Applied Projects - Measure Phase PDF
Document Details
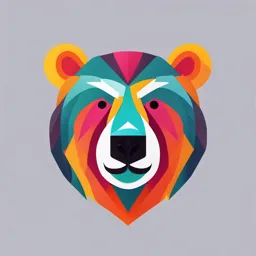
Uploaded by ChasteMannerism
Amelia Abernathy
Tags
Summary
This document is about the measure phase of the DMAIC model in Lean Six Sigma. It discusses applied projects and various data collection methods.
Full Transcript
Green Belt Certification Measure Phase of the DMAIC Model Applied Projects Lean Six Sigma Amelia Abernathy Measure Phase – What we will cover Process Types of Y and X Lean Metrics Mapping Data Data...
Green Belt Certification Measure Phase of the DMAIC Model Applied Projects Lean Six Sigma Amelia Abernathy Measure Phase – What we will cover Process Types of Y and X Lean Metrics Mapping Data Data Value stream Six sigma Sampling MSA Mapping Metrics Data Collection Why Use a Process Map Show what the current process looks like. Identify deviations from the norm. Show relationships between steps or departments involved. Identify where to collect data & investigate further for improvement opportunities. Serve as a training aid (shows how the work should be done). Serve as process documentation and standardization Mapping Processes What is the path that our actions and processes follow? Process Mapping is essential in all DMAIC steps: Creating a common understanding of the process Defining not only the process you are interested in, but the upstream, downstream, or supporting processes Defining the Total Life Cycle performance of a process, organization or business enterprise Identifying improvement opportunities (process complexity, waste, delays, inefficiencies, and bottlenecks) Process Mapping What are we mapping People, parts, paper, information (computers, networks) From what perspective will we draw the process map As Was – a historical reference of how the process used to be Should Be – the way documentation says it is supposed to be or the way you think it is working As Is/Current State – an actual reflection of how the process is actually working Future State – a projection of how you want the process to work Utopia State – the way the process could work if there were no restrictions Process Map Example from Assignment Workflow (Spaghetti) Maps What: a picture of how a process flows within a work layout. How is it Useful: studies a process by mapping movements of people, materials, documents, information, etc. in a sequential manner to identify unnecessary transportation and motion. How Can Data Help You? Data Can Show What Really Is Data helps us… Establish performance baseline Identify and understand relationships that might explain variation Confirm or disprove preconceived ideas and theories Measure the impact of changes to a process Control a process The “Right” Data … Describes the problem you’re studying Describes related conditions that might provide clues about causes Can be analyzed in ways that answer your questions Useful data is: Representative Sufficient Relevant Contextual Main Types of Data Quantitative Qualitative Information that deals with numbers Information about descriptors and and things you can measure objectively characteristics that can’t easily be measured, but can be observed Count or measure things to create subjectively quantitative data Classify or make a judgement to create qualitative data Examples: Counts, prices, volume, time, height, Examples: width, etc. Color, tastes, textures, smells, defect types, etc. Data Selection Binomial Accept/Reject Yes/No Nominal (Name, Label) Product/Customer/Defect Types Office: Department X, Dept. Y, Dept. Z Color: Yellow/Red/Blue, etc. Ordinal (Rank, Order) Ranking: “Top 10” Likert scale (1 – 7) Rating (1 = Excellent, 2 = Very good, etc…) Status: Red/Yellow/Green Data Selection Count Data Number of Widgets Number of Complaints/Defects % of Incomplete Orders Measure Data Time Money Temperature Height, Length, Weight Volume Time per Delivery Days between Incidents “Y” Data The type of data depends on what “Y” (output) was selected by your team as contributing to changing the project metric. Outputs or “Y”’s measure performance (how well a project is meeting its goals). Y’s can usually be charted or graphed Prioritizing and Selecting “Y”’s Start with your SIPOC diagram outputs and CTQs Measure only what is important! Important to the customer Linked to strategic goals Keep the number of measures small Use a family of measures Reduces “false” improvement from focusing on just one variable Effectiveness AND Efficiency Quality, Cost, AND Lead Time “X” Data The type of data depends on which “X”’s (inputs) were selected by your team as contributing to