All Notes Test 1 PDF
Document Details
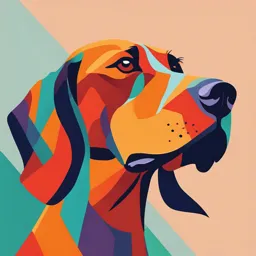
Uploaded by MemorableAgate1690
Tags
Summary
This document is a collection of notes about total quality management (TQM). It covers key characteristics, elements, and concepts of the approach. The notes also include video questions about a specific company (CFA).
Full Transcript
Chapter 1 – The Total Quality Approach to Quality Management Quality has been defined in a number of ways. When viewed from a consumer’s perspective, it means meeting or exceeding customer expectations. Total quality is an approach to doing business that attempts to maximize an organization’s com...
Chapter 1 – The Total Quality Approach to Quality Management Quality has been defined in a number of ways. When viewed from a consumer’s perspective, it means meeting or exceeding customer expectations. Total quality is an approach to doing business that attempts to maximize an organization’s competitiveness through the continual improvement of the quality of its products, services, people, processes, and environments. What does it mean to continually improve? Why might you want to continually improve? What about a company? Video Questions: What are some things CFA uses to differentiate itself from other fast food restaurants? What are some aspects of quality that CFA might use to measure success? For each of these aspects, how might they measure it? How do we know that their strategy is working? Key characteristics of the total quality approach are as follows: Strategically based Customer focus Obsession with quality Scientific approach Long-term commitment Teamwork Employee involvement and empowerment Continual process improvement Bottom-up education and training Freedom through control Unity of purpose. The key elements of total quality: Strategically-based - Total quality organizations have a comprehensive strategic plan that contains at least the following elements: vision, mission, broad objectives, and activities that must be completed to accomplish the broad objectives. The strategic plan for a total quality organization is designed to give it a sustainable competitive advantage in the marketplace. Customer Focus - In a total quality setting, the customer is the driver. This applies to both internal and external customers. Obsession with Quality - This means all personnel at all levels approach all aspects of the job from the perspective of "How can we do this better?" When an organization is obsessed with quality, good enough is never good enough. Scientific Approach - While it is true that people skills, involvement, and empowerment are important in a total quality setting, they represent only a part of the equation. Another important part of the equation is the use of the scientific approach in structuring work and in decision making and problem solving that relates to the work. Long-Term Commitment - Organizations that implement management innovations after attending short-term seminars often fail in their initial attempt to adopt the total quality approach. This is because they approach total quality as just another management innovation rather than as a whole new way of doing business that requires a whole new corporate culture. Teamwork- Internal competition tends to use energy that should be focused on improving quality, and, in turn, external competitiveness. Continual Improvement of Systems - In order to continually improve the quality of products or services: which is a fundamental goal in a total quality setting. It is necessary to continually improve systems. Continual Process Improvement - Products are developed and services are delivered by people using processes within environments (systems). To continually improve the quality of products and services—which is a fundamental goal in a total quality setting—it is necessary to continually improve the processes that make up the organization’s systems. Education and Training - Education and training are fundamental to total quality because they represent the best way to improve people on a continual basis. In a total quality organization, everyone is constantly learning. Freedom through Control - Involving and empowering employees is fundamental to total quality as a way to simultaneously bring more minds to bear on the decision making process and increase the ownership employees feel in decisions that are made. The freedoms enjoyed in a total quality setting are actually the result of well-planned and carried out controls. Unity of Purpose - In order to apply the total quality approach, organizations must have unity of purpose. Collective bargaining is about wages, benefits, and working conditions, not about corporate purpose and vision. Employees should feel more involved and empowered in a total quality setting than in a traditionally managed situation, but the goal of total quality is to enhance competitiveness not to eliminate unions. Employee involvement - The basis for involving employees increases the likelihood of a good decision1 a better plan, or a more effective improvement by bring more minds to bear on the situation: not just any minds, but the minds of the people who are closest to the work in quest. It also promotes ownership of decisions by involving the people who will have to implement them. Empowerment means not just involving people but involving them in ways that give them a real voice. Peak Performance - When effectively practiced, total quality allows every aspect of an organization to operate at peak levels. This means that personnel and processes operate at their best. Peak performance is essential to organizations that operate in a global environment where competition is intense, constant, and unforgiving. The rationale for total quality can be found in the need to compete in the global marketplace. Countries that are competing successfully in the global marketplace are seeing their quality of living improve. Those that cannot are seeing theirs decline. Firms improve from the pressure of competition!!! Explain the rationale for the total quality approach to doing business. Total quality is not just one individual concept. It is a number of related concepts pulled together to create a comprehensive approach to doing business. Many people contributed in meaningful ways to the development of the various concepts that are known collectively as total quality. But Professor Parker, that value is derived from better Marketing – you know the really cool cow commercials? I wore a suit to eat and got a free meal! Marketing cannot make a Burger King chicken sandwich as good as a Chick-fil-a sandwich. You have to have something good (high quality, consistent, etc.) to market or the customer will not pay you a premium for it. Why does a firm exist? → “It’s all about the Benjamins” W. Edward Deming is best known for his ○ Fourteen Points - describe what is necessary for a business to survive and be competitive today. They summarize what a company must do to effect a positive transition from business-as-usual to world-class performance. They contain the essence of all of Dr. Deming's teachings and are the heart of his philosophy. 1. Create constancy of purpose toward the improvement of products and services in order to become competitive, stay in business, and provide jobs. 2. Adopt the new philosophy. Management must learn that it is a new economic age and awaken to the challenge, learn their responsibilities, and take on leadership for change. 3. Stop depending on inspection to achieve quality. Build in quality from the start. 4. Stop awarding contracts on the basis of low bids. 5. Improve continuously and forever the system of production and service, to improve quality and productivity, and thus constantly reduce costs. 6. Institute training on the job. 7. Institute leadership. The purpose of leadership should be to help people and technology work better. 8. Drive out fear so that everyone may work effectively. 9. Break down barriers between departments so that people can work as a team. 10. Eliminate slogans, exhortations, and targets for the workforce. They create adversarial relationships. 11. Eliminate quotas and management by objectives—substitute leadership. 12. Remove barriers that rob employees of their pride of workmanship. 13. Institute a vigorous program of education and self-improvement. 14. Make the transformation everyone's job and put everyone to work on it. ○ The Deming Cycle - developed to link the production of a product with consumer needs and focusing the resources of all departments (research, design, production, and marketing) in a cooperative effort to meet those needs 1. Conduct consumer research and use it in planning the product (plan). 2. Produce the product (do). 3. Check the product to make sure it was produced in accordance with the plan (Check). 4. Market the product (act). 5. Analyze how the product is received in the marketplace in terms of quality, cost, and other criteria, or how it measures up against expectations (analyze). ○ The Seven Deadly Diseases - Sins summarize Dr. Deming's views on what can inhibit the transformation from business-as-usual to worldclass quality. 1. Lack of constancy of purpose to pan products and services that have a market sufficient to keep the company n business and provide jobs. 2. Emphasis on short-term profits; short4erm thinking that is driven by a fear of unfriendly takeover attempts and pressure from bankers and shareholders to produce dividends. 3. Personal review systems for managers and management by objectives without providing methods of resources to accomplish objectives. Performance evaluations, merit ratings, and annual appraisals are all part of it - its disease. 4. Job hopping by managers. 5. Using only visible data and information in decision making with little or no consideration given to what is not known or cannot be known. 6. Excessive medical costs. 