ATA 24 - SEP 2024 PDF
Document Details
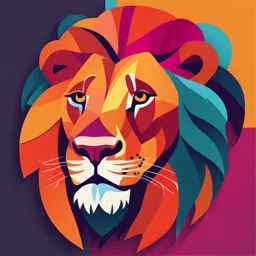
Uploaded by FavorableOnyx3775
Sister Nivedita Girls' High School
2024
Tags
Summary
This document is a training manual for the De-Havilland DHC-8-400, focusing on electrical power systems. It covers topics including the battery system, main 28 VDC generation system, APU 28 VDC generation system, and external DC/AC power systems. It's designed for maintenance training purposes.
Full Transcript
COURSE CODE DGM12CBXX3Q4PW De-Havilland DHC-8-400 B1 & B2 TRAINING MANUAL ISSUE 02 DATE 20 Sep 2024 REVISION DATE...
COURSE CODE DGM12CBXX3Q4PW De-Havilland DHC-8-400 B1 & B2 TRAINING MANUAL ISSUE 02 DATE 20 Sep 2024 REVISION DATE CHAPTER ATA 24 ELECTRICAL POWER THIS MANUAL IS INTENDED FOR TRAINING PURPOSE ONLY REV 2.0 20 Sep 2024 PAGE 1 DGM12CBXX3Q4PW TRAINING PURPOSE ONLY MAINTENANCE TRAINING ORGANISATION DHC-8-400 B1 & B2 TRAINING MANUAL THIS PAGE IS INTENTIONALLY LEFT BLANK REV 2.0 20 Sep 2024 PAGE 2 DGM12CBXX3Q4PW TRAINING PURPOSE ONLY MAINTENANCE TRAINING ORGANISATION CONTENTS DHC-8-400 B1 & B2 TRAINING MANUAL CONTENTS CONTENTS.................................................................................................................................................................................................................................. 2 ELECTRICAL POWER, GENERAL................................................................................................................................................................................................... 4 BATTERY SYSTEM........................................................................................................................................................................................................................ 7 MAIN 28 VDC GENERATION SYSTEM....................................................................................................................................................................................... 22 APU 28 VDC GENERATION SYSTEM.......................................................................................................................................................................................... 92 EXTERNAL DC POWER............................................................................................................................................................................................................ 106 DC ELECTRICAL LOAD DISTRIBUTION..................................................................................................................................................................................... 120 AC GENERATION SYSTEM....................................................................................................................................................................................................... 141 EXTERNAL AC POWER............................................................................................................................................................................................................. 186 AC ELECTRICAL LOAD DISTRIBUTION..................................................................................................................................................................................... 202 REV 2.0 20 Sep 2024 PAGE 3 DGM12CBXX3Q4PW TRAINING PURPOSE ONLY MAINTENANCE TRAINING ORGANISATION ELECTRICAL POWER, GENERAL DHC-8-400 B1 & B2 TRAINING MANUAL ELECTRICAL POWER, GENERAL galleys. Introduction It also supplies power to the Transformer Rectifier Units (TRUs), which are part of the direct current (dc) generation system. Refer Figure - Electrical System Control and Indication Refer Figure - EPGDS Block Diagram The power is distributed by an electrical bus system. It reconfigures for individual power source and bus failures, by the automatic closing and opening The Electrical Power Generation and Distribution System (EPGDS) is used to of bus tie contactors. supply the electrical energy for all onboard electrical equipment. The EPGDS has DC and AC generating systems. The DC generation system includes a battery There are both DC and AC external power receptacles for Ground Power Unit system. The EPGDS provides for energy conversion, distribution, storage, (GPU) connection. control, protection, monitoring, and indication to the flight crew. Provision is made for external connection of DC or AC external power while on the ground. All AC and DC aircraft services can be operated from the AC generators or the AC external power alone. The EPGDS provides for: The EPGDS has the sub−systems that follow: Energy conversion Distribution Alternating current variable frequency (24–21–00) Storage Main 28 Vdc generation (24–31–00) Battery (24–32–00) Control Protection Auxiliary Power Unit (APU) 28 Vdc (24–33–00) Monitoring External ac ground power (24–41–00) Indication. External dc ground power (24–42–00) AC electrical load distribution (24–51–00) The DC generation system is supplied by three NiCad batteries, two engine DC electrical load distribution (24–61–00). driven starter/generators, two Transformer Rectifier Units (TRUs) and an optional Auxiliary Power Unit (APU). The TRUs supply 28Vdc and are powered by the two engine driven Alternating Current (AC) generators that supply 115 Volts Alternating Current (VAC). The ac variable frequency generators make 115 Vac three phase electrical power for ac systems that are not frequency sensitive, such as deicing heaters, fuel auxiliary pumps, the Standby Power Unit (SPU) hydraulic pump and the REV 2.0 20 Sep 2024 PAGE 4 DGM12CBXX3Q4PW TRAINING PURPOSE ONLY MAINTENANCE TRAINING ORGANISATION DHC-8-400 B1 & B2 TRAINING MANUAL FIGURE - ELECTRICAL SYSTEM CONTROL AND INDICATION REV 2.0 20 Sep 2024 PAGE 5 DGM12CBXX3Q4PW TRAINING PURPOSE ONLY MAINTENANCE TRAINING ORGANISATION DHC-8-400 MAINTENANCE TRAINING MANUAL FIGURE - EPGDS BLOCK DIAGRAM REV 2.0 20 Sep 2024 PAGE 6 COURSE Code TRAINING PURPOSE ONLY MAINTENANCE TRAINING ORGANISATION BATTERY SYSTEM DHC-8-400 B1 & B2 TRAINING MANUAL BATTERY SYSTEM Vent and Drains, Standby Battery Introduction The contactors to connect the main and auxiliary batteries are located in the DC Contactor Box (DCCB) and the contactors that control the standby battery The battery system supplies emergency 28 Vdc electrical power to the aircraft operation are located in the Standby Battery Contactor Box (SBCB). Refer to dc essential busses and to the #3 Standby Hydraulic Pump. Main 28 VDC Generation System. General Description Figure - Battery System Block Diagram, Indications The battery power system of the aircraft has three batteries and switching devices to supply electrical power to the essential busses during emergency flight conditions. The main, auxiliary, and standby batteries are connected to the main feeder busses to receive a charging current. The main and the auxiliary batteries also connected to the main feeder busses to supply electrical power to start the engines. During an engine start condition, the standby battery is disconnected from the main feeder bus, but stays connected to the essential busses to maintain a minimum voltage level on the essential bus. The dc control panel in the flight compartment has the toggle switches to control the battery system. The Engine and System Integrated Display (ESID) system shows main 28 Vdc generation system electrical indications. The Battery system has the components that follow: Battery and Box, Main Vent and Drains, Main Battery Battery and Box, Auxiliary Vent and Drains, Auxiliary Battery Battery and Box, Standby REV 2.0 20 Sep 2024 PAGE 7 DGM12CBXX3Q4PW TRAINING PURPOSE ONLY MAINTENANCE TRAINING ORGANISATION DHC-8-400 B1 & B2 TRAINING MANUAL FIGURE - BATTERY SYSTEM BLOCK DIAGRAM, CONTROL REV 2.0 20 Sep 2024 PAGE 8 DGM12CBXX3Q4PW TRAINING PURPOSE ONLY MAINTENANCE TRAINING ORGANISATION DHC-8-400 B1 & B2 TRAINING MANUAL FIGURE - BATTERY SYSTEM BLOCK DIAGRAM, INDICATIONS REV 2.0 20 Sep 2024 PAGE 9 DGM12CBXX3Q4PW TRAINING PURPOSE ONLY MAINTENANCE TRAINING ORGANISATION DHC-8-400 B1 & B2 TRAINING MANUAL Detailed Description If a start attempt is made during the emergency condition, the batteries will automatically reconnect to the main