changing the “Y”’s (outputs). For example: Suppose we want to improve the engine overhaul performance. To possible X’s: X1 – Number of parts to replace X2 – Difficult in replacing parts Value Stream Mapping Value Stream Wandering around your organization and its processes often leads to great discoveries. Mapping: A good map to guide you will help you find your way there, Building More around, and back faster, more precisely and more reliably. The more comprehensive your maps are, the better your Complex chances of finding your treasures. You will reduce the trial, error and variation in your journey. Models of Value Stream Maps are one of the places where “classic” Lean and “classic” Six Sigma meet. Your Process What is value? Who defines what value is? You? Your boss? Your customers? What steps add value to your process? What steps do not add value? What steps seem to be necessary to enable or support value adding steps Value Stream (VS): All the actions currently required to take a request and bring it through the main flows essential to transform it into a product or a service. Customer’s Customer Customer YOU Suppliers Sub- Contractors A Value Stream Map (VSM) visually breaks down essential steps in a value stream, showing how the pieces fit together all the way from your supplier to your customer. Why Map a Value Stream? To visualize work as a ‘system’ Activities, Pathways, Connections To make the flow to the customer more visible Sales IT Services Finance Request Deliverable To see what the customer is feeling To prioritize cross-functional process issues To see better the horizontal flow that cuts across functions or departments Diagram: Value Stream Map “Value Stream Mapping” is generally practiced according to the principles from “Learning to See” Control Department or Organization Supplier Customer Information Flow Material Flow Process Process Process Process Step 1 Step 2 Step 3 Step 4 IN Data Box Data Box Data Box Data Box Wait Wait Wait Wait Total Lead Time Processing Time Process Time Process Time Process Time Process Time %C&A Lead Time Ladder 2 0 Value Stream Mapping Typical Benefits Helps you see the sources of waste in the process Shows linkage between the information flow and the material flow Provides a common language for talking about the processes Makes decisions about the flow more obvious Forms the basis for an implementation plan Accelerates lean transformation Increased visibility of critical operations Improved allocation of resources Improved understanding of processes by suppliers and customers / stakeholders VSM Objectives Eliminate Waste: Identify and quantify the non-value added activities of the value stream that are candidates for Lean improvements Document the Current State (As-Is) and Future State, in order to develop an action plan for implementing lean initiatives Avoid the pitfall of implementing lean initiatives in vacuums. The VSM process brings together Removes problems of Ownership/Silos/Isolationism stakeholders and process operators in communication VSM ID Opportunities for Improvement VSM: Reveals the impact of non-value added (NVA) activities on total lead time by calculating those activities in terms of customer demand Example: In a push-system where customer demand is 3 parts/day, a WIP Level of 45 parts is 15 days of NVA activity in the value stream Value Added Actions: An activity that transforms or changes the inputs in a way that is meaningful to the product / service (Also called “Touch Time”) Any activity a Customer is willing to pay for Does not include rework activities / time Classifying Value Value Added (VA) Non-Value Added (NVA) Necessary Non-Value Added (NNVA) Does the task add form, feature, or If the user knew we were doing Is this task required by law, policy, function to the process or service? this, would they request that we or regulation? eliminate the activity to reduce Does the task reduce financial Does the task enable an cost? advantage (cost, speed, quality)/ risk? Does the cost fit into either of the Would the process of producing Would the user be willing to pay other two categories? for this task? the service break down if this task Is the task one of the seven were removed? wastes? VSM Transformation Elements Problem Product / Service Identify the Product / Service Family Family A group of products / services that use the same or similar processing steps and equipment Current State Current State Map: Map As-Is view of the value stream (may or may not contain any Lean characteristics) Future State Map: Future State Map Goal for your value stream