Chapter 5 - Clay and Clay Products PDF
Document Details
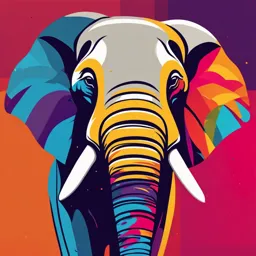
Uploaded by BlissfulCosecant
Adama Science and Technology University
2024
Zerihun M.
Tags
Summary
These lecture notes from Adama Science and Technology University cover the chapter on clay and clay products. The document details the manufacturing process, different types of clays and bricks, and raw materials used.
Full Transcript
ADAMA SCIENCE AND TECHNOLOGY UNIVERSITY SCHOOL OF CIVIL ENGINEERING AND ARCHITECTURE Course name: Construction Materials Course Code: CEng- 2205 Course Instructor: Zerihun M. Lecture Note for 2nd year students...
ADAMA SCIENCE AND TECHNOLOGY UNIVERSITY SCHOOL OF CIVIL ENGINEERING AND ARCHITECTURE Course name: Construction Materials Course Code: CEng- 2205 Course Instructor: Zerihun M. Lecture Note for 2nd year students Chapter 5: Clay and Clay Products Year- 2024 GC. Adama, Ethiopia Compiled by Zerihun M. [Lecture Notes on Clay & Clay Products] Chapter 5: Clay and Clay Products Introduction Clay products used in construction and Buildings Civil engineering presents many products of building materials like bricks, flooring tiles, roofing tiles, timber etc. Here we are going to introduce certain aspects of clay and clay products used in the civil engineering field. Clays: - are finely grained soils resulted from decay of rocks. (They could be residual clays formed from the decay of the underlying rocks, or sedimentary if removed from the parent rock, transported and deposited somewhere else by water or wind. ▪ Chemical constituents of clay The formation of hydrate of alumina silicate (A12O3. 2SiO2.2H2O) is, in fact, one of the commonest minerals in clay. - Silica (SiO2) - Ferric Oxide (Fe2O3) - Lime (CaO) - Magnesia (MgO) - Carbon dioxide (CO2) - Alkalies, water, etc. On account of the different phases they might have gone through and their history of formation, clays are generally found mixed with other materials (impurities) which influence their properties. Compiled by Zerihun M. [Lecture Notes on Clay & Clay Products] 1 Manufacturing process of clay products The manufacturing process of clay involves several steps, depending on the type of clay being produced. Here is a generalized overview of the process: 1. Mining - The first step in manufacturing clay is mining the clay minerals from the earth's crust. This can be done through open-pit mining or by using heavy machinery to remove the clay from underground mines. 2. Processing - Once the clay has been mined, it is processed to remove any impurities or contaminants. This may involve washing the clay with water or treating it with chemicals. 3. Blending - Next, different types of clay are blended together to achieve the desired properties and characteristics. The different types of clay may include kaolin, ball clay, fire clay, and bentonite, among others. 4. Forming - After blending, the clay is formed into various shapes and sizes. This can be done through a variety of methods, such as extrusion, rolling, or pressing. 5. Drying - Once the clay is formed, it is dried to remove any remaining moisture. This can be done through air-drying or by using a kiln. 6. Firing - The final step is firing the clay. This involves exposing it to high temperatures in a kiln, which causes the clay particles to fuse together and become hard and durable. Types of Clay Products Bricks Bricks are artificial stones that are usually made of clay. These are used in buildings construction and for ornamental purposes. These are one of the basic materials used for good construction. These are easily available, cheap and light-weighted. They can be moulded into the required shape and size. The property manufactured bricks are nearly as strong as stone. Different types of bricks can be used in construction from different materials, such as mud bricks, refractory bricks, silica bricks, cement, and bricks, fire bricks. Compiled by Zerihun M. [Lecture Notes on Clay & Clay Products] 2 Raw materials Bricks are manufactured from clays generally found in abundance in many parts of the world. Clays are fine-grained soils that have resulted from the decay of rocks (they could be residual clays formed from the decay of the underlying rocks or sedimentary if removed from the parent rock, transported and deposited somewhere else by water or wind). They generally consist of the following chemical elements: Alumina (Al2O3) Silica (SiO2) Ferric Oxide (Fe2O3) Lime (CaO) Magnesia (MgO) Carbon Dioxide (CO2) Sulphur trioxide (SO3) Alkalies (K2O, Na2O) Water (H2O) On account of the different phases they might have gone through and their history of formation, clays are generally found mixed with other materials (impurities) that influence their properties. A clay soil for brick making should be such that when prepared with water, it can be moulded, dried and burnt without cracking or changing its shape or warping. Such material should preferably have the following composition: Clay 20-40% Sand 30-50% Others (lime, silt, loam etc.)