WSTP 212: Advance Machining 1 Learning Module PDF
Document Details
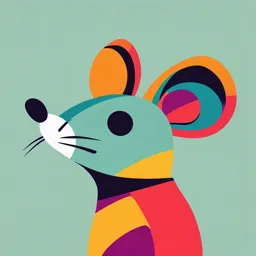
Uploaded by SuperbSuprematism
Technological University of the Philippines Visayas
2020
Engr. Aldrin S. Fernando, MT
Tags
Summary
This learning module covers WSTP 212: Advance Machining 1. It provides information on topics such as milling machines, tools, and techniques. Compiled in 2020 by Engr. Aldrin S. Fernando, MT.
Full Transcript
TECHNOLOGICAL UNIVERSITY OF THE PHILIPPINES VISAYAS Capt. Sabi St., City of Talisay, Negros Occidental College of Engineering Office of the Program Coordinator LEARNING MODULE WSTP 212: Advance Machining 1 DEP...
TECHNOLOGICAL UNIVERSITY OF THE PHILIPPINES VISAYAS Capt. Sabi St., City of Talisay, Negros Occidental College of Engineering Office of the Program Coordinator LEARNING MODULE WSTP 212: Advance Machining 1 DEPARTMENT: MECHANICAL ENGINEERING COMPILED BY: ENGR. ALDRIN S. FERNANDO, MT 2020 This module is a property of Technological University of the Philippines Visayas and intended for EDUCATIONAL PURPOSES ONLY and is NOT FOR SALE NOR FOR REPRODUCTION. VISION The Technological University of the Philippines shall be the premier state university with recognized excellence in engineering and technology at par with leading universities in the ASEAN region. MISSION The University shall provide higher and advanced vocational, technical, industrial, technological and professional education and training in industries and technology, and in practical arts leading to certificates, diplomas and degrees. It shall provide progressive leadership in applied research, developmental studies in technical, industrial, and technological fields and production using indigenous materials; effect technology transfer in the countryside; and assist in the development of small-and-medium scale industries in identified growth center. (Reference: P.D. No. 1518, Section 2) QUALITY POLICY The Technological University of the Philippines shall commit to provide quality higher and advanced technological education; conduct relevant research and extension projects; continually improve its value to customers through enhancement of personnel competence and effective quality management system compliant to statutory and regulatory requirements; and adhere to its core values. CORE VALUES T - Transparent and participatory governance U - Unity in the pursuit of TUP mission, goals, and objectives P - Professionalism in the discharge of quality service I - Integrity and commitment to maintain the good name of the University A - Accountability for individual and organizational quality performance N - Nationalism through tangible contribution to the rapid economic growth of the country S - Shared responsibility, hard work, and resourcefulness in compliance to the mandates of the university This module is a property of Technological University of the Philippines Visayas and intended for EDUCATIONAL PURPOSES ONLY and is NOT FOR SALE NOR FOR REPRODUCTION. TABLE OF CONTENTS Page Numbers TUP Vision, Mission, Quality Policy, and Core Values……………… 1 Table of Contents……………………………………………………..... 2 Course Description……………………………………………… 3 Couirse Outcomes……………………………………………... 3 General Guidelines/Class Rules………………………………… 4 Grading System………………………………………………… 4 Introduction to Milling (Activity No. 1) …………………….... 5 I. EXPECTED COMPETENCIES…………………… 5 II. THEORIES / PRINCIPLES………………………… 5 III. TOOLS, EQUIPMENT & MATERIALS…………… 11 IV. TASKS (STEPS) & KEY POINTS……………………. 12 V. TEST REVIEW EXERCISES…………………….…… 16 VI. PRODUCTIVITY TEST SHEET/RUBRICS………….. 17 Name of Activity (Activity No. 2) ………………………………… 18 I. EXPECTED COMPETENCIES………………………………… II. THEORIES / PRINCIPLES………………………………… III. TOOLS, EQUIPMENT & MATERIALS……………… IV. TASKS (STEPS) & KEY POINTS……………………. V. TEST REVIEW EXERCISES……………………. VI. PRODUCTIVITY TEST SHEET/RUBRICS……………… Name of Activity (Activity No. 3) ……………………………………………. I. EXPECTED COMPETENCIES………………………………… II. THEORIES / PRINCIPLES………………………………… III. TOOLS, EQUIPMENT & MATERIALS……………… IV. TASKS (STEPS) & KEY POINTS……………… V. TEST REVIEW EXERCISES……………… VI. PRODUCTIVITY TEST SHEET/RUBRICS……………… Name of Activity (Activity No. 4) ……………………………………………. I. EXPECTED COMPETENCIES………………………………… II. THEORIES / PRINCIPLES………………………………… III. TOOLS, EQUIPMENT & MATERIALS……………… IV. TASKS (STEPS) & KEY POINTS……………… V. TEST REVIEW EXERCISES……………… VI. PRODUCTIVITY TEST SHEET/RUBRICS……………… List of References……………………………………………… About the Author/s…………………………………………………………….. This module is a property of Technological University of the Philippines Visayas and intended for EDUCATIONAL PURPOSES ONLY and is NOT FOR SALE NOR FOR REPRODUCTION. COURSE DESCRIPTION This subject is the continuation of workshop subject WSTP 132 (Basic Machining). It deals with the actual manipulation of the basic machine tools used in the machine shop such as surface grinder, milling machine, and other conventional machines available in the shop. The utilization of such machine tools involves different machining operations with emphasis on the practices suitable for the kind of machine tool. COURSE OUTCOMES CO1 Operate with confidence any machine tools emphasizing machine shop safety. CO2 Identify the parts and control of any machine tools in the machine shop. CO3 Select proper tools and attachment for the set-ups and operations needed in machining operations. CO4 Produce a certain kind of work by machining on a machine tool with accuracy. CO5 Perform any kinds of machining works in the machine shop. This module is a property of Technological University of the Philippines Visayas and intended for EDUCATIONAL PURPOSES ONLY and is NOT FOR SALE NOR FOR REPRODUCTION. GENERAL GUIDELINES/CLASS RULES GRADING SYSTEM This module is a property of Technological University of the Philippines Visayas and intended for EDUCATIONAL PURPOSES ONLY and is NOT FOR SALE NOR FOR REPRODUCTION. Introduction to Milling (Activity No. 1) I. EXPECTED COMPETENCIES The student should be able to: 1. Know the different terminologies used in milling operation. 2. Differentiate different kinds of Milling Machine. 3. Enumerate the process involve in milling. 4. Familiarize with the different parts of a Milling Machine. II. THEORIES / PRINCIPLES History of Milling Machine and Milling Process A milling machine is a wheel-cutting machine, dating from the 1700s and used by clockmakers, were the precursors of industrial milling machines. Although it is unclear who invented the first actual milling machine–a device similar to the lathe that features a rotating cutting tool rather than a rotating work piece–evidence supports its existence by 1818 in the United States. Eli Whitney is most often mentioned as the first to design and construct a milling machine that was dependable and which served as a prototype for later, improved cutting machines. Whitney produced the machine, along with several others, with an eye toward originating mass production of gun parts. In 1798 he contracted with the federal government to produce a large order of muskets. All guns, at the time, were hand-crafted, and so gun parts were not interchangeable. Whitney remedied this with his construction of a semi-automated, machine tool factory. In 1867, American engineer Joseph R. Brown (1805-1870) introduced his universal milling machine at the Paris Exhibition. Brown’s machine arose following the testing in 1861 of one designed to solve the problem of producing spiral flutes for twist drills. This machine proved amazingly versatile, and led to Brown’s significant addition in 1864 of a formed cutter. Ever since, milling machines have vied with lathes as the most employed industrial machine tool. Their high adaptability is demonstrated by the numerous cutting jobs they perform, including flat surfaces, grooves, shoulders, inclined surfaces, slots, and dovetails. A turret milling machine is an example of a miller used in conjunction with a related machine tool, the drill. Another specialized miller is the hobbing machine, used to make gears. Perhaps the milling machine’s greatest distinction is that in 1954 