Polymers (Revision): Engineering Chapter 20 PDF
Document Details
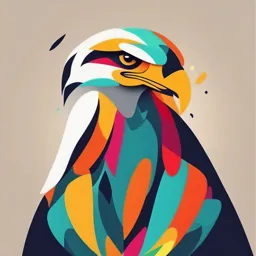
Uploaded by RazorSharpMorganite9424
Yangon Technological University
Dr War War
Tags
Summary
This document is a revision chapter on polymers from an Engineering Chemistry textbook. It covers topics such as polymerization, including addition and condensation reactions, and the properties of different polymers. Includes examples of Polyethylene, and nylon 66. The document originates from Yangon Technological University.
Full Transcript
Chapter 20 POLYMERS (revision) Dr War War Associate Professor Engineering Chemistry Department Yangon Technological University Polymerization Polymers are macromolecules of high molecular weight which are formed by linkage between large numbers of small molecules call...
Chapter 20 POLYMERS (revision) Dr War War Associate Professor Engineering Chemistry Department Yangon Technological University Polymerization Polymers are macromolecules of high molecular weight which are formed by linkage between large numbers of small molecules called monomers. Molar masses of polymers (i) Number average molar mass Mn (ii) Weight average molar mass Mw (i) Number average molar mass Mn N1M1 + N2M2 + …….. + NiMi NiMi Mn = = N1 + N2 + ………… + Ni Ni N1 = molecules have molar mass M1 N2 = molecules have molar mass M2 Mn is the ratio of the total mass (w) of all the molecules of polymer divided by the total number of molecules present. (ii) Weight average molar mass Mw w1M1 + w2M2 + …….. + wiMi wiMi Mw = = w1 + w2 + ………… + wi wi w1 = the mass of polymers with molar mass M1 w Numbers of moles n= , w =nM M n1M21 + n2M22 + …….. + niM2i niM2i Mw = = n1M1 + n2M2 + ………… + niMi niMi Mw Distribution ratio Mw Mn , 1 Mn Mw = 1, the polymer is homogeneous & contains polymers of same chain length Mn > 1 The degree of heterogeneity of the polymer Degree of polymerization(DP) The no. of repeating units present in a polymer molecule. n[ CH2= CH2] [CH2 - CH2 ]n n = a whole number , the degree of polymerization Molar mass of = degree of x molar mass addition polymer polymerization of monomer Mn = DP x molar mass of monomer Polymer do not have the same DP and show variation in molar mass. # only average DP and average molar mass (Mn) # 2. Mechanism of free radical addition polymerization Three major steps 1. Initiation 2. Propagation 3. Termination Initiation Step 1. R - R 2R° endothermic reaction R= peroxides, azocompounds or peracids Step 2. R° + CH2 = CH2 R - CH2 - ºCH2 free radicals ethylene monomer free radicals exothermic reaction Energy of endothermic < energy of exothremic Propagation R-CH2- CH2° + CH2 = CH2 R- CH2 - CH2- CH2- CH2° monomer free Dimmer free radical radical R- CH2 - ( CH2 )n - CH2 - CH2° polymer free radical Chain extension Energy of exothermic reaction Termination By coupling of one polymer free radical with another polymer free radical or initiator free radical to form stable dead polymer. R-(CH2 ) n1 - CH2 - CH2° + R-(CH2 ) n2 - CH2 - CH2° R-(CH2 ) n1 - CH2 - CH2 - CH2 - CH2 (CH2 ) n2 - R Dead heavy polymer Energy of exothermic reaction By disproporation of two polymer free radicals, a H atom attached to one of the free radicals is shifted to other intermediate polymer; two dead polymers, one unsaturated and other saturated are formed. R-(CH2 ) n1 - CH2 - CH2° + R-(CH2 ) n2 - CH2 - CH2° CH - CH°2 H R-(CH2 ) n2 - CH = CH2 R-(CH2 ) n1 - CH2 - CH3 Saturated polymer Unsaturated polymer Polyamide HOOC-(CH2)4-COOH + H2N - (CH2)6- N H2 OC-(CH2)4-CO- HN - (CH2)6-NH- Nylon 66 Adipic acid Hexamethylene Amide linkage diamine Uses: Tooth brushes, ropes, carpets, clothing e.g condensation polymerization polyester O O O“ O“ “ “ HO –C- -C –OH + HO- -OH HO –C- - C –O- -OH Ester linkage Dicarboxylic acid Diol Polyester (PET) Uses: Fibers, clothing soft-drink bottles, magnetic tape, plastic products Q. 1. What is functionality of a monomer? Ans. It is the number of bonding sites of monomer Q. 7. Differentiate between addition and condensation polymerization. Ans. Addition polymerization is a reaction that gives a polymer, which is an exact multiple of the original monomers. Condensation polymerization takes place through different functional groups of monomers with elimination of small molecules like H2O etc. Q. 8. What is copolymerization? Ans. Copolymerization is the point polymerization of two or more monomers, e.g., butadiene and styrene to yield GR-S rubber. 1.