W13 U8 JO BBA S6 Operations Management PDF
Document Details
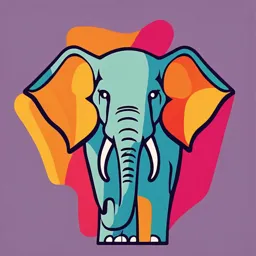
Uploaded by FeistyDallas6021
JGI
Tags
Related
- Unit 9 Operations Management BBA PDF
- Operations Management: Competitiveness, Strategy, and Productivity PDF
- Operations Management Final Exam Review PDF
- Location, Facilities, and Capacity Planning, Layout Strategy (PDF)
- Facility Location Decision PDF
- Operations Management: Chapter 8 Location Strategy PDF
Summary
This document is a study material for students of business administration covering operations management. It provides details on location and layout strategies and the importance of location decisions for businesses.
Full Transcript
Operations Management Unit – 08 Location and Layout Strategies Semester-06 Bachelors of Business Administration Operations Management...
Operations Management Unit – 08 Location and Layout Strategies Semester-06 Bachelors of Business Administration Operations Management JGI x UNIT Location and Layout Strategies Names of Sub-Unit Strategic Importance of Location Decisions, Factors Affecting Location Decision, Location Strategy in the Services Industry, Importance of Layout Decisions, Types of Layout, Warehouse Layouts, Storage Layouts. Overview This unit explores the strategic significance of location decisions in business, examining the factors influencing these decisions and their implementation, particularly in the services industry. It also delves into the importance of layout decisions, including various types of layouts such as warehouse and storage layouts. Learning Objectives Understand the strategic importance of location decisions and their impact on business operations. Identify the key factors influencing location decisions and how they differ across industries. Analyze location strategies specific to the services industry and their role in enhancing competitiveness. Evaluate the importance of layout decisions in optimizing efficiency, safety, and customer experience within facilities. 2 UNIT 08: Location and Layout Strategies Learning Outcomes Upon completing this course, participants will Ability to assess the economic, competitive, and regulatory factors influencing location decisions. Proficiency in developing location strategies tailored to the needs of service-based businesses. Competence in selecting and implementing appropriate layout decisions to enhance operational effectiveness. Skills in analyzing and optimizing warehouse and storage layouts to maximize space utilization and streamline operations. Pre-Unit Preparatory Material Article: "Strategic Location Decisions: A Comprehensive Guide" - Available on Harvard Business Review website. Book Chapter: "Operations Management in the Services Industry" from "Service Operations Management" by Robert Johnston and Graham Clark. Table of topics 8.1 Strategic Importance of Location Decisions 8.2 Factors Affecting Location Decision 8.3 Location Strategy in the Services Industry 8.4 Importance of Layout Decisions 8.5 Types of Layout 8.6 Warehouse Layouts 8.7 Storage Layouts 8.8 Conclusion 3 Operations Management JGI 8.1 Strategic Importance of Location Decisions Strategic location decisions play a critical role in the success of businesses across various industries. Each factor you mentioned - economic, competitive, legal/regulatory, and operational - contributes to shaping the optimal location for a business. Let's delve deeper into each: Economic Factors: Cost Considerations: Businesses need to analyze factors such as real estate prices, labor costs, utilities, and taxes. Lowering costs can significantly improve profitability. Market Access: Proximity to customers, suppliers, and distribution channels can reduce transportation costs and enhance responsiveness to market demands. Labor Availability: Access to skilled labor pools or specific expertise required for operations is crucial for businesses to operate efficiently and competitively. Competitive Factors: Proximity to Competitors: Being close to competitors can provide insights into industry trends, facilitate collaboration, or prompt differentiation strategies. Market Positioning: Location can influence how a business is perceived by consumers and stakeholders. For instance, being in an upscale neighborhood may enhance a luxury brand's image. Legal and Regulatory Factors: Zoning Laws: Compliance with local zoning regulations ensures that the business operations align with the intended land use, avoiding potential legal issues. Tax Incentives: Governments often provide tax incentives or subsidies to attract businesses, influencing location decisions. Environmental Regulations: Businesses need to consider environmental laws to mitigate risks and ensure sustainable operations. Operational Factors: Transportation Infrastructure: Access to highways, ports, airports, and railroads affects the efficiency of transporting goods and materials. Logistics Efficiency: Proximity to major transportation hubs or suppliers can streamline logistics operations and reduce lead times. 4 UNIT 08: Location and Layout Strategies Supply Chain Resilience: Location decisions should account for risks such as natural disasters, political instability, or disruptions in the supply chain. Businesses must carefully weigh these factors to select the most advantageous location that aligns with their strategic objectives and operational requirements. Additionally, the dynamic nature of markets and regulations necessitates periodic reassessment of location decisions to maintain competitiveness and adapt to changing circumstances. 