EE 261 Asynchronous and DC Machines PDF
Document Details
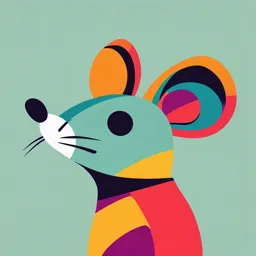
Uploaded by SweepingSugilite6768
Kwame Nkrumah University of Science and Technology
Ing. Francis Boafo Effah, PhD
Tags
Summary
These lecture notes cover DC machines, including their basics, types of connections, and operating characteristics. Topics include field windings, armature windings, commutators, and equivalent circuits. The document provides a general overview of the subject, focusing on foundational concepts.
Full Transcript
EE 261 ASYNCHRONOUS AND DC MACHINES Ing. Francis Boafo Effah, PhD Senior Lecturer Department of Electrical & Electronic Eng. Faculty of Computer & Electrical Eng. College of Engineering Room BKB 13, Bamfo Kwakye Building 1 Email: [email protected] UNIT 2 DC MACHINES...
EE 261 ASYNCHRONOUS AND DC MACHINES Ing. Francis Boafo Effah, PhD Senior Lecturer Department of Electrical & Electronic Eng. Faculty of Computer & Electrical Eng. College of Engineering Room BKB 13, Bamfo Kwakye Building 1 Email: [email protected] UNIT 2 DC MACHINES 2 DC Machines 1. Principles of operation 2. The commutator 3. Equivalent circuit 4. Winding connections 5. Operating characteristics 6. Torque and size 3 Basics (1) The DC machine, in its simplest form, has two windings: 1. Field winding:– generally on the stator of the machine. This provides the excitation flux, the “B” in the torque equation. This winding has a low-volt-amp product. 2. Armature winding:- generally on the rotor of the machine. This provides the “I” in the torque equation. The coils of the armature winding are connected to the machine’s terminals through a commutator. Current is transferred via carbon brushes. The commutator ensures orthogonal field and torque-producing currents in the armature winding. This winding has a high-volt-amp product and is responsible for energy conversion. 4 Basics (2) What is special about DC machines? 1. DC machines are the most straightforward electrical machines for understanding machine operations and modelling them mathematically. This helps us understand electrical machine operation concepts and is often used as the basis of AC electrical machine control – dq axis vector control. 2. The field current can be maintained constant for control purposes, consequently having a constant field. Torque is then directly proportional to the armature current. 3. In an ideal machine, we would want the field and armature currents to be independently controlled – the DC machine comes very close to this. 5 The Commutator (1) The commutator plays a very important role in DC machines as it ensures the correct direction of the current under each pole to produce a net positive torque. As the rotor with its armature winding rotates, the conductors in the slots move from being under one pole (say a north pole) to the next (which will then be a south pole) – and thus, the sign of B changes! Consequently, the current direction in the conductors must change so that the direction of force and torque remains the same. This process of changing the current direction is called COMMUTATION. 6 The Commutator (2) https://www.youtube.com/watch?v=Xi7o8cMPI0E 7 The Commutator (3) The currents in the conductor thus change direction in a very short interval when the brush on the commutator short-circuits the coil they are part of. The sudden change in current requires a very high di/dt, and as the coil is inductive, there will be a high associated 𝑣 = 𝐿𝑑𝑖/𝑑𝑡. The brush contact drop depends on the material; however, it is in the region of 1 V. Most times, this is neglected in calculations as it is very small compared to the voltage applied to the armature. We will look at commutation later on in the course. 