandrin, tout comme dans le cas d'un montage en l'air, tandis que de l'autre côté de la pièce, elle est soutenue par une pointe tournante montée sur la poupée fixe. Le mandrin est utilisé pour maintenir fermement la pièce en place et la faire tourner, ce type de montage est conçu pour les pièces de grande longueur. Cependant, il ne permet pas l'usinage de l'intérieur des pièces (figure 23). Figure 23 Montage mixte c) Montage entre pointes : La fixation de la pièce est effectuée à l'aide de deux pointes, qui sont placées dans les centres de la pièce. Ce type de montage est principalement utilisé lorsque l'on souhaite éviter la flexion des pièces, en particulier lorsque la longueur de la pièce (L) est significativement plus grande que son diamètre (D), généralement lorsque L > 2 à 3 D. Ce montage permet d'obtenir des conditions géométriques spécifiques et est souvent utilisé lorsque des tolérances strictes doivent être respectées. L'entraînement de la pièce est généralement assuré par un dispositif de type CHTOUROU S ENIT 24/60 Cours : Procédés de production mécanique 2AGI "toc et pousse-toc" pour éviter le glissement ou la rotation non désirée de la pièce pendant l'usinage (figure 24). Figure 24 Montage entre pointes CHTOUROU S ENIT 25/60 Cours : Procédés de production mécanique 2AGI Partie 2: Procédés avec enlèvement de matière : Procédé de Fraisage 1. Définition de fraisage : Le fraisage est un processus d'usinage qui utilise une fraise rotative pour enlever de la matière et donner forme à une pièce en la coupant ou en la façonnant. L'outil à dents multiples, communément appelé "fraise", tourne en effectuant un mouvement circulaire uniforme, ce qui génère le mouvement de coupe. Parallèlement, la pièce est déplacée en ligne droite par rapport à la fraise, créant ainsi le mouvement d'avance (figure 25). Figure 25 Procédés de fraisage La machine est dite fraiseuse (figure 26). Elle est utilisée principalement pour l'usinage de pièces prismatiques. L'enlèvement de matière se fait par l'interaction entre la trajectoire de la pièce et la rotation de l'outil, produisant des copeaux. Figure 26 Composants d’une fraiseuse CHTOUROU S ENIT 26/60 Cours : Procédés de production mécanique 2AGI 2. Modes de fraisage : Il existe deux modes distincts de fraisage : le fraisage de face, également connu sous le nom de fraisage en bout, et le fraisage de profil, également désigné sous le nom de fraisage en roulant (figure 27). Le fraisage en bout (frb) se caractérise par l'orientation de l'axe de la fraise, qui est perpendiculaire au plan usiné. Cela implique que la fraise est positionnée de manière à travailler directement sur la face de la pièce. Le fraisage en roulant (frr) suppose que la génératrice de la fraise soit parallèle à la surface usinée. Dans ce mode, la fraise est disposée de manière à effectuer un mouvement latéral le long de la pièce, permettant ainsi la création de formes ou de profils spécifiques. Fraisage en bout Fraisage en roulant Fraisage combiné Fraisage en opposition Fraisage en avalant Figure 27 Modes de fraisage CHTOUROU S ENIT 27/60 Cours : Procédés de production mécanique 2AGI 3. Outils de fraisage : L’outil de fraisage (fraise) est caractérisé par : Sa taille : En fonction du nombre d'arêtes tranchantes par dent, il existe des fraises à une taille, deux tailles ou trois tailles. Nombre de dents Sa forme : La forme des fraises varie en fonction du profil de leurs génératrices par rapport à l'axe de l'outil. On distingue principalement les fraises cylindriques, les fraises coniques, et les fraises de forme (figure 28). Figure 28 Classification de l’outil de fraisage selon sa forme Sa denture : La denture des fraises dépend du sens d'inclinaison des arêtes tranchantes par rapport à l'axe de la fraise. On distingue les dentures hélicoïdales à droite ou à gauche, ainsi que les dentures à double hélice alternées. Si l'arête tranchante est parallèle à l'axe de la fraise, on parle de denture droite (figure 29). Figure 29 Classification de l’outil de fraisage selon le type de sa denture Mode de fixation : A trou lisse ou taraudé ; à queue cylindrique ou conique (figure 30). Figure 30 