Steel Making - CH5-SMS-gpoe_2024 PDF
Document Details
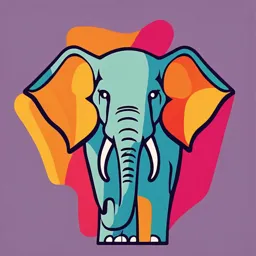
Uploaded by PraisingCerium
Tags
Summary
This document provides an overview of several steel making processes, including hot metal desulphurization, open/twin hearth furnaces, and basic oxygen furnaces (BOF). It discusses the inputs, outputs, and key processes involved in converting raw materials into steel.
Full Transcript
Chapter – 5 STEEL MAKING 5.1 Introduction The Hot Metal also known as molten pig iron which is produced by Blast Furnaces contains various impurities. Main impurity present is Carbon and other impurities like phosphorus, sulphur, silicon, non metallic inclusions etc are also present. Steel making is...
Chapter – 5 STEEL MAKING 5.1 Introduction The Hot Metal also known as molten pig iron which is produced by Blast Furnaces contains various impurities. Main impurity present is Carbon and other impurities like phosphorus, sulphur, silicon, non metallic inclusions etc are also present. Steel making is the process of purification of this Hot Metal. Steel such produced is the pure form of metal. Hot Metal contains around 4% of Carbon which is to be reduced below 0.10% as per the requirement. Other impurities like sulphur, phosphorus are also removed and alloying elements such as Manganese, Silicon, Nickel, Chromium and Vanadium are added to produce the exact steel required. The schematic view and various processes involved in steel making are as follows: Slabs/ Bloom HMDS—HOT METAL DESULPHURISATION BOF—BASIC OXYGEN FURNACE OH/THF—OPEN HEARTH/TWIN HEARTH FURNACES ARS—ARGON RINSING STATION LF—LADLE FURNACE RH DEGASSER—RUHR –STAHL HERAUS (Process is named on a German town and a German scientist) VAD—VACCUM ARC DEGASSER VOD—VACCUM OXYGEN DECARBURISATION CCS/CCP—CONTINUOUS CASTING SHOP/ PLANT The Hot Metal from Blast furnace comes in Hot metal ladles / Torpedo Ladle to Steel Melting Shop by rail. It is poured into a vessel called Mixer. It is then taken out from mixer as per requirement of the Converter. It can either go through Hot metal desulphurization unit (HMDS) or directly to the process of steel making i.e. Basic Oxygen Furnace (BOF). Advancements in Steel Making Process Bessemer process > Open Hearth /Twin Hearth > LD Convertor 65 Hot Metal Desulphurisation Sulphur is mainly present in iron ore and coal. Reducing the sulphur content to less than 0.020% in the blast furnace is difficult from an economical standpoint. As the steel quality often requires a sulphur content of 0.010%, the hot metal must be desulphurized in another way. In desulphurization methods lime orcalcium carbide and magnesium reagent may be used in proper proportion. They are injected into the metal with a special designed lance under a gaseous stream. In this way, the Sulphur content can be reduced to levels below 0.005 %. Hot metal in a ladle is brought to Desulphurization unit by *EOT cranes or rail. After proper positioning of the ladle, injection lance is lowered deep into the metal. Then start injection of the said material through the lance and is continued for 5 to 10 minutes depending on sulphur content in hot metal. Sulphur impurityis removed in the form of magnesium sulphide in a violent reaction. Ladle is then taken to slag racking machine to remove the slag formed during the injection process. Hot metal is then sent to converter. 5.2 Open /Twin Hearth Furnaces One of the oldest established process of steel making, most open hearth furnaces were closed by early 1990’s, because of their fuel inefficiency, low productivity and cumbersome operation. Basic oxygen steel making (BOF) or LD process replaced open hearth furnaces. Twin hearth furnace consists of two hearths separated by a bridge wall with a common roof. Twin hearth furnace works on synchronization between the two hearths, there by both the hearths are engaged in different operations. While one is in solid period, the other will be in liquid period. The fundamental principle of Twin Hearth Furnace is physical and chemical heat generated during blowing in one hearth is utilized in the adjoining hearth for preheating the charge, making the process faster. The tap to tap time of THF is cut by half since the furnace is tapped from both the hearth alternatively at an interval of one half of the heat duration in one hearth. Operational efficiency of the furnace is based on the equal duration of the both cold and hot period i.e. in one hearth when melting starts the other hearth is ready to betapped. Activities in the furnace can basically be divided into two parts. Activities during cold period and activities during hot period run parallel at the same time for one of the two hearths in such a way that if one hearth is in cold period other will be in hot period. Cold period includes the time given to the furnace for tapping, fettling, charging and heating of the cold charge up to the end of pouring of hot metal in the furnace. The activities taking place during the hot period can be categorized into melting, refining and holding. *EOT-Electrically operated Overhead Travel 5.3 1. 2. 3. 4. 