8 Equivalent Circuit DC Machine Equivalent circuit DC Machine Equations 𝑑𝑖𝑎 𝑣𝑎 = 𝑅𝑎 𝑖𝑎 + 2𝑣𝑏 + 𝐿𝑎 + 𝐾𝑎 𝑖𝑓 𝜔𝑚 𝑑𝑡 𝑑𝑖𝑓 𝑣𝑓 = 𝑅𝑓 𝑖𝑓 + 𝐿𝑓 𝑑𝑡 𝑑𝑖 In steady state ( = 0) and 𝑑𝑡 neglecting brush voltage drop 𝑣𝑎 = 𝑅𝑎 𝑖𝑎 + 𝐾𝑎 𝑖𝑓 𝜔𝑚 𝑣𝑓 = 𝑅𝑓 𝑖𝑓 9 Winding Connections (1) Separately Excited Series connection Most common form DC or AC (Universal motor) – used for car starters and DC traction motors. Shunt connection The two circuits above are Compound connection connected to the same voltage This motor has two windings per source field coil pole. One is connected in Can be dangerous – see armature parallel with the armature, and the reaction effects later on other is connected in series. 10 Winding Connections (2) 11 Operating Characteristics (1) Mechanical power and electrical power conversion 𝐸𝑎 𝑖𝑎 = 𝑇𝑒 𝜔𝑚 = 𝐾𝑎 𝑖𝑓 𝜔𝑚 𝑇𝑒 = 𝐾𝑎 𝑖𝑓 𝑖𝑎 𝑣𝑎 = 𝐸𝑎 = 𝐾𝑎 𝑖𝑓 𝜔𝑚 Neglecting resistive and brush voltage drops 12 Operating Characteristics (2) Constant Torque or Constant Field Operation 𝑖𝑓 is kept constant once established Torque is then proportional to 𝑖𝑎 𝑣𝑎 must change directly with speed, ignoring the voltage drop in the winding resistance When 𝑖𝑓 is kept constant, the armature voltage increases with the motor speed up to a maximum speed. Operation from a fixed DC voltage source needs a means of limiting the current flow if the armature is connected directly to the supply when the speed is zero. 13 Operating Characteristics (3) Example: a 35 kW, 440 V machine will have: An armature current of approximately 83 A The armature resistance will be approximately 0.21 Ω The zero speed current for a direct-on-line start will be, therefore, 2100 A (dangerous) Ways of operation: Supplied from a controllable DC voltage source OR a variable series resistance is used for starting on a fixed DC supply (except for very small motors) 𝑣 𝑇𝑒 = 𝐾𝑎 𝑖𝑓 𝑖𝑎 𝜔𝑚 = 𝐾 𝑎𝑖 𝑎 𝑓 14 Operating Characteristics (4) Constant Power Region of Operation 𝑣𝑎 is held constant once it is established, 𝑖𝑎 has a maximum safe value, so power is constant. Increasing speed is obtained by REDUCING the field current. Torque then reduces as 𝑖𝑓 reduces. Mechanical power is, therefore, constant. Torque reduces in inverse proportion to speed increase. 15 Torque in a DC motor 16 Torque in a DC motor Definitions Torque developed by an electrical machine Physics of torque production in electrical machines Practical issues Copper versus Iron machines 17 Definitions Magnetic Loading The magnetic loading is the average airgap flux density over one pole: 𝐵𝑎𝑣𝑔. Electrical Loading The electrical loading is defined as the total effective (RMS) current in the machine per unit length of the machine’s air gap periphery. 18 Definitions Electrical Loading 𝑆∙𝑧∙𝐼 𝑍∙𝐼 𝐴= = [A/m] 2∙𝜋∙𝑅 2∙𝜋∙𝑅 where: 𝐼 is the rms current or DC value 𝑆 is the total number of slots 𝑧 is the total number of conductors per slot 𝑍 is total number of conductors (𝑆 × 𝑧) 𝑅 is the airgap radius of the machine 19 Torque in an Electrical Machine From the Lorentz equation, force on a current-carrying conductor in an orthogonal field is: 𝑑𝐹 = 𝐵𝐿𝑑𝐼 And the torque produced at a radius R is: 𝑑𝑇𝑒 = 𝐵𝑑𝐼𝐿𝑅 Consider the figure shown: Torque developed by the machine can be written as: 2𝜋 𝑇𝑒 = 𝐿 න 𝐵(𝜃) ∙ 𝐴(𝜃) ∙ 𝑅2 ∙ 𝑑𝜃 0 20 Torque in an Ideal DC motor Torque developed by an ideal DC motor: 𝜋 where: 𝑇𝑒 = 2 න 𝐵 ∙ 𝐿 ∙ 𝐴 ∙ 𝑅 2 ∙ 𝑑𝜃 0 ❖ A is current loading, and 𝑇𝑒 = 2 ∙ 𝐵 ∙ 𝐿 ∙ 𝐴 ∙ 𝑅 2 ∙ 𝜋 ❖ B is the magnetic loading 𝑇𝑒 = 2 ∙ 𝑉 ∙ 𝐵 ∙ 𝐴 Torque = k * Electrical Loading * Magnetic Loading * Volume 21 Torque in an Ideal DC motor The salient field winding tooth (pole) usually spans (𝜆𝑓 ) only about 70% of the pole pitch (𝜆𝑝 ) Torque produced by DC motor: 𝜆𝑓 𝑇𝑒 = 2 ∙ 𝑉 ∙ 𝐵 ∙ 𝐴 𝜆𝑝 22 Conductors in slots Consider the simple magnetic circuit providing a force acting on a conductor in the airgap. The force is BIL. 23 Consider a system with a movable slotted Conductors in slots element that carries the conductor. The airgap lg2 is much smaller than l g1. Thus, B is larger in the airgap, or NI does not need to be so big (one important point). All flux passes through the magnetic teeth on either side of the conductor. Negligible flux passes through the slot. Hence, the force acts on the magnetic steel (armature), not the conductor (another important point). This makes it easier for the machine to carry large forces. 