Classification de l’outil de fraisage selon le mode de fixation CHTOUROU S ENIT 28/60 Cours : Procédés de production mécanique 2AGI Dimensions : Pour une fraise deux tailles : diamètre et hauteur taillée. Pour une fraise trois tailles : diamètre de l’outil, épaisseur, diamètre de l’alésage. Pour une fraise conique pour queue d’aronde : l’angle, le diamètre de l’outil et l’épaisseur. Type de plaquette : (figure 31) Figure 31 Classification de l’outil de fraisage selon le type de plaquette L’outil de fraisage se compose par : fraise, plaquette, dispositif de fixation et porte fraise comme montre la figure 32. Figure 32 Composant de l’outil de fraisage 4. Maintien de la pièce : Pour le maintien de la pièce sur la table de la fraiseuse, il existe plusieurs méthodes telles que : L’étau (figure 33) : Il sert à maintenir les pièces prismatiques. Composé de deux mors, le mors fixe est attaché au bâti, tandis que le mors mobile, relié au bâti par une glissière, permet de serrer la pièce. Figure 33 Etau de serrage CHTOUROU S ENIT 29/60 Cours : Procédés de production mécanique 2AGI La plaque support (figure 34) : Elle permet de fixer les pièces minces grâce à des trous taraudés M8 espacés de 30 mm. Figure 34 Plaque support Le mandrin (figure 35) : Utilisé pour les pièces cylindriques, il permet d’usiner des poches ou des trous de passage pour les vis. Figure 35 Mandrin Plateau circulaire (figure 36) : Généralement il est équipé de rainures en T ou de brides pour sécuriser les pièces. Il est utilisé pour les opérations nécessitant des mouvements circulaires, comme le fraisage de profils arrondis, la découpe d'engrenages ou la réalisation de trous circulaires équidistants. Figure 36 Plateau circulaire Diviseur (figure 37) : Il permet de diviser une pièce en segments égaux pour réaliser des opérations précises comme le fraisage de dentures d'engrenages, de cannelures ou de profils réguliers. CHTOUROU S ENIT 30/60 Cours : Procédés de production mécanique 2AGI Figure 37 Diviseur 5. Opérations de fraisage : La figure 38 décrit les différentes opérations de fraisage. Figure 38 Opérations de fraisage 6. Paramètres de coupe : Pour obtenir des résultats satisfaisants lors de l'usinage, tels qu'un bon état de surface, une vitesse d'usinage optimale, et une usure modérée de l'outil, il est essentiel de choisir judicieusement les paramètres de coupe (figure 39). Vitesse de rotation de l’outil (N) (tr/min) : 1000 Vc N D Avec D est le diamètre de l’outil (mm). Vitesse de Coupe (Vc) [m/min] : Cela fait référence à la vitesse linéaire de déplacement de l'outil dans le sens du mouvement de coupe. La vitesse de rotation (N) [tr/min] est également CHTOUROU S ENIT 31/60 Cours : Procédés de production mécanique 2AGI importante, et elle représente le nombre de tours par minute que réalise la pièce en cours d'usinage. Ces deux paramètres sont liés par la formule : D N Vc 1000 Avance par dent (f) [mm/tr] : Il s'agit du déplacement de l'outil lors du mouvement d'avance, équivalent à un tour complet de la pièce. Cette valeur influe sur la quantité de matière enlevée à chaque passe. Vitesse d’avance (Vf) (mm/min) : la vitesse de déplacement d’un point considéré de l’outil ou de la pièce qui se déplace pendant l’usinage (qui possède le mouvement d’avance Mf). Vf f Z N Avec Z est le nombre des dents Profondeur de Passe (ap) [mm] : La profondeur de passe désigne l'épaisseur de la couche de matière retirée de la pièce lors de chaque passe de l'outil. Le choix de cette valeur peut influencer la durée de vie de l'outil et la qualité de la surface usinée. Figure 39 Paramètres de coupe lors de fraisage CHTOUROU S ENIT 32/60 Cours : Procédés de production mécanique 2AGI Partie 3: Procédés avec enlèvement de matière : autres Procédés 1. Perçage : Le perçage est une opération d'usinage qui consiste à créer des trous cylindriques dans une pièce à l'aide d'un outil rotatif appelé foret. Cette opération est réalisée sur des machines spécifiques, comme les perceuses ou les centres d'usinage, ou sur des machines polyvalentes, comme les tours ou les fraiseuses. La perceuse (figure 40) est principalement utilisée pour percer les