it became the first machine tool to be controlled numerically, thereby representing one of the greatest industrial advances of the twentieth century. Process of Milling The time required to produce a given quantity of parts includes the initial setup time and the cycle time for each part. The setup time is composed of the time to setup the milling machine, plan the tool movements (whether performed manually or by machine), and install the fixture device into the milling machine. The cycle time can be divided into the following four times: This module is a property of Technological University of the Philippines Visayas and intended for EDUCATIONAL PURPOSES ONLY and is NOT FOR SALE NOR FOR REPRODUCTION. Load/Unload time - The time required to load the workpiece into the milling machine and secure it to the fixture, as well as the time to unload the finished part. Cut time - The time required for the cutter to make all the necessary cuts in the workpiece for each operation. The cut time for any given operation is calculated by dividing the total cut length for that operation by the feed rate, which is the speed of the cutter relative to the workpiece. Idle time - Also referred to as non-productive time, this is the time required for any tasks that occur during the process cycle that do not engage the workpiece and therefore remove material. Tool replacement time - The time required to replace a tool that has exceeded its lifetime and therefore become to worn to cut effectively. In determining the cycle time, the tool replacement time is adjusted for the production of a single part by multiplying by the frequency of a tool replacement, which is the cut time divided by the tool lifetime. Following the milling process cycle, there is no post processing that is required. However, secondary processes may be used to improve the surface finish of the part if it is required. The scrap material, in the form of small material chips cut from the workpiece, is propelled away from the workpiece by the motion of the cutter and the spraying of lubricant. Therefore, no process cycle step is required to remove the scrap material, which can be collected and discarded after the production. Cutting Parameters In milling, the speed and motion of the cutting tool is specified through several parameters. These parameters are selected for each operation based upon the workpiece material, tool material, tool size, and more. Cutting Feed - The distance that the cutting tool or workpiece advances during one revolution of the spindle and tool, measured in inches per revolution (IPR). For a multi-point tool, the cutting feed is also equal to the feed per tooth, measured in inches per tooth (IPT), multiplied by the number of teeth on the cutting tool. Cutting Speed - The speed of the workpiece surface relative to the edge of the cutting tool during a cut, measured in surface feet per minute (SFM). Spindle Speed - The rotational speed of the spindle and tool in revolutions per minute (RPM). The spindle speed is equal to the cutting speed divided by the circumference of the tool. Feed Rate - The speed of the cutting tool's movement relative to the workpiece as the tool makes a cut. The feed rate is measured in inches per minute (IPM) and is the product of the cutting feed (IPR) and the spindle speed (RPM). Axial Depth Of Cut - The depth of the tool along its axis in the workpiece as it makes a cut. A large axial depth of cut will require a low feed rate, or else it will result in a high load on the tool and reduce the tool life. Radial Depth Of Cut - The depth of the tool along its radius in the workpiece as it makes a cut. If the radial depth of cut is less than the tool radius, the tool is only partially engaged and is making a peripheral cut. If the radial depth of cut is equal to the tool diameter, the cutting tool is fully engaged and is making a slot cut. A large radial depth of cut will require a low feed rate, or else it will result in a high load on the tool and reduce the tool life. Operations This module is a property of Technological University of the Philippines Visayas and intended for EDUCATIONAL PURPOSES ONLY and is NOT FOR SALE NOR FOR REPRODUCTION. During the process cycle, a variety of operations may be performed to the workpiece to yield the desired part shape. The following operations are each defined by the type of cutter used and the path of that cutter to remove material from the workpiece. End milling - An end mill makes either peripheral or slot cuts, determined by the step-over distance, across the workpiece in order to machine a specified feature, such as a profile, slot, pocket, or even a complex surface contour. Chamfer Milling - A chamfer end mill makes a peripheral cut along an edge of the workpiece or a feature to create an angled surface, known as a chamfer Chamfer - 45° angle that can be machined on either the exterior or interior of a part— either straight or curved path Face Milling - A face mill machines a flat surface of the workpiece in order to provide a smooth finish. Drilling - A drill enters the workpiece axially and cuts a hole with a diameter equal to that of the tool. Boring - A boring tool enters the workpiece axially and cuts along an internal surface to form different features. Boring is commonly performed after drilling a hole in order to enlarge the diameter or obtain more precise dimensions. Counterboring - An counterbore tool enters the workpiece axially and enlarges the top portion of an existing hole to the diameter of the tool. Countersinking - A countersink tool enters the workpiece axially and enlarges the top portion of an existing hole to a cone-shaped opening. Common included angles for a countersink = 60°, 82°, 90°, 100°, 118°, & 120° Reaming - A reamer enters the workpiece axially and enlarges an existing hole to the diameter of the tool. Reaming removes a minimal amount of material and is often performed after drilling to obtain both a more accurate diameter and a smoother internal finish. Tapping - A tap enters the workpiece axially and cuts internal threads into an existing hole. The existing hole is typically drilled by the required tap drill size that will accommodate the desired tap. Threads may be cut to a specified depth inside the hole (bottom tap) or the complete depth of a through hole (through tap). Different Types of Milling Machine A. Column and Knee Type most used type of milling machine, where the table is mounted on the knee- casting which in turn is mounted on the vertical slides of the main column. 1. Hand Milling Machine - the simplest of all types of milling machine in which table feeding is controlled by hand. - The cutter is mounted on a horizontal arbour and is rotated by power. - small in size and suitable for light and simple milling operations. 2. Plain Milling Machine - much stronger than hand millers. - the table feeding is done either by hand or power - the plain milling machine having a horizontal spindle is also called as a horizontal spindle milling machine. Feed: Longitudinal – when the table is moved at right angles to the spindle. This module is a property of Technological University of the Philippines Visayas and intended for EDUCATIONAL PURPOSES ONLY and is NOT FOR SALE NOR FOR REPRODUCTION. Cross – when the table is moved parallel to the spindle. Vertical – when the table is adjusted in the vertical plane. 3. Universal Milling Machine - it can be adapted to a wide range of milling operations. - the table can be swiveled to any angle up to 45° on either side of the normal position. Helical milling operation can also be performed by having the table fed at an angle to the milling cutter. The capacity of this type of machine is increased by using special attachments such as: Dividing head or Rotary attachment index head Slotting Vertical milling attachment attachment This machine can produce spur, bevel, spiral, twist drill, reamer, milling cutter. All operations that are performed on a shaper can be done using a universal milling machine. 