Tricot Machine PDF
Document Details
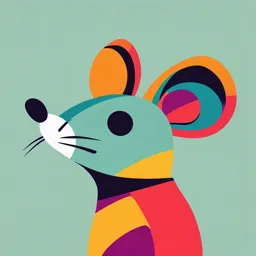
Uploaded by SimplestSaxhorn
Tags
Summary
This document provides an in-depth explanation of the tricot machine, including its components, functions, and the knitting cycle. It features diagrams showcasing the different stages of the cycle, focusing on the actions of needles, guides, sinkers, and pressers. The information presented is valuable for understanding the workings of this essential textile machinery.
Full Transcript
Knitting Technology Tricot Machine Tricot Machine The main parts of tricot machine are : â–º The warp beam carrying warp threads. â–º The sley bars which space the warp threads. â–ºThe tension bar which maintains tension in the warp threads, one bar for each warp. â–ºThe knitting ele...
Knitting Technology Tricot Machine Tricot Machine The main parts of tricot machine are : â–º The warp beam carrying warp threads. â–º The sley bars which space the warp threads. â–ºThe tension bar which maintains tension in the warp threads, one bar for each warp. â–ºThe knitting element, comprising the warp guides, sinkers, needles & presser bar. Tricot Machine â–ºThe fabric take up rollers which take the fabric from the rollers at a constant rate. â–ºThe batch roller which winds up the fabric on a large rolls. â–ºThe crank shaft drive within a case which holds the mechanism for driving the knitting elements. Knitting Elements The Needles â–ºThe needles mounted in lead are inserted vertically in the needle bar. â–º This bar gets motion from the main cam shaft. â–ºThe machine gauge, which normally varies between 20-36. â–ºThe length of the needle bar determines the width of the machine which varies between 210cm to 420cm. The Guides â–ºGuides are thin flat still wires and the unit in leads of 25mm wide are attached vertically to a complete guide bar assembly. â–ºUsually minimum 2 guide bars are provided on a tricot machine, 3 & 4 guide bar machines are also common. â–ºThe guide bar receives 2 types of motion, one forward and backward motion from main cam shaft and the lateral motion (shogging) from the pattern wheel. The Sinkers â–ºSinkers are also made of thin punched steel sheet the number of sinkers per 25 mm determine the gauge. â–ºThe function of sinker are, one, to hold the fabric down in the throat of the sinker, as the needle rises, and the other to prevent the needle rising through the old loop thus helping in knock over. â–ºThese are mounted in a movable sinker bar which also derives its motion from main cam shaft of machine. The Presser â–ºOn all the beard needle machines an external agency is provided to close the beard of the needle during the loop formation. â–ºThis is achieved through a presser which is a strip of fibrous or plastic material fitted to the presser bar along the needle bed. Knitting Cycle â–ºThe rest position (a). The needles have risen to 2/3 of their full height from knock-over and have their beards towards the back of the machine. â–º The presser is withdrawn. Knitting Cycle â–ºThe guides are at the front of the machine with the sinkers forward, holding the old overlaps in their throats so that they are maintained at the correct height on the needle stems. Knitting Cycle â–ºBackward swing and overlap shog (b, c). After swinging through the needles to the beard side, the guides are overlapped across the beards, usually by one needle space in opposite directions. Knitting Cycle â–ºThe return swing and second rise (c, d). As the guides swing to the front, the needles rise to their full height so that the newly- formed overlaps slip off the beards onto the stems above the old overlaps. Knitting Cycle â–ºThis arrangement reduces the amount of guide-bar swing necessary and therefore the time required. Knitting Cycle â–º Pressing (e). The needle bar descends so that the open beards cover the new overlaps. â–º There is a slight pause whilst the presser advances and closes the beards. Knitting Cycle â–ºLanding (f). As the sinkers withdraw, the upward curve of their bellies lands the old overlaps onto the closed beards. Knitting Cycle â–ºKnock-over and underlap shog (g). The presser is withdrawn and the continued descent of the needle bar causes the old overlaps to be knocked- over as the heads of the needles descend below the upper surface of the sinker bellies. Knitting Cycle â–ºThe underlap shog which can occur at any time between pressing and knock-over usually occurs in opposite directions on the two guide bars. Knitting Cycle â–ºThe sinkers now move forward to hold down the fabric loops and push them away from the ascending needles, which are rising to the rest position.