VACUTAP® VT® On-load Tap-changer Operating Instructions PDF
Document Details
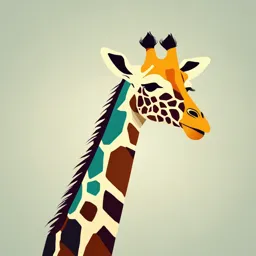
Uploaded by BestSellingBeige
null
Tags
Related
- On-Load Tap Changer Type T Operating Instructions PDF
- On-Load Tap Changer Type T Operating Instructions PDF
- VACUTAP® VM 300 On-load tap-changer Operating Instructions PDF
- VACUTAP® VV® On-load tap-changer Operating Instructions PDF
- On-Load TapChanger Type D Operating Instructions PDF
- On-Load Tap Changer Type A Operating Instructions PDF
Summary
This document provides operating instructions for an on-load tap-changer. It covers safety precautions, appropriate use, maintenance intervals, and details about the product's electrical and mechanical components. It includes illustrations, and diagrams, focusing on practical use and technical maintenance.
Full Transcript
On-load tap-changer VACUTAP® VT® Operating instructions 4349309/03 EN © All rights reserved by Maschinenfabrik Reinhausen Dissemination and reproduction of this document and use and disclosure of its content are strictly prohibited unless expressly permitted. Infringements will result in liability...
On-load tap-changer VACUTAP® VT® Operating instructions 4349309/03 EN © All rights reserved by Maschinenfabrik Reinhausen Dissemination and reproduction of this document and use and disclosure of its content are strictly prohibited unless expressly permitted. Infringements will result in liability for compensation. All rights reserved in the event of the granting of patents, utility models or designs. The product may have been altered since this document was published. We reserve the right to change the technical data, design and scope of supply. Generally the information provided and agreements made when processing the individual quotations and orders are binding. The original operating instructions were written in German. Table of contents Table of contents 1 Introduction......................................................................................................................... 5 1.1 Manufacturer....................................................................................................................................... 5 1.2 Completeness..................................................................................................................................... 5 1.3 Safekeeping........................................................................................................................................ 5 1.4 Notation conventions.......................................................................................................................... 6 1.4.1 Hazard communication system............................................................................................................................. 6 1.4.2 Information system................................................................................................................................................ 7 1.4.3 Instruction system................................................................................................................................................. 7 2 Safety................................................................................................................................... 9 2.1 Appropriate use.................................................................................................................................. 9 2.2 Inappropriate use.............................................................................................................................. 10 2.3 Fundamental safety instructions....................................................................................................... 10 2.4 Personal protective equipment......................................................................................................... 12 2.5 Personnel qualification...................................................................................................................... 13 3 Product description.......................................................................................................... 14 3.1 Scope of delivery.............................................................................................................................. 14 3.2 On-load tap-changer......................................................................................................................... 14 3.2.1 Function description............................................................................................................................................ 14 3.2.2 Design................................................................................................................................................................. 15 3.2.3 Name plate.......................................................................................................................................................... 17 3.3 Drive shaft......................................................................................................................................... 