Chapter 11: Managing Economies of Scale in a Supply Chain PDF
Document Details
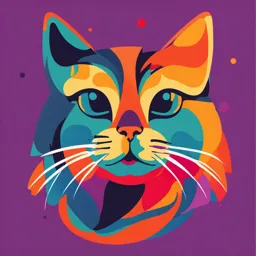
Uploaded by DeservingConnemara3538
Florida International University
Tags
Summary
This chapter delves into the role of cycle inventory in supply chains, emphasizing how large lot sizes impact costs. It covers topics such as fixed ordering costs, quantity discounts, and replenishment policies. The goal is to reduce cycle inventory without increasing cost, improving a firm's efficiency.
Full Transcript
Here is the converted text from the supplied images. # Chapter 11 ## Managing Economies of Scale in a Supply Chain Cycle Inventory ### Learning Objectives After reading this chapter, you will be able to: * **11.1** Describe the role of cycle inventory in a supply chain. * **11.2** Choose the...
Here is the converted text from the supplied images. # Chapter 11 ## Managing Economies of Scale in a Supply Chain Cycle Inventory ### Learning Objectives After reading this chapter, you will be able to: * **11.1** Describe the role of cycle inventory in a supply chain. * **11.2** Choose the optimal lot size given fixed ordering costs in a supply chain. * **11.3** Evaluate how aggregation is best implemented to reduce cycle inventory in a supply chain. * **11.4** Understand the impact of quantity discounts on lot size and cycle inventory. * **11.5** Devise appropriate discounting schemes for a supply chain. * **11.6**Understand the impact of trade promotions on lot size and cycle inventory. * **11.7** Develop replenishment policies to improve synchronization in multiechelon supply chains. * **11.8** Identify managerial levers that reduce lot size and cycle inventory in a supply chain without increasing cost. Cycle inventory exists because producing or purchasing in large lots allows a stage of the supply chain to exploit economies of scale and thus lower cost. The presence of fixed costs associated with ordering and transportation, quantity discounts in product pricing, and short-term discounts or promotions encourages different stages of a supply chain to exploit economies of scale and order in large lots. In this chapter, we study how each of these factors affects the lot size and cycle inventories within a supply chain. Our goal is to identify managerial levers that reduce cycle inventory in a supply chain without raising cost. ### 11.1 Describe the role of cycle inventory in a supply chain. ## The Role of Cycle Inventory in a Supply Chain A **lot or batch size** is the quantity that a stage of a supply chain either produces or purchases at a time. Consider, for example, a computer store that sells an average of four printers a day. The store manager, however, orders 80 printers from the manufacturer each time he places an order. The lot or batch size in this case is 80 printers. Given daily sales of four printers, it takes an average of 20 days before the store sells the entire lot and purchases a replenishment lot. The computer store holds an inventory of printers because the manager purchases a lot size larger than the store's daily sales. Cycle inventory is the average inventory in a supply chain due to either production or purchases in lot sizes that are larger than those demanded by the customer. The image included displays a graph with **Inventory** on the Y axis and **Time** on the X axis. Graph included shows Inventory Profile of Jeans at Jean-Mart. In the rest of this chapter, we use the following notation: * Q: Quantity in a lot or batch size * D: Demand per unit time Here, we ignore the impact of demand variability and assume that demand is stable. In Chapter 12, we introduce demand variability and its impact on safety inventory. Let us consider the cycle inventory of jeans at Jean-Mart, a department store. The demand for jeans is relatively stable at $D = 100$ pairs of jeans per day. The store manager at Jean-Mart currently purchases in lots of $Q = 1,000$ pairs. The inventory profile of jeans at Jean-Mart is a plot depicting the level of inventory over time, as shown in Figure 11-1. Because purchases are in lots of $Q = 1,000$ units, whereas demand is only $D = 100$ units per day, it takes 10 days for an entire lot to be sold. Over these 10 days, the inventory of jeans at Jean-Mart declines steadily from 1,000 units (when the lot arrives) to 0 (when the last pair is sold). This sequence of a lot arriving and demand depleting inventory until another lot arrives repeats itself every 10 days, as shown in the inventory profile in Figure 11-1. When demand is steady, cycle inventory and lot size are related as follows: For a