pièces, l'enlèvement de matière étant réalisé par la combinaison des mouvements de rotation et de translation de l'outil dans la pièce (figure 41). Figure 40 Description de la perceuse Figure 41 Principe de perçage 2. Rectification : La rectification d'une pièce mécanique améliore sa précision dimensionnelle et son état de surface. C’est un usinage par abrasion. Les deux principales techniques sont (figure 42) : Rectification plane : concerne les surfaces planes. Réalisée sur une rectifieuse plane. CHTOUROU S ENIT 33/60 Cours : Procédés de production mécanique 2AGI Lors de la rectification plane, l'enlèvement des copeaux est principalement assuré par les grains situés sur la périphérie de la meule. Rectification cylindrique : concerne les surfaces cylindriques. Il existe deux types de rectification cylindrique : la rectification cylindrique longitudinale extérieure et la rectification cylindrique intérieure. Rectification plane Rectification cylindrique Figure 42 deux principales techniques de rectification 3. L'usinage par décharge électrique (EDM) L'usinage par décharge électrique (EDM) est une technique de fabrication qui consiste à retirer de la matière d'une pièce à usiner par une série de décharges électriques rapides entre des électrodes immergées dans un fluide diélectrique (figure 43). Ce procédé est idéal pour créer des pièces difficiles ou impossibles à usiner à l'aide de méthodes traditionnelles, car il repose sur des forces électriques plutôt que mécaniques. Figure 43 Principe d'usinage par décharge électrique (EDM) CHTOUROU S ENIT 34/60 Cours : Procédés de production mécanique 2AGI 4. Usinage par Découpe laser : L'usinage par découpe laser est une méthode de fabrication qui utilise un faisceau laser pour découper ou graver des matériaux avec une grande précision (figure 44). Le principe de fonctionnement est basé sur : Un laser qui focalise une grande quantité d'énergie sur une petite surface du matériau. Une chaleur intense qui provoque la fusion, la combustion ou la vaporisation du matériau. Un jet de gaz (air, azote ou oxygène) qui élimine les débris ou améliore la coupe. Figure 44 Usinage par Découpe laser 5. Usinage par découpe par jet d’eau : L'usinage par découpe par jet d’eau (figure 45) est une technique d’usinage qui utilise un jet d'eau à très haute pression, parfois mélangé à des abrasifs, pour découper une large gamme de matériaux. En effet, un jet d'eau sous pression, souvent supérieur à 4000 bars, est projeté à grande vitesse (jusqu'à 900 m/s) par une buse. Par exemple, les matériaux tendres (caoutchouc, plastique) sont découpés avec de l’eau pure. Les matériaux durs (métaux, céramiques) nécessitent un abrasif (généralement de la grenaille de grenat) ajouté au jet. CHTOUROU S ENIT 35/60 Cours : Procédés de production mécanique 2AGI (1) Tube de collimation d’eau (2) Buse de débit (3) Chambre de mélange (4) Capuchon anti-éclaboussures (5) Jet haute pression (6) Matériau à découper (7) Grille de support (8) Bassin d’eau (9) Matériau découpé (10) Canon de focalisation (11) Abrasif Figure 45 Usinage par découpe par jet d’eau CHTOUROU S ENIT 36/60 Cours : Procédés de production mécanique 2AGI Procédés de fabrication sans enlèvement de matière CHTOUROU S ENIT 37/60 Cours : Procédés de production mécanique 2AGI Partie 1: Procédés sans enlèvement de matière : procédés de moulage 1. Définition : La fonderie, ou moulage, est un procédé de fabrication de pièces brutes par coulage de matériaux métalliques. Elle consiste à produire des pièces brutes en coulant des métaux fluides avec une température de fusion et un retrait limité, comme les fontes, aciers, aluminium et cuivre. Le moulage consiste à : Fondre le métal. Le couler dans un moule reproduisant l'empreinte de la pièce. Démouler la pièce une fois solidifiée. 