8.2 Factors Affecting Location Decision location decisions are influenced by a variety of factors, and the ones you've listed cover key aspects that businesses need to consider: Market Factors: Customer Demographics: Understanding the demographic profile of potential customers helps in targeting the right market segments. Demand Patterns: Analyzing demand trends and fluctuations allows businesses to align production and distribution strategies accordingly. Market Trends: Staying abreast of market trends, such as changes in consumer preferences or emerging technologies, enables businesses to adapt and innovate. Infrastructure Factors: Access to Utilities: Reliable access to utilities such as electricity, water, and gas is essential for uninterrupted operations. Transportation Networks: Efficient transportation systems, including roads, railways, ports, and airports, facilitate the movement of goods and services. Communication Services: Access to reliable internet connectivity and telecommunications infrastructure supports business operations and connectivity with customers and suppliers. Labor Factors: Availability: Assessing the availability of a skilled workforce in different locations ensures that businesses can meet their staffing needs. Skills: Evaluating the skill level and expertise of the labor pool helps match workforce capabilities with job requirements. Wage Rates: Labor costs vary across regions, and analyzing wage rates enables businesses to optimize labor expenses while maintaining quality. Political Factors: 5 Operations Management JGI Stability: Political stability in a region reduces the risk of disruptions to business operations due to civil unrest or political instability. Government Policies: Understanding government regulations, taxation policies, and incentives can impact the overall business environment and profitability. Geopolitical Risks: Considering geopolitical factors such as trade tensions, sanctions, or regional conflicts helps businesses anticipate potential risks and uncertainties. By considering these factors comprehensively, businesses can make informed decisions regarding the location of their operations, whether for setting up new facilities, expanding existing ones, or entering new markets. Conducting thorough analyses and periodically reassessing these factors can help businesses adapt to changing market dynamics and maintain competitiveness. 8.3 Location Strategy in the Services Industry In the services industry, where the delivery of intangible services is paramount, location strategy plays a crucial role in meeting customer needs, enhancing competitiveness, and managing costs. Here's how these factors influence location decisions in the services sector: Customer Convenience: Proximity to Target Markets: Service providers often choose locations that are close to their target customer base to minimize travel time and enhance accessibility. Ease of Access: Selecting locations with convenient access, such as proximity to major transportation hubs or high-traffic areas, makes it easier for customers to reach the service provider. Service Accessibility: Reachability: Ensuring that locations are easily reachable by various modes of transportation, including public transit, cars, or walking, is essential for attracting and retaining customers. Convenience for Service Delivery: Service providers need to consider how easily their staff can access the location to deliver services efficiently. Competitive Positioning: 6 UNIT 08: Location and Layout Strategies Brand Visibility: Choosing locations in high-visibility areas or alongside complementary businesses can enhance brand exposure and attract potential customers. Competitive Advantage: Selecting locations that offer unique advantages, such as proximity to industry clusters or specialized markets, can differentiate the service provider from competitors. Cost Considerations: Rental or Lease Expenses: Balancing the cost of renting or leasing a location with the revenue potential and cost efficiencies is crucial for maintaining profitability. Cost Efficiency: Assessing factors such as overhead costs, utility expenses, and labor costs associated with operating in a particular location helps optimize cost-effectiveness. Additionally, service providers in the industry should consider factors such as zoning regulations, parking availability, and the local business environment when making location decisions. Moreover, the flexibility to adapt to changing customer preferences and market dynamics is essential for long-term success in the services sector. By carefully evaluating these factors, service providers can develop a robust location strategy that aligns with their business objectives and enhances customer satisfaction. 8.4 Importance of Layout Decisions Layout decisions are critical in shaping the efficiency, safety, flexibility, and overall customer experience within a facility. Let's explore the importance of each aspect: Efficiency: Workflow Optimization: A well-designed layout streamlines the flow of materials, information, and personnel, reducing bottlenecks and improving productivity. Minimized Material Handling: By strategically placing workstations and storage areas, unnecessary material movements are minimized, saving time and reducing the risk of errors or damage. Reduced Production Lead Times: An efficient layout shortens production cycles by minimizing delays and idle time, allowing for faster delivery of products or services to customers. 