5. Basic Oxygen Furnace (BOF - LD Converter) Sequence of operation in BOF Lime/dolomite addition at converter bottom. Scrap charging Hot metal charging Oxygen blowing Addition of fluxes in batches during blow 66 6. After blowing oxygen lance is lifted and converter tilted for sample and temperature recording 7. Tapping in ladle 8. Addition of de-oxidiser in ladle during tapping Basic Oxygen Furnace is commonly known as BOF process or LD process. It is named so because this process was developed in LINZ and DONAWITZ, two cities in Austria. The process is also called basic because of refractory type used for lining the vessel to withstand the high temperature of molten metal. As compared to Open / Twin hearth, BOF process is fast, energy efficient and simple. It reduces the time of smelting, and increased labor productivity. Tap to tap time in BOF is around 45-50 minutes. The name BOF is derived from the manner in which the compositional adjustments are achieved. Oxygen is the reagent/fuel that is used to remove most of the undesirable elements via a number of complex oxidation processes. Basic refers to the fact that the reaction takes place in a Vessel called converter lined with basic refractory. 67 Inputs: The major input materials in BOF or LD converter are:  Hot Metal: Hot metal containing around 4% carbon is the main input in the BOF.  Scrap: It is used as a coolant as the process is exothermic. The large thermal energy is produced during the process so as to get targeted end/tapping temperature, it is important to maintain the proper charge balance, the ratio of hotmetal to scrap.  Fluxes: Fluxes such as calcined Lime, calcined Dolomite etc are used in the process for slag making. Slag is required to absorb/extract impurities from metal. An emulsion of metal and slag formed during blowing helps in refining.  Oxygen: one of the important inputs comes mainly from captive Oxygen plants in addition to the purchased liquid oxygen. Oxygen purity should be more than 99.5%.  Nitrogen: It is not directly taking part in the process but used for purging and ceiling purpose. It is also used for slag splashing to coat vessel refractory lining.  Ferro-Alloys: while tapping the steel Ferro-alloy such as Fe-Si, Si-Mn, Fe-Mnetc are being added to make the desired grade of steel. A complete cycle consists of the following phases: 1. Scrap Charging, 2. Hot Metal Charging, 3. O2 blowing, 4. Sampling & Temperature recording 5. Tapping. Process:  Mixer and Desulphurization: The process start with mixer in steel melting shop. Metal is stored in Mixers and it is taken out as and when needed. Before charging it into BOF, external desulphurization is done as per requirement to reduce Sulphur content in Hot metal. Calcium carbide or lime powder and magnesium compound are injected into hot metal through a lance with Nitrogen as a conveying gas. After compound injection is over slag racking is done to remove the slag which is necessary to avoid reversal of sulphur.  Converter blowing: The process of blowingmeans reaction of Oxygen with hot metal and fluxes in LD converter. The hot metal along with scrap is charged into converter with the help of EOT cranes by tilting the converter. A typical composition of Hot metal is C- 4.0%, Si – 0.60 %, Mn – 0.10 %, P- 0.15%, S68 0.050% and temperature is around 1300ºC. After charging, converter is kept vertical and lance is lowered in the converter through which oxygen is blown at a pressure of around 14-20 kg/cm2. During the blowing process fluxes such as lime, Calcined dolomite, iron ore etc are added to make slag. The most important flux is lime. The slag is basic in nature. Main impurity carbon reacts with oxygen and is removed in the gaseous form (CO/CO2) Impurities like Si, P, S and other non metallic impurities are removed in the form of slag, which is lighter than metal so it floats on metal surface. The blowing process usually takes 15-17 mints. When the blowing is complete converter is tilted to take out the slag in a slag pot. Sample and temperature is also taken manually. At the end of the blow the temperature is generally in the range of 1650ºC - 1690ºC and a typical bath analysis is C – 0.07 %, Mn – 0.08 %, P – 0.020 %, S- 0.030 %. When the desired composition and temperature is achieved the steel is tapped. HEAT BALANCE in a Convertor i.e. Heat Input = Heat Output is balanced as: Heat Input as a. Sensible heat of hot metal in BOF. b. Oxidation of Carbon. c. Oxidation of Silicon. d. Oxidation of Manganese. e. Oxidation of Phosphorus. f. Heat output as a. Sensible heat of Steel. b. Sensible heat of Slag. c. Sensible heat of off gases. d. Chemical heat of off gases. e. Sensible heat of dust f. Heat loses through convection and radiation of the converter  Tapping: Tapping means discharging the liquid steel into ladle through the tap hole present in the converter by tilting it. As per the grade of steel the Ferro-alloys are also added into ladle during tapping. As soon as the steel finishes the converter is lifted and tapping is complete. Good tap hole maintenance and slag free tapping devices like pre tap plugs,Slag Stopper,darts, electromagnetic slag detection sensors etc commonly used to prevent slag carryover into the ladle.  Nitrogen Splashing: After tapping, the residual slag in the converter is splashed with the help of nitrogen along with addition of Lime and/or coke. Converter is kept vertical and lance is lowered. Through the same lance nitrogen is blown which splashes the basic residual slag in the converter and gives a coating on the refractory bricks. Main advantage of nitrogen splashing is to increase the lining life of the converter.  