Saudi Arabia Railways Terminals, Mines and Ports Operations Handbook PDF 2024
Document Details
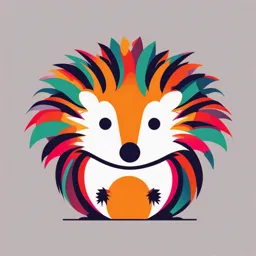
Uploaded by CureAllLlama3114
2024
Wael Al Shamrani
Tags
Summary
This document is a handbook for operations management at terminals, mines, and ports for Saudi Arabia Railways (SAR). It details freight operations, responsibilities, procedures, safety protocols, and communications for staff. The handbook is effective from February 12, 2024.
Full Transcript
Function: Freight Dept.: Operations Management Document Title: Terminals, Mines and Ports Operations Handbook...
Function: Freight Dept.: Operations Management Document Title: Terminals, Mines and Ports Operations Handbook Doc. No.: SAR-005-100-3-004 Rev. No.: 02 Effective Date: 12 February 2024 Saudi Arabia Railway P.O Box 64447, Riyadh 11536 [I] Internal Function: Freight Department: Operations Management Document Title: Terminals, Mines and Ports Operations Handbook Document Control Documentation type Confidentiality level Confidential ☐ Non-confidential ☒ Safety criticality Critical ☒ Non-critical ☐ Targeted end user usage Frequent ☒ Not frequent ☐ Update & archiving frequency Frequent ☐ Not frequent ☒ Document information Information Document Owner Freight Business Unit Director Document Language ☒English / ☐Arabic / ☐ Other Distribution list Name Dept. Wael Al Shamrani Freight Business Unit Document Approvals This Document has been approved electronically by SAR document management system. A screenshot for the document approval from SAR document management system can be share upon request. This document contains proprietary and confidential information. All information, data and materials submitted to the Recipient in electronic or written form shall be used solely for the purpose of which it was furnished dealings with the Saudi Arabia Railways (SAR). It’s the Recipient responsibility to inform its employees or agents who have access to its content of its confidential nature. Recipient's obligations with respect to the protection of Discloser's Proprietary Information shall be to use the same reasonable degree of care which Recipient uses to protect its own information of similar character. Upon discovery of any such inadvertent disclosure, Recipient shall endeavor to correct the effects thereof and to prevent any further inadvertent disclosure Saudi Arabia Railways (SAR) retains all title, ownership and intellectual property rights to the material and trademarks contained herein, including all supporting documentation, files, marketing material, and multimedia. BY ACCEPTANCE OF THIS DOCUMENT, THE RECIPIENT AGREES TO BE BOUND BY THE AFOREMENTIONED STATEMENT. All PRINTED COPIES OF THIS DOCUMENT ARE UNCONTROLLED [I] Internal Document No.: Rev. No.: Effective Date: Page 1 SAR-005-100-3-004 02 12 February 2024 Function: Freight Department: Operations Management Document Title: Terminals, Mines and Ports Operations Handbook CONTENTS 1 PURPOSE....................................................................................................................................................................... 4 2 OBJECTIVE..................................................................................................................................................................... 4 3 SCOPE............................................................................................................................................................................ 4 4 DEFINITIONS / ABBREVIATIONS................................................................................................................................. 5 4.1 Definitions................................................................................................................................................................ 5 4.2 Abbreviations........................................................................................................................................................... 5 5 RESPONSIBILITIES....................................................................................................................................................... 6 5.1 Freight Train Operations Senior Manager............................................................................................................... 6 5.2 Terminal and Yard Section Head............................................................................................................................. 6 5.3 Terminal Master....................................................................................................................................................... 6 5.4 Groundstaff.............................................................................................................................................................. 7 6 DOCUMENT DESCRIPTION.......................................................................................................................................... 8 GENERAL................................................................................................................................................................................ 8 6.1 Reporting for Duty.................................................................................................................................................... 8 6.2 Medical..................................................................................................................................................................... 8 6.3 Sunglasses............................................................................................................................................................... 8 6.4 Methods of Work and Wagon Briefs........................................................................................................................ 8 6.5 Personal Protective Equipment (PPE)..................................................................................................................... 9 6.6 Personal Equipment................................................................................................................................................. 9 6.7 Publications.............................................................................................................................................................. 9 6.8 Health and Safety.................................................................................................................................................. 10 6.9 Lifestyle and Professional Operations................................................................................................................... 11 COMMUNICATIONS............................................................................................................................................................. 12 6.10 General Principles.................................................................................................................................................. 12 6.11 Emergency Call...................................................................................................................................................... 12 6.12 Rail Dangerous Goods Emergency Call................................................................................................................ 12 6.13 Mobile Phones....................................................................................................................................................... 13 6.14 Correct use of Radios............................................................................................................................................ 13 6.15 Shunting Communications..................................................................................................................................... 13 6.16 Radio...................................................................................................................................................................... 13 6.17 Hand Signals.......................................................................................................................................................... 13 6.18 Telephone.............................................................................................................................................................. 13 6.19 Controlling Train Movement................................................................................................................................... 14 6.20 Stopping Trains...................................................................................................................................................... 14 6.21 Hand Signals.......................................................................................................................................................... 15 SHUNTING............................................................................................................................................................................ 16 6.22 Personal Safety...................................................................................................................................................... 16 6.23 Reducing Shunting Risk......................................................................................................................................... 17 6.24 Controlling Speed.................................................................................................................................................. 