7. Excessive costs of liability driven up by lawyers who work on contingency fees. Joseph M. Juran is best known for ○ Juran’s Three Basic Steps to Progress - broad steps that, in Juran's opinion, companies must take if they are to achieve world-class quality. He also believes there is a point of diminishing return that applies to quality and competitiveness. 1. Achieve structured improvements on a continual basis combined with dedication and a sense of urgency. 2. Establish an extensive training program. 3. Establish commitment and leadership on the part of higher management Continual structured improvements Extensive training (or continuous learning) Higher Management commitment and leadership Ex: Philip Morris mug story ○ Juran’s Ten Steps to Quality Improvement - Ten steps which overlap with Deming's Fourteen Points. They mesh well with the philosophy of quality experts. Slide Version 1. Awareness 2. Improvement goals 3. Organization 4. Training 5. Problem solving projects 6. Progress reports 7. Recognition 8. Communicating results 9. Monitor (keep score) 10.Build-in all improvements Speaker Notes Version 1.Build awareness of both the need for improvement and opportunities for improvement. 2.Set goals for improvement. 3.Organize to meet the goals that have been set. 4.Provide training. 5.Implement projects aimed at solving problems. 6.Report progress. 7.Give recognition. 8.Communicate results. 9.Keep score. 10.Maintain momentum by building improvement into the company's regular systems. ○ the Pareto Principle Organizations should concentrate their energy on eliminating the vital few sources that cause the majority of problems Sometimes called the 80/20 rule 80% of the trouble comes from 20% of the problems Though named for turn-of-the-century economist, Vilfredo Pareto, it was Dr. Juran who applied this idea to management Dr. Juran advises us to concentrate on the vital few sources of problems and not be distracted by those of lesser importance. ○ the Juran Trilogy - summarizes the three primary managerial functions. They are: Quality Planning, Quality Control, and Quality Improvement Quality Planning Who are the customers? What are their needs? Develop products with features to meet those needs. Develop systems and processes to provide those features. Execute those plans. Quality Control Assess the quality performance Compare performance with goals Bridge the gap” Quality Improvement Put in infrastructure to improve annually Improve specific areas Use project teams for these improvements Provide the teams the resources they need Common errors made when starting quality initiatives include: Senior management delegation and poor leadership ○ Why is the organization doing this? Team mania The deployment process A narrow, dogmatic approach Conflicting priorities Confusion about the differences among education, awareness, inspiration, and skill building. Speaker Notes Summarize the most common errors made when starting quality initiatives. Senior management delegation and poor leadership Team mania Deployment process Taking a narrow dogmatic approach Confusion about the differences among education, awareness, inspiration, and skill building. Trends affecting the future of quality management include: Demanding global customers ○ Ex: Does anyone still go to the Mall? Shifting customer expectations ○ Ex: Why are fast food chains offering “healthy” alternatives? Opposing economic pressures ○ Ex: Can a firm be low cost, differentiated and innovative? New approaches to management ○ Ex: Neanderthal management Speaker Notes Explain the trends that are affecting the future of quality management are as follows: Increasing global competition. Today’s customers share two common characteristics: ○ 1) they are part of regional trade alliances ○ 2) they expect both high quality and added value. Increasing customer expectations ○ Customers want an excellent product or service from an organization that also provides accurate billing, reliable delivery, and after purchase support. Opposing economic pressures ○ The global marketplace exerts enormous unrelenting pressure on organizations to continually improve quality while simultaneously reducing the prices they charge for goods and services. New approaches to management ○ Companies that succeed in the global marketplace have learned that you manage budgets, but lead people. Quality = meeting or exceeding customer expectations Some TQM ideas on this: “the customer defines quality” “the customer is always right” “the customer always comes first” “the customer is king” “quality begins and ends with the customer” That all sounds really cool but... You can have a lot of diverse customers Customer preferences change Daughter Becca – “Email is how old people communicate” Some customers are... difficult Some customers have different goals from the firm Ex: Distributors or resellers Customers struggle to articulate problems Firms have a finite amount of money Ultimately, this is hard to do but we will talk more about how to do this in coming chapters. Chapter 1 Review Questions Question 1 Quality deals not only products and services but also includes people, processes, and environments. (T or F) True Question 2 Peak performance is essential to organizations that operate in a globally competitive environment. (T or F) True Question 3 One focus of Joseph M. Juran was on the Pareto rinciple which states that a company must address and eliminate all areas of errors rather than concentrate on a few. (T or F) False Question 4 What functions/areas are a part of the Juran Trilogy? 1. Quality Planning 2. Quality Control 3. Quality Improvement Question 5 Philip Crosby’s Quality Vaccine consists of what 3 ingredients? 1. Determination 2. Education 3. Implementation Chapter 2 - Quality and Global Competitiveness Major Topics The Relationship between Quality and Competitiveness Cost of Poor Quality Competitiveness and the U.S. Economy Factors Inhibiting Competitiveness Comparisons of International Competitors Human Resources and Competitiveness What is Globalization? Characteristics of World-Class Organizations Management by Accounting, Antithesis of Total Quality U.S. Companies: Global Strengths and Weaknesses Quality Management Practices in Asian Countries. What is Globalization? Globalization is a process of interaction and integration among the people, companies, and governments of different nations, a process driven by international trade and investment and aided by information technology. What are some good things about Globalization? What are some bad things about Globalization? For a firm, Global competition requires a firm to continuously improve! The relationship between quality and competitiveness can be summarized as follows: In a modern global marketplace, quality is the key to competitiveness. Why? What are some issues faced when competing globally? Explain the relationship between quality and competitiveness. Companies that used to compete only on a local, regional, or national level now find themselves competing against companies from throughout the world. Some of these companies find the competition to be more intense than any they have ever encountered. Those who are able to produce world-class quality can compete at this level. The costs of poor quality include the following: waste, rejects, retesting, rework, customer returns, inspection, recalls, excessive overtime, pricing errors, billing errors, excessive turnover, premium freight costs, development cost of the failed product, field service costs, overdue receivables, handling complaints, expediting, system costs, planning delays,… Explain how the cost of poor quality can affect competitiveness. The need to improve an organization’s financial condition correlates directly with the process of making and measuring quality improvements. Lower deficiencies will lead to lower total costs. Improvements in product or service features can lead to higher market share at a better price, which means higher revenue. …late paperwork, lack of follow-up, excess inventory, customer allowances, and unused capacity. What does this mean practically? Profit = Sales – Costs Typically about 1/20th of a Sales or Revenue dollar goes to profit after costs. (Ex: 5% Return on Sales) Key concept: $1 of cost savings goes straight to profit!!! ○ Ex: Co-op presentation at Philip Morris on new device to improve cigarette quality. The United States came out of World War II as the only major industrialized nation with its manufacturing sector completely intact. Germany and Japan were devastated by damage during the war. Germany and Japan rebuilt their manufacturing bases on the assumption that to compete globally, they would have to produce goods of world-class quality. That strategy helped them recover and become world leaders in manufacturing. Describe the evolution of the rebuilding effort undertaken by Japan and Germany following World War II. As Japanese and German manufacturers rebuilt, two things became apparent to them: 1) In order to succeed, they would have to compete globally; and 2) In order to compete globally; they would have to produce goods of world-class quality. This meant producing better goods but at reasonable competitive prices. The United States car companies started to see intense competition from small cars in the 1970’s Meet the Ford Pinto!!! Explain the actions of U.S. manufacturers during the same period on which Japan and Germany were rebuilding following World War II. The U.S. came out of World War II as the only major industrialized nation with its manufacturing sector completely intact. A well-oiled manufacturing sector and the availability of abundant raw materials helped the U.S. become the world leader in the production and export of durable goods. This resulted in a period of unparalleled prosperity and one of the highest standards of living ever experienced by any country. While the U.S. was enjoying its position as the world's preeminent economic superpower, the other industrialized nations of the world, particularly Japan and Germany, were busy rebuilding their manufacturing