18 3.3.1 Function description............................................................................................................................................ 18 3.3.2 Design/versions................................................................................................................................................... 19 4 Commissioning................................................................................................................. 20 4.1 Commissioning transformer at operating site................................................................................... 20 4.1.1 Performing trial tap-change operations............................................................................................................... 20 4.1.2 Commissioning the transformer.......................................................................................................................... 20 5 Operation........................................................................................................................... 21 5.1 Operating the motor-drive unit with the hand crank.......................................................................... 21 6 Fault elimination............................................................................................................... 23 Maschinenfabrik Reinhausen GmbH 2021 4349309/03 EN VACUTAP® VT® 3 Table of contents 7 Maintenance...................................................................................................................... 24 7.1 Inspection......................................................................................................................................... 24 7.1.1 Cleaning and lubricating on-load tap-changer.................................................................................................... 25 7.2 Maintenance intervals....................................................................................................................... 27 7.3 Measuring DC resistance on transformer......................................................................................... 28 8 Technical data................................................................................................................... 29 8.1 On-load tap-changer properties........................................................................................................ 29 8.2 Permissible ambient conditions........................................................................................................ 29 9 Drawings........................................................................................................................... 30 9.1 VACUTAP® VT I 500, installation drawing (898312)....................................................................... 30 9.2 VACUTAP® VT I 500, dimensional drawing (897979)..................................................................... 31 9.3 VACUTAP® VT I 500, switching sequence (899507)....................................................................... 32 9.4 VACUTAP® VT I 500, fitting variants (897377)................................................................................ 33 9.5 VACUTAP® VT I 500, adjustment plan (898613)............................................................................. 34 9.6 VACUTAP® VT I 500, determining insulating shaft length (897975)............................................... 35 9.7 TAPMOTION® ED with CD 6400, limit dimension of vertical drive shaft (898598).......................... 36 9.8 Bevel gear CD 6400, dimensional drawing (892916)....................................................................... 37 List of key words.............................................................................................................. 38 4 VACUTAP® VT® 4349309/03 EN Maschinenfabrik Reinhausen GmbH 2021 1 Introduction 1 Introduction This technical file contains detailed descriptions for monitoring during opera- tion, fault elimination, and maintenance. It also includes safety instructions and general information about the prod- uct. Information about installation can be found in the installation and commis- sioning instructions. This technical file is intended solely for specially trained and authorized per- sonnel. 1.1 Manufacturer The product is manufactured by: Maschinenfabrik Reinhausen GmbH Falkensteinstraße 8 93059 Regensburg Tel.: (+49) 9 41/40 90-0 E-mail: [email protected] Further information on the product and copies of this technical file are avail- able from this address if required. 1.2 Completeness This technical file is incomplete without the supporting documents. The following documents are considered supporting documents: ▪ Unpacking instructions ▪ Supplement ▪ Routine test report ▪ Connection diagrams ▪ Dimensional drawings ▪ Order confirmation 1.3 Safekeeping Keep this technical file and all supporting documents ready at hand and ac- cessible for future use at all times. Maschinenfabrik Reinhausen GmbH 2021 4349309/03 EN VACUTAP® VT® 5 1 Introduction 1.4 Notation conventions 1.4.1 Hazard communication system Warnings in this technical file are displayed as follows. 