18 [I] Internal Document No.: Rev. No.: Effective Date: Page 2 SAR-005-100-3-004 02 12 February 2024 Function: Freight Department: Operations Management Document Title: Terminals, Mines and Ports Operations Handbook 6.25 Propelling Movements........................................................................................................................................... 18 6.26 Attaching or Detaching a Wagon/Locomotive........................................................................................................ 19 DANGEROUS GOODS......................................................................................................................................................... 20 6.27 Classification, Identification and Hazard................................................................................................................ 20 6.28 Action by Terminal Staff and Traincrew................................................................................................................. 22 6.29 Safety Distances.................................................................................................................................................... 22 6.30 PPE Requirements................................................................................................................................................ 23 6.31 First Aid Measures................................................................................................................................................. 23 6.32 Tank Wagon Inspection Checklist.......................................................................................................................... 23 ADDITIONAL OPERATIONAL PROCEDURES................................................................................................................... 24 6.33 Electronically Controlled Pneumatic (ECP) Brakes............................................................................................... 24 6.34 Fitting an End of Train (EOT) Device..................................................................................................................... 26 6.35 Operating a Wagon Handbrake............................................................................................................................. 27 6.36 Isolating Wagon Brakes......................................................................................................................................... 28 6.37 Point Clamps.......................................................................................................................................................... 28 6.38 Bearing Inspection................................................................................................................................................. 29 6.39 Pre-Departure Check............................................................................................................................................. 30 6.40 Roll-by Inspection................................................................................................................................................... 31 7 RECORDS..................................................................................................................................................................... 32 8 REFRENCES................................................................................................................................................................. 32 9 APPENDIX..................................................................................................................................................................... 32 10 DOCUMENT HISTORY................................................................................................................................................. 32 10.1 Appendix A- Local Operation of Switches............................................................................................................. 33 10.2 Appendix B- Pre-departure and Roll-by Checklist................................................................................................. 38 [I] Internal Document No.: Rev. No.: Effective Date: Page 3 SAR-005-100-3-004 02 12 February 2024 Function: Freight Department: Operations Management Document Title: Terminals, Mines and Ports Operations Handbook 1 PURPOSE The purpose of the Terminal, Mines, and Ports Operations Handbook is to serve as a comprehensive reference guide for SAR Operations staff engaged in various aspects of freight train operations, encompassing loading, unloading, shunting, marshalling, and train preparation. This handbook is designed to provide a detailed overview of the relevant processes and procedures associated with these operations, offering a valuable resource for staff members to ensure a standardized and efficient approach to their responsibilities within the terminal, mines, and ports environments. 2 OBJECTIVE The objective of the Terminal, Mines, and Ports Operations Handbook is to provide SAR Operations Staff with pertinent and comprehensive information essential for their roles in the loading, unloading, shunting, marshalling, and preparation of SAR Freight trains. This document aims to serve as a practical and accessible guide, equipping staff members with the necessary knowledge and procedures to facilitate safe, efficient, and standardized operations across terminal, mines, and ports environments within the SAR network. 3 SCOPE The scope of the Terminal, Mines, and Ports Operations Handbook encompasses all SAR Operations staff engaged in the loading, unloading, shunting, marshalling, and preparation of SAR freight trains. This handbook serves as a comprehensive resource to guide and inform staff members across various operational aspects within terminal, mines, and ports environments, ensuring a standardized and informed approach to their respective responsibilities. [I] Internal Document No.: Rev. No.: Effective Date: Page 4 SAR-005-100-3-004 02 12 February 2024 Function: Freight Department: Operations Management Document Title: Terminals, Mines and Ports Operations Handbook 4 DEFINITIONS / ABBREVIATIONS 4.1 Definitions Term Definition Locomotive (Loco) A self-propelled motive power unit. Local Traffic Control (LTC) Control facility for the operation of switches within a Terminal, Mine or Port. May be manned (mLTC) or unmanned (uLTC). Person In Charge (PIC) The person responsible for work activities and for determining a safe system of work. Propelling Movement The control of movement in the direction of travel - other than from the leading end. Rolling Stock Wheeled vehicles that run on railway lines, either a locomotive) or a wagon. Scotch (s) A wooded or metal device placed under the wheel to prevent wagon/loco movement. Shunting The movement and positioning of rolling stock within the yard as determined by operational or maintenance requirements. Switch Also referred to as ‘Points’ or ‘Turnouts’. Device used to allow a train or vehicle to cross from one track to another. Track The rails on which a train or vehicle move. Vehicle An item (or items) of Rolling Stock. 4.2 Abbreviations Abbreviation/ Short-Form Expanded / Full-Form DG Dangerous Goods EOT End-of-Train Device. ERTMS European Rail Traffic Management System. GSM-R Global System for Mobile Communication-Railway LFOP Local Field Operating Panel. Used for the local control of Switches and de- railers. MOW Method of Work. OCC Operations Control Centre. PDX Pre-Departure Examination. PPE Personal Protective Equipment. PTS Personal Track Safety RSM Rolling Stock Maintenance. SAR Saudi Railway Company [I] Internal Document No.: Rev. No.: Effective Date: Page 5 SAR-005-100-3-004 02 12 February 2024 Function: Freight Department: Operations Management Document Title: Terminals, Mines and Ports Operations Handbook 5 RESPONSIBILITIES 5.1 Freight Train Operations Senior Manager The Freight Train Operations Senior Manager is responsible for: Personnel Compliance: The Freight Train Operations Senior Manager holds the responsibility of ensuring that all personnel who are affected by the procedures outlined in this document acknowledge, understand, and fully comply with these procedures. This involves creating awareness among relevant personnel and ensuring their adherence to the documented operational protocols. Procedure Modification: The Freight Train Operations Senior Manager is also accountable for initiating any necessary changes or updates to the procedures detailed in this document. If there is a need to modify or enhance the procedures for any reason, the Freight Train Operations Senior Manager is responsible for initiating this process. Document Control: In accordance with SAR's documented Control of Document Procedure, SAR-010-400-2-001, the Freight Train Operations Senior Manager ensures that any proposed changes to this procedure are appropriately directed through the Document Controller. This ensures that modifications are managed and documented in compliance with SAR's established procedures for controlling document revisions. 5.2 Terminal and Yard Section Head They are responsible for: Ensuring Compliance: The Terminal and Yard Section Head, working in collaboration with the Terminal Masters, is tasked with the critical responsibility of ensuring that all Groundstaff thoroughly understand and adhere to this Operations Handbook document. This involves: Verifying that Groundstaff are well-informed about the specific procedures, safety protocols and guidelines laid out in this document. Monitoring and supervising the implementation of these arrangements to guarantee that they are consistently followed by all Operations personnel. 