AMT-1206-PRELIM-MODULE-NO.3.docx
Document Details
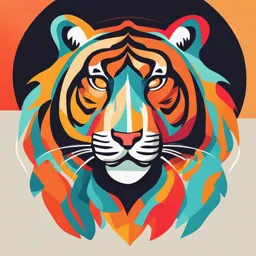
Uploaded by HaleSuccess9635
Full Transcript
**AMT 1206 -- Aircraft Powerplant II (Turbo prop & Jet Engine)** **Prelim Module 2** **Types of Gas Turbine Engine** **\ AMT Instructor** **TABLE OF CONTENTS** Title Ref. no Page ----------------------------- ------------- ------ Types of Gas Turbine Engine...
**AMT 1206 -- Aircraft Powerplant II (Turbo prop & Jet Engine)** **Prelim Module 2** **Types of Gas Turbine Engine** **\ AMT Instructor** **TABLE OF CONTENTS** Title Ref. no Page ----------------------------- ------------- ------ Types of Gas Turbine Engine 1 3 Turbo Jet Engine 1 4 Turbo Prop Engine 1 5 Turbo Fan Engine 1 7 Turbo Shaft Engine 1, 2, 3 & 4 9 Activity 12 **TABLE OF REFERENCES** References No. ------------------------------------------------------------------------------------------------------------- ----- Aircraft Gas Turbine Engines Types https://www.aircraftsystemstech.com/p/gas-turbine-engines-types-and.html 1 Turbo Shaft Engine https://www.skybrary.aero/index.php/Turboshaft\_Engine 2 Turbo Shaft https://www.britannica.com/technology/turboshaft 3 Main Types of Aircraft Jet Engines https://www.aircraftcompare.com/blog/types-of-aircraft-engines/ 4 **TIMEFRAME:** You should be able to complete this module including all the self-assessments, research works, assignments, and other performance tasks within **3.93 hours** **Introduction** This module will tackle the Different Types of Gas Turbine Engine and its Operations ***\ Types of Gas Turbine Engine*** In a [reciprocating engine](https://www.aircraftsystemstech.com/p/reciprocating-engines-designand.html), the functions of intake, compression, combustion, and exhaust all take place in the same combustion chamber. Consequently, each must have exclusive occupancy of the chamber during its respective part of the combustion cycle. A significant feature of the gas turbine engine is that separate sections are devoted to each function, and all functions are performed simultaneously without interruption. A typical gas turbine engine consists of: 1. [An air inlet](https://www.aircraftsystemstech.com/p/air-entrance.html), 2. [Compressor section](https://www.aircraftsystemstech.com/p/compressor-section-compressor-section.html), 3. [Combustion section](https://www.aircraftsystemstech.com/p/combustion-section-combustion-section.html), 4. [Turbine section](https://www.aircraftsystemstech.com/p/turbine-section-turbine-transforms.html), 5. [Exhaust section](https://www.aircraftsystemstech.com/p/exhaust-section-exhaust-section-of-gas.html), 6. [Accessory section](https://www.aircraftsystemstech.com/p/gas-turbine-accessory-section.html) and 7. The systems necessary for starting, lubrication, fuel supply, and auxiliary purposes, such as anti-icing, cooling, and pressurization. The major components of all gas turbine engines are basically the same; however, the nomenclature of the component parts of various engines currently in use varies slightly due to the difference in each manufacturer's terminology. These differences are reflected in the applicable maintenance manuals. One of the greatest single factors influencing the construction features of any gas turbine engine is the type of compressor or compressors for which the engine is designed. Turbine engines are classified according to the type of compressors they use. There are three types of compressors---centrifugal flow, axial flow, and centrifugal-axial flow. Compression of inlet air is achieved in a centrifugal flow engine by accelerating air outward perpendicular to the longitudinal axis of the machine. The axial-flow engine compresses air by a series of rotating and stationary airfoils moving the air parallel to the longitudinal axis. The centrifugal-axial flow design uses both kinds of compressors to achieve the desired compression. The path the air takes through the engine and how power is produced determines the type of engine. Four types of gas turbine engines are used to propel and power aircraft. They are the turbojet, turbofan, turboprop, and turboshaft. ### Turbojet The term "turbojet" was used to describe any gas turbine engine used in aircraft. As gas turbine technology evolved, these other engine types were developed to take the place of the pure turbojet engine. A turbojet engine was first developed in Germany and England prior to World War II and is the simplest of all jet engines. The turbojet engine has problems with noise and fuel consumption in the speed range that airliners fly (.8 Mach). These engines are limited on range and endurance and today are mostly used in military aviation. The turbojet engine consists of four sections---compressor, combustion chamber, turbine section, and exhaust. The compressor section passes inlet air at a high rate of speed to the combustion chamber. The combustion chamber contains the fuel inlet and igniter for combustion. The expanding air drives a turbine, which is connected by a shaft to the compressor, sustaining engine operation. The accelerated exhaust gases from the engine provide thrust. This is a basic application of compressing air, igniting the fuel-air mixture, producing power to self-sustain the engine operation, and exhaust for propulsion. turbine engine type Advantages of turbojet engine; - Relatively simple design - Capable of very high speeds Disadvantages of turbojet engine; - High fuel consumption - Loud ### ### Turboprop Between 1939 and 1942, a Hungarian designer, Gyorgy