sectors. The U.S. manufacturers were slow to catch on that the game had changed from mass production with acceptable levels of waste to quality production with things done right the first time every time. With foreign companies, through a combination of better people, better technology, and better management began to eat away at markets, U.S. companies, mistakenly seeing cost rather than quality as the issue, learned that quality was the key to success in the global marketplace, Japan, Germany, Taiwan, and Korea had made major inroads into global markets previously dominated by U.S. manufacturers (i.e., steel, automobiles, computers, and consumer electronics). Several factors can inhibit competitiveness, including those related to business and government, family, and education. How does government impact competitiveness? How does education impact competitiveness? Explain how education-related factors can inhibit competitiveness. The quality of a country's education system is a major determinant of the quality of its labor pool. The higher the quality of the labor pool, the higher the quality of entry-level employees. The higher the quality of entry-level employees, the faster they can become productive employees and contribute to the competitiveness of their employers. Consequently, a high-quality education system is an important component of the competitiveness equation. What all this means is that businesses in the U.S. are forced to spend money helping employees learn the basic skills of reading and writing while their competitors are able to devote their training dollars to developing advanced work-related skills. If international competition can be viewed as a footrace, this is the equivalent of forcing U.S. firms to start 100 yards behind the other competitor in a 200-yard race. When making comparisons among internationally competing countries, the following indicators are usually used: ○ Standard of living, ○ Trade and export growth ○ Manufacturing productivity. How does a nation's ability to compete affect its quality of life? A nation's ability to compete in the global marketplace has a direct bearing on the quality of life of its citizens. Because the ability to compete translates into the ability to do a better job of producing quality goods, it is critical that nations and individual organizations within them focus their policies, systems, and resources in a coordinated way on continually improving both quality and competitiveness. Human Development Index (2015): The Human Development Index (HDI) is a composite statistic of life expectancy, education, and income per capita indicators. A country scores higher HDI when the life expectancy at birth is longer, the education period is longer, and the income per capita is higher. It is used to distinguish whether the country is a developed, a developing or an underdeveloped country. Explain how education-related factors can inhibit competitiveness. The quality of a country's education system is a major determinant of the quality of its labor pool. The higher the quality of the labor pool, the higher the quality of entry-level employees. The higher the quality of entry-level employees, the faster they can become productive employees and contribute to the competitiveness of their employers. Consequently, a high-quality education system is an important component of the competitiveness equation. What all this means is that businesses in the U.S. are forced to spend money helping employees learn the basic skills of reading and writing while their competitors are able to devote their training dollars to developing advanced work-related skills. If international competition can be viewed as a footrace, this is the equivalent of forcing U.S. firms to start 100 yards behind the other competitor in a 200-yard race. What are some factors in why these countries have a higher standard of living, life expectancy and better educational opportunities? The most important key in maximizing competitiveness is the human resource. Following World War II, this was the only resource that Germany and Japan had to draw on. Consequently, they built economic systems that encourage private employers to make business decisions that emphasize improved productivity and quality, rather than price. Compare investment and manufacturing productivity in the U.S with investment and manufacturing productivity in Japan. Investment, from the perspective of global competitiveness, is the percent of gross national product spent on education, equipment, facilities, and research and development in the period of 1970-90, Japan led the list of competitive countries, with an investment level of approximately 30 percent. The U.S. invested just over 20 percent during this period. The other countries, taken as a group, invested slightly more than the U.S. when education is removed from the list of investments, the U.S. invested as much or more than all other countries except Canada. However, there is evidence that American dollars invested in education are not used as effectively as those invested by other competing nations. It should be noted also that Japanese investment in equipment began to decline in 1992. During the first three quarters of the twentieth century, the U.S. enjoyed the highest productivity levels in the world. For example, in 1972 U.S. manufacturing productivity was 56 percent better than that of Japan. By 1987, this lead had dwindled to just 6 percent. By 1993, Japan equaled the U.S. in productivity. Some advantages from Germany and Japan social constructs after World War II ○ Cooperation among business, labor and government ○ Cooperation in society as a result ○ High-quality education and training ○ Employee involvement and empowerment ○ Leadership at all levels ○ Teamwork The basic philosophical constructs underlying the human-resource aspects of the competitiveness of both Japan and Germany are explained in the following list: Cooperation among business, labor, and government. The term social partners is used in Japan just as it is in Germany. Prior to the war, this prevailing view among top business executives was very like that of the American rugged individualist. As in Germany, however, the crisis provoked by defeat shifted the balance toward those who believed that business must join with the other major economic actors in the task of rebuilding the society, tying its own goals with the larger interests of the nation as a whole. Cooperation Cooperation that was prompted by the devastation brought by war caught on and became the cornerstone of the competitiveness of both countries. High-quality education and training Germany and Japan take different routes, but they arrive at the same place regarding education and training. Germany uses a highly structured apprenticeship program that emphasizes both skills development and academic achievement. Japan relies on excellent primary and secondary education supplemented by industry-based training to prepare front-line employees. Employee involvement and empowerment In both Germany and Japan, employees are involved in functions traditionally viewed as management functions in the U.S. These functions include setting working hours, introducing new technologies, establishing compensation levels, human-resource planning, work design, and the provision of training. Leadership at all levels In both Germany and Japan, leadership occurs at all levels and leadership training is provided not just for managers but also for front-line employees. This is important in that it tends to improve the quality of employee involvement in continual improvement efforts. Teamwork In Germany and Japan, not only is work done by teams of employees, but the planning and designing of work, introduction of new technologies, and establishment of compensation levels are also done by teams that involve representatives from labor and management. Chapter 2 Review Questions Question 1 A nation's ability to compete in the global marketplace has a direct bearing on the quality of life of its citizens. (T or F) True Question 2 As a company expands geographically from local to regional to national to international markets, the intensity of competition increases but the quality of products decreases.. (T or F) False Question 3 Firms that use management-by-accounting strategies can quickly improve their quality systems through better cost control. (T or F) False Question 4 Industrialization in countries like Japan, South Korea and China really improved as a result of: Adoption of quality management principles in the 1980’s Question 5 According to the textbook, the United States has a number of competitive advantages in the global marketplace including: 1. Strong entrepreneurial spirit 2. Presence of a Small Cap stock market 3. Rapidly advancing technologies 4. Comparatively low taxes 5. Low rate of unionization 6. World class higher education (colleges and universities) Chapter 3 - Strategic Management: Planning and Execution for Competitive Advantage Strategies that organizations can adopt for gaining a sustainable competitive advantage are: ○ Cost leadership (Operational Effectiveness) ○ Differentiation (Customer Orientation) ○ Market-niche (Innovation). Key Concept: A firm cannot be excellent in all of these areas due to limited resources and conflicting incentives. What is strategic management? Strategic management is management that bases all actions, activities, and decisions on what is most likely: within an ethical framework: to ensure successful performance in the marketplace. From the perspective of the strategic manager, resources are wasted unless they contribute to success in the marketplace, and the more direct the contribution, the better. Differentiation Strategy (Innovation) A company that employs a differentiation strategy does so with the intention of creating a product or service that is valued and perceived by its customers as unique and better than the competition. Companies that succeed in implementing