1.4.1.1 Warning relating to section Warnings relating to sections refer to entire chapters or sections, sub-sec- tions or several paragraphs within this technical file. Warnings relating to sections use the following format: WARNING Type of danger! Source of the danger and outcome. ► Action ► Action 1.4.1.2 Embedded warning information Embedded warnings refer to a particular part within a section. These warn- ings apply to smaller units of information than the warnings relating to sec- tions. Embedded warnings use the following format: DANGER! Instruction for avoiding a dangerous situation. 1.4.1.3 Signal words and pictograms The following signal words are used: Signal word Definition DANGER Indicates a hazardous situation which, if not avoided, will result in death or serious injury. WARNING Indicates a hazardous situation which, if not avoided, could result in death or serious injury. CAUTION Indicates a hazardous situation which, if not avoided, could result in minor or moderate injury. NOTICE Indicates measures to be taken to prevent damage to property. Table 1: Signal words in warning notices 6 VACUTAP® VT® 4349309/03 EN Maschinenfabrik Reinhausen GmbH 2021 1 Introduction Pictograms warn of dangers: Pictogram Definition Warning of a danger point Warning of dangerous electrical voltage Warning of combustible substances Warning of danger of tipping Warning of danger of crushing Table 2: Pictograms used in warning notices 1.4.2 Information system Information is designed to simplify and improve understanding of particular procedures. In this technical file it is laid out as follows: Important information. 1.4.3 Instruction system This technical file contains single-step and multi-step instructions. Single-step instructions Instructions which consist of only a single process step are structured as fol- lows: Maschinenfabrik Reinhausen GmbH 2021 4349309/03 EN VACUTAP® VT® 7 1 Introduction Aim of action ü Requirements (optional). ► Step 1 of 1. ð Result of step (optional). ð Result of action (optional). Multi-step instructions Instructions which consist of several process steps are structured as follows: Aim of action ü Requirements (optional). 1. Step 1. ð Result of step (optional). 2. Step 2. ð Result of step (optional). ð Result of action (optional). 8 VACUTAP® VT® 4349309/03 EN Maschinenfabrik Reinhausen GmbH 2021 2 Safety 2 Safety ▪ Read this technical file through to familiarize yourself with the product. ▪ This technical file is a part of the product. ▪ Read and observe the safety instructions provided in this chapter. ▪ Read and observe the warnings in this technical file in order to avoid func- tion-related dangers. ▪ The product is manufactured on the basis of state-of-the-art technology. Nevertheless, risks to life and limb for the user or impairment of the prod- uct and other material assets due to the function may arise in the event of improper use. 2.1 Appropriate use The product is an on-load tap-changer and adjusts the transmission ratio of transformers without interrupting the load flow. The product is designed solely for use in electrical energy systems and facilities. If used as intended and in compliance with the requirements and conditions specified in this technical file as well as the warning notices in this technical file and attached to the product, then the product does not present any danger to people, property or the environment. This applies throughout the service life of the product, from delivery, installation and operation to removal and disposal. The following is considered appropriate use: ▪ Use the product only with the transformer/motor-drive unit specified in the order. ▪ The serial numbers of on-load tap-changer and on-load tap-changer ac- cessories (drive, drive shaft, bevel gear, protective relay, etc.) must match if the on-load tap-changer and on-load tap-changer accessories are sup- plied as a set for one order. ▪ You will find the standard valid for the product and the year of issue on the nameplate. ▪ Operate the product in accordance with this provided technical file, the agreed delivery conditions and technical data. ▪ Ensure that all necessary work is performed by qualified personnel only. ▪ Only use the equipment and special tools included in the scope of delivery for the intended purpose and in accordance with the specifications of this technical file. ▪ For this on-load tap-changer, indoor installation in accordance with envi- ronmental class E0 in accordance with IEC 60076-11:2004 is mandatory. Fire class F0 in accordance with IEC 60076-11:2004 is satisfied. ▪ Take suitable measures to ensure that no condensation forms on the on- load tap-changer and that the on-load tap-changer is not susceptible to dew condensation or icing. The on-load tap-changer has no protective housing. Maschinenfabrik Reinhausen GmbH 2021 4349309/03 EN VACUTAP® VT® 9 2 Safety Permitted electrical operating conditions In addition to the design data in accordance with the order confirmation, ob- serve the following limits for the through-current and the step voltage: In the standard version, the on-load tap-changer is designed for sinusoidal 50/60 Hz alternating current with a curve form symmetrical to the zero axis and can switch 2 times the rated through-current Ir at its rated step voltage Uir. Exceeding the rated step voltage Uir by up to 10% for a short period is per- mitted as long as the rated step capacity PStN permissible for this step volt- age is not exceeded. 