7 Operations Management JGI Safety: Employee Safety: Layout decisions influence the ergonomic design of workstations, aisle widths, and equipment placement, reducing the risk of injuries and improving employee well-being. Hazard Mitigation: Proper layout planning considers potential hazards such as sharp edges, heavy machinery, or chemical exposure, implementing safety measures to mitigate risks and ensure compliance with regulations. Flexibility: Adaptability to Change: Flexible layouts can easily accommodate changes in production processes, technology upgrades, or shifts in product demand without significant disruptions or costly redesigns. Scalability: Layout decisions that allow for modular expansions or reconfigurations enable businesses to scale operations efficiently in response to growth or changing market conditions. Customer Experience: Improved Flow: An intuitive layout enhances customer flow within retail spaces or service facilities, making it easy for customers to navigate and find what they need. Accessibility: Layout decisions should consider the needs of customers with disabilities, ensuring that facilities are accessible and inclusive. Enhanced Satisfaction: A well-designed layout contributes to a positive overall customer experience by reducing wait times, improving service efficiency, and creating a welcoming atmosphere. layout decisions impact various aspects of operations, from internal processes and employee well-being to customer satisfaction and competitive advantage. By prioritizing efficiency, safety, flexibility, and customer experience in layout planning, businesses can optimize their operations and position themselves for long-term success in a dynamic marketplace. 8.5 Types of Layout four common types of layouts found in manufacturing and service environments. Let's briefly explore each one: Process Layout: 8 UNIT 08: Location and Layout Strategies In a process layout, equipment and workstations are arranged based on the sequence of production steps or processes required to manufacture various products or perform different tasks. This layout is suitable for job shops or facilities that produce a wide variety of products with different processing requirements. Each department or workstation specializes in performing specific tasks, and products move between them as they progress through the production process. Product Layout: A product layout, also known as a line layout, organizes equipment and workstations in a linear flow to produce a specific product or product family. This layout is commonly used in assembly lines, where each workstation is dedicated to performing a specific task or operation in the production process. Products move along the line sequentially, with each workstation adding value to the product until it is completed. Cellular Layout: In a cellular layout, machines and workstations are grouped into cells or modules, each dedicated to producing a particular product or product family. This layout promotes small-batch production and team-based work, allowing for greater flexibility and responsiveness to customer demands. Cross-functional teams often work within each cell, with members responsible for all aspects of production, from design and manufacturing to quality control and maintenance. Fixed-Position Layout: In a fixed-position layout, the product remains stationary while workers, equipment, and materials move around it during the production process. This layout is commonly used in projects such as construction, shipbuilding, and aircraft assembly, where the size or complexity of the product makes it impractical to move. Workers typically bring tools and materials to the product's location, where assembly or construction takes place. Each type of layout has its advantages and is suitable for different production environments and business requirements. By carefully selecting and implementing the appropriate layout, organizations can optimize their operations, improve efficiency, and meet customer needs effectively. 9 Operations Management JGI 8.6 Warehouse Layouts These are common warehouse layouts used to optimize space utilization, streamline operations, and improve efficiency: Block Stacking: In block stacking, goods are stacked directly on top of each other in blocks, without the use of pallets or shelving. This layout maximizes vertical space utilization, making it suitable for warehouses with high ceilings. It is often used for storing goods that can be stacked safely, such as boxed or palletized items, and where selective access to individual items is not a primary concern. Cross-Docking: Cross-docking involves the rapid transfer of goods from inbound to outbound trucks with minimal or no storage in between. Incoming goods are received at the warehouse and immediately sorted and loaded onto outbound trucks for distribution, reducing storage time and handling costs. This layout is commonly used in distribution centers or transportation hubs to expedite the flow of goods and meet tight delivery schedules. Narrow Aisle Layout: Narrow aisle layouts utilize narrow aisles and tall shelving to maximize storage capacity in warehouses with limited floor space. Forklifts or automated guided vehicles (AGVs) navigate through the narrow aisles to retrieve and store goods, allowing for efficient use of vertical space. This layout requires specialized equipment and is suitable for warehouses with high SKU (stock-keeping unit) variability and fast-moving inventory. Bulk Storage Layout: Bulk storage layouts involve storing large quantities of homogeneous products in bulk storage areas. Products are typically stored directly on the warehouse floor or on pallets in designated storage zones, allowing for efficient handling and retrieval. This layout is ideal for goods that do not require individual picking or sorting, such as raw materials, commodities, or items with long shelf lives. 