Chemical Reactions: There are a lot of complex chemical reactions taking place in the BOF during blowing. Main reactions in simplified form are given below Fe + O = FeO C + O = CO/CO2 Si + 2O = SiO2 69 Mn + O = MnO 2P + 5O =P2O5 These reactions are exothermic in nature. Lot of heat is evolved during blow. Scrap is used as a coolant to maintain the thermal balance. Due to addition of fluxes the chemical reaction with CaO from Lime and Dolomite and Si, Mnetc from hot metal takes place to make complex compounds which are basic in nature thus helping in making a basic slag which facilitates dephosphorisation.  Slag Composition: The slag formed during the BOF process is basic in nature. It is a complex oxide compound of Ca along with Si, P and other non metallic inclusions. A typical slag analysis at the end of the blowing is as follows: CaO= 45-50%, MgO= 9-11%, FeO= 15-20% Basicity= CaO/SiO2 ≥ 3.0  Functions of Slag a. To transfer the oxygen required for refining. b. To create favourable conditions for decarburisation of dispersed metal droplets. c. To provide a means of removing phosphorus from the liquid pig iron. d. To provide means of eliminating some sulphur from the bath.  Refractories: Refractory plays a very important role in BOF shop. As liquid metal is handled in BOF Shop so all vessels like mixer, converter, ladles etc are lined with refractory bricks. It protects the shell of vessel and retains the metal temperature. Different types of refractory is used as per their usage are given below: o Converter Vessel: The bricks used here are basic in nature. Dolomite bricks or magnesia carbon bricks are commonly used in converter. In recent times magnesia carbon bricks have replaced dolomite bricks. Number of heats made in a converter from one new lining to next lining is known as the lining life of the converter. Now a days all plants are trying to achieve higher lining life. The tap hole in the converter is also made up of refractory, which wears with number of heats tapped. It is changed from time to time. o Mixer: The bricks used here are normally high alumina and magnesite bricks o Ladles: The small vessel which carryHot Metal for charging the converter are called hot metal ladle. They are lined with high alumina bricks. The steel is tapped in steel ladles. This ladle carries steel to secondary refining and finally for casting. The bricks used are again high alumina and magnesia carbon. Equipments: Major equipments in BOF shop are:  Mixer: A large cylindrical or rectangular refractory lined vessel with tilting mechanism, and it is used to store molten metal coming from Blast Furnace. Mixer has a Charging hole from where Hot metal is being charged into the mixer with the 70 help of EOT cranes and a spout to take out hot metal by tilting the mixer. Main functions of mixer are storage and homogenization. Mixed gas is supplied through side burners in order to maintain temperature in Mixers.  Converter: A converter is an open pear shaped vessel made of steel and lined from inside with basic refractory bricks. It can be rotated through 3600. Charging and deslagging is done through mouth where as tapping of steel is done through a hole called tap hole.  Lance: It is made of three concentric steel tubes where water is circulated in the outer tubes and oxygen in the inner tube. Tip of the lance is made of copper. Generally 5 or 6 holes lances are used. A stand by lance is always provided in converter for continuous blowing operation.  Gas Cleaning Plant(GCP):A huge quantity of waste gases with high temperature and containing dust particles, generated during theLD or BOF process is passed through the GCP. Primarily water is sprayed over the gases to separate the solid dust 71 particles and to cool and collect them. Cleaned gases are either collected in a gas holder or is burnt in the atmosphere to control air pollution. o A large water cooled hood sits above converter. The vast quantity of waste gas produced during steel making pass through hood and then collected and cleaned. An ID fan is present which draws the gases up into hood. A movable skirt is attached to bottom of hood which closes the gap and sits on the converter mouth thus controlling the level of air ingress during the blow and avoids burning of CO gas at Convertor mouth. Safety Aspects: As we deal with liquid metal in the Shop, personal as well as equipment safety is of large concern. We should strictly follow the safety norms.  Before charging, converter must be inspected thoroughly and make sure that no liquid slag should be left in the converter. If there is liquid slag, it must be dried up by adding lime before charging.  Do not allow anyone to stand in front of Converter during charging.  There should not be any water in the slag pot in which the slag is to bedumped.  Persons working in the steel melting shop should use personal protective equipment (PPEs) like gloves, blue glass, fire retarding jackets.  Blowing should not be done if there is any water leakage in the lance/hood/skirt.  In case of excessive water logging below the converter blowing should be stopped immediately till the water is cleared.  