2. Classification : Figure 46 décrit les différents types de moulage selon la moule et le modèle. Figure 46 Types de moulage 3. Moulage en sable : Le moulage en sable est un moulage avec moule non permanent et un modèle permanent. Le moule non permanent est fabriqué principalement à partir de matériaux de moulage, comme le sable. Il est constitué d’une ou plusieurs parties formant une empreinte correspondant à la forme de la pièce (figure 47). Après la solidification et le refroidissement de l’alliage, le moule est détruit pour extraire la pièce brute, d’où le terme moulage en moule non permanent. CHTOUROU S ENIT 38/60 Cours : Procédés de production mécanique 2AGI Châssis inférieur et supérieur : Cadre Système de remplissage : métallique retenant le sable comprimé Ensemble permettant de remplir autour du modèle (moulage en moule l’empreinte (descente et chenal). non permanent). Joint de moule (plan de joint) : Masselotte : Réserve de métal Zone de séparation entre les compensant le retrait volumique lors de châssis. Une pièce nécessitant la solidification et limitant les défauts plusieurs châssis aura plusieurs dans la pièce. plans de joint Évent : Canal facilitant Empreinte : Cavité reproduisant la l’évacuation des gaz de forme de la pièce brute. l’empreinte. Figure 47 Moulage en sable 3.1.Moule : Il existe trois types de moules : Moule à un élément qui se compose d'une seule partie comme indique la figure 48a. L'empreinte reste ouverte sur la partie supérieure ou peut être fermée à l'aide d'un noyau. Moule à deux éléments qui est constituée de deux châssis (figure 48b), un inférieur et un supérieur. La plus grande surface des modèles doit être positionnée dans le plan de joint des châssis. Moule à plusieurs éléments qui est composé de trois éléments ou plus (figure 48c). Le châssis nommé chape est situé entre le châssis supérieur et le châssis inférieur. En effet, le modèle utilisé doit comporter deux plans de joints. a) b) c) Figure 48 Types de moules : a) moule à un élément, b) moule à deux éléments c) moule à plusieurs éléments 3.2.Sable de moulage Le sable de moulage doit être : -Infusible pour résister à la chaleur. -Résistant pour éviter l’érosion. -Poreux pour laisser passer les gaz. Il se compose de : Sable siliceux (86-96%) : Résiste à la fusion. CHTOUROU S ENIT 39/60 Cours : Procédés de production mécanique 2AGI Argile (3-10%) : Lie les grains et maintient le moule. Noir de fonderie (2-6%) : Assure porosité et évacuation des gaz. 3.3.Modèle : Le modèle est utilisé pour créer une cavité dans le sable, permettant d’obtenir une pièce brute après coulée et refroidissement du métal. Il est en bois ou en métal (grandes séries). L’empreinte prend en compte : Retrait : Contraction du métal au refroidissement. Dimensions majorées de 1 % pour la fonte et 2 % pour l'acier. Surépaisseur d'usinage : Ajout de 2 à 3 mm pour permettre l'usinage. Dépend du métal, de la taille et de la position de la pièce. Dépouille : Pentes (2 à 5 %) sur les parois pour faciliter le démoulage. Portées du noyau : Assurent la stabilité du noyau pour les pièces creuses. 3.4.Noyau : Le noyau doit : Résister à la poussée du métal liquide et faciliter les manipulations. Être perméable aux gaz pendant la coulée. Rester infusible pour éviter la pénétration du métal. Se désagréger facilement après la coulée pour libérer les parties creuses. 3.5.Etapes : Figure 49 Etapes de moulage en sable CHTOUROU S ENIT 40/60 Cours : Procédés de production mécanique 2AGI Partie 2: Procédés sans enlèvement de matière : Procédés de formage par déformation plastique 1. Formage : Le formage par déformation plastique utilise des métaux malléables, comme l’acier, le cuivre, l’aluminium et le zinc, qui supportent de grandes déformations à froid ou à chaud sans se rompre. Figure 50 décrit les divers types de procédés de formage par déformation plastique. Figure 50 types de procédés de formage par déformation plastique 2. Matriçage: Le matriçage est un forgeage réalisé avec des matrices (supérieure et inférieure) qui donnent la forme de la pièce (Figure 51). Il consiste à déformer plastiquement, après chauffage, des lopins en alliages non ferreux comme l’aluminium, le cuivre, le titane ou le nickel. L'excédent de métal forme une bavure, découpée ensuite lors du dérasage. Figure 51 Matriçage CHTOUROU S ENIT 41/60 Cours : Procédés de production mécanique 2AGI 3. Estampage: L’estampage est un forgeage en trois étapes (ébauche, finition, ébavurage) utilisant de l’acier (Figure 52). Ce procédé