2.2 Inappropriate use Use is considered inappropriate if the product is used in a way other than as described in the "Appropriate use" section. In addition, observe the following: Prohibited electrical operating conditions All operating conditions that do not comply with the design data in accor- dance with the order confirmation are prohibited. Prohibited operating conditions may arise due to short circuits as well as due to inrush current impulses when energizing transformers or other electrical machines. This applies to the affected transformer itself just as it does to transformers electrically connected in parallel or serially or other electrical machines. Higher voltages may occur due to transformer overexcitation following load shedding, for example. Operations outside of the permitted operating conditions can lead to injury to persons and damage to the product. ▪ Prevent any such operations outside of the permitted operating conditions by taking suitable measures. 2.3 Fundamental safety instructions To prevent accidents, malfunctions and damage as well as unacceptable ad- verse effects on the environment, those responsible for transport, installa- tion, operation, maintenance and disposal of the product or parts of the prod- uct must ensure the following: 10 VACUTAP® VT® 4349309/03 EN Maschinenfabrik Reinhausen GmbH 2021 2 Safety Personal protective equipment Loosely worn or unsuitable clothing increases the danger of becoming trapped or caught up in rotating parts and the danger of getting caught on protruding parts. This poses a danger to life and limb. ▪ Wear appropriate personal protective equipment such as a helmet, work gloves, etc. for the respective activity. ▪ Never wear damaged personal protective equipment. ▪ Never wear rings, necklaces, or other jewelry. ▪ If you have long hair, wear a hairnet. Work area Untidy and poorly lit work areas can lead to accidents. ▪ Keep the work area clean and tidy. ▪ Make sure that the work area is well lit. ▪ Observe the applicable laws for accident prevention in the relevant coun- try. Working during operation The product may only be operated in a sound, operational condition. Other- wise it poses a danger to life and limb. ▪ Regularly check the operational reliability of safety equipment. ▪ Comply with the inspection work, maintenance work and maintenance in- tervals described in this technical file. Explosion protection Highly flammable or explosive gases, vapors and dusts can cause serious explosions and fire. This increases the danger to life and limb. ▪ Do not install, operate or perform maintenance work on the product in ar- eas where a risk of explosion is present. Safety markings Warning signs and safety information plates are safety markings on the product. They are an important aspect of the safety concept. ▪ Observe all safety markings on the product. ▪ Make sure all safety markings on the product remain intact and legible. ▪ Replace safety markings that are damaged or missing. Ambient conditions To ensure reliable and safe operation, the product must only be operated under the ambient conditions specified in the technical data. ▪ Observe the specified operating conditions and requirements for the in- stallation location. Maschinenfabrik Reinhausen GmbH 2021 4349309/03 EN VACUTAP® VT® 11 2 Safety Auxiliary materials and operating materials Auxiliary materials and operating materials not approved by the manufac- turer can lead to personal injury, damage to property and malfunctions of the product. ▪ Only use lubricants and auxiliary materials approved by the manufacturer. ▪ Contact the manufacturer. Modifications and conversions Unauthorized or inappropriate changes to the product may lead to personal injury, material damage and operational faults. ▪ Only modify the product after consultation with Maschinenfabrik Rein- hausen GmbH. Spare parts Spare parts not approved by Maschinenfabrik Reinhausen GmbH may lead to physical injury, damage to the product and malfunctions. ▪ Only use spare parts that have been approved by Maschinenfabrik Rein- hausen GmbH. ▪ Contact Maschinenfabrik Reinhausen GmbH. 2.4 Personal protective equipment Personal protective equipment must be worn during work to minimize risks to health. ▪ Always wear the personal protective equipment required for the job at hand. ▪ Never wear damaged personal protective equipment. ▪ Observe information about personal protective equipment provided in the work area. Protective clothing Close-fitting work clothing with a low tearing strength, with tight sleeves and