Casting and Casting Defects PDF
Document Details
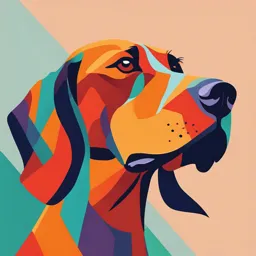
Uploaded by FlatteringSatyr
Dr. Kholoud Mohamed
Tags
Summary
This presentation discusses casting and casting defects, covering definitions, requirements, and classifications of dental alloys. It explores various melting techniques and different casting machine types, including torch melting, electric melting, and vacuum-pressure casting, along with the associated advantages and disadvantages.
Full Transcript
CASTING AND CASTING DEFECTS Presented by: DR KHOLOUD MOHAMED Casting Definition. Casting is the process by which a wax pattern of a restoration is converted to a replicate in a dental alloy. Used to make dental restoration such as inlay , onlay , crowns...
CASTING AND CASTING DEFECTS Presented by: DR KHOLOUD MOHAMED Casting Definition. Casting is the process by which a wax pattern of a restoration is converted to a replicate in a dental alloy. Used to make dental restoration such as inlay , onlay , crowns , bridges and RPD. Definition of casting alloys. Combination between two or more metallic elements , its soluble in each other in molten state Requirements of casting alloys: 1-Biological Requirements. 2-Funcational Requirements. 3-Working Requirements. 1-Biological Requirements: Not allergic. No health hazard. Resistant to tarnish and corrosion. This is achieved by : 1- Use solution alloy (one phase =homogenous). 2- Use of noble alloys. 3- Use of base metal alloy with the passive layer protective layer produced by oxidation 2- Functional Requirements: High yield strength can absorb max stress without change Resist permanent deformation. High resilient. Absorb energy of elastic deformation so that not all the stress will be transmitted to patient structure. High toughness. To absorb energy of fracture. High sag resistance. subject with high viscosity has high resistance than low one 2- Functional Requirements: To resist plastic deformation(permenant distortion that occurwhen material subjected to stress) during soldering. High fatigue strength. To resist cyclic loading. High ductility(can be thinned without become brittle) and Burnish- ability. High hardness. High modulus of elasticity. To resist elastic deformation. High cantilever bending. 3- Working Requirements: A) Ease of casting: Low melting temperature to use simple melting technique and to avoid high casting shrinkage. Narrow solidus liquid us range(liquidus lowest temp at w alloy is completely liquid ,solidus highest temp at w alloy is completely solid) to avoid coring and oxides formation. High density to obtain complete casting with low casting force. Sufficient fluidity to rapidly fill the mold. 3- Working Requirements: B) Ease of soldering: High sag resistant(high viscosity) to avoid melting or flow. Must wet the alloy surface C) Ease of working and burnish ability. Special notes for Requirements: IN CERAMO-METALLIC Functional requirement in cream-metallic 1-Melting temperature of metal higher than firing temp, of ceramic To resist sag or melting of metal. 2-Metal must form oxide layer (it react chemically with ceramic and allow bonding ) 3-Metal must not discolor porcelain. 4-Metal must have surface roughness For mechanical bonding with ceramic.. Special notes for Requirements: IN CERAMO-METALLIC Functional requirement in cream-metallic 5-Coeffecient of thermal expansion of metal slight higher than porcelain. Rate at which material expand To bring ceramic in state of compression which close the crack at the interface. To obtain compressive bonding between both of them. 6-To strength ceramic use in thin section to allow enough space for ceramic. Classification of dental alloys 1-General classification. 2-Specific use. 3-properties. 1-General classification of dental alloys: High noble alloys : More than 40% by wt. gold + 60%wt other noble metal Noble alloys : More than 25%wt noble metal Base metal alloy : More than 75%wt base metal +less than 25%wt noble metal Dental alloy Base metal Noble metal alloys alloys Cobalt-chromium Gold alloy Nickel –chromium Silver palladium Titanium and Palladium silver titanium alloy 2-Specific use: -Alloys for all metal restoration -Alloys for metal-ceramic restoration -Alloys for implant -Alloys for frame work for RPD properties of base metal alloys 1-biological properties : Biocompatibility. (Except that contain , nickel and beryllium ). Resist to tarnish and corrosion (due to present of passive layer). 