(a) Define the terms Degree of polymerization. (ii) Co-polymerization 1. (a) Explain tke terms with example (i) addition polymerization (ii) co-polymerization (iii) condensation polymerization Strength of polymer Plastic deformation Physical state Solubility and chemical resistance Shapes and forms – mechanical properties Effect of heat Cross linked polymer Giant, three dimensional structure, strong &tough Strength depends the chain length; Straight chain polymer Low MW: soft & gummy but brittle, Higher chain length: tougher & more resistant. Presence of polar group: intermolecular forces & strength increases. Linear –chain molecules are always soluble ---------------------------thermoplastics 3D polymer molecules are insoluble in any solvent --------------------thermosetting Qualities of polymer depends on structure of the polymers Artificially creating crosslinking converts thermoplastics material into thermosetting. Amorphous state : Random arrangement of molecules in the polymer flexibility Crystalline state: regular arrangements of molecules or chain in a polymer intermolecular force of attraction increases: higher softening point, greater rigidity, brittleness & strength Elastic character: very long chain polymer : free rotating groups irregularly coil entangled snorts: stretched and again returned back to original state Polymer soluble polar solvent (polar groups) (water, alcohols) ( -OH gps or -COOH) Polymer Soluble non-polar solvent (non-polar groups) (benzene, toluene, CCl4) H/C polymer The greater the degree of cross-linking, less is the solubility of the polymer in a solvent. The internal arrangement of long –chain molecules --------- fibers, plastics , rubbers Internal forces between molecules low, Molecules become bulky, Rubbery character Form random arrangement , Internal forces are high, Fibrous nature orderly arrangement Intermediate force -------------- plastic nature Strength of polymer is controlled by the length of the polymer chains & its cross-linking. On increasing strain continuously ultimately the polymer chains are uncoiled and fully stretched called necking. After this point the polymers reaches its break point and yields. Glass Transition Temperature , Tg Viscous liquid Both segmental & molecular motion Visco fluid state Flow temperature Only mixture ( no sharp mpt) Tf Rubbery state (soft, flexible) Segmental motion (visco elastic state) not Molecular motion Tg Glassy state : Segmental motion No amorphous polymer Molecular motion (hard , brittle plastic) Rigid solid (frozen state) Behavior of polymer is controlled by the temperature. Amorphous polymer do not have mpt have softening points At very low temp: both crystalline & amorphous polymer ;;;;;;; glass On heating , Tg is reached after soft. Amorphous polymer becomes rubbery and then gummy and on further heating it liquefies. Crystalline polymer on heating above Tg shows thermoplastic behavior and finally liquifies. (i) Resin (iv) Waxes, oils, stearates & soaps (ii) Fillers (v) Coloring materials (iii) Plasticizers (vi) Other additives Processing of plastics (i) Calendaring. (v) Injection moulding. (ii) Die casting (vi) Blow moulding (iii) Film casting (vii) Extrusion moulding (iv) Compression moulding. (viii)Thermoforming(or) Vacuum forming. No. Processing of plastics Types of polymer 1 Calendaring. thermoplastics 2 Die casting thermoplastics 3 Film casting thermoplastics 4 Compression moulding. thermoplastics & thermosetting 5 Injection moulding. thermoplastics 6 Blow moulding thermoplastics 7 Extrusion moulding thermoplastics 8 Thermoforming(or) Vacuum forming. Important Thermoplastic 1. Polyethylene (PE) Ethylene (colorless gas at rtp) Dehydration of ethanol at 160°C m H2SO4 (lab) gas polymerization. 1500 atm,200 °C (upper) & 120 °C (lower) (manufactured) ▪ Two types of Polyethylenes : (i) Low density polyethylene LDPE (ii) High density polyethylene HDPE (i) Low density polyethylene LDPE by using high pressure methods (1050-2000 kgf/cm2 ) using free radical initiator (ii) High density polyethylene HDPE by using low pressure methods (31 kgf/cm2 ) using ionic catalysts Property PE LDPE HDPE Appearance rigid, waxy, white, low sp. gr. low higher softening point, Properties translucent non-polar hardness greater rigidity but low material impact strength and it is opaque and relatively brittle Chemical good chemical Low swells & High does not swell or resistance resistance but acids, dissolves in H/C dissolve in solvents alkalis and salt solvents solutions, good insulating property but it is susceptible to organic solvents Chemical structure highly symmetrical branched structure Linear polymer structure so it and it is flexible and crystalizes easily tough Uses sheets, tubes ,toys , coated-wires &cables, bags bottles, caps, insulating No. Polymer Monomer Properties 1 PE CH2=CH2 good chemical resistance but acids, alkalis and salt ethene solutions, good insulating property but it is susceptible to organic solvents highly symmetrical structure so it crystalizes easily LDPE Low swells & dissolves in H/C solvents branched structure and it is flexible and tough HDPE High does not swell or dissolve in solvents Linear polymer No. Polymer Monomer Properties 2. PP [CH3CH = CH2] isotactic, highly crystalline polymer. propylene strength, moisture proofing quality, hardness Lightest all polymer. 