with no protruding parts. It mainly serves to protect the wearer against being caught by moving machine parts. Safety shoes To protect against falling heavy objects and slipping on slippery surfaces. Safety glasses To protect the eyes from flying parts and splashing liq- uids. Visor To protect the face from flying parts and splashing liq- uids or other dangerous substances. Hard hat To protect against falling and flying parts and materials. Hearing protection To protect against hearing damage. Protective gloves To protect against mechanical, thermal, and electrical hazards. Table 3: Personal protective equipment 12 VACUTAP® VT® 4349309/03 EN Maschinenfabrik Reinhausen GmbH 2021 2 Safety 2.5 Personnel qualification The person responsible for assembly, commissioning, operation, mainte- nance and inspection must ensure that the personnel are sufficiently quali- fied. Electrically skilled person The electrically skilled person has a technical qualification and therefore has the required knowledge and experience, and is also conversant with the ap- plicable standards and regulations. The electrically skilled person is also pro- ficient in the following: ▪ Can identify potential dangers independently and is able to avoid them. ▪ Is able to perform work on electrical systems. ▪ Is specially trained for the working environment in which (s)he works. ▪ Must satisfy the requirements of the applicable statutory regulations for accident prevention. Electrically trained persons An electrically trained person receives instruction and guidance from an electrically skilled person in relation to the tasks undertaken and the poten- tial dangers in the event of inappropriate handling as well as the protective devices and safety measures. The electrically trained person works exclu- sively under the guidance and supervision of an electrically skilled person. Operator The operator uses and operates the product in line with this technical file. The operating company provides the operator with instruction and training on the specific tasks and the associated potential dangers arising from im- proper handling. Technical Service We strongly recommend having maintenance, repairs and retrofitting carried out by our Technical Service department. This ensures that all work is per- formed correctly. If maintenance is not carried out by our Technical Service department, please ensure that the personnel who carry out the mainte- nance are trained and authorized by Maschinenfabrik Reinhausen GmbH to carry out the work. Authorized personnel Authorized personnel are trained by Maschinenfabrik Reinhausen GmbH to carry out special maintenance. Maschinenfabrik Reinhausen GmbH 2021 4349309/03 EN VACUTAP® VT® 13 3 Product description 3 Product description 3.1 Scope of delivery The product is delivered as follows: ▪ On-load tap-changer ▪ Motor-drive unit ▪ Drive shaft with coupling parts and bevel gear ▪ Technical files Note the following information: ▪ Check the shipment for completeness on the basis of the shipping docu- ments. ▪ Store the parts in a dry place until installation ▪ The product must remain in its airtight, protective wrapping and may only be removed immediately before installation You will find more information in the "Packaging, transport, and storage" chapter. 3.2 On-load tap-changer 3.2.1 Function description On-load tap-changers are used to adjust the transmission ratio of transform- ers without interrupting the load flow. This makes it possible to compensate for aspects such as fluctuations in voltage occurring in the power transmis- sion grid. For this purpose, on-load tap-changers are fitted in transformers and connected to the active part of the transformer. A motor-drive unit which receives a control impulse (e.g. from a voltage reg- ulator) changes the operating position of the on-load tap-changer, as a result of which the transformer's transmission ratio is adapted to the prevailing op- erating requirements. 14 VACUTAP® VT® 4349309/03 EN Maschinenfabrik Reinhausen GmbH 2021 3 Product description Figure 1: Overview of a 3-phase system 1 Transformer tank 5 Insulating shaft (horizontal drive shaft) 2 Motor-drive unit 6 Bevel gear of on-load tap-changer 3 Square tube (vertical drive shaft) 7 On-load tap-changer 4 Bevel gear of motor-drive unit 8 Active part 3.2.2 Design The following drawing shows the main components of the on-load tap- changer. Maschinenfabrik Reinhausen GmbH 2021 4349309/03 EN VACUTAP® VT® 15 3 Product description You will find a detailed drawing of the on-load tap-changer in the "Drawings [►Section 9, Page 30]" section. Figure 2: Design 1 Insulating plate 6 Switching element 2 Screening sleeve 7 Threaded spindle 3 Insulating shaft 8 Bevel gear 4 Take-off contact 9 Mounting bridge 5 Connection contact 16 VACUTAP® VT® 4349309/03 EN Maschinenfabrik Reinhausen GmbH 2021 3 Product description 3.2.3 Name plate The name plate is located on the bevel gear's mounting arm: Figure 3: Name plate Maschinenfabrik Reinhausen GmbH 2021 4349309/03 EN VACUTAP® VT® 17 3 Product description 3.3 Drive shaft 3.3.1 Function description The drive shaft is the mechanical connection between the drive and the on- load tap-changer/de-energized tap-changer. The bevel gear changes the direction from vertical to horizontal. Accordingly, the vertical drive shaft has to be mounted between drive and bevel gear, and the horizontal drive shaft between bevel gear and on-load tap-changer or de-energized tap-changer. 