a differentiation strategy have one or a combination of the following attributes: ○ Leading scientific research ○ Highly skilled and creative product-development personnel ○ Excellent customer interfaces like a strong sales team or technical team ○ A strong reputation for quality and innovation. They get a premium price for their product or service! What does Hallmark actually sell? What is the profit margin of a Hallmark card? Why do you choose a premium card over a “cheap” one? What are some new features premium cards have added in the last few years? How would you feel if the person opening the card had “quality problems” with it? Cost Leadership Strategy (Operational Effectiveness) Cost leadership is a concept developed by Michael Porter, used in business strategy. It describes a way to establish the competitive advantage. Cost leadership, in basic words, means the lowest cost of operation in the industry. Companies that succeed in implementing a cost leadership strategy have one or a combination of the following attributes: ○ Continuous improvement ○ Cost control throughout the value chain (suppliers, internal, customers, information systems, etc.) ○ May or may not emphasize quality (Costco vs. cheap disposable product) ○ Monitor costs rigorously and effectively ○ Products are typically commoditized They maximize profit by taking market share via being the low cost provider! Why do people shop at Walmart? Is Walmart under any type of competitive pressure? How did Walmart get such low prices? What do you think they are really, really good at doing? What is it like being a supplier for Walmart? My wife will NOT go to Walmart? Why not? Market-niche Strategy (Customer Focus) A company that employs a Market-niche or customer focus provides a good or service with features that appeal to a particular smaller market subgroup. A typical product marketed using a niche strategy will be easily distinguished from other products, and it will also be produced and sold for specialized uses within its corresponding niche market. Companies that succeed in implementing a market-niche strategy have one or a combination of the following attributes: Approaches that provide excellent customer feedback and interface Fast response to market Strong marketing programs for specific customers Avoid direct competition with cost leaders (try to avoid notice) They find unique, unmet customer needs and fill them or problems and solve them! What is the “unmet market need” being met by this paint? This is very cool technology yet it only sells a miniscule market share of paint? Why? How can a firm make money in small, niche markets? Why does a small paint company choose a small niche market? Why can’t Hallmark, Walmart and Sto Corp. pursue all three strategies at the same time? Different incentives Different focus of activities Different leadership – who (what department or group) would lead each type of strategic effort in these three types of strategies? Mixed messages to employees Mixed messages to customers (Ex: Walmart store selling high end Italian suits) UGA Strategic Directions: Building on Excellence in Undergraduate Education Enhancing Graduate and Professional Programs Investing in Proven and Emerging Areas of Research Excellence Serving the Citizens of the State of Georgia and Beyond Improving Faculty Recognition, Retention, and Development Improving and Maintaining Facilities and Infrastructure Improving Stewardship of Natural Resources and Advancing Campus Sustainability Put together and measured by Academic Planning (http://oap.uga.edu/strategic_planning/) The mission of Academic Planning is to provide vision and leadership for evidence-based decision making at the University of Georgia. The central elements of this mission are: ○ Continuous improvement of UGA’s programs through systematic assessment of established outcomes ○ Accurate and timely analysis of institutional data for decision making purposes; ○ Coordination of the University’s accreditation process; and ○ Implementation of the UGA strategic plan for 2020. (http://oap.uga.edu/about_oap/) To accomplish its mission, Academic Planning: Plans and implements strategies to assess the extent to which the University achieves its mission and strategic goals. Integrates data and planning information in budget and resource allocation processes. Collects, organizes, maintains, and analyzes institutional and other data to support University management, operations, decision making, and planning. Coordinates a comprehensive system of evaluation for all programs and units that contribute to the mission and strategic goals of the University. Promotes the implementation of improvements identified through assessment and evaluation. Maintains ongoing relationships with the Southern Association of Colleges and Schools Commission on Colleges and facilitates the process of reaffirmation of accreditation. Integrates, to the extent possible, internal evaluation processes with external accrediting and reporting needs. The mission of Academic Planning is to provide vision and leadership for evidence-based decision making at the University of Georgia. (http://oap.uga.edu/about_oap/) What you see here with UGA is very common. What might be some barriers to execution of this plan or even criticisms from your perspective? It has some language all employees might not know. It has a lot of detail. It is trying to unify a lot of disparate ideas and concepts. How might you improve it? Strategies are approaches adopted by organizations to ensure successful performance in the marketplace. Core competencies are things an organization develops so well they can be viewed as providing a competitive advantage. List the steps in the strategic planning process. SWOT Analysis, Develop the Vision, Develop the Mission, Develop the Guiding Principles, Develop the Broad Strategic Objectives, and Develop the Specific Tactics What is a core competency? A core competency is anything an organization does so well that it can be viewed as a competitive advantage. An organization’s core competencies might be based on its ability to achieve economy of scale, proprietary access to a given technology, expertise that is difficult to replicate, the ability to maintain world-class performance from critical processes, market proximity, a high-performance corporate culture, research and development expertise, the ability to respond rapidly to market research, or any other factor that contributes directly and significantly to the organization’s ability to provide superior value consistently over time. What do you think are some things that Apple does really, really well? The Apps are where it is at Ease of use – Intuitive design Beautiful, elegant store design Well trained, excellent Genius Bar staff Jerry Haller – “their stuff just works” What laptops do you see in movies and TV shows? Invent cool new stuff that people love My first iPAD… These are Core competencies! Strategic management is management that bases all actions, activities, and decisions on what is most likely to ensure successful performance in the marketplace. The two major components of strategic management are strategic planning and strategic execution. Part of strategic planning is thinking creatively to eliminate “sacred cows” that work against competitiveness. What is a “sacred cow”? Why and how do they stifle strategic planning? Strategic planning is the process whereby organizations develop their vision, mission, guiding principles, broad objectives, and tactics for accomplishing the broad objectives. Explain why creative thinking is important in strategic planning and how to encourage it. So as to ferret out things that are done the same way year after year just because that is the way they have always been done. This approach will not make an organization more competitive. What is a Strategic planning session like? Who attends the sessions? How many people? What departments and why? How long does it take? What is the format? How are disagreements worked out? Who works out decisions on conflict and how? How and who approves it? How is Quality strategy linked to the process? It depends … An organization’s vision is its guiding force, the dream of what it wants to become and its reason for being. The best Vision has a feeling associated with it! It gives some context to each person’s job beyond a paycheck. Vision – who are we and/or who do we want to be? The very best ones are inspirational and aspirational! What are some example visions you understand for some companies you know? Write a sample vision for a hypothetical organization: The Institute for Corporate Competitiveness will be recognized by its customers as the provider of choice for organizational development products that are the best in the world. An organization’s mission describes who an organization is, what it does, and where it is going. The best mission statements are clearly stated. A good mission helps the entire organization to be able to tie their work and effort to. Practically, how do you tie the employee efforts to the mission of the company? Write a mission statement for this hypothetical organization: The Institute for Corporate Competitiveness (ICC) is a business-development company dedicated to helping organization's continually improve their ability to compete in the global marketplace. To this end, ICC provides high-quality competitiveness: enhancing products and services to an ever-increasing number of organizations in the United States. An organization’s guiding principles establish the framework within which it will pursue its mission. Together, the guiding principles summarize an organization’s value system, the things it believes are most important. What might be a “guiding principle” and how does it work? Give me an example from a company. Draft a set of guiding principles for the hypothetical organization. XYZ Company will uphold the highest ethical standards in all of its operations. At XYZ Company, customer satisfaction is the highest priority. XYZ Company will make every effort to deliver the highest quality products and services in the business. At XYZ Company, all stakeholders (customers, suppliers, and employees) will be treated as partners. At XYZ Company, continued improvement of products, processes, and people will be the norm. XYZ Company will provide employees with a safe and healthy work environment that is conducive to consistent peak performance. XYZ Company will be a good corporate neighbor in all communities where its facilities are located. XYZ Company will take all appropriate steps to protect the environment. An organization’s broad strategic objectives translate its mission into more specific terms that represent actual targets at which the organization aims. The objectives are more specific than the mission, but they are still broad. Tell me what an objective might be for a company and how do you make is “measurable”? Most companies use an acronym to help people understand the types of goals and objectives … SMART Establish a few broad objectives for the hypothetical organization: 1. To produce organizational-development products of world-class quality that are improved continually. 