feeder busses for the duration of the start The BATTERY MASTER toggle switch is set to the ON position to close battery sequence. contactors K3, K4 and K24 and connect the three batteries to the essential busses of the aircraft. Contactor K3, K4 and K24 are controlled directly by the The AUX BATT and MAIN BATT toggle switches connect directly to their BATTERY MASTER toggle switch. Their operation is independent of the Electrical contactor. The other connection to the contactor is routed through normally Power Control Unit (EPCU). The essential busses energize the EPCU. closed contacts of a relay in the EPCU. The BATTERY MASTER toggle switch must be set to the ON position before the The relay in the EPCU is controlled by logic. In some conditions, the relays in the battery toggle switch selections are made to connect the batteries to the main EPCU open to disable the contactor. The batteries disconnect from the main feeder busses. feeder busses by the conditions that follow: Each battery is connected to the main feeder busses by a related battery toggle APU or DC GCUs senses an over current condition switch to receive a charging current. A STBY BATT toggle switch selection will Batteries are disconnected when charging is not allowed. cause the standby battery to connect to the left main feeder bus through The batteries can be charged by an ac external power source through contactor K25. An AUX BATT toggle switch selection will cause the auxiliary the TRUs. battery to connect to the left main feeder bus through contactor K7. A MAIN BATT toggle switch selection will cause the main battery to connect to the right NOTE main feeder bus through contactor K8. Battery charging must be monitored. During an emergency condition, the batteries are the electrical power sources for the main 28 Vdc generation system. Contactors K25, K7 and K8 will open to disconnect the standby, auxiliary and main batteries from their related main feeder bus. The essential distribution busses stay energized by the standby, auxiliary and main batteries. The emergency mode is caused by the conditions that follow: Electrical power is not available from the two dc starter/generators, and Electrical power is not available from one or two TRUs, The aircraft is airborne. REV 2.0 20 Sep 2024 PAGE 10 DGM12CBXX3Q4PW TRAINING PURPOSE ONLY MAINTENANCE TRAINING ORGANISATION DHC-8-400 B1 & B2 TRAINING MANUAL A manual STBY BATT toggle switch selection will connect the standby battery to the left main feeder bus by closing contactor K25. The EPCU causes contactor K25 to close when conditions that follow are correct: No engine is in start sequence An emergency condition is not sensed. The batteries are charged while they are connected to the main feeder busses. The charging sources are either the dc starter/generators, the dc external power, or the aircraft Transformer Rectifier Units (TRUs). A constant potential voltage is supplied to the battery terminals to charge the batteries. When the dc starter/generators are used to charge the batteries, a regulated 28.5 Vdc output is supplied to the batteries. When the batteries are charged from a dc external power source or ac external power source through the TRUs, the charging current, voltage and temperature of the batteries must be visually monitored. The battery current shunts supply output current data from the standby, auxiliary, and main batteries to the EPCU for EIS indication. The negative terminal of each battery is connected through separate current shunts to airframe ground potential. The battery current shunts are located near the batteries. The batteries have two independent internal sensors that sense battery temperature. A thermal sensor supplies battery temperature data to the EPCU for EIS indications, and a bi−metallic temperature switch supplies temperature exceedance data to the caution and warning system for warning indications. The internal sensor wires are routed through a circular connector attached to FIGURE - MAIN, AUXILIARY AND STANDBY BATTERIES the battery case. REV 2.0 20 Sep 2024 PAGE 11 DGM12CBXX3Q4PW TRAINING PURPOSE ONLY MAINTENANCE TRAINING ORGANISATION DHC-8-400 MAINTENANCE TRAINING MANUAL When the battery toggle switch located on the dc control panel is set to BATTERY MASTER position, the standby, auxiliary and main batteries energize the essential busses if no other dc power source is available. FIGURE - EIS, ELECTRICAL SYSTEM PAGE SELECTION FIGURE - DC CONTROL PANEL The electrical page shows the dc starter/generator indications that follow: When the battery toggle switches are set to STBY BATT, AUX BATT, and MAIN, the standby, auxiliary and main batteries will connect to the main feeder busses Digital indication of the standby, auxiliary and main battery loads to receive a charging current. Digital indication of standby, auxiliary and main battery temperature. The Electrical Power Control Unit (EPCU) supplies indication data through the The battery indication has a BATT title in white letters. The indication has MAIN, two Input/output Processors (IOP1, IOP2) located in the Integrated Flight AUX and STBY titles in white fonts to show the load and temperature of the Cabinets (IFCs) to the Electronic Instruments System (EIS). main, auxiliary and standby batteries. The MFD1 and MFD2 reversion switches located on the ESID Control Panel Battery Load Indication: The battery load indication shows the battery load in (ESCP) are used to select the electrical page on the multi−functional displays. white numbers. The numbers show the battery output load as a percentage of the total rated output. A + symbol before the numbers is used to show an overload condition of the battery. The symbol is out of view when the load is less than 100% REV 2.0 20 Sep 2024 PAGE 12 COURSE Code TRAINING PURPOSE ONLY MAINTENANCE TRAINING ORGANISATION DHC-8-400 B1 & B2 TRAINING MANUAL A — symbol shows a discharge condition. Battery Temperature Indication: The battery temperature indication shows the battery temperature in degrees Celsius in white numbers. The indication changes to yellow when temperature is more than 50 and less than 65 °C. If the temperature is more than 65 °C, the indication will change to red. FIGURE - EIS, BATTERY SYSTEM INDICATIONS REV 2.0 20 Sep 2024 PAGE 13 DGM12CBXX3Q4PW TRAINING PURPOSE ONLY MAINTENANCE TRAINING ORGANISATION DHC-8-400 B1 & B2 TRAINING MANUAL The battery system malfunctions are shown with the caution lights that follow: STBY BATT AUX BATT MAIN BATT The battery system malfunctions are shown with the warning lights that follow: STBY BATT HOT AUX BATT HOT MAIN BATT HOT STBY BATT, AUX BATT, MAIN BATT Caution Lights: The STBY BATT, AUX BATT or MAIN BATT caution light comes on to show that the battery is not connected to its main feeder bus for charging. STBY BATT HOT, AUX BATT HOT, MAIN BATT HOT Warning Lights: The STBY BATT HOT, AUX BATT HOT or MAIN BATT HOT warning light comes on to show that the battery temperature is more than 71 °C. It goes out when the temperature is less than 63 °C. FIGURE - CAUTION AND WARNING PANEL, BATTERY SYSTEM WARNING AND CAUTION INDICATIONS REV 2.0 20 Sep 2024 PAGE 14 DGM12CBXX3Q4PW TRAINING PURPOSE ONLY MAINTENANCE TRAINING ORGANISATION DHC-8-400 B1 & B2 TRAINING MANUAL Main and Auxiliary Batteries temperature switch is used to sense a temperature exceedance for a warning Figure - Main, Auxiliary and Standby Batteries indication. The main and auxiliary batteries are self-contained power sources that operate in the charge and discharge modes. The internal sensor wires are routed through a circular connector attached to the battery case. The main 28 Vdc generation system supplies electrical power to the battery during the charge mode. The amount of charge current is determined by the The left lower nose compartment door must be opened to access the batteries. state of charge and the internal resistance of the battery. After a long discharge The battery is secured to the airframe in the nose compartment by tabs that are period, the initial charge current can peak at 200 A. The current rapidly part of the battery case cover. The case is a steel box with a removable cover to decreases as the battery starts to charge. gain access for inspection. It also has a vent