containing lean elements to reduce waste and improve flow Action Plan: Work Plan & Steps to take to move the current state toward the future state Implementation VSM Data Collection/Analysis Obtain observed data or machine Do not rely on your ideas of what Sources of data data!!! you think is happening. Stop-watch Video tapes Historical reports Automated systems already in place Last resort: standard times Available Time (work time minus breaks) Processing Time (PT) Delay Time (DT) Lead Time (LT) Takt Time (TT) Inventory # of People Common Data Scrap Rate or Yield or % Complete & Accurate (%C & A) % Reliability (e.g., system down time) Requirements Changeover Time (C/O) – Time to switch from doing one type of work to a different type of work (also called Set-Up time) Cycle Time (CT) Number of Shifts Batch Size Pack Size – Number of items in a shipment carton Uptime - Percentage of time equipment really runs, compared to the time it is scheduled to run Value Stream SUMMARY Total Lead Time: 20 days Map Total Processing Time: 1 day Total Delay Time: 19 days % C & A (RTY): 5.44% Client HED Receives Information From Client P/T Task 30 minutes A/T 420 minutes %C/A 16 % Shelly Reviews & Formation Documents Sent To Documents Filed In Box Documents In Box In Box Documents Filed in In Box Delegates New Documents In Box In Box Client for Review & with Secretary of Reviewed by Shelly Minute Book Matter Prepared Signature State P/T 45 minutes P/T 180 minutes P/T 60 minutes P/T 30 minutes P/T 60 minutes P/T 30 minutes A/T 420 minutes A/T 420 minutes A/T 420 minutes A/T 420 minutes A/T 420 minutes A/T 420 minutes %C/A 16 % %C/A 60 % %C/A 70 % %C/A 90 % %C/A 90 % %C/A 100 % Non-Value Added Non-Value Added Non-Value Added Non-Value Added Non-Value Added 3 days waiting on 2 days in Attorney's 1 day in Legal Asst 8 days waiting on 5 days waiting on Client information In-Box In-Box Client to return Docs SOS to return docs Value Added 1,260 minutes Value Added 840 minutes Value Added 420 minutes Value Added 3,360 minutes Value Added 2,100 minutes Value Added 45 minutes 180 minutes 60 minutes 30 minutes 60 minutes 30 minutes P/T = Process Time A/T = Available Time % C/A = % Complete and Accurate Lean Metrics Lead Time – the elapsed time it takes to produce a product, or complete an activity, from start to finish, including batch and process delays. Basic Cycle Time – the actual production rate, or the elapsed time it takes to complete the tasks required for a work process Lean Takt Time – paces the production rate to Metrics customer demand Delay Time – wait time; delays can be during, or, between process steps Cycle Time vs Process Time Process Time Cycle Time The total time the product is in the process or The rate at which the process produces a process step (machine time) single unit (unit time) Example: If a single part spends 4 minutes in Example: If 2 parts fit in the cleaner, C/T = the cleaner, P/T = 4 min 4min/2 parts = 2 min/part Or, a part exits the cleaner every two minutes. Basic Lean Metrics Takt Time Takt time is the production rate needed to satisfy customer orders on time. Drum beat of production Based on actual internal or external demand Available work time per shift Takt Time = Customer demand per shift Available Time: Scheduled minutes per shift (8 hours*60 minutes/hour)= 480 minutes Subtract approved breaks, lunch, meetings*, and 5S+1 activity times to find available work time per shift Typically, assume 60 minutes per hour, 5 workdays per week Takt Time: Example The garnishment order processing team receives 400 garnishment orders per week.* What is the Takt time for this process? Daily Demand: 400 orders / 5 days = 80 orders per day 480 - 60 Takt time = minutes per order 80 *Assume 5 days/week; one 8 hour shift/ ay; 60 minutes for lunch and breaks. CYCLE TIME VS. TAKT TIME Do not subtract estimated disturbance time from Available time to determine the Takt time. Avoid changing Takt time frequently to adjust for variability - inefficient, creates problems Assume we have a seven station operation, 1 – 7 in sequence, to produce an item at the customer requested rate of 30 per day. Assume we have one shift operation allowed two 15 min breaks and one 60 min lunch period. Assume also average walk time between stations is 4 sec., and the following task times: Station Task time (min) 1 10 2 7 3 9 Class Exercise 4 12 5 8 6 11 7 10 Calculate Cycle Time and Takt time. Is the production capacity adequate to satisfy the customer demand? Lead Time Total Lead Time - the elapsed time between recognition of the need to produce a item, and