génère des pertes par bavure : le métal, soumis à une contrainte entre les matrices, s'écoule latéralement. L'écoulement est freiné à la sortie, créant une bavure. Figure 52 Estampage: 4. Laminage: Le laminage est une déformation plastique qui réduit la section d’un produit long en le faisant passer entre deux ou plusieurs rouleaux tournants (Figure 53). La rotation des rouleaux entraîne le produit par frottement. Figure 53 Laminage 5. Extrusion: Le filage (ou extrusion) est un procédé de transformation à chaud des métaux (Figure 54). Il consiste à forcer un bloc de métal chauffé à travers un orifice plus petit que l’entrée, sous pression élevée. L’utilisation d’un lubrifiant et d’une chauffe homogène prévient les défauts en évitant des contraintes trop fortes sur le métal. CHTOUROU S ENIT 42/60 Cours : Procédés de production mécanique 2AGI Figure 54 Extrusion 6. Emboutissage: L’emboutissage est un procédé de formage qui transforme des tôles minces non développables en pièces complexes. La tôle est entraînée sous l'action d’un poinçon dans la matrice pour obtenir la forme désirée (Figure 55). Figure 55 Emboutissage 7. Pliage: Le pliage (ou cambrage) est une opération de déformation permanente de tôles effectuée à froid. Elle consiste à donner la forme désirée en dépassant la limite élastique du matériau pour assurer une déformation plastique permanente (Figure 56). Lors du pliage, la tôle subit une déformation plastique. Les fibres internes sont comprimées, tandis que les fibres externes s’étirent. L’angle formé après pliage est appelé « angle de pliage ». Figure 56 Pliage CHTOUROU S ENIT 43/60 Cours : Procédés de production mécanique 2AGI 8. Découpage: Le découpage-poinçonnage est le procédé le plus rapide et économique pour obtenir un profil dans les métaux en feuille, adapté aux grandes, moyennes et petites séries (Figure 57). Figure 57 Découpage 9. Cintrage: La matière d'œuvre (produit plat ou profilé) subit des flexions successives, provoquant une incurvation. Généralement bi-appuyée sur deux cylindres, elle est sollicitée en flexion par un troisième cylindre. La rotation des cylindres déplace la pièce de manière tangentielle, assurant le formage continu (Figure 58). Figure 58 Cintrage CHTOUROU S ENIT 44/60 Cours : Procédés de production mécanique 2AGI Partie 3: Procédés sans enlèvement de matière : Autres Procédés 1. Impression 3D : 1.1. Définition : L'impression 3D est un procédé de fabrication additive où un objet est créé en ajoutant de la matière couche par couche à partir d'un modèle numérique (Figure 59). Figure 59 Impression 3D 1.2. Historique : 1981 : Première idée d'impression 3D par Hideo Kodama. 1986 : Apparition du brevet SLA par Charles Hull. 2000s : Popularisation avec l'arrivée de machines accessibles. 1.3. Technologies principales: FDM (Fused Deposition Modeling) Fonctionnement : Dépôt de fil fondu à travers une buse chauffée. Applications : Prototypage, éducation. Exemple : Pièces pour drones. SLA (Stereolithography) Fonctionnement : Solidification d’une résine liquide avec un laser UV. Applications : Prothèses dentaires, joaillerie. Exemple : Modèles dentaires précis SLS (Selective Laser Sintering) Fonctionnement : Fusion de particules de poudre polymère/métal avec un laser. Applications : Pièces fonctionnelles dans l’aéronautique. Exemple : Boîtiers en nylon pour l’électronique 1.4. Principe de fonctionnement L’impression 3D est basée sur les étapes suivantes (Figure 60): CHTOUROU S ENIT 45/60 Cours : Procédés de production mécanique 2AGI Modélisation CAO : Logiciels comme SolidWorks, Fusion 360, ou Blender. Tranchage (Slicing) : Préparation des fichiers pour l'impression via des logiciels comme Cura ou PrusaSlicer. Fabrication couche par couche : Dépôt ou fusion contrôlée par ordinateur. Figure 60 Etapes de l’impression 3D 2. Soudage : 2.1 Définition : Le soudage est un procédé permettant d’assembler de façon permanente deux ou plusieurs éléments métalliques. Il trouve des applications dans divers domaines comme les charpentes métalliques, la chaudronnerie, la construction mécanique et les ponts (figure 61). Soudure : Assemblage caractérisé par la fusion des