2. To provide organizational-development services of world-class quality that is improved continually. 3. To establish and maintain a world-class workforce at all levels of the organization. 4. To continually increase the organizations market share for its existing products/services. 5. To continually introduce new products/services to meet emerging needs in the organizational development market. SMART GOALS and/or OBJECTIVES S - specific, significant, stretching M - measurable, meaningful, motivational A – agreed upon, achievable,, attainable, acceptable, action-oriented R - results-oriented, realistic, relevant, reasonable, rewarding T - time-based, time-bound, timely, tangible, trackable SMART GOALS and/or OBJECTIVES (Cont.) Specific Well defined Clear to anyone that has a basic knowledge of the project Measurable Know if the goal is obtainable and how far away completion is Find out when you have achieved your goal Agreed Upon Agreement with all the stakeholders what the goals should be Realistic Within the availability of resources, knowledge and time Time-Based Enough time to achieve the goal Not too much time, which can affect project performance Tactics are well defined, finite projects and activities undertaken for the purpose of specific desired outcomes in support of the broad objectives. Best practice – these tactics drive the employee goals and objectives in performance reviews. They are reviewed and measured for completion regularly. They are action statements broken into “doable” parts They are written in clear, concise, understandable language since they cross functions and departments Even the best strategic plan will serve no purpose unless it is effectively executed. To promote successful execution of strategies, organizations should undertake the following activities: Communicate, build capabilities Establish strategy-supportive stimuli Eliminate administrative barriers Identify advocates and resisters Exercise strategic leadership Monitor, measure and adjust as needed. One excellent tool companies use in strategic planning is called a SWOT Analysis … SWOT Analysis Internal View: ○ Strengths ○ Weaknesses External View: ○ Opportunities ○ Threats What is SWOT analysis? SWOT is the acronym for Strengths, Weaknesses, Opportunities, and Threats. A SWOT analysis answers the following questions: What are this organization's strengths? What are this organization's weaknesses? What opportunities exist in this organization's business environment? What threats exist in this organization's business environment? Strengths (Questions to Ask): What advantages does your organization have? What do you do better than anyone else? What unique or lowest-cost resources can you draw upon that others can't? What do people in your market see as your strengths? What factors mean that you "get the sale"? What is your organization's Unique Selling Proposition (USP)? Weaknesses (Questions to Ask): What could you improve? What should you avoid? What are people in your market likely to see as weaknesses? What factors lose you sales? What problems do you have that people are just not willing to talk about? What are customers complaining about? What are employees complaining about? Opportunities (Questions to Ask): What good opportunities can you spot? What interesting trends are you aware of? What changes in technology and markets are happening in your business segment? What regulatory or government policy related changes are happening that affect your business? What unmet market needs (i.e. problems to solve) do you encounter? How and where are your customers (or competitor customers) asking for help? Threats (Questions to Ask): What obstacles do you face? What customers have you lost and why? Are quality standards or specifications for your job, products or services changing? Is changing technology threatening your position? Is your industry growing overall? If not, why not? What external issues worry you or keep you up at night? What one thing could happen and shut your business down in a short period of time? Andy Grove CEO Intel: “Success breeds complacency. Complacency breeds failure. Only the paranoid survive.” Some Careers in Strategic Planning: Quality Manager (guides quality planning processes) Product Manager (typically in Marketing – new products, channel management and customer management, pricing and strategic management Strategic Planner or Facilitator (Strategic planning processes have to be managed and facilitated for best results) Frankly, any company manager is typically involved in this process. Only the best employees are selected! Porters 5 Forces Model SWOT Analysis Chapter 3 Review Questions Question 1 What is strategic management? Strategic management is management that bases all actions, activities, and decisions on what is most likely: within an ethical framework: to ensure successful performance in the marketplace. From the perspective of the strategic manager, resources are wasted unless they contribute to success in the marketplace, and the more direct the contribution, the better. Question 2 What are some typical steps in the Strategic Planning process? SWOT Analysis, Develop the Vision, Develop the Mission, Develop the Guiding Principles, Develop the Broad Strategic Objectives, and Develop the Specific Tactics Be prepared to know what these are and how they are different. Question 3 What is a core competency? A core competency is anything an organization does so well that it can be viewed as a competitive advantage. An organization’s core competencies might be based on its ability to achieve economy of scale, proprietary access to a given technology, expertise that is difficult to replicate, the ability to maintain world-class performance from critical processes, market proximity, a high-performance corporate culture, research and development expertise, the ability to respond rapidly to market research, or any other factor that contributes directly and significantly to the organization’s ability to provide superior value consistently over time. Question 4 Explain why creative thinking is important in strategic planning and how to encourage it. So as to ferret out things that are done the same way year after year just because that is the way they have always been done. This approach will not make an organization more competitive. Question 5 What is SWOT analysis? SWOT is the acronym for Strengths, Weaknesses, Opportunities, and Threats. A SWOT analysis answers the following questions: What are this organization's strengths? What are this organization's weaknesses? What opportunities exist in this organization's business environment? What threats exist in this organization's business environment? Question 6 In order to survive in a globally competitive environment, organizations must adopt a broad strategy that gives them a sustainable competitive advantage. (T/F) True Question 7 An organization's vision is a specific measurable goal it tries to achieve.(T/F) False Question 8 A firm should consider internal factors like opportunities and threats as part of a SWOT analysis.(T/F) False Chapter 15 - Overview of Total Quality Tools Pareto Charts Pareto charts are useful for separating the important from the trivial. They are named after Italian economist and sociologist Vilfredo Pareto. Pareto charts are important because they can help an organization decide where to focus limited resources. The Pareto Principle holds that a few significant causes lead to the majority of problems. In class exercise on a common problem – computer problems. Explain the purpose of a Pareto Chart. Give an example of when one would be used. The purpose of a Pareto chart is to show you where to apply your resources by revealing the significant few from the trivial many. A sample might show that 75% of company’s sales are the result of just two customers. Fishbone Diagram The cause-and-effect or Fishbone diagram was developed by the late Dr. Kaoru Ishikawa, a noted Japanese quality expert; others have thus called it the Ishikawa diagram. Its purpose is to help identify and isolate the causes of problems. It is the only one of the seven basic quality tools that is not based on statistics. Describe the origin and use of cause-and-effect diagrams. Dr. Kaoru Ishikawa, a noted Japanese quality expert developed the cause-and-effect diagram, so sometimes the diagram is called an Ishikawa diagram. It is also often called a fishbone diagram because that is what it looks like. The fishbone diagram is the only tool of the seven tools that is not based on statistics. This chart is simply a means of visualizing how the various factors associated with a process affect the process's output. The cause-and-effect diagram provides a graphic view of the entire process that is easily interpreted by