5.3 Terminal Master They are responsible for: Compliance Oversight: Terminal Masters are accountable for ensuring strict adherence to the guidelines and procedures outlined in the handbook to maintain operational safety and efficiency. They play a crucial role in overseeing that Groundstaff and those staff involved in loading, unloading, shunting marshalling and preparation of SAR freight trains comply with the standards set forth in the handbook. Procedure Alterations Briefing: Terminal Masters are responsible for staying informed about any updates or alterations to the procedures outlined in this handbook. They have the responsibility to promptly brief the relevant operations staff on any changes to procedures, ensuring that all staff members are aware of and understand the modifications. Distribution of Current Handbook Version: Terminal Masters must facilitate the distribution of the current version of this Operations Handbook to all relevant staff members. They are accountable for ensuring that all relevant operations staff have access to the most up-to-date information, promoting consistency and accuracy in operational practices. Communication and Training: Terminal Masters are responsible for effective communication with operational staff, providing clear and concise information about the contents of this handbook. They may conduct training/briefing sessions to ensure that staff members are well-versed in the procedures outlined in the handbook, fostering a culture of continuous improvement and adherence to standards. Competency: Terminal Masters are responsible for ensuring that Groundstaff are assessed and are competent in line with the Competence Management System (SAR-005-100-2-032). [I] Internal Document No.: Rev. No.: Effective Date: Page 6 SAR-005-100-3-004 02 12 February 2024 Function: Freight Department: Operations Management Document Title: Terminals, Mines and Ports Operations Handbook 5.4 Groundstaff Adherence to Procedures: Groundstaff are directly responsible for strictly adhering to the procedures and guidelines outlined in this Operations Handbook. They must ensure that their actions and decisions align with the prescribed standards to maintain operational safety and efficiency. Full Understanding of Procedures: Groundstaff are accountable for fully understanding the procedures detailed in the handbook. It is their responsibility to familiarize themselves with the content of the handbook to ensure a comprehensive understanding of the operational protocols. Implementation of Safety Measures: Groundstaff must actively implement the safety measures and best practices outlined in the handbook during all phases of train operations. They are responsible for integrating safety protocols into their daily activities to mitigate risks and enhance overall safety. Continuous Compliance: Groundstaff are expected to maintain continuous compliance with the handbook's procedures, adapting to any updates or alterations communicated by Terminal Masters. They play a key role in upholding operational standards and contributing to a culture of consistency and reliability. Communication with Terminal Masters: In the event of any uncertainties or challenges related to the handbook procedures, Groundstaff are responsible for communicating with Terminal Masters. They should seek clarification and guidance to ensure proper understanding and adherence to the outlined processes. [I] Internal Document No.: Rev. No.: Effective Date: Page 7 SAR-005-100-3-004 02 12 February 2024 Function: Freight Department: Operations Management Document Title: Terminals, Mines and Ports Operations Handbook 6 DOCUMENT DESCRIPTION GENERAL 6.1 Reporting for Duty You are to report for duty at the location and time laid down in local instructions. When doing so you are certifying that you are: In a fit state of health. Not under the influence of alcohol or drugs. Not taking any prescribed medication or medication purchased over the counter that has not been previously declared to SAR. Have had the required amount of rest since the last turn of duty. In possession of PTS card and SAR ID. Have all the required PPE. In possession of any approved spectacles or hearing aids (and a spare). In possession of all appropriate equipment and publications. Have your SAR issued Mobile Communication equipment (Phone or GSM-R handset) and it is fully charged. Have signed for all relevant notices. Have all the required Operational forms. 6.2 Medical Medical Condition You must notify your Terminal Master of any medical condition not already on record with SAR. This notification must be made as soon as you become aware of the condition. It is not limited to those conditions discovered during required medical examinations. Medication You must notify the OCC of any medication not already on record with SAR. If you are prescribed any medication by your doctor, you must report it to your Terminal Master as soon as possible - but at the latest when you book on duty. Always tell your doctor that you are involved in safety-critical work, since this will help him to prescribe appropriate medication. Corrective Lenses If you require the use of corrective lenses, you must: Wear them while performing your duties. Have a second pair with you while on duty if the lenses are required for distance vision. 6.3 Sunglasses You may wear sunglasses when exposed to direct sunrays or the glare of the sun. 6.4 Methods of Work and Wagon Briefs You must familiarize yourself with all relevant methods of work or local working arrangements. You must also familiarize yourself with all relevant SAR wagon briefs. [I] Internal Document No.: Rev. No.: Effective Date: Page 8 SAR-005-100-3-004 02 12 February 2024 Function: Freight Department: Operations Management Document Title: Terminals, Mines and Ports Operations Handbook 6.5 Personal Protective Equipment (PPE) You must always wear the appropriate and approved PPE. Your PPE will be designated by your role and your location. When working on or about the railway, you MUST wear the minimum requirement of: High-visibility vest/jacket or coat Steel-toed boots You must also wear any additional site-specific PPE, as required in the local Method of Work or other instructions. All PPE vests/jackets/coats must have reflective strips. Garments must be kept clean and in good condition. 6.6 Personal Equipment You must always carry your company ID. You must also ensure that you are in possession of equipment necessary to perform your duties. Your equipment may include: Mobile phone Radios Hand lamp/torch Notebook and pen Defect Cards Train documentation Clamp Keys 6.7 Publications You must maintain copies of the following documents - and, when on duty, have them with you: SAR rule book Site method of work or local working instructions Any special instructions relevant to your post [I] Internal Document No.: Rev. No.: Effective Date: Page 9 SAR-005-100-3-004 02 12 February 2024 Function: Freight Department: Operations Management Document Title: Terminals, Mines and Ports Operations Handbook 6.8 Health and Safety Responsibility When on duty you are to ensure the safety of: Yourself, your fellow employees and the general public Customers inside and outside of the Company Property inside and outside of the Company The environment Safe System of Work Follow the method of work; it is there for your protection. You must: Always use the correct tools provided, providing you are trained and competent in the use of those tools. If the correct tools are unavailable, DO NOT perform the task. Never place your hand into machinery that has not been shut down and secured; it may move without warning, resulting in a severe injury. Accident/Incident Reporting Always report accidents/incidents immediately so that all perishable evidence can be gathered and they can be investigated: Always report unsafe conditions to your supervisor. Never assume an injury is too small to report. Accident/Incident Management If an accident or incident occurs, all train movements must stop immediately. The following further actions must then be undertaken: Stop loading/unloading and associated activities. Protect the train so that no other train can become involved – this may require an emergency call to the OCC. Call the emergency services (if necessary). Inform the Terminal Master or representative. Comply fully with all local emergency procedures, including the completion of any necessary documentation. Once the site has been made safe and all the above actions have been completed, you must: Complete an interview with your Line Manager. Submit a written report before booking off duty. Take photos (if you have a camera available). Record any other information that you believe may be of value to the accident investigator. DO NOT interfere with, disturb or remove any evidence of the possible cause of the accident - except to help the injured or to prevent further injury or damage. Safe Walking Routes A Safe Walking Route is a route that has been specially designated for your use. Details of authorized walking routes and points of access are published locally. As far as reasonably practicable, you must stay on authorized Safe Walking Routes when performing your duties. [I] Internal Document No.: Rev. No.: Effective Date: Page 10 SAR-005-100-3-004 02 12 February 2024 Function: Freight Department: Operations Management Document Title: Terminals, Mines