------------20-35% Each of the components and their constituents play different roles in the manufacture of bricks and influence the characteristics of the final product. Functions of the constituent materials Each of the constituents of the raw material used for making bricks has a function that can be summarized as follows: Compiled by Zerihun M. [Lecture Notes on Clay & Clay Products] 3 Alumina: A fine-grained mineral that makes the major part of clay,becomes plastic when mixed with water and is capable of being moulded to the desired shape. On drying it loses its plasticity and becomes hard. This can be accompanied with shrinkage that might result in warping and cracking depending on the speed and magnitude of drying. When burnt, alumina becomes stronger and harder as a result of the homogeneity created by fusion. Bricks of very high alumina content are likely to be refractory. Silica: A coarse-grained mineral, which can be present either inform of pure sand or compound of silicate of alumina. It is useful in reducing shrinkage and warping in burning. Its presence in bricks produces hardness and durability; however, a large percentage of uncombined silica is undesirable because it leads to brittleness of the product. Silica fuses only at very high temperature and hence increases the refractoriness of low alumina clay and makes bricks resistant to heat.In firebricks the silica content may rise to 98%. Lime: When present in small quantities, lime acts as a flux and lower the fusion point of silica. Lime in carbonate form breaks into CO2 and CaO at around 900oC. It also acts as a binder to the clay and silica particles leading to greater strength. Excess of lime may cause the bricks to melt and lose their shape. Iron oxide: It lowers the fusion point of the clay and silica and hence, helps the fusion of brick particles. It is this element that imparts the color of the clay and the burnt product. Depending on the percentage of iron oxide present in the clay, the color of the bricks may vary from light yellow to red. A high percentage may make the bricks dark blue. If iron is present in the form of pyrites (sulphide of iron), it can get oxidized, crystallized and split the bricks to pieces. Manufacture of Brick There are four basic stages in brick manufacture, though many of the operations are interdependent. A particular brick will pass through these stages in away designed specifically to suit the raw material used and the final product. Compiled by Zerihun M. [Lecture Notes on Clay & Clay Products] 4 Clay preparation After digging out (winning), the clay is prepared by crushing and/or grinding and mixing until it is of a uniform consistency. Water may be added to increase plasticity (a process known as ‘tempering’) and in some cases chemicals may be added for specific purposes, for example, barium carbonate that reacts with soluble salt producing an insoluble product, therefore reducing effloresence in the final product. At this stage sand and water are added to produce the desired consistency for molding. Molding The molding technique is designed to suit the moisture content of the clay. The soft-mud process: This method utilizes a clay, normally from shallow surface deposits, in a very soft condition, the moisture content being as high as 30%. Consists of mechanically forcing wet, soft clay (moisture content 30%) into molds. The molding machine forces the wet clay into several molds under pressure, cuts of excess clay, and turns the molded bricks out onto a pallet or conveyor, to be carried away for drying. The inside of the moldmay be sprayed or dipped in water to prevent the clay from sticking. These bricks are called water-struck bricks. Sand-struck bricks generally have sharper, cleaner edges than water struck bricks. The green bricks are very soft and must be handled carefully prior to drying. A similar process produces hand-made bricks. The stiff-mud process- here enough water is used to form the clay into a cohesive mass, which is then forced or extruded in a column through dies in a brick-making machine. The column of clay is forced into a wire-cutting table, where it is cut into appropriate length by taut wires. This produces a wire-cut face. Brick may be end cut or side cut, depending on the size and shape of the die. Dry-pressed brick is manufactured of relatively dry or non-plastic clays. The material is fed into the machine by hoppers, where it is compressed into molds under high pressure. Dry pressed bricksare compact, strong, and well formed. Drying When the bricks