port that attaches to a tube that routes the gas overboard through a containment vessel. During the discharge mode, the battery supplies electrical power. The battery output voltage decreases as the current load increases. On aircraft without ModSum 4−309299 incorporated, the batteries are 40 A hour batteries with an assembly of individual cells contained in a steel case. The 40 A hour batteries have a rated discharge of 40A for one hour. The Each cell is connected in series to make 24 Vdc at the terminals. Solid copper discharge rate is not linear. The capacity is usually less than the rated value bus bars are used to connect the cells. when the discharge current is more than the nominal value. Standby Battery NOTE The Standby battery is a self-contained power source that operates in charge The voltage at the battery terminals cannot be used as an indication of the and the discharge modes. battery state of charge. The main 28 Vdc generation system supplies electrical power to the battery The battery has nickel and cadmium (NiCad) plates with potassium hydroxide during the charge mode. The amount of charge current is determined by the electrolyte. The NiCad battery has relatively constant voltage for most of the state of charge and the internal resistance of the battery. After a long discharge discharge condition. period, the initial charge current can peak at 200A. The current rapidly decreases as the battery starts to charge. A main power positive and negative electrical connection to the battery terminals is made with a power plug connector attached to the case. During the discharge mode, the battery supplies electrical power. The battery output voltage decreases as the current load increases. The batteries have two independent internal sensors that sense battery temperature. A Resistive Temperature Device (RTD) thermal sensor is used to measure the battery temperature for an EIS indication and a bi−metallic REV 2.0 20 Sep 2024 PAGE 15 DGM12CBXX3Q4PW TRAINING PURPOSE ONLY MAINTENANCE TRAINING ORGANISATION DHC-8-400 MAINTENANCE TRAINING MANUAL The 17A hour batteries have a rated discharge of 17A for one hour. The vessel. discharge rate is not linear. The capacity is usually less than the rated value when the discharge current is more than the nominal value. NOTE The voltage at the battery terminals cannot be used as an indication of the battery state of charge. The battery has nickel and cadmium (NiCad) plates with potassium hydroxide electrolyte. The NiCad battery has relatively constant voltage for most of the discharge condition. A main power positive and negative electrical connection to the battery terminals is made with a power plug connector attached to the case. The battery has two independent internal sensors that sense battery temperature. A Resistive Temperature Device (RTD) thermal sensor is used to measure the battery temperature for an EIS indication and a bi−metallic temperature switch is used to sense a temperature exceedance for a warning indication. The internal sensor wires are routed through a circular connector attached to the battery case. On the aircraft without ModSum 4−309300 incorporated, the battery is a 17 or 40A hour battery with an assembly of individual cells contained in a steel case. Each cell is connected in series to make 24 Vdc at the terminals. Solid copper bus bars are used to connect the cells. If the aircraft has a 17 A hour or 40 A hour or 43 A hour standby battery installed with Auxiliary Power Unit (APU), it is located in the forward fuselage nose compartment. The left upper nose compartment door must be opened to access the battery. The battery is secured to the airframe in the nose compartment by tabs that are part of the battery case cover. The case is a steel box with a removable cover to gain access for inspection. It also has a vent port that attaches to a tube that route the gases overboard through a containment REV 2.0 20 Sep 2024 PAGE 16 COURSE Code TRAINING PURPOSE ONLY MAINTENANCE TRAINING ORGANISATION DHC-8-400 B1 & B2 TRAINING MANUAL FIGURE - OPERATION- MANUAL CONTROL OF BATTERY CONTRACTORS REV 2.0 20 Sep 2024 PAGE 17 DGM12CBXX3Q4PW TRAINING PURPOSE ONLY MAINTENANCE TRAINING ORGANISATION DHC-8-400 B1 & B2 TRAINING MANUAL A DC CONTROL PANEL AUX BATTERY toggle switch selection connects For manual control of the battery contactors, the battery has the interfaces that the AUX BATTERY to the BATT PWR BUS in the LEFT DC CBP through the follow: DC CONTACTOR BOX, toggle switch, and diode CR21. Refer Figure - Operation- Manual Control of Battery Contractors The STANDBY BATTERY energizes the 28 VDC BATT (PWR) BUS in the RIGHT DCCBP through the STANDBY CONTACTOR BOX. A DC CONTROL PANEL MASTER BATTERY toggle switch selection energizes BATT MASTER RELAY 3-K4, K4 BATTERY BUS CONTACTOR, K3 BATTERY BUS CONTACTOR, and K24 ESSENTIAL BUS CONTACTOR. When BATT MASTER RELAY 3-K4 is energized, a DC CONTROL PANEL MAIN BATTERY toggle switch selection energizes K8 BATTERY BUS TIE CONTACTOR through the toggle switch, BATT MASTER RELAY 3-K4 and [K8 FS SRC] and [K8 RTN] of the EPCU. When BATT MASTER RELAY 3-K4 is energized, a DC CONTROL PANEL AUX BATTERY toggle switch selection energizes K7 BATTERY BUS TIE CONTACTOR through the toggle switch, BATT MASTER RELAY 3-K4 and [K7 FS SRC] and [K8 RTN] of the EPCU. When BATT MASTER RELAY 3-K4 is energized, a DC CONTROL PANEL STBY BATTERY toggle switch selection energizes K25 MAIN BUS CONTACTOR through the toggle switch, BATT MASTER RELAY 3-K4 and [STBY BATT CONTROL] and [K25 DRIVE] of the EPCU. A DC CONTROL PANEL MAIN BATTERY toggle switch selection connects the MAIN BATTERY to the BATT PWR BUS in the LEFT DC CBP through the DC CONTACTOR BOX, toggle switch, and diode CR20. REV 2.0 20 Sep 2024 PAGE 18 DGM12CBXX3Q4PW TRAINING PURPOSE ONLY MAINTENANCE TRAINING ORGANISATION DHC-8-400 B1 & B2 TRAINING MANUAL For indication, the battery system has the interfaces that follow: Refer Figure 24- 11 Operation- Battery System Indications A temperature switch in the MAIN BATTERY, AUX BATTERY, and STANDBY BATTERY closes when the battery is hot to supply a ground signal to the CAUTION AND WARNING PANEL. A resistive thermal device (RTD) in the MAIN BATTERY, AUX BATTERY, and STANDBY BATTERY supplies temperature readings to the EPCU. Auxiliary contacts in K8 BATTERY BUS TIE CONTACTOR, K7 BATTERY BUS TIE CONTACTOR, and K25 MAIN BUS CONTACTOR close when the contactor is de-energized to supply a ground signal to the CAUTION AND WARNING PANEL. REV 2.0 20 Sep 2024 PAGE 19 DGM12CBXX3Q4PW TRAINING PURPOSE ONLY MAINTENANCE TRAINING ORGANISATION DHC-8-400 B1 & B2 TRAINING MANUAL FIGURE - OPERATION- BATTERY SYSTEM INDICATIONS REV 2.0 20 Sep 2024 PAGE 20 DGM12CBXX3Q4PW TRAINING PURPOSE ONLY MAINTENANCE TRAINING ORGANISATION DHC-8-400 B1 & B2 TRAINING MANUAL Refer Figure - Operations-Emergency For emergency, the EPCU opens the circuit to the K8 BATTERY BUS TIE CONTACTOR, K7 BATTERY BUS TIE CONTACTOR, and K25 MAIN BUS CONTACTOR to de-energize the contactors. REV 2.0 20 Sep 2024 PAGE 21 DGM12CBXX3Q4PW TRAINING PURPOSE ONLY MAINTENANCE TRAINING ORGANISATION DHC-8-400 B1 & B2 TRAINING MANUAL FIGURE - OPERATIONS-EMERGENCY REV 2.0 20 Sep 2024 PAGE 22 DGM12CBXX3Q4PW TRAINING PURPOSE ONLY MAINTENANCE TRAINING ORGANISATION DHC-8-400 B1 & B2 TRAINING MANUAL Units, Electrical Power Control MAIN 28 VDC GENERATION SYSTEM Panel, DC Control Units, DC Transformer Rectifier Introduction Boxes, DC Contactor Contactors, DC Contactor Box The main 28 Vdc generation system makes and supplies 28 Vdc electrical power Box, Standby Contactor to the aircraft DC busses. Transformers, DC Current Shunts, Current General Description Refer Figure - Main 28V DC Generation System Block Refer Figure - Main 28 Vdc Generation System Block Diagram, Indication The main 28 Vdc generation system has two dc starter/generators, one on each engine, and two Transformer Rectifier Units (TRUs) to supply electrical power independently to the left and right DC bus systems. When a DC starter/generator or TRU malfunctions, the main 28 Vdc generation system automatically connects its bus to another serviceable electrical source for continuous operation. A DC external power receptacle and control circuitry allows the system to be powered