and Ports Operations Handbook 6.9 Lifestyle and Professional Operations Rest and Fatigue Being tired at work can be just as dangerous as taking alcohol or drugs because you: Lose concentration. Don’t judge speed and distance so well. React more slowly. May even fall asleep. Any of the above could put you and other people in danger. Being tired can also make some people moody and irritable, which can cause them to take risks. Danger signs of drowsiness include: You keep yawning and your thoughts keep wandering. You suddenly realize that you haven’t been concentrating. Your eyes close for a moment - or they go out of focus. You have trouble keeping your head up. What to do if you are Feeling Drowsy The only cure for feeling drowsy and tired is sleep, but there are temporary steps that can increase your alertness. If you can’t take a break immediately, you should try the following: Have a drink of cold water; eat a sandwich or eat piece of fruit. Rinse your face with cold water. If you feel that you may be affected by drowsiness or fatigue – and feel unable to deal with it yourself - advise your Manager/Supervisor. Ensure that you are well rested, and have had adequate sleep, before reporting for duty. It is important that your lifestyle does not conflict with the responsibilities of your job. Heat Exposure Working in a very hot climate saps your energy and makes you feel tired and lethargic. Sensible precautions to take include: Drinking lots of water. Don't underestimate how much you will need - and remember to drink it. Staying out of direct sun during the hottest part of the day (as far as possible) - so from 10am to 4pm, try and stay in the shade. Dress comfortably in light clothing and wear a wide-brimmed hat. Apply sunscreen protection factor [SPF] of at least 30 and re-apply every 2 hours. Personal Preparation Make sure you are fit for duty and have a copy of (or are aware of) all operational safety information relating to the place in which you will be working: Take all the rest you need before coming to work. Make sure that you are aware of the method of work for the location where you are working. Be in possession of all relevant documents and equipment, and ensure that the equipment is working correctly. Be aware of any relevant restrictions for the location where you are working. CAUTION: returning from leave or extended illness introduces risk. Ensure that you are fully familiar with any changes or amendments which affect your work. [I] Internal Document No.: Rev. No.: Effective Date: Page 11 SAR-005-100-3-004 02 12 February 2024 Function: Freight Department: Operations Management Document Title: Terminals, Mines and Ports Operations Handbook COMMUNICATIONS 6.10 General Principles Always use the approved method of communicating, whether this is phone, radio or hand signals. When using communication equipment, always ensure your message is clearly understood. Repeat back any message you have been given so that the other person can be sure you have fully understood the message. Do not permit any train movement to commence unless you are 100% sure that the instructions you have given or received have been fully understood by both parties. To prevent misunderstandings, always use the phonetic alphabet. This is especially important when establishing your location. Phonetic Alphabet A- ALPHA J- JULIET S- SIERRA B- BRAVO K- KILO T- TANGO C- CHARLIE L- LIMA U- UNIFORM D- DELTA M- MIKE V- VICTOR E- ECHO N- NOVEMBER W- WHISKY F- FOXTROT O- OSCAR X- X-RAY G- GOLF P- PAPA Y- YANKEE H- HOTEL Q- QUEBEC Z- ZULU I- INDIA R- ROMEO 6.11 Emergency Call In the event of an accident or serious incident, you must make an emergency call to the OCC. To ensure that you provide all relevant information, use the following sequence – Say: “This is an Emergency Call”, then… Give your name and your job title. Describe where you are speaking from. Give your phone contact details – if applicable. Describe the exact location and details of the incident. State the action you require the OCC to take. Get the train controller to read back your message. 6.12 Rail Dangerous Goods Emergency Call In the event of an accident or serious incident involving Dangerous Goods (DG), you must make a Rail Dangerous Goods emergency call to the OCC. In addition to the information above you must also provide: Unless the incident is minor (no damage to wagon, tank, container or flask) advise the OCC to stop all trains passing on adjacent lines. List the following for any wagon involved in the incident: o Wagon numbers (if you know them) o Positions on train or in siding o UN number shown on the Wagon What protection arrangements have been applied. [I] Internal Document No.: Rev. No.: Effective Date: Page 12 SAR-005-100-3-004 02 12 February 2024 Function: Freight Department: Operations Management Document Title: Terminals, Mines and Ports Operations Handbook 6.13 Mobile Phones When at work, you may only use your mobile phone if your duties require it, and if you are in a position of safety. The use of mobile phones is prohibited when: Operating the controls of a moving train, engine or machine. Occupying the controlling cab of a moving train or engine and not operating the controls. However, you may use a phone if the call directly relates to duties, and you are not distracting the driver. In control of a company vehicle. 6.14 Correct use of Radios When you use a radio / GSM-R handset with a ‘transmit’ or ‘speak’ button, you must press the button fully before you start speaking and must not release the button until after you have finished speaking. Before speaking on the radio, listen to ensure that the channel you want to use is not already in use. Make sure your message is understood by speaking: Directly into the mouthpiece with the mouthpiece near (but not too near) to your mouth. With a natural rhythm, and at the same volume as you would use in normal conversation. Use clear sentences. Use normal ‘Railway’ words and phrases found in the rules, regulations and instructions. Use the Phonetic Alphabet to spell words that are difficult to say. Avoid slurring one word into another and making hesitation sounds such as, “um” and “err”. Ensure messages are repeated back and that you understand the message. If you do not understand the message, ask for the message to be repeated back. All safety-critical communication must be undertaken in English. If the caller speaks in an accent or dialect which is unfamiliar to you, take time to make sure your message is understood and that you understand the other person’s message. 6.15 Shunting Communications All communications must be conducted in accordance with safe practices. 6.16 Radio Two-way radio or GSMR handsets are the primary methods for shunting communication. Before starting work, inspect your radio and ensure that there is sufficient battery power to last the duration of the work activity. Ensure that your radio is always turned on, is adjusted to the correct frequency and that the volume set so that all transmissions can be heard clearly. 6.17 Hand Signals In the event that a radio is not available, short formation shunting by hand signal is permitted, provided that a clear understanding has been reached between all affected parties and a suitable method of work has been agreed. 6.18 Telephone In emergency situations, if a radio is not available, a mobile phone may be used, provided continuous communication can be maintained. [I] Internal Document No.: Rev. No.: Effective Date: Page 13 SAR-005-100-3-004 02 12 February 2024 Function: Freight Department: Operations Management Document Title: Terminals, Mines and Ports Operations Handbook 6.19 Controlling Train Movement When controlling train movement by radio or phone, ensure that you: Are standing in a position of safety. Clearly identify the correct train and driver. Keep in constant communication with the driver (or other person controlling the movement) throughout each movement. Speak continuously (every 5 seconds) when controlling a propelling movement. Instruct the driver to stop immediately, if you notice that the transmission is failing. Make sure the driver stops immediately if there is a break in transmission. The driver must only restart on the instruction of the person controlling the movement. Never interrupt when shunting is taking place unless it is an emergency. Always wait until there is a natural break in the conversation and then ask if you may speak. Say ‘Break, Break’ before interrupting. If the Shunter is about to make a move he will say no, if not he will say yes and you may then pass your message: Keep messages brief and to the point. Do not mess about on the radio or use inappropriate language. If you see something dangerous and need to stop a movement simply say ‘EMERGENCY STOP, STOP, STOP’. Do not try and explain what is going wrong first, stop the movement then explain. 