come to the brick-making machine, they contain from 7 to 30% moisture, depending on the process used. They may be stacked in open sheds for periods of 7 days to 6 weeks for final drying. Most brick is now dried in chambers under controlled conditions of heat, moisture and air velocity for 2 to 4 days. Drying enables the bricks to be stacked higher in the kiln Compiled by Zerihun M. [Lecture Notes on Clay & Clay Products] 5 without lower bricks becoming distorted by the weight of bricks above them. Drying is also enables the firing temperature to be increased more rapidly without problems such as bloating, which may result when gases or vapor are trapped within the brick. Firing The object of firing is to cause localized melting (sintering) of the clay, which increases strength and decrease the soluble salt content without loss of shape of the clay unit. The main constituents of the clay-silica and alumina-do not melt, since their melting point are very high; they are merely fused together by the lower melting point minerals such as metallic oxides and lime. The main stages of firing are: 100oC Evaporation of free water 400oC Burning of carbonaceous matter 700oC Dehydration 900oC Oxidation 900o – 1000oC Sintering of clay Fuels may assist the latter stages of firing whether present naturally in the clay or those added during processing. The control of the rate of increase of temperature and the maximum temperature is most importantin order to produce bricks having satisfactory strength and quality; in particular, too-rapid firing will cause bloating and over burning of external layers, while too low a temperature seriously impairs strength and durability. Stronger bricks, such as engineering bricks, are normally fired at higher temperature. Firing of ordinary- quality bricks or common bricks is at 900oC and for that of engineering brick isgreater than 1000oC. Brick kilns Kiln may be either intermittent or continuous. In the intermittent kiln, the bricks must be fired, the fires extinguished, the bricks allowed to cool, the kiln dismantled, and the bricks removed before a new pile of green bricks is piled to be fired. The development of the continuous kiln greatly speeded up the process. The continuous kiln may consist of several compartments fired by a single oven. The heat is regulated in each section so that while the remaining water is being removed from the brick in one compartment, bricks are being fired in a second compartment and cooled in a third. The continuous kiln is now widely used. The kiln consists of either a straight or a curved Compiled by Zerihun M. [Lecture Notes on Clay & Clay Products] 6 tunnel, with several zones in which heat is carefully controlled. Bricks are loaded on to special cars and pulled through the preheating, firing, and cooling zones at a constant rate of speed. The tunnel kiln is very efficient and produces a more uniform product. Types of Bricks Common Bricks: -these are ordinary bricks that are not designed to provide good finish appearance or high strength. They are, therefore, in general, the cheapest bricks available. Facing Bricks: - these are designed to give attractive appearance; hence they are free from imperfections such as cracks. Facing bricks may be derived fromcommon bricks to which a sand facing and/or pigment has been applied prior to firing. Engineering Bricks: - these are designed primarily for strength and durability. They are usually of high density and well fired. Types of Bricks (According to ESC) Two types of clay bricks are manufactured in Ethiopia at present. These are the - Solid clay bricks - Hollow clay bricks and beam tiles Solid Clay bricks Ethiopian standard ESC. Dr. 026.1973 (1) specifies requirements for burnt solid clay bricks manufactured from suitable clay material and used in the building industry. According to the standard, the solid bricks are of the following three types. Brick without holes or depression (Type TS) Brick with holes up to 20mm in diameter each and having a total cross- sectional area not exceeding 25 percent of the base area of the brick (Type TH) Brick with depression not exceeding 25 percent of the base area and havinga maximum depth of depression not more than 10mm (Type TD). The nominal dimensions of solid bricks are 60 mm x 120 mm x 250 mm or 55 mm x 120 mm x 245 mm with dimensional tolerances of 2.5 mm, + 5 mm and +8.10 mm for the height, the width, and the length respectively. Hollow Clay bricks and beam tiles According to ESC. D4.026.1973 (2) burnt hollow clay bricks and beam tiles manufactured from Compiled by Zerihun M. [Lecture Notes on Clay & Clay Products] 7 suitable clay material and used in the building industry are of the following three types: a. With two faces keyed (combed or scared) for plastering or rendering (TypeKK) b. With two faces smooth and suitable for used without plastering orrendering on either side (Type SS) c. With one face smooth and another face keyed for plastering (Type SK). The nominal dimensions of the hollow clay bricks and hollow clay beam tiles are given in Table1. Table 1: Nominal dimensions of hollow clay bricks and hollow clay beam tiles Nominal Dimensions in millimeter (mm) Height (h) Width (w) Length (l) Hollow Clay Bricks 100 200 300 100 150 350 100 250 300 120 250 300 150 200 300 Hollow Clay Beam Tiles 140 250 250 140 400 250 160 250 250 160 400 250 Indentations & perforation in bricks They assist in forming strong bond between the brick & the remainder ofthe structure. They reduce effective thickness of the brick and hence reduce firing time. They reduce the material and hence the overall cost of the brick with outserious in – situ strength loss. Compiled by Zerihun M. [Lecture Notes on Clay & Clay Products] 8 Tests and classification of Bricks Two classes of Test are used to determine the quality of building bricks: field tests and laboratory test. Field Tests Field tests such as appearance, hammer test and hardness test can easily be made at the construction site. Appearance tests such as shape, planeness using vernier caliper, color, checks and blister form valuable indications of quality. When struck with a hammer, a properly burnt dry brick free from cracks emits a highly metallic ring. The hardness of a brick sample can be checked by scratching its surface or broken section with a nail. A well-burnt brick will be scratched with difficulty. Laboratory Tests. The Ethiopian Standard specifies a number of tests including visual inspection, checking of dimensions and planeness, compressive strength, water absorption, saturation coefficient and efflorescence tests on solid clay bricks. Infact, according to the standard, solid clay bricks are classified according to the numerical values of their compressive strength, water absorption, saturation coefficient and efflorescence as follows: Table 2. Minimum Compressive Strength Minimum Compressive Strength Class Average of 5 Bricks N/mm2 Individual Brick N/mm2 A 20 17.5 B 15 12.5 C 10 7.5 D 7.5 5.0 Compiled by Zerihun M. [Lecture Notes on Clay & Clay Products] 9 Table 3 Maximum Water Absorption After 24 hrs. Immersion After 5 hrs. Boiling Class Average of 5 Individual Average of 5 Individual bricks % brick % bricks % brick % A 21 23 22 24 B 22 24 23 24 C, D No limit No limit No limit No limit In the case of hollow clay bricks and beam tiles the minimum compressive strength and maximum allowable value for water absorption are given in Tables 4 and 5. Table 4. Minimum Compressive Strength Minimum Compressive Strength Individual Brick Type Average of 5 Bricks N/mm2 N/mm2 KK 7 5.5 SS 7 5.5 SK 7 5.5 Table 5. Maximum Water Absorption After 1 hr. Submersion in Boiling Water Type Average of 5 Bricks % Individual Brick % KK 21.5 23 SS 21.5 23 SK 21.5 23 Efflorescence This is the name given to the build-up of white surface deposits on drying out. It results from dissolved salts in the brick and quite commonly spoils the appearance of new brick Work, Compiled by Zerihun M. [Lecture Notes on Clay & Clay Products] 10 especially of exposed to weather, as in parapet, or to the prevailing wind. The effect is most noticeable after periods of wet weather. In the test for efflorescence, bricks are saturated with distilled water in order to dissolve any salts present and allowed to dry such that salts are carried to one exposed face. The apparatus is shown in the figure below. The efflorescence is assessed as follows. (BS) No perceptible deposit of efflorescence...............................Nil No more than 10% of area covered with Thin deposit of salts but unaccompanied By powering or flaking of the surface..................................Slight A heavier deposit than slight covering up to 50% of the area of the face but Unaccompanied by powdering or flaking of the face....................Moderate A heavy deposit of salts covering more Than 50% of the area of the face and/or Powdering or flaking of the surface......................................Heavy Expansion on wetting Fired clay products of many types undergo a progressive irreversible expansion as moisture penetrates pores and is absorbed on to internal surfaces. Over a period of years, this expansion may amount to over 1000x10-6, especially in more porous bricks, though the movement of the Compiled by Zerihun M. [Lecture Notes on Clay & Clay Products] 11 brickwork is normally only about 60% of this unless, for some reason, the mortar is expansive. Movement joints should be provided at least every 12m for clay brickwork and more frequently where openings, such as window, might act as crack initiators. Thermal