from an external power source while the aircraft is on the ground. Toggle switches on the DC control panel in the flight compartment give manual control of the main 28 Vdc generation system. The Engine and System Integrated Display (ESID) system shows main 28 Vdc generation system electrical indications. The Main 28 Vdc Generation System has the components that follow: Starter/Generators, DC Units, DC Generator Control REV 2.0 20 Sep 2024 PAGE 23 DGM12CBXX3Q4PW TRAINING PURPOSE ONLY MAINTENANCE TRAINING ORGANISATION DHC-8-400 MAINTENANCE TRAINING MANUAL FIGURE - MAIN 28V DC GENERATION SYSTEM BLOCK DIAGRAM, CONTROLS REV 2.0 20 Sep 2024 PAGE 24 COURSE Code TRAINING PURPOSE ONLY MAINTENANCE TRAINING ORGANISATION DHC-8-400 B1 & B2 TRAINING MANUAL FIGURE - MAIN 28 VDC GENERATION SYSTEM BLOCK DIAGRAM, INDICATION REV 2.0 20 Sep 2024 PAGE 25 DGM12CBXX3Q4PW TRAINING PURPOSE ONLY MAINTENANCE TRAINING ORGANISATION DHC-8-400 B1 & B2 TRAINING MANUAL Detailed Description K21 to move to a cross−tie position to connect its main feeder bus to the other DC starter/generator. The direct current (DC) system operates in the modes that follow: When the main feeder bus tie toggle switch on the DC control panel is set to the Normal MAIN BUS TIE position, the main feeder busses are manually connected Protection together through main feeder bus tie contactor, K21. Fault Tolerant Emergency The two DC generators supply 28 Vdc electrical power through the bus Diagnostics and Monitoring. contactors, K1 and K2 to their related left or right main feeder bus. When the DC GCU senses a DC starter/generator malfunction, it will cause the bus Refer Figure - Main 28 Vdc Generation System Operation contactor, K1 or K2 to open the circuit of the DC starter/generator source. Normal Function: The DC electrical power from DC starter/generators and DC current transformers at the negative (−) and positive (+) connections of the Transformer Rectifier Units (TRUs) is supplied to the DC busses through a DC DC starter/generator supply current data to the DC GCUs to control the DC contactor box located in the nose compartment of the aircraft. The contactor starter/generator’s output. Current shunts at the “−“connection of the DC box contains the switching, protection, and measurement components. starter/generators supply current data to the EPCU for indication. When the aircraft engines are operating with no external DC power connected, The TRU electrical power is supplied to the DC secondary distribution busses in and the DC generator toggle switches on the DC control are set to GEN 1 or GEN the flight compartment through the secondary feeder busses located in the DC 2 positions, the DC generators are connected to their related main feeder contactor box. busses for normal operation. The related DC GCU automatically disconnects its DC starter/generator when it senses a DC starter/generator malfunction. When the EPCU senses a TRU malfunction, it will cause the secondary feeder bus tie contactor, K22 to move to a cross−tie position to connect its secondary Each DC starter/generator is turned by the engine auxiliary gearbox. The DC feeder bus to the other TRU. starter/generator is controlled by its related DC Generator Control Unit (GCU). Current shunts at the “−” connection of the TRUs supply current data to the Each DC GCU automatically controls the operation of its DC starter/generator EPCU for indication. by monitoring output voltage, current, and speed. After an engine start, the DC GCU controls its generator output and controls the operation of its bus contactor K1 or K2. When the Electrical Power Control Unit (EPCU) senses a DC starter/generator malfunction, it will cause the main feeder bus tie contactor, REV 2.0 20 Sep 2024 PAGE 26 DGM12CBXX3Q4PW TRAINING PURPOSE ONLY MAINTENANCE TRAINING ORGANISATION DHC-8-400 MAINTENANCE TRAINING MANUAL FIGURE - MAIN 28 VDC GENERATION SYSTEM OPERATION REV 2.0 20 Sep 2024 PAGE 27 COURSE Code TRAINING PURPOSE ONLY MAINTENANCE TRAINING ORGANISATION DHC-8-400 B1 & B2 TRAINING MANUAL Figure - Main 28 Vdc Generation System, External Power Operation The input from an external DC power source is selected from the flight compartment. When the DC external power toggle switch located on the DC control panel is set to EXT PWR, the DC external power source is connected to the main, essential, and secondary DC busses. The DC external power condition is sensed by the EPCU and it operates as follows: The external power contactor K9 connects the dc external power source to the left main bus The main bus tie contactor K21 connects the left main feeder bus to the right main feeder bus The secondary/main feeder bus contactors, K5 and K6 connect the secondary feeder busses to the main feeder busses. An inhibit signal is sent from the EPCU to the DC GCUs to open the bus contactors K1, K2 and to de−energize the DC starter/generator while external power is selected. REV 2.0 20 Sep 2024 PAGE 28 DGM12CBXX3Q4PW TRAINING PURPOSE ONLY MAINTENANCE TRAINING ORGANISATION DHC-8-400 B1 & B2 TRAINING MANUAL FIGURE - MAIN 28 VDC GENERATION SYSTEM, EXTERNAL POWER OPERATION REV 2.0 20 Sep 2024 PAGE 29 DGM12CBXX3Q4PW TRAINING PURPOSE ONLY MAINTENANCE TRAINING ORGANISATION DHC-8-400 B1 & B2 TRAINING MANUAL The DC electrical power is supplied to the DC distribution busses through a DC and voltage are stable. The DC GCU controls the contactors to supply DC contactor box in the nose compartment of the aircraft. The DC starter/generator power to the aircraft busses. The DC GCU also monitors the starter/generator electrical power is supplied to the main distribution busses in DC starter/generator current and controls its bus contactor. the flight compartment through the main feeder busses and the generator bus contactors, K1 and K2 located in the DC contactor box. The main distribution The EPCU automatically controls the main 28 Vdc generating system. Toggle busses supply their related essential distribution busses through isolation switches in the flight compartment are used to control the main 28 Vdc diodes, CR3 and CR2. The isolation diodes make sure that the left and right main generating system when the EPCU malfunctions. distribution busses energize their related essential distribution busses and that the essential distribution busses cannot energize the main feeder busses. When electrical power is not available from the main feeder busses, the essential busses are energized by the standby, auxiliary, and main batteries through battery bus contactors K24, K3, and K4, and isolation diodes, CR8, CR5 and CR4. NOTE The left and right essential distribution busses are connected together through circuit breakers on each essential distribution bus. When the DC GCU senses a DC starter/generator malfunction, it will cause the bus contactor, K1 or K2 to open circuit the DC starter/generator. A fault signal is sent to the EPCU to cause the main bus tie contactor, K21 to connect the bus to the other DC starter/generator. The TRU electrical power is supplied to the secondary distribution busses in the flight compartment through the main feeder busses in the DC contactor box. When the EPCU senses a TRU malfunction, it will cause its bus to connect to the FIGURE - DC CONTACTOR BOX other TRU through the secondary bus tie contactor, K22. Protection Function: The protective functions in the main 28 Vdc generation system prevent damage to the DC starter/generators, TRUs, or other related The DC GCUs sense their related DC starter/generators speed and voltage while equipment malfunctions, or there is an overload condition. the DC generator toggle switch is set to the DC GEN position. The DC GCU controls its DC starter/generator voltage when the DC starter/generator speed REV 2.0 20 Sep 2024 PAGE 30 DGM12CBXX3Q4PW TRAINING PURPOSE ONLY MAINTENANCE TRAINING ORGANISATION DHC-8-400 MAINTENANCE TRAINING MANUAL The main 28 Vdc generation system continuously monitors itself. When a fault Over Voltage: When the voltage from a DC starter/generator is more than 32.5 is sensed, it isolates the effect of the fault from the remaining system to allow ±0.5 VDC, its DC GCU de−energizes the DC starter/generator and opens its continued operation. related bus−tie contactor, K1 or K2. The EPCU connects its