Gießerei (Öntészet) PDF
Document Details
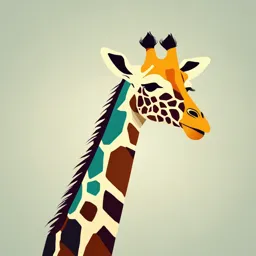
Uploaded by BountifulHeliotrope1090
Budapest University of Technology and Economics
Tags
Summary
This document provides information about casting processes. It discusses the basic principles of casting, different types of molds, and the materials used in the process. It also details the manufacturing process and related considerations regarding materials, costs, and energy requirements.
Full Transcript
Gießerei Grundprinzip der Gießerei Flüssiges Metall wird indem Guss entsprechende (negative) Form (Kavität) gegossen. Das Metall nimmt die Form der Form auf, nach Erstarren wird das Guss aus der Form entfernt. Es gibt einmal und mehrmals benutzbare Formen. MSZ EN 1707, prEN 12...
Gießerei Grundprinzip der Gießerei Flüssiges Metall wird indem Guss entsprechende (negative) Form (Kavität) gegossen. Das Metall nimmt die Form der Form auf, nach Erstarren wird das Guss aus der Form entfernt. Es gibt einmal und mehrmals benutzbare Formen. MSZ EN 1707, prEN 12258-1 Gießen: ist ein solches Vorgang, wobei geschmolzenes Metall in ein Form gegossen wird indem es erstarrt. Folie: 2 NNS/NS Technologien Die Entwicklung der Materiawissenschaft, Mess-, und Regelungstechnik, usw. Ermöglichte mit den früheren Vor-Herstellungsprozesse (plastische Umformung, Gießen, Pulvermetallurgie) fertige oder nahezu fertige Werkstücke herzustellen. (Near Net Shape/Net Shape) Es ist für Kosten-, Energie-, Arbeitsstunden-, und Werkstoffverminderung maßgebend. Folie: 3 Werkstoff- und Energiebedarf der Werkstückherstellung Energiebedarf Rohstoffausnutzen Herstellungsmethode für 1 kg Produkt 90 Gießen 0-38 95 Pulvermetallurgie 29 85 Kalt-, oder Halbwarmumformen 41 75-80 Gesenkschmieden 41-49 45-40 Spanende bearbeitung 66-82 100% 0% 0 MJ 100 MJ Spanen ist wegen der benötigte Genauigkeit des Werkstückes nicht zu vermeiden. Die erhöhten technische Anforderungen benötigen immer präzisere Bearbeitung, die Nanotechnologie generell. Folie: 4 Geschichte der Gießerei I.e. 3000-1500 Bronsallter (Zinnbronse) I.e. 224 Kolosse von Rhodos (32 m hoch, Bronse) 1252 Great Buddha Japan (120 t (9% Sn, 20% Pb)) 1400 (Ming) Great Bell (Khina, Beijing) 46 t, 120 dB-20 km) 1709 Gusseisen Brücke (USA Coalbrookdale) 1735 Glocke von Kreml (193 t) 1735 der Zars Kanone Gábor Áron, Ganz Ábrahám Folie: 5 Die Kolosse von Rhodos Folie: 6 Great BUDDHA 13,35 m hoch, 120 tonne (9% Sn, 20% Pb) Folie: 7 Folie: 8 Folie: 9 Gussstücke Folie: 10 Gussmaterialien Theoretisch sind alle Materialien gießbar Bedingungen der praktischen Gießbarkeit: niedrige Schmelzpunkt kleines Erstarrungstemperatur-Bereich Dünnflüssigkeit kleine Reaktionsfähigkeit mit der Formwand kleine Schrumpfung die eutektische Legierungen (und die reinen Metalle) sind gut gießbar Folie: 11 Sandformen Klassisches Werkstoff der Formen ist Sand mit Lehm gebunden – es ist die Roh Sandformen. Lehm hat tixotrope Eigenschaften, umhüllt die Sandteilchen und klebt sie zusammen. Die entstehende Gase, Dampfe zwischen der Sandkörner können entweichen (es wird auch mit Atmungsbohrungen unterstützt). Es werden geteilte und nicht geteilte Formen benutzt. Folie: 12 