Maintenance Instructions WA 290/02 PDF
Document Details
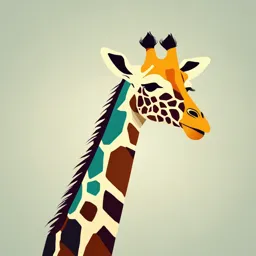
Uploaded by BestSellingBeige
null
Tags
Related
- On-Load Tap Changer Type T Inspection Instructions PDF
- VACUTAP® VM 300 On-load tap-changer Operating Instructions PDF
- VACUTAP® VV® On-load tap-changer Operating Instructions PDF
- IA 75/80 (Partial Issue) On-Load Tap-Changer Inspection Instructions PDF
- VACUTAP® VT® On-load Tap-changer Operating Instructions PDF
- VACUTAP® VR II III Maintenance Manual PDF
Summary
This document provides maintenance instructions for Reinhausen on-load tap-changers. It covers safety procedures, preparation, removal, and other maintenance aspects. The document includes drawings and diagrams.
Full Transcript
www.reinhausen.com On-load tap-changers VACUTAP® VRC, VRE, VRD, VRF, VRG Maintenance Instructions WA 290/02 Contents Contents 1 Safety..............
www.reinhausen.com On-load tap-changers VACUTAP® VRC, VRE, VRD, VRF, VRG Maintenance Instructions WA 290/02 Contents Contents 1 Safety........................................................................................................................ 5 1.1 Safety labels.................................................................................................................................................. 5 1.2 Safety instructions........................................................................................................................................ 5 2 Notes on the Maintenance Instructions............................................................. 7 2.1 Purpose and associated documents........................................................................................................... 7 2.2 Using the Maintenance Instructions.......................................................................................................... 7 3 General information.............................................................................................. 8 3.1 Operating principle....................................................................................................................................... 8 3.2 Type Identifictaion (ID)................................................................................................................................ 10 3.3 Models............................................................................................................................................................ 10 3.4 Configuration................................................................................................................................................ 10 3.5 Monitoring during operation...................................................................................................................... 13 3.6 Maintenance intervals.................................................................................................................................. 13 3.7 Scope of maintenance.................................................................................................................................. 13 4 Preparation.............................................................................................................. 14 4.1 Safety procedures......................................................................................................................................... 14 4.2 Auxiliary equipment...................................................................................................................................... 14 4.3 Removal position........................................................................................................................................... 15 5 Removal.................................................................................................................... 16 5.1 Adjustment position...................................................................................................................................... 16 5.2 Removing the drive shaft............................................................................................................................. 16 5.3 Lowering the oil level.................................................................................................................................... 16 5.4 Removing the head cover............................................................................................................................. 17 5.5 Removing the diverter switch insert........................................................................................................... 18 6 Maintenance............................................................................................................ 20 6.1 Oil compartment........................................................................................................................................... 20 6.1.1 Cleaning.................................................................................................................................................................. 20 6.1.2 Visual inspection................................................................................................................................................... 20 6.1.3 Covering the oil compartment.......................................................................................................................... 20 6.2 Diverter switch insert................................................................................................................................... 21 6.2.1 Cleaning.................................................................................................................................................................. 21 6.2.2 Visual inspection................................................................................................................................................... 21 6.3 Checking the coupling tube......................................................................................................................... 21 6.4 Checking the movable main contacts........................................................................................................ 22 6.5 Checking the transition resistors................................................................................................................ 22 6.6 Replacing the vacuum interrupters and stranded cable.......................................................................... 22 6.7 Checking the plain bearings........................................................................................................................ 