6.20 Stopping Trains Give adequate warning for the driver to stop, allowing sufficient time for communication with the driver - and for the driver to stop the train. Always remain focused on the stopping point, particularly when approaching signals, fouling points, other vehicles and buffer stops. Do not allow yourself to become distracted. When approaching the required stopping point, you are to give the driver a controlled countdown: When propelling over a long-distance use meters: o 300m, 200m, 100m, down to 10m 6, 5, 4, 3, 2, 1. o Prepare to Stop. o Stop, standby. When splitting wagons or clearing switches use wagon lengths: o 4 wagons, 3 wagons, 2 wagons, 1 wagon - last wagon. o Prepare to Stop. o Stop, standby. [I] Internal Document No.: Rev. No.: Effective Date: Page 14 SAR-005-100-3-004 02 12 February 2024 Function: Freight Department: Operations Management Document Title: Terminals, Mines and Ports Operations Handbook 6.21 Hand Signals By Day Move away from the Move towards the Ease up Shunter Shunter Slow down Stop immediately Stop when on a vehicle By Night [I] Internal Document No.: Rev. No.: Effective Date: Page 15 SAR-005-100-3-004 02 12 February 2024 Function: Freight Department: Operations Management Document Title: Terminals, Mines and Ports Operations Handbook SHUNTING 6.22 Personal Safety The safety of Operations Staff is the responsibility of the Yard Master or Terminal Team Leader; however, this does not release the individual from the responsibility of maintaining their own safety. You must: Always ensure that you reach a clear understanding of current and intended actions with all personnel who may come into contact with any shunting movement. Be aware of limited clearances – never take a chance. Make sure you keep a good lookout at all times. You must not: o Get on or off a moving rail vehicle. o Ride on any vehicle other than a loco. o Go between vehicles unless you are absolutely certain that they cannot move. o Remain between vehicles during any movement (ease-up, coupling-up, detaching loco). If you have to go between vehicles, you must: Wait until the vehicles have stopped completely. Inform the driver you are “going in between”. Instruct other staff that they are not to make any movement towards you with either wagons or loco until you are clear. When crossing the track, keep 7m from any stationary vehicles in case they move without warning. If you have to cross from one side of a train to the other, cross over the wagons using the steps and access platform, do not cross by climbing over or under the coupler. [I] Internal Document No.: Rev. No.: Effective Date: Page 16 SAR-005-100-3-004 02 12 February 2024 Function: Freight Department: Operations Management Document Title: Terminals, Mines and Ports Operations Handbook 6.23 Reducing Shunting Risk Prior to the Movement Before making any shunting movement, reach a clear understanding with all those involved, such as the Driver, Pilot, RSM and other operations staff. Clearly establish the following: Who will be controlling the movement? How the movement is to be controlled? What is the purpose of the movement? Also, make sure that you are in possession of all relevant information. If you are not sure, ask, and check the following: The sidings involved. The current working conditions and restrictions (such as capacity), whether vehicles are already stabled within the siding, whether scotches are in place, the lighting conditions, etc. The type of vehicles to be moved and any degraded mode of working involved (such as the movement of vehicles with isolated brakes or a propelling movement). Whether anyone is working on (or near) the track or on (and around) vehicles. Whether a road or foot crossing is involved. That depot protection has been lowered and that the necessary authority to proceed has been obtained. You have the correct authority before commencing movement. Any issues that may impact on safe coupling and uncoupling procedures (such as curvature of the track). Any restrictions on visibility. That when the move is finished, it will not impact on any fouling points or cause any risk to subsequent movements leaving the siding. Reducing the Risk of Derailment Check all switches prior to any movement, looking for proper fitting and the absence of blade damage. Do not assess correct fitment from a distance: even a few feet can be enough to misjudge the alignment of switch blades. Check that trailing switches are correctly set for the direction of travel, since the risk of damage increases when these are run through in the ‘open’ position. If a vehicle has been stabled over the top of a switch for a period of time, check that they have not been moved. Comply with all applicable speed restrictions; excessive speed is often a factor in derailments. Make sure you check for scotches or any debris fouling the track. Take extra care in poor lighting conditions. DO NOT operate an LFOP unless you have been trained and authorized. Reducing the Risk of Collision Reach a clear understanding with others working in the yard. Be aware of any other movements taking place in the yard. Make sure that all switches have been set correctly. Keep a good look-out for anything left foul of the line you are working on (such as wagons or road vehicles). Do not leave wagons/locos foul of switches; ensure that they are well clear. Use the ‘Safe Clearance Markers’ as a guide. [I] Internal Document No.: Rev. No.: Effective Date: Page 17 SAR-005-100-3-004 02 12 February 2024 Function: Freight Department: Operations Management Document Title: Terminals, Mines and Ports Operations Handbook Reducing the Risk of Uncontrolled Movement Ensure that the required number of handbrakes have been applied to all stabled wagons. DO NOT remove scotches or release handbrakes unless the wagon(s) are attached to other secured wagons or a loco. DO NOT buffer up to wagons or a loco until you have confirmed that they are correctly secured. 6.24 Controlling Speed Ensure the speed of the train does need exceed the speed limit and be prepared to instruct the driver to slow down if the movement is being made too fast. You must: Take particular care when approaching any hazard and reduce the speed of the train if the hazards can’t be seen at the usual distance, due to degraded visibility (for example, during sandstorms). Always comply with the speed limits set out in local instructions. 6.25 Propelling Movements When controlling a propelling movement: You must always be in advance of a propelling movement, unless stated otherwise in the local MOW. If you are unable to proceed on foot, you are to move to a position of safety beforehand, and then call the train up to you. Stop, then move again if necessary. You may ride on the designated platform on the leading Loco, provided that the safety barrier is in place and fully functional. Remain in constant communication (every 5 seconds). Maintain a constant look-out for hazards, i.e. crossings, trespassers. Warn others of approaching movements. Keep a check on the train to ensure that it is moving correctly. Stop 5 meters from any vehicles, stop-blocks or shed doors. [I] Internal Document No.: Rev. No.: Effective Date: Page 18 SAR-005-100-3-004 02 12 February 2024 Function: Freight Department: Operations Management Document Title: Terminals, Mines and Ports Operations Handbook 6.26 Attaching or Detaching a Wagon/Locomotive General Remain in a position of safety at all times and be aware of any hazards that could result in you tripping / falling between the vehicles whilst they are being coupled up. Come to a clear understanding with the driver (and any other person who may be involved in the movement) before you go in between vehicles to couple /uncouple. To prevent heavy impact with vehicles, always stop short before coupling up. Before touching the ICC, check with the driver that train line power is switched off. Inform the driver you are “going in between” and await a reply. After coupling/uncoupling and before getting out from between vehicles, check whether any movements may occur on adjacent lines or sidings – never assume it is clear. There are many hazardous associated with coupling / uncoupling vehicles – never take short cuts. Make sure you have a good understanding of the location and hazards. Always wear gloves. Coupling Sequence Ensure that you are in a position of safety away from any possible movement of the couplers if they should miss each other – NEVER stand in between. The correct sequence for coupling a wagon or locomotive is: Stop the vehicles at least 5 meters apart to enable safe preparation of the coupler. Open the coupler jaw. (Pull the release lever, ensuring that the locking pin fully disengages from the coupling jaws and pull the jaws open). When the couplers are set and lined up, complete the movement - checking that couplers engage correctly. To assist coupling, particularly on a curve, it is good practice to open the jaws on both wagons. This avoids the risk of the jaws closing before they have engaged correctly. Having coupled up, and before releasing any handbrakes, perform a pull test by instructing the driver to draw forward. If the coupling has locked correctly, the train will be unable to move. Stop the movement. Release handbrakes. Connect air pipes and the ICC. The correct sequence is: 1. Door Air Pipe 2. Brake Air Pipe then, 3. ICC- Before touching the ICC, check with the driver that train-line power is switched off. Open air cocks – half open, wait for pressure to equalize then fully open. Uncoupling Sequence The correct sequence for un-coupling a wagon or locomotive is: Ensure the vehicles have stopped completely and inform the driver you are “going in between” and wait for a reply. Close the air cocks. Disconnect the ICC. Before touching the ICC, ensure the train-line power is switched off. Hoses and ICC cables are to be secured with the appropriate retainer. Apply handbrakes to vehicles being stabled. Move to a position of safety, pull the coupling release lever and instruct the driver to “ease off”. If the locking pin is tight, tell the driver to “ease up” to release the tension on the pin. [I] Internal Document No.: Rev. No.: Effective Date: Page 19 SAR-005-100-3-004 02 12 February 2024 Function: Freight Department: Operations Management