10 UNIT 08: Location and Layout Strategies Each warehouse layout offers unique advantages and is chosen based on factors such as the nature of the goods being stored, space constraints, throughput requirements, and operational priorities. By selecting the most appropriate layout for their specific needs, organizations can optimize warehouse efficiency, reduce operating costs, and enhance overall supply chain performance. 8.7 Storage Layouts These are various storage layouts commonly used in warehouses to optimize space utilization, improve efficiency, and facilitate streamlined operations: Random Storage: In random storage, items are stored throughout the warehouse without following a specific order or pattern. This layout maximizes space utilization by filling available storage locations as efficiently as possible. It allows for easy access to items since there is no predefined location for each SKU, reducing travel time during picking. Zone Picking: Zone picking involves dividing the warehouse into distinct zones and assigning pickers to specific zones. Each picker is responsible for picking orders only from their assigned zone, which reduces travel time and increases picking efficiency. Zone picking is particularly useful in large warehouses with high SKU variability or when dealing with large volumes of orders. Mezzanine Storage: Mezzanine storage involves installing intermediate levels or platforms within the warehouse to increase storage capacity vertically. It allows warehouses to maximize storage space without expanding the footprint of the facility, making it ideal for facilities with limited floor space. Mezzanines can be used for various purposes, including additional storage, office space, or assembly areas. Automated Storage and Retrieval Systems (AS/RS): AS/RS systems utilize robotic technology to automate the storage, retrieval, and movement of goods within the warehouse. These systems typically consist of automated storage racks, conveyors, and robotic picking devices controlled by a central computer system. 11 Operations Management JGI AS/RS systems significantly improve efficiency, accuracy, and throughput by reducing reliance on manual labor and minimizing errors in picking and inventory management. Each storage layout offers unique advantages and is chosen based on factors such as inventory characteristics, order profiles, space constraints, and operational requirements. By selecting the most appropriate storage layout and leveraging technology where applicable, warehouses can optimize storage space utilization, enhance picking efficiency, and improve overall warehouse performance. 8.10 Conclusion: Strategic location decisions are crucial for businesses across industries, with factors like economic, competitive, and regulatory considerations shaping choices. In the services sector, customer convenience and competitive positioning are paramount. Layout decisions, including warehouse and storage layouts, impact efficiency, safety, and customer experience. Various types of layouts offer unique advantages, from maximizing space utilization to enhancing picking efficiency. By carefully considering these factors, businesses can optimize their operations and maintain a competitive edge in the market. 8.11 Glossary: Location Decisions: Strategic choices made by businesses regarding the optimal geographic placement of their operations or facilities. Economic Factors: Influential aspects such as cost considerations, market access, and labor availability that impact location decisions. Location Strategy: A plan devised by businesses to determine where to locate their services or operations to maximize competitive advantage. Layout Decisions: Strategic decisions concerning the arrangement of equipment, workspaces, and facilities to optimize efficiency and productivity. Process Layout: Arrangement of equipment and workstations based on the sequence of production steps. Product Layout: Organizing equipment and workstations in a linear flow to produce a specific product or product family. Cellular Layout: Grouping machines and workstations into cells to facilitate small-batch production and team-based work. 12 UNIT 08: Location and Layout Strategies Fixed-Position Layout: Keeping the product stationary while workers and equipment move around it during production. Random Storage: Storing items in no particular order to maximize space utilization and ease of access. Automated Storage and Retrieval Systems (AS/RS): Robotic systems used to automate the storage, retrieval, and movement of goods within a warehouse. Descriptive Questions: 1. How do economic factors influence location decisions for businesses in the services industry? 2. What role does customer convenience play in determining the strategic location of service-based businesses? 3. How do different types of layouts impact warehouse efficiency and operational effectiveness? 4. What are the key considerations when designing storage layouts in warehouses to optimize space utilization? 5. How can businesses balance cost considerations with the need for flexibility in their location and layout decisions? Post Unit Reading Material "The Importance of Location Strategy for Businesses" - www.businessnewsdaily.com "Optimizing Warehouse Layouts for Efficient Operations" - www.logisticsmgmt.com Topics for Discussion forum Best Practices in Location Strategy: Share insights and experiences on how businesses can effectively leverage location strategy to gain a competitive advantage. Innovations in Warehouse Layouts: Discuss emerging trends and technologies shaping warehouse layout design and optimization for improved efficiency and productivity. 13 Operations Management JGI 14