24 Conflict between copper and iron Conflict for space close to the air gap. Using narrow teeth gives more conductor area and a higher “I” but reduces the “B” average in the air gap as maximum “B” is limited by iron saturation. Using wide teeth improves airgap “B” but reduces copper area and hence current loading for a given current density. Maximum force usually comes from using approximately equal tooth and slot widths. 25 Summary Torque is proportional to the volume of the machine, electrical loading and magnetic loading. Torque scales up with volume for a given magnetic loading (limited by iron saturation) and electrical loading (limited by winding temperature). Machines often have their conductors placed in slots. This ensures that the effective airgap length is small enough so that a high average flux density in the air gap can be obtained without excessive excitation current (excessive current makes the machine hot or requires additional cooling) The BIL force acts on the magnetic steel when conductors are located in slots. Only a small force acts on the conductor. The steel teeth are directly connected to the shaft and stator frame. Mechanical transmission of the force is, therefore, a simple process. 26 DC Machines 1. Winding arrangements 2. Torque and EMF in terms of physical parameters 3. EMF as a function of 𝑖𝑓 27 DC machine windings Lap and wave windings. In a lap winding, the number of parallel paths always equals the number of poles and brushes. In a wave winding, the number of parallel paths is always two. There might be two or more brushes. 28 Torque and Back EMF (1) Assume a DC motor where: 𝑖𝑎 - is the armature current 𝑖𝑓 - is the field current 𝑆 - is the total number of slots on the armature 𝑧 - is the total number of conductors per slot Z – is the total number of conductors in the machine 𝑅 - is the airgap radius of the machine 2𝑝 – number of poles in the machine 2𝑎 = 𝑐 – number of parallel paths in the armature winding 29 Torque and Back EMF (2) We have: 𝐼𝑎 𝐼𝑤 = 𝑐 𝑆∙𝑧∙𝐼𝑤 𝑍∙𝐼𝑤 𝑍∙𝐼𝑎 𝐴= = = 2∙𝜋∙𝑅 2∙𝜋∙𝑅 2∙𝜋∙𝑅∙𝑐 The flux per pole: Torque can be written as: 𝜙𝑝 = 𝐵 ∙ 𝑃𝑜𝑙𝑒𝑎𝑟𝑒𝑎 𝜆𝑓 2𝜋𝑅 𝜆𝑓 𝑇𝑒 = 2 ∙ ∙𝑉∙𝐵∙𝐴 𝜆𝑝 𝜙𝑝 = 𝐵 ∙ ∙𝑙∙ 2𝑝 𝜆𝑝 30 Torque and Back EMF (3) Substituting for B and A: 𝜆𝑓 2 𝑍𝐼𝑎 𝑇𝑒 = 2 ∙ ∙ 𝜋𝑅 𝑙 ∙ 𝐵 ∙ 𝜆𝑝 𝜋𝑅𝑐 𝜆𝑓 2𝜋𝑅 𝑍𝐼𝑎 ∙ 2𝑝 ⇒ 𝑇𝑒 = ∙ ∙𝑙∙𝐵∙ 𝜆𝑝 2𝑝 2𝜋𝑐 Recall from the previous slide: 𝑍𝐼𝑎 ∙ 2𝑝 2𝜋𝑅 𝜆𝑓 ⇒ 𝑇𝑒 = ∙ 𝜙𝑝 𝜙𝑝 = 𝐵 ∙ ∙𝑙∙ 2𝑝 𝜆𝑝 2𝜋𝑐 31 Torque and Back EMF (4) Power segregation in DC machines: Field circuit (steady-state): 𝑉𝑓 = 𝑖𝑓 ∙ 𝑅𝑓 Power lost in the field: 𝑉𝑓 ∙ 𝑖𝑓 = 𝑖𝑓2 ∙ 𝑅𝑓 Armature circuit (steady-state): 𝑉𝑎 = 𝑅𝑎 𝑖𝑎 + 2𝑉𝑏𝑟𝑢𝑠ℎ + 𝐸𝑎 Power: 𝑉𝑎 𝑖𝑎 = 𝑅𝑎 𝑖𝑎2 + 2𝑉𝑏𝑟𝑢𝑠ℎ 𝑖𝑎 + 𝐸𝑎 𝑖𝑎 Terminal Power conversion Power lost Power lost - Mechanical power power in resistance in contact voltage drop 32 Torque and Back EMF (5) EMF: 2𝜋𝑁𝑚 Power conversion: 𝐸𝑎 𝐼𝑎 = 𝑇𝑒 ∙ 𝜔𝑚 = 𝑇𝑒 ∙ 60 𝑍𝐼𝑎 ∙2𝑝 2𝜋𝑁𝑚 Substituting for 𝑇𝑒 : 𝐸𝑎 𝐼𝑎 = ∙ 𝜙𝑝 ∙ 2𝜋𝑐 60 𝑍∙𝜙𝑝 ∙𝑁𝑚 ∙2𝑝 𝑍∙𝜙𝑝 ∙𝑁𝑚 ∙2𝑝 𝑍∙𝜙𝑝 ∙𝑁𝑚 ∙𝑝 𝐸𝑎 = = = 60𝑐 60∙2𝑎 60𝑎 Where 𝑁𝑚 is the mechanical speed of rotation in rev/min N.B. For a lap winding, a = 𝑝, for a wave winding, a = 1. 