Fuel System - Chapter 10 PDF
Document Details
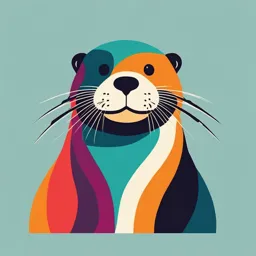
Uploaded by WiseCreativity
School of Mechanical and Aeronautical Engineering
Tags
Summary
This document is a chapter on fuel system and fuel system overview. It includes details on fuel facts, fuel system components, diagrams, electronic engine control, and fuel calculation. The document also describes the components of the fuel system along with their functionalities.
Full Transcript
Chapter 10: Fuel System Reference: The Jet Engine (Rolls Royce 1996) Introduction Fuel Facts Types of aviation fuel Qualities of Aviation Fuel Fuel System Function of Fuel System Fuel System Diagram Fuel System Components...
Chapter 10: Fuel System Reference: The Jet Engine (Rolls Royce 1996) Introduction Fuel Facts Types of aviation fuel Qualities of Aviation Fuel Fuel System Function of Fuel System Fuel System Diagram Fuel System Components Electronic Control System Chapter 14: Fuel System Electronic Engine Control FADEC - Full Authority Digital Engine Control EEC Redundancy Data Entry Plug Consumption of Fuel Calculation Fuel uplift for a flight Thrust specific fuel consumption TSFC 2 Fuel Facts 3 Civil Jet Fuels Aviation turbine fuels are used for powering jet and turbo- prop engine aircraft. There are currently two main grades of turbine fuel in use in civil commercial aviation : Jet A-1 and Jet A, both are kerosene type fuels. There is another grade of jet fuel, Jet B which is a wide cut kerosene (a blend of gasoline and kerosene) but it is rarely used except in very cold climates. e.g. Canada 4 JET A-1 & Jet A Fuel Jet A-1 is a kerosene grade of fuel suitable for most turbine engine aircraft. It is produced to a stringent internationally agreed standard, has a flash point above 38°C (100°F) and a freeze point maximum of -47°C. It is widely available outside the U.S.A. Jet A is a similar kerosene type of fuel, produced to an ASTM specification and normally only available in the U.S.A. It has the same flash point as Jet A-1 but a higher freeze point maximum (-40 c). 5 JET B Jet B is a distillate covering the naphtha and kerosene fractions. It can be used as an alternative to Jet A-1 but because it is more difficult to handle (higher flammability), there is only significant demand in very cold climates where its better cold weather performance is important. In Canada it is supplied against the Canadian Specification CAN/CGSB 3.23 6 Military Fuel JP-4 is the military equivalent of Jet B with the addition of corrosion inhibitor and anti-icing additives. JP-5 is a high flash point kerosene. JP-8 is the military equivalent of Jet A-1 with the addition of corrosion inhibitor and anti-icing additives 7 Precautions When Performing Mixed Refuelling 1. Mixture of jet A-1 and jet B is very explosive. 2. Safety distances are increased whenever there is mixed refuelling. 3. Three subsequent refuelling must take this extra precaution. 4. Refuelling instructions manual of the operator must be strictly followed 8 Qualities of Aviation Fuel 9 Fuel System Overview 10 Function of Fuel System Provide the engine with fuel for combustion Control the flow to the required quantity necessary for easy starting, acceleration and stable running, at all engine operating conditions. Torque motoring for control of air flow using Variable Stator Vanes and operating the Turbine Case Cooling system 11 2D View of The Generic Fuel System Diagram *T900 Training Notes 12 Generic Fuel System Block Diagram LP SOV LP Pump FOHE LP Filter HP Pump Fuel Metering (Servo Fuel) Unit Drain Drain VSV Drain V/V HP SOV Mast Collector HMU FF Transmitter Fuel Manifold Fuel Nozzles 13 Generic Fuel System 14 Fuel Components 15 Components Of The Fuel System 1. Fuel LP & HP Valve / LP & HP Cock 2. Fuel Pump 3. Fuel Filter (LP & HP) 4. Fuel Oil Heat Exchanger (FOHE/FCOC/Fuel Heater) 5. Fuel Control Unit / Hydromechanical Unit 6. Fuel Flow Transmitter 7. Flow Divider 8. Fuel Nozzles 9. Pressurizing and Dump Valve 16 1. Fuel LP & HP Valve (LP & HP Cock) LP Valve is located at the boundary of the aircraft fuel system and the engine fuel system and is used for isolation or interconnection between the two systems. The LP Valve is normally controlled by the Engine Fire Switch or by the Engine Master Switch. The HP Valve is used to stop the engine by cutting off the fuel supply to the Combustion Chamber from the fuel control units. Unlike the LP Valve which cuts off fuel supply from the aircraft fuel system to the engine fuel system, the HP Valve cuts off fuel supply from the HMU to the Fuel Nozzles. 