4. Ominversal Milling Machine - also has four movements of the universal milling machine - It can also be tilted in a vertical plane by providing a swivel arrangement at the knee. 5. Vertical Milling Machine - the position of the spindle is vertical or perpendicular to the table - adapted for machining grooves, slots, and flat surfaces - may be of the plain or universal type - spindle head is clamped to the vertical column which is swivelled at an angle B. Manufacturing or Fixed Bed Type Milling Machine these machines are large, heavy and rigid in construction differ from column and knee type milling machines by the construction of its table mounting table is mounted directly on the ways of a fixed bed classified as: This module is a property of Technological University of the Philippines Visayas and intended for EDUCATIONAL PURPOSES ONLY and is NOT FOR SALE NOR FOR REPRODUCTION. Simplex – single spindle head. Duplex – two spindle head. Triplex – three spindle head. C. Planer Type Milling Machine types of milling machine are also called as “Plano-Miller” a massive machine used for heavy-duty work having spindle heads adjustable in vertical and transverse direction relates a planer and like a planing machine has a cross rail capable of being raised or lowered carrying the cutters it has their heads, and the saddles, all supported by rigid uprights. D. Special Types of Milling Machine this machine has a spindle for rotating the cutter and provision for moving the tool or the work in different directions 1. Rotary Table Milling Machine - the table is circular in nature and rotates about a vertical axis. - cutters are set at different heights which results in one cutter roughing the workpiece and other one cutter finishing them 2. Drum Milling Machine - like a rotary table milling machine - its workpiece supporting table is called as “DRUM” and it rotates in the horizontal axis. 3. Planetary Milling Machine - workpiece is held stationary while the revolving cutter - the cutter moves in a travelling path to finish a cylindrical surface on the workpiece either internally or externally - adapted for milling internal and external threads 4. Pantograph Milling Machine - can duplicate a job by using a pantograph mechanism - allows the size of the workpiece reproduced to be smaller than, equal to or greater than the size of a template - also used for the different model for special purposes - Pantograph a mechanism that is generally constructed of four bars or links which are connected in the form of a parallelogram This module is a property of Technological University of the Philippines Visayas and intended for EDUCATIONAL PURPOSES ONLY and is NOT FOR SALE NOR FOR REPRODUCTION. 5. Profiling Milling Machine - duplicated the full size of the template attached to the machine - the spindle can be adjusted vertically and the cutter horizontally across the table 6. Tracer Controlled Milling Machine - reproduces irregular or complex shapes of dies - moulds by synchronized (matched) movements of the cutter and tracing elements - the movement of the stylus energized an oil relay system which in turn operates the main hydraulic system for the table MILLING MACHINE PARTS Arbor Support Spindle Table Cross Feed Hand Wheel Knee Figure 1 : Left Side view of a Gualdoni Milling Machine in ME Machine Shop This module is a property of Technological University of the Philippines Visayas and intended for EDUCATIONAL PURPOSES ONLY and is NOT FOR SALE NOR FOR REPRODUCTION. Figure 2: Front view of a Gualdoni Milling Machine in ME Machine Shop III. TOOLS, EQUIPMENT & MATERIALS……………………. 1. Tools 1.1.Set of Allen Wrench 2. Materials 2.1.Detailed drawing 3. Equipment 3.1.Milling Machine IMPORTANT 1. Keep machines and tools clean. 2. Always check machines and tools before and after using 3. Place tools in a safe place when not in use 4. Turn off machines after the operation is completed This module is a property of Technological University of the Philippines Visayas and intended for EDUCATIONAL PURPOSES ONLY and is NOT FOR SALE NOR FOR REPRODUCTION. IV. TASKS (STEPS) & KEY POINTS…………………….……. 1. Familiarization of the Milling Machine 1.1 Prepare tools, materials and equipment 1.1.1 Secure the detailed drawing from the INSTRUCTOR - Study it and note down specifications 1.1.2 Secure tools and materials from the tool keeper - Be sure to check them for damage before taking out for use. Replace damaged tools with good ones 1.1.3 Inspect the machine - Note down any irregularities of the machine and report to the instructor 1.2 Speed and Rotation Selection 1.2.1 Make sure that the power knob is in the 0 position in the panel board 1.2.2 Select the correct speed setting in the speed selector. 1.2.3 Turn the Power knob to the desired speed 1 for black rim and 2 for the red rim speed in the speed selector. Turn also the Power knob on the desired rotation. Clockwise or counter clockwise as indicated. Power Knob Figure 3 : Panel Board Figure 4: Speed Selector This module is a property of Technological University of the Philippines Visayas and intended for EDUCATIONAL PURPOSES ONLY and is NOT FOR SALE NOR FOR REPRODUCTION. 1.3 Table Traverse 1.3.1 Move the table forward or backward using Table Traverse hand wheel. Table Traverse Hand Wheel Figure 5. Table Traverse Hand Wheel 1.4 Cross Feed Traverse 1.4.1 Move the Cross Feed forward or backward using Cross Feed hand wheel. Cross Feed hand wheel Figure 6. Cross Feed Hand Wheel 1.5 Vertical Feed Traverse 1.5.1 Vertical Feed Traverse Hand Wheel controls the upward and downward motion. This module is a property of Technological University of the Philippines Visayas and intended for EDUCATIONAL PURPOSES ONLY and is NOT FOR SALE NOR FOR REPRODUCTION. Vertical Feed Traverse Hand Wheel Figure 7. Vertical Feed Traverse Hand Wheel 1.6 Automatic Traverse System 1.6.1 Automatic Traverse system is controlled using the switches shown in figure 8. Negative Displacement Switch Positive Displacement Switch Traverse Speed Selector Figure 8. Panel Board 1.6.2 Setting the Traverse Speed Selector will make the traverse slow or fast. 1.6.3 Engaging the automatic clutch for the table will make the table traverse as shown in Figure 9. Automatic Clutch Table Figure 9. Automatic Clutch Table This module is a property of Technological University of the Philippines Visayas and intended for EDUCATIONAL PURPOSES ONLY and is NOT FOR SALE NOR FOR REPRODUCTION. 1.6.4 Vertical and cross feeding will be using the same clutch as shown in figure 10. Engaging it up will make it automatically traverse vertically, while engaging it down will make it traverse in the direction of cross feed. Clutch for Vertical and Cross Feeding Figure 10. Clutch for Vertical and Cross Feeding This module is a property of Technological University of the Philippines Visayas and intended for EDUCATIONAL PURPOSES ONLY and is NOT FOR SALE NOR FOR REPRODUCTION. V. TEST REVIEW EXERCISES Select the best answer. Write the letter of the correct answer on the blank provided before each number. ________ 1. Makes a peripheral cut along an edge of the workpiece or a feature to create an angled surface a. End Milling b. Face Milling c. Chamfer Milling d. Up Milling _________ 2. Type of milling machine where the table is mounted directly on the ways of a fixed Bed a. Universal Milling b. Manufacturing Milling c. Knee and Column Milling d. Plain Milling _________ 3. The hand wheel that controls the up and down motion of the milling a. Table traverse hand wheel b. Cross feed hand wheel c. Vertical feed hand wheel d. Clutch _________ 4. Special Type of milling machine that allows the size of the workpiece reproduced to be smaller than, equal to or greater than the size of a template. a. Drum Milling b. Profiling Milling c. Pantograph Milling d. Planetary Milling _________ 5.The milling process of making a larger hole. a. Drilling b. Reaming c. Boring d. Countersinking e. This module is a property of Technological University of the Philippines Visayas and intended for EDUCATIONAL PURPOSES ONLY and is NOT FOR SALE NOR FOR REPRODUCTION. VI. PRODUCTIVITY TEST SHEET/RUBRICS……………………. SUBJECT MODULE ACTIVITY / PROJECT:INTRODUCTION