In case of charging and tapping of converter lot of care has to be taken to avoid any metal splashes. Quality Requirements: Now a day as the quality norms are quite stringent and customers specification are becoming very strict so at all stages quality has to be monitored. In BOF the slag decides the quality of steel. A good slag leads to good steel. Slag carry over to the steel ladles while tapping should be minimum. Slag arrestors are used to minimize slag carry over. Waste and environment management: In BOF during the steel making process, lot of wastes are generated. Some of them are as follows:  During the blowing process lot of waste gases are generated along with dust. CO gas evolved during blowing process is collected in a gas holder and it is further used as a fuel in different units. The dust collected from GCP as slurry is required to be disposed properly or re-used / recycled as input feed for BF or Sinter Plant.  Slag generated during the steel making operation is also recycled. It is dumped and cooled then it is used by Blast Furnaces, sintering plant and Steel Melting Shop.  The slag that is disposed off can be used for making pellets / briquettes for consumption in Sinter Plant.  Effective dog-house must be installed to capture the fugitive emissions from the Converter. Tapping practices to be performed in convertor: 72           Deslagging after blow finish Sample and temperature Reblow if required 97% straight blow practice Tapping of steel in steel ladle Average cast slab wt-273t Deoxidation by aluminium and silicon Tapping temperature-1660 to 1680 deg centigrade Tapping time >6 mins Tap hole life >110 heats Practices to be followed for convertor nurturing: 5.4 Splashing of retained slag for 3 mins by nitrogen blow through lance Addition of coke for better splashing Coating of converter Slag dumping in slag pot after splashing and coating before next charging Secondary Steel Making Objective: Achieving the required properties of steel often requires a high degree of control over carbon, phosphorus, sulphur, nitrogen, hydrogen and oxygen contents. Individually or in combination, these elements mainly determine material properties such as formability, strength, toughness, weldability, and corrosion behaviour. There are limits to the metallurgical treatments that can be given to molten metal in high performance melting units, such as converters or electric arc furnaces. The nitrogen and phosphorus content can be reduced to low levels in the converter but for further reducing carbon, sulphur, oxygen and hydrogen contents (< 2 ppm) to very levels it can only be obtained by subsequent ladle treatment. To ensure appropriate conditioning of steel before the casting process, the alloying of steel to target analysis and special refining treatments are carried out at the ladle metallurgy stand. The objectives of secondary steelmaking can be summarized as follows:  Refining and deoxidation  Removal of deoxidation products (Mn0, SiO2, Al2O3)  Desulphurization to very low levels (< 0,008%)  Homogenization of steel composition  Temperature adjustment for casting, if necessary by reheating (ladle furnace)  Hydrogen removal to very low levels by vacuum treatment. The high oxygen content of the converter steel would result in large blow-hole formation during solidification. Removal of the excess oxygen ("killing") is therefore vital before subsequent casting of the steel. Steels treated in this way are described as killed steels. All secondary steelmaking processes allow deoxidising agents to be added to the ladle 73 Deoxidation can be performed by the following elements classified by increasing deoxidation capacity; carbon - manganese - silicon - aluminium.The most popular are silicon and aluminium. After addition, time must be allowed for the reaction to occur and for homogeneity to be achieved before determination of the final oxygen content using EMF probes (electrochemical probe for soluble oxygen content). Secondary Refining Secondary steel making units can be categorized as: a) Stirring Systems b) Ladle Heating Systems c) Vacuum Degassing Systems and d) Addition Systems (RH Process and Tank degassing unit) a. Stirring systems These systems involve in stirring the molten steel bath for obtaining homogenous temperature, composition, floatation of inclusions and promotion of slag-metal refining reaction.As most of deoxidation agents form insoluble oxides, which would result in detrimental inclusions in the solid steel, they have to be removed by one of the following processes during the subsequent refining stage: Argon stirring and/or injection of reactants (CaSi, and/or lime based fluxes) achieves:  Homogeneous steel composition and temperature  Removal of deoxidation products  Desulphurisation of aluminium-killed steel grades  Sulphide inclusion shape control. Argon stirring can be done by refractory lined lance (Top lance) or by means of porous plug made by high alumina material (bottom purging). b. Ladle heating systems These furnaces, act as buffer between the primary melting unit and the continuous casting unit giving precise temperature and compositional control. This provides an option to the primary melting unit to tap at low temperatures leading to saving in time and energy and also the cost of Ferro-Alloys / De-oxidisers apart from increasing the refractory life of BOF. Through appropriate slag composition control, de-oxidation practice and argon stirring, it is possible to produce clean steels through Ladle furnace. Stirring of the melt