lot size of 1,000 units, Jean-Mart carries a cycle inventory of $Q/2 = 500$ pairs of jeans. From Equation 11.1, we see that cycle inventory is proportional to the lot size. A supply chain in which stages produce or purchase in larger lots has more cycle inventory than a supply chain in which stages produce and purchase in smaller lots. For example, if a competing department store with the same demand purchases in lot sizes of 200 pairs of jeans, it will carry a cycle inventory of only 100 pairs of jeans. Lot sizes and cycle inventory also influence the flow time of material within the supply chain. Recall from Little's Law (**Equation 3.1**) that $Average \space flow \space time = \frac{average \space inventory}{average \space flow \space rate}$ For any supply chain, average flow rate equals demand. We thus have $Average \space flow \space time \space resulting \space from \space cycle \space inventory = \frac{cycle \space inventory}{demand} = \frac{Q}{2D}$ For lot sizes of 1,000 pairs of jeans and daily demand of 100 pairs of jeans, we obtain Average flow time resulting from cycle inventory = $\frac{Q}{2D} = \frac{1,000}{2 \times 100} = 5$ days Cycle inventory at the Jean-Mart store thus adds five days to the average amount of time that jeans spend in the supply chain. The larger the cycle inventory, the longer the lag time between when a product is produced and when it is sold. There are many benefits to being able to lower cycle inventory without increasing costs. A lower level of cycle inventory decreases a firm's vulnerability to demand changes in the marketplace. A lower cycle inventory also decreases a firm's working capital requirement. Toyota, for example, keeps a cycle inventory of only a few hours of production between the factory and most suppliers. As a result, Toyota is never left with unneeded parts, and its working capital requirements are less than those of its competitors. Toyota also allocates very little space in the factory to inventory. Zara and Seven-Eleven Japan are two companies that have built their strategy on the ability to replenish their stores in small lots. Seven-Eleven replenishes its stores in Japan with fresh food three times a day. The small replenishment batch allows Seven-Eleven to provide product that is always very fresh. Zara replenishes its European stores up to three times a week. Each replenishment batch thus contains only about two days of demand. This ensures that Zara's inventory on hand closely tracks customer demand. In both instances the firms have used small batch replenishment to ensure that their supply closely tracks customer demand trends. Before we suggest actions that a manager can take to reduce cycle inventory, it is important to understand why stages of a supply chain produce or purchase in large lots and how lot size reduction affects supply chain performance. Cycle inventory is held to take advantage of economies of scale and reduce cost within a supply chain. For example, apparel is shipped from Asia to North America in full container loads to reduce the transportation cost per unit. Similarly, an integrated steel mill produces hundreds of tons of steel per lot to spread that high cost of setup over a large batch. To understand how the supply chain achieves these economies of scale, we first identify supply chain costs that are influenced by lot size. The average price paid per unit purchased is a key cost in the lot-sizing decision. A buyer may increase the lot size if this action results in a reduction in the price paid per unit purchased. For example, if the jeans manufacturer charges $20 per pair for orders under 500 pairs of jeans and $18 per pair for larger orders, the store manager at Jean-Mart gets the lower price by ordering in lots of at least 500 pairs of jeans. The price paid per unit is referred to as the material cost and is denoted by $C$. It is measured in dollars per unit. In many practical situations, material cost displays economies of scale—increasing lot size decreases material cost. The fixed ordering cost includes all costs that do not vary with the size of the order but are incurred each time an order is placed. There may be a fixed administrative cost to place an order, a fixed trucking cost to transport the order, and a fixed labor cost to receive the order. Jean-Mart incurs a cost of $400 for the truck regardless of the number of pairs of jeans shipped. If the truck can hold up to 2,000 pairs of jeans, a lot size of 100 pairs results in a transportation cost of $4/pair, whereas a lot size of 1,000 pairs results in a transportation cost of $0.40/pair. Given