Pulvermetallurgie - Werkstoff- und Energiebedarf PDF
Document Details
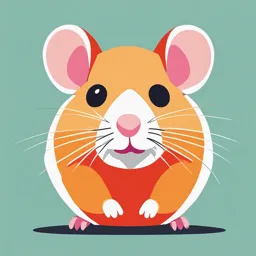
Uploaded by EnviableOlivine
Budapest University of Technology and Economics
Tags
Summary
Dieses Dokument behandelt die Pulvermetallurgie und den Werkstoff- und Energiebedarf bei der Werkstückherstellung. Es gibt eine breite Einführung in die verschiedenen Verfahren, Materialien, und Eigenschaften dieser Technik. Diese Methode des Herstellungsprozesses ist in den Bereichen der Metallverarbeitung und technischen Anwendung entscheidend.
Full Transcript
Pulvermetallurgie Werkstoff- und Energiebedarf der Werkstückherstellung Energiebedarf Rohstoffausnutzen Herstellungsmethode für 1 kg Produkt...
Pulvermetallurgie Werkstoff- und Energiebedarf der Werkstückherstellung Energiebedarf Rohstoffausnutzen Herstellungsmethode für 1 kg Produkt 90 Gießerei 0-38 95 Pulvermetallurgie 29 85 Kalt-, oder Halbwarmumformen 41 75-80 Gesenkschmieden 41-49 45-40 Spanende Bearbeitung 66-82 100% 0% 0 MJ 100 MJ Spanen ist wegen der benötigte Genauigkeit des Werkstückes nicht zu vermeiden. Die erhöhten technische Anforderungen benötigen immer präzisere Bearbeitung, die Nanotechnologie generell. Folie: 2 Pulvermetallurgie Bei der Pulvermetallurgie Techniken werden die Grundstoffe die Pulver mit/und Zusatzstoffe mit Pressen ins Form gebracht, dann wird mit Wärmebehandlung zwischen der Pulverteilchen Kohäsionsbindung hergestellt während die Kavitäten Zwischen der Teilchen kleiner werden *. Folie: 3 Pulvermetallurgie Während der Wärmebehandlung verringert sich das Volumen, deswegen nennt man dieses Vorgang auch als Schrumpfen. (Beim keramischen Werkstoffen wird es als Ausbrennen bezeichnet obwohl kein Ausbrennvorgang vor sich geht.) Von dieser Ausdruck der Technologie ist der Ausdruck Sintern verbreitet (Sinterbronze, Sinterlager usw.). Die Temperatur der Wärmebehandlung ist die Rekristallisationstemperatur (0,3-0,7 mal die Schmelztemperatur in ⁰K). Folie: 4 Pulvermetallurgie ist ein „genaues” Herstellungsprozess Pulvermetallurgie ist eine der am progressivsten entwickelnde moderne Massenherstellungs- Prozesse für Bearbeitung spezielle Werkstoffen (große Produktivität, gutes Materialausbeute, kleines Energiebedarf. Metalle, Keramiken und auch Verbundwerkstoffe können aufgearbeitet werden usw.) Typisches Near-Net–Shape/NNS Technologie. Fertig oder nahezu fertige Produktion (im allgemeinen ist zusätzlich nur Feinbearbeitung nötig) Folie: 5 Geschichte der Pulvermetallurgie 1. 3000 v.Chr. Wurde in Egypt für Werkzeugherstellung Eisenschwamm benutzt 1870 USA Patent für Schrumpfen für Gleitlagermaterialien 1900. Herstellung von porösen Metallfilter in der USA Herstellung von W-Faser aus der Mischung von W- Pulver und 3% Ni Gemisch unter der Schmelztemperatur von Ni 1920 massenhafte Verwendung selbstschmierende Gleitlager in der USA 1925 Verwendung von Hartmetallen in Deutschland als Werkzeugwerkstoff VIDIA (WC+Co) Folie: 6 Geschichte der Pulvermetallurgie 2. 