by argon or by an inductive stirring equipment and arc heating of the melt (low electric power, typical 200 KVA/t) allows:  long treatment times  high ferro-alloy additions  high degree of removal of deoxidation products due to long treatment under optimized conditions  homogeneous steel composition and temperature 74  desulphurisation, if vigorous stirring by argon. In ladle furnace the produced exhaust waste gases are cleaned by means of bag filters/ESP. c. Vacuum Degassing Systems The concept of degassing started primarily to control the hydrogen content in steels but sooner it served many purposes for production of clean steels. The degassing systems can be further classified as Circulation Degassers, Tank Degassers. Vacuum-Treatment: RH process (Ruhrstahl-Heraeus) In the RH process the steel is sucked from the ladle by gas injection into one leg of the vacuum chamber and the treated steel flows back to the ladle through the second leg. Tank degassing unit In the tank degasser process, the steel ladle is placed in a vacuum tank and the steel melt is vigorously stirred by argon injected through porous plugs in the bottom of the ladle. Millibar is term used for measurement of vacuum. Steam is used for creating vacuum. Vacuum treatment achieves:   reduction of the hydrogen content to less than 2 ppm considerable decarburisation of steel to less than 30 ppm when oxygen is blown by a lance (RH - OB) alloy addition under vacuum  homogeneous steel composition, high degree of cleanliness from deoxidation products High temperature losses (50 - 100°C) are a disadvantage; therefore high superheat of the melt prior to this process is essential. 75 Ferro alloy addition facility for trimming addition These contain bunkers for storage of ferro alloys, weighing hoppers, conveyor belt, skip; addition hoppers etc. Addition during vacuum is also possible. For most secondary steelmaking techniques it is either desirable or essential to stir the liquid steel. Gentle stirring is sufficient for inclusion removal; non-metallic inclusions are brought into contact with liquid slag on top of the melt where they can be fixed. For degassing and desulphurisation however, violent stirring is necessary to increase the surface of steel exposed to vacuum (H2-removal) or to mix the steel and slag for good desulphurisation efficiency. Other Steel Refining Units 76 Metallurgical Principles ( ) means in slag. [ ] means in steel. Deoxidation As steel making process is an oxidation refining process, tap steel from primary furnace contains significant amount of oxygen(400-1000 ppm).The solubility of O2 in liquid steel is 0.16% but in solid steel it is only 0.003%.Excess oxygen causes defects like blow holes and non-metallic inclusions. Oxygen is lowered by deoxidisers like Mn, Si, Al etc. Through vacuum treatment oxygen is removed as CO. Decarburisation Reaction of ‘C’ and ‘O’ removal is given by [C] + [O] = CO [C] +1/2O2 = CO [C] +(FeO) = CO +Fe ‘C’ removal is controlled by vacuum level, Argon flow rate, initial level of ‘C’, bath Oxygen content, Amount of Oxygen injected Control is required during tapping , LF & VAD operation to avoid recarburisation. Some other sources of recarburisation are ferro-alloys, graphite electrodes during arcing. Desulphuristion Removal of sulphur depends on i) High sulphidecarryingcapacity of slag - high basicity ii) High (S)/[S] - sulphur partition iii) Fluid slag - addition of spar or synthetic slag iv) High stirring intensity - increased slag-metal reaction. v) Low O potential in slag and metal- low Feo+Mno< 5% Removal of H2& N2 Hydrogen removal Reaction is 2[H] = H2 [H] = k*H2 i) H content varies with p H2 ii) To get very low H , vacuum level must be low and improved stirring. So H removal is controlled by vacuum level, Ar flow rate, initial level of H. Nitrogen removal Reaction is 2[N] = N2 I. To get very low N vacuum level must be very low. II. Compared to H , nitrogen removal rate is low due to low diffusibility 77 5.5 Casting Continuous Casting of Steel: Basic Principles Background Continuous Casting is the process whereby molten steel is solidified into a "semifinished" billet, bloom, or slab for subsequent rolling in the finishing mills. Prior to the introduction of Continuous Casting in the 1950s, steel was poured into stationary moulds to form "ingots". Since then, "continuous casting" has evolved to achieve improved yield, quality, productivity and cost efficiency. Figure 1 shows some examples of continuous caster configurations. Casting of Liquid Steel Molten steel is continuously poured into a water cooled Cu mould that is open at the top and bottom. The steel gradually cools and begins to set solid in the mould. The rate at which molten steel is poured into the top is matched with the rate at which the solid steel is pulled out at bottom. In this way, a long continuous piece is formed. So, the process is called continuous casting. Steel formed can then be cut into length as desired. Figure 1 - Examples of Continuous Casters 78 Steel from the electric or basic oxygen furnace is tapped into a ladle and taken to the continuous casting machine. The ladle is raised onto a turret that rotates the ladle into the casting position above the tundish. Referring to Figure 2, liquid steel flows out of the ladle (1) into the tundish (2), and then into a water-cooled copper mould (3). Solidification begins in the mould, and continues through the First Zone (4) and Strand Guide (5). In this configuration, the strand is straightened (6), torch-cut (8), then discharged (12) for intermediate storage or hot charged for finished rolling. Figure 2 - General Bloom/Beam Blank Machine Configuration 1:Ladle Turret, 2:Tundish/Tundish Car, 3:Mould, 4:First Zone (Secondary Cooling), 5:Strand Guide (plus Secondary Cooling), 6:Straightener Withdrawal Units, 7:Dummy Bar Disconnect Roll, 8:Torch Cut-Off Unit, 9:Dummy Bar Storage Area, 10:Cross Transfer Table, 11:Product Identification System, 12:Product Discharge System Figure 3 depicts a Slab Caster layout. Note the extended roller containment compared to that for a Bloom/Beam Blank (as in Figure 2), required to maintain product shape through final solidification. Depending on the product end-use, various shapes are cast (Figure 4). In recent years, the melting/casting/rolling processes have been linked while casting a shape that substantially conforms to the finished product. The Near-Net-Shape cast section has most commonly been applied to Beams and Flat Rolled products, and results in a highly efficient operation. The complete process chain from liquid metal to finished rolling can be achieved within two hours. 79 Figure 3 -Slab Caster Layout Figure 4 - Continuous Cast Shapes (sizes in millimeters) Before going into the details of CCM a brief description of the caster is given below: => Raw/Crude Steel from converter => => Refining crude steel i.e. killing, Homogeneous Temperature and Composition => Turret, Ladle S/Gate, Shroud => Tundish => Mould Liquid steel comes from the ladle into the tundish. Tundish is a device where it collects, accumulates liquid steel from the ladle and feeds to two or more moulds through SEN depending on the m/c and process The basic design of the caster is to solidify liquid steel to its solid products uninterruptedly/continuously. For that the steel to be cast must be killed. Steel from which oxygen (dissolved in steel during steel making in BOF) is removed at SRU deoxidising elements like Al (Aluminum) Si (silicon) etc. is called KILLED STEEL. Oxygen in steel is measured using Celox Temp and expressed in ppm. Steel that is to be cast should not have high ppm of O2 otherwise casting cannot be done because O2 of steel will form unwanted oxides viz CaO, SiO2 , MgO and will be deposited over the entry nozzle and thus will restrict the flow of steel into the mould. Caster Preparation: 1. Steel that is to be cast is treated well at SRU for smooth casting. 2. Tundish through which casting will be done is to be prepared. 80 Tundish is a device through which continuity of the casting is maintained. There are two types of casting practices are in use namely cold tundish and hot tundish practices. Liquid steel comes from the ladle into the tundish and in turn the tundish feeds the liquid steel into the mould through different outlet at the bottom of the tundish. Tundish is made of steel and inside of which is lined with refractory bricks or castable. After that tundish boards are fixed over the refractory lined. Submerged entry nozzle (SEN) are fixed by clamping device in each of the tundish outlet. 3. Mould Preparation: Mould is the most important equipment in the caster m/c. primarily mould is prepared according to the shape and size of the product. For solidification of the initial liquid steel that enters into the mould one DUMMY BAR head is used, which is fed into the mould with a fixed rod or flexible chain. This DUMMY BAR head is packed. Mould is made purely of copper as copper has the most heat discharge capacity than any other metal economically available. All sides of this mould is made up of Cu plate and heat from liquid steel immediately discharges trough the copper plates by mould cooling system Copper plates are cooled by circulating soft water through designed tubes in the form of coils. Here the difference of MOULD COOLING WATER Outlet Temperature & Inlet Temperature is monitored continuously. It is very much hazardous part in caster m/c during casting. An alarm is provided as soon as the difference of temperature raises more. Immediate actions are to be taken and if necessary casting should be stopped without waiting for any other decision to be asked from anyone. Casting Process Liquid steel taken into ladle is refined at SRU is placed over the turret arm and ladle SG is fixed. Then one shroud is fixed at the bottom of the ladle collector nozzle so that no stream of liquid steel comes in contact with the atmosphere and no spillage occurs. This liquid steel gradually fills the tundish and from there liquid steel leaves tundish nozzle/TSG through SEN into the mould. Initially steel rests on the DUMMY BAR head on which some chillers are placed to get the liquid steel freeze/solidifies quickly then the m/c starts with MOM & casting powder is to be sprayed continuously at a certain mould level. The process continues after the DUMMY BAR head is disconnected as it reaches at its particular position. Length of the slab/billet is maintained by using cutting torch/ shearing blades. 