the fixed transportation cost per batch, the store manager can reduce transportation cost per unit by increasing the lot size. The fixed ordering cost per lot or batch is denoted by $S$ (commonly thought of as a setup cost) and is measured in dollars per lot. The ordering cost also displays economies of scale—increasing the lot size decreases the fixed ordering cost per unit purchased. Holding cost is the cost of carrying one unit in inventory for a specified period of time, usually one year. It is a combination of the cost of capital, the cost of physically storing the inventory, and the cost that results from the product becoming obsolete. The holding cost is denoted by $H$ and is measured in dollars per unit per year. It may also be obtained as a fraction, $h$, of the unit cost of the product. Given a unit cost of $C$, the holding cost $H$ is given by The total holding cost increases with an increase in lot size and cycle inventory. To summarize, the following costs must be considered in any lot-sizing decision: * Average price per unit purchased, $C/unit * Fixed ordering cost incurred per lot, $S/lot * Holding cost incurred per unit per year, $H/unit/year = hC$ Later in the chapter, we discuss how the various costs may be estimated in practice. However, for the purposes of this discussion, we assume they are already known. The primary role of cycle inventory is to allow different stages in a supply chain to purchase product in lot sizes that minimize the sum of the material, ordering, and holding costs. If a manager considers the holding cost alone, he or she will reduce the lot size and cycle inventory. Economies of scale in purchasing and ordering, however, motivate a manager to increase the lot size and cycle inventory. A manager must make the trade-off that minimizes total cost when making lot-sizing decisions. As a result, any stage of the supply chain exploits economies of scale in its replenishment decisions in the following three typical situations: 1. A fixed cost is incurred each time an order is placed or produced. 2. The supplier offers price discounts based on the quantity purchased per lot. 3. The supplier offers short-term price discounts or holds trade promotions. In the following sections, we review how purchasing managers can best respond to these situations. Ideally, cycle inventory decisions should be made considering the total cost across the entire supply chain. In practice, however, it is generally the case that each stage makes its cycle inventory decisions independently. As we discuss later in the chapter, this practice increases the level of cycle inventory as well as the total cost in the supply chain. ##### Summary of Learning Objective 1 Cycle inventory builds up in a supply chain because product is produced or purchased in large lots to lower the sum of material, ordering, and holding costs by exploiting economies of scale. Opportunities to exploit economies of scale arise if a fixed cost is incurred each time an order is placed or produced, the supplier offers price discounts based on the quantity purchased per lot, or the supplier offers short-term price discounts. A reduction in cycle inventory improves a supply chain's ability to match supply with demand. #### Test Your Understanding *11.1.1 The quantity of inventory that a stage of the supply chain either produces or purchases at a given time is* *11.1.2 A graphical plot depicting the level of inventory over time is* ### 11.2 Choose the optimal lot size given fixed ordering costs in a supply chain. ## Economies of Scale to Exploit Fixed Costs To better understand the trade-offs discussed in this section, consider a situation that often arises in daily life-the purchase of groceries and other household products. These may be purchased at a nearby convenience store or at a Costco (a large warehouse club selling consumer goods), which is generally located much farther away. The fixed cost of going shopping is the time it takes to go to either location. This fixed cost is much lower for the nearby convenience store. Prices, however, are higher at the local convenience store. Taking the fixed cost into account, we tend to tailor our lot size decision accordingly. When we need only a small quantity, we go to the nearby convenience store because the benefit of a low fixed cost outweighs the cost of higher prices at the convenience store. When we are buying a large quantity, however, we go to Costco, where the lower prices over the larger quantity purchased more than make up for the higher fixed cost. In this section, we focus on the situation in which