23 6.8 Replacing the flexible connectors of the connecting contact................................................................ 23 6.9 Replacing the varistor connection cables.................................................................................................. 23 6.10 Replacing the diverter switch insert........................................................................................................... 24 6.11 Replacing the fixed main contacts............................................................................................................. 24 6.12 Tap selector maintenance............................................................................................................................ 24 290/02 EN WA 290/02 - VACUTAP® VR 3 Contents 7 Installation............................................................................................................... 25 7.1 Installing the diverter switch insert............................................................................................................ 25 7.2 Oil filling......................................................................................................................................................... 27 7.3 Connecting the drive shaft.......................................................................................................................... 28 7.4 Coupling the OLTC and the motor drive unit............................................................................................ 28 8 Further checks......................................................................................................... 29 8.1 Function control............................................................................................................................................ 29 8.2 Protective relay RS 2001.............................................................................................................................. 29 9 Appendix - VACUTAP® VR OLTC......................................................................... 31 9.1 Maintenance schedule - Tasks.................................................................................................................... 31 9.2 Switching sequence (728533)...................................................................................................................... 32 9.2 Switching sequence (728533)...................................................................................................................... 33 9.3 Adjustment positions (728557)................................................................................................................... 34 9.4 Adjustment plan for VACUTAP® VRC, VRE with coarse tap selector (719852)...................................... 35 9.5 Adjustment plan for VACUTAP® VRC, VRE without change-over selector (719853)............................ 36 9.5 Adjustment plan for VACUTAP® VRC, VRE without change-over selector (719853)............................ 37 9.6 Adjustment plan for VACUTAP® VRC III/ II, VRE III with reversing change-over selector (719850).. 38 9.7 Adjustment plan for VACUTAP® VRC I and VRE I with reversing change-over selector (719851)...... 39 9.8 Adjustment plan for VACUTAP® VRD, VRF without change-over selector (721089)............................ 40 9.8 Adjustment plan for VACUTAP® VRD, VRF without change-over selector (721089)............................ 41 9.9 Adjustment plan for VACUTAP® VRD, VRF with coarse tap selector (721091)..................................... 42 9.10 Adjustment plan for VACUTAP® VRG with reversing change-over selector (727074).......................... 43 9.11 Adjustment plan for VACUTAP® VRG with coarse tap selector (727075).............................................. 44 9.12 Tools (723016)............................................................................................................................................... 45 9.13 Fax template.................................................................................................................................................. 46 NOTE!! The product may have been modified after this document went to press. We expressly reserve the right to make changes to the technical data, the design or the scope of delivery. In general, the information provided and the arrangements agreed during processing of the relevant offers and orders are binding. The copying, distribution and utilization of this document as well as the communication of its con- tents to others without expressed authorization is prohibited. Offenders will be held liable for the payment of damages. All rights reserved in the event of the grant of a patent, utility model or ornamental design registration 290/02 EN 4 WA 290/02 - VACUTAP® VR 1 Safety 1 Safety 1.1 Safety labels The following specific safety warnings are used in these opera- ting instructions: The following safety labels relating to the operation of the VACUTAP® VR on-load tap changers are used in these mainten- ance instructions. These labels must be observed at all times! DANGER! Fire hazard! Risk of electric shock! Risk of tipping! 1.2 Safety instructions Refers to an imminent danger that may result in death or severe injury. CAUTION! Modified maintenance intervals for units delivered from 1 July CAUTION! 2006! Due to technical improvements the maintenance interval was extended Refers to a potentially harmful si- from 150,000 to 300,000 tap tuation that may result in damage change operations for units deliver- to the product or adjacent equip- ed from 1 July 2006. ment. A label at the inside of the door of motor drive ED clearly specifies the maintenance interval. NOTE! Door of motor drive ED Contains important information and special notes. Special safety labels are used for certain hazards, such as elec- tric shock: Hazard-specific symbol, e.g. DANGER! Electric shock! Refers to an imminent danger th- rough electricity that may result in death or severe injury. Label Figure 1: Maintenance interval label 290/02 EN 5 WA 290/02 - VACUTAP® VR 1 Safety All warnings and safety instructions must be observed at Only suitably qualified personnel should work at the all times! VACUTAP® VR! Danger of death and risk of injury! The VACUTAP® VR on-load tap-changer is designed exclusi- Failure to follow the safety instructions may lead to accidents vely for application in electrical or energy systems and faci- and severe personal injury. lities operated by appropriately trained staff. Please read these operating instructions before commis- Installation, electrical connection and commissioning of the sioning the equipment! on-load tap changer may only be carried out by qualified, Reading the operating instructions before commissioning the skilled personnel and only in accordance with these operating VACUTAP® VR. As the operator, you are responsible for ensu- instructions, i.e. staff who are familiar with the installation, ring that users of the equipment have fully understood the assembly, commissioning and operation of such products. operating and safety instructions. Train your staff! Before asking staff to work with the VACUTAP® VR, provide DANGER! training regarding general and special safety instructions and accident prevention regulations. Fire hazard! All relevant fire protection regulations must be observed. 