bords à assembler, effaçant leurs contours primitifs. Elle peut être réalisée avec ou sans pression extérieure. Brasure : Le joint est constitué uniquement par le métal d’apport. Les métaux de base des pièces à assembler sont chauffés sans atteindre leur point de fusion, conservant ainsi leurs contours primitifs. Soudo-brasure : Brasage particulier où le métal d’apport fond progressivement au fur et à mesure du déplacement de la source de chaleur sur le joint. CHTOUROU S ENIT 46/60 Cours : Procédés de production mécanique 2AGI Métal de base : Matériau constituant les pièces à assembler. Les pièces peuvent être de même nature ou de natures différentes. Métal d’apport : Matériau utilisé pour former le joint. Il peut être identique ou différent du métal de base et intervenir partiellement ou totalement dans l’assemblage. Métal de joint : Constitué du métal déposé et des bords fondus dilués. Une zone thermiquement affectée (ZAT) autour du joint peut subir des modifications structurales. Soudure autogène : Assemblage homogène, réalisé sans métal d’apport ou avec un métal d’apport de même nature que le métal de base. Soudure hétérogène : Assemblage réalisé avec un métal d’apport de nature chimique différente de celle du métal de base. Figure 61 Soudage 2.2. Types de soudure : Soudage électrique à l'électrode enrobée : Le soudage à l'arc avec électrode enrobée repose sur un arc électrique entre l'âme métallique de l'électrode et la pièce à souder. L'arc fond simultanément les pièces, l'âme de l'électrode et son enrobage, formant un bain de fusion. La source de courant est un générateur électrique en courant continu ou alternatif, avec une intensité de 30 à 400 A, selon le diamètre de l'électrode, l'enrobage, la position de soudage et les caractéristiques des pièces. L’'électrode est composée d’un âme métallique (Cylindre central conduisant le courant et apportant le métal de soudure) et un enrobage (Enveloppe extérieure protégeant le bain de fusion contre l'oxydation en générant une atmosphère gazeuse et déposant un laitier protecteur sur le cordon de soudure). Le laitier prévient l'oxydation et assure un refroidissement contrôlé tout en stabilisant l'arc (figure 62). CHTOUROU S ENIT 47/60 Cours : Procédés de production mécanique 2AGI Figure 62 Soudage électrique à l'électrode enrobée Procédé T.I.G (Tungstène Inert Gas) Le soudage T.I.G utilise un arc électrique entre une électrode infusible en tungstène et la pièce à souder (figure 63). Métal d'apport : Introduit manuellement (baguette de fil) ou automatiquement à l’aide d’un dévidoir motorisé. Protection : Le bain de fusion est isolé de l'atmosphère par un gaz inerte (argon, ou argon mélangé à hélium ou hydrogène pour les procédés automatiques). Procédé M.I.G (Metal Inert Gas) Le procédé M.I.G utilise un arc électrique entre un fil-électrode, qui fournit le métal d’apport, et la pièce à souder (figure 63). Protection : Le bain de fusion est protégé par un gaz inerte (argon ou hélium), similaire au procédé T.I.G. Fil-électrode : Déroulé à vitesse constante pour maintenir une longueur d'arc stable. Il est relié au pôle positif, ce qui provoque un échauffement élevé, favorisant sa fusion et l’autorégulation de l’arc. Procédé M.A.G (Metal Active Gas) Le procédé M.A.G est un soudage à l'arc sous une atmosphère de gaz actif, principalement du dioxyde de carbone (CO₂) (figure 63). CHTOUROU S ENIT 48/60 Cours : Procédés de production mécanique 2AGI Gaz de protection : Remplace l'argon ou l'hélium par du CO₂ pur, un mélange CO₂- argon, ou un gaz récent composé d'argon, d'oxygène et de CO₂. Ce dernier améliore la soudure des aciers au carbone et faiblement alliés, réduit les fumées et les projections. Fil d’apport : Contient du manganèse et du silicium, parfois enrichi en aluminium, titane ou zirconium, pour contrer l’effet oxydant du CO₂ et stabiliser la fusion. Figure 63 Soudage TIG, MIG et MAG Soudage mécanique par friction La rotation crée la friction nécessaire au soudage (figure 64). Principe : o Une pièce, serrée dans un mandrin rotatif, tourne grâce à un moteur. o Cette pièce doit présenter une symétrie de révolution au niveau de la zone