a fixed cost associated with placing, receiving, and transporting an order is incurred for each order. A purchasing manager wants to minimize the total cost of satisfying demand and must therefore make the appropriate cost trade-offs when making the lot-sizing decision. For this decision, we assume the following inputs: ### Estimating Cycle Inventory Related Costs in Practice When setting cycle inventory levels in practice, a common hurdle is estimating the fixed order cost and holding cost. Given the robustness of cycle inventory models, it is better to get a good approximation quickly rather than spend a lot of time trying to estimate costs exactly. In practice, we should identify incremental costs that change with the lot-sizing decision and ignore costs that are unchanged with a change in lot size. For example, if a factory is running at 50 percent of capacity and all labor is full time and not earning overtime, it can be argued that the incremental setup cost for labor is zero. Reducing the lot size in this case will not have any impact on setup cost until either labor is fully utilized (and earning overtime) or machines are fully utilized (with a resulting loss in production capacity). #### INVENTORY HOLDING COST Holding cost is estimated as a percentage of the cost of a product and is the sum of the following major components: *Cost of capital:* This is the dominant component of holding cost for products that do not become obsolete quickly. The appropriate approach is to evaluate the weighted-average cost of capital (WACC), which takes into account the required return on the firm's equity and the cost of its debt (see Brealey and Myers, 2000). These are weighted by the amount of equity and debt financing that the firm has. The formula for the WACC is $WACC = \frac{E}{D+E} (R_f + \beta \times MRP) + \frac{D}{D+E} R_b (1-t)$ where Most of these numbers can be found in a company's annual report and in any equity research report on the company. The borrowing rate comes from tables listing the rates charged for bonds from firms with the same credit ratings. The risk-free rate is the return on U.S. Treasury bonds, and the market risk premium is the return of the market above the risk-free rate. If access to a company's financial structure is not available, a good approximation can be made by using numbers from public companies in the same industry and of similar size. *Obsolescence (or spoilage) cost:* The obsolescence cost estimates the rate at which the value of the stored product drops because its market value or quality falls. This cost can range dramatically, from rates of many-thousand percent to virtually zero, depending on the type of product. Perishable products have high obsolescence rates. Even nonperishables can have high obsolescence rates if they have short life cycles. A product with a life cycle of six months has an effective obsolescence cost of 200 percent. At the other end of the spectrum are products such as crude oil that take a long time to spoil or become obsolete. For such products, a low obsolescence rate may be applied. *Handling cost:* Handling cost should include only incremental receiving and storage costs that vary with the quantity of product received. Quantity-independent handling costs that vary with the number of orders should be included in the order cost. The quantity-dependent handling cost often does not change if quantity varies within a range. If the quantity is within this range (e.g., the range of inventory a crew of four people can unload per period of time), incremental handling cost added to the holding cost is zero. If the quantity handled requires more people, an incremental handling cost is added to the holding cost. *Occupancy cost:* The occupancy cost reflects the incremental change in space cost due to changing cycle inventory. If the firm is being charged based on the actual number of units held in storage, we have the direct occupancy cost. Firms often lease or purchase a fixed amount of space. As long as a marginal change in cycle inventory does not change the space requirements, the incremental occupancy cost is zero. Occupancy costs often take the form of a step function, with a sudden increase in cost when capacity is fully utilized and new space must be acquired. *Miscellaneous costs:* The final component of holding cost deals with a number of other relatively small costs. These costs include theft, security, damage, tax, and additional insurance charges that are incurred. Once again, it is important to estimate the incremental change in these costs on changing cycle inventory. #### ORDERING