6 WA 290/02 - VACUTAP® VR 290/02 EN 2 Notes on the Maintenance Instructions 2 Notes on the Maintenance Instructions 2.1 Purpose and associated documents The figures in the individual sections not always show all details for the respective components, but focus on the main informa- These Maintenance Instructions contain all the information re- tion. More detailed information can be found in the overviews quired for timely and proper maintenance of VACUTAP® VR on- in Figs. 4 and 5 or in the associated documents. load tap-changers. In these Maintenance Instructions the term “on-load tap-chan- Please note that the Maintenance Instructions focus on inspec- ger” always refers to VACUTAP® VR on-load tap-changers. tion and maintenance procedures. Full details regarding confi- guration, operating principle and operation of VACUTAP® VR The Maintenance Instructions are structured into different sec- on-load tap-changers can be found in the following docu- tions that are arranged according to technical and didactical ments: criteria. Operating Instructions BA 42 “Drive shaft” 2.3 Abbreviations Operating Instructions BA 59 “Protective relay RS 2001” The following abbreviations are used in these Maintenance In- Operating Instructions BA 138 “Motor drive unit ED” structions: Operating Instructions BA 288 “On-load tap-changers VACUTAP® VRC, VRE, VRD, VRF, VRG” BA Operating Instructions LU Diverter Switch 2.2 Using the Maintenance Instructions MC Main contact MR Maschinenfabrik Reinhausen GmbH These operating instructions form part of VACUTAP® VR on- MSV Main switching contact (vacuum interrupter), main path load tap-changers and must be retained throughout their life MTF Transfer switch, main path cycle. OLTC On-load tap-changer Any subsequent amendments from Maschinenfabrik Reinhau- SSE Tap change indication wheel section sen GmbH must be attached to or enclosed with the Mainten- TTF Transfer switch, transition path ance Instructions. Anyone carrying out maintenance on TTV Transition contact (vacuum interrupter), transition path VACUTAP® VR on-load tap-changers must follow both the Ope- Um Maximum equipment voltage (in kV) rating Instructions and the Maintenance Instructions. Before VW Change-over selector carrying out maintenance the Maintenance Instructions must WA Maintenance Instructions be read in full. ZnO ZnO conductor In order to avoid mistakes during maintenance and to ensure trouble-free operation of VACUTAP® VR on-load tap-changers, the complete document must be available at all times to all staff involved in maintenance tasks. 290/02 EN 7 WA 290/02 - VACUTAP® VR 3 General information 3 General information 3.1 Operating principle OLTCs are used for setting the required tap of a tap winding under load. During the tap changing operation the fine tap selector first selects the required tap setting of the tap winding. The diverter Oil compartment switch then switches from the current-carrying tap to the pre- with diverter switch selected tap. During this tap changing operation one step of insert the tap winding is temporarily bypassed with an ohmic resis- tance, so that the diverter switch operation occurs without cur- rent interruption. The tap change operation sequence is shown $ in Fig. 3. More detailed information about the switching sequence of the 9 : diverter switch insert can be found in the Appendix, Section 9.2 “Switching sequence”, Dwg. No. 728533. Fine tap selector Change-over selector 8 8 9 9 : : Figure 2: VACUTAP® VRD, VRF, VRG on-load tap-changer 8 WA 290/02 - VACUTAP® VR 290/02 EN 3 General information Figure 3: Tap change operation sequence 290/02 EN 9 WA 290/02 - VACUTAP® VR 3 General information 3.2 Type Identifictaion (ID) Table 1 shows the type ID of a three-phase VACUTAP® VRF OLTC, with a max. rated through-current of 1300 A, for star point OLTCs are available in several versions. Each OLTC version has a circuit, Um = 72.5 kV, tap selector size C. The basic circuit dia- different type ID. gram is 10 19 1G, i.e. pitch of tap selector contact circle = 10, All OLTCs are therefore clearly identified. 19 operating position, one of which is the mid-position. The change-over selector is used as a coarse tap selector. Type No. of Max. rated through- Application Max equipped voltage Um in kV Tap selector size Basic circuit phases current Insulation to ground diagram VRF III 1300 Y 72.5 C 10 191 G Table 1: Type ID example (VACUTAP® VRF) 3.3 Models 3.4 Configuration These Maintenance instructions apply to all standard models of The OLTC consists of a diverter switch insert installed in its own the OLTC variants specified below, which are available with or oil compartment, and a tap selector mounted below. without change-over selector. The on-load tap changer is attached to the transformer cover Single-phase OLTC also available as OLTC sets, e.g. by means of the on-load tap changer head. The tap selector is equipped with a change-over selector if required. On-load tap 3 x VACUTAP® VRC I changer models without change-over selector are available up 3 x VACUTAP® VRE I to a maximum of 18 operating positions. Models with change- 3 x VACUTAP® VRD I 1301 over selector can have up to 35 operating positions. 