shipping of the finished item to the customer. Operation Lead Time - Measured from the time a job is assigned to an operation to the time it becomes the responsibility of the next operation Lead Time includes purchasing of raw materials. “Batch and Queue” Most processes follow this approach to some degree. In Batch and Queue environments, batches of unfinished goods move through each process step together in an effort to minimize setup changes Not Lean Elements of Lead Time - Batch & Queue – accumulate orders, then wait to be processed - Setup Time – prepare to process next job - Run Time – processing time per unit Often less than 1% of cycle time Only value-added step of Lead time Lean Metrics Elements of Lead time Why do we have Move, Wait Why do we have Excessive & Queue Set-up and Run Times Set-up, run, wait, move, queue Poor layout Poor workplace organization: Large batch size Excessive people travel, material travel, searching time Un balance lines Non-standard processes: variable Orders that are pushed to the next cycle times, inconsistent quality, person rework scrap Inefficient process: Complex tooling, poor workflow, set-up not externalized, poor maintenance Lead Time Another way of looking at this: Move Queue Set-up Run Wait Move Queue Set-up Value Even though only a small added portion of the total lead time portion Lead time also includes is value added, lead time the time necessary to order includes the time included supplies. in all of these steps. Percentage Value Added (PCE) is typically 5% SET-UP TIME Setup time is the elapsed time to prepare a machine to produce a specific product; or in an office, the elapsed time to transition from doing one type of work to doing another type of work. Involves tool (equipment & software app) changes & preparation to process first piece Starts when last good piece of a job is complete; Ends when first good piece of the next job is complete Internal set-up: While machine is shut-down External set-up: While machine is working Set-Up Time (S/U) is also known as Changeover Time (C/O) We can attack Move, Wait, and Queue by: Moving processes together Simplifying routings LEAD TIME Reducing set-up times Moving “products” in smaller batches or one at a time Balancing lines (equalizing time spent on process steps to avoid bottlenecks) Six Sigma Metrics Process Baseline At the end of the Measure phase, the six-sigma project team, should have a process baseline to add to the project charter If a process, or product, has specification limits associated with it, capability indices are appropriate measures of the process baseline. For processes without specification limits, Pareto Plots, Histograms and Run Charts may be used to assess and report the current process baseline Process “Capability” Capability: The ability of a process to deliver defect-free output (service, product, information) Based on understanding the critical Ys Measuring performance against customer requirements Determined by the effect of the important Xs on the Y Assess by: Defect-based measures Cost/efficiency-based measures Capability index measures Why Assess Process Capability? Allows us to quantify the nature of the problem we will attack as one of the following: Are the specifications correct for the parameter (Y) of interest (process or performance output variable)? Is the location of the central tendency of the parameter (Y) centered within the appropriate specifications? Is the process variation in the parameter greater than allowed by the specifications? Is the measurement system affecting our ability to assess true process capability? Allows the organization to predict defect levels **Sometimes customers don’t realize what is realistic Defect Measures: Key Terms Unit: one item of the process throughput or output Ex. An application, a check, a pallet, a phone call, a product Defect: Any failure to meet an essential requirement of a customer (internal or external) Defective: Any unit with one or more defects Defect Opportunity: A type of potential defect on a unit of throughput/output that is important to the customer! A check may have: wrong amount, wrong payable line, missing signature, wrong date, etc. (easily FOUR opportunities) Metric Application Examples PPM (parts per million) Short or long term predicted defective number 1) Scrap/million built of units per million evaluated. Used in projects 2) Lost Orders/million quoted where leveling for complexity is not an issue 3) Field returns/million shipped and 1 defect maximum is allowed. DPMO (defects per million Used in situations where multiple 1) Release Software Errors/million lines of opportunities) opportunities for errors exist for each unit of code output. Often used to level against significant 2) PCB Component errors/million loaded variation in complexity. DPU (defects per unit output) Used typically on projects which will utilize RTY 1) Rework hours/unit shipped as an indicator. 