bus to the other DC starter/generator. This protection has an inverse time delay to make sure that The main 28 Vdc generation system protective functions are classified as the disconnect time is inversely proportional to the magnitude of the over passive protection and active protection. voltage level. The main 28 Vdc generation system uses circuit breakers and fuses for passive Over Current: When the current from the DC starter/generator is more than protection so that a malfunction condition will not cause damage to the DC 700 A for more than 5 seconds, the EPCU sends a trip signal to the related DC starter/generator and TRUs. The circuit breakers and fuses are protection GCU to de−energize its DC starter/generator and open its related bus−tie devices that open circuit during excessive current flow. Unlike fuses, circuit contactor, K1 or K2. If the EPCU does not supply a trip signal to the DC GCU, the breakers can be reset without having to be replaced. DC GCU de−energizes its DC starter/generator and opens its related bus−tie contactor, K1 or K2 after 7 seconds. The DC starter/generator will supply current Circuit breakers in the DC contactor box are thermally compensated for an for a maximum of 7 seconds to let the fault clear itself before disconnecting the operating temperature range of −55° C to +71° C. Each circuit breaker current DC starter/generator. The EPCU does not connect its bus to the other generator. rating is dependent on the circuit that it protects. NOTE Fuses are used in the DC Contactor Box (DCCB) to protect the environment A current limit signal is supplied to the DC GCU to limit its DC cooling system fan power, and the secondary bus cross−tie and contactor K22. starter/generator’s output current at 400 A during an opposite engine start condition. The main 28 Vdc generation system uses its DC GCUs and EPCU to control the contactors for active protection so that a fault condition will not cause damage Differential Feeder Protection: The current flow at “−” and “+” connections of to the DC starter/generators and TRUs. It uses the protective functions that the DC starter/generator is compared by the DC GCU differential current follow: sensing circuits. When the differential feeder current is more than 75 A, the DC GCU de−energizes its related DC starter/generator and opens its related bus−tie Over voltage contactor, K1 or K2. Over current Differential feeder protection Build−up ground fault The EPCU connects its bus to the other DC starter/generator. Time delay circuits Reverse current in the DC GCU prevent usual transients caused by on and off switching of External power monitor different loads to cause contactor operation. TRU under voltage detection. DC current transformers at the “−” and “+” connections of the DC starter/generators supply DC current data to the DC GCUs to control the DC REV 2.0 20 Sep 2024 PAGE 31 COURSE Code TRAINING PURPOSE ONLY MAINTENANCE TRAINING ORGANISATION DHC-8-400 MAINTENANCE TRAINING MANUAL starter/generator’s output. Fault Tolerant: The EPCU monitors the main 28 Vdc generation system symptoms for active malfunctions. If a malfunction is sensed, the EPCU will send Reverse Current: The DC GCU monitors for a reverse current condition. When a the required signals to reconfigure the DC bus system. To protect the AC reverse current condition exceeds 10% of the rated load, the DC GCU generators, the alternating current variable frequency system monitors itself de−energizes its related DC starter/generator and opens its related bus−tie for the faults that follow: contactor, K1 or K2. The EPCU connects its bus to the other DC starter/generator. Source Bus. External Power Monitor: The EPCU makes sure that good DC external power is allowed to energize the DC busses. When source or bus faults occur, the contactors open, and stay open until the EPCU is reset to prevent a reconnection to a fault condition. The BUS FAULT The EPCU checks the external power source for the parameters that follow: toggle switch on the DC control panel is set to the RESET position and then back to OFF position. Refer Figure - Main 28 Vdc Generation System, Dc Starter/Generator No. 1 Source Fault Source Fault: Each DC starter/generator usually supplies its own main feeder bus. When a DC starter/generator or DC GCU malfunctions, its related bus contactor, K1 or K2 will open to disconnect the DC starter/generator. Its related main feeder bus is energized by the other DC starter/generator. The EPCU will cause the main feeder bus tie contactor, K21 to connect the busses. In this When the DC external power source is more than the permitted limits, the EPCU reconfigured condition, all aircraft loads stay energized. de−energizes the DC external power contactor K9. The DC external power contactor K9 opens the circuit between the left main feeder bus and the DC Refer Figure - Main 28 Vdc Generation System, Left TRU Source Fault external power source. Each TRU supplies its own secondary feeder bus. When a TRU malfunctions, its related secondary feeder bus is energized by the other TRU. The EPCU will cause TRU under Voltage Detection: If the TRU output voltage is less than 15 Vdc for the secondary feeder bus tie contactor, K22 to connect the busses. In this more than 7 seconds, the TRU is considered defective. reconfigured condition, all aircraft loads stay energized. The EPCU will cause the secondary bus cross−tie contactor, K22 to connect the two secondary feeder busses together. REV 2.0 20 Sep 2024 PAGE 32 COURSE Code TRAINING PURPOSE ONLY MAINTENANCE TRAINING ORGANISATION DHC-8-400 B1 & B2 TRAINING MANUAL. FIGURE - MAIN 28 VDC GENERATION SYSTEM, DC STARTER/GENERATOR NO. 1 SOURCE FAULT REV 2.0 20 Sep 2024 PAGE 33 DGM12CBXX3Q4PW TRAINING PURPOSE ONLY MAINTENANCE TRAINING ORGANISATION DHC-8-400 B1 & B2 TRAINING MANUAL FIGURE - MAIN 28 VDC GENERATION SYSTEM, LEFT TRU SOURCE FAULT REV 2.0 20 Sep 2024 PAGE 34 DGM12CBXX3Q4PW TRAINING PURPOSE ONLY MAINTENANCE TRAINING ORGANISATION DHC-8-400 B1 & B2 TRAINING MANUAL Refer Figure - Main 28 Vdc Generation System, Two Dc Starter/Generator Source Fault When the two DC starter/generator or DC GCU malfunction, their related bus contactors, K1 and K2 will open to disconnect the DC starter/generators. Their related main feeder bus will be energized by the related TRUs. The EPCU will cause the secondary/main feeder bus tie contactors, K5 and K6 to connect the busses. In this reconfigured condition, all aircraft loads stay energized. REV 2.0 20 Sep 2024 PAGE 35 DGM12CBXX3Q4PW TRAINING PURPOSE ONLY MAINTENANCE TRAINING ORGANISATION DHC-8-400 B1 & B2 TRAINING MANUAL FIGURE - MAIN 28 VDC GENERATION SYSTEM, TWO DC STARTER/GENERATOR SOURCE FAULT REV 2.0 20 Sep 2024 PAGE 36 DGM12CBXX3Q4PW TRAINING PURPOSE ONLY MAINTENANCE TRAINING ORGANISATION DHC-8-400 MAINTENANCE TRAINING MANUAL Refer Figure - Main 28 Vdc Generation System, Two TRU Source Fault When the two TRUs malfunction, their related secondary feeder bus will be energized by the related DC starter/generators. The EPCU will cause the secondary/main feeder bus tie contactors, K5 and K6 to connect the busses. In this reconfigured condition, all aircraft loads stay energized. REV 2.0 20 Sep 2024 PAGE 37 COURSE Code TRAINING PURPOSE ONLY MAINTENANCE TRAINING ORGANISATION DHC-8-400 B1 & B2 TRAINING MANUAL FIGURE - MAIN 28 VDC GENERATION SYSTEM, TWO TRU SOURCE FAULT REV 2.0 20 Sep 2024 PAGE 38 DGM12CBXX3Q4PW TRAINING PURPOSE ONLY MAINTENANCE TRAINING ORGANISATION DHC-8-400 B1 & B2 TRAINING MANUAL Refer Figure - Main 28 Vdc Generation System, Dc Starter/Generator No. 1 and Left TRU Source Fault When one DC starter/generator or DC GCU and one TRU malfunction, the related bus contactors, K1 or K2 will open to disconnect the DC starter/generator. Its related main feeder bus will be energized by the other DC starter/generator. The EPCU will cause the main feeder bus tie contactor, K21 to connect the busses. When a TRU malfunctions, its related secondary feeder bus will be energized by the other TRU. The EPCU will cause the secondary feeder bus tie contactor, K22 to connect the busses. In this reconfigured condition, all aircraft loads stay energized. REV 2.0 20 Sep 2024 PAGE 39 DGM12CBXX3Q4PW TRAINING PURPOSE ONLY MAINTENANCE TRAINING ORGANISATION