3 x VACUTAP® VRF I 1301 3 x VACUTAP® VRG I 1301 Figs. 4 and 5 show the names of the main OLTC components. with a common motor drive unit. The VACUTAP VRC I , VRC II and VACUTAP VRF I, VRF II OLTC combinations features a two-column design and a common motor drive unit. 10 WA 290/02 - VACUTAP® VR 290/02 EN 3 General information 1 A 2 3 4 5 6 5 A Complete head cover B B Diverter switch insert 7 C Oil compartment 8 1 Central gear unit 9 2 Head cover 10 3 Round rubber gasket 11 4 Lifting lugs 12 5 Screening rings 6 Coupling tube 13 7 Energy accumulator 8 Upper bearing plate 14 9 MTF/TTF 10 Vacuum interrupters 15 11 Movable main contact (roller contact) 16 12 Lower bearing plate 13 Transition resistors 14 Supports 17 15 Pipe connections 16 OLTC head 17 Screening rings (only for 170 kV; 245 kV; 300 kV; 362 kV) 18 Oil compartment bottom 17 C 18 Figure 4: Main on-load tap-changer components (VACUTAP® VRF) 290/02 EN 11 WA 290/02 - VACUTAP® VR 3 General information 19 20 21 22 23 24 D 25 D Tap selector E Top view of oil compartment (closed) F Top view of oil compartment (open) 19 Tap selector leads 20 Tap selector suspension 26 21 Tap selector gear 22 Change-over selector 23 Change-over selector terminals „K“ or „O“ 27 24 Change-over selector terminals „+“ or „-“ 25 Fine tap selector 26 Fine tap selector terminals 27 Pipe connection S with 28 Bleeder screw 28 Inspection glass 29 Bleeder valve E1 E 29 30 Nameplate 31 Pipe connection R for protective relay 30 32 Protective relay 33 Drive shaft for tap position indicator 34 Toothed gearing 35 Tap selector coupling 31 36 Fixed main contacts 32 33 34 F 35 36 Figure 5: Main on-load tap-changer components (VACUTAP® VRF) 12 WA 290/02 - VACUTAP® VR 290/02 EN 3 General information 3.5 Monitoring during operation Monitoring of the OLTC and the motor drive unit is limited to CAUTION! occasional visual checks of the OLTC head, the protective relay and the motor drive unit. These inspections can usually be com- Severe damage to the OLTC and bined with other common transformer checks. the transformer! OLTCs have to be serviced regularly Pay special attention to: in order to maintain high operating Oil tightness at the sealing locations of the OLTC head, the reliability. protective relay and the pipe connections Adhere to the specified mainten- Gaskets of the protective housing of the motor drive unit ance intervals! Proper function of the in-built electric heater in the protective Please ensure that all maintenance housing of the motor drive unit tasks are carried out fully and pro- State of the dehydrating breather (drying agent) for the OLTC perly! oil conservator Functional test of the protective relay according to Operating This ensures that all work is carried out properly, and that speci- Instructions No. 59. fic components are replaced with state of the art components as required. If a service is not carried out by our Technical Ser- The insulating oils in the transformer including the OLTC are to vice department, please ensure that the personnel carrying out be monitored by the operator according to the relevant in- the service are trained by MR or are otherwise suitably qualified structions (see Section 3.6). to carry out the work. For any maintenance work not carried out by our Technical Service, please forward appropriate main- 3.6 Maintenance intervals tenance reports so that we can update our maintenance re- OLTCs have to be serviced after 300,000 tap change opera- cords. A fax template is included in Appendix 9 (No. 723041) tions. The counter installed at the motor drive unit indicates the for this purpose. For spare part enquiries please specify the number of operations. serial number (see OLTC nameplate, overview in Fig. 5) and the number of operations (see counter in the „motor drive unit On-load tap changers with VACUTAP® vacuum switching tech- display panel“ Fig. 6). nology have considerably longer maintenance intervals than conventional tap changers with oil switching technology, which When changing the drying medium for the oil conservator of dramatically reduces operating and maintenance costs. Proper the on-load tap changer, the dielectric strength of the diverter maintenance is therefore particularly important. switch oil should be determined as a precaution. The limit va- lues for the dielectric strength can be found Table 2. The tempe- For this reason we strongly recommended to have the mainte- rature of the oils at the time of measuring the dielectric strength nance carried out by our Technical Service. should be recorded. The specified dielectric strength values are valid for oil temperatures of 20 ± 5 °C. On-load tap-changer Dielectric strength *) Three pole design OLTCs 30 kV/ 2.5 mm (minimum) One and two phase OLTCs 40 kV/ 2.5 mm (minimum) *) measured according to IEC 60156 Table 2: Limit values for changing or treating the OLTC oil 3.7 Scope of maintenance Given appropriate preparation, a proper service can be carried out within one day. The maintenance tasks required are listed in Counter the maintenance schedule in the Appendix, see Section 9.1. Figure 6: Motor drive unit display panel 290/02 EN 13 WA 290/02 - VACUTAP® VR 4 Preparation 4 Preparation 4.1 Safety procedures 4.2 Auxiliary equipment The following auxiliary equipment is required for servicing DANGER! OLTCs: Clean empty barrels and transformer oil according to Table 3 Risk of electric shock! for cleaning and oil change (the oil quantity depends on the Danger of death or severe inju- OLTC type and its rated voltage Um). ries! Oil pump Please implement the following Absorbent, lint-free cleaning rags safety precautions before carrying Workbench out maintenance work: Oil sump Switch off the transformer and se- Crane or MR lifting device (available from MR on request); the cure it against restarting! withdrawal height of the diverter switch insert depends on the Visibly connect all transformer ter- OLTC type and its rated voltage Um (see Table 4). minals to ground (grounding leads) Max. weight of diverter switch insert = 50 kg and short-circuit them! Tools (tools required in addition to the standard equipment see Appendix, Section 9.12) CAUTION! CAUTION! Fixtures (locking pins, retaining screws, lock nuts, etc.) and gaskets Damage to the OLTC and trans- (i.e. round rubber gasket of the head former! cover) should only be used once and Always use original spare parts from should be replaced after removal. MR. For self-securing screws with Spare parts of different origin may threads coated with microencapsu- jeopardize the trouble-free operati- lated adhesive not the expiration on of the OLTC and the transformer. date of the replacement parts. Rated voltage Um [kV] Type of OLTC 72.5 123 170 245 300 362 VRC max. 155 max. 175 max. 190 max. 210 max. 235 VRD, VRE, VRF, VRG max. 175 max. 195 max. 210 max. 230 max. 255 max. 280 Table 3: Oil quantity for oil change (liters) Rated voltage Um [kV] Type of OLTC 72.5 123 170 245 300 362 VRC 1120 1250 1350 1450 1580 VRD, VRE, VRF, VRG 1250 1380 1480 1580 1710 1840 Table 4: Removal height of the diverter switch insert during maintenance (millimeters) 14 WA 290/02 - VACUTAP® VR 290/02 EN 4 Preparation Please contact MR Technical Service in good time before main- tenance is due, specifying the serial number (see OLTC name- plate in the overview in Fig. 5) and the current number of ope- rations (see counter in the motor drive unit display panel in Fig. 6). 