the human brain. Let’s do a FishBone diagram together. Someone suggest a problem in school that we might all solve together? Operator – Machine – Methods – Measurement – Environment – Materials. Check Sheet The check sheet is a tool that facilitates collection of relevant data, displaying it in a visual form easily understood by the brain. Check sheets make it easy to collect data for specific purposes and to present it in a way that automatically converts it into useful information. Usually created in Excel with a format that allows whoever is collecting the data to easily write it on the sheet. How would a check sheet be used in a modern production facility? The check sheet is used to simultaneously make the collection of data easy, while at the same time displaying it in a manner that provides useful information to the user. The only rules are that data collection must be the equivalent of entering a check mark, and that the resulting data display must provide meaningful information. The purpose of the check sheet is to make it easy to collect data for specific purposes and to present the data in a way that facilitates conversion from data to useful information. For example, the logged checkmarks on a check sheet might form a histogram illustrating the effectiveness of a process, or it might present a picture of where, in a product, defects are occurring. The check sheet’s utility is restricted only by the imagination of the person seeking information. Histogram Histograms have to do with variability. Two kinds of data are commonly associated with processes: attributes data and variables data. An attribute is something that the output product of the process either has or does not have. Variables data are data that result when something is measured. A histogram is a measurement scale across one axis and a frequency of like measurements on the other. What is a histogram and how is one used? A histogram is used to chart the frequency of occurrence of particular values or events across a continuous variable. How often does something happen? The “somethings” are laid out in a continuous scale, usually on the horizontal axis, and may be measurements (variables data) or physical characteristics (attributes data). The vertical axis logs how many times each of the individual measurements or attributes occur. In a normal distribution the resulting histogram will trace a bell shaped curve. The curve, in both its shape and position along the horizontal axis provides information on how well the process is working. Thus the histogram provides a graphical picture of a current state, and may predict a future state. Describe the difference between variables and attributes data. Variables data concern measured values of the subject object such as dimensions, weight, voltage, etc. Attributes data, on the other hand, concerns something that can be said of the subject, for example: it either has something or it does not, it is good or it is bad, it passes test or does not, it is accepted or rejected, it conforms or does not conform. Data Types Attributes Data: Has or has not Good or Bad Pass or Fail Accept or Reject Conforming or non-conforming Variables Data: Measured Values: (dimension, weight, voltage, surface, etc.) (has units like inches, pounds, kilograms, etc.) What is a histogram and how is one used? A histogram is used to chart the frequency of occurrence of particular values or events across a continuous variable. How often does something happen? The “somethings” are laid out in a continuous scale, usually on the horizontal axis, and may be measurements (variables data) or physical characteristics (attributes data). The vertical axis logs how many times each of the individual measurements or attributes occur. In a normal distribution the resulting histogram will trace a bell shaped curve. The curve, in both its shape and position along the horizontal axis provides information on how well the process is working. Thus the histogram provides a graphical picture of a current state, and may predict a future state. Describe the difference between variables and attributes data. Variables data concern measured values of the subject object such as dimensions, weight, voltage, etc. Attributes data, on the other hand, concerns something that can be said of the subject, for example: it either has something or it does not, it is good or it is bad, it passes test or does not, it is accepted or rejected, it conforms or does not conform. Math Scatter Diagram The scatter diagram is arguably the simplest of the seven basic quality tools. It is used to determine the correlation between two variables. It can show a positive correlation, a negative correlation, or no correlation. These are very common in the business world across departmental functions due to simplicity and power to convey some messages or help reach conclusions. Explain the purpose of the scatter diagram. Give an example of how one would be used. The scatter diagram is used to determine the correlation (relationship) between two characteristics (variables). Suppose you have an idea that there is a relationship between automobile fuel consumption and the rate of speed at which people drive. To prove or disprove such an assumption you could record data on a scatter diagram that has miles per gallon (MPG) on the y-axis and the miles per hour (MPH) on the x-axis. MPG and MPH are the two characteristics. Examination of the scatter diagram shows that the aggregate of data points contains a slope down and to the right. This is correlation, and it supports the thesis that the faster cars travel, the lower the MPG. Had the slope been upward to the right, as it actually appears to be between 20 and 30 MPH, then the correlation would have suggested that the faster you travel, the better the fuel mileage. Suppose however, that the data points did not form any recognizable linear or elliptical pattern but were simply in a disorganized configuration. This would suggest that there is no correlation between speed and fuel consumption. Stratification Stratification is a tool used to investigate the cause of a problem by grouping data into categories. Grouping of data by common element or characteristic makes it easier to understand the data and to draw insights from them. A Pareto Chart is the most common stratification of data you will see in business. 7 Total Quality Tools In the context of the seven total quality tools, run charts and control charts are typically thought of as being one tool together. The control chart is a more sophisticated version of the run chart. The run chart records the output results of a process over time. For this reason, the run chart is sometimes called a trend chart. Contrast and compare run charts and control charts. The run chart is straightforward, and the control chart is a much more sophisticated outgrowth of it. Therefore, the two are usually thought of together as a single tool. Both can be very powerful and effective for the tracking and control of processes, and they are fundamental to the improvement of processes. The run chart records the output results of a process over time. The problem with the run chart, and in fact, many of the other tools, is that it does not tell us whether the variation is the result of special causes--things like changes in the materials used, machine problems, lack of employee training--or common causes that are purely random. In evaluating problems and finding solutions for them, it is important to distinguish between special causes and common causes. Not until Dr. Walter Shewhart made that distinction in the 1920s was there a real chance of improving processes through the use of statistical techniques. Shewhart, then an employee of Bell Laboratories, developed the control chart to separate the special causes from the common causes. Run Chart The weakness of the run chart is that it does not tell whether the variation is the result of special causes or common causes. This weakness gave rise to the control chart. On such a chart, data are plotted just as they are on a run chart, but a lower control limit, an upper control limit, and a process average are added. The plotted data stays between the upper control limit and lower control limit while varying about the center line or average only so long as the variation is the result of common causes such as statistical variation When control chart data point lies above UCL, or below LCL, it is considered the result of what kind of cause? It is considered the result of a special cause, and not the result of normal statistical variation's common causes. Explain why arbitrarily set upper and lower control limits (e.g. set to the product's specifications) are ineffective for control chart use. A control chart's upper and lower control limits are determined from the normal process variation, and must be calculated from that process data. Only then can a control chart show valid special cause information, and that is the reason for using a control chart. Other useful quality tools are five-S, flowcharts, surveys, failure mode and effects analysis (FMEA), and design of experiments (DOE). Five-S is used to eliminate waste and reduce errors, defects, and injuries. Flowcharts are used in a total quality setting for charting the inputs, steps, functions, and outflows of a process to understand more fully how the process works and who or what has input to and influence on the process, what its inputs and outputs are, and even its timing. Explain how Five-S can help an organization in pursuit of TQM. Five-S requires the organization to discard everything that is not useful (Sort), put the useful things where they are easily available without wasting time looking (Store), keep the workplace and it's equipment in top shape to minimize errors (Shine), find the best way to perform the tasks, and make those best practices standard operating procedure (Standardize), and then ensure that all employees abide by these practices (Sustain). An