Sandformen Die Formkavität wird mittels einer Modell hergestellt. Die Modell kann verlorene (Wachs, Polimerschaum usw.), oder mehrmals gebrauchbar sein, was vor gießen zu entfernen ist. Die Modell ist die positive Kopie des Werkstückes, mit Toleranzen, Gießsrägheit, Kernzeichen eventuell mit Einflusssystem. Eindringen des flüssiges Metalls in die Hohlräume des Werkstückes wird mit Kernen verhindert. Flüssiges Metall wird durch das Einfluss-system in die Form gegossen. Folie: 13 Herstellung der Modell und Kern Werkstoff für Modell kann Holz, Metall oder Polimer sein. Möglichst leicht, leicht zu bearbeiten, verschleißfest und nicht flüssigkeitabsorbierend. Die Holzteile werden von Modell-Tischler hergestellt, und werden bemahlt. Die Kerne werden von besseren Materialien, von Sand und Bindemittel, größere Mechanische und thermische Belastung in Kernkasten (holz) hergestellt, oder können mit Spanen gemacht werden. Möglicherweise kann mit Metallnetz verstärkt werden. Allgemein ist der Modell und auch der Kern geteilt hergestellt (Teilungsebene). Folie: 14 Sandformen im Formkasten 1. Folie: 1515 Folie: Sandformen im Formkasten 2. Folie: 16 Einfluss-system Folie: 17 Guss mit Aufgüsse und Einfluss-system Folie: 18 Schritte der manuelles Sandformen I. Folie: 19 Schritte der manuelles Sandformen II. Folie: 20 Schritte der manuelles Sandformen IV. Folie: 21 Schritte der manuelles Sandformen V. Guss nach der Entfernung der Form (vor der Abschneiden der Speiser) Video Link: 1 2 Folie: 22 Schablonenformerei Folie: 23 Sandformen mit Bindematerialien Für größere, kompliziertere Formen getroknete Sandformen Pflanzenöle Wasserglas (+CO2) Kunstharz: auf Hitze härtend (HOT BOX) chemische Bindung (COLD BOX) Schalenformen Zementbindung Folie: 24 Genauere Gussherstelluns- verfahren Sandformen mit Kunstharzbindung: (Box-, und Schahlenformen) Präzisionsgießen (ausschmelzende Wachsmodell) Keramisches Formen Gravitazionskokillengießen Druckgießen: Niedrigdruck Warmkammer Hochdruck Warmkammer Hochdruck Kaltkammer Pressgießen (im Erstarrungstemperaturbereich, TIXO, usw.) Folie: 25 Verfahren mit Kunstharzbindung Zur Formsand wird za. 2% Kunstharz gemischt, Bindung wird mit Hitze oder mit chemische Beschläuniger erreicht. Beim automatisierten Verfahren ist sowohl die Sandmischung als auch die Bewegung der Formkasten automatisiert. Es sind drei verschiedene Kunstharze verbreitet: Furanharz, Fenolharz (cold box) und Karbamidharz (hot box). Folie: 26 Cold Box Kern Folie: 27 Genauigkeit der Cold Box Verfahren Folie: 28 Schalenformerei Formen mit kippbares Behälter Formen mit Konturplatte Kleine Aufmaß, Rippen, gute Größenreproduzierbarkeit, Gute Oberflächenqualität, hohes Genauigkeit Folie: 29 Maskenformerei Folie: 30 Modellausschmelzverfahren Folie: 31 Präzisionsgießen I. Folie: 32 Präzisionsgießen II. Video Links: 2 Folie: 33 Präzisionsgießen III. Die Vorteile der Präzisionsgießen gegenüber der Sandformverfahren sind: Beliebiges Gussform kann gegossen werden Ermöglicht dass Gießen von Metallen mit hohe Schmelztemperatur und schlechte Gießbarkeit (Präzisionsgießen mit Zentrifugalgießen) Güsse mit kleineren Toleranzen sind machbar Güsse mit besseren