4.3 Removal position For removing the diverter switch insert move the OLTC into the adjustment position. In the tap position indicator in the motor drive unit display panel this is indicated with an arrow. Adjustment position Tap position indicator Figure 7: Tap position indicator on the motor drive unit display panel CAUTION! OLTC damage! Never operate the motor drive unit while the OLTC and the motor drive unit are uncoupled! As a precaution, block the motor drive unit against electrical operati- on by actuating the motor protecti- ve switch (see Operating Instructions no. 138 for motor drive unit ED). 290/02 EN 15 WA 290/02 - VACUTAP® VR 5 Removal 5 Removal 5.1 Adjustment position The diverter switch insert must be removed in the adjustment Upper gear unit position (see Section 4.3 „Removal position“). Drive shaft Make a note of the current operating position of the OLTC (see Fig. 8). OLTC head Upper gear unit Head cover Guard Head cover Coupling bracket Figure 9: Drive shaft at the OLTC head 5.3 Lowering the oil level Before opening the head cover the oil level in the oil compart- ment must be lowered. DANGER! Fire hazard! The switching oil of the OLTC should always be treated as an inflammab- le liquid. E Avoid open fire and observe the re- levant fire protection regulations! 1. Close the stop valve between the oil conservator and the OLTC. 2. Place a bucket (10 l) under the drain cock of the OLTC for collecting the drained oil and open the drain cock. 3. Open the bleeder valve E1 of the head cover (see Fig. 10). To Figure 8: Operating position indicator this end open the screw cap (M30/w.s.36) and lift the valve tappet with a screwdriver. 5.2 Removing the drive shaft 4. The oil level will drop automatically. For removing this drive components please also refer to Opera- ting Instructions no. 42 for the drive shaft. 1. Release the hose clamps of the guard for the horizontal drive shaft. Now remove the guard plate from the drive shaft (Fig. 9). 2. Release the 4 screws (M6/w.s.10) at the coupling bracket for the upper gear unit of the OLTC. Take care of coupling bolts and screws. 3. Then release the 4 screws (M6/w.s.10) at the coupling bracket of the bevel gear from the square tube. The horizontal drive shaft can now be removed. 16 WA 290/02 - VACUTAP® VR 290/02 EN 5 Removal Bleeder valve E1 CAUTION! Risk of blocking! Damage to the OLTC and transfor- mer! Avoid dropping parts into the diver- ter switch oil compartment. During maintenance therefore ple- ase keep all screws and small parts away from the open oil compart- ment. Make sure you have the correct number of small parts during disas- sembly and reinstallation. Valve tappet CAUTION! Damage to the diverter switch! Never carry out tap change opera- tions of the diverter switch insert in the oil compartment without the head cover in place, because this would damage the diverter switch! Figure 10: Bleeder valve E1 5.4 Removing the head cover Remove all 24 screws (M10/w.s.17) with locking washers of the head cover (see Fig. 11). Head cover OLTC head Screws Figure 11: OLTC head and head cover 290/02 EN 17 WA 290/02 - VACUTAP® VR 5 Removal 5.5 Removing the diverter switch insert For removing the diverter switch insert move the OLTC into the CAUTION! adjustment position (see Section 9.3 „Adjustment positions“, Dwg. No. 728557). Risk of blocking! Damage to the OLTC and transfor- Make sure you have the correct number of small parts during mer! disassembly and reinstallation. Avoid dropping parts into the di- Proceed as follows: verter switch oil compartment! Head cover Round rubber gasket Step 1: Remove the head cover (24 screws M10/w.s.17 with locking washers). Avoid damaging the faying surfaces on the head cover and the OLTC head during disassembly or other tasks (round rubber gasket, see Fig. 12). Figure 12: Head cover with gasket Tap change monitoring unit Clip Position indicator disc Step 2: Pull the clip from the shaft end and remove the position indicator disc (see Fig. 13). For disassembly of the bend (oil suction connection) cut the cable tie and remove the support plate and the bend (oil suction connection). Take care to avoid parts falling into the oil compartment! Bend (oil suction connection) Nuts M8/w.s.13 Transformer cover Figure 13: OLTC head components Connection cable Step 3: Plug connector Remove the tap change monitoring unit, if present. To this end remove 3 nuts M8/w.s.13 and the associated locking washers (see Fig. 13). Avoid damaging or tearing the connecting cables when re- moving the tap change monitoring unit (mounting plate with insulating shaft). Unplug the connector (see Fig. 14)! Figure 14: Tap change monitoring unit detail 18 WA 290/02 - VACUTAP® VR 290/02 EN 5 Removal Upper screening ring Lifting lugs Step 4: Before dismantling the diverter switch position the coup- ling tube according to the adjustment positions specified (see Section 9.3). This can be achieved by slight turning of the upper screening ring. Insert the lifting gear in the lifting lugs of the coupling tube (see Fig. 15) and position the lifting gear directly vertically above the diverter switch. Lift the diverter switch insert slowly and vertically. Once the diverter switch insert has been removed, the posi- tion of the tap selector coupling (see Fig. 16) must not be Coupling tube changed during assembly work. Figure 15: Coupling tube with lifting lugs Step 5: Position the diverter switch insert on the six supports (see Fig. 16). Secure the diverter switch insert against tipping! The diverter switch insert must not be operated while remo- ved from the system! Supports Tap selector coupling Figure 16: Diverter switch insert DANGER! Risk of tipping! Risk of severe injuries or death! All equipment must be supported securely when working on the OLTC, the motor drive unit or other com- ponents! Uncontrolled tipping of individual devices must be prevented! 