2) Non-value added operations/unit output RTY (rolled throughput yield) Used where process improvement is the Example: 60% objective. Evaluates probability of a single unit of output going through process without error. 'Z' Value or 'Sigma' Level Used to show capability of a process output Example: 'Z = 1.2' equals a '1.2 Sigma' against a target or specification value. process Six Sigma Metrics Overview Defect Measure Formulas Proportion Defective: Fraction of units with defects (% wrong) = # of Defectives / # of Units Ex. 43 of 250 applications have defects 17.2% defective Final Yield (% right) 1 – Proportion Defective Ex. 1 -.172 = 82.8% Yield Defect Measure Formulas # of Defects / # of Units DPU: Ex. 52 defects on applications out of 250 Defects/Unit applications.21 DPU # of Defects / (# of Units x # of Opps/Unit) DPO: Defects/ Ex. From above, each unit has 4 opportunities Opportunity for defect (think check example from earlier) 52 / (250 x 4) =.052 DPO Defect Measure Formulas DPMO: Defects / Million Opportunities DPO x 1,000,000 (# of defects / (# of units x # of opps/unit)) x 1,000,000 Ex. (52/ (250 x 4)) x1,000,000 = 52,000 DPO This normalizes your process Makes your problem look more “important” Usually the best for presentation Sampling A population is the entire group that have the characteristic that we are Population vs. interested in studying. Sample A sample is a subset of the target population selected for study. Statistics help us to work with and analyze sample data to draw conclusions and make decisions about the entire population. Sampling: How much data do we need? Sampling Why Sample? Questions: A statistical principle that allows us Looking at all the data may be too How many samples are taken in an to gather reasonable amounts of expensive, too time-consuming, and / opinion poll? information and analyze it in detail to or destructive (e.g., taste tests) Do Inspectors test the entire draw conclusions & make decisions production line or do they test about the entire population or random samplesrom the population? process. When sales and marketing people call you to offer promotions and say:”You have been selected to participate…” is it really random? Sampling Terms & Approaches Confidence Interval - is a range around a measurement that conveys how precise the measurement is. Also called “margin of error,”e.g., 60 + 3%. Confidence Level - associated with a confidence interval states how much certainty we have that this interval contains the true population parameter Target population – is the entire group a researcher is interested in Random sampling - a sampling technique where we select a group of subjects (a sample) for study from a larger group (a population) Simple random sampling - is the basic sampling technique where we select a group of subjects (a sample) for study from a larger group (a population). Sampling Develop a Sampling Plan You can use your process knowledge supplemented by the knowledge of the stakeholders in the project to get the best sample you can Often, you are limited by what you can collect Often the data is not “clean” or usable Sometimes, we have to just “get what we can” then, hope for the best results State your assumptions and known biases when you develop this plan, especially where there is very little data How big should the sample be? Some Rough guidelines: There are various sample size calculators on the internet that can be fun to try. They offer guidelines on what to collect with different confidence levels Try to get at least 20-30 data points for continuous data Try to get 50-100 points for attribute / discrete data Collect data until you see patterns repeating or until you are not seeing new things Measurement System Analysis (MSA) Measurement is the act or process of assigning numbers, value, or judgment to observations according to a rule. When measurement data is being used to make decisions regarding the process, and business in general, it is vital that the data is accurate. If there are errors in our measurement system we will be making decisions based on incorrect data. The term measurement system refers to a system of related components that enable the quantification of particular characteristics. It consists of measuring