DHC-8-400 MAINTENANCE TRAINING MANUAL FIGURE - MAIN 28 VDC GENERATION SYSTEM, DC STARTER/GENERATOR NO. 1 AND LEFT TRU SOURCE FAULT REV 2.0 20 Sep 2024 PAGE 40 COURSE Code TRAINING PURPOSE ONLY MAINTENANCE TRAINING ORGANISATION DHC-8-400 MAINTENANCE TRAINING MANUAL Refer Figure - Main 28 Vdc Generation System, Dc Starter/Generator No. 1 and Two TRU Source Fault When one DC starter/generator or DC GCU and two TRUs malfunction, the related bus contactors, K1 or K2 will open to disconnect the DC starter/generator. Its related main feeder bus will be energized by the other DC starter/generator. The EPCU will cause the main feeder bus tie contactor, K21 to connect the busses. In this reconfigured condition, the secondary feeder busses are not energized. The main and essential aircraft loads stay energized. REV 2.0 20 Sep 2024 PAGE 41 COURSE Code TRAINING PURPOSE ONLY MAINTENANCE TRAINING ORGANISATION DHC-8-400 MAINTENANCE TRAINING MANUAL FIGURE - MAIN 28 VDC GENERATION SYSTEM, DC STARTER/GENERATOR NO. 1 AND TWO TRU SOURCE FAULT REV 2.0 20 Sep 2024 PAGE 42 COURSE Code TRAINING PURPOSE ONLY MAINTENANCE TRAINING ORGANISATION DHC-8-400 MAINTENANCE TRAINING MANUAL Refer Figure - Main 28 Vdc Generation System, Two Dc Starter/Generator And Two TRU Source Fault When two DC starter/generators or DC GCUs and two TRUs malfunction, the related bus contactors, K1 or K2 will open to disconnect the DC starter/generator. The EPCU will cause the contactors, K7, K8, and K25 to disconnect the busses. In this reconfigured condition, the secondary feeder busses and main feeder busses are not energized. The essential aircraft loads stay energized. Bus Fault: The EPCU and the DC GCUs sense bus faults and reconfigure the main 28 Vdc generation system to make sure that the main feeder busses and secondary feeder busses are protected. The DC GCU uses the interpole voltage to sense an overcurrent condition of the DC starter/generator. The interpole series winding voltage in a DC starter/generator changes in relation to the load current of the generator. When the DC GCU senses an interpole voltage level that is more than twice the usual level, an overcurrent signal is sent to the EPCU. REV 2.0 20 Sep 2024 PAGE 43 COURSE Code TRAINING PURPOSE ONLY MAINTENANCE TRAINING ORGANISATION DHC-8-400 MAINTENANCE TRAINING MANUAL FIGURE - MAIN 28 VDC GENERATION SYSTEM, TWO DC STARTER/GENERATOR AND TWO TRU SOURCE FAULT REV 2.0 20 Sep 2024 PAGE 44 COURSE Code TRAINING PURPOSE ONLY MAINTENANCE TRAINING ORGANISATION DHC-8-400 B1 & B2 TRAINING MANUAL Refer Figure - Main 28 Vdc Generation System, Left Main Feeder Bus Fault With two DC starter/generators and two TRUs available, the EPCU locks out the main feeder bus tie contactor, K21 one second after an over current condition is sensed. The secondary/main feeder bus tie contactors, K5 and K6 are locked out 100 ms later. If the over current condition continues for more than 5 seconds, the EPCU sends a trip signal to the DC GCU. The related bus contactor, K1 or K2 will open to disconnect the DC starter/generator. The EPCU also causes contactors, K25 and K7 or K8 to open to disconnect the standby and auxiliary batteries or the main battery from the main feeder bus. REV 2.0 20 Sep 2024 PAGE 45 DGM12CBXX3Q4PW TRAINING PURPOSE ONLY MAINTENANCE TRAINING ORGANISATION DHC-8-400 B1 & B2 TRAINING MANUAL FIGURE - MAIN 28 VDC GENERATION SYSTEM, LEFT MAIN FEEDER BUS FAULT REV 2.0 20 Sep 2024 PAGE 46 DGM12CBXX3Q4PW TRAINING PURPOSE ONLY MAINTENANCE TRAINING ORGANISATION DHC-8-400 MAINTENANCE TRAINING MANUAL Refer Figure - Main 28 VDC Generation System, DC Starter/Generator No. 1 Source and Main Feeder Bus Faults With one DC starter/generator energizing the left and right main feeder busses and an over current condition is sensed for more than one second, the EPCU causes the main feeder bus tie contactor, K21 to open. If the over current condition continues, within seven seconds, the EPCU sends a trip signal to the DC GCU. The related bus contactor, K1 or K2 will open to disconnect the online DC starter/generator from the faulty bus. The EPCU also causes the shorted bus side battery contactors K8, or K25 and K7 to open, to disconnect the main battery or the standby and auxiliary batteries from the main feeder bus. The contactor K22 will close to tie the secondary busses and the contactor K5 or K6 closes to energize the remaining main bus. NOTE The contactor K22 will get closed to prevent overloading of one TRU. It is necessary for both the TRUs to be serviceable for this scenario to work. REV 2.0 20 Sep 2024 PAGE 47 COURSE Code TRAINING PURPOSE ONLY MAINTENANCE TRAINING ORGANISATION DHC-8-400 B1 & B2 TRAINING MANUAL FIGURE - MAIN 28 VDC GENERATION SYSTEM, DC STARTER/GENERATOR NO. 1 SOURCE AND MAIN FEEDER BUS FAULTS REV 2.0 20 Sep 2024 PAGE 48 DGM12CBXX3Q4PW TRAINING PURPOSE ONLY MAINTENANCE TRAINING ORGANISATION DHC-8-400 B1 & B2 TRAINING MANUAL Refer Figure - Main 28 Vdc Generation System, Dc Starter/Generator No. 1 Source And Main Feeder Bus Faults If the over current condition stops after the main feeder busses are isolated, the bus fault is on the other main feeder bus. After 200 milliseconds the EPCU causes contactors, K25 and K7 or K8 to open to disconnect the standby and auxiliary batteries or the main battery from the main feeder bus. REV 2.0 20 Sep 2024 PAGE 49 DGM12CBXX3Q4PW TRAINING PURPOSE ONLY MAINTENANCE TRAINING ORGANISATION DHC-8-400 MAINTENANCE TRAINING MANUAL FIGURE - MAIN 28 VDC GENERATION SYSTEM, DC STARTER/GENERATOR NO. 1 SOURCE AND MAIN FEEDER BUS FAULTS REV 2.0 20 Sep 2024 PAGE 50 COURSE Code TRAINING PURPOSE ONLY MAINTENANCE TRAINING ORGANISATION DHC-8-400 MAINTENANCE TRAINING MANUAL Refer Figure - Main 28 Vdc Generation System, Dc Starter/Generator No. 1 Source And Secondary Feeder Bus Faults An over current condition on a secondary feeder bus causes its related TRU circuit breaker to open. The EPCU then senses a TRU source fault and causes the secondary feeder bus tie contactor, K22 to close after 7 seconds. The high current condition causes the cross tie fuse that protects the other TRU from the effect of the bus fault to open. REV 2.0 20 Sep 2024 PAGE 51 COURSE Code TRAINING PURPOSE ONLY MAINTENANCE TRAINING ORGANISATION DHC-8-400 MAINTENANCE TRAINING MANUAL FIGURE - MAIN 28 VDC GENERATION SYSTEM, DC STARTER/GENERATOR NO. 1 SOURCE AND SECONDARY FEEDER BUS FAULTS REV 2.0 20 Sep 2024 PAGE 52 COURSE Code TRAINING PURPOSE ONLY MAINTENANCE TRAINING ORGANISATION DHC-8-400 MAINTENANCE TRAINING MANUAL Refer Figure - Main 28 Vdc Generation System, Two Dc Starter/Generator Source And Main Feeder Bus Faults An over current condition on a main feeder bus causes the TRU circuit breaker to open. The EPCU then senses a TRU source fault and causes the secondary feeder bus tie contactor, K22 to close after 7 seconds. The high current condition causes the cross tie fuse that protects the other TRU from the effect of the bus fault to open. After 100 milliseconds the EPCU causes the secondary/main feeder bus tie contactors, K5 and K6 to open. NOTE With one TRU operating, the main 28 Vdc generation system operates in the emergency mode. Contactors, K25, K7, and K8 open to disconnect the standby and auxiliary batteries or the main battery from the main feeder bus. The standby, auxiliary, and main batteries will supply the essential distribution busses only. REV 2.0 20 Sep 2024 PAGE 53 COURSE Code TRAINING PURPOSE ONLY MAINTENANCE TRAINING ORGANISATION DHC-8-400 MAINTENANCE TRAINING MANUAL FIGURE - MAIN 28 VDC GENERATION SYSTEM, TWO DC STARTER/GENERATOR SOURCE AND MAIN FEEDER BUS FAULTS REV 2.0 20 Sep 2024 PAGE 54 COURSE Code TRAINING PURPOSE ONLY MAINTENANCE TRAINING ORGANISATION DHC-8-400 MAINTENANCE TRAINING MANUAL Refer Figure - Main 28 Vdc Generation System, Two TRU Source And Secondary Feeder Bus Faults An over current condition on a secondary feeder bus causes the TRU circuit breaker to open. After 1 second the EPCU causes the secondary/main feeder bus tie contactors, K5 and K6 to open to isolate the bus fault. REV 2.0 20 Sep 2024 PAGE 55 COURSE Code TRAINING PURPOSE ONLY MAINTENANCE TRAINING ORGANISATION DHC-8-400 MAINTENANCE TRAINING MANUAL FIGURE - MAIN 28 VDC GENERATION SYSTEM, TWO TRU SOURCE AND SECONDARY FEEDER BUS FAULTS