de soudage. Processus : o La friction entre les faces en contact génère de la chaleur. o Cette chaleur, par diffusion, élève la température des extrémités des pièces. o Lorsque la température de soudage est atteinte, la rotation s’arrête. o Un effort de forgeage est appliqué pour former la soudure. Figure 64 Soudage mécanique par friction CHTOUROU S ENIT 49/60 Cours : Procédés de production mécanique 2AGI Soudage électrique par résistance Ce procédé utilise la chaleur générée par l’effet Joule lors du passage d’un courant électrique de forte intensité à travers les pièces à souder (figure 65). Soudage par points : Les pièces sont superposées et serrées localement entre deux électrodes en alliage de cuivre. Le courant traverse l’ensemble et génère une fusion localisée au point de contact des électrodes. Soudage à la molette : Les molettes tournantes remplacent les électrodes fixes. Ce procédé permet une soudure continue et étanche grâce au passage continu du courant. Figure 65 Soudage électrique par résistance CHTOUROU S ENIT 50/60 Cours : Procédés de production mécanique 2AGI Contrôle et métrologie CHTOUROU S ENIT 51/60 Cours : Procédés de production mécanique 2AGI Contrôle et métrologie 1. Introduction : La métrologie est l'ensemble des opérations et des techniques permettant de contrôler la qualité d'un produit, c'est-à-dire de vérifier et d'assurer la conformité d'un produit aux spécifications du cahier des charges. La métrologie est la base de la qualité. 2. Caractéristiques d’un instrument de mesure : L’instrument de mesure permet d’établir une relation entre la grandeur à mesurer ‘Mesurande M’et la valeur lue ‘L’ avec une certaine incertitude. Sa qualité est caractérisée par l’étendu de mesurage, la fidélité, la justesse, la précision et la résolution. 2.1.Etendue de mesurage : est définie comme le domaine de variation possible de la grandeur à mesurer ou capacité. 2.2.Fidélité : C’est la capacité d’un instrument de mesure à indiquer la même dimension. Le défaut de fidélité est calculé comme suit ; V V n 2 i moy i 1 n 1 Avec, Vi : valeur de i ème mesure n V i Vmoy :valeur moyen Vmoy i 1 n n: nombre de mesure 2.3.Justesse : C’est l’exactitude de la valeur indiquée (de la graduation de l’instrument de mesure). L’erreur de justesse Ej est calculé comme suit ; E j Vmoy Vex Avec, Vex : valeur théorique exacte. 2.4.Précision : Un appareil de mesure est dit précis s’il est fidèle et juste. CHTOUROU S ENIT 52/60 Cours : Procédés de production mécanique 2AGI 2.5.Résolution : Elle est définie comme la petite variation perceptible de la grandeur à mesure. 3. Classification des instruments de mesure : Deux approches principales sont utilisées pour le mesurage dimensionnel : la mesure directe et la mesure indirecte (figure 67). Le choix de l’instrument de mesure adéquat dépond des critères bien défini tels que : Les caractéristiques de l’instrument de mesure: capacité, classe de précision, fidélité, justesse… Mode opératoire. Matériau de la pièce à mesurer (Acier, Plastique …). Figure 66 Classification des instruments de mesure 3.1.Instruments de mesure directe : Dans cette méthode de mesure, la valeur de la grandeur recherchée est directement obtenue en lisant l'affichage des instruments de mesure utilisés. Ces instruments comprennent le pied à coulisse, la jauge de profondeur, le micromètre (palmer)…, comme l’indique le tableau suivant. CHTOUROU S ENIT 53/60 Cours : Procédés de production mécanique 2AGI Vérificateur à dimensions variables Instruments de mesure directe CHTOUROU S ENIT 54/60 Cours : Procédés de production mécanique 2AGI Rapporteur d’angles a)Pied à coulisse : Cet instrument permet de mesurer diverses dimensions telles que les dimensions extérieures, intérieures et la profondeur, en fonction de la longueur et de la forme de ses becs (figure 68). Il se compose principalement d'une règle fixe sur laquelle se déplace un curseur équipé d'un vernier (figure 69). Pour mesurer les dimensions extérieurs d’une pièce, on utilise les becs extérieurs de pied à coulisse. Pour mesurer les dimensions intérieures ou un diamètre internes, on utilise les becs intérieurs. CHTOUROU S ENIT 55/60 