ACTIVITY CODE: WSTP TITLE TO MILLING NO. 1 212 ADVANCE MACHINING 1 NAME OF STUDENT: DIRECTION: This form should afford the Instructor to rate the Productivity/Performance of the student/s for a given Employable Skill/Activity/Project. On the space provided for, write the points which likely coincide with your evaluation for each of the following factors: OUTSTANDING – (9-10); PLUS SATISFACTORY (7-8); SATISFACTORY (5-6); BELOW SATISFACTORY (3-4 / NEED TO REPEAT) SATISFACTORY TASK PERFORMANCE REQUIREMENT Provided with detailed drawing nos., complete tools and materials, the student should be able to: 1. Set up the Milling Machine with 1.1 Correct speed and direction of rotation 1.2 Manual control for traverse 1.3 Automatic control for traverse 2. Finished Set up exercises in approximately 5 min. FACTORS RATING A. ACCURACY/CRITICALITY (Exactness of Dimension/specification, High, Medium, Low Criticality) B. SPEED (50% over estimated time / 50% time save over estimated) C. METHOD (Economical; use of tools, materials, Safety and Hygiene, Initiative) FINAL GRADE REMARKS: ___________________________________________________________________________ ___________________________________________________________________________ Assessed by: ______________________________ Instructor This module is a property of Technological University of the Philippines Visayas and intended for EDUCATIONAL PURPOSES ONLY and is NOT FOR SALE NOR FOR REPRODUCTION. Milling Cutters and Attachments (Activity No. 2) I. EXPECTED COMPETENCIES The student should be able to: 1. Know the different Milling Cutters and its usage. 2. Know the different milling attachments and its applications. 3. Mount and set the different milling arbors. 4. Mount the milling cutters to the milling attachments. II. THEORIES / PRINCIPLES………………………………… I. Milling Cutters A. End Mill - a cutting tool used in industrial milling applications - can generally cut in all directions, though some cannot cut axially - Specified by its material, shape and number of flutes. Figure 11: End Mill B. Face Mill o A tool who cuts at the direction parallel to the rotation - Staggered Tooth Face Milling Cutter o also known as Chidori Tooth o it is staggered tooth for breaking & releasing chip more effectively to reduce the processing obstruction Figure 12: Staggered Tooth Face Milling Cutter This module is a property of Technological University of the Philippines Visayas and intended for EDUCATIONAL PURPOSES ONLY and is NOT FOR SALE NOR FOR REPRODUCTION. - Powerful Oblique Tooth Face Milling Cutter o it is oblique tooth for breaking & releasing chip more effectively to reduce the processing obstruction Figure 13: Powerful Oblique Tooth Face Milling Cutter - Right-Angle Indexable Face Milling Cutter o for milling L-shaped o insert is 90° vertically Figure 14 : Right-Angle Indexable Face Milling Cutter C. Gear Cutter - used to create a gear - the cutter number has to do with the pitch of the cut (1-7) - usually specified by diametral pitch or module Figure 15 : Modular Gear Cutter This module is a property of Technological University of the Philippines Visayas and intended for EDUCATIONAL PURPOSES ONLY and is NOT FOR SALE NOR FOR REPRODUCTION. D. Reamer - a type of rotary cutting tool used in metalworking o precision reamers are designed to enlarge the size of a previously formed hole by a small amount but with a high degree of accuracy to leave smooth sides o non-precision reamers which are used for more basic enlargement of holes or for removing burrs Figure 16: Reamers E. Fly Cutter - works well to take of material in one pass on a larger surface - can be hard on the machine when working with hard metals because of how far away the cutter is from the center of the tool Figure 17: Fly Cutters F. Bevel Cutter - make uniform bevel cuts in your stock Figure 18: Bevel Cutters This module is a property of Technological University of the Philippines Visayas and intended for EDUCATIONAL PURPOSES ONLY and is NOT FOR SALE NOR FOR REPRODUCTION. II. Attachments and Accessories for Milling Machine The various attachments are described below and also how they increase the versatility of the milling machine. 1. Horizontal Milling Attachment - Used usually in slotting and gear making. It employs a horizontal spindle motion. Figure 19: Horizontal Milling Attachment 2. Vertical Milling Attachment or Swivel Attachment - desirable on horizontal milling machines for substituting the horizontal spindle by a vertical spindle motion - the operation of milling horizontal surfaces and making grooves and slots Figure 20: Horizontal MillingAttachment 3. High-Speed Milling Attachment - the speed of the spindle can be increased three to four times so that the operation with small cutters could be carried out efficiently - mounted on the column with four bolts and can be swiveled also at any angle Figure 21: High-Speed Milling Attachment This module is a property of Technological University of the Philippines Visayas and intended for EDUCATIONAL PURPOSES ONLY and is NOT FOR SALE NOR FOR REPRODUCTION. 4. Slotting Attachment - square holes, slots and a variety of jobs is the use of this attachment - mounted on the column face and converts rotary motion into reciprocating motion - allows the machining of keyways, slots and certain grooves Figure 22: Slotting Attachment 5. Universal Dividing Head - also known as Index Head - very essential attachment that is used for cutting gear teeth, slots or grooves on the periphery of the work - with its help the job can be rotated by exact degrees and by various methods of indexing (direct, simple or compound), nearly any number of exact slots or teeth can be cut Figure 23: Universal Dividing Head 6. Circular Milling Attachment - a sort of rotary table provided with T-slots - its circumference is divided into degrees and may be hand-indexed for spacing or locating slots, grooves, or holes - for the purpose of milling a circular arc or groove on the job, an arrangement can be used to make it power-operated to provide continuous motion Figure 24: Circular Milling Attachment This module is a property of Technological University of the Philippines Visayas and intended for EDUCATIONAL PURPOSES ONLY and is NOT FOR SALE NOR FOR REPRODUCTION. 7. Rack Milling Attachment - used for milling straight or inclined racks or cross-slotted pieces of large lengths on horizontal or universal milling machine - consists of a milling unit, a fixture and a rack indexing unit - has a spindle having its horizontal axis at right angles to that of the machine Figure 25: Rack Milling 8. Vise - generally used as dead centre to support the job - a very essential attachment and is bolted to the top of the table - can be fastened to the table in any position by fastening the T-bolt on the ears at the end of the vise Figure 26: Milling Vise 9. Arbors - are used to hold milling cutter on milling machines - the cutter is driven through a key fitted on the arbor - one or more arbor supports may be provided to ensure added rigidity Figure 27: Horizontal Arbor Figure 28: Vertical Arbor 10. Hydraulic Clamping Vice - accurate, and easily adjustable vice - simple and rapid operation by hydraulic action This module is a property of Technological University of the Philippines Visayas and intended for EDUCATIONAL PURPOSES ONLY and is NOT FOR SALE NOR FOR REPRODUCTION. 