18 VACUTAP® VT® 4349309/03 EN Maschinenfabrik Reinhausen GmbH 2021 3 Product description 3.3.2 Design/versions The drive shaft consists of a square tube and is coupled at each end by two coupling brackets/coupling sleeves and one coupling bolt to the driving or driven shaft end of the device to be connected. Figure 4: Components of the drive shaft 1 Bevel gear 2 Hose clip 3 Telescopic protective tube 4 Coupling bracket 5 Square tube 6 Coupling bolt 7 Adapter ring 8 Insulating shaft (square tube) 9 Screening sleeve 10 Coupling sleeve 11 Coupling bolt Maschinenfabrik Reinhausen GmbH 2021 4349309/03 EN VACUTAP® VT® 19 4 Commissioning 4 Commissioning WARNING Danger of explosion! Overloading the on-load tap-changer can lead to explosion. ► Ensure that the on-load tap-changer is not overloaded. ► Ensure use of the on-load tap-changer in accordance with section "Ap- propriate use". ► Prevent operations outside of the permitted operating conditions by tak- ing suitable measures. 4.1 Commissioning transformer at operating site Check that the motor-drive unit functions correctly before energizing the transformer. 4.1.1 Performing trial tap-change operations Before energizing the transformer, trial tap-change operations must be car- ried out to check the mechanical functions of on-load tap-changer and mo- tor-drive unit. 1. NOTICE! Damage to the on-load tap-changer due to time interval be- tween successive tap-change operations being too short. Manually under- take trial tap-change operations (33 hand crank revolutions on motor-drive unit) across entire tapping range. Wait at least 60 seconds between the individual tap-change operations. 2. NOTICE! An incorrectly coupled motor-drive unit will lead to damage to the on-load tap-changer. Ensure that in each operating position the tap position indicator of the motor-drive unit matches the contact designation on the on-load tap-changer. 3. In both end positions, check the function of the electrical and mechanical end stop in accordance with the motor-drive unit operating instructions. 4.1.2 Commissioning the transformer 1. Switch on transformer. 2. NOTICE! Inrush current impulses can be significantly greater than the transformer rated current and may lead to current paths with asymmetrical or non-sinusoidal curve shapes and, as a result, overload the on-load tap- changer during the diverter switch operation. Only perform tap-change op- erations - whether under no load or under load conditions - once the in- rush current impulse has subsided. 20 VACUTAP® VT® 4349309/03 EN Maschinenfabrik Reinhausen GmbH 2021 5 Operation 5 Operation 5.1 Operating the motor-drive unit with the hand crank WARNING Danger of explosion! Unauthorized operation of the motor-drive unit with the hand crank may re- sult in death or serious injury. ► Never operate the motor-drive unit electrically or with the hand crank be- fore the transformer has been disconnected if you think there may be a fault in the transformer or on-load tap-changer / de-energized tap- changer. ► Never use the hand crank to complete a tap-change operation that has begun electrically, but has not been ended completely. ► If the hand crank is difficult to move, you must stop using it. ► When operating the motor-drive unit with the hand crank, never reverse the direction of rotation. ► If there is any doubt about the on-load tap-changer / de-energized tap- changer being in proper working condition or about the cause of a fault in the motor-drive unit, contact the Technical Service department of Maschi- nenfabrik Reinhausen GmbH immediately. ► To operate the motor-drive unit manually, only use the hand crank mounted in the motor-drive unit. For information about fault rectification, refer to the "Fault elimination" chap- ter. Normal operation During normal operation, there is no need to operate the unit with the hand crank. The hand crank is mainly required during installation and for tests in the transformer plant. Use of the hand crank for operating the motor-drive unit is permitted if the transformer is disconnected, e.g. for maintenance tasks, if there is no de- tectable fault on the transformer or on-load tap-changer / de-energized tap- changer and the previous tap-change operation has been completed cor- rectly. Emergency operation exception An operation is considered an emergency operation if a tap-change opera- tion is absolutely necessary when a transformer is energized, despite a fault in the motor-drive unit. In this case, be sure to observe the warnings listed above. Maschinenfabrik Reinhausen GmbH 2021 4349309/03 EN VACUTAP® VT® 21 5 Operation Operating the motor-drive unit with the hand crank To carry out a tap-change operation with the hand crank, proceed as follows: 1. Open the door of the protective housing for the motor-drive unit. 2. Switch off motor protective switch Q1 (position 0). 