33 Example A 3 kW, 4-pole lap wound DC machine has 32 slots, each holding 12 conductors. The machine has a mean airgap diameter of 10 cm and is 12 cm long. The field winding is wound on stator poles spanning 68o. The maximum airgap flux density under the field poles is 1 T. If at rated load, the armature draws a terminal current of 40 A, determine the rated: a) torque, b) speed, c) terminal voltage, if the armature resistance is 0.4 Ω and the voltage drop across each brush is 1 V. 34 solution 𝑝=2 a) Torque: 𝑆 = 32 𝑆∙𝑧∙𝑖𝑤 32×12×10 𝐴= 2∙𝜋∙𝑅 = 𝜋∙0.1 = 12,223 A/m 𝑧 = 12 𝐼𝑎 = 40 A 𝐼𝑎 40 𝜆𝑓 𝐼𝑤 = = = 10 A 𝑇𝑒 = 2 ∙ 𝜆 ∙ 𝐵 ∙ 𝐴 ∙ 𝜋𝑅2𝑙 2𝑝 4 𝑝 𝐷 = 0.1 m 𝜆𝑓 = 68o, 𝜆𝑝 = 360 = 90o 4 𝑙 = 0.12 m 𝑅𝑎 = 0.4 Ω 68 𝑇𝑒 = 2 ∙ 90 ∙ 1 ∙ 12,223 ∙ 𝜋 ∙ 0.052 ∙ 0.12 = 17.4 Nm 𝑉𝑏 = 1 V 35 solution b) Speed: 3000 P = 𝑇𝑒 ∙ 𝜔𝑚 ⇒ 𝜔𝑚 = = 172.4 rad/s 17.4 c) Terminal voltage: 𝑉𝑎 = 𝑅𝑎 𝑖𝑎 + 2𝑉𝑏𝑟𝑢𝑠ℎ + 𝐸𝑎 𝑇𝑒 ∙𝜔𝑚 3000 𝐸𝑎 = = = 75 V 𝑖𝑎 40 Therefore, 𝑉𝑎 = 0.4 × 40 + 2 × 1 + 75 = 93 V 36 Simple Test to determine 𝐸 and 𝑲𝒂 (1) Consider the following test setup: 1. The motor drives the armature of the DC machine at a fixed speed. 2. The armature voltage is measured with a voltmeter. 3. The armature current is zero as the armature is only connected to the voltmeter. 4. Thus, Va is identical to E. 5. The field current 𝑖𝑓 is varied from zero to above rated value in steps. 6. At each field current step, the armature voltage, which is equivalent to E, is measured. 37 Simple Test to determine 𝐸 and 𝑲𝒂 (2) A plot of E against 𝑖𝑓 for a DC machine: 38 Simple Test to determine 𝐸 and 𝑲𝒂 (3) Using machine winding parameters, one can calculate the flux per pole and air gap flux density curves derived from the open circuit curve. 39 Non-linearities in DC Machines 40 DC Machines – Non-linearities Armature reaction Compound windings and compensating windings Commutation Inter-poles to aid commutation Commutation limits the maximum power of a DC motor 41 Armature Reaction So far, we have assumed that the flux in the airgap is generated only by the field coils and that the armature carries the torque-producing currents. There is, however, another component of the airgap flux generated by the armature winding. This is orthogonal to the field flux. The armature current thus combines with the field current to produce the net B in the machine. The torque on the stator must be the same as the torque on the rotor but in the opposite direction. Field currents interact with armature flux to do this. Superposition does not apply to fluxes since the magnetic material has a nonlinear relation between B and the current needed to establish it. 42 Armature Reaction – Field MMF and B 43 Armature Reaction – Armature MMF 44 Armature Reaction – Total MMF 45 Armature Reaction – Airgap B (1) 46 Armature Reaction – Airgap B (2) 47 Armature Reaction – Airgap B (3) 48 Armature Reaction – Problems (1) 1. Armature flux OPPOSES the field flux over one-half of the field poles and AIDS it over the other half. 2. Saturation of the pole magnetic material prevents the decrease in flux under one pole half from being compensated by an increase over the other half. 3. The result is a decrease of net flux cutting the armature as the armature current increases. 49 Armature Reaction – Problems (2) 4. Particular problem in shunt-connected motors Assume the machine is operating from a fixed DC voltage source Reducing field flux causes a speed increase Speed increase causes an increase in the mechanical load power This requires more armature current Hence, further reduction in field flux! ETC, ETC, until bang!!! 50 Armature Reaction – Solutions (1) 1. Use a very big field MMF compared to the armature. This saturates the field poles so heavily that armature MMF has little influence 2. Use a series machine. Hence, the field MMF increases as armature MMF increases. (However, series machines have widely varying speeds with changing loads.) 