Jendrassik designed the first turboprop engine. However, the design was not implemented into an actual aircraft until Rolls Royce converted a Derwint II into the RB50 Trent which flew on September 20, 1945 as the first turboprop jet engine. The turbopropeller (turboprop) engine is a combination of a gas turbine engine, reduction gear box, and a propeller. Turboprops are basically gas turbine engines that have a compressor, combustion chamber(s), turbine, and an exhaust nozzle (gas generator), all of which operate in the same manner as any other gas engine. However, the difference is that the turbine in the turboprop engine usually has extra stages to extract energy to drive the propeller. In addition to operating the compressor and accessories, the turboprop turbine transmits increased power forward through a shaft and a gear train to drive the propeller. The increased power is generated by the exhaust gases passing through additional stages of the turbine.  A turboprop engine is a turbine engine that drives a propeller through a reduction gear. The exhaust gases drive a power turbine connected by a shaft that drives the reduction gear assembly. Reduction gearing is necessary in turboprop engines because optimum propeller performance is achieved at much slower speeds than the engine's operating rpm. Turboprop engines are a compromise between turbojet engines and reciprocating powerplants. Turboprop engines are most efficient at speeds between 250 and 400 mph and altitudes between 18,000 and 30,000 feet. They also perform well at the slow airspeeds required for takeoff and landing and are fuel efficient. The minimum specific fuel consumption of the turboprop engine is normally available in the altitude range of 25,000 feet to the tropopause. Approximately 80 to 85 percent of the energy developed by the gas turbine engine is used to drive the propeller. The rest of the available energy exits the exhaust as thrust. By adding the horsepower developed by the engine shaft and the horsepower in the exiting thrust, the answer is equivalent shaft horsepower. aircraft turbine engine type Some engines use a multirotor turbine with coaxial shafts for independent driving of the compressor and propeller. Although there are three turbines utilized in this illustration, as many as five turbine stages have been used for driving the two rotor elements, propeller, and accessories. The exhaust gases also contribute to engine power output through thrust production, although the amount of energy available for thrust is considerably reduced. Two basic types of turboprop engine are in use: fixed turbine and free turbine. The fixed turbine has a mechanical connection from the gas generator (gas-turbine engine) to the reduction gear box and propeller. The free turbine has only an air link from gas generator to the power turbines. There is no mechanical link from the propeller to the gas turbine engine (gas generator). Since the basic components of normal gas-turbine and turboprop engines differ slightly only in design features, it should be fairly simple to apply acquired knowledge of the basic gas turbine to the turboprop. The typical turboprop engine can be broken down into assemblies as follows: 1. The power section assembly---contains the usual major components of a gas turbine engine (i.e., compressor, combustion chamber, turbine, and exhaust sections). 2. The reduction gear or gearbox assembly---contains those sections unique to turboprop configurations. 3. The torque meter assembly---transmits the torque from the engine to the gearbox of the reduction section. 4. The accessory drive housing assembly---mounted on the bottom of the compressor air inlet housing. It includes the necessary gear trains for driving all power section driven accessories at their proper rpm in relation to engine rpm. There are advantages and disadvantages of each system, with the airframe generally dictating the system used. Advantages of turboprop engine; - Very fuel efficient - Most efficient at mid-range speed between 250-400 knots - Most efficient at mid-range altitudes of 18,000-30,000 feet Disadvantages of turboprop engine; - Limited forward airspeed - Gearing systems are heavy and can break down ### Turbofan Turbofans were developed to combine some of the best features of the turbojet and the turboprop. Turbofan engines are designed to create additional thrust by diverting a secondary airflow around the combustion chamber.  So, almost all airliner-type aircraft use a turbofan engine. It was developed to turn a large fan or set of fans at the front of the engine and produces about 80 percent of the thrust from the engine. This engine was quieter and has better fuel consumption in this speed range. Turbofan engines have more than one shaft in the engine; many are two-shaft engines. This means that there is a compressor and a turbine that drives it and another compressor and turbine that drives it. These two shafted engines use two spools (a spool is a compressor and a shaft and turbines that driven that compressor). In a two-spool engine, there is a high-pressure spool and a low-pressure spool. The low-pressure spool generally contains the fan(s) and the turbine stages it takes to drive them. The high-pressure spool is the high-pressure compressor, shaft, and turbines. This spool makes up the core of the engine, and this is where the combustion section is located. The high-pressure spool is also referred to as the gas generator because it contains the combustion