3. PVC CH2 = CHCl PVC is a colorless, odorless, non-flammable, chemically-inert powder. Vinyl Chloride It contains 53-55% Cl2 and softens at around 80°C. It is resistant to water, light, O2, inorganic acids and alkalies, oil, petrol etc., but soluble in hot chlorinated hydrocarbons 4. PTFE [CF2 = CF2] Teflon is a linear polymer with high degree of crystallinity of ~ 95% Teflon tetrafluoroethylene Its flow temp: is high (327°C ) It is insoluble in all solvent. It is chemically inert and not attacked by acids, alkalis, oxidizing and reducing agents It is not wetted by oil or water. It has high resistance to impact and wear and tear. It is thermally stable and has a good electrical insulating property. No. Polymer Monomer Properties 5. PU Di isocynate & polyol PUs are spongy transparent linear thermoplastics It has low thermal conductivity. Its greatest advantage lies in fact that it can be made where they are needed without any complex machinery—two liquid ingredients can be mixed and moulded. 6 Nylon 66 Adipic acid & Nylon is strong, tough, elastic and can be dyed easily. Hexamethylene diamine Nylon possesses high abrasion resistance and is chemically stable. It possesses high temperature stability and also high melting (160°C-264°C). It is insoluble in common organic solvents but soluble in phenol, formic acid Q. 5. What is the basic difference between nylon 6 and nylon 66? Ans. Nylon 6 is an homopolymer whereas nylon 66 is a hexo polymer. In nylon 6, the composition of the monomer is the same as that of the polymer, but nylon 66 is formed from the composition of the monomers are different. Q. 6. Differentiate between a homopolymer and copolymer? Ans. A homopolymer consists of many identical monomer units whereas a copolymer consists of monomers of different chemical structures Q. 11. Why is the density of HDPE different from LDPE? Ans. HDPE is completely a linear polymer and hence packing of the chains is efficient and hence its density is high. But for LDPE, due to its branched structure, packing efficiency is low and hence density is low. Q. 12. Why thermosetting plastics cannot be reused? Ans. In thermosetting plastics, the monomers are bound to each other by strong covalent bonds, which cannot be broken on heating. Thus by heating it cannot be softened to reshape and reuse. What are the classification of polymers based on their thermal behavior with examples? Based on the thermal behavior, polymers are classified into thermoplastic polymers (Ex, PE, Polycarbonate, Polytetrafluoroethylene) and thermosetting polymers (Ex, phenol-formaldehyde, urea-formaldehyde). Q. 14. Why is teflon highly chemical resistant? Ans. In teflon the most electronegative element F contributes to the strong attractive force within the chains and hence is non-reactive towards other chemicals. Important Thermosetting Resins Important Thermosetting Resins No. Polymer Monomers Properties 1 Phenolic resins (or ) phenol with phenolic resins are rigid, hard, water resistant Bakelite formaldehyde resistant to non-oxidising acids, organic solvents but are susceptible to alkalies. Solubilities and melting point of resin gradually change with rise of molecular weight. possess electrical insulating properties 2. Epoxy resin 2, 2-(bis)-4-hydroxy Adhesion to various materials phenyl propane Flexibility [bis-phenol] Chemical inertness epichlorohydrin Toughness Stability at high temperature Low shrinkage during cure 3 Polyester ethylene glycol the structure of the polymer is symmetrical and a Terylene or Dacron with terephthalic number of polar groups are present it forms fiber easily. acid The fiber has high tensile strength and resiliency and is stable to hydrolysis. The fabric made from the fiber is crease resistant. Limitations of natural rubber Natural rubber softens at high temperature and becomes brittle at low temperature. It is attacked by acids, oxidising agents, non-polar solvents. it is oxidised by air. Also on excessive stretching it gets permanently deformed