Expansion The coefficient of thermal expansion of clay brickwork is approximately 7x10-6 per 0C, considerably less than that of most other building materials, so that thermal movement is not normally a problem. Tiles Tiles may be defined as thin slabs of bricks which are burnt in a kiln. They are thinner than bricks and hence they should be carefully handled to avoid damage to them. Tiles used in engineering constructions are divided into the following two classes. Common tiles Encaustic tiles Encaustic tiles: - They are used for decorative purposes on floors, walls, ceilings and roofs. Common tiles: - They are used for roofing, flooring, paving, drains, walls, etc. These tiles have different shapes and sizes. One of the most common tile is ceramic. Ceramics The word ceramic is derived from the greek term keramos, which means “potter’s clay” and keramikos means “clay products”. Till 1950s, the most important types of ceramics were the traditional clays, made into pottery, bricks, tiles etc. Ceramic artefacts play an important role in historical understanding of the technology and culture of the people who lived many years ago. A ceramic material is an inorganic, non-metallic material and is often crystalline. Traditional ceramics are basically clays. The earliest application was in pottery. Most recently, different types of ceramics used are alumina, silicon carbide etc. Latest advancements are in the bio-ceramics with examples being dental implants and synthetic bones. A comparative analysis of ceramics with other engineering materials is shown in table 1. The purpose of presenting this comparative analysis is to show importance of ceramics among different engineering metals and polymers. This comparison would enable to justify application areas of ceramics. Compiled by Zerihun M. [Lecture Notes on Clay & Clay Products] 12 Table 1 Comparison of ceramics with metals and polymers Property Ceramic Metal Polymer Density Low High Lowest Hardness Highest Low Lowest Ductility Low High High Wear resistance High Low Low Corrosion resistance High Low Low Thermal conductivity Mostly low High Low Electrical conductivity Mostly low High Low Applications Pottery products, sanitary ware, floor and roof tiles Crucibles, kiln linings, other refractories High end applications such as in ceramic matrix composites, tiles in space shuttle, bullet proof jackets, disk brakes, ball bearing applications, bio-ceramics Classification of ceramics materials Ceramics can be classified in diverse ways i.e. there are number of ways to classify the ceramic materials. Most commonly, the ceramics can be classified on the following basis: - Classification based on composition - Classification based on applications The detailed classification is shown in figure 1. Compiled by Zerihun M. [Lecture Notes on Clay & Clay Products] 13 Classification based on composition (i) Silicate ceramics Silicates are materials generally having composition of silicon and oxygen (figure 2a). Four large oxygen (O2) atoms surround each smaller silicon (Si) atom as shown in figure 2b. The main types of silicate ceramics are based either on alumosilicates or on magnesium silicates. Out of these two, the former include clay-based ceramics such as porcelain, earthenware, stoneware, bricks etc. while the latter consists of talc-based technical ceramics such as steatite, cordierite and forsterite ceramics. Silicate ceramics are traditionally categorized into coarse or fine and, according to water absorption, into dense (< 2 % for fine and < 6 % for coarse) or porous ceramics (> 2% and > 6 %,respectively). Compiled by Zerihun M. [Lecture Notes on Clay & Clay Products] 14 Figure 2 (a) Silicate ceramics Figure 2 (b) Structure of silicate ceramics (ii) Oxide ceramics Oxide ceramics include alumina, zirconia, silica, aluminium silicate, magnesia and other metal oxide based materials. These are non-metallic and inorganic compounds by nature that include oxygen, carbon, or nitrogen. Oxide ceramics possess the following properties: (a) High melting points (b) Low wear resistance (c) An extensive collection of electrical properties These types of ceramics are available with a variety of special features. For example, glazes and protective coatings seal porosity, improved water or chemical resistance, and enhanced joining to metals or other materials. Oxide ceramics are used in a wide range of applications, which include materials and chemical processing, radio frequency and microwave applications, electrical and high voltage power applications and foundry and metal processing. Aluminium oxide (Al2O3) is the most important technical oxide ceramic material. This synthetically manufactured material consists of aluminium oxide ranging from 80 % to more than 99 %. (figure 3a and 3b). Compiled by Zerihun