1940 Ausarbeiten von Eisenpulvermetallurgie- technologien in Mittel-Europa 1970 warmes isostatisches Pressen, pulvermetallurgische Werkzeugstähle und Superlegierungen 1986 Pulverschmieden (Ford Kolbenstange) 1988 Anwendung der Spritzgießen in der Pulvermetallurgie. 1990 Anwendung der sogenannte „Nanotechnologie” ( Verwendung von Pulver mit 10-9 Korngröße), neue Möglichkeiten USA seit 1986, 500 Millionen PKV Kolbenstange (60%) Folie: 7 Eigenschaften der Pulvermetallurgie 1. Können außerordentliche Mikrostruktureigenschaften erreicht werden Kleines Materialverlust und Jeder Schritt der Herstellungsprozess ist automatisierbar Mit anderen Methoden nicht herstellbare Legierungen und Speudolegierungen sind machbar Für Herstellung und Verwendung hochreine Metalle auch geeignet Gute Genauigkeit (mit Kalibration IT 7 kann erreicht werden, in Pressrichtung ist die Genauigkeit kleiner) Folie: 8 Eigenschaften der Pulvermetallurgie 2. Besondere mit anderen herkömmlichen Methoden nicht machbare physikalische mechanische und andere Eigenschaften lassen sich einstellen (magnetische, Wärme, Korrosion usw.) Nach Anspruch lassen sich homogene oder inhomogene Materialien herzustellen Poröse Materialien für, Filter, selbstschmierende Gleitlager Gute Oberflächenqualität Beachtliche Spanungskosten können erspart werden Materialen mit höheren Schmelzpunkt zB.: W, Mo, Ta usw. Können aufgearbeitet werden. Folie: 9 Eigenschaften der Pulvermetallurgie 3. Man braucht das Material nicht wieder einzuschmelzen. Der Abfall kann meistens wieder gebraucht werden Durch Mischung der Elementare Pulver lassen sich von wenigen Pulver weite Legierungen hergestellt werden (meistens wird es nicht ausgenutzt, Legierungspulver werden verwendet) Produkte aus Hochleistungskeramiken lassen sich herstellen Herstellung von metallischen und keramischen Verbundwerkstoffen Möglichkeit der mechanische Legierung Folie: 10 Eigenschaften der Pulvermetallurgie 4. Nachteile Der relativ hohe Materialkosten und spezielle Großinvestitionskosten. Eine Richtung der Entwicklungen ist diese Kosten zu senken. Heutzutage ist es für Massenproduktionstechnologie, bei gemeinen Bauteilen wo der Sinken der Spanungskosten der Ziel ist. 50-100 tausend ist der kritische Stückzahl. Mit Ausnahme der speziellen Methoden (z.B. warmes isostatisches Pressen) Werkstücke mit kleinen oder mittelmäßigen Masse (20-500g) lassen sich herstellen Einige Pulver sind explosionsgefährlich und giftig Folie: 11 Einfluss der Herstellungsmethode auf die Ermüdungsgrenze Folie: 12 Pulvermetallurgische PKV Bestandteile Folie: 13 Pulvermetallurgie: Werkstücke Folie: 14 Pulvermetallurgie: Werkstücke Folie: 15 Pulvermetallurgie: Werkstücke Folie: 16 Pulvermetallurgie: Werkstücke Folie: 17 Pulvermetallurgie: Werkstücke Siliziumnitrid (SiN) Keramiken Folie: 18 Pulvermetallurgie: Werkstücke Aluminiumnitrid (AlN) Keramiken Folie: 19 Keramische Kugellager Werkstoffe: SiN, SiC, Al2O3, SiAlON Folie: 20 Pulvermetallurgie: Werkstücke Schneidwerkzeuge Folie: 21 Pulvermetallurgie: Werkstücke Superhartmetall-produkte Folie: 22 BME-EU Projekte AluSiForm FP5 Project High Efficiency Forming Technology of Light