Vulcanization Rubber Is a process (heating natural rubber with S at 135°C and (1-4 hours) To improve the properties of natural rubber ‘S’ atoms form bridges between poly neoprene chains (a part of double bonded carbon atoms) Degree of vulcanization ∞ the amt of ‘S’ added S Tensile stregth, chemical resistance and wear and tear resistance Tyre ---3-5% S , filler--- C are added 32% S----full saturation ---a rigid non flexible rubber ( ebonite) Synthetic rubber No. Synthetic rubber Monomer Uses 1. GR-S or Buna 1,3 butadiene + styrene manufacture of tyres, S. general-purpose soles and other components of shoes, synthetic rubbers for insulating wires and cables, as adhesives and lining for vessels. 2. GRA or Buna-N butadiene and acrylonitrile to manufacture parts for automobiles, Abrasion-resistant aircraft. rubber used for making conveyer belts, adhesives and oil resistant foams 3. GR-M or Neoprene chloroprene or a chlorinated for making conveyer belts, adhesives, Commercial Grade butadiene. gaskets, as linings for reaction vessels and Neoprene Rubber for making pipes to carry corrosive gases and oils. Reclaimed Rubber waste rubber articles by the process of reclamation waste rubber articles are cut and powdered in a cracker. The unwanted ferrous materials are separated by electromagnetic separator and then changed to an autoclave and digested with caustic soda solution at 200°C under pressure for 8-15 hours. The fibres get hydrolysed i.e., devulcanization takes place. Sulphur is removed as sodium sulfide. It is washed, dried and finally reinforced with carbon black etc. Uses Reclaimed rubber is used for making tyres, tubes, belts, shoe soles, floor mats etc. Conducting Polymers π-electrons conducting polymer. Conducting element-filled polymer Inorganic polymer Doped-conducting polymer. Blended conducting polymer Q. 18. What changes take place with polymers near glass transition temperature? Ans. Below the glass transition temperature, the polymer is brittle and above it, they would deform but not break. Q. 15. Why is PVC soft and flexible but bakelite is hard and brittle? Ans. In PVC the molecular chains are bonded to each other by Van der Waal's forces and hence these long chains are flexible and can slip or twist on applying force but in the case of bakelite the thermosetting polymer chains are crosslinked by covalent bonds, so, it is hard and no deformation can take place on applying force. When the force becomes too large the covalent bonds are broken and it becomes brittle. Q. 16. Why is natural rubber compounded? Ans. Natural rubber possesses many undesirable properties and so to improve its properties it is usually compounded with different ingredients like plasticizers, antioxidants, filler, colorant etc. Q. 17. Why is natural rubber vulcanized? Ans. Raw rubber has high elasticity, thickness, poor chemical resistance, poor strength, large water absorption capacity etc. Vulcanization i.e., adding some sulfur at 100°C-140°C causes saturation of the double bonds by S and hence stiffening of the polymer takes place. Vulcanization, thus, improves all the above properties. Q. 3. What is ageing of rubber? Ans. Ageing is the autooxidation of rubber with time due to the presence of double bond and due to this rubber becomes hard. Q. 4. When is vulcanization done? Mention some of the uses of vulcanized rubber. Ans. Vulcanization is done after shaping the article. Tke shaping is done with raw rubber along with suphur and other ingredients like accelerators, antioxidants, fillers etc. Uses. Vulcanized rubber is used in vehicle tyres, hose, conveyer belt, electrical insulation. Q. 13. What is natural rubber and what is gutta-percha? Ans. Natural rubber is long-coiled chains of poly cis isoprene and gutta-percha is toughform of poly trans isoprene. Q. 16. Why is natural rubber compounded? Ans. Natural rubber possesses many undesirable properties and so to improve its properties it is usually compounded with different ingredients like plasticizers, antioxidants, filler, colorant etc. Q. 17. Why is natural rubber vulcanized? Ans. Raw rubber has high elasticity, tackiness, poor chemical resistance, poor strength, large water absorption capacity etc. Vulcanization i.e., adding some sulfur at 100°C-140°C causes saturation of the double bonds by S and hence stiffening of the polymer takes place. Vulcanization, thus, improves all the above properties. Q. 18. What changes take place with polymers near glass transition temperature? Ans. Below the glass transition temperature, the polymer is brittle and above it, they would deform but not break.