290/02 EN 19 WA 290/02 - VACUTAP® VR 6 Maintenance 6 Maintenance 6.1 Oil compartment 6.1.2 Visual inspection 6.1.1 Cleaning Check the fixed main contacts and the inside of the oil com- partment with a mirror and a lamp (see Fig. 17). The contacts · Open the stop valve between the OLTC head and the oil should have a matt silver appearance. conservator of the OLTC. · Rinse the oil conservator of the OLTC with transformer oil. Check for mechanical or electrical damage (leakage path, di- scharge tracking) at the inside of the oil compartment. · Drain the oil from the oil compartment using an oil pump. · Ensure that the oil compartment is drained fully. A small quantity of transformer oil and absorbent, lint-free clea- CAUTION! ning rags are required for cleaning the oil compartment. A pho- Damage to the OLTC and transfor- to camera may be useful for documenting any defects. mer! Check the dehydrating breather and replace the drying agent if Replace any damaged parts imme- necessary. diately! If you are unsure, please contact the Technical Service of Ma- schinenfabrik Reinhausen GmbH. DANGER! In such a cases photographs of the affected sections are always useful. Fire hazard! Use pump equipment and hoses Fixed main contacts approved for inflammable liquids! CAUTION! Damage to the OLTC and transfor- mer! The oil compartment and the diver- ter switch insert must only be clea- ned with transformer oil! Other cleaning agents are unsuitable and jeopardize the trouble-free ope- ration of the OLTC and the transfor- Figure 17: Top view of oil compartment with fixed main mer. contacts 6.1.3 Covering the oil compartment After the inspection close the oil compartment with the head NOTE! cover. Avoid damaging the inner surface CAUTION! of the oil compartment and the as- sociated contacts. Damage to the OLTC and transfor- mer! Avoid dropping parts into the open diverter switch oil compartment. 20 WA 290/02 - VACUTAP® VR 290/02 EN 6 Maintenance 6.2 Diverter switch insert 2. Lift the lower screening ring and remove the six spacer sleeves using pliers (see Fig. 19). 6.2.1 Cleaning Thoroughly rinse the diverter switch insert with transformer oil. 6.2.2 Visual inspection Visually inspect the diverter switch insert with adequate ligh- ting. Check for mechanical or electrical damage (leakage path, discharge tracking). Coupling tube CAUTION! Damage to the OLTC and transfor- mer! Spacer sleeves Never carry out tap change opera- tions of the diverter switch in the oil compartment without the head co- ver in place. The diverter switch in- sert must not be operated while removed from the system. Replace any damaged parts imme- diately! Consult with MR. 6.3 Checking the coupling tube For all one- and two-phase OLTCs the coupling tube should be checked thoroughly. To this end the coupling tube has to be Figure 19: Spacer sleeves at the lower screening ring removed from the diverter switch insert. 1. Removal the 6 screws (M8/w.s.13, tightening torque 30 Nm) 3. Now pull off the coupling tube. holding the lower screening ring (see Fig. 18). 4. Clean the coupling tube with transformer oil. Note the oil quality limit values! 5. Visually inspect the inside and outside of the coupling tube. Check for mechanical or electrical damage (leakage path, discharge tracking). The coupling tube is reinstalled in reverse order. Coupling tube During reassembly ensure that position of the hole at the top of the coupling tube matches the adjustment marker on the diver- Screws ter switch insert (see Appendix Section 9.3 “Adjustment positi- ons”). In order to ensure the correct position of the adjustment mar- kers, during assembly of the coupling tube the parts must be arranged in the same ways as before disassembly. Figure 18: Screws at the lower screening ring 290/02 EN 21 WA 290/02 - VACUTAP® VR 6 Maintenance 6.4 Checking the movable main contacts The measurement should be taken at the movable main contact with the largest area affected by wear. If the mean height is Check the contact surfaces of the movable main contacts (rol- ler contacts) (see Fig. 20)! hmean = 1/3 (h1 + h2 + h3) > 5 mm please contact MR Technical Service! If you are unsure, please contact the MR Technical Service. In such a cases photographs of the affected sections are always useful. 6.5 Checking the transition resistors Visually inspect the transition resistors for irregularities. 6.6 Replacing the vacuum interrupters and stranded cable The vacuum interrupters (see Fig. 22) and the pigtails (see Fig. 23) should be replaced after 600,000 tap change operations. Please contact MR Technical Service. Stranded cable Movable main contact Figure 20: Movable main contact (roller contact) Determine the mean height of the areas affected by wear using a caliper gauge (see Fig. 21). Area affected by wear MSV Figure 22: Vacuum interrupter MSV Figure 21: Movable main contact (roller contact) and areas affected by wear 22 WA 290/02 - VACUTAP® VR 290/02 EN 6 Maintenance 6.8 Replacing the flexible connectors of the connecting contact Stranded cable The flexible connectors of the connecting contact at the upper bearing plate should be replaced after 300,000 tap change operations (see Fig. 25). Please contact MR Technical Service. Flexible connectors TTV Figure 23: Vacuum interrupter TTV Figure 25: Flexible connectors of the connecting contact 6.7 Checking the plain bearings 6.9 Replacing the varistor connection cables During reassembly of the diverter switch insert in the oil com- The upper varistor connecting cables and their fasteners should partment ensure that all six plain bearings are properly located be replaced after 600,000 tap change operations (see Fig. 26). in the upper bearing plate (see Fig. 24). If one of the plain Please contact MR Technical Service. bearings is not in its position, fix it with pure vaseline (petrole- um jelly). Fasteners Bearing plate (top) Plain bearing Connection cable Varistor Figure 24: Plain bearing in the upper bearing plate Figure 26: Varistor with connection cable 290/02 EN 23 WA 290/02 - VACUTAP® VR 6 Maintenance 6.10 Replacing the diverter switch insert 6.12 Tap selector maintenance The complete diverter switch should be replaced after 1.2 milli- The tap selector should be serviced after 1.2 million tap change on tap change operations. Please contact MR Technical Service. operations. Please contact MR Technical Service. Maschinenfabrik Reinhausen GmbH 6.11 Replacing the fixed main contacts Technical Service The fixed main contacts (MC) should be replaced after 1.2 mil- P.O. Box 12 03 60 lion tap change operations (see Fig. 27). 