11. Mechanically Operated High Pressure Clamping Vice - robust and strong design - head and clamping slide can be shifted and positioned on the lower slide section by means of adjustable pins 12. Helical Milling Device - this device combined with the vertical milling head and the spindle slide permits the manufacture of pieces with helical gashes (limited conical form) - consists of a universal indexing device which enables direct, indirect and differential indexing 13. Vertical Indexing - used for direct or indirect indexing and indexing by degrees on a scale - the work piece can be clamped between centers; three- jaw chucks, face plates or collets 14. Punch Milling Attachment - enables a considerably simpler, quicker and more accurate work like, manufacture of blanking punches, extended range of application with broaching device (keyways, conic milling device, etc.) 15. Adjustable Multi-Angle Milling Head - suitable for the accurate machining of internal angles and inner edges of work piece parts which are not easily accessible 16. Right-Angle Milling Head - can be swiveled through 360° inside its axial fitting housing according to the same graduated scale and shifted by 60 mm - specially suited for producing keyways, oil grooves and internal pockets 17. Universal Cross-Slide Milling Head - was developed as an auxiliary attachment for milling machines - the rotary motion is actuated either manually or mechanically by worm gear drives - the milling head can be fitted rapidly on the quill of the machine spindle by means of an adapter flange This module is a property of Technological University of the Philippines Visayas and intended for EDUCATIONAL PURPOSES ONLY and is NOT FOR SALE NOR FOR REPRODUCTION. III. TOOLS, EQUIPMENT & MATERIALS……………………. 1. Tools 1.1.Set of Allen Wrench 2. Materials 2.1.Detailed drawing 3. Equipment 3.1.Milling Machine IMPORTANT 1. Keep machines and tools clean. 2. Always check machines and tools before and after using 3. Place tools in a safe place when not in use 4. Turn off machines after the operation is completed IV. TASKS (STEPS) & KEY POINTS…………………….……. 1. Setting Up the Milling 1.1 Prepare tools, materials and equipment 1.1.1 Secure the detailed drawing from the INSTRUCTOR - Study it and note down specifications 1.1.2 Secure tools and materials from the tool keeper - Be sure to check them for damage before taking out for use. Replace damaged tools with good ones 1.1.3 Inspect the machine - Note down any irregularities of the machine and report to the instructor 1.2 Converting to horizontal milling 1.2.1 Unfasten the lock and push forward the attachment for horizontal milling as shown in figure 29. 1.2.2 Attach the horizontal arbour on the spindle and fasten it using the bolt provided at the back as shown in figure 30. This module is a property of Technological University of the Philippines Visayas and intended for EDUCATIONAL PURPOSES ONLY and is NOT FOR SALE NOR FOR REPRODUCTION. Lock Push Figure 29: Horizontal Milling Attachment Bolt to Attaching arbor to the Fasten spindle Figure 30: Attaching the Arbor to the Spindle 1.2.3 Attach the arbor support and fasten the lock to complete the set up as shown in figure 31. Slide the Fasten the Arbor Support lock Figure 31: Complete Set Up This module is a property of Technological University of the Philippines Visayas and intended for EDUCATIONAL PURPOSES ONLY and is NOT FOR SALE NOR FOR REPRODUCTION. 1.3 Converting to vertical and angle milling 1.3.1 Start by unfastening the locks and retracting the horizontal attachment as shown in figure 32. Retract Figure 32: Horizontal Attachment 1.3.2 Mount the vertical milling attachment to the spindle as shown in figure 33. Figure 33: Vertical Attachment and the Spindle 1.3.3 Attach threaded keys on the column ways to secure the vertical attachment. Refer to figure 34. Column Ways Threaded Keys Figure 34: Attaching Threaded Keys to Column This module is a property of Technological University of the Philippines Visayas and intended for EDUCATIONAL PURPOSES ONLY and is NOT FOR SALE NOR FOR REPRODUCTION. 1.3.4 Fasten the bolts to secure the attachment as shown in figure 35. Fasten the bolts Figure 35: Bolt to fasten in vertical attachment 1.3.5 Complete the set up by selecting the angle of swivel for angular cutting or no swivel for vertical milling. Secure the angle set by fastening the lock as shown in figure 36. Lock for Swivel Angular Scale Figure 36: Set up and lock for the angle of swivel 2. Setting up the Milling Cutters 2.1 Horizontal Milling Cutter 2.1.1.a For Fly Cutters, attach in to the slot on the milling arbour and fasten it by a bolt as shown in figure 37. Fly Cutter on its slot fastened by a bolt Figure 37: Fly Cutter in a Horizontal Attachment This module is a property of Technological University of the Philippines Visayas and intended for EDUCATIONAL PURPOSES ONLY and is NOT FOR SALE NOR FOR REPRODUCTION. 2.1.1.b For Gear or formed cutters, slide to the arbour in between ring fasteners and finally fastening it by a nut. Refer to figure 38. Ring Fastener Nut Cutter Figure 38: Formed Cutter on its Arbour 2.1.2 Use the arbour support to stabilize the arbour and to finish the set up as shown in figure 39. Lock Arbour Support Figure 39: Complete Set up for Horizontal Milling 2.2 Vertical Milling Cutter 2.2.1 Attach the arbour and fasten it using the bolt provided. See figure 40 This module is a property of Technological University of the Philippines Visayas and intended for EDUCATIONAL PURPOSES ONLY and is NOT FOR SALE NOR FOR REPRODUCTION. Bolt for Fastening Figure 40: Attaching the Arbour to the Spindle 2.2.2 Fasten the cutter to the arbour to complete the set up shown in figure 41. Cutter Holder Figure 41: Complete set Up for Vertical Milling This module is a property of Technological University of the Philippines Visayas and intended for EDUCATIONAL PURPOSES ONLY and is NOT FOR SALE NOR FOR REPRODUCTION. V. TEST/ REVIEW/ EXERCISES…………………….…….…….……. Select the best answer. Write the letter of the correct answer on the blank provided before each number. ________ 1. Also known as Chidori Tooth a. End Mill b. Bull Mill c. Gear Hobber d. Staggered Milling Cutter _________ 2. Very essential attachment that is used for cutting gear teeth, slots or grooves on the periphery of the work a. Circular Milling Attachment b. Slot Milling Attachment c. Indexing Head Attachment d. Plain Milling _________ 3. Generally used as dead centre to support the job a. Vise b. Cross feed hand wheel c. Vertical feed hand wheel d. Indexing Head _________ 4. Are used to hold milling cutter on milling machines a. Arbours b. Slots c. Cutter Holder d. Spindle _________ 5. Works well to take of material in one pass on a larger surface a. Gear Cutter b. Face Mill c. Fly Cutter d. End Mill This module is a property of Technological University of the Philippines Visayas and intended for EDUCATIONAL PURPOSES ONLY and is NOT FOR SALE NOR FOR REPRODUCTION. VI. PRODUCTIVITY TEST SHEET/RUBRICS……………………. SUBJECT MODULE ACTIVITY / PROJECT:MILLING CUTTER ACTIVITY CODE: WSTP TITLE AND ATTACHMENTS NO. 2 212 ADVANCE MACHINING 1 NAME OF STUDENT: DIRECTION: This form should afford the Instructor to rate the Productivity/Performance of the student/s for a given Employable Skill/Activity/Project. On the space provided for, write the points which likely coincide with your evaluation for each of the following factors: OUTSTANDING – (9-10); PLUS SATISFACTORY (7-8); SATISFACTORY (5-6); BELOW SATISFACTORY (3-4 / NEED TO REPEAT) SATISFACTORY TASK PERFORMANCE REQUIREMENT Provided with detailed drawing nos., complete tools and materials, the student should be able to: 1. Set up the Milling Machine with 1.1 Correct attachment 1.2 Correct Cutter 2. Finished Set up exercises in approximately 30 min. FACTORS RATING D. ACCURACY/CRITICALITY (Exactness of Dimension/specification, High, Medium, Low Criticality) E. SPEED (50% over estimated time / 50% time save over estimated) F. METHOD (Economical; use of tools, materials, Safety and Hygiene, Initiative) FINAL GRADE REMARKS: ___________________________________________________________________________ ___________________________________________________________________________ Assessed by: ______________________________ Instructor This module is a property of Technological University of the Philippines Visayas and intended for EDUCATIONAL PURPOSES ONLY and is NOT FOR SALE NOR FOR REPRODUCTION. MILLING MACHINE PROCESSES (Activity No.3)…………………………………. I. EXPECTED COMPETENCIES………………………………… The student should be able to: 1. Know the different cutting arrangement in milling. 2. Know the different set up in cutting. 3. Mount and set the work piece on the table. 