3. Use a compound machine Here, the series field boosts the field MMF, BUT stable, constant speed is possible due to the shunt field, which prevents field flux from reducing sharply as the load is removed – still unbalanced field distribution. 51 Armature Reaction – Solutions (2) 4. Use a separately excited machine with Power Electronic speed control. The speed control loop causes the armature voltage to drop as the load is applied, and the effective field flux drops. Hence, there is no instability. 5. The most elegant solution is to use a compensating winding connected in series with the armature and mirror the rotor winding. As a result, the armature reaction is cancelled (Expensive solution). 52 Commutation 53 Commutation example Consider: a typical brush in a large machine might carry 300 A or 150 A per coil. During commutation, the current in the coil will change from -150 A to 150 A, i.e., by 300 A. If the speed of the machine is 3000 rpm and the coil is shorted for approximately 1/80 of a revolution, the time for commutation is: 60 1 𝑡𝑐 = ∙ = 0.00025 s 3000 80 300 𝐴 𝑑𝑖/𝑑𝑡: = 1.2 million A/s 0.00025 𝑠 Under-commutation – current jumps over as a spark from the commutator to the brush; the commutator wears out from pitting. 54 Commutation - Solutions Poor commutation is characterised by sparking, normally at the trailing edge of the brush, but it can also be at the leading edge. Poor commutation leads to a short lifespan of brushes and commutators and increased maintenance. An effective way to ease current commutation is to add interpoles. 55 Adding interpoles (1) We have seen that the current in the coil between the commuting segments needs to be reversed during commutation. This is hindered by: 1. Coil inductance 2. Speed EMF induced in coil (this is due to armature flux in between the poles) This is the axis of the armature flux. This flux is small due to the long air gap at that point. Naturally, this speed EMF is in a direction that also opposes the change in current. 56 Adding interpoles (2) Point 2 above indicates a solution – use interpoles to generate a flux which helps the commutation process. These are connected in series with the armature circuit to compensate for the increased armature reaction flux when the load increases. Thus, they carry the armature current. The interpole winding MMF is designed to oppose and reverse the speed EMF induced in the shorted coil. The flux from the interpole induces a speed EMF, which can aid in changing the current direction in the coil. 57 Adding interpoles (3) Opened out cross-section of a 2-pole motor with interpoles to help current commutation. Note: interpole coils are connected in series with the armature winding. 58 Adding interpoles (4) Thus: 1. The speed EMF induced in the coil opposes and neutralises the Ldi/dt voltage of the coil. 2. As the machine rotates faster, the di/dt increases since the time for current reversal is inversely proportional to speed. 3. However, as the machine speeds up, the speed EMF from interpole flux also increases, and so the balance is maintained. 4. As the armature current grows at a fixed speed, the di/dt increases (more amps to change in the fixed time). 5. However, as the armature current grows, so does the interpole flux. Thus, the speed EMF increases to balance the increased di/dt. 6. The commutation process is thus successful as long as the interpoles do not saturate. 