Lean Culture PDF
Document Details
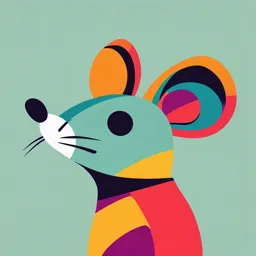
Uploaded by AdventuresomeBoolean
BITS Pilani, Pilani Campus
Tags
Related
- Lean Problem-Solving for Team Members and Leaders PDF
- Lean Problem-Solving for Team Members and Leaders PDF
- Week 5 - Integration of Lean into Health Care Culture
- Reviewer - Org Structure PDF
- Capítulo 22: Cree su propia empresa lean que aprende, asumiendo ideas del modelo Toyota PDF
- Tema 3. Diseño centrado en las personas - PDF
Summary
This document provides an overview of lean culture, its principles, and its applications within a business or organizational context. It explores several key components, such as PDCA (Plan-Do-Check-Act), standardization, visual management, teamwork, and the concept of intensity. The document also examines how a lean culture should ideally feel.
Full Transcript
LEAN CULTURE OBJECTIVES o What is lean culture? o PDCA o Standardization o Visual management o Team work oParadox o Intensity & do of lean culture o How does lean culture feel? ◾The day-to-day experience of our team members ◾Current behavior Day-to-da...
LEAN CULTURE OBJECTIVES o What is lean culture? o PDCA o Standardization o Visual management o Team work oParadox o Intensity & do of lean culture o How does lean culture feel? ◾The day-to-day experience of our team members ◾Current behavior Day-to-day experience and behavior in each includes the following: ◾ Plan-do-check-act What is lean ◾ Standardization culture? ◾ Visual management ◾ Teamwork ◾ Paradox ◾ Intensity ◾ The do concept PDCA GTS – grasping the situation, big picture, key parts, what is-should happen, trends, value-goal-related. ◦ Plan – 5Ws + 1H, measurement plan, visual system ◦ Do – contains its own PDCA cycle with pilot activities; assessment of team capabilities, assess current condition. ◦ Check – metrics to check outcome (final score) and process (along the way). Go see what is happening. ◦ Act – reflect on our condition, standardize when outcomes are on-target, make countermeasures – when outcome or process results are substandard. (stop bleeding or root cause) A manager’s job is to practice and teach PDCA, do it in the day-to-day. Warm Heart Principle – Hard on problem, easy on people. Standard – the best current method, but is meant to continually change. Standards make out-of-standard conditions obvious. STANDARDIZATION A problem is a deviation from a standard (gap). Problem-solving funnel Five Why’s (should get at root cause), which is usually: inadequate standards, inadequate adherence to standard, or inadequate system. VISUAL MANAGEMENT Visual management triangle Management as theatre – make problems visible Line-side process reviews Safety or quality “auctions” presentation (attendees can ask questions, give advice, offer to help investigation) Current condition presentations Hoshin (strategic) planning presentations Safety first – core Employment value, like security – last productivity & choice quality Uniforms – same No executive TEAMWORK regardless of position offices and no walls No executive Genchi genbutsu dining rooms or (Go see) – shop parking floor Jidoka – Stop production so that production never has to stop. Standards – change all the time. One-at-a-time production – is more effective than batch production. PARADOX Maximizing unit efficiencies – does not maximize overall efficiency. Don’t make something - unless a customer has ordered it. Team members – not industrial engineers, develop standardized work. Seek perfection – even though we know we will never achieve it. (humility) INTENSITY & “DO” OF THE LEAN CULTURE Intensity (more and greater The “do” concept is a “path” or a demands) “way” compels recognizing muda (waste) and kaizen Humility (make small improvements). Lifelong learning Recognize strain Respect for people Provide support and training Maintain intensity of improvement How does lean culture feel? ◾ Disciplined ◾ Freewheeling ◾ Warm ◾ Indomitable PDCA provides both scientific discipline and the freewheeling spirit of inquiry that asks: “How can we do this better?” Respect for people creates pleasing warmth and camaraderie. Team members interact as equals. “Them versus us” does not exist. Meeting daunting challenges year after year gives us confidence in the future. This then is the culture of Lean production, the soil in which this remarkable system thrives. In your Lean implementation efforts, please reflect on these ideas and take action to improve.