81 To summarize, the casting process is comprised of the following sections:  A tundish, located above the mould to feed liquid steel to the mould at a regulated rate  A primary cooling zone or water-cooled copper mould through which the steel is fed from the tundish, to generate a solidified outer shell sufficiently strong enough to maintain the strand shape as it passes into the secondary cooling zone  A secondary cooling zone in association with a containment section positioned below the mould, through which the still mostly-liquid strand passes and is sprayed with water or water and air to further solidify the strand  Except straight Vertical Casters, an Unbending & Straightening section  A severing unit (cutting torch or mechanical shears) to cut the solidified strand into pieces for removal and further processing Liquid Steel Transfer There are two steps involved in transferring liquid steel from the ladle to the moulds. First, the steel must be transferred (or teemed) from the ladle to the tundish. Next, the steel is transferred from the tundish to the moulds. Tundish The shape of the tundish is typically rectangular, but delta and "T" shapes are also common. Nozzles are located along its bottom to distribute liquid steel to the moulds. The tundish also serves several other key functions: 82     Enhances oxide inclusion separation. Provides a continuous flow of liquid steel to the mould during ladle exchanges. Maintains a steady metal height above the nozzles to the moulds, thereby keeping steel flow constant and hence casting speed constant as well. Provides more stable stream patterns to the mould(s). Tundish performance largely depends on key process parameters like:  Chemistry  Fluid Flow  Temperature Clogging of SEN due to deposit formation is a major problem and leads to:  Affects the stream flow pattern in mould.  Reduces the pouring rate.  May lead to premature changing of SENs and termination of casting operation.  Steel quality may be affected. Factors affecting SEN clogging:  Steel chemistry (alloying elements, total inclusions, etc.)  Casting conditions (tundish depth, superheat, speed, etc.)  SEN chemical composition, geometry & design.  Argon injection rate  Air aspiration into the SEN  Oxygen provided by the refractory materials Mould The main function of the mould is to establish a solid shell sufficient in strength to contain its liquid core upon entry into the secondary spray cooling zone. 83 The mould is basically an open-ended box structure, containing a water-cooled inner lining fabricated from a high purity copper alloy. Mould water transfers heat from the solidifying shell. The working surface of the copper face is often plated with chromium or nickel to provide a harder working surface, and to avoid copper pickup on the surface of the cast strand. Mould heat transfer is both critical and complex. Mathematical and computer modeling are typically utilized in developing a greater understanding of mould thermal conditions, and to aid in proper design and operating practices. Heat transfer is generally considered as a series of thermal resistances as follows:     Heat transfer through the solidifying shell Heat transfer from the steel shell surface to the copper mould outer surface Heat transfer through the copper mould Heat transfer from the copper mould inner surface to the mould cooling water Mould Oscillation Mould oscillation is necessary to minimize friction and sticking of the solidifying shell, and avoid shell tearing, and liquid steel breakouts, Friction between the shell and mould is reduced through the use of mould lubricants such as oils or powdered fluxes. Oscillation is achieved either hydraulically or via motor-driven cams or levers which support and reciprocate (or oscillate) the mould. Mould oscillating cycles vary in frequency, stroke and pattern. However, a common approach is to employ what is called "negative strip", a stroke pattern in which the downward stroke of the cycle enables the mould to move down faster than the section withdrawal speed. This enables compressive stresses to develop in the shell that increase its strength by sealing surface fissures and porosity. 84 Mould Flux      Functions of mould powder Provides thermal insulation to the liquid steel meniscus to prevent premature solidification Prevents re-oxidation of liquid steel in the mould by atmospheric air Absorbs inclusions Provides a lubricating film of molten slag between solidifying shell and mould wall Secondary Cooling Typically, the secondary cooling system is comprised of a series of zones, each responsible for a segment of controlled cooling of the solidifying strand as it progresses through the machine. The sprayed medium is either water or a combination of air and water. Figure 5 - Secondary Cooling –– Three (3) basic forms of heat transfer occur in this region:  Radiation  Conduction As the product passes through the rolls, heat is transferred through the shell as conduction and also through the thickness of the rolls, as a result of the associated contact. 