2-Mechanical properties : When compared to gold alloys , the base metals are : Slight stronger (higher yield and ultimate strength ). Double stiffer (double modulus of elasticity ). Used in thin section. Less ductility (less burnish able). Harder (difficult to finished and polished ). 3-Physical properties : Melting rang 1400 C Need complicated and expensive tech. For melting. Need ceramic crucible by oxygen acetylene flame or electric induction. They are very reactive with atmosphere need vacuum casting. Melting and casting of dental alloys The dental alloy to be cast can be heated and melted by the use of : Torch (gas /air ) Electric current Torch melting : The two most common torch flames used to melt dental alloys are generated by : Natural gas and oxygen Propane (liq. Petroleum gas ) and oxygen LPG/oxygen is the most popular choice , because it produce hotter flame. Torch melting is done by directing the flame into dental alloy to be melted The heat produced from this flame is then radiated throughout the dental alloy until its molten and ready to cast. Torch melting is generally used with centrifugal casting machines. Flame zones Torch flame can be divided into four zones : Mixing zone Combustion zone Reducing zone Oxidizing zone 1- mixing zone: The inner most part of the flame. its colorless and consists of unburnt gas. 2-combustion zone : This area is greenish blue. This area is oxidizing zone. 3- Reducing zone : dim blue area , its the hottest area of the flame. 4-oxidizing zone : the outer area. Electric melting : There are 3 type of electric heating used to melt dental alloys Resistance Induction Arc Resistance melting : All resistance melters use some kind of high temp. Wire (like the wire in light bulbs ). When electricity moves through the wire , the wire offers resistance to the electricity and become hot enough that the heat radiates through the crucible to heat the metal. This type of melting provides the best means of temp. Control , and can be used for all types of crown and bridge alloys. It can used with centrifugal or vacuum pressure casting machine. Induction melting : Induction melting works by inducing electrical eddy currents in the metal. The source is the water –cooled induction coil that carries an alternating current and surrounds the crucible. The eddy currents heat the metal eventually melting it. This method provides the fastest way of melting an alloy , but can lead to problems with temp. Control. It requires pyrometer , that is focused on the alloy to monitor the temp. of the melt. It is used mainly for : cobalt-chromium , nickel chromium and titanium alloy. induction melting can be used with centrifugal or vacuum-pressure casting machines. Arc melting : Arc melting is a process of melting where heat is generated by an electric arc between two electrodes and the metal. The electric discharge or arc is created between the electrodes in an argon gas atmosphere. Arc melting is generally not used in dental laboratory as the machine is expensive and extremely large. Casting machines Centrifugal casting machine : This machine works on the principle of centrifugal force , the metal can be accelerated outward by rapid spinning. When the alloy is completely molten , the hot casting ring is placed behind the crucible that contains the molten alloy and the crucible ring assembly is spun rapidly , which accelerate the alloy into casting ring into the space previously occupied by the sprue and wax pattern. Casting machines Vacuum – pressure casting machine : This pressure vacuum casting machine produce pressure over the molten alloy. A vacuum is applied at the bottom of the mold. The molten alloy is pushed and sucked simultaneously into the mold. The vacuum-pressure casting machine first evacuates the melting chamber to reduce oxidation and then applies air pressure uniformly around the casting ring , forcing the alloy into the mold. Casting defects 1-No casting: Gate obstruction Presence of Investment fragment. Presence of Metallic sprue former. Molten alloy not properly directed during casting Flat crucible former. Improper alignment of crucible & ring during casting. Premature soldification of alloy during casting Thick sprue Inadequate casting pressure Cold ring Incompletely heated & melted alloy Casting defects 2-Casting defects by addition : a) Fins. b) Bubbles or nodules. c) Roughs surface. Casting defects 2-Casting defects by addition : fins: Cracked investment Molten alloy filled the crack Accessory wing to the cast restoration Due to : Disturbing the ring during setting of the investment Dropped mold High w/p ratio Rapid heating of investment (mold still wet) Weak investment Pattern too near to edge of investment Casting defects 2-Casting defects by addition : Bubbles/nodules: Site: At lower surface Due to excessive vibration. At other areas due to Air entrapped during investing. Size & number: large nodule due to Air entrapped during investing. Multiple small nodules due to Inadequate vacuum , improper brush tech, lack of surfactant. Casting defects 2-Casting defects by addition : Rough surface: 1-Rough surface of wax pattern. 