Document Title: Terminals, Mines and Ports Operations Handbook DANGEROUS GOODS 6.27 Classification, Identification and Hazard Classification When transported in commercial quantities by rail some products are classified as Dangerous Goods as they are determined to be capable of posing an unreasonable risk to health, safety, and property. Goods are classified according to their chemical and/or physical properties. There are nine numeric hazard classes: Class 1: Explosives. Class 2: Gases. Class 3: Flammable Liquids. Class 4: Other Flammables. Class 5: Oxidizers and Organic Peroxide. Class 6: Toxic and Infectious Substances. Class 7: Radioactive Material. Class 8: Corrosive Substances. Class 9: Miscellaneous Items. SAR currently transports two products that are classed as Dangerous Goods: Molten Sulfur: Class 4.1 – Flammable Solid Phosphoric Acid: Class 8 – Corrosive Identification- Hazard Placards Molten Sulfur When transported in a molten state Sulfur is extremely hot (150oC) and is classified as a flammable solid. At high temperatures Sulfur reacts with hydrocarbons (such as diesel) to give off Hydrogen Sulphide (H2S) gas. Class 4.1 Flammable Solids [I] Internal Document No.: Rev. No.: Effective Date: Page 20 SAR-005-100-3-004 02 12 February 2024 Function: Freight Department: Operations Management Document Title: Terminals, Mines and Ports Operations Handbook Phosphoric Acid A corrosive viscous liquid that reacts with most metals to form flammable hydrogen gas. Class 8 Corrosives Identification- United Nations (UN) Number In addition to warning placards, wagons and containers must display an orange plate with the UN Number identifying the dangerous good contained. Wagons transporting Molten Sulfur and Phosphoric Acid will display the following placards: ٨٤٤٢ Molten Sulfur 2448 ٥٠٨١ Phosphoric Acid 1805 Identification- Other Markings (Elevated Temperature) [I] Internal Document No.: Rev. No.: Effective Date: Page 21 SAR-005-100-3-004 02 12 February 2024 Function: Freight Department: Operations Management Document Title: Terminals, Mines and Ports Operations Handbook Hazard Molten Sulfur Adverse symptoms may include the following: Ingestion: Toxic if swallowed. Inhalation: Respiratory tract irritation, coughing. Skin: Irritation, redness, especially under repeated or prolonged contact or when moisture is present. Eyes: Pain or irritation, watering, redness. Phosphoric Acid Adverse symptoms may include the following: Ingestion: Digestive tract burns including mouth, esophagus and stomach. Inhalation: Respiratory tract irritation, coughing. Skin: Severe skin burns with permanent damage (scarring). Eyes: Serious eye damage and possible blindness 6.28 Action by Terminal Staff and Traincrew In the event of an incident, terminal staff and train crew are to notify the OCC immediately by the quickest possible means – this will usually be done by the Driver using the emergency button on the GSM-R radio. Staff are then to take the following actions: Where safe and practicable to do so: o Bring the train/shunting movement to a stop in a suitable place, bearing in mind the type of hazard (e.g. fire, loss of load), the local conditions (e.g. tunnel, built-up area) and possible actions by the emergency services (accessibility, evacuation), if necessary, by agreement with the OCC. o Switch off the locomotive in accordance with the operating instructions. Avoid sources of ignition, in particular, do not smoke, use electronic cigarettes or similar devices or switch on any electrical equipment. Inform the OCC giving as much information as possible about the accident or incident and dangerous goods involved. Keep information on the dangerous goods being carried (if necessary, the transport documents) readily available for the emergency services on arrival. When leaving the locomotive, put on the prescribed PPE. Move away from the immediate vicinity of the accident or incident, advise other persons to move away. Stay up-wind of any spillage, fire or smoke. Do not walk into or touch spilled substances and avoid inhalation of fumes, smoke, dusts and vapours. Remove any contaminated clothing and dispose of it safely. 6.29 Safety Distances All personnel are to remain outside the following safety distances unless authorized by a Dangerous Goods Expert. Loss of Containment (Spillage): 100 meters. Fire: 800 meters. [I] Internal Document No.: Rev. No.: Effective Date: Page 22 SAR-005-100-3-004 02 12 February 2024 Function: Freight Department: Operations Management Document Title: Terminals, Mines and Ports Operations Handbook 6.30 PPE Requirements You must not approach the site of the incident until authorized by the Dangerous Goods specialist. The following PPE is to be worn by anyone attending a DG Incident: Hard Hat. Safety Glasses with side shields. Long sleeved shirt and long trousers. Hi-Vis vest. Gloves. Safety Boots (6” high lace up). H2S Monitor (Molten Sulfur incidents only). 6.31 First Aid Measures Eye Exposure: Immediately flush eyes with plenty of water for at least 15 minutes. Hold eyelids apart. Remove contact lenses, if present and easy to do. Continue rinsing. Get medical attention immediately. Skin Exposure: Immediately flush with plenty of water for at least 20 minutes while removing contaminated clothing and shoes. Get medical attention immediately. Inhalation: Remove victim to fresh air and keep at rest in a position comfortable for breathing. If breathing is difficult, give oxygen. Get medical attention immediately. Ingestion: Rinse mouth with water and afterwards drink plenty of water. Do not induce vomiting Get medical attention immediately. 6.32 Tank Wagon Inspection Checklist Check for the following when inspecting wagons: Signs of any leak from pipes or valves. Signs of product spillage. Manway covers, outlet caps and plugs are in place and secure. Locking pins are in all fitting covers. Record serial number of any security seals that have been applied. Acceptable Spillage Acceptable Spillage NOT Acceptable Spillage [I] Internal Document No.: Rev. No.: Effective Date: Page 23 SAR-005-100-3-004 02 12 February 2024 Function: Freight Department: Operations Management Document Title: Terminals, Mines and Ports Operations Handbook ADDITIONAL OPERATIONAL PROCEDURES 6.33 Electronically Controlled Pneumatic (ECP) Brakes Components The following components are required for a train fitted with ECP brakes: Head End Unit (Fire Screen) – in the driving cab and operated by the driver. Inter Car Connector (ICC) Cables – an electrical connection between each vehicle. Each wagon has: Car Control & ID Device (CCID). ECP Manifold fitted to the brake distributer. End Of Train (EOT) device. Inter Car Connector (ICC) Cable The ICC cable runs the length of a train and provides a data link between the Head End Unit (HEU) in the locomotive, each wagon CCID and the End Of Train (EOT) unit at the rear of the last wagon. It also provides electrical power (Train- line power) to each wagon CCID and the EOT. There is an ICC cable connector at each end of a wagon. The ICC cable operates at 230v. Before connecting ICC cables either the connection between the loco and wagons must be broken, or the train line power must be switched off. Each connector has two locking indicators, a red square and a blue line. If the ICC is coupled correctly, the red squares will be hidden and the blue lines will join up. Before connecting, ensure there is no sand or debris in the connections. Give it a shake! To connect two inter-car connectors, depress the spring tab button until the spring tab is fully retracted, and then slide the two connectors together. Properly mated inter-car connectors will click when tugged upon. To disconnect the cable, undertake same procedure in reverse: depress the spring tab buttons and pull the connectors apart. [I] Internal Document No.: Rev. No.: Effective Date: Page 24 SAR-005-100-3-004 02 12 February 2024 Function: Freight Department: Operations Management Document Title: Terminals, Mines and Ports Operations Handbook Car Control and ID Device (CCID) Each wagon is fitted with a CCID which can run on train-line power or internal batteries. There is a red LED on the side of each CCID. A steady light indicates that train line power is connected. A flashing light indicates that train line power is off and the CCID is running on battery power (They only last for approximately 4 hours). No light indicates the wagon is de-energized or asleep. Manifold Each wagon is fitted with a manifold mounted on the side of the brake distributer. The manifold receives brake commands from the CCID and controls the release of air, through the distributer, to the brakes. There are two types of manifold: Standalone – Fitted to the Phosphate wagons. When operating in conventional mode a standalone manifold only enables to the driver to fully apply or release the brakes. Overlay – Fitted to the Bauxite and all Tank wagons. When operating in conventional mode an Overlay manifold gives the driver full control of the brakes. End of Train (EOT) Device The EOT is a self-contained, portable device that is placed on the coupler of the last wagon to make up an ECP-equipped train. The EOT uses 240v DC train-line power to run its electronics and charge its batteries. If train-line power is lost, the EOT runs on its internal batteries. The EOT is physically the last network node in the train, and transmits a status message (EOT Beacon) to the loco once per second. If communication is lost, the train brakes are automatically applied. The EOT also provides a marker light (Tail Lamp) at the rear of the