93025 Regensburg Germany Please contact MR Technical Service. Phone:+49 94140 90-0 Fax:+49 9 41 40 90-501 E-mail: [email protected] Internet: www.reinhausen.com Figure 27: Fixed main contacts (MC) 24 WA 290/02 - VACUTAP® VR 290/02 EN 7 Installation 7 Installation 7.1 Installing the diverter switch insert The diverter switch insert is reinstalled in reverse order, see Figs. 28 to 34. Adjustment markers Figure 28: Oil compartment bottom (VACUTAP® VRC, VRE) Adjustment markers Step 1: The adjustment position of the tap selector coupling for installing the diverter switch insert is shown in Figs. 28 to 30 for the individual OLTC versions (Fig. 28 for VACUTAP® VRC, VRE, Fig. 29 for VACUTAP® VRD, VRF, Fig. 30 for VACUTAP® VRG). Ensure that the energy accumulator of the diverter switch insert is locked in (the eccentric disc of the energy accumu- lator is at its highest point, see Section 9.4 - 9.11 „Adjust- ment plan“ for this diverter switch version). Attach the diverter switch insert to the lifting gear and posi- Figure 29: Oil compartment bottom (VACUTAP® VRD, VRF) tion it above the diverter switch oil compartment. The adjustment markers (red markings) of the upper sup- Adjustment markers porting plate (see Fig. 31 and Section 9.3 „ „adjustment positions“. Dwg. No. 728557) of the diverter switch insert and the OLTC head must be opposite each other. Slowly lower the diverter switch insert until reaches its res- ting position. Apply slight pressure until the upper bearing plate is positi- oned securely 32). The shape of the coupling claws (see Fig. 31) ensures that coupling is only possible in the correct position. Figure 30: Oil compartment bottom (VACUTAP® VRG) Upper bearing plate Figure 31: Upper bearing plate 290/02 EN 25 WA 290/02 - VACUTAP® VR 7 Installation Surface for applying pressure Step 2: Measure the distance between the upper edge of the diver- ter switch coupling tube and the head flange. It should be 10 ± 2 mm (see Fig. 32). Figure 32: Distance between the upper edge of the coupling tube and the head flange Bend (oil suction connection) Support plate Step 3: Insert the bend (oil suction connection) and fasten it to the support plate using a new, oil-resistant cable tie (width 3-5 Cable tie mm, length approx. 150 mm; included with the device) (see Fig. 33). If present, re-install the mounting plate for the tap change Figure 33: Bend (oil suction connection) monitoring unit and reconnect the plug connector (see Fig. 34). Connect the plug connector outside its bracket and Tap change monitoring unit Clip Position indicator disc before placing it in the bracket. Attach the position indicator dial: The coupling pin ensures that the position indicator disc is mounted in the correct position (see Fig. 34). Push the clip onto the shaft end. 1234567890123456789 1234567890123456789 12345678901234567890 1234567890123456789 12345678901234567890 1234567890123456789 Bend (oil suction 1234567890123456789 12345678901234567890 12345678901234567890 1234567890123456789 Plug connector 12345678901234567890 1234567890123456789 connection) 1234567890123456789 Transformer cover Figure 34: OLTC head components 26 WA 290/02 - VACUTAP® VR 290/02 EN 7 Installation Head cover Round rubber gasket Step 4: Close the OLTC head by lowering the head cover. Avoid damaging the new round rubber gasket in the head cover (order no. 860258). Fasten the head cover uniformly with 24 screws M10/w.s. 17. The tightening torque is 34 Nm (see Fig. 35). Figure 35: Head cover with gasket The temperature at the time of measuring the dielectric strength CAUTION! should be recorded. The specified dielectric strength values are valid for oil temperatures of 20 ± 5 °C. Damage to the OLTC! 1. Fill the oil compartment with transformer oil up to the upper During installation observe the red edge of the coupling shaft. adjustment markers (see Section 9.3 2. Replace the round rubber gasket (Order no. 860258) at head „Adjustment positions“, Dwg. No. cover (see Fig. 35). Ensure that all faying surfaces are clean. 728557)! 3. Close the OLTC head by lowering the head cover. Tighten all 24 M10 cover bolts (w.s. 17) uniformly (tightening torque 34 Nm). Ensure proper sealing. 7.2 Oil filling 4. Open the stop valve between the protective relay and the oil The OLTC oil compartment and the associated oil conservator conservator. must only be filled with new mineral insulating oil for transfor- 5. Fill the oil conservator with transformer oil. mers according to Table 5 based on IEC 60296 (Specification for unused mineral insulating oils for transformers and switch- CAUTION! gear) and IEC 60422 (Supervision and maintenance guide for mineral insulating oils in electrical equipment). Damage to the OLTC and trans- former! The use of oils other than those spe- cified in Table 5 may put the trou- ble-free operation of the on-load tap changer and the transformer at risk! *) measured according to IEC 60156 Table 5: Limit values for changing or treating the OLTC oil 290/02 EN 27 WA 290/02 - VACUTAP® VR 7 Installation 8 Further checks 6. Vent the OLTC head at the bleeder valve E1 of the head cover. 7.3 Connecting the drive shaft Open the screw cap (M30/w.s.36, tightening torque for 1. Connect the horizontal drive shaft with the upper gear unit closing 10 Nm) and lift the valve tappet with a screwdriver (see and the bevel gear (4 screws M6/w.s.10, tightening torque 9 Section 5.3 „Lowering the oil level“). Nm). 7. Vent the pipe connection at connection S (see Fig. 36) of the 2. Check the horizontal and vertical drive shaft, particularly at the OLTC head. Open the screw cap (M16/w.s.22, tightening coupling points (ensure that all screw joints are tight). If torque 9 Nm) and the bleeder screw (M6, slotted, tightening necessary lubricate the coupling bolt and the O-rings (e.g. torque 2 Nm) of the pipe connection. with Shell 6432), and set the axial clearance to 3 mm. 3. For special versions with ball joints check the concertina Bleeder screw covers and the grease supply of the ball joints. A detailed description of the procedure for installing the drive shaft can be found in Operating Instructions No. 42. 7.4 Coupling the OLTC and the motor drive unit Bleeder valve Connect the OLTC and the motor drive unit according to Opera- ting Instructions No. 138 for motor drive unit ED. CAUTION! Damage to the OLTC and trans- Pipe connection S former! The transformer may only be swit- ched on once the tasks described in Section 8 „Further checks“ have Figure 36: Pipe connection S with bleeder screw been carried out! CAUTION! Damage to the OLTC and trans- former! The transformer may only be swit- ched on after a stand-by period of at least one hour! 28 WA 290/02 - VACUTAP® VR 290/02 EN 8 Further checks 8 Further checks 8.1 Function control In both end positions check the automatic switch-off and the function of the electrical and mechanical end position limitati- Before applying voltage to the transformer some test opera- on (see Operating Instructions no. 138 for motor drive ED for tions must be carried out to check the mechanical functions of further maintenance instructions). tap changer and motor drive. For these test operations the tap changer has to be run through the entire operating range. 