devices, operational definitions, procedures, and personnel. Each of these, along Measurement with the items being measured and the environment, are a source of variation in a measurement process. Systems Measurement System Analysis (MSA) estimates the quality of the measurement system for a given application. It is defined as an experimental and mathematical Analysis method of determining how much variation within the measurement process contributes to the overall process variation. Most MSA examines two primary sources of variation – the parts and the measurement of those parts. The experiment, Gage Repeatability, and Reproducibility (Gage R & R), involves measuring the same items repeatedly using the same measuring process and tools but different workers to evaluate the process, the tools being used, and the workers for a proper definition, accuracy, precision, repeatability, and reproducibility. If the variation in the measurement system is large compared to the part-to-part variation, it is an indication that the measurement system cannot adequately distinguish between parts, and the measurements may not provide useful information. A MSA can be performed with both continuous and attribute data. Data Collection Data Collection What is your plan to collect your data? Considerations: 1) What data will you collect? – What must be considered when collecting the following types of data: Historical data Recent data New data What are the 'good' Data collected by others things and 'bad' things Automated data with data sources? Customer supplied data Benchmark data Other sources: _______ An Operational Definition is a precise description that tells how to assign a value to a characteristic that you are trying to measure. The two elements of an operational definition are: Identification of the logical sub-groups included in the object of measurement Boundary conditions that set the limits on the method of Operational measurement Following an operational definition, the way to measure Definition the defined variable should be specified Purpose: To remove ambiguity and assure everyone has the same understanding or common language about the variable To provide a clear approach to process measurement: Identifies what to measure Identifies the limits of measurement Assures that the results are repeatable and reproducible Data Collection What is your plan to collect your data? Where will you collect it? Look at your process maps Identify the best spots to collect data Where are your concerns? Data Collection What is you plan to collect you data? Who will collect it? Your team Operations/workers Automated data collection systems When will you collect it Time frame What are the constraints or biases involved Holidays End of Month Middle of the day Be aware of the interference you may create in the workplace Data Collection What is your plan to collect data “Walk” your process How much will you collect Get out there and see, feel & touch the data and Consider your sampling plan the people in the process Collect population data This is very important! Get the best “real” data Get as. Much as you can possible Meet with you team and process stakeholders Collect pictures, crib sheets, notes, guides, “post- it” notes Collect primary & Secondary metrics Listen to the process Data Collection Plan Example Data Collection Plan Recording what data you are going to collect reminds you of what you want to accomplish. DATA COLLECTION PLAN How & Where Related Data Sampling Data Description Data Type How Measured* Recorded (Data to Capture** Plan Collection Instrument) See CS VSM Refer to date on CS What is your Lead Time Cont. Hours for details VSM plan for starting # of Clerk s Wait Time Cont. Minutes data collection? Time of day An operational Machine # Jams Discrete Count Preserve time element definition defines Shift exactly how to What stratification collect and record factors and a particular Measurement System Validation/Gage R&R Comments potential causes, do measurement you want to monitor as you collect data? Sample size calculations: Discrete: n=(2/d)2(p)(1-p) Consider the Continuous: n=(2s/d)2 6M’s: Noting the type *Include the unit of measure and perform measurement system validation 1. Machine of data helps you **Related data to capture are factors that you anticipate using for C&E Analysis 2. Method decide how you 3. Material How will you ensure consistency? What will 4. Manpower should analyze you do to make sure the data collected at 5. Measurement the data one point in time is comparable to data 6. Mother Nature collected at other times?