2-Increased w/p ratio. 3-Excessive surfactant (wetting agent) or investing before complete dryness of wetting agent. 4-Investment material with large grains. 5-Exessive burnout temperature(over heated investment & alloy). Casting defects 3-Casting defects by loss (incomplete casting): At Margins : - Rough margin: -Foreign body in mold cavity. - -).. - Casting defects 3-Casting defects by loss (incomplete casting): At Thin areas : Due to lack of accessory Sprue (Ex: veneered surface) Casting defects 4- Porosity: Voids or pores within a substance. Micro Not Seen By Naked Eye. Macro Easily Identified. Types: Surface Porosity. Sub-surface Porosity. Casting defects 4- Porosity: Surface Porosity ( External Porosity ) : Lead to Roughness and Galvanic Corrosion. Back Pressure. Suck Back. Micro Porosity. Surface Porosity. Shrink Spot. Sub-surface Porosity (Internal Porosity) : Leads to Weakening of alloy.. Casting defects 4- Porosity: A) Back Pressure Porosity : Due To Failure OF Air to escapement from Mold through pores. Casting defects 4- Porosity: B) Suck Back Pressure Porosity : Due to Presence of Over Heated Area (hot spot ) At Entrance of Molten alloy If the Metal in the sprue solidifies before the metal in the Mold As May Happen when sprue is too narrow ,too long or incorrectly located. Casting defects 4- Porosity: C) Micro Porosity : Inside any cast restoration Due to Unequal Distribution of Solidification ( Not Appear By Naked Eye ). causes : Rough Restoration Galvanic Cell Tarnish &corrosion. Casting defects 4- Porosity: D) Surface Porosity : Appear as Rough surface Due to :- 1-Rough wax pattern. 2-over Heated Ring. 3-Incorrect investing. 4-High W\P Ratio. 5-Not Using Vacuum. 6-Excess Use of wetting agent. 7- Using of Investment with large grains. Casting defects 4- Porosity: E) Shrink Spot Porosity (localized ) : Due to : Cast Restoration and Sprue Solidification at same Time and Compensate Shrinkage from area of connection to sprue Separation between them. Casting defects 4- Porosity: F) Gas Inclusion Porosity : Entrapment of Air gas in Molten Alloy G)Inclusion Porosity : Particle of Investment Dislodged during casting. Casting defects 4- Porosity: H) Sub-Surface Porosity: Cause Weakness of Metal. Due to : Casting of Metal in Cold Mold At which Outer layer of Metal solidify first and Compensate Shrinkage from inside Part. Very Dangerous as Casting Appear accurate But porosity appear on Finishing of Casting. Casting defects 6- Oversized or undersized restoration: Due to expansion of investment. Both types must be remake as they expose cervical margin (dissolves cement & recurrent caries). Oversized (open margin). Under sized (short margin). Casting defects 7- Wrapped or distorted restoration: Due to: 1- incorrect impression or die construction. 2- incorrect handling of wax pattern before investing. 3- incorrect examination >>>> stress relaxation of wax. >>>> quality of setting & hygroscopic expansion. 4- incorrect processing of pattern in ring. 5- usage of force during removal of pattern from ring or during finishing & polishing. Casting defects classified during Steps 1- During impression &modeling: Improper impression & modeling (dimensional changes) so Distorted casting or over and under sized restorations. 2- During wax pattern: rough wax pattern : rough casting. delayed investing & wax pattern so stress relaxation so distorted restoration. improper handling of wax pattern so distorted restoration. Casting defects classified during Steps 3- During Spruing: Definition of spruing: It is a channel through which molten alloy can reach the mold in an investment ring after the wax has been eliminated Role of sprue: Holds the wax pattern to avoid its distortion. Creates a channel to allow the molten wax to escape from the mold. Enables the molten alloy to flow into the mold. Casting defects classified during Steps 3- During Spruing: material diameter attachment location orientation length Absence of reservoir No auxiliary sprue Casting defects classified during Steps 3- During Spruing: Material Plastic