59 Power and Commutation (1) The need for commutation imposes a limit on the size of DC machines. Practical values of allowed voltage usually range from 14 V per commutator segment pair if uncompensated to 20 V if compensated. The maximum E induced in between commutator segments: 𝐷 𝐸 = 𝐵𝑙𝑢 = 𝐵𝑃 ∙ 𝑙 ∙ 𝑁 ∙ 2 ∙ 𝜔𝑚 2 BP is the peak flux density, N is the turns per coil between commutator segments (2N as in two conductors per turn) However, the average voltage per turn can be written as: 𝜆𝑓 𝜆𝑓 𝐸𝑎𝑣 =𝐸∙ = 𝐵𝑃 ∙ 𝑙 ∙ 𝑁 ∙ 𝜔𝑚 ∙ 𝐷 ∙ 𝜆𝑝 𝜆𝑝 60 Power and Commutation (2) Now, the torque produced by a DC machine is: 𝜆𝑓 𝜋𝐷2 𝑙 𝑇𝑒 = 2 ∙ ∙𝐴∙𝐵∙ 𝜆𝑝 4 And substituting: 𝜋𝐷 1 𝑇𝑒 = ∙ 𝐴 ∙ 𝐸𝑎𝑣 ∙ or 2 𝑁∙𝜔𝑚 𝜋𝐷 ∙ 𝐴 ∙ 𝐸𝑎𝑣 𝑃 = 𝑇𝑒 ∙ 𝜔𝑚 = 2𝑁 61 Power and Commutation (3) Note 1. Power limit is independent of length 𝜋𝐷 ∙ 𝐴 ∙ 𝐸𝑎𝑣 𝑃 = 𝑇𝑒 ∙ 𝜔𝑚 = 2. Power is limited by E – which is 2𝑁 limited to 20 V! 3. Main problems start at 500 kW Example: 1. Consider a 500 MW DC machine. Let 𝐴 = 50 × 103 A/m 2. Assume an 𝐸𝑚𝑎𝑥 = 20 V and let 𝑁 = 1 (this will give the smallest diameter as minimum number of turns is 1!) 62 Power and Commutation (4) 2𝑁 2 6 𝐷=𝑃∙ = ∙ 500 ∙ 10 𝜋 ∙ 𝐴 ∙ 𝐸𝑎𝑣 𝜋 ∙ 50 ∙ 103 ∙ 20 𝐷 ≈ 320 m 15−floor storey − building is 45 m approx.! 𝜆𝑓 From: 𝐸𝑎𝑣 = 𝐵𝑃 ∙ 𝑙 ∙ 𝑁 ∙ 𝜔𝑚 ∙ 𝐷 ∙ 𝜆𝑝 And for a Bp of 1 T: 20 = 𝑙 ∙ 𝜔𝑚 ∙ 320 ∙ 0.7 Resulting in: 𝜔𝑚 ≈ 0.09 ≈ 0.85 rpm 𝑇𝑒 ≈ 5.6 × 109 𝑙 ≈1𝑚 Unrealistic!! 63 Starting of DC motor 64 At starting, the speed is zero, and thus, the armature current is limited by only the armature resistance: 𝑉𝑎 = 𝐸 + 𝐼𝑎 𝑅𝑎 = 𝐼𝑎 𝑅𝑎 Very small motors are started direct-on-line, i.e., full voltage is applied when stationary to start it. For larger machines, the armature resistance is small; therefore, starting them directly results in a highly excessive armature current. Very probable consequences of a highly excessive armature current are: 65 armature winding burning out damage to the commutator and brushes owing to heavy sparking overloading of the feeder the shaft snapped off due to mechanical shock damage to the driven equipment because of the sudden mechanical hammer blow (like a stroke with a hammer). 66 The starting current must be limited to 1.5 to 2.5 times the rated current. If the supply is at a constant nominal voltage, the starting current is limited by connecting resistors in series with the armature. A liquid rheostat gives a smooth variation in resistance, but robust metallic resistors are usually preferred. The metallic resistors are arranged in series sections, which are cut out successively by manual or automatic operations. Today, electronic methods are often used to limit the starting current and to provide speed control. 67 Example A 240-V DC shunt motor has a full-load speed of 750 rev/min and a full-load armature current of 20 A. The armature resistance is 1 Ω. The maximum armature current during the starting period is 30 A. Calculate the total resistance of the starter. Solution At start, the back emf = 0 𝑉 240 Hence 𝑅𝑎 + 𝑅𝑠𝑡 = = =8Ω 𝐼 30 and 𝑅𝑠𝑡 = 8 − 1 = 7 Ω Note: If it is started direct-on-line, the starting (armature) current will be 𝐼𝑎 = 𝑉 240 = = 240 𝐴 which is 12 times 𝐼𝑎𝑓𝑙 (full-load armature current) 68 𝑅𝑎 1 Grading starting resistance for shunt and separately excited motors (constant flux) 69 In grading the starting resistance, we are required to ensure that the starting current varies between specified upper and lower limits I1 and I2 The lower limit is necessary to ensure rapid acceleration. We note the following: If the starter has (n-1) elements, then the start will be made in n steps by cutting out the sections in sequence At switch-on (step 1) the total armature-circuit resistance R1 is made up of n series sections: r1, r2,........,rn-1 and rn = Rm 70 70 ▪ Where Rm is the total resistance of the motor. ▪ The sections can be obtained as follows: ▪ Let ❖ R1 = the total armature-circuit resistance at switch-on = r1+ r2 +.........+ rn (rn = Rm) ❖R2 = the total armature-circuit resistance when section 1 is shorted out = r2+ r3 +.........+ rn ❖R3 = the total armature-circuit resistance when sections 1 and 2 are shorted out = r3+ r4 +.........