Oberflächenqualität sind machbar Nachteile der Präzisionsgießen: Nur für relativ kleine Gussmassen geeignet Relativ kostbare Methode, im vergleich mit der 100% Kosten der Rohsandformen kosten für Schalenformensind 250-300%, für Präzisionsgießen 700-1500%. Folie: 34 Anwendungsbereiche der Prezisionsgiessen Für kostbare Metalle (Gold, Silber, Platin, Wolfram, Chrom, Molybdän, Kobalt, Nickel und bei deren Legierungen) Für komplizierte Formen, genaue Güsse (Skulpturen Schmuck, Computer, feine Geräte…usw.) Für hochlegierte Werkstoffe (Hitze und korrosionsbeständige usw. Materialien z.B. Werkzeuge, Turbinenschaufel) Kann nur bei Mittel- und Großserienproduktion wirtschaftlich angewendet werden, wo die höhere Kosten der Gussherstellung mit der wenigere nachbearbeitungskosten kompensiert werden. Folie: 35 Kheramisches Formen (Shaw Verfahren) Folie: 36 Manuelle Gravitationskokille I. Folie: 37 Manuelle Gravitationskokille II. Folie: 38 Manuelle Gravitationskokille III. Folie: 39 Druckgießen (Niedrigdruck, Warmkammer) Folie: 40 Druckgießen (Hochdruck, Warmkammer) Folie: 41 Druckgießen (Hochdruck, Kaltkamer) Folie: 42 Zentrifugalgießen Video Links: 1, 2, 3 Folie: 43 Zentrifugalgießen Video Links: 1, 2, 3 Folie: 44 Maße Einfluss der Gießverfahren Masse (kg) Oberfläch- 0,01 0,1 1 10 100 1000 10000 Verfahren enq. Ra= rohes Sandformen -------------- ----------- ------ getroknetes Sandoberfläche ------------------ -------------------- 100 µm getroknetes Sandform ----------- ------- Chrommagnesit Mischung ----------- ----------- Samottmischung ----------- ----------- Wasserglas+CO2 Sandform ---------------- ------ 50-80 µm Kunststoffgebundenes Sandf. ----------- ----------- ----------- 15-25 µm (Cold-Box, Hot-Box Verf.) Schalenformen ----------- ----------- 15-25 µm Prezisionsgießen ----------- ----------------------- ------ < 10 µm keramisches Formen ------------------------ < 10 µm Kokillengießen (Al, Mg, Cu) Gravitationsießen --------- --------- --------- 10-50 µm Druckgießen --------- --------- --------- --------- 1,6-10 µm Folie: 45 Vergleich der Gießverfahren Kennwert/ Gravitations- Sandform~ Druck~ Zentrifugal~ Prezisions~ Gießverfahren kokillen~ Verwendbare alle Al-, Cu-, Zn- Legierungen alle Legierungen Wanddicke min. 3-6 1-3 1-2 10 0.8-1.5 (mm) Schale 2-4 Mechanische genügend gut sehr gut beste gut Eigenschaften Oberflächen- genügend gut sehr gut akzeptierbar sehr gut qualität Formgebungs- gut gut sehr gut schwach sehr gut freiheit Relative Kosten bei niedrigste hoch sehr hoch mittelmäßig hoch niedrige Stückzahl Relative Kosten bei mittelmäßig niedrig niedrigste hoch hoch großen Stückzahl Genauigkeit schlecht gut sehr gut genügend Sehr gut, 0.05 (d100 mm) 1 mm 0.2 mm 0.02-0.2 mm Flexibilität der beste schwach kleinste gut gut Veränderung Folie: 46 Gussplanung / Konstruktion Folie: 47 Toleranzen, Gießschiefigkeit Folie: 48 Schrumpfungen (Stahl mit 0,35% C Gehalt) Spezifische Volumenänderung (dm3/kg) Schrumpfung im 1725ºC 0,1475 flüssigen Zust.: 1,6% Schrumpfung beim 0,1425 Erstarrung: 3% Schrumpfung im 0,1375 festen Zust.:7,2 % 0,1325 0,1275 0 400 800 1200 1600 2000 Temperatur (ºC) Folie: 49 Schrumpfung verschidene Metallegierungen