COST The ordering cost includes all incremental costs associated with placing or receiving an extra order that are incurred regardless of the size of the order. Components of ordering cost include the following: * *Buyer time:* Buyer time is the incremental time of the buyer placing the extra order. This cost should be included only if the buyer is utilized fully. The incremental cost of getting an idle buyer to place an order is zero and does not add to the ordering cost. Electronic ordering can significantly reduce the buyer time to place an order. * *Transportation costs:* A fixed transportation cost is often incurred regardless of the size of the order. For instance, if a truck is sent to deliver every order, it costs the same amount to send a half-empty truck as it does a full truck. Less-than-truckload pricing also includes a fixed component that is independent of the quantity shipped and a variable component that increases with the quantity shipped. The fixed component should be included in the ordering cost. * Receiving costs: Some receiving costs are incurred regardless of the size of the order. These include any administration work such as purchase order matching and any effort associated with updating inventory records. Receiving costs that are quantity dependent should not be included here. * Other costs: Each situation can have costs unique to it that should be considered if they are incurred for each order regardless of the quantity of that order. The ordering cost is estimated as the sum of all its component costs. ### Optimal Lot Sizing for a Single Product (Economic Order Quantity) In this section we obtain the optimal lot size when a single product is purchased or produced to meet steady demand. Consider the purchasing manager at Best Buy who places a replenishment order for a new lot of Q Apple computers each time the store is running out of stock. Including the cost of transportation, Best Buy incurs a fixed cost of \$S per order. The purchasing manager must decide on the number of computers to order from Apple in a lot. Assume that Apple does not offer any discounts, and each unit costs \$C no matter how large an order is. The holding cost is thus given by $H = hC$ (using Equation 11.2). The model is developed using the following basic assumptions: 1. Demand is steady at D units per unit time. 2. No shortages are allowed—that is, all demand must be supplied from stock. 3. Replenishment lead time is fixed (initially assumed to be zero). The purchasing manager makes the lot-sizing decision to minimize the total cost for the store. He or she must consider three costs when deciding on the lot size: * Annual material cost * Annual ordering cost * Annual holding cost Because purchase price is independent of lot size, we have $Annual \space material \space cost = CD$ The number of orders must suffice to meet the annual demand D. Given a lot size of Q, we thus have Because an order cost of S is incurred for each order placed, we infer that Given a lot size of Q, we have an average inventory of $Q/2$. The annual holding cost is thus the cost of holding $Q/2$ units in inventory for one year and is given as $Annual\space holding \space cost = (\frac{Q}{2}) hC$ The total annual cost, $TC$, is the sum of all three costs and is given as $Total \space annual \space cost, \space TC = (\frac{D}{Q})S + (\frac{Q}{2}) hC + CD$ Figure 11-2 shows the variation in different costs as the lot size is changed. Observe that the annual holding cost increases with an increase in lot size. In contrast, the annual ordering cost declines with an increase in lot size. The material cost is independent of lot size because we have assumed the price to be fixed. The total annual cost thus first declines and then increases with an increase in lot size. From the perspective of the manager at Best Buy, the optimal lot size is one that minimizes the total cost to Best Buy. It is obtained by taking the first derivative of the total cost with respect to Q and setting it equal to 0 (see Appendix 11A at the end of this chapter). The optimal lot size is referred to as the economic order quantity (EOQ). It is denoted by $Q^*$ and is given by the following equation: For this formula, it is important to use the same time units for the holding cost rate h and the demand D. With each lot or batch of size $Q^*$, the cycle inventory in the system is given by $Q^*/2$. The flow time spent by each unit in the system is given by $Q^*/(2D)$. As the optimal lot size increases, so does the cycle inventory and the flow time. The optimal ordering frequency is given by $n^*$, where The image included displays a graph describing the lot size, holding cost, ordering costs and material costs. Graph has the cost running up the left side of the page as the Y axis and the lot size running along the bottom of the page as the X axis. In **Example 11-1** (see spreadsheet **Chapter11-examples1-6**, worksheet **Example 11-1**), we illustrate the EOQ formula and the procedure to make lot-sizing decisions. #### EXAMPLE 11-1 **Economic Order Quantity** Demand for the Deskpro computer at Best Buy is 1,000 units per month. Best Buy incurs a fixed order placement, transportation, and receiving cost of $4,000 each time an order is placed. Each computer costs Best Buy $500 and the retailer has an annual holding cost of 20 percent. Evaluate the number of computers that the store manager should order in each replenishment lot. ##### Analysis: In this case, the store manager has the following inputs: Annual demand, \*D = 1,000 × 12 = 12,000 units Order cost per lot, \$S = \$4,000 Unit cost per computer, \$C = \$500 Holding cost per year as a fraction of unit cost, h = 0.2 Using the EOQ formula (**Equation 11.5**), the optimal lot size is $Optimal\space order \space size \space= Q^* = \sqrt{\frac{2 \times 12,000 \times 4,000}{0.2 \times 500}} = 980$ To minimize the total cost at Best Buy, the store manager orders a lot size of 980 computers for each replenishment order. The cycle inventory is the average resulting inventory and (using Equation 11.1) is given by $Cycle \space inventory = \frac{Q^*}{2} = \frac{980}{2} =490$ For a lot size of **Q* = 980**, the store manager evaluates $Number \space of \space orders \space per \space year = \frac{D}{Q^*} = \frac{12,000}{980}= 12.24$ $Annual\space ordering\space and \space holding \space cost = \frac{D}{Q^*}S + (\frac{Q^*}{2})hC = \$97,980$ $Average \space flow \space time = \frac{Q^*}{2D} = \frac{980}{2 \times 12,000} = 0.041 \space year = 0.49 \space month$ Each computer thus spends 0.49 month, on average, at Best Buy before it is sold because it was purchased in a batch of 980. A few key insights can be gained from **Example 11-1** (see worksheet **Example 11-1**). Using a lot size of 1,100 (instead of 980) increases annual costs to $98,636 (from $97,980). Even though the order size is more than 10 percent larger than the optimal order size ***Q\***, total cost increases by only 0.67 percent. This issue can be relevant in practice. Best Buy may find that the economic order quantity for flash drives is 6.5 cases. The manufacturer may be reluctant to ship half a case and may want to charge extra for this service. Our discussion illustrates that Best Buy is perhaps better off with lot sizes of six or seven cases, because this change has a small impact on its inventory-related costs but can save on any fee that the manufacturer charges for shipping half a case. **Key Point** Total ordering and holding costs are relatively stable around the economic order quantity. A firm is often better served by ordering a convenient lot size close to the EOQ rather than the precise EOQ. If demand at Best Buy increases to 4,000 computers a month (demand has increased by a factor of 4), the EOQ formula shows that the optimal lot size doubles and the number of orders placed per year also doubles. In contrast, average flow time decreases by a factor of 2. In other words, as demand increases, cycle inventory measured in terms of days (or months) of demand should reduce if the lot-sizing decision is made optimally. This observation can be stated as the following **Key Point**: **Key Point** If demand increases by a factor of k, the optimal lot size increases by a factor of $\sqrt{k}$. The number of orders placed per year should also increase by a factor of $\sqrt{k}$. Flow time attributed to cycle inventory should decrease by a factor of $\sqrt{k}$. Let us return to the situation in which monthly demand for the Deskpro model is 1,000 computers. Now assume that the manager would like to reduce the lot size to $Q = 200$ units to reduce flow time. If this lot size is decreased without any other change, we have $Annual \space inventory-related \space costs = (\frac{D}{Q})S + (\frac{Q}{2}) hC = \$250,000$ This is significantly higher than the total cost of \$97,980 that Best Buy incurred when ordering in lots of 980 units, as in **Example 11-1**. Thus, there are clear financial reasons that the store manager would be unwilling to reduce the lot size to 200. To make it feasible to reduce the lot size, the manager should work to reduce the fixed order cost S. If the fixed cost associated with each lot is reduced