8.2 Protective relay RS 2001 Before the functional test visually inspect the protective relay and the OLTC head. Pay special attention to oil tightness at the CAUTION! sealing locations of the OLTC head, the protective relay, and the pipe connections. OLTC malfunction! The transformer must switch off when the protective relay is The OLTC should only be operated triggered by the circuit breakers. The functional test of the pro- via the upper gear unit! Direct ope- tective relay must therefore include the operation of the circuit ration via the coupling tube may breakers. cause problems! A maximum speed During the test the transformer must remain de-energized. The of 250 rpm must not be exceeded! ground connection at transformer must be retained. Ensure that activation of any fire extinguishing system that may be coupled with tripping of the protective relay is prevented. Make sure that in each operating position the indications of motor drive and tap changer (inspection window in the tap changer head) show the same position. DANGER! CAUTION! Risk of electric shock! Damage to the OLTC and trans- Before checking the protective re- former! lay ensure that the transformer is A coupling fault between tap chan- disconnected from the grid on all ger and motor drive unit exists, if sides, short-circuited, and groun- tap changer and motor drive unit ded at all terminals (including all star show a different operating positi- point terminals)! on. In this case the transformer must not be put into service! 290/02 EN 29 WA 290/02 - VACUTAP® VR 8 Further checks To check the protective relay proceed as follows: If the protective relay is triggered the diverter switch insert must be removed and check according to these Maintenance In- 1. Press the „OFF“ button on the protective relay. structions. 2. Leave the danger zone of the transformer! 3. It must no longer be possible to close the circuit breaker of the The procedure is described in Operating Instructions No. 59 for transformer: protective relay RS 2001. This also applies to triggering of addi- => “Passive protection test”. tional OLTC safety devices, such as the pressure relief valve. 4. Press the “ON” button on the protective relay. In case of major faults with the OLTC or the motor drive unit, 5. Leave the danger zone of the transformer! which cannot easily be rectified on site, or in the event of the 6. Close the circuit breaker of the transformer with isolating protective relay being triggered, please contact your MR repre- switches open and the transformer grounded on all sides. sentative, the transformer manufacturer, or 7. Press the “OFF” button on the protective relay. 8. The circuit breaker of the transformer should now open: => Maschinenfabrik Reinhausen GmbH “Active protection test”. Technical Service 9. Reset the protective relay by pressing the “ON” button. P.O. Box 12 03 60 93025 Regensburg Germany CAUTION! Phone:+49 94140 90-0 Fax: +49 9 41 40 90-501 Damage to the OLTC and trans- E-mail: [email protected] former! Internet: www.reinhausen.com After triggering of the protective re- lay, do not reset it until the on-load tap changer and the transformer have been checked. Do not recommission the system until you have made sure that the OLTC and the transformer are unda- maged. Reconnection of the transformer without prior checking is prohibi- 30 WA 290/02 - VACUTAP® VR 290/02 EN 9 Appendix - VACUTAP® Appendix VR OLTC - VACUTAP® VR OLTC 9.1 Maintenance schedule - Tasks No. of switching operations Required maintenance tasks 300.000 600.000 900.000 1.200.000 Cleaning the oil compartment and visual x x x x inspection Cleaning of the oil conservator x x x x Cleaning the diverter switch insert and visual x x x inspection Checking the coupling tube x x x Checking the movable main contacts x x x Checking the transition resistors x x x Replacing the vacuum interrupters and stranded x cables Checking the plain bearings x x x x Replacing the flexible connectors of the x x x connecting contact Replacing the varistor connection cables x Replacing the diverter switch insert x Replacing the fixed main contacts x Tap selector maintenance x Replacing the round rubber gasket in the head x x x x cover 290/02 EN WA 290/02 - VACUTAP® VR 31 7285331E_1 9 Appendix - VACUTAP® VR OLTC 9.2 Switching sequence (728533) 290/02 EN 32 WA 290/02 - VACUTAP® VR 7285331E_2 9 Appendix - VACUTAP® VR OLTC 9.2 Switching sequence (728533) 290/02 EN WA 290/02 - VACUTAP® VR 33 7285570E 9 Appendix - VACUTAP® VR OLTC 9.3 Adjustment positions (728557) 290/02 EN 34 WA 290/02 - VACUTAP® VR 7198522E 9 Appendix - VACUTAP® VR OLTC 9.4 Adjustment plan for VACUTAP® VRC, VRE with coarse tap selector (719852) 290/02 EN WA 290/02 - VACUTAP® VR 35 7198532E_1 9 Appendix - VACUTAP® VR OLTC 9.5 Adjustment plan for VACUTAP® VRC, VRE without change-over selector (719853) 290/02 EN 36 WA 290/02 - VACUTAP® VR 7198532E_2 9 Appendix - VACUTAP® VR OLTC 9.5 Adjustment plan for VACUTAP® VRC, VRE without change- over selector (719853) 290/02 EN WA 290/02 - VACUTAP® VR 37 7198502E 9 Appendix - VACUTAP® VR OLTC 9.6 Adjustment plan for VACUTAP® VRC III/ II, VRE III with reversing change-over selector (719850) 290/02 EN 38 WA 290/02 - VACUTAP® VR 7198512E 9 Appendix - VACUTAP® VR OLTC 9.7 Adjustment plan for VACUTAP® VRC I and VRE I with reversing change-over selector (719851) 290/02 EN WA 290/02 - VACUTAP® VR 39 7210891E_1 9 Appendix - VACUTAP® VR OLTC 9.8 Adjustment plan for VACUTAP® VRD, VRF without change-over selector (721089) 290/02 EN 40 WA 290/02 - VACUTAP® VR 7210891E_2 9 Appendix - VACUTAP® VR OLTC 9.8 Adjustment plan for VACUTAP® VRD, VRF without change- over selector (721089) 290/02 EN WA 290/02 - VACUTAP® VR 41 7210911E 9 Appendix - VACUTAP® VR OLTC 9.9 Adjustment plan for VACUTAP® VRD, VRF with coarse tap selector (721091) 290/02 EN 42 WA 290/02 - VACUTAP® VR 7270742E 9 Appendix - VACUTAP® VR OLTC 9.10 Adjustment plan for VACUTAP® VRG with reversing change- over selector (727074) 290/02 EN WA 290/02 - VACUTAP® VR 43 7270752E 9 Appendix - VACUTAP® VR OLTC 9.11 Adjustment plan for VACUTAP® VRG with coarse tap selector (727075) 290/02 EN 44 WA 290/02 - VACUTAP® VR 7230160E 9 Appendix - VACUTAP® VR OLTC 9.12 Tools (723016) 290/02 EN WA 290/02 - VACUTAP® VR 45 9 Appendix - VACUTAP® VR OLTC 9.13 Fax template From: Department: From: Phone: E-mail: Date: To: Maschinenfabrik Reinhausen GmbH Technical Service Tel. +49 941 40 90-0 PO Box 12 03 60 Fax +49 941 40 90-501 D-93059 Regensburg E-mail [email protected] Type: Serial number: Counter reading: Comments: 290/02 EN 46 WA 290/02 - VACUTAP® VR ®Maschinenfabrik Reinhausen GmbH Phone +49 (0)941 4090 0 www.reinhausen.com Falkensteinstrasse 8 Fax +49 (0)941 4090 111 93059 Regensburg, Germany e-mail [email protected] WA 290/02 EN 0708/500 F0154601 Printed in Germany