M. [Lecture Notes on Clay & Clay Products] 15 Figure 3 (a) Aluminium oxide Figure 3 (b) Structure of aluminium oxide (iii) Non-Oxide ceramics The use of non-oxide ceramics has enabled extreme wear and corrosion problems to be overcome, even at high temperature and severe thermal shock conditions. These types of ceramics find its application in different spheres such as pharmaceuticals, oil and gas industry, valves, seals, rotating parts, wear plates, location pins for projection welding, cutting tool tips, abrasive powder blast nozzles, metal forming tooling etc. (iv) Glass ceramics These are basically polycrystalline material manufactured through the controlled crystallization of base glass. Glass-ceramic materials share many common characteristics with both glasses and ceramics. Glass-ceramics possess an amorphous phase and more than one crystalline phases. These are produced by a controlled crystallization procedure. Glass-ceramics holds the processing advantage of glass and has special characteristics of ceramics. Glass-ceramics yield an array of materials with interesting properties like zero porosity, fluorescence, high strength, toughness, low or even negative thermal expansion, opacity, pigmentation, high temperature stability, low dielectric constant, machinability, high chemical durability, biocompatibility, superconductivity, isolation capabilities and high resistivity. These properties can be altered by controlling composition and by controlled heat treatment of the base glass. Compiled by Zerihun M. [Lecture Notes on Clay & Clay Products] 16 Earthenware It means where are articles prepared from clay which is burnt at low temperatures and called down slowly. Glazed earthenware’s are not affected by acids or atmospheric agencies. Terra-cotta is a kind of earthenware. The earthenware is generally soft and porous. When glazed, earthenware becomes impervious to the water and they are not affected by acids or atmospheric agencies. The terra-cotta is a kind of earthenware. The earthenware is used for making ordinary drain pipes, electoral cable conduits, partition blocks etc. Stoneware It means the wares or articles prepared to form a mixture of refractory clay, stone and cursed pottery which are burnt at high temperature and then cooled down slowly. Stone wares are largely used for making sanitary articles such as basins, sewer pipes, glazed tiles, water closets, gully traps, etc. The stoneware is more compact and dense than earth ware. When glazed, the stoneware becomes impervious to the water and they are not affected by acids or atmospheric agencies. The sound stone wares have given a clear ringing sound when struck with each other. The stoneware is strong, impervious, durable and resistant to corrosive fluids and they resemble fire blocks. The stoneware can be kept clean easily. Types of clay products Porcelain The term porcelain is used to indicate fine earthenware which is white, thin and semi-transparent. Since the colour of porcelain is white, it is also referred to as whitewater. The clay of sufficient purity and possessing a high degree of tenacity and plasticity is used in preparing porcelains, it is hard, brittle and non-porous. It is prepared from clay, feldspar, quartz, and minerals, the constituents are finely ground and thenthey are thoroughly mixed in a liquid state. The mixture is given the desired shape and burnt at a high temperature. The various types of porcelains are available and they are adopted for multiple uses such as sanitary wares, electric insulators, stone vessels, reactor chambers, crucibles, etc. Summary chart Type of Firing Characteristics Ceramic Temperature Dense, durable, and non-porous. Often used for functional Stoneware 1200-1300°C pieces such as dishes and mugs. Compiled by Zerihun M. [Lecture Notes on Clay & Clay Products] 17 Porous and less durable than stoneware. Often used for Earthenware 800-1100°C decorative pieces and tableware. Translucent and delicate. Often used for decorative pieces Porcelain 1250-1450°C and fine tableware. Clay Blocks The blocks can be prepared from clay and they are used in the construction of portions, such blocks may either be solid or hollow. The blocks are usually of section 300 mm x 200 mm and the thickness of hollow blocks varies from 50 mm to 150 mm. The thickness, in the case of solid black, is about 40 mm. The blocks are provided with grooves on the top, bottom and sides. These grooves help make the joins rigid and serve as a key to the plaster. Sometimes the surface of blocks is made glazed in a variety of colours. It is found that the partition of clay blocks is efficient in preventing fire and the passage of sound. They are light in weight and are non- shrinkable. Compiled by Zerihun M. [Lecture Notes on Clay & Clay Products] 18