4. Know the correct speed, direction and feeding using milling. II. THEORIES / PRINCIPLES………………………………… MILLING MACHINE PROCESSES 1. Up Milling - also known as conventional milling - the cutter rotates against direction of feed - chip width size is zero at initial cut and increase with feed - it is maximum at the end of feed - in this process, heat is diffuse to the work piece which causes the change in metal properties - tool wear is more because the tool runs against the feed - the cutting chips are carried upward by the tool - the cutting chips fall down in front of the cutting tool which again cut the chips cause less surface finish - due to upward force by tool, high strength zig and fixture required to hold the work piece - high quality cutting fluid is required because heat diffuse in the work piece - it required high cutting force compare to down milling 2. Down Milling - also known as climb milling - the cutter rotates with direction of feed - in this cutting process, chip size is maximum at start of cut and decrease with the feed - most of heat diffuse to the chip does not change the work piece properties - tool wear is less compare to the up milling, due to the cutter rotate with the feed - the chips are carried downward by the tool - the cutting chips fall down behind the tool, this gives better surface finish - downward force act on work piece normal jig and fixture required - heat does not diffuse in the work piece, so simple cutting fluid is required This module is a property of Technological University of the Philippines Visayas and intended for EDUCATIONAL PURPOSES ONLY and is NOT FOR SALE NOR FOR REPRODUCTION. Figure 42: Difference Between Up and Down Milling 3. Straddle Milling - two or more parallel vertical surfaces are machined at a single cut operation - accomplished by mounting two side milling cutters on the same arbor, set apart at an exact spacing - two sides of the workpiece are machined simultaneously and final width dimensions are exactly controlled - the workpiece is usually mounted between centers in the indexing fixture or mounted vertically in a swivel vise - the two side milling cutters are separated by spacers, washers, and shims so that the distance between the cutting teeth of each cutter is exactly equal to the width of the workpiece area required - when cutting a square by this method, two opposite sides of the square are cut, and then the spindle of the indexing fixture or the swivel vise is rotated 90°, and the other two sides of the workpiece are straddle milled Figure 43: Straddle Milling Set Up 4. Gang Milling - simultaneous machining of a number of flat horizontal and vertical surfaces of a workpiece by using a combination of more than two cutters mounted on a common arbor. This module is a property of Technological University of the Philippines Visayas and intended for EDUCATIONAL PURPOSES ONLY and is NOT FOR SALE NOR FOR REPRODUCTION. - may involve 2 or more milling operation used for mass production. - differs with straddle milling because it can cut surfaces other than that of parallel. Figure 44: Gang Milling Set U 5. Face Milling - the milling of surfaces that are perpendicular to the cutter axis - produces flat surfaces and machines work to the required length - the feed can be either horizontal or vertical - the teeth on the periphery of the cutter do practically all of the cutting - when the cutter is properly ground, the face teeth actually remove a small amount of stock which is left as a result of the springing of the workpiece or cutter, thereby producing a finer finish - the workpiece may be clamped to the table or angle plate or supported in a vise, fixture, or jig - Large surfaces are generally face milled on a vertical milling machine with the workpiece clamped directly to the milling machine table to simplify handling and clamping operations. 6. Peripheral milling - contrast to face milling - is a machining process in which the milling cutter is placed parallel to the workpiece. - the milling cutter is positioned so that the sides of the cutter grind away at the top of the workpiece. - more effective at removing large amount or bigger depth of cuts from workpieces because it uses the sides of the milling cutter rather than the tip. This module is a property of Technological University of the Philippines Visayas and intended for EDUCATIONAL PURPOSES ONLY and is NOT FOR SALE NOR FOR REPRODUCTION. Figure 45: (a)Peripheral Milling and (b) Face Milling 7. End Milling - fluted cutting edges are arranged on the circumference and end of a rotating shaft that is vertical to the workpiece. - the cutting teeth are found on the end of the cutter and the circumference of the cutter body. - similar to that of face milling but it is used for smaller diameter or a formed cut that depend on the shape of the end mill used. Figure 46: End Milling 8. Gear Milling - one of the different types of form milling process - is a multi point machining process in which individual tooth spacing are created by a rotating multi edge cutter having a cross-section similar to that of the generated teeth (involute) This module is a property of Technological University of the Philippines Visayas and intended for EDUCATIONAL PURPOSES ONLY and is NOT FOR SALE NOR FOR REPRODUCTION. - after cutting each space, the gear is returned to its original position, and the gear blank is indexed for the next cut Figure 47: Gear Milling Set Up III. TOOLS, EQUIPMENT & MATERIALS……………………. 1. Tools 1.1. Set of Allen Wrench 1.2. Adjustable Wrench 1.3. Combination Wrench #22 1.4. Combination Wrench #14 1.5. Colet 1.6. End Mill 1.7. Module 2 Cutter 4 involute cutter 2. Materials 2.1. Detailed drawing 2.2. 50 mm x 100mm round bar 3. Equipment 3.1.Milling Machine 3.2.Universal Dividing Head 3.3.Tailstock 3.4.Machine Vise IMPORTANT 1. Keep machines and tools clean. This module is a property of Technological University of the Philippines Visayas and intended for EDUCATIONAL PURPOSES ONLY and is NOT FOR SALE NOR FOR REPRODUCTION. 2. Always check machines and tools before and after using 3. Place tools in a safe place when not in use 4. Turn off machines after the operation is completed IV. TASKS (STEPS) & KEY POINTS…………………….……. 1. Setting Up for End Milling/Face Milling and Peripheral Milling 1.1 Prepare tools, materials and equipment 1.1.1 Secure the detailed drawing from the INSTRUCTOR - Study it and note down specifications 1.1.2 Secure tools and materials from the tool keeper - Be sure to check them for damage before taking out for use. Replace damaged tools with good ones 1.1.3 Inspect the machine - Note down any irregularities of the machine and report to the instructor 1.2 Set up for end or face milling process 1.2.1 Reorient the milling machine for vertical milling as shown in module 2 1.2.2 For End Milling and Face Milling operation set the angle to 0° as shown in figure 48. Figure 48. 0° angle set up This module is a property of Technological University of the Philippines Visayas and intended for EDUCATIONAL PURPOSES ONLY and is NOT FOR SALE NOR FOR REPRODUCTION. 1.2.3 Insert the End mill or a Face mill in the Colet and fasten it to the arbour as shown in module 2. 1.2.4 Fasten the workpiece to the milling table. Use a milling vise for clamping. Alternative clamps can also be use when a vise is not available. 1.2.5 With the correct speed and direction set, power up the machine and supply coolant to the workpiece using the switch shown in figure 49 and projecting the coolant nozzle to the tip of the cutter. Coolant Switch Figure 49. Coolant Switch 1.2.6 Start cutting the face of the workpiece to the specification given by the Instructor. 1.3 Setting for peripheral milling 1.3.1 Start by loosening the lock on the vertical milling attachment and tilting it to 90° as shown in the graduation. Refer to 1.2.2 for angle set up. 1.3.2 Insert the Peripheral mill in the Colet and fasten it to the arbour as shown in module 2. 1.3.3 Do steps 1.2.4 to 1.2.6 from face or end milling to perform the peripheral milling process. This module is a property of Technological University of the Philippines Visayas and intended for EDUCATIONAL PURPOSES ONLY and is NOT FOR SALE NOR FOR REPRODUCTION. 