organization successfully implementing Five-S will have completed a valid entry point for TQM. Five-S supports TQM. The survey is used to obtain relevant information from sources that otherwise would not be heard from in the context of providing helpful data. Give an example of how a survey might be used in a modern production setting. Remember that the purpose of a survey is to obtain information that you might not otherwise get. A typical department in any organization has both internal suppliers and internal customers. Like external customers, internal customers can be dissatisfied with the product they receive from their internal suppliers. A survey could be used to see if the internal supplier is meeting the needs of the internal customer, or if some change might make his product easier for the internal customer to use. We might find that the internal customer has ideas for improving the process or product, etc. Using the customer-oriented point of view in a survey has proven to be a powerful tool for opening communications within and among departments and getting people and departments to work together for the common goal. Failure mode and effects analysis (FMEA) tries to identify all possible potential product or process failures and prioritize them for elimination according to their risk. Explain the difference between design FMEA and process FMEA. FMEA tries to identify all the possible types (modes) of failures that could happen to a product or process--before they happen. Once the possible failure modes have been identified the effects of these failures are analyzed, and the consequences are ranked by seriousness/criticality to the customer; probability of that failure to actually occur; and the difficulty of detection of the issue resulting in the failure mode. This ranking will show the organization where to apply its resources in an effort to make the product safer or more reliable. Design FMEA is employed during the design phase of a product or service, hopefully starting at the very beginning of the project. In this way, the designers will be able to develop a design that has fewer potential failures, and those that cannot be avoided can be made less severe. Also, by using FMEA concurrently with the design activity, it is more likely that test and inspection methods will be able to catch the problems before they get to the customer. A second version is process FMEA. In this case, FMEA is looking at the potential failures (errors, miscues) of a process. The process might be that of an accounting firm, a hospital, a factory, a governmental agency, or any other entity. One can imagine that in a hospital there are many processes that can have lots of failure modes, some probably not too important, but some as severe as they come. One would hope that FMEA is in every hospital’s tool kit. FMEA tries to identify all possible potential product or process failures and prioritize them for elimination according to their risk. Murphy’s Law - “Whatever can go wrong will go wrong” FMEA tries to anticipate and stop problems from happening before they happen FMEA is a “preventative” quality method rather than reactive It is “contingency planning” in product or process design. Uses company experts (cross-functional) to brainstorm potential problems and design better process to avoid before implementation. Process Failure Modes Example Questions: In what way could the process fail to perform its intended function? What could go wrong with this process? What has gone wrong with this process in the past? What concerns do you have with this process? Are there parts of this process you have no control over? Will the new process meet the intended purpose? Why or why not? Note: This can be used for any significant process like Customer Care. Process Impact/Effects Example Questions: What is the consequence of a service failure? If the operation fails, what will be the consequences for the client? For the vendor (like Halski)? For the Customer Care team? For the CEMs? In the computer system? Will the failure cause potential harm to anyone? Who and how? Will the failure cause potential violation of regulations? Root Cause Example Questions: How can a potential service problem occur? Why? What could cause the service to fail in this manner? Why? What unique circumstances could cause the service experience to be worst than expected? Why? Are there any redundant steps in the process that can lead to process or service issues? Control (Controls in place to prevent problems) Questions: What (or who) is already in place that could possibly detect the cause of potential problems? What (or who) is not in place yet but is currently planned that could possibly detect the cause of potential problems? What metrics or measurements might help see problems as they occur? What system design features up front (ex: phone menu) might avoid problems in the first place? Failure mode and effects analysis (FMEA) tries to identify all possible potential product or process failures and prioritize them for elimination according to their risk. Explain the difference between design FMEA and process FMEA. FMEA tries to identify all the possible types (modes) of failures that could happen to a product or process--before they happen. Once the possible failure modes have been identified the effects of these failures are analyzed, and the consequences are ranked by seriousness/criticality to the customer; probability of that failure to actually occur; and the difficulty of detection of the issue resulting in the failure mode. This ranking will show the organization where to apply its resources in an effort to make the product safer or more reliable. Design FMEA is employed during the design phase of a product or service, hopefully starting at the very beginning of the project. In this way, the designers will be able to develop a design that has fewer potential failures, and those that cannot be avoided can be made less severe. Also, by using FMEA concurrently with the design activity, it is more likely that test and inspection methods will be able to catch the problems before they get to the customer. A second version is process FMEA. In this case, FMEA is looking at the potential failures (errors, miscues) of a process. The process might be that of an accounting firm, a hospital, a factory, a governmental agency, or any other entity. One can imagine that in a hospital there are many processes that can have lots of failure modes, some probably not too important, but some as severe as they come. One would hope that FMEA is in every hospital’s tool kit. FMEA tries to identify all possible potential product or process failures and prioritize them for elimination according to their risk. Murphy’s Law - “Whatever can go wrong will go wrong” FMEA tries to anticipate and stop problems from happening before they happen FMEA is a “preventative” quality method rather than reactive It is “contingency planning” in product or process design. Uses company experts (cross-functional) to brainstorm potential problems and design better process to avoid before implementation. Design of experiments (DOE) is a sophisticated method for experimenting with complex processes for the purpose of optimizing them. Review DOE example with Philip Morris “paper making” process. Under what circumstances might design of experiment (DOE) be appropriate for an improvement process? DOE is appropriate for complicated processes which have multiple process factors and variables. The use of DOE in such situations can reduce the effort involved in identifying the specific factors needing improvement, which require close monitoring by control charts or other methods, and which are not critical, and require less attention. The Role of Management (Management Style) has changed since TQM. Directing ------> Facilitating What is an effective management style as a boss? “Chameleon” … do unto others as they want to be dealt with Chapter 16 - Problem Solving and Decision Making Two effective problem-solving models are the Deming Cycle and the Toyota Practical Problem-Solving Process. The Deming Cycle is also called the PDCA cycle or plan-do-check-act (adjust). Describe the PDCA Cycle. Plan: Develop a plan to improve Even before problems occur, create a plan for improving your area of responsibility, particularly the processes in that area. Then, when problems occur, they can be handled within the context of Deming's model for continual improvement. Developing such a plan involves the following four steps: 1) Identity opportunities for improvement; 2) Document the current process; 3) Create a vision of the improved process; and 4) Define the scope of the improvement effort. Do: Carry Out the Plan Implement the plan for improvement. The recommended approach is to first implement on a small scale over a specified period of time. This is the equivalent of developing and testing a prototype of a design before moving to full production. Check: Examine the Results Examine and record the results achieved by implementing the plan. The recorded results form the basis for carrying out the steps in the next component. Act: Adjust as Necessary Make adjustments as necessary based on what was learned in the previous component. Then repeat the cycle for the next planned improvement by returning to the first component of the model. Deming or PDCA cycle Plan Define the problem Gather information Identify the root cause Develop alternatives Weigh alternatives Select the best solution Do Implement the solution Best practice to test or prototype before final implementation Likely includes training and education Communication plan to those who are affected Check Monitor the solution Gather relevant data Analyze the data Determine if the solution eliminated (or greatly reduced) the original problem Complete any sensitivity analysis needed to see if solution is robust Act or Adjust Iterative if the solution is not permanent Could be a completely different solution Could be an incremental approach Try to minimize the impact on customers where possible Toyota Practical Problem-Solving Process. 