train. Modes of Operation The brakes on a train can be operated in one of 3 modes: RUN Mode: Train-line power is switched on. EOT required. SWITCH Mode: Train-line power is turned off. EOT NOT required. (Caution: the driver can turn the power back on) CONVENTIONAL: The ECP brake system is not functioning. EOT NOT required but Train-line power may still be live. [I] Internal Document No.: Rev. No.: Effective Date: Page 25 SAR-005-100-3-004 02 12 February 2024 Function: Freight Department: Operations Management Document Title: Terminals, Mines and Ports Operations Handbook 6.34 Fitting an End of Train (EOT) Device Installation Release the securing handle from the lock and unscrew the handle until the coupler mount hook is lying flat. Insert the hook into the top coupler clevis. Tighten the handle clockwise until the hook rotates upright and draws the EOT unit firmly against the coupler. The EOT may require jostling as the handle is tightened, to ensure the unit is fitted securely. Ensure that the handle is secured with the lock to provide anti- rotation protection. Secure with optional padlock, with clasp through handle. Connect the EOT ‘gladhand’ to the Brake Pipe (BP) end hose and open BP cock. Note: If brake pipe pressure is present, the EOT may activate the High Visibility Marker if ambient light conditions justify. Connect EOT train-line cable to the wagon ICC. Turn on ECP to pulse the train-line. Press the test switch and check that the EOT is operational. Removal To remove an EOT Device: Ensure that train-line Power is off. Disconnect the EOT train-line cable from the wagon ICC. Close BP end valve. Pressurized air is present in the brake pipe. Injury may occur if it is not released. Depress Pressure Relief Valve located on the EOT ‘gladhand’ until all air has been allowed to exhaust. Disconnect the EOT ‘gladhand’ from the train brake pipe end hose. Remove the optional padlock’s clasp from coupler handle lock. Supporting the EOT, turn handle counterclockwise to release finger from clevis of coupler. Set unit on its back or side for transport. [I] Internal Document No.: Rev. No.: Effective Date: Page 26 SAR-005-100-3-004 02 12 February 2024 Function: Freight Department: Operations Management Document Title: Terminals, Mines and Ports Operations Handbook 6.35 Operating a Wagon Handbrake Each wagon is fitted with a manual handbrake at the ‘B’ end of the wagon. Turning the wheel to the right applies the brake and to the left releases it. Gloves must be worn when operating the handbrake. To prevent trapping fingers use two hands and hold on to the outer rim of the hand brake and not the spindles. The handbrake also has a quick release handle, pushing the handle up releases the brake. When using the quick release handle do not hold onto the handbrake wheel as this will prevent the handbrake from releasing and may also result in injury. To help determine if the handbrake is applied or released the final links of chain closest to the handbrake wheel are painted a different colour to the rest of the chain. If the links are visible the handbrake is off, if they are not visible the handbrake is on. Quick Release Handle- Quick Release Handle- Hand Brake Wheel- In the pressure-holding position. In the released position. When the hand brake is released, a length of different coloured chain is exposed. YOU MUST RECEIVE PERMISSION FROM EITHER THE DRIVER OR THE PERSON IN CHARGE OF THE MOVEMENT BEFORE YOU GO BETWEEN THE WAGONS TO APPLY/RELEASE THE HANDBRAKE. Before operating a wagon handbrake: Ensure that the vehicles have stopped. Inform the driver you are “going in between” and wait for a reply. When releasing handbrakes check all wagons on the train, not just those you expect to have brakes applied. Check the following indicators to ascertain whether or not the handbrake is applied: o Coloured links on the handbrake chain. o Tension on the handbrake chain. o Piston Travel Indicator. o Brake block clearance. Where possible, ensure that a departure roll-by examination is carried out to check that all wheels are turning freely. [I] Internal Document No.: Rev. No.: Effective Date: Page 27 SAR-005-100-3-004 02 12 February 2024 Function: Freight Department: Operations Management Document Title: Terminals, Mines and Ports Operations Handbook 6.36 Isolating Wagon Brakes In the event that the brakes are damaged or defective they can be isolated to allow the wagon to be moved. The isolating cock is mounted on the Brake Distributer attached to the Manifold. The procedure is the same for all the bulk cargo wagons in the SAR fleet. The cut-out cock is also the same on each wagon though the pull rod handles differ. The photographs (below) are of a Phosphate wagon. To isolate the brakes: Before isolating the brakes consult RSM. Turn the cut-out cock to the closed position. Pull the release valve pull rod (located on each side of the wagon) and hold it until all air is exhausted. The air in the brake cylinder will exhaust automatically and the brakes will release. Check the piston travel indicator is showing that the brakes have released. Physically check that the brakes blocks are not touching the wheels. Brake System Cut-Out Cock- Brake System Cut-Out Cock- Brake Valve Pull Rod. In the OPEN position. In the CLOSED position. 6.37 Point Clamps In the event of equipment failure, switches can be secured by applying a point clip. The clip is a G-clamp device that fits under the rail and, when fastened, secures the switch blade against the stock rail. To attach the clip, rotate the hand wheel anti-clockwise until the threaded bar is withdrawn sufficiently to allow the clip to fit under the rails. Position the clip so that it fits around both the stock rail and the switch blade. When correctly fitted, turn the hand-wheel clockwise and tighten as firmly as possible. NOTE: the clamp must not be fitted to the end of the switch rail (as in the photo right) as it is possible for it to become dislodged. The clip is to be fitted approximately 25cm from the end of the blade. Finally, slide the locking bar through one of the holes in the hand wheel and secure with a padlock. [I] Internal Document No.: Rev. No.: Effective Date: Page 28 SAR-005-100-3-004 02 12 February 2024 Function: Freight Department: Operations Management Document Title: Terminals, Mines and Ports Operations Handbook 6.38 Bearing Inspection Be extra vigilant when examining wagons during both the pre-departure inspection and departure roll-by. Particular attention is to be paid to the following: Pre-departure Inspection Check BOTH bearings. Looks for signs of a bearing collapse – does it look the same as the one next to it? Are there signs of damage to the end caps – holes or cracks? Are all 3 bolts secure, they should all be done up tightly? Is the locking plate in place? Are the locking tabs folded up stopping the bolts from coming undone? Is there any sign of leaking grease? Are there signs of burnt paint – the result of extreme heating? [I] Internal Document No.: Rev. No.: Effective Date: Page 29 SAR-005-100-3-004 02 12 February 2024 Function: Freight Department: Operations Management Document Title: Terminals, Mines and Ports Operations Handbook 6.39 Pre-Departure Check The following items are the minimum to be visually checked on all wagons before a train is released onto the Main Line. You must also complete the Pre-departure and Roll-by Checklist form (Appendix B). COUPLING: No signs of excessive wear. No Cracks. PIPES: No air leaks. Fully open/closed. Pipes not in use hung on appropriate dummy coupling. WHEELS: Flats. Cavities. Scaling/Metal build up. Flange Height. Rollover. Note: Please see document SAR-005-100-3-002 Driver Operations Handbook for further details on wheel requirements. SPRINGS: Displaced, Broken or Cranked springs must all be detached. Coil Bound – may indicate that the wagon is overloaded. Note: Any empty wagon may travel with a broken inner spring. HANDBRAKE: Hand brakes fully off. Do not rely on indicators when checking, wind on and off to ensure movement. If possible, check brake blocks. Additionally for Tank Wagons: MANWAYS: Ensure all manways are closed and safety chains are in place. Any covers are in place. SPILLAGE: Product spills are at an acceptable level. Any product leaks are reported immediately in line with dangerous goods procedures. [I] Internal Document No.: Rev. No.: Effective Date: Page 30 SAR-005-100-3-004 02 12 February 2024 Function: Freight Department: Operations Management Document Title: Terminals, Mines and Ports Operations Handbook 6.40 Roll-by Inspection When conducting a departure roll-by inspection you are to complete the Pre-departure and Roll-by Checklist form (Appendix B) and ensure you: 1. LOOK FOR: a) Signs of smoke coming from a bearing b) Glowing metal 2. LISTEN FOR: a) Squealing or grinding noises. 3. SMELL: a) Hot metal. b) Hot cooking fat. 4. FEEL FOR: a) Extreme heat radiating from the bogie as it passes. Note: If you pick up anything on a PDX report to the OCC immediately to inform the relevant department to attend to the problem. The same apply on a Roll-By if you pick up anything, the train to be stopped immediately and inform the OCC. 5. PIPES: No air leaks. Fully open/closed. Pipes not in use hung on appropriate dummy coupling. 6. SPRINGS: Displaced, Broken or Cranked springs must all be detached. NOTE: Any empty wagon may travel with a broken inner spring. Coil Bound – may indicate that the wagon is overloaded. 7. HANDBRAKE: Hand brakes fully off. Do not rely on indicators when checking, wind on and off to ensure movement. If possible, check brake blocks. Additionally for Tank Wagons: 8. MANWAYS: a) Ensure all manways are closed and safety chains are in place. b) Any covers are in place. 