2. Setting Up for the Climb and Conventional Milling 2.1 Set up for Climb Milling Process 2.1.1 Start by converting the machine to horizontal milling operation. Refer to module 2 for the steps. 2.1.2 Insert the cutter to the arbour in the orientation shown in figure 50. Fasten it and support it as shown in module 2. Figure 50. Orientation for Climb 2.1.3 Set the correct speed and use the clockwise direction for climb milling. 2.1.4 Using the universal dividing head and tail stock clamp the workpiece as shown in figure 51. Figure 51: Workpiece held by Dividing Head and Tailstock This module is a property of Technological University of the Philippines Visayas and intended for EDUCATIONAL PURPOSES ONLY and is NOT FOR SALE NOR FOR REPRODUCTION. 2.1.5 Cut the workpiece as specified by the Instructor. 2.2 Set up for Conventional Milling process 2.2.1 With the same horizontal orientation of climb milling. Insert the cutter in the orientation shown in figure 52. Figure 52: Orientation for Conventional 2.2.2 Set the correct Speed and use the counter clockwise direction for conventional milling. 2.2.3 Repeat the steps 2.1.4 to 2.1.5 from climb milling to finish the set up. This module is a property of Technological University of the Philippines Visayas and intended for EDUCATIONAL PURPOSES ONLY and is NOT FOR SALE NOR FOR REPRODUCTION. V. TEST/ REVIEW/ EXERCISES…………………….…….…….……. 1. Differentiate up milling and down milling. _______________________________________________________________ _______________________________________________________________ _______________________________________________________________ _______________________________________________________________ _______________________________________________________________ _______________________________________________________________ __________________ 2. Differentiate straddle milling and gang milling. _______________________________________________________________ _______________________________________________________________ _______________________________________________________________ _______________________________________________________________ _______________________________________________________________ _______________________________________________________________ __________________ 3. Differentiate Face milling and Peripheral Milling. _______________________________________________________________ _______________________________________________________________ _______________________________________________________________ _______________________________________________________________ ____________ _______________________________________________________________ _______________________________________________________________ ______ This module is a property of Technological University of the Philippines Visayas and intended for EDUCATIONAL PURPOSES ONLY and is NOT FOR SALE NOR FOR REPRODUCTION. VI. PRODUCTIVITY TEST SHEET/RUBRICS……………………. SUBJECT MODULE ACTIVITY / PROJECT:MILLING ACTIVITY CODE: WSTP TITLE MACHINE PROCESSES NO. 3 212 ADVANCE MACHINING 1 NAME OF STUDENT: DIRECTION: This form should afford the Instructor to rate the Productivity/Performance of the student/s for a given Employable Skill/Activity/Project. On the space provided for, write the points which likely coincide with your evaluation for each of the following factors: OUTSTANDING – (9-10); PLUS SATISFACTORY (7-8); SATISFACTORY (5-6); BELOW SATISFACTORY (3-4 / NEED TO REPEAT) SATISFACTORY TASK PERFORMANCE REQUIREMENT Provided with detailed drawing nos., complete tools and materials, the student should be able to: 1. Set up the Milling Machine with 1.1 Correct Attachment 1.2 Correct Cutter Orientation 1.3 Correct Clamping 1.4 Appropriate Speed and Cutting Direction 2. Finished Set up exercises in approximately 30 min. FACTORS RATING G. ACCURACY/CRITICALITY (Exactness of Dimension/specification, High, Medium, Low Criticality) H. SPEED (50% over estimated time / 50% time save over estimated) I. METHOD (Economical; use of tools, materials, Safety and Hygiene, Initiative) FINAL GRADE REMARKS: ___________________________________________________________________________ Assessed by: ______________________________ Instructor This module is a property of Technological University of the Philippines Visayas and intended for EDUCATIONAL PURPOSES ONLY and is NOT FOR SALE NOR FOR REPRODUCTION. SLAB MILLING (Activity No. 4)…………………………………. I. EXPECTED COMPETENCIES………………………………… The student should be able to: 1. Set the cutting tool with respect to the workpiece 2. Manipulate and control the table, cross and vertical feed efficiently II. THEORIES / PRINCIPLES………………………………… SLAB MILLING Cutting of metal and forming it to its useful shape is performed in various ways. But to accurately and precisely cut the metal for a specific industrial use will be done using machine tools. Machinist should be able to learn these skills set in order for him to accurately and precisely cut a workpiece. 1. Workpiece Set Up Workpiece or work must be accurately and firmly place in the milling table. For this to happen work should be held and place using the following techniques. a. Using Spirit Level Using spirit level to ensure flatness of the work may come handy in setting up the workpiece. This is usually done in cutting not so dimension critical works. b. Using Dial Test Indicator Dial Test Indicator plays a vital factor for a successful machining process. To ensure the dimension of the flatness, straightness and correct position of the workpiece in the table dial test indicator plays the very important role in doing the work. Figure 53 shows example in doing that. Figure 53: Dial Test Indicator Used in Setting Up the Work This module is a property of Technological University of the Philippines Visayas and intended for EDUCATIONAL PURPOSES ONLY and is NOT FOR SALE NOR FOR REPRODUCTION. After the work is in place the machinist will fasten it to the table using available method. Using a jig or fixture will also be needed. 2. Cutting Tool Set Up In order to accurately cut the workpiece, a machinist must be able to identify and visualize first the cutting axis and must set the origin as the basis of the cut being made. Figure 54 shows the cutting axis represented by x as the table traverse, y as the cross feed and z as the vertical feed. The intersection of the 3 axis is the origin. Cutting tool Origin of workpiece Workpiece Figure 54: Axis and origin of the workpice To synchronize the origin of the tool and the workpiece, the machinist should be able to locate the zero position for the 3 axis. The tool must be just in touch with the workpiece or its surface must be tangent to the axis being set. There are several ways of doing it. Machinist may use the following methods: a. Cutter and paper or feeler or gage block technique The idea is to approach the part with the endmill and use a spacer of some kind so the endmill doesn’t actually contact the part. Common spacers include a piece of paper, a feeler gage, or a gage block. Except in the case of the paper, you will want the spindle to be stationary for this method. These methods are not so precise and the oldest method in setting up the tool. b. Edge Finder To use this method, put your part in the milling vise or fixture. You’re typically going to make the corner part zero. So, part zero sits in space rather than actually being on the part. This module is a property of Technological University of the Philippines Visayas and intended for EDUCATIONAL PURPOSES ONLY and is NOT FOR SALE NOR FOR REPRODUCTION. Edge Finders come in many varieties, but we’ll group them into mechanical and electrical categories. Electrical edge finders light up and/or beep when they come into contact with the workpiece. They rely on the workpiece to be electrically conductive so a circuit is closed when the edgefinder touches the workpiece. Here is a typical electrical edge finder. Figure 55: Electrical Edge Finder c. Dial Test Indicator Pre Setter Using these method the tool will be in contact with the pre setter attached on the workpiece, the dial test indicator will show the tolerance or the part zero being set. Figure 56: Dial Test Indicator Pre Setter With the methods presented, the outcome should be seen in the Figures 57, 58 and 59. It shows the synchronized the origin of x, y and z axis respectively. This module is a property of Technological University of the Philippines Visayas and intended for EDUCATIONAL PURPOSES ONLY and is NOT FOR SALE NOR FOR REPRODUCTION. Figure 57: Synchronized x axis Figure 58: Synchronized y axis Figure 59: Synchronize z axis III. TOOLS, EQUIPMENT & MATERIALS……………………. 