to $1,000 (from the current value of $4,000), the optimal lot size reduces to 490 (from the current value of 980). We illustrate the relationship between desired lot size and order cost in **Example 11-2** (see worksheet **Example 11-2**). #### EXAMPLE 11-2 **Relationship Between Desired Lot Size and Ordering Cost** The store manager at Best Buy would like to reduce the optimal lot size d from 980 to 200. For this lot size reduction to be optimal, the store manager wants to evaluate how much the ordering cost per lot should be reduced. ##### Analysis: In this case, we have Desired lot size, $Q^* = 200$ Annual demand, $D = 1,000 × 12 = 12,000 units$ Unit cost per computer, $C = $500 Holding cost per year as a fraction of inventory value, $h = 0.2$ Using the EOQ formula (**Equation 11.5**), the desired order cost is $S = \frac{hC(Q^*)^2}{2D} = \frac{0.2 \times 500 \times 200^2}{2 \times 12,000} = \$166.7$ Thus, the store manager at Best Buy would have to reduce the order cost per lot from $4,000 to $166.7 for a lot size of 200 to be optimal. As we will discuss later, aggregating multiple products in a single order can often help reduce the fixed order cost S. The observation in **Example 11-2** may be stated as in the following **Key Point**: #### Key Point To reduce the optimal lot size by a factor of k, the fixed order cost *S* must be reduced by a factor of $k^2$ . ### Production Lot Sizing In the EOQ formula, we have implicitly assumed that the entire lot arrives at the same time. While this may be a reasonable assumption for a retailer receiving a replenishment lot, it is not reasonable in a production environment in which production occurs at a specified rate, say, P. In a production environment, inventory thus builds up at a rate of P – D when production is on, and inventory is depleted at a rate of D when production is off. With $D$, $h$, $C$, and $S$ as defined earlier, the EOQ formula can be modified to obtain the economic production quantity (EPQ) as follows: $Q^p = \sqrt{\frac{2DS}{(1 - D/P)hC}}$ The annual setup cost in this case is given by $(\frac{D}{Q^p})S$ The annual holding cost is given by: $(1 - D/P)(\frac{Q^p}{2})hC$ Observe that the economic production quantity is the EOQ multiplied by a correction factor that approaches 1 as the production rate becomes much faster than the demand. For the remainder of this chapter, we restrict our attention to the case in which the entire replenishment lot arrives at the same time, a scenario that applies in most supply chain settings. ### Lot Sizing with Capacity Constraint In our discussion so far we have assumed that the economic order quantity for a retailer will fit on the truck. In reality the truck has a limited capacity, say K. If the economic order quantity Q is less than K, the retailer should order Q units in each order. If the economic order quantity Q is more than the K, the retailer will have to pay for more than one truck. In this case, the optimal order quantity is obtained by comparing the annual cost of ordering K units per lot (a full truck for each lot) and Q units per lot (requiring [Q/K] trucks for each lot). If the setup cost S arises primarily from the cost of a truck, it is never optimal to order more than one truck. In this case, the optimal order size is the minimum of the EOQ and the truck capacity (K). __Summary of Learning Objective 2__ In deciding on the optimal lot size, the supply chain goal is to minimize the total cost-the order cost, holiding cost, and material cost. As lot size increases, so does the annual holding cost. However, the annual order cost and, in some instances, the annual material cost decrease with an increase in lot size. The EOQ balances the three costs to obtain the optimal lot size. The higher the order and transportation cost, the higher the lot size and cycle inventory. The optimal lot size can be decreased if the fixed cost associated with each lot is reduced. #### Test Your Understanding *11.2.1 Total ordering and holding costs* *11.2.2 Ordering costs would include which of the following?