Weight MMC Components for Automotive and Household Applications 2001-2004 Consortium HUT (Fi), UMM (Pl), BUTE (Hu), IMR-SAS (Sk, Kassa), AMA (Nl, Holland), IMN (Pl, Krakkó), BERVA (Hu), FDB (F), GIAS-AIN(Sp, Pamplona), FISCARS (Fi) Folie: 23 Modellmotor Kolbenstange (BME ATT) Folie: 24 Hauptschritte der klassischen Pulvermetallurgie Pulverherstellung Vorbereitung der Pulver: Sortieren, Weichen, Vermischen, Zusatzmittel Einmischen Pressen der Pulvermischung, Verdichten Wärmebehandlung der gepressten Produktes: Schrumpfen (Sintern) (bei manchen Technologien werden die vorigen zwei Schritte nochmal wiederholt.) Zusätzliche Operationen (nachträglich): Kalibrieren, Prägen, Oberflächenbehandlungen, Wärmebehandlung, Eintränken, Korrosionsschutz usw. Folie: 25 Blockdiagramm der klassischen Pulvermetallurgie In Pulverform: Vermischung Einfüllung Pressen Ausstoßen Folie: 26 Grundmetalle Legierungselemente Zusatzmaterialien „lockeres” Volumen (2,6-3,1)x der Pulver Kalibration Abkühlung Schrumpfen Entfernung der Zusatzmaterialien Wärmebeh. Nachbeh. Folie: 26 Herstellung der Metallpulver 1. Mit mechanisches Zerkleinern: meist bei harten, spröden Materialien und Legierungen (Hammermühle, Kugelmühle, Rotationsmühle, Spanen usw.) Charakteristische Größe 20-400 μm, unregelmäßige Formen – gute Rohfestigkeit („Pulverteilchen klemmen sich ineinander”) Aluminiumpigmentherstellung. In Mikrometer Größenordnung mechanisches Legieren. Mit Sprühen vom flüssigen Metall : mit Gas-, Dampf-, Wasserstrahl, oder mit schnell drehende Scheibe usw. Charakteristische Größe 20-400 μm, regelmäßiges Form, glatte Oberfläche (nicht so gute Rohfestigkeit ) Schnellkristallisieren: Übersättigte Lösungen (Kolbenlegierung usw.), feine Kornstruktur. Folie: 27 Herstellung der Metallpulver 2. Chemisch: z.B. Aus Oxiden mit Reduktion, Charakteristische Gröβe 0,1-10 μm z.B. Aus Wolframoxid Metall Wolfram (mit Wasserstoff) oder WC mit Karbon reduziert Mit Elektrolyse (Kathodenmetall) Cu, Ag, Fe Andere Methoden: aus Dampf abscheiden, mit Plasma usw. Feines Pulver ist explosionsgefährlich!!!! (Al, Mehl, Zucker) große spezifische Oberfläche. Folie: 28 Pressen obere Umformstempel Füllschablone Werkzeug untere Umformstempel (Ausstoß) Kernstempel Einfüllen Pressen Auswerfen Folie: 29 Stauchung beim Pressen Folie: 30 Dichtheit der (rohe) Gepresste Teile 1. Folie: 31 Schrumpfen (Sintern) Ziel der Schrumpfen ist Diffusions- oder Adhesionsverbindung zwischen den Pulverteilchen herzustellen, während sich das Material rekristallisiert. Infolge wächst die Dichte, Festigkeit, Verlängerung. Die elektrische und magnetische Eigenschaften lassen ich einstellen, das Volumen der Körper wird kleiner. Die Abrundungsradien (lekerekítési sugár) der Mikrokavitäten wachsen. Die Kavitätsverminderung ist günstig aber daneben tritt der Kornvergröberung auch auf was nicht vorteilhaft ist, deswegen ist es kritisch die Temperatur und Schrumpfzeit zu synchronisieren. Mit Zusätze kann die Kornvergröberung verzögert eventuell verhindert werden. Folie: 32 Verlauf der Sinter- und Schrumpfprozess Folie: 