17 1. LP Valve System 18 2. Fuel Pump The two-stage fuel pump has a boost stage and a main stage. The boost stage is a centrifugal pump. The main stage is a geartype positive displacement pump. It also supplies servo fuel (Pf) to the fuel bypass valve and to these interface engine components. 19 2. Fuel Pump Assembly *T900 Training Notes 20 3. Fuel Filter Upstream filter from the main fuel tank are called LP Filter because they are located in the LP circuit (subjected to low pressure) Downstream filter from the FCU are called HP Filter because they are located in the HP circuit (subjected to high pressure) The differential pressure switch/indicator is for monitoring/indication for filter clog condition The Bypass valve is to allow fuel to bypass the filter if it get clogged 21 3. Types Of Fuel Filters 22 3. Cleanable Wafer Screen Filter Assembly 23 4. Fuel Oil Heat Exchanger (FOHE/FCOC/Fuel Heater) Also known as fuel oil cooler, cools the oil adequately when fuel flow is high. Fuel gets heated by the oil at the heat exchanger. If the oil tank smells of fuel when servicing check, then possibly FOHE is leaking 24 4. Fuel oil heat exchanger *T900 Training Notes 25 5. Fuel Control Unit The primary function is to ‘compute’ the right amount of fuel and to meter this fuel to the nozzles accordingly Other functions such as fuel shutoff, overspeed protection and to supply servo fuel to various fuel pressure operated actuators 26 5. Inputs To The Fuel Control Unit Thrust lever position Inlet total pressure Inlet temperature Shaft rpm (N1, N2 and N3) Burner pressure or Compressor Discharge Pressure Exhaust Gas Temperature 27 5. Fuel Control Unit / Hydromechanical Unit Fuel outlet Pump and control units Fuel flow control Fuel inlet Anticipator Hydromechanical control unit *Turbomeca Training notes 28 6. Fuel Flow Transmitter It provides electrical signal for indication of the fuel flow in the cockpit on a gauge This parameter is useful during starting as an indication of the opened HP shutoff valve and to monitor excessive fuel flow to prevent a high EGT condition. 29 6. Fuel Flow Transmitter 30 7. Fuel Manifold & Fuel Spray Unit *T900 Training Notes 31 8. Flow Nozzles The function of the fuel nozzles is to inject fuel to the combustion chamber which aids the combustion process. There are 2 types of Nozzles namely: Simplex Type & Duplex Type For good burning process the following conditions are preferred: Fuel is evenly distributed Well centred within the combustion chamber to prevent hot spots and damaging the combustion liner 32 8. Simplex Nozzle 33 8. Duplex nozzle 34 8. Stray pattern of a duplex fuel nozzle 35 8. Duplex nozzle During engine running at low rpm only primary manifold is pressurized. During high engine rpm both primary and main (secondary) fuel manifold are pressurized. Duplex nozzle enables better atomizing at all rpm than simplex nozzle , hence wider usage in the industry. 36 9. Dump Valve The function of the Dump Valve is to remove the fuel inside fuel manifold downstream of the shutoff valve and fuel nozzles after engine shut down. This valve is normally opens when the Fuel Shutoff Valve closes. When open it will drain the fuel to a drain collector tank which stores this fuel and supplies it back to the fuel pump inlet by a jet pump during next engine start 37 9. Dump Valve 38 Electronic Engine Control System 39 Electronic Engine Control 40 Electronic Engine Control (EEC) The purpose of the EEC is to interface with aircraft and engine components through electrical, hydraulic and pneumatic subsystems. The EEC provides the following benefits to the engine. Benefit 1: Improves efficiency through control of these components and functions: – Compressor bleeds – Variable stator vanes – Cooling airflows – Engine oil cooling – IDG oil cooling – Fuel