REV 2.0 20 Sep 2024 PAGE 56 COURSE Code TRAINING PURPOSE ONLY MAINTENANCE TRAINING ORGANISATION DHC-8-400 MAINTENANCE TRAINING MANUAL Refer Figure - Main 28 Vdc Generation System, Reconfiguration Logic for Source Malfunctions The main 28 Vdc generation system reconfiguration logic for source malfunctions is summarized. FIGURE - MAIN 28 VDC GENERATION SYSTEM, RECONFIGURATION LOGIC FOR SOURCE MALFUNCTIONS REV 2.0 20 Sep 2024 PAGE 57 COURSE Code TRAINING PURPOSE ONLY MAINTENANCE TRAINING ORGANISATION DHC-8-400 B1 & B2 TRAINING MANUAL Emergency Mode: The main 28 Vdc generation system operates in the shows that no fault conditions sensed by the CBIT. When the indication is out emergency mode when the two main feeder busses are disconnected from all of view, the FAULT REVIEW push−button switch is pushed to do a display test. DC power sources caused by source or bus fault conditions. Contactors, K25, K7, It will show “88” for correct operation. and K8 open to disconnect the standby and auxiliary batteries or the main battery from the main feeder bus. The standby, auxiliary, and main batteries Three seconds after the display test indication or after the FAULT REVIEW will supply the essential distribution busses only. push−button switch is pushed again and there are fault codes recorded, the EPCU will show the first fault code recorded. The emergency mode is caused by the conditions that follow: The EPCU display shows codes 01 through 37 for faults that are sensed by the Electrical power is not available from the two DC starter/generators CBIT. The FAULT REVIEW push−button switch on the face of the EPCU is Electrical power is not available from one or two TRUs, and pushed again to access more recorded fault codes. A “99” indications shows The aircraft is in flight. that there are no more fault codes. If the FAULT REVIEW push−button switch is pushed again, the EPCU will show the first fault code that was recorded. When a source or bus fault occurs, the main 28 Vdc generation system reconfigures, and stays reconfigured until the EPCU is reset by a main bus tie toggle switch selection. This feature is known as anti−cycling. Diagnostics and Monitoring: The electrical power system uses an on condition monitoring and diagnostic system. The system operational status is monitored by flight compartment indications, DC GCU, EPCU functions. The DC Generator Control Units (GCUs) and EPCU give continuous monitoring of subsystem operation. The integrity of the protective functions in the DC GCU is checked by an Initiated Built In Test (IBIT) function in the EPCU so that other components are not affected by a defective test circuit. The Electrical Power Control Unit (EPCU) records main 28 Vdc generation system fault conditions. It has an interface panel on its front face to look at the fault codes that represent fault conditions sensed by the Continuous Built in Test (CBIT). It uses FAULT REVIEW and CLEAR push−button switches and a digital display to show the fault codes. The CBIT operates only when the aircraft is on the ground. A blank indication FIGURE - EPCU LOCATION, EPCU FRONT PANEL REV 2.0 20 Sep 2024 PAGE 58 DGM12CBXX3Q4PW TRAINING PURPOSE ONLY MAINTENANCE TRAINING ORGANISATION DHC-8-400 MAINTENANCE TRAINING MANUAL Refer Figure - Main 28 VDC Generation System, DC Control Panel Refer Figure - EIS, Electrical System Page Selection When the aircraft engines are operating with no external AC and DC power The MFD1 and MFD2 reversion switches located on the ESID Control Panel connected, and the DC starter/generator toggle switches located on the DC (ESCP) are used to set the electrical page on the multi−functional displays. control panel are set to GEN 1 and GEN 2, the DC starter/generators are connected to their related DC main feeder busses for operation. The DC starter/generator toggle switches are set to the OFF position to de−energize the DC generators and reset latched functions in the DC GCU. The bus fault toggle switch is set to BUS FAULT RESET position to reset latched functions in the EPCU. The Electrical Power Control Unit (EPCU) supplies indication data through the two Input/Output Processors (IOP1, IOP2) located in the Integrated Flight Cabinets (IFCs) to the Electronic Instruments System (EIS). FIGURE - EIS, ELECTRICAL SYSTEM PAGE SELECTION Refer Figure - EIS Main 28 VDC Generation System Indications The electrical page shows the DC starter/generator indications that follow: Digital indication of the DC essential, main, and secondary bus voltages FIGURE - MAIN 28 VDC GENERATION SYSTEM, DC CONTROL PANEL Digital indication of DC starter/generator loads Digital indication of TRU loads. REV 2.0 20 Sep 2024 PAGE 59 COURSE Code TRAINING PURPOSE ONLY MAINTENANCE TRAINING ORGANISATION DHC-8-400 MAINTENANCE TRAINING MANUAL The DC voltage indication has a DC BUS L and DC BUS R title in white fonts to show the voltage of the essential, main, and secondary busses. The DC load indication has a DC GEN1 and DC GEN2 title in white fonts to show the load of the DC starter/generators and it has a TRU1 and TRU2 title in white fonts to show the load of the TRUs. DC Voltage Indication: The DC voltage indication shows the DC essential, main, and secondary bus voltage in white numbers. DC Starter/Generator and TRU Load Indication: The DC starter/generator load indication shows the DC starter/generator output load. The numbers show the DC starter/generator output load as a percentage of the total rated output. A 1.00 indication is used to show 100%. A “+” symbol before the numbers is used to show an overload condition of the DC starter/generator or TRU. It is out of view when the load is in less than 100%. When the voltage or load data malfunctions, the digits are replaced by white dashes. FIGURE - EIS MAIN 28 VDC GENERATION SYSTEM INDICATIONS REV 2.0 20 Sep 2024 PAGE 60 COURSE Code TRAINING PURPOSE ONLY MAINTENANCE TRAINING ORGANISATION DHC-8-400 B1 & B2 TRAINING MANUAL more than 330° F. It goes out when the temperature is less than 300 °F (149 °C). Refer Figure 24- 36 Main 28V DC System Caution Lights L TRU HOT, R TRU HOT Caution Light: The L TRU HOT or L TRU HOT caution light The main 28 Vdc generation system malfunctions are shown with the caution comes on to show that the generator temperature is more than 160 °F (71.1 °C) lights that follow: and goes out when the temperature is less than 155 °F (68 °C). #1 DC GEN #2 DC GEN L TRU The left main and right main busses supply electrical power through 5 A circuit R TRU breakers to the related AC Generator Control Units (GCUs). The circuit breakers DC BUS are located in position D7 on the left circuit breaker panel and P7 on the right #1 DC GEN HOT circuit breaker panel. #2 DC GEN HOT L TRU HOT The left essential bus supplies electrical power through a 5 A circuit breaker to R TRU HOT. connector J1 of the EPCU. The circuit breaker is located in position G10 on the left circuit breaker panel. #1 DC GEN, #2 DC GEN Caution Light: The #1 DC GEN or #2 DC GEN caution light comes on to show that the generator is not connected to its bus because of a The right essential bus also supplies electrical power through a 5 A circuit source fault condition, the DC starter/generator toggle switches are set to the breaker to connector J2 of the EPCU. The circuit breaker is located in position OFF position, or external DC power is energizing the left and right main feeder H10 on the right circuit breaker panel. busses. The Proximity Sensor Electronics Unit (PSEU) supplies a Weight On Wheels L TRU, R TRU Caution Light: The L TRU or R TRU caution light comes on to show (WOW) signal to the EPCU. that the a secondary feeder bus is not energized by its related TRU because of a source fault condition or the AC generator toggle switches are set to the OFF position. DC BUS Caution Light: The DC BUS caution light comes on to show that the EPCU has reconfigured the main 28 Vdc generation system because of a source or bus fault condition. If the bus fault is reset, the indication will go out. #1 DC GEN HOT, #2 DC GEN HOT Caution Light: The #1 DC GEN HOT or #2 DC GEN HOT caution light comes on to show that the generator temperature is REV 2.0 20 Sep 2024 PAGE 61 DGM12CBXX3Q4PW TRAINING PURPOSE ONLY FIGURE 24- 3 MAIN 28V DC SYSTEM CAUTION LIGHTS MAINTENANCE TRAINING ORGANISATION DHC-8-400 B1 & B2 TRAINING MANUAL Figure 24- 4Operation - Voltage Regulation FIGURE - OPERATION - VOLTAGE REGULATION REV 2.0 20 Sep 2024 PAGE 62 DGM12CBXX3Q4PW TRAINING PURPOSE ONLY MAINTENANCE TRAINING ORGANISATION DHC-8-400 B1 & B2 TRAINING MANUAL BOX to supply 28 VDC through circuit breaker K8 (DC GEN 1 EXCITE) of the L ESS Refer Figure - Operation - Voltage Regulation BUS, RELAY 1, to [ESS BUS PWR] of the No.1 DC GENERATOR CONTROL UNIT to For voltage regulation, the main 28 VDC generation system has the interfaces energize the DC GCU. that follow: NOTE The [SPEED SENSE] and [SPEED SENSE RTN] signal from the No.1 DC RELAY 1 is also energized during a start of the No.1 or No.2 engine. GENERATOR is supplied to the No.1 DC GENERATOR CONTROL UNIT to stop the start cycle. 