33 Bindung durch Diffusion Gepresster Zustand Gesinterter Zustand Folie: 34 Kotinuierlich arbeitendes Ofen Folyamatos működésű zsugorító kemence Folie: 35 Kotinuierlich arbeitende Öfen Folie: 36 Zyklisch arbeitende Öfen Zylkisch Arbeitende Öfen: Glocke und Hebeltyp Vakuuomöfen Schrumpfen in Schutzatmosphäre (H. N, Ar, CO) Temperatur: 400-3200 oC Zeit: 15-90 Min. Folie: 37 Kosten Material 15-25 % Pressen 20-30 % Sintern 20-30% Zusatzoperationen 10-20% Werkzeugkosten 10-20% Kritische Stückzahl: ca. 10 000 St. Folie: 38 Zusätzliche Operationen Kalibrieren, Prägen (dombornyomás) Graten (sorjázás) Wärmebehandlung: Vergüten, Nitridieren, Einsatzhärten, Ausscheidungshärten usw. Tränken, Sättigen Oberflächenvorbereitung (Behandlung mit Dampf, Bemalen, galvanische Beschichtung usw. Folie: 39 Moderne pulvermetallurgische Verfahren Izostatisches Pressen (kalt/warm CIP/HIP) Spritzgießen (Metalle, Keramiken) Schrumpfen unter Druck Lasersintern Pulverschmieden (1,4x Zeitstandfestigkeit) Verwendung von rasch Kristallisierte Pulver Mechanisches Legieren Nanotechnoligien Folie: 40 CIP "wet bag" Von außen unter Druck gesetzt Direkt mit Kolben unter Druck gesetzt Folie: 41 CIP "dry bag" Ringsum und axial unter Druck Ringsum unter Druck gesetzt gesetzt Folie: 42 HIP Ringsum und axial unter Druck Ringsum unter Druck gesetzt gesetzt https://www.google.hu/imgres?imgurl=https%3A%2F%2Fwww.pickpm.com%2Fwp- content%2Fuploads%2F2016%2F08%2FHotIsostaticPressingProcess.jpg&imgrefurl=https%3A%2F%2Fwww.pickpm.com%2Fdesign-resource-center%2Fpowder-metallurgy-consolidation- processes%2F&docid=Uos9ph2jI8JQTM&tbnid=lh54cXHn6KR2LM%3A&vet=10ahUKEwiRj6Lg9PjdAhWoo4sKHQ8JAT8QMwg9KAUwBQ..i&w=271&h=245&bih=987&biw=2133&q=hip%20powder%2 0metallurgy&ved=0ahUKEwiRj6Lg9PjdAhWoo4sKHQ8JAT8QMwg9KAUwBQ&iact=mrc&uact=8#h=245&imgdii=U_wPxjlE6heOaM:&vet=10ahUKEwiRj6Lg9PjdAhWoo4sKHQ8JAT8QMwg9KAUwBQ..i Folie: 43 &w=271 Hartmetallherstellung (auch Keramiken) Folie: 44 Herstellung von keramischen Werkstücke Allgemeinen Pulvermetallurgisch (selten gegossen SiO2 -Gläser mit Zusatzmittel) Schlammgiessen Verfahren mit Giessschlamm Druckpressgiessen Spritzgiessen Zentrifugalgiessen Pulverpressen +Schrumpfen (Sintern-Ausbrennen) Folie: 45 Ausbrenn- (Sintertemperaturen) einige Keramiken Ziegel 700-900 oC Klinker Ziegel 1150-1250 oC Fliese, industrielles Bindematerial 900-1300 oC Porzellan >1300 oC WC-Co 1350-1450 oC AI2O3, Korund 1400-1900 oC Si3N4 1700-1850 oC Folie: 46 Pulvermetallurgie Technologien Pulvermetallurgie Technologien werden verwendet, wenn: spezielle Eigenschaften erwünscht sind die mit anderen Technologien nicht erreicht werden können (z.B: Porosität, Homogenität) Wenn wir Materialien mit hohen Schmelztemperatur verarbeiten möchten ohne zu Schmelzen, mit hohe Reinheit (W, Ta, Keramiken…) Wegen Wirtschaftlichkeitsgründen: kleine Energiebedarf, kleines Materialverlust NNS/NS Technologie (bei Bestandteilherstellung) (selbstverständlich nur wenn die Herstellungsbedingungen erfüllt sind) Folie: 47 Pulvermetallurgie Danke für die Aufmerksamkeit! Videos: 1, 2, 3, 4