+ rn, etc. 71 ▪ At switch-on, the starting current, ❖ I1 = V/R1 ▪ The motor current falls as the motor gains speed, and the motor EMF builds up. ▪ The resistance r1 is cut out when the current falls to I2, where ❖ I2 = (V - Eb)/R1 or Eb = V – I2R1 ▪ When resistor r1 is cut out, the current jumps back to I1, where this time ❖ I1 = (V - Eb)/R2 or Eb = V – I1R2 ▪ The back EMFs (Ebs) in the above two equations are equal. ▪ This is so because Eb is proportional to the speed of the motor, and the speed cannot change instantaneously. 72 ▪ Hence ❖ I1R2 = I2R1 or ❖R2/R1 = I2/I1 = k or ❖R2 = kR1 ▪ Similarly, ❖R3 = kR2=k2R1 ▪ and after the nth step ❖Rn = Rm= kn-1R1 ▪ The section resistances are ❖ r1 = R1 - R2 = R1(1-k); ❖ r2 = R2 - R3 = R2(1-k). =kR1(1-k) = kr1 ❖ rn-1 = kn-2 r1, ❖ rn = Rm ▪ Both the total resistances R and the section resistances r are in geometrical progression. 73 ▪ Normally either I1 or I2 and the number of sections of the starter (= n – 1) are given and we have to determine the resistance of the sections. ▪ I2 is determined by the maximum value of the load torque at starting and during acceleration. ▪ From ❖ Rn = Rm = kn-1 R1, ▪ we obtain ❖ Rn = Rm = kn-1V/I1 or ❖ Rn = Rm = kn-1V/(I2/k) = kn V/I2 ▪ Equations required to grade the starter are given below: ❖ Rm = kn-1V/I1 or Rm = knV/I2 ❖ I2/I1 = k ❖ I1 = V/R1 ❖ R2 = kR1 ❖ r1 = R1 – R2 74 ❖ We need also to remember that the section resistances r are in geometrical progression. ❖ We proceed as follows: ❖ Use Rm = kn-1V/I1 when I1 is given or Rm = knV/I2 when I2 is given to find k ❖ Use I2/I1 = k to find I1 when I2 is given ❖ Use I1 = V/R1 to find R1 ❖ Use R2 = kR1 to find R2 ❖ Use r1 =R1 – R2 to find r1 ❖ Find r2 = kr1, r3 = kr2, r4 = kr3…… 75 Example Evaluate the five rheostat sections for the starter of a 220 V, 45 kW shunt motor with Ra = 0.045 ohms, the lower current limit being 200 A. What will be the upper current limit? Solution: For five rheostat sections n = 5 + 1 = 6 From Rm = knV/I2, 𝑘 6 = (𝑅𝑚 /𝐼2 )/𝑉 = (0.045 × 200)/220 = 0.0409 Therefore 𝑘 = 0.04091/6 = 0.5869 𝐼1 = 𝐼2 /𝑘 = 200/0.5869 = 341 A 𝑅1 = 𝑉/𝐼1 = 220/341 = 0.64516 𝛀 and 𝑅2 = 𝑘𝑅1 = 0.5869 × 0.64516 = 0.37864 𝛀 Hence 𝑟1 = 𝑅1 − 𝑅2 = 0.64516 − 0.37864 = 0.267 𝛀 and 𝑟2 = 𝑘𝑟1 = 0.5869 × 0.2652 = 𝟎. 𝟏𝟓𝟔 𝛀, 76 𝑟3 = 𝑘𝑟2 = 𝟎. 𝟎𝟗𝟐 𝛀, 𝑟4 = 𝑘𝑟3 = 𝟎. 𝟎𝟓𝟒 𝛀, and 𝑟5 = 𝑘𝑟4 = 𝟎. 𝟎𝟑𝟏 𝛀. Manual starters 77 Faceplate starter ▪ A diagram of a faceplate starter for a shunt motor is shown here. ▪ Essential components are: ▪ The current-limiting resistors 𝑟1 , 𝑟2 , 𝑟3 , and 𝑟4. ▪ Conducting arm 1 with insulated handle 2 is used to cut out the resistors successively. 78 ▪ Contact M, is a dead contact. At this position, the motor circuit is open. ▪ Electromagnet 4 in series with the shunt field holds the arm at the close position. ▪ Spring 3 pulls the arm to the dead position when the electromagnet releases it. ▪ If the supply voltage should fail or the field excitation should be lost, the electromagnet releases the arm allowing it to return to its dead position, under the pull of spring 3. ▪ This safety feature prevents the motor ▪ from restarting unexpectedly when the supply voltage is reestablished and also ▪ from being energized when the excitation is lost. ▪ The faceplate starter is obsolete except for small motors up to 5 kW. ▪ They are limited electrically because they tend to arc between the sliding surfaces, resulting in rapid wear of the contacting surfaces. ▪ They are also not operator-proof and cannot be used in simple applications such as motor reversal or braking. 79 Drum controller ▪ This is an improved manual starter. ▪ Stationary contact fingers under spring pressure make contact with a set of contact bars mounted on a cylindrical drum. ▪ The required switching is made by rotating the drum manually. ▪ The manual effort needed for operation limits the application to motors of about 100 kW. ▪ They are used on crane motors, elevators, machine tools and other applications for start, stop, reverse and speed control. 