* ### 11.3 Evaluate how aggregation is best implemented to reduce cycle inventory in a supply chain. ## Aggregating Multiple Products in a Single Order As we have discussed earlier, a key to reducing lot size is the reduction of the fixed cost incurred per lot. One major source of fixed costs is transportation. In several companies, the array of products sold is divided into families or groups, with each group managed independently by a separate product manager. This results in separate orders and deliveries for each product family, thus increasing the overall cycle inventory. Aggregating orders and deliveries across product families lowers the fixed transportation cost per family and is an effective mechanism to lower cycle inventories. We illustrate the benefits of aggregating shipments using the following example. Consider the data from **Example 11-1**. Assume that Best Buy purchases four computer models, and the demand for each of the four models is 1,000 units per month. In this case, if each product manager orders separately, he or she would order a lot size of 980 units (as in **Example 11-1**) for each model. Across the four models, the total cycle inventory would thus be $4 \times 980/2 = 1,960$ units. Now consider the case in which a store manager at Best Buy realizes that all four model shipments originate from the same source. She asks the product managers to coordinate their purchasing to ensure that all four products arrive on the same truck. In this case, the optimal combined lot size across all four models turns out to be 1,960 units (use $S = $4,000, $D = 4 \times 12,000 = 48,000$, $hC = $500 \times 0.2 = $10 in Equation 11.5). This is equivalent to a lot size of 490 units for each model. As a result of aggregating orders and spreading the fixed transportation cost across multiple products originating from the same supplier, it becomes financially optimal for the store manager at Best Buy to reduce the lot size for each individual product from 980 to 490. This action significantly reduces the cycle inventory, as well as the cost to Best Buy. Other ways to achieve aggregation include having a single delivery coming from multiple suppliers (allowing fixed transportation cost to be spread across multiple suppliers) or having a single truck delivering to multiple retailers (allowing fixed transportation cost to be spread across multiple retailers). Firms that import product to the United States from Asia have worked hard to aggregate their shipments across suppliers (often by building hubs in Asia that all suppliers deliver to), allowing them to maintain transportation economies of scale while getting smaller and more frequent deliveries from each supplier. Walmart and other retailers, such as Seven-Eleven Japan, have facilitated aggregation across multiple supply and delivery points without storing intermediate inventories through the use of cross-docking. Each supplier sends full truckloads to the DC, containing an aggregate delivery destined for multiple retail stores. At the DC, each inbound truck is unloaded, product is cross-docked, and outbound trucks are loaded. Each outbound truck now contains product aggregated from several suppliers destined for one retail store. When considering fixed costs, one cannot ignore the receiving or loading costs. As more products are included in a single order, the product variety on a truck increases. The receiving warehouse now has to update inventory records for more items per truck. In addition, the task of putting inventory into storage now becomes more expensive because each distinct item must be stocked in a separate location. Thus, when attempting to reduce lot sizes, it is important to focus on reducing costs that increase with variety. Advance shipping notices (ASNs) are files that contain precise records of the contents of the truck that are sent electronically by the supplier to the customer. These electronic notices facilitate updating of inventory records as well as the decision regarding storage locations, helping reduce the fixed cost of receiving. RFID technology can also help reduce the fixed costs associated with receiving that are related to product variety. The reduced fixed cost of receiving makes it optimal to reduce the lot size ordered for each product, thus reducing cycle inventory. We next analyze how optimal lot sizes may be determined when there are fixed costs associated with each lot as well as the variety in the lot. #### Lot Sizing with Multiple Products or Customers In general, the ordering, transportation, and receiving costs of an order grow with the variety of products or pickup points. For example, it is cheaper for Walmart to receive a truck containing a single product than it is to receive a truck containing many different products, because the inventory update and restocking effort is less for a single product. A portion of the fixed cost of an order can be related to transportation (this depends only on the load and is independent of product variety on the truck). A portion of the fixed cost is related to loading and receiving (this cost increases with variety on the truck). We now