I. Metallgüte Schrumpfung (%) Stahl, unlegiert oder schwach leg. 2,0 Stahl, legiert, austenitisch 2,5…3,0 Gusseisen mit Lamellengraphit 1,0 Gusseisen mit Kugelgraphit in gegossenen Zustand 0,8…1,0 Gusseisen mit Kugelgraphit auf ferrit-perlitisch 0,3 wärmebehandelt Gusseisen mit Kugelgraphit auf ferritsch 0,0 wärmebehandelt Temperguss, weiß* 1,0…2,0 Temperguss, schwarz* 0,0…1,0 Temperguss, perlitisch* 0,5…1,5 * Werte sind als gesamtes Ergebnis der Schrumpfung beim Abkühlung und Zunahme beim Wärmebehandlung angegeben. Folie: 50 Schrumpfung verschidene Metallegierungen II. Metallgüte Schrumpfung (%) Zinnbronze (Cu+Sn) 1,5 Rotlegierungen (Cu+Sn+Pb+Zn) 1,5 Messing (Cu+Zn) 1,6…2,2 Aluminiumbronze (Cu+Al) 1,6…2,2 Bleibronze (Cu+Pb) 1,5 Cu 1,8 Al-Si Legierungen 1,0...1,2 Al-Mg Legierungen 1,0...1,5 Mg Legierungen 1,0...1,4 Folie: 51 Schrumpfung verschidene Metallegierungen III. Material Größe Schrumpfung (%) Grauguss kleine Gussstücke 0,8…1,2 mittlere Gussstücke 0,6…1,0 große Gussstücke 0,4…0,8 Stahl kleine Gussstücke 1,8…2,2 mittlere Gussstücke 1,6…2,0 große Gussstücke 1,4…1,8 Cu - Leg. kleine Gussstücke 1,4…1,6 mittlere Gussstücke 1,0…1,4 große Gussstücke 0,8…1,2 Al- und Mg- Leg. kleine Gussstücke 0,8…1,2 mittlere Gussstücke 0,5…1,0 große Gussstücke 0,3…0,8 Folie: 52 Folie: 53 Beispiele digitales Photoaparatgehäuse Folie: 54 Beispiele digitales Photoaparatgehäuse Anwender: Digital Still Camera Housing, Fujix DS-300 Fuji Film. Größe: (50mm) x (137mm) x (165mm) Gebräuchliche Dimensionen: (1 mm) Wanddicken Gewicht: nicht gegeben Legierung : AZ91D (Mg-Al-Zn) Massenprodukt: ja Thixo Anwender: MG Precision- Japan Oberflächenqualität : dekorativ/Schutz Folie: 55 Beispiele Digitalkamera Gehäuse Produkt Anwender: VL-PDI; Sharp Electronics Größe: 57mm x 145mm x 230mm Gebräuchliche Dimensionen: Wanddicken 0.8 - 1mm Gewicht : Gehäuse 650 g Legierung : AZ91D Massenprodukt : ja Thixo Anwender : Nifuko - Japan Oberflächenqualität: dekorativ/Schutz Folie: 56 Beispiele Notebook Gehäuse Ultra-thin, ultra-light, ultra-fast, ultra-cool. The Mitsubishi Pedion EM™ is the ultimate road machine for the ultimate executive. When you look at its sleek magnesium alloy case you know that this is a truly unique computer. Folie: 57 Beispiele Notebook Gehäuse Werkstückverwendung: Laptop/Notebook Bestandteile; Toshiba, Matsushita Electric, Mitsubishi Electric, Sharp, Panasonic Gateway und NEC. Größe: 18 mm min. Wanddicke x 330 mm x 254 mm Gebräuchliche Dimensionen: sehr dünne Wanddicken 0.70 mm Gewicht: nicht gegeben Legierung: AZ91D Massenprodukt: ja Thixo Anwender: Japanese Licensees Oberflächenqualität: dekorativ/Schutz Folie: 58 Sandformen 1: Füllung der Formkasten Folie: 59 Sandformen 2: Sand verdichten, schichtweise stampfen Folie: 60 Sandformen 3: Glättung der Sandoberflächen Folie: 61 Sandformen 4: Trennung der Formkastenteile Folie: 62 Sandformen 5: Reinigung der Formoberflächen, entfernung der Modell, Ausbau der Fließkanäle Folie: 63 Sandformen 6: Schmelzen, Temperatur-, und Zusammensetzungskontrolle Folie: 64 Sandformen 7: Scmelzenentnahme ins Pfanne Folie: 65 Sandformen 8: Giessen (Spiralprobe) Folie: 66 Gießerei Danke für die Aufmerksamkeit!