Cours : Procédés de production mécanique 2AGI Pour mesurer la profondeur ou la hauteur d’une pièce, on utilise la jauge de profondeur. Figure 67 Méthode de mesure avec un pied à coulisse Figure 68 Composant d’un pied à coulisse Méthode de mesure : Lorsque le zéro du vernier coïncide précisément avec un trait de l'échelle de la règle graduée, la mesure est donnée par le nombre de millimètres comptés à gauche du zéro du vernier. Cependant, si le zéro du vernier se situe entre deux traits de l'échelle de la règle graduée, la mesure est obtenue en additionnant le nombre de millimètres comptés à gauche du zéro du vernier avec la fraction de millimètre indiquée par le trait du vernier correspondant à un trait de la règle graduée. Il est caractérisé par sa capacité maximale et son type de vernier. Il existe trois types de verniers selon le nombre n des divisions : Vernier au 1/10eme : il possède 10 graduations égales et mesure 9 mm. Une graduation égale 0,9 mm. La résolution relative est 0,1 mm (figure 70a). Vernier au 1/20eme : il possède 20 graduations égales et mesure 19 mm. Une graduation égale 0,95 mm. La résolution relative est 0,05 mm (figure 70b). Vernier au 1/50eme : il possède 50 graduations égales et mesure 49 mm. Une graduation égale 0,98 mm. La résolution relative est 0,02 mm (figure 70c). CHTOUROU S ENIT 56/60 Cours : Procédés de production mécanique 2AGI a) Vernier au 1/10eme b) Vernier au 1/20eme c) Vernier au 1/50eme Figure 69 Types de pied à coulisse. b) Micromètre ou palmer : Cet instrument permet de mesurer les longueurs et il est largement employé en mécanique pour évaluer les épaisseurs, les diamètres de surfaces cylindriques (micromètre d'extérieur) ainsi que les diamètres de perçage ou d'alésage (micromètre d'intérieur), comme l’indique la figure 71. Un exemple de mesure est présenté dans la figure 72. Micromètre extérieur: Il est utilisé pour mesurer des dimensions extérieure. Micromètre intérieur: Il est utilisé pour mesurer des dimensions intérieures. CHTOUROU S ENIT 57/60 Cours : Procédés de production mécanique 2AGI Micromètre de profondeur: Il est utilisé pour mesurer des profondeurs. Micromètre à lames: Il est utilisé pour mesurer des épaisseurs de feuilles ou de films. Figure 70 Types du micromètre Figure 71 Composants du micromètre et sa méthode de mesure 3.2.Instruments de mesure indirecte : a) Mesure par comparaison : Pour évaluer la différence entre les dimensions d'une pièce et celles d'un étalon proche, des écarts très minimes sont mesurés. Une lecture précise de ces écarts est rendue possible grâce à l'utilisation d'un dispositif d'amplification (un comparateur) en raison de leur faible magnitude. CHTOUROU S ENIT 58/60 Cours : Procédés de production mécanique 2AGI Comparateur à cadran : Comparateur s’appelle aussi un amplificateur (figure 73). En effet, l’amplification des déplacements du palpeur, qui est solidaire d’une crémaillère, est obtenue par des engrenages. Instruments de mesure indirect Capteur de l’écart Figure 72 Comparateur b) Mesure par calibrage : Les vérificateurs de tolérances sont utilisés afin de garantir que les dimensions des pièces réalisées se situent effectivement à l'intérieur des plages de tolérance spécifiées dans les plans. Dans le processus de vérification, différents outils sont utilisés selon les types de dimensions à contrôler (figure 74) : Pour les alésages, on utilise des outils tels que les tampons doubles et les jauges plates (à double face ou à une seule face). Pour les arbres, on recourt à des calibres à mâchoires (double dissymétrique, à une seule face, dissymétrique rigide, en deux pièces), des bagues lisses ou des lunettes. Les filetages sont vérifiés à l'aide de peignes de filetage extérieur et de calibres à filetage intérieur. Les rayons sont mesurés avec des jauges dédiées. Pour évaluer les jeux entre deux pièces, on utilise des jauges d'épaisseur de précision. CHTOUROU S ENIT 59/60 Cours : Procédés de production mécanique 2AGI Vérificateur à dimension fixe Pour Alésages: Pour Arbres: Pour filetages : Pour Angles : Pour Longueurs : Figure 73 Exemples des vérificateurs à dimension fixe CHTOUROU S ENIT 60/60