received_1315407053100110.jpeg
Document Details
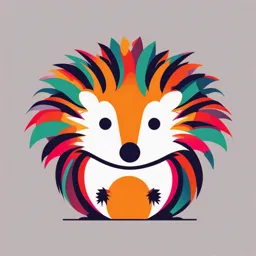
Uploaded by MomentousSet982
St. Paul University Quezon City
Full Transcript
# 8. Torsion ## 8.1 Introduction ### Twisting Moment * A twisting moment is applied *perpendicular* to the longitudinal axis of the member. * Also referred to as a *torque*. ### Torsion * The resulting stresses and deformations. ### Examples * Drive shafts * Drill bits ### Objectiv...
# 8. Torsion ## 8.1 Introduction ### Twisting Moment * A twisting moment is applied *perpendicular* to the longitudinal axis of the member. * Also referred to as a *torque*. ### Torsion * The resulting stresses and deformations. ### Examples * Drive shafts * Drill bits ### Objectives * Determine stress distributions * Determine angles of twist * Design shafts such that failure *does not* occur. ## 8.2 Torsional Stresses in a Circular Shaft ### Assumptions * Circular cross section * Axisymmetric * Material is homogeneous and isotropic * Material behaves in a linear-elastic manner * i.e., follows Hooke's Law ### Deformation * Shaft fixed at one end * Torque T applied at free end * Consider an element on the surface ### Angle of Twist * Define $\phi$ as the angle of twist. * $\phi$ varies linearly along the axis of the shaft * Therefore: $\frac{d\phi}{dx} = $ constant ### Shear Strain * Define $\gamma$ as the shear strain. * $\gamma$ varies linearly with radial position $\rho$ * Therefore: $\frac{\gamma}{\rho} = $ constant ### Shear Stress * From Hooke's Law: $\tau = G\gamma$, where G is the shear modulus. * Since $\gamma$ varies linearly with radius, so does $\tau$ * $\frac{\tau}{\rho} = $ constant * $\tau_{max}$ occurs at the outer surface, where $\rho=c$. * $\frac{\tau}{\rho} = \frac{\tau_{max}}{c}$ * $\tau = \frac{\rho}{c}\tau_{max}$ ## 8.3 The Torsion Formula ### Equilibrium * Torque $T$ is the *resultant* of the shear stress distribution. * $T = \int_A \rho \tau dA$ ### Torsion Formula * Using this result: * $\tau_{max} = \frac{Tc}{J}$ * $\tau = \frac{T\rho}{J}$ * Where: * $T$ = Internal torque at the section of interest * $\rho$ = Radial distance from the center of the shaft to the point of interest * $c$ = Radius of the outer surface * $J$ = Polar moment of inertia of the cross section ### Polar Moment of Inertia * Solid section: $J = \frac{\pi}{2}c^4$ * Tubular section: $J = \frac{\pi}{2}(c_o^4 - c_i^4)$ ### Limitations * The torsional stress formula can only be used for: * Circular shafts * Homogeneous and isotropic material * Material behaves in a linear-elastic manner ## Angle of Twist ### Constant Torque * Consider a shaft of length $L$ with constant cross section and constant applied torque. * $\phi = \int_0^L \frac{T}{JG} dx$ * $\phi = \frac{TL}{JG}$ ### Sign Convention * Use the *right-hand rule* * Fingers curl in the direction of the torque * Thumb points in the direction of the angle of twist vector * If $T$ and $\phi$ are in the same direction, the sign is positive. If they are in opposite directions, the sign is negative. ### Multiple Torques / Cross Sections * If the shaft is subjected to several different torques, or the cross section changes: * $\phi = \sum_i \frac{T_i L_i}{J_i G_i}$ * Make sure to apply proper sign convention to each segment. ## 8.5 Statically Indeterminate Torsional Members ### Statically Indeterminate * When the moment equation of equilibrium is not sufficient to solve for the unknowns, the member is statically indeterminate. * Need to consider *compatibility* ### Compatibility * Relate the angle of twist at one end of the shaft to the angle of twist at the other end. * $\phi_A = \phi_B$ * $\phi = \frac{TL}{JG}$ ## 8.6 Solid Noncircular Sections ### Stress Concentrations * The torsional stress formula *only* applies to circular sections. * Noncircular sections experience significant warping, and do not behave in an axisymmetric manner. * At the location of an inside corner, large stress concentrations will occur, and the material will yield. ### Rectangular Shaft * For a rectangular shaft of width $a$ and thickness $b$, where $a > b$: * $\tau_{max} = \frac{T}{c_1 ab^2}$ * $\phi = \frac{TL}{c_2 ab^3 G}$ * The constants $c_1$ and $c_2$ depend on the ratio $a/b$. | a/b | $c_1$ | $c_2$ | | :----- | :------ | :------ | | 1.0 | 0.208 | 0.1406 | | 1.2 | 0.219 | 0.1661 | | 1.5 | 0.231 | 0.1958 | | 2.0 | 0.246 | 0.229 | | 2.5 | 0.258 | 0.249 | | 3.0 | 0.267 | 0.263 | | 4.0 | 0.282 | 0.281 | | 5.0 | 0.291 | 0.291 | | 10.0 | 0.312 | 0.312 | | $\infty$ | 0.333 | 0.333 | ## 8.7 Thin-Walled Tubes Having Closed Cross Sections ### Shear Flow * $q = \tau t$ * $q = \frac{T}{2A_m}$ * $\tau = \frac{T}{2tA_m}$ * Where: * $T$ = Torque applied to the shaft * $t$ = Thickness of the tube where $\tau$ is being calculated * $A_m$ = Area enclosed by the *median* line of the tube's cross section. ### Angle of Twist * $\frac{d\phi}{dx} = \frac{T}{4A_m^2 G} \oint \frac{ds}{t}$ * If $t$ is constant: * $\phi = \frac{TSL}{4A_m^2 Gt}$ * Where: * $s$ is the length along the median line of the tube's cross section.