3. Insert the hand crank mounted in the motor-drive unit into the hand crank aperture in the upper cover plate. ð The built-in hand crank interlock switch interrupts the motor circuit at two poles. The control circuit will not be interrupted. 4. NOTICE! Damage to the on-load tap-changer due to tap-change opera- tion not being completed correctly. Turn the hand crank in one direction until the pointer has fully circled the tap-change indicator once and is again in the mid-position of the area marked in gray on the tap-change in- dicator. ð The tap-change operation is complete. 5. Remove the hand crank and return it to the mounting bracket. 6. Switch on motor protective switch Q1 (position I). 7. Close the door of the protective housing for the motor-drive unit. 22 VACUTAP® VT® 4349309/03 EN Maschinenfabrik Reinhausen GmbH 2021 6 Fault elimination 6 Fault elimination The table below is intended to assist with detecting and, where possible, remedying faults. For more serious problems with the on-load tap-changer and motor-drive unit, which cannot be easily corrected on site, please inform your authorized MR representative, the transformer manufacturer or contact us directly at Maschinenfabrik Reinhausen GmbH Technischer Service Postfach 12 03 60 93025 Regensburg Germany Phone: +49 94140 90-0 Fax: +49 9 41 40 90-7001 E-mail: [email protected] Internet: www.reinhausen.com Error pattern Action Tripping of motor protective switch in motor-drive unit Request "Information sheet on motor protective switch trip- ping" from MR, complete and return to MR. On-load tap-changer not changing tap position (sluggish- Contact MR. ness, Raise keys/Lower keys not working, diverter switch action not audible) No change in voltage on transformer despite change in po- Contact MR. sition on motor-drive unit Tap position indicator on motor-drive unit and on-load tap- Contact MR. changer different Noises on drive shaft or motor-drive unit when changing Check that the drive shaft is attached correctly as de- tap position scribed in the "Attaching drive components" section. Check that hose clips and protective covers are seated correctly. Contact MR in the event of noise from the motor-drive unit. Red message on monitoring unit If possible read out database and send to MR along with error code. Deviation from desired value when measuring winding re- Contact manufacturer of transformer and, if necessary, MR sistance of transformer and provide measured values. Deviation from desired value during transformer ratio test Contact manufacturer of transformer and, if necessary, MR and provide measured values. Table 4: Fault elimination Maschinenfabrik Reinhausen GmbH 2021 4349309/03 EN VACUTAP® VT® 23 7 Maintenance 7 Maintenance DANGER Electric shock! An energized transformer could cause death or serious injuries. ► Switch off transformer on high and low-voltage side. ► Lock transformer to prevent unintentional restart. ► Ensure that everything is de-energized. ► Visibly connect all transformer terminals to ground (grounding leads, grounding disconnectors) and short circuit them. ► Cover or cordon off adjacent energized parts. NOTICE Damage to motor-drive unit! Damage to the motor-drive unit due to condensate in protective housing of motor-drive unit. ► Always keep protective housing of the motor-drive unit tightly closed. ► In the event of operation interruptions of more than 2 weeks, connect and operate the anti-condensation heater in the motor-drive unit. If this is not possible, e.g. during transportation, place a sufficient amount of desiccant in the protective housing. 7.1 Inspection Monitoring the on-load tap-changer and motor-drive unit is limited to occa- sional visual checks of the on-load tap-changer and motor-drive unit. For ef- ficiency reasons these visual inspections can be combined with the usual checks on the transformer. Check the following: Interval Action Every 6 months Clean and lubricate on-load tap-changer [►Section 7.1.1, Page 25]. Annually Check door seal, cable bushings, and ventilation of protective housing of motor-drive unit/control cabinet. Annually Check correct functioning of the installed electrical heater in the protective housing of the motor-drive unit/control cabinet. Table 5: Inspection plan 24 VACUTAP® VT® 4349309/03 EN Maschinenfabrik Reinhausen GmbH 2021 7 Maintenance 7.1.1 Cleaning and lubricating on-load tap-changer 1. DANGER! Danger to life due to electric shock. Ensure that the trans- former is switched off on the high-voltage side and low-voltage side and that it cannot be switched back on. 2. Clean all sides of insulating plates and insulating shaft with a dry cloth. Figure 5: Insulating plates and insulating shafts 1 Insulating plates 2 Insulating shafts Maschinenfabrik Reinhausen GmbH 2021 4349309/03 EN VACUTAP® VT® 25 7 Maintenance 3. Remove used grease from the parts specified in the table below. Figure 6: Parts to be lubricated 1 Threaded spindle 5 Movable output terminal 2 L guide bar 6 Movable shunt contact 3 Output terminal bar 7 Movable resistor contact 4 Connection contact 8 Auxiliary contact bar 4. Lubricate specified parts with new lubricant ISOFLEX TOPAS NCA 5051 (available on request). 