section. Turbofan engines can be low bypass or high bypass. The amount of air that is bypassed around the core of the engine determines the bypass ratio. As can be seen in Figure, the air generally driven by the fan does not pass through the internal working core of the engine. The amount of air flow in lb/sec from the fan bypass to the core flow of the engine is the bypass ratio. Bypass ratio = [100 lb/sec flow fan] = 5:1 bypass ratio              20 lb/sec flowcore Some low-bypass turbofan engines are used in speed ranges above.8 Mach (military aircraft). These engines use augmenters or afterburners to increase thrust. By adding more fuel nozzles and a flame holder in the exhaust system extra fuel can be sprayed and burned which can give large increases in thrust for short amounts of time. Two different exhaust nozzle designs are used with turbofan engines. The air leaving the fan can be ducted overboard by a separate fan nozzle, or it can be ducted along the outer case of the basic engine to be discharged through the mixed nozzle (core and fan exhaust together). The fan air is either mixed with the exhaust gases before it is discharged (mixed or common nozzle), or it passes directly to the atmosphere without prior mixing (separate nozzle). Turbofans are the most widely used gas turbine engine for air transport aircraft. The turbofan is a compromise between the good operating efficiency and high thrust capability of a turboprop and the high speed, high altitude capability of a turbojet. Advantages of turbofan engine; - Fuel efficient - Quieter than turbojets - They look awesome Disadvantages of turbofan engine; - Heavier than turbojets - Larger frontal area than turbojets *\ * ### Turboshaft The fourth common type of jet engine is the turboshaft. It delivers power to a shaft that drives something other than a propeller. The biggest difference between a turbojet and turboshaft engine is that on a turboshaft engine, most of the energy produced by the expanding gases is used to drive a turbine rather than produce thrust. Many helicopters use a turboshaft gas turbine engine. In addition, turboshaft engines are widely used as auxiliary power units on large aircraft. aircraft turbine engine type With regard to aircraft, the turboshaft engine is a gas turbine engine made to transfer horsepower to a shaft that turns a helicopter transmission or is an onboard auxiliary power unit (APU). An APU is used on turbine-powered aircraft to provide electrical power and bleed air on the ground and a backup generator in flight. Turboshaft engines can come in many different styles, shapes, and horsepower ranges. *\ *A turboshaft engine uses the same principles as a [turbojet](https://www.skybrary.aero/index.php/Turbojet_Engine) to produce energy, that is, it incorporates a compressor, combustor and turbine within the gas generator of the engine. The primary difference between the turboshaft and the turbojet is that an additional power section, consisting of turbines and an output shaft, has been incorporated into the design. In most cases, the power turbine is not mechanically linked to the gas generator. This design, which is referred to as a \"free power turbine\", allows the speed of the power turbine to be optimised for the machinery that it will energize without the need for an additional reduction gearbox within the engine. The power turbine extracts almost all of the energy from the exhaust stream and transmits it via the output shaft to the machinery it is intended to drive. A turboshaft engine is very similar to a [turboprop](https://www.skybrary.aero/index.php/Turboprop_Engine) and many engines are available in both variants. The principal difference between the two is that the turboprop version must be designed to support the loads of the attached [propeller](https://www.skybrary.aero/index.php/Propeller) whereas a turboshaft engine need not be as robust as it normally drives a transmission which is structurally supported by the vehicle and not by the engine itself.  The 5 Main Types of Aircraft Jet Engines - Aircraft Compare Turboshaft aircraft engines are commonly used on helicopters. The only difference between turbojets and turboshafts is that the latter uses much of their power for turning a turbine instead of producing thrust. The turboshaft engine is similar to a turbojet engine, but it has a large shaft that connects the front to the back. Since most of the turboshaft engines are used on helicopters, the shaft connects to the transmission of the rotor blade. Advantages of turboshaft engine; - Much higher power-to-weight ratio than piston engines - Typically smaller than piston engines Disadvantages of turboshaft engine; - Loud - Gear systems connected to the shaft can be complex and break down ***Enrichment Activity (essay form)*** ***\ You should be able to complete the activity within 30 minutes.*** ***1. Give and explain the process of each types of Gas Turbine Engine*** ***-*** ***-*** ***-*** ***-*** Students name and signature Parent / guardian signature ======================================================= **RESEARCH/ESSAY RUBRICS** **CONTENT (70%)** --------------------------------------------------------- ---- ---- --- --- --- --------- --- *KNOWLEDGE ON THE TOPIC* C1 35 *INFORMATION BASED ON TECHNICAL MANUALS/JOURNALS/BOOKS* C2 25 *QUALITY OF INFORMATION* C3 10  **70**         **FORMAT (30%)** FORMAT BASED ON THE GIVEN INSTRUCTIONS F1 5 GRAMMAR, USAGE, SPELLING F2 5 *WORD COUNT& QUALITY OF WRITING* F3 20       **30**  **100**