85  Convection This heat transfer mechanism occurs by quickly-moving sprayed water droplets or mist from the spray nozzles, penetrating the steam layer next to the steel surface, which then evaporates. Specifically,in the spray chamber (Secondary Cooling) heat transfer serves the following functions: i. ii. iii. Enhance and control the rate of solidification, and for some casters achieve full solidification in this region Strand temperature regulation via spray-water intensity adjustment Machine Containment Cooling Strand Containment The containment region is an integral part of the secondary cooling area. A series of retaining rolls contain the strand, extending across opposite strand faces. Edge roll containment may also be required. The focus of this area is to provide strand guidance and containment until the solidifying shell is self-supporting. Bending and Straightening Equally important to strand containment and guidance from the vertical to horizontal plane are the unbending and straightening forces. As unbending occurs, the solid shell outer radius is under tension, while the inner radius is under compression. The resulting strain is dictated by the arc radius along with the mechanical properties of the cast steel grade. If the strain along the outer radius is excessive, cracks could occur, seriously affecting the quality of the steel. These strains are typically minimized by incorporating a multi-point unbending process, in which the radii become progressively larger in order to gradually straighten the product into the horizontal plane. Figure 7 - Curved Section of Multi-Strand Beam Blank Caster prior to Unbending Figure 8 - Straightener Withdrawal Units for Strand Unbending 86 After straightening, the strand is transferred on roller tables to a cut off machine, which cuts the product into ordered lengths. Sectioning can be achieved either via torches or mechanical shears. Then, depending on the shape or grade, the cast section will either be placed in intermediate storage, hot-charged for finished rolling or sold as a semi-finished product. Abnormalities: During casting some unwanted hard oxides which gets deposited over the steel into the mould and interrupts the steel flow and casting gets aborted. This phenomenon is called Chocking. In some cases temperature at which liquid steel gets solidified may be reached during casting which caused solidification at SEN and restricts the steel flow, and then also casting continuity gets disturbed and casting stops. This is called Freezing. Another major problem that hinders the casting process is Break Out. Some Casting Defects: Types of defects:  Surface cracks  Internal cracks  Blow holes, Pin holes etc Remedial measures:  Control of superheat of liquid steel (appropriate temperature)  Steel chemistry  Casting speed Safety Measures:  Mould cooling temperature and its difference of temperature of Inlet water and Outlet water is to be monitored continuously.  Tundish walls and slidegate m/c fixed on it is to be observed carefully. 5.6 Ingot Casting A Teeming ladle is prepared for each and every heat. The liquid steel is teemed through the nozzle present at the bottom of the teeming ladle. The flow of metal into the mould through the nozzle can be controlled using slide gate system. Earlier stopper rod assembly was in use. The ingots are stripped off from these moulds. These ingots are then sent to soaking pit. These moulds are again prepared (i.e. cooling by water, cleaning and coating) for another. Teeming temperature is one of the most important parameters in ingot casting practice. High temperature leads to sticker formation while low temperature leads to chocking of nozzle. Care should be taken so that center pouring is done in a mould. There are many types of defects associated with ingot casting. Surface defects such as scabs, cracks and lappiness are common. Bottom pouring of steel into fluted ingot moulds is done in DSP for special steel grades required for manufacturing Wheels and Axles for Railways. 87 Advantages of Continuous Casting over Ingot Casting:     One of the main advantages of continuous casting over ingot casting is the high increase in yield from liquid steel to semi-finished cast product. Ingot casting yield can be as low as 80%. Continuous casting yield depends mainly on ladle capacity, Section sizes and sequence length. Yields of >95% or even higher are not uncommon. SAFETY LD Process or Primary Steel Making safety hazards:  Lance / Lance tip puncture to be avoided and taken care of to avoid any water leakage inside the convertor  During blowing CO gas monitor to be always used for multilevel activities above the convertor area Secondary steel unit pose certain safety hazards to personnel working like: During argon purging metal splashes can cause burn injury. In ladle furnace, there is danger of metal splashes and electrocution due to very high current of electrode. In VAD, VOD & RH vacuum present inside treatment area can pose serious danger of suction. Body parts may get sucked inside if isolating plate collapse. Also fumes coming out may cause suffocation. Danger of carbon monoxide is also there in vacuum treatment stations Do & Don’t: Avoid going near high current line & high current cables in running ladle furnace and in VAD If red spot is observed in ladle, STOP arcing. It may lead to ladle through. People must always be aware of the safety hazards of their areas. Steel Making MCQs: 1 2 The following gas used for slag splashing in Converter b. Nitrogen a. Oxygen c. 4 5 d. Air Gangue d. Alloying element Lime is used in Converter as a a. Flux 3 CO2 b. Slag c. Converter vessels are usually line with a. High alumina b. Silica bricks bricks c. Magnesia carbon bricks The fuel gas recovered from BOF process comprises of c. CO a. Methane b. C.N.G Argon is used for Ladle stirring because 88 d. Fire clay brick d. CO2