1.Perceive the initial problem Realize that there is a problem Are there any sub-problems (stratified)? If the problem is unclear, at least list all of the symptoms in one place May need some process or product experts at this point 2.Clarify the problem Be careful – the pressure of the problem often causes people (bosses especially) to jump to “confusions” Must be open minded – have had to use “Sherlock Holmes” method on complex problems What is it not? Make sure to compare back to a standard or “what good looks like” What is the variance to standard? Is it measurable? If not, can a test be developed? Is there more than one variance? Prioritize the work using Pareto or FMEA techniques Set a clear, quantified improvement objective 3.Determine the actual POC (Point of Cause) Where did we see the problem? When did it occur? Move upstream – did something earlier in the process lead to the problem? Are there any issues or concerns regarding the test method? Are there any issues or concerns with the customer feedback? 4.Determine the Root Cause (Five-Why for example) May need process or product experts for this The team composition may change as the various potential root causes are considered May take fewer or more Why questions depending on the complexity 5.Develop and implement a solution Communication and implementation plan 6.Evaluate the effectiveness of the solution Test and monitor with data where possible 7.Change the original standard product or procedure Implement a new product specification, process, product design element, work instruction, etc. Make sure this becomes the new standard This is part of continuous improvement Securing reliable information is an important part of problem solving and decision making. W. Edward Deming recommended the use of the following tools: Cause-and-effect diagrams Flowcharts Pareto charts Run charts Histograms Control charts Scatter diagrams The use of TQM allows a company to continuously improve and solve problems proactively. Here is a video of how Honda practically solves quality problems in one of their factories. Watch for examples of how the team works on solving problems … (Go to 3:51 on video) http://www.viddler.com/embed/f80ef75b/?f=1&player=arpeggio&secret=23048325&make _responsive=0 Why is proactive or preventative quality better than reacting to customer complaints? What are some proactive/preventative TQM actions in the video? How were the “bosses” and “employees” interfacing in the video? The decision-making process is a logically sequenced series of activities through which decisions are made. Objective versus Subjective Decision-Making Scientific Decision-Making and Problem Solving Employee Involvement in Decision-Making Role of Information in Decision-Making Using Management Information Systems (MIS) Creativity in Decision-Making Decision Making is the process of selecting one course of action from among two or more alternatives. Decisions should be evaluated not just by results but also by the process used to make them. Define decision making as it relates to total quality. Decision making is the process of selecting one course of action from among two or more alternatives. Contrast problem solving with decision making. Decision making is concerned more with selecting options that can affect the organization in some significant and tangible way. Problem solving is concerned with reacting to a certain situation that has just presented itself and must be deal with now. Hence, decision making is typically more concerned with the future and problem solving is more concerned with the here and now. A problem is a situation in which what exists does not match what is desired or, put another way, the discrepancy between the current and the desired state of affairs. Problem solving in a total quality setting is not about putting out fires. It is about continual improvement. These activities in problem solving include: Identifying or anticipating the problem Gathering relevant facts Considering alternative solutions Choosing the best alternative Implementing Monitoring Adjusting All approaches to decision making are objective, subjective, or a combination of the two. Scientific decision-making means making decisions based on data rather than on hunches. Complexity in scientific decision making means nonproductive, unnecessary work that results when organizations try to improve processes in a haphazard, nonscientific way. Explain how to evaluate decisions in a total quality environment. There are two ways to evaluate decisions. The first is to examine the results. In every case when a decision must be made1 there is a corresponding result. That result should advance an organization toward the accomplishment of its goals. To the extent it does, the decision is usually considered a good decision. Managers have traditionally had their decisions evaluated based on results. Regardless of results, however, it is wise to also evaluate the process used in making a decision. Positive results can cause a manager to overlook the fact that a faulty process was used, and, in the long run, a faulty process will lead to negative results more frequently than to positive. The different types of complexity include errors and defects, breakdowns and delays, inefficiency, and variation. There are advantages and disadvantages to employee involvement. Techniques to enhance group decision-making are brainstorming, NGT (Nominal Group Technique – type of brainstorming), and teams. Managers should be prepared to counteract groupshift and groupthink. Information is data that have been converted into a usable format that is relevant to the decision-making process. Decision makers are receivers of information who base decisions in whole or in part on what they receive. Technological developments have introduced the potential for information overload, or the condition that exists when people receive more information than they can process in a timely manner. A management information system (MIS) is a system used to collect, store, process, and present information. Such a system has three components: ○ Hardware ○ Software ○ People. A management information system can do an outstanding job of providing information about predictable and routine matters. However, many decisions that managers have to make concern problems that are not predictable for which no data are tracked. Creativity is an approach to problem solving and decision-making that is imaginative, original, and innovative. The creative process proceeds in four stages: ○ Preparation (learning and gathering information) ○ Incubation (give ideas time to grow) ○ Insight (becoming clear on idea and outcome) ○ Verification (does the idea actually help or work) Factors that inhibit creativity include: Looking for just one right answer Being too logical Avoiding ambiguity Avoiding risk Forgetting how to play Fearing rejection Saying “I’m not creative.” Three strategies for helping people think creatively are 1. Idea vending (facilitation strategy looking at outside sources for ideas or solutions) 2. Listening (ask the right questions) 3. Idea attribution (encourage team to pursue some direction or approach All Test 1 Review Questions Question 1 A Pareto chart is mostly used to: To show where to apply resources by revealing the significant few from the trivial many; Focus efforts on the 20% of activities that solve 80% of the issues or problem Question 2 What is 5-S? a better way to organize a work unit or a production line Question 3 What is the purpose of a 5-Why analysis? To determine the root cause of a problem Question 4 When would the use of Failure Mode and Effects Analysis be appropriate? Ranking potential product and/or process failures for elimination Question 5 Factors that inhibit problem solving creativity include: 1. Looking for just one right answer 2. Being too logical 3. Avoiding ambiguity 4. Avoiding risk 5. Forgetting how to play 6. Fearing rejection or looking bad 7. Saying “I’m not creative.” Question 6 What are some ways to help people think creatively? Idea vending (facilitation strategy looking at outside sources for ideas or solutions) Listening (ask the right questions) Idea attribution (encourage team to pursue some direction or approach) Question 7 What are some of the parts of a control chart? 1. Upper control limit 2. Average 3. Lower control limit 4. Actual run data Question 8 What is stratification? Grouping problems into categories like in a Pareto chart Question 9 Does TQM with all of its standardized approaches allow for creativity in the work place? Of course Question 10 One of the key features of TQM (Total Quality Management) is: Teamwork Question 11 In addition to an excellent product and service, a customer wants good: Reliable delivery and after purchase support Question 12 What are some things that are part of a total quality approach? 1. Customer Focus 2. Employee empowerment 3. Unity of purpose Question 13 Who or what is the ultimate driver of quality products and/or services? The customer Question 14 Who are some of the key pioneers in quality and what did they do? 1. Edward Deming – The Deming Cycle, Deming’s 7 Deadly Diseases 2. Joseph Juran – 10 Steps to Quality Improvement, 3. Application of the Pareto Principle to Quality, TheJuran Trilogy 4. Philip Crosby – Quality Vaccine and 14 steps to quality improvement Question 15 World-Class manufacturers tend to have excellent strategies in the areas of: Supply-Chain Competitive Analysis Compensation Customization Question 16 When making comparisons among internationally competing countries, the following indicators are used: Standard of living and investment Question 17 The most critical area for maximizing competitiveness is: Human resources Question 18 An example of where World-Class manufacturers recognize employees and managers by measuring and rewarding: Improvements in customer service