AMT-127 Engine Components And Accessories PDF
Document Details
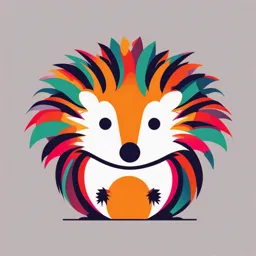
Uploaded by PromisedGyrolite3591
Canadore College
Tags
Summary
This document provides information on the components of an engine, particularly airplane engines, including bearings, crankshafts, and other relevant details. The content is suitable for professional learning or studying mechanical engineering. It is not an exam paper.
Full Transcript
AMT ‐ 127 Engine Components and Accessories Bearings Minimum friction and maximum wear Revolve (roller) and support (plain) Strong yet allow free movement Must hold parts in exact positions with tight tolerances Thrust loads‐ thrust bearings R...
AMT ‐ 127 Engine Components and Accessories Bearings Minimum friction and maximum wear Revolve (roller) and support (plain) Strong yet allow free movement Must hold parts in exact positions with tight tolerances Thrust loads‐ thrust bearings Radial loads or combination of both require ball bearings Thrust and Radial loads Plain Bearing Usually radial loads‐ if flanged can be used for thrust Connecting rods, crank and cam shafts on low powered opposed engines Silver, bronze, lead, alloys Common style is steel backed with silver with a thin layer of lead applied to the actual bearing surface. (bronze backed with lead or babbitt) Bronze high compressive but Babbitt better for friction Roller Bearing Antifriction bearing for radial or thrust Straight roller radial loads Tapered roller for thrust and radial The Race is the guide or channel in which the rollers travel Roller situated between inner and outer race Race made of case hardened steel Used as main brgs. To support crankshaft Ball Bearings Least rolling friction of all bearings Good for all loads especially heavy thrust loads. Inner and outer race with polished steel balls and a ball retainer (spaced) Thrust in a certain direction will have a heavier race, thus req. proper installation Main bearings and small accessories Some prelubricated and sealed, care not to damage seals on installation and removal Crankshaft The crankshaft is the backbone of the reciprocating engine. It is subjected to most of the forces developed by the engine. Main purpose is to change reciprocating motion (piston/connecting rod) to rotary for propeller Shaft composed of one or more cranks or throws, forged then machined SAE 4330 (steel alloy strong) One or more pieces Crankshaft Crankshaft main bearing must be supported rigidly in the crankcase. Usually accomplished by means of transverse webs in the crankcase. One for each main bearing. The webs form an integral part of the structure and in addition to supporting the main bearings add to the strength of the entire case. Web Types of Crankshafts Four Principle Types: 1. Single throw 2. Double throw 3. 4 throw 4. 6 throw Higher output engines would require better balanced and wear ability Single‐throw‐ position of crank 360 degrees Single row radial 2 bearings in single or two‐piece Single must be used with split master rod Two‐piece‐ clamp type (split‐clamp) front section has main brg. Journal, check and weights. Rear has joined sections, weights and journal Two‐piece‐ spline, split in crankpin male/female spines and bolt Double Throw Crankshaft 180 degree crankshaft Usually twin‐row 1 throw for each bank Construction 1 or 3 piece and brgs. May be ball or roller Four‐Throw In‐line 4”s, opposed 4’s and V 8’s In‐line and opposed 2 throws are 180 from the other 2 throws 3‐5 main journals Plain split shell brg. Drilled oil passages in checks Six‐Throw 6 cylinder in‐line, V 12 and 6 cylinder opposed 6 opposed common‐ 60 degree crank, one piece, 4340 forging, 4 main journals and one double flanged main‐thrust journal Static/dynamic balanced, shipped with weights no interchange Weight reduction‐ crank hollow and plugged, recessed crankpins Oil tubes in shaft Main journal‐ or called main bearing journal, supported by and rotates in bearings Carries load Maintains alignment Surface hardened by nitrating 0.015‐0.025 depth reduce wear All engines have 2 or more Main Bearings Piston Engine Components continued https://www.youtube.com/watch?v=jdW1t8r8qYc&t=49s Crankpin Connecting‐rod bearing journal (throw) Crankshaft rotates when force applied to pin Hollow for weight, passage for lubrication, sludge and carbon Lubrication by drilled passages from main journals During overhaul important to make sure all passages and sludge chamber clean Crank Cheek Crank arm connects crankpin to main journal Used to support a counterweight to balance the crankshaft Drilled passages Rigid construction Crankshaft Balance Excessive vibration results in fatigue failure of the metal structures and can cause moving parts to wear rapidly. In an engine, excessive vibration can because by a crankshaft that's not balanced. Crankshaft is statically balanced when the weight of the entire assembly of crank pins crank cheeks and flyweights is balanced around the axis of rotation. This is done by placing the crankshaft on two knife edges. Run out is checked at overhaul because a bent crankshaft will be out of static balance Counterweights Static balance for crankshaft More than 2 throw does not always need counter weights (balanced by the throws) Single throw must have counterweights Crankshaft Dynamic Balance A crankshaft is dynamically balanced when all the forces created by the crankshaft rotation and power impulses are balanced within themselves so that little or no vibration is produced when the engine is operating Dynamic Dampers Relieve vibration caused by the rotation of the crank Suspended or installed in specified crank cheeks or placing floating dampers in counter weights Vibrations caused by power impulses of the engine match natural vibration of crankshaft and propeller as a unit Weight free to move in a direction and at a frequency that dampen natural frequency of shaft Note: A dynamic dampener is essentially a pendulum Moveable slotted steel counter weights (mode #)