5. Carry out trial tap-change operations (2 x regulating range). 26 VACUTAP® VT® 4349309/03 EN Maschinenfabrik Reinhausen GmbH 2021 7 Maintenance 7.2 Maintenance intervals Interval Action Detail Action performed by After 2 years or First maintenance ▪ Check for damage. Maschinenfabrik Rein- 100,000 tap- If 100,000 tap-change operations are reached: hausen GmbH change operations, depending on what ▪ Replace weight compensation spring. is reached first. ▪ Replace both plug blocks. ▪ Replace shock absorbers. After every 100,000 Maintenance ▪ Replace weight compensation spring. Maschinenfabrik Rein- tap-change opera- hausen GmbH tions ▪ Replace both plug blocks. ▪ Replace shock absorbers. After 200,000 oper- Additional work ▪ Replacing TTV vacuum interrupter. Maschinenfabrik Rein- ations hausen GmbH After 400,000 oper- Additional work ▪ Replace complete switching element. Maschinenfabrik Rein- ations hausen GmbH After 600,000 oper- Additional work ▪ Replacing TTV vacuum interrupter. Maschinenfabrik Rein- ations hausen GmbH After 800,000 oper- Replacement On-load tap-changer needs to be replaced. - ations Table 6: Maintenance plan Maschinenfabrik Reinhausen GmbH 2021 4349309/03 EN VACUTAP® VT® 27 7 Maintenance Figure 7: Parts on switching element requiring maintenance 1 Transition resistor 4 Plug blocks 2 Weight compensation springs 5 Shock absorbers 3 TTV vacuum interrupter 7.3 Measuring DC resistance on transformer Note the measurement scenarios listed below and the associated maximum measured currents when measuring DC resistance on the transformer. The measured DC current is normally restricted to 10% of the rated current of the measured transformer winding in order to prevent the winding from overheating. Take DC resistance measurement in various on-load tap-changer operating positions of measured current as described below: You can take the DC re- sistance measurement with or without interruption of measured current dur- ing the change of operating position: ▪ Without interruption in measured current: Maximum 10 A DC ▪ With interruption: Maximum 50 A DC – When changing operating position, the measured current must be 0 A 28 VACUTAP® VT® 4349309/03 EN Maschinenfabrik Reinhausen GmbH 2021 8 Technical data 8 Technical data An overview of all key technical data for the on-load tap-changer and motor- drive unit exists in the form of separate documents, which are available on request. 8.1 On-load tap-changer properties Electrical data for VACUTAP® VT I 500 On-load tap-changer VT I 500 Max. rated through-current Ium [A] 500 Rated short-time current [kA] 5 Rated duration of short-circuits [s] 3 Rated peak withstand current [kA] 12.5 1) Max. rated step voltage Uim [V] 900 Step capacity PStN [kVA] 250 Rated frequency [Hz] 50...60 Table 7: Electrical data for VACUTAP® VT I 500 Mechanical data for VACUTAP® VT I 500 Number of operating positions Max. 9, change-over selector not available Dimensions See dimensional drawings Weight [kg] Approx. 70 Table 8: Mechanical data for VACUTAP® VT I 500 8.2 Permissible ambient conditions Air temperature during operation -25°C…+65°C Transport temperature, storage temperature -40°C…+65°C Installation height above sea level See technical data TD 61 – General Section Table 9: Permissible ambient conditions Maschinenfabrik Reinhausen GmbH 2021 4349309/03 EN VACUTAP® VT® 29 9 Drawings 9 Drawings 9.1 VACUTAP® VT I 500, installation drawing (898312) 30 VACUTAP® VT® 4349309/03 EN Maschinenfabrik Reinhausen GmbH 2021 9 Drawings 9.2 VACUTAP® VT I 500, dimensional drawing (897979) Maschinenfabrik Reinhausen GmbH 2021 4349309/03 EN VACUTAP® VT® 31 9 Drawings 9.3 VACUTAP® VT I 500, switching sequence (899507) 32 VACUTAP® VT® 4349309/03 EN Maschinenfabrik Reinhausen GmbH 2021 9 Drawings 9.4 VACUTAP® VT I 500, fitting variants (897377) Maschinenfabrik Reinhausen GmbH 2021 4349309/03 EN VACUTAP® VT® 33 9 Drawings 9.5 VACUTAP® VT I 500, adjustment plan (898613) 34 VACUTAP® VT® 4349309/03 EN Maschinenfabrik Reinhausen GmbH 2021 9 Drawings 9.6 VACUTAP® VT I 500, determining insulating shaft length (897975) Maschinenfabrik Reinhausen GmbH 2021 4349309/03 EN VACUTAP® VT® 35 9 Drawings 9.7 TAPMOTION® ED with CD 6400, limit dimension of vertical drive shaft (898598) 36 VACUTAP® VT® 4349309/03 EN Maschinenfabrik Reinhausen GmbH 2021 9 Drawings 9.8 Bevel gear CD 6400, dimensional drawing (892916) Maschinenfabrik Reinhausen GmbH 2021 4349309/03 EN VACUTAP® VT® 37 List of key words List of key words D F T DC resistance measurement 28 Faults 23 Trial tap-change operation 20 38 VACUTAP® VT® 4349309/03 EN Maschinenfabrik Reinhausen GmbH 2021 Maschinenfabrik Reinhausen GmbH Falkensteinstrasse 8 93059 Regensburg +49 (0)941 4090-0 [email protected] www.reinhausen.com 4349309/03 EN - VACUTAP® VT® - - 10/21 - Maschinenfabrik Reinhausen GmbH 2021 THE POWER BEHIND POWER.