heating Benefit 2: Enhances these basic control functions: – Starting – Idle – Acceleration – Deceleration – Stability – Thrust control 41 Electronic Engine Control Benefit 3: Protects the engine by limiting: – Critical speeds (N1 and N2 rotors) and pressure (Pb) – Thrust – Overboost Benefit 4: Improves operational reliability by using: – Two channel control – Automatic fault detection – Automatic fault compensation – Redundant inputs and outputs 42 Electronic Engine Control Benefit 5: Provides easier engine maintenance through these functions: – Monitoring – Self-tests – Fault isolation Benefit 6: Improves communication with the flight deck through these functions: – Automatic control of EPR – Automatic agreement between the throttle lever position and engine thrust 43 EEC Inputs Thrust lever position Ambient pressure Inlet total pressure Exhaust total pressure Shaft RPM N1,N2,N3 Burner pressure Start lever/switch position Ignition switch selection VSV position EGT Inlet Temperature 44 FADEC - Full Authority Digital Engine Control FADEC is a system that consists of the following components shown below: 45 FADEC - Full Authority Digital Engine Control Purpose: Full Authority Digital Electronic Control (FADEC) is a computer-based control system that regulates and monitors engine operations. It also acts as the primary interface between the engine and aircraft systems. 46 FADEC - Full Authority Digital Engine Control Facts on FADEC: Found in both aircraft and engine systems, FADEC components work together to improve efficiency, enhance control functions, protect the engine, and provide operational reliability. All FADEC aircraft and engine components are overseen by the Electronic Engine Control (EEC), which is itself a component of the FADEC system. The EEC sends, receives, and interprets information between aircraft and engine systems, while controlling and monitoring engine functions. 47 FADEC - Full Authority Digital Engine Control (FYI) FADEC aircraft systems that interact with the EEC include the following. Thrust Management Computer (TMC) Flight Management Computer (FMC) Air Data Computer (ADC) Engine Indication Crew Alert System (EICAS) Electronic Flight Instrument System (EFIS) 48 FADEC System 49 EEC Redundancy (Channel A and B) Vital parameters of EEC have dual inputs or redundancy Electrical power for EEC has redundancy. Redundancy helps in continued safe operation of the engine, even if there is loss of a single key input. All servo actuators have dual monitors. 50 EEC Programming Plug Description: 1. The programming plug’s engine thrust data and EPR modification data are input to Channel A/B during engine start. 2. This same data is cross-wired and cross-talked from Channel A to Channel B. Note that if the EEC programming plug is not installed, the EEC will not permit the engine to start. If the EEC programming plug disconnects in flight, the engine will continue to operate normally. Since the programming plug is matched to the engine, it must stay with the engine in the event that the EEC is replaced. 51 EEC Programming Plug 52 Consumption of Fuel Calculation 53 Fuel uplift (top-up) for a flight Average fuel flow rate x no. of engines =hourly consumption of the aircraft. Hourly consumption x trip duration = trip fuel Trip fuel + reserve fuel + Alternate Fuel = departure fuel Departure fuel – arrival fuel = uplift fuel Uplift fuel in kg/ sg. of fuel = uplift in litres. 54 Thrust specific fuel consumption TSFC TSFC= Fuel Flow rate/ THRUST Fuel consumption required per unit thrust Lower the TSFC more efficient is the engine. It burns less fuel to produce unit thrust. Units for TSFC kg per hour/newton lb per hour/ lbf 55 Recap 1 The most common type of fuel used in civil aviation and military aviation The precautions when performing mixed refuelling Qualities of aviation fuel Draw out the Gas Turbine Engine Fuel System Explain the functionality of all major components that are in the diagram Functionality / input of FCU 56 Recap 2 Functionalities of EEC Inputs of EEC Functionalities of FADEC Inputs of FADEC Explain about EEC redundancy Explain about programming plug Calculation of TSFC and fuel required during flight 57