1. Tools 1.1. Set of Allen Wrench 1.2. Adjustable Wrench 1.3. Combination Wrench #22 1.4. Combination Wrench #14 This module is a property of Technological University of the Philippines Visayas and intended for EDUCATIONAL PURPOSES ONLY and is NOT FOR SALE NOR FOR REPRODUCTION. 1.5. Colet 10 mm 1.6. End Mill 10 mm 1.7. Surface Gage 1.8. Vernier Caliper 1.9. Dial Test Indicator (DTI) 2. Materials 2.1. Detailed drawing 2.2. 40 mm x 40 mm x 100mm square bar 3. Equipment 3.1.Milling Machine 3.2.Machine Vise IMPORTANT 1. Keep machines and tools clean. 2. Always check machines and tools before and after using 3. Place tools in a safe place when not in use 4. Turn off machines after the operation is completed IV. TASKS (STEPS) & KEY POINTS…………………….……. 1. Slab Milling 1.1 Prepare tools, materials and equipment 1.1.1 Secure the detailed drawing from the INSTRUCTOR - Study it and note down specifications 1.1.2 Secure tools and materials from the tool keeper - Be sure to check them for damage before taking out for use. Replace damaged tools with good ones 1.1.3 Inspect the machine - Note down any irregularities of the machine and report to the instructor 1.2 Setting Up the Workpiece 1.2.1 Fasten the Square Bar in the Milling vise. - Lightly fasten the block to allow adjustments This module is a property of Technological University of the Philippines Visayas and intended for EDUCATIONAL PURPOSES ONLY and is NOT FOR SALE NOR FOR REPRODUCTION. 1.2.2 Attach the DTI to the spindle and move it to the workpiece. By means of the table traverse, cross feed and vertical feed handwheels, check for the flatness, straightness and position of the workpiece. - Gently tap the workpiece to adjust its position 1.2.3 Tightly fasten the workpiece to the vise and make sure that all fasteners are in place. 1.3 Setting Up the Cutting Tool 1.3.1 Attached the tool to the spindle using the method discussed in module 3. 1.3.2 Using cutter and feeler gage block technique synchronize the origin of the workpiece and the cutting tool. 1.3.3 After synchronization adjust the scale marks on each of the handwheel to zero as shown in figure 60. Figure 60: Adjustment of scale to zero 1.3.4 Finish the set up by checking all fastener and locks are in place. 1.4 Milling the Stock 1.4.1 With the given working drawing by the instructor, finish the given activity in 3 hours. This module is a property of Technological University of the Philippines Visayas and intended for EDUCATIONAL PURPOSES ONLY and is NOT FOR SALE NOR FOR REPRODUCTION. V. TEST/ REVIEW/ EXERCISES…………………….…….…….……. 1. Describe the 2 process involve in setting up the workpiece. _______________________________________________________________ _______________________________________________________________ _______________________________________________________________ _______________________________________________________________ _______________________________________________________________ _______________________________________________________________ _______________________________________________________________ _______________________________________________________________ _______________________________________________________________ ___________________________ 2. Differentiate the 3 process in setting up and synchronization of cutting tool to the workpiece _______________________________________________________________ _______________________________________________________________ _______________________________________________________________ _______________________________________________________________ _______________________________________________________________ _______________________________________________________________ _______________________________________________________________ _______________________________________________________________ _______________________________________________________________ _______________________________________________________________ _______________________________________________________________ _______________________________________________________________ _______________________________________________________________ _______________________________________________________________ _______________________________________________________________ _______________________________________________________________ _______________________________________________________________ _______________________________________________________________ ______________________________________________________ This module is a property of Technological University of the Philippines Visayas and intended for EDUCATIONAL PURPOSES ONLY and is NOT FOR SALE NOR FOR REPRODUCTION. VI. PRODUCTIVITY TEST SHEET/RUBRICS……………………. SUBJECT MODULE ACTIVITY / PROJECT:SLAB MILLING ACTIVITY CODE: WSTP TITLE NO. 4 212 ADVANCE MACHINING 1 NAME OF STUDENT: DIRECTION: This form should afford the Instructor to rate the Productivity/Performance of the student/s for a given Employable Skill/Activity/Project. On the space provided for, write the points which likely coincide with your evaluation for each of the following factors: OUTSTANDING – (9-10); PLUS SATISFACTORY (7-8); SATISFACTORY (5-6); BELOW SATISFACTORY (3-4 / NEED TO REPEAT) SATISFACTORY TASK PERFORMANCE REQUIREMENT Provided with detailed drawing nos., complete tools and materials, the student should be able to: 1. Set up the Work and the Cutting Tool 1.1 Correct Position of Origin 1.2 Synchronized work and cutting tool 1.3 Correct Clamping 1.4 Appropriate Speed and Cutting Direction 2. Finished the exercises in approximately 3.5 Hours. FACTORS RATING J. ACCURACY/CRITICALITY (Exactness of Dimension/specification, High, Medium, Low Criticality) K. SPEED (50% over estimated time / 50% time save over estimated) L. METHOD (Economical; use of tools, materials, Safety and Hygiene, Initiative) FINAL GRADE REMARKS: ___________________________________________________________________________ Assessed by: ______________________________ Instructo This module is a property of Technological University of the Philippines Visayas and intended for EDUCATIONAL PURPOSES ONLY and is NOT FOR SALE NOR FOR REPRODUCTION. LIST OF REFERENCES https://www.slideshare.net/sureshbabuem/machine-shop-notespdf http://uhv.cheme.cmu.edu/procedures/machining/ch1.pdf Machine Shop Practice, Vol. 1 by Karl Moltrecht, 1971 Machine Shop Operations and Setups by Orville D. Lascoe, 4th edition (June 1, 1973) This module is a property of Technological University of the Philippines Visayas and intended for EDUCATIONAL PURPOSES ONLY and is NOT FOR SALE NOR FOR REPRODUCTION. ABOUT THE AUTHOR/S Aldrin Sapanza Fernando is a licensed Mechanical Engineer and a graduate of Masters of Technology. A faculty of Mechanical Engineering Department of Technological University of the Philippines Visayas handling subjects including Workshop Theory and Practice for almost 9 years. He was trained in Department of Science and Technology – Metals Industry Research and Development Center (DOST- MIRDC) in Die and Mold Design and Fabrication. Currently he is the Machine Shop In Charge of the Mechanical Engineering Department of Technological University of the Philippines Visayas. This module is a property of Technological University of the Philippines Visayas and intended for EDUCATIONAL PURPOSES ONLY and is NOT FOR SALE NOR FOR REPRODUCTION. 0 This module is a property of Technological University of the Philippines Visayas and intended for EDUCATIONAL PURPOSES ONLY and is NOT FOR SALE NOR FOR REPRODUCTION.