80 Automatic starters 81 ▪ In modern industrial applications, ▪ push-button is used to initiate the starting of most DC motors (both small and large) and contactors are used for the subsequent switching. ▪ There are basically three types of automatic starters: ▪ direct-on-line, ▪ current-limit and ▪ definite-time starters. 82 Direct-on-line starter ▪ This is used to start small DC motors. ▪ These motors draw low starting current so starting resistance is not necessary. ▪ We consider a direct-on-line starter using a dual winding contactor. ▪ Dual contactor has two windings (or coils) known as starting winding and holding winding. ▪ During the closing of the contactor a large magnetic pull is required so both windings are energized. ▪ In the closing position, a small holding force is required so only the holding is energized. ▪ Pressing the start push button, both coils are energized through the start push button and the NC contact M2 of the dual contactor M. ▪ As soon as the contactor M picks up, the NC contact M2 opens to disconnect the starting coil. ▪ At the same time the sealing contact M1 closes to provide a path around the start push button to keep the holding coil energized. 83 DC Machines Exercises 84 Exercise 1: A separately excited motor runs at 1045 rpm, with a constant field current and an armature current of 50 A at 120 V. The armature resistance is 0.1 ohm. The motor is further loaded to draw a current of 95 A at 120 V. 1. What is the motor speed at this load? What is the power and torque delivered? 2. If the armature voltage is now increased to 180 V and the load torque remains the same, what is the new speed of the machine? 3. If the field current is reduced by 25%, what will the armature current and speed of the motor be for the same torque and armature voltage above? 85 Exercise 2: The armature winding of a 4-pole, permanent magnet-excited DC machine is lap-wound in 46 slots with 18 conductors per slot. The permanent magnet field poles span 70% of the pole pitch, and the peak air gap flux density is 0.7 T. The machine has an air gap diameter of 15 cm and a core axial length of 25 cm. 1. If the armature is designed to carry a continuous line current of 100 A, what is the maximum electromagnetic torque developed by the machine? 2. Calculate the voltage induced in the armature winding when the rotor speed is 1800 rpm. 3. If the machine is supplied from a constant DC voltage source of 380 V and the armature resistance 𝑅𝑎 = 0.5 ohm, what is the rotor speed if a load of 20 Nm is applied? State any assumptions made. 86 Exercise 3: A permanent magnet DC motor has the following characteristics: ▪ Nominal voltage: U=12 V ▪ back emf to speed ratio: K = 10-3 V/rpm ▪ Armature resistance: Ra=3.5 Ω The motor is supplied with a 12 V battery of negligible internal resistance. 1. The motor armature current is 𝐼𝑎 = 0.2 A at no load. Calculate the induced voltage (EMF) and the rotor speed. What happens if we reverse the connection between the armature winding terminals? 87 Exercise 3 cont.: 2. At full load, the motor armature current is 𝐼𝑎 = 0.83 A; calculate the: ▪ input power ▪ copper losses ▪ output power ▪ motor efficiency ▪ rotor speed ▪ electromagnetic power ▪ electromagnetic torque 88 Exercise 3 cont.: 3. Explain why electromagnetic torque is proportional to the armature current 𝐼𝑎. Verify that the torque/current ratio equals 9.55 10-3 Nm/A. 4. Calculate the starting current. Deduce the starting torque. 5. During normal operation, explain what happens if a mechanical failure suddenly blocks the rotor. 89 THANK YOU ANY QUESTIONS? 90