9. SPILLAGE: c) Product spills are at an acceptable level. d) Any product leaks are reported immediately in line with dangerous goods procedures. [I] Internal Document No.: Rev. No.: Effective Date: Page 31 SAR-005-100-3-004 02 12 February 2024 Function: Freight Department: Operations Management Document Title: Terminals, Mines and Ports Operations Handbook 7 RECORDS Document Reference Number Document Title SAR-005-100-3-107 Pre-departure and Roll-by Checklist 8 REFRENCES Document Reference Number Document Title SAR-006-300-2-020 SAR Operating Rules 9 APPENDIX Ref No. Title Title 10.1 Appendix A Local Operation of Switches 10.2 Appendix B Pre-departure and Roll-by Checklist 10 DOCUMENT HISTORY Rev. No. Date Comments “Please detailed the changes” 00 7-Jan-18 First issue 01 23-Mar-22 Format and job titles changed Format updated, removal of wagon appendices due to having 02 12-Feb-24 standard wagon briefs, and correction of errors. [I] Internal Document No.: Rev. No.: Effective Date: Page 32 SAR-005-100-3-004 02 12 February 2024 Function: Freight Department: Operations Management Document Title: Terminals, Mines and Ports Operations Handbook 10.1 Appendix A- Local Operation of Switches Switch Control Switches on the SAR network can be controlled from one of three locations: Operations Control Centre (OCC): The OCC controls all switches on the main line and some switches in terminals, mines and ports. Local Traffic Control (LTC): An LTC may be either manned (mLTC) or unmanned (uLTC). An mLTC, such as the one to be installed in the Nariyah Depot, controls all switches within a designated site. A uLTC controls only one siding. Local Field Operations Panel (LFOP): The LFOP enables a shunter or pilot controlling a specific movement to operate a switch(s) locally. Local Field Operations Panel The LFOP is mounted on a pole adjacent to the track. An LFOP controls a ‘field operations area’ with a maximum of 3 devices (switches or derailers) within its immediate vicinity. The panel consists of: An identification plate. Two buttons for each of the SWITCH(s) within the field operation area. A READY button. Each control button can have the following states: Dark - Off Flashing On State Function Ready Button Dark Field operations area has not been handed over. Ready Button Flashing Field operations area has been handed over but is not supervised. (*) Ready Button On Field operations area has been handed over and is supervised. Field operation of the switch has not been handed over or the switch is not Switch Buttons Dark available. Switch Buttons Flashing The switch is moving or is not supervised (not fitted correctly). Field operation of the switch has been handed over and the switch is Switch Buttons On supervised (fitted correctly). [I] Internal Document No.: Rev. No.: Effective Date: Page 33 SAR-005-100-3-004 02 12 February 2024 Function: Freight Department: Operations Management Document Title: Terminals, Mines and Ports Operations Handbook Switch Indicator Attached to each switch is a reflective indicator that gives the direction in which the switch is set. The indicator displays three symbols. This symbol indicates to a driver that he is approaching a facing switch and will be leaving the Turning to the LEFT direct route. The indicator can point to the left or the right Turning to the RIGHT This symbol indicates to a driver that he is approaching a switch (Facing or Trailing) and will remain on the direct route. If a driver is approaching a trailing switch to join the main route but sees this symbol he must STOP immediately as the switch is set against his direction of travel. This symbol indicates to a driver that he is Joining from the LEFT approaching a trailing switch and will be joining the direct route. Joining from the RIGHT The vertical white bar indicates that the de- The red disc indicates that the de-railer is ‘Down’ – STOP. railer is ‘Up’ – it is safe to proceed. [I] Internal Document No.: Rev. No.: Effective Date: Page 34 SAR-005-100-3-004 02 12 February 2024 Function: Freight Department: Operations Management Document Title: Terminals, Mines and Ports Operations Handbook Operation of the LFOP Authority Before a Shunter or Pilot may operate a switch, control of the associated LFOP must be released by the relevant controller, either in the OCC or LTC. Communicating with the OCC or LTC When contacting the OCC or LTC the following procedure is to be used: Identify yourself. E.g. Name, Yard Shunter or Polot. Give your location. E.g. Nariyah or Ras-Al-Khair. Request the Zone and LFOP you require. Example: This is shunter xxx at Nariyah Yard, Operator will you please release LFOP 16 Z.2. NOTE: The OCC will release all of the LFOP within a Zone, not just an individual one. Switch Button Operation When the LFOP has been released to the Shunter or Pilot the ready button and switch buttons will illuminate, and the switches may be operated for as long as required. Each pair of switch buttons has an identification plate as well as the switch number printed on the buttons. To operate the switch, press BOTH buttons of the required switch: Duration Activity Switch will operate. While the switch is moving the switch buttons will 1 to 5 seconds. flash. 5 to 10 seconds. No action, the switch will not operate. The system will lock out. The switch lights will go out and the Ready More than 10 seconds. light will start flashing. Contact the OCC/LTC to have the system reset. The ideal duration is 3 seconds. Count, do not estimate!! The switches operate slowly, taking between 6 & 9 seconds to move. Ensure that all rail movement is stopped before operating a switch. Do not attempt to operate the switch when a train is approaching. Switch Failure (bad switch) If the switch is obstructed by sand or debris and unable to reach a supervised end position (fitted correctly) the buttons will continue to flash. Press both buttons again and the switch will move back to its original position to allow the sand/debris to be cleared safely. Once the obstruction is cleared operate the switch again. Return of LFOP To return the LFOP to the control of either the OCC or LTC press the ‘Ready’ button for between 1-5 seconds (Ideally 3 seconds). Contact the OCC/LTC to confirm that you have finished with the LFOP. [I] Internal Document No.: Rev. No.: Effective Date: Page 35 SAR-005-100-3-004 02 12 February 2024 Function: Freight Department: Operations Management Document Title: Terminals, Mines and Ports Operations Handbook Failure of Switch Motor In the event that a Switch can’t be operated from the LFOP due to a switch motor failing, or for any other reason, the switch can be wound over to the desired alignment. A Disconnection Ring and Crank Handle are required to perform this task. Disconnection Ring Crank Handle Note the ring has two locator pins. Locate the cover for the winding gear. Clear the area of all loose sand to prevent contamination of the internal mechanism when the cap is removed. Using the disconnection ring unscrew the cover. Place the cover and ‘O’ Ring to one side and protect from sand. Removing the cover exposes the RED power ring. NOTE: there is a notch at the 3-o-Clock position. Insert the disconnection ring with the handle in the horizontal position – inserting the locator pin closest to the end of the disconnection ring into the notch in the power ring. With the key in this position the switch motor power is still ON. Turn the key through 900 anti-clockwise to the vertical position. With the key in this position the switch motor power is OFF. [I] Internal Document No.: Rev. No.: Effective Date: Page 36 SAR-005-100-3-004 02 12 February 2024 Function: Freight Department: Operations Management Document Title: Terminals, Mines and Ports Operations Handbook Insert the crank handle with the locator pin at 12-o-Clock so that it fits into the notch in the power ring. To move the switch blade towards you turn the crank clockwise. To move the switch blade away from you turn the crank anti-clockwise. Crank Handle Locating Pin When the switch blade is correctly fitted the winding mechanism will make a clicking sound - STOP. Once the switch is in the desired position turn the power back on by turning the power ring 900 clockwise. Then replace the winding gear cap to prevent sand ingress ensuring that there is no sand on the cap or ‘O’ ring seal. OCC Contact Numbers Telephone GSM-R Emergency Chief Train Controller 011 525 0500 8284 9002 0546948221 Train Controller 1 011 525 0502 8284 9000 0546961224 Train Controller 2 011 525 0501 8284 9001 0546961229 [I] Internal Document No.: Rev. No.: Effective Date: Page 37 SAR-005-100-3-004 02 12 February 2024 Function: Freight Department: Operations Management Document Title: Terminals, Mines and Ports Operations Handbook 10.2 Appendix B- Pre-departure and Roll-by Checklist [I] Internal Document No.: Rev. No.: Effective Date: Page 38 SAR-005-100-3-004 02 12 February 2024 Function: Freight Department: Operations Management Document Title: Terminals, Mines and Ports Operations Handbook [I] Internal Document No.: Rev. No.: Effective Date: Page 39 SAR-005-100-3-004 02 12 February 2024 Function: Freight Department: Operations Management Document Title: Terminals, Mines and Ports Operations Handbook [I] Internal Document No.: Rev. No.: Effective Date: Page 40 SAR-005-100-3-004 02 12 February 2024 Function: Freight Department: Operations Management Document Title: Terminals, Mines and Ports Operations Handbook [I]