28 VDC [CONTR PWR OUT] from the No.1 DC GENERATOR CONTROL UNIT is supplied through the GEN1 toggle switch on the DC CONTROL PANEL back to the No.1 DC GENERATOR CONTROL UNIT for generator control [GEN CONT]. A generator output [GEN OUT] signal is also supplied through the GEN1 toggle switch and back for generator on [GEN ON]. If the GEN 1 toggle switch is set to the OFF position, the generator output [GEN OUT] is supplied back for generator reset [GEN RESET]. The + (28 VDC) output from the No.1 DC GENERATOR is supplied through circuit breaker CB23 on the DC CONTACTOR BOX to the [FIELD SUPPLY] of the No.1 DC GENERATOR CONTROL UNIT to energize the DC GCU. The + (28 VDC) output from the No.1 DC GENERATOR is supplied through circuit breaker CB25 on the DC CONTACTOR BOX to the [GEN SENSING] of the No.1 DC GENERATOR to control the generator field [GEN FIELD] output to the No.1 DC GENERATOR [FIELD]. K1 GENERATOR BUS CONTACTOR TIE energizes RELAY 1 in the DC CONTACTOR REV 2.0 20 Sep 2024 PAGE 63 DGM12CBXX3Q4PW TRAINING PURPOSE ONLY MAINTENANCE TRAINING ORGANISATION DHC-8-400 B1 & B2 TRAINING MANUAL FIGURE - OPERATION - CONTROL OF THE LINE CONTACTORS (SHEET 1 OF 2) REV 2.0 20 Sep 2024 PAGE 64 DGM12CBXX3Q4PW TRAINING PURPOSE ONLY MAINTENANCE TRAINING ORGANISATION DHC-8-400 B1 & B2 TRAINING MANUAL Refer Figure 24- 4Operation - Voltage Regulation For control and monitor of the line contactors, the main 28 VDC generation system has the interfaces that follow: A [K1 COIL] signal from the No.1 DC GENERATOR CONTROL UNIT is supplied to the K1 GENERATOR L BUS CONTACTOR to energize its coil. The [K1 STATUS] is supplied back through an auxiliary contact of K1 to the ELECTRICAL POWER CONTROL UNIT (EPCU) for CBIT. 28 VDC is supplied from the + output of the No.1 DC GENERATOR through K1 GENERATOR L BUS CONTACTOR to the L MAIN FEEDER BUS. 28 VDC is supplied from the + output of the L TRANSFORMER RECTIFYING UNIT (TRU) directly to L SEC FEEDER BUS. A [L TRU STATUS] signal is supplied to the EPCU for monitoring. 28 VDC is supplied through the circuit breaker J9 (LEFT BUS TIE) on the R ESS BUS, [K5 DRV SRC] and [K5 DRIVE] of the EPCU, to the K5 SECONDARY FEEDER BUS TIE CONTACTOR to energize its coil The [K5 STATUS] is supplied back through an auxiliary contact of K5 to the EPCU for CBIT. 28 VDC is supplied through the circuit breaker M8 (BUS FAULT RESET SW) on the L ESS BUS, the BUS FAULT RESET toggle on the DC CONTROL PANEL, to [RESET] of the EPCU. REV 2.0 20 Sep 2024 PAGE 65 DGM12CBXX3Q4PW TRAINING PURPOSE ONLY MAINTENANCE TRAINING ORGANISATION DHC-8-400 B1 & B2 TRAINING MANUAL FIGURE - OPERATION - CONTROL OF THE LINE CONTACTORS (SHEET 2 OF 2) REV 2.0 20 Sep 2024 PAGE 66 DGM12CBXX3Q4PW TRAINING PURPOSE ONLY MAINTENANCE TRAINING ORGANISATION DHC-8-400 B1 & B2 TRAINING MANUAL Refer Figure - Operation - Control of the Line Contactors (Sheet 2 of 2) 28 VDC is supplied through the circuit breaker H9 (SEC BUS TIE) on the R ESS BUS, [K22 DRV SRC] and [K22 DRIVE] of the EPCU, to the K22 SECONDARY FEEDER BUS TIE CONTACTOR to energize its coil. The [K22 STATUS] is supplied back to the EPCU for CBIT. 28 VDC is supplied through circuit breaker G8 (DC BUS TIE CONT) of the R ESS BUS, [K21 DRV SRC] and [K21 DRIVE] signal of the EPCU, to the K21 MAIN FEEDER BUS TIE CONTACTOR to energize its coil. The [K21 STATUS] is supplied back through an auxiliary contact of K21 to the ELECTRICAL POWER CONTROL UNIT (EPCU) for CBIT. If the K21 is closed, an [EQUALIZING BUS] signal from the No.1 DC GENERATOR CONTROL UNIT and No.2 DC GENERATOR CONTROL UNIT is connected together through K21. The main 28 VDC generation system has a K5, K6 fault (fail safe) circuit to continue to control the K5 and K6 SECONDARY FEEDER BUS TIE CONTACTORS if the EPCU malfunctions. 28 VDC is supplied from the + output of the No.1 DC GENERATOR, through CB31 on the DC CONTACTOR BOX, [K5/K6 FEED] and [K5/K6 FS] of the EPCU, K1 GENERATOR L BUS CONTACTOR, K2 GENERATOR R BUS CONTACTOR, K9 DC INTERNAL POWER CONTACTOR, K22 SECONDARY FEEDER BUS CONTACTOR, diode CR15, to the K5 SECONDARY FEEDER BUS TIE CONTACTOR to energize its coil. Then, the electrical power is supplied through K5 to energize the coil of K6. REV 2.0 20 Sep 2024 PAGE 67 DGM12CBXX3Q4PW TRAINING PURPOSE ONLY MAINTENANCE TRAINING ORGANISATION DHC-8-400 B1 & B2 TRAINING MANUAL FIGURE - OPERATION - PROTECTIVE FUNCTIONS REV 2.0 20 Sep 2024 PAGE 68 DGM12CBXX3Q4PW TRAINING PURPOSE ONLY MAINTENANCE TRAINING ORGANISATION DHC-8-400 B1 & B2 TRAINING MANUAL Refer Figure - Operation - Protective Functions For protection, the main 28 VDC generation system has the interfaces that follow: The + (28 VDC) output from the No.1 DC GENERATOR is supplied through K1 GENERATOR L BUS CONTACTOR, circuit breaker CB27 on the L MAIN FEEDER BUS in the DC CONTACTOR BOX to [BUS SENSING] of the No.1 DC GENERATOR CONTROL UNIT to monitor for overvoltage. The [INTERPOLE] voltage of the No.1 DC GENERATOR is supplied to the No.1 DC GENERATOR CONTROL UNIT to monitor for reverse current and a bus fault (overcurrent) Current transformer CT1 supplies a signal to [DIFF PROT RTN] of the No.1 DC GENERATOR CONTROL UNIT and CT3 supplies [DIFF PROT PWR] to monitor for a feeder fault. If a bus fault is sensed, the No.1 DC GENERATOR CONTROL UNIT will supply an [OVERCURRENT] signal to the ELECTRICAL POWER CONTROL UNIT to start a bus isolation sequence. If the bus fault continues, a [TRIP] signal is supplied back to the No.1 DC GENERATOR CONTROL UNIT to de-energize the No.1 DC GENERATOR and open the K1 GENERATOR L BUS CONTACTOR. If a source fault of the No.1 DC GENERATOR is sensed, the No.1 DC GENERATOR CONTROL UNIT will stop supplying a [PWR RDY] signal to [PWR RELAY] of the ELECTRICAL POWER CONTROL UNIT to start a reconfiguration of the line contactors. If a source fault of the L TRANSFORMER RECTIFYING UNIT is sensed, the L TRU will stop supplying a [TRU STATUS] signal to [L TRU STATUS] of the EPCU to start a reconfiguration of the line contactors. REV 2.0 20 Sep 2024 PAGE 69 DGM12CBXX3Q4PW TRAINING PURPOSE ONLY MAINTENANCE TRAINING ORGANISATION DHC-8-400 B1 & B2 TRAINING MANUAL FIGURE - OPERATION - VOLTAGE AND LOAD INDICATION REV 2.0 20 Sep 2024 PAGE 70 DGM12CBXX3Q4PW TRAINING PURPOSE ONLY MAINTENANCE TRAINING ORGANISATION DHC-8-400 B1 & B2 TRAINING MANUAL Refer Figure - Operation - Voltage and Load Indication For voltage and load indicator on the multifunctional display unit (MFD) ELECTRICAL system page, the main 28 VDC generation system has the interfaces that follow: The VOLT IND voltage of the 28 VDC L SEC BUS is monitored by the [L SEC] inputs of the electrical power control unit (EPCU) for voltage indication. The DC PWR MON voltage of the 28 VDC L ESS BUS is monitored by the [L ESS] inputs of the EPCU for voltage indication. The VOLT IND voltage of the 28 VDC L MAIN BUS is monitored by the [L MAIN] inputs of the EPCU for voltage indication. SHUNT R1 supplies a [SHUNT] and [SHUNT RTN] signal to the [SHUNT] and [SHUNT RTN] to the EPCU for load indication. [ARINC 429] AC variable frequency, main 28 VDC generation, and battery system indication data is supplied from the EPCU through IOP1 and IOP2 [ARINC 429] to the electronic instrument system (EIS) for indication. NOTE The No.1 part of the main 28 VDC generation system is described. The No.2 part is similar. REV 2.0 20 Sep 2024 PAGE 71 DGM12CBXX3Q4PW TRAINING PURPOSE ONLY MAINTENANCE TRAINING ORGANISATION DHC-8-400 B1 & B2 TRAINING MANUAL