The Spindle Shaper PDF
Document Details
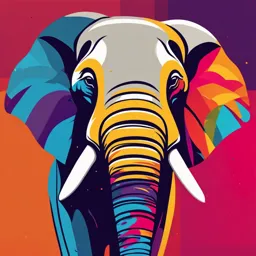
Uploaded by AttractiveJaguar
Tags
Summary
This document provides a comprehensive overview of spindle shapers and their applications. It details the various components, functions, and accessories, suitable for professionals working on engineering or manufacturing jobs.
Full Transcript
The Spindle Shaper Aka Shaper Main goal is to impart a shaped edge/face to stock o Mostly used for mouldings o Can be equipped with small saw blade o Very versatile machine Fixed profile cutter-heads o Carbide tipped o Were the standard for a long time o Moving away from this technology Insert tec...
The Spindle Shaper Aka Shaper Main goal is to impart a shaped edge/face to stock o Mostly used for mouldings o Can be equipped with small saw blade o Very versatile machine Fixed profile cutter-heads o Carbide tipped o Were the standard for a long time o Moving away from this technology Insert technology is becoming more popular/common One block with several profile options Basic Shaper o A motor and a spindle (some have interchangeable ones) for mounting cutterblocks Spindle will have a locking nut and various thickness’ of spacers Can be used to help adjust the height of the cutter o Enclosed base o Table top with table way and concentric rings around spindle Allows to vary the opening in the table around the cutter Opening should be as small as possible o Fence with guard Open where cutter head is o Must be variable speed Different diameter cutters require different speeds o Spring hold-downs for holding stock close to the cutter ctterblock Feather boards work too Helps with consistent cut Double spindle shapers increase production o Can even have 3 spindle shapers o Allow the running of multiple profiles Can have the same profile with one spindle climb cutting Helps deal with contrary grain Tilting arbor (spindle) shapers o 45° forward and 15° back o Allows you to alter the profiles of your cutters increasing versatility CNC shapers o Our Martin is one Has programmable settings for cutters Makes repeated set-ups easier and more accurate Standard rotation is counter clockwise, when looking down at the table o Feed stock from right to left Most machines will have a reverse function Feed from left to right OR can be used for climb-cutting when dealing with erratic grain (maple) o NEVER climb-cut without a power feeder Also a good idea to add a 2nd locking nut to the top of the spindle Power Feeder o Controls feed rate and applies pressure o 2 main types Rubber wheels that are spring loaded Track system, like a bulldozer o Good to have for production runs Prevents operator fatigue Gives a better result most times as the feed rate and pressure are constant o Can be used on other machines as well Table saw Jointer Bandsaw Router table o Must be very careful with short pieces o Running a ball bearing or rub collar is important What we did for the single door commode door panel o Using a sliding table/clamping jig will also help Don’t want the part to be sucked into the cutter Useful for cope and stick On the end grain of rails Freehand shaping o Remove fence assembly o Not well guarded Watch hand placement o Requires a start pin or steady pin Acts as a fulcrum against which your part can pivot Once part makes contact with the rub collar/ball bearing you can come off the pin Shaper fences are independent o Move separately forward and backwards o For full edge removal fences are out of alignment to prevent snipe Outfeed matches new profile edge o For partial edge removal fences are in line with one another o Most fences have sacrificial wood boards on them Slide side to side to close gap around cutter Depends on how much you what to remove you can create zero-clearance fence Breakthrough fence is the safest o Like a zero-clearance insert o Clamp a solid board across the opening o Move fence back into cutter – allow the cutter to cut through the board o Has the disadvantage of losing some of the profile of the cutter Cutters can be flipped o Must use reverse function and feed left to right Still feeding against to rotation Shaper Accessories Cutter blocks o More costly than the machine over time o Slot spindle (French Head) More of a scraping action Good for contrary woods o Square block (must be a power fed machine o Stair trencher (rebates and dados in stair stringers) o Circular block 2,3 or more HSS knives, depending on diameter Blanks can be custom ground Must be same profile on a block for balance Projection of knives does not affect the balance, just the cut o Solid profile cutter block – most common shapes Guards o Cage guard Also known as a hood guard Surrounds the cutter block with steel cage o Shaw guard Guides the part against the fence and holds down against table Less control when part exits Difficult to injure oneself as you can’t really get fingers in front of cutter o Tunnel guard Similar to Shaw guard No down force Hard to clear piece o Breakthrough fence Most often used with large diameter cutters Zero clearance opening Sacrificial fence o Auxiliary fences Purpose made fences o Ring fence Not so much a fence as a guide Versatile Great for curved work Replaces ball bearing, rub collar and lead-in Profile grinders o For custom shaped knives o Ensures same profile and projection Stacked cutter blocks o For complicated profiles with grooves, dadoes, etc. o Usually have insert knives Can lever-in, like a drop on o Must use a stop block