ERP Project Risk Assessment - A Case Study PDF 2009
Document Details
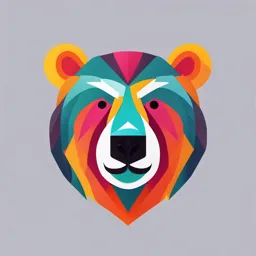
Uploaded by ProudRubidium
2009
Päivi Iskanius
Tags
Summary
This research article presents a case study of ERP project risk assessment in three manufacturing SMEs. Using a company-specific risk analysis method and characteristics analysis, the critical risks of ERP projects were identified and assessed, and recommendations were provided on how to subdivide complex projects into more manageable sub-projects. The author analyses different kinds of risks in ERP implementation.
Full Transcript
Proceedings of the World Congress on Engineering 2009 Vol I WCE 2009, July 1 - 3, 2009, London, U.K. The ERP Project Risk Assessment – A case study Päivi Iskanius...
Proceedings of the World Congress on Engineering 2009 Vol I WCE 2009, July 1 - 3, 2009, London, U.K. The ERP Project Risk Assessment – A case study Päivi Iskanius resources are badly needed in the daily business operations. Abstract—Information and communication (ICT) technology Risks are part and parcel of ERP projects, but a planned related projects, such as enterprise resource planning (ERP) and systematically adopted risk management procedure projects have a high failure rate. Planned and systematically throughout the implementation project reduces the possibility adopted risk management procedure is crucial to keep projects on time and within budget with all requirements fulfilled. In of risks occurring. The risks are higher for SMEs as the cost this paper, we have analysed the critical risks of ERP projects overruns during implementation may put financial strain on through the case study of three manufacturing small and the firm and thus substantially impact firm performance. medium size enterprises (SMEs). First, by using In addition, SMEs have less of a chance of recovering from a company-specific risk analysis method, the critical risks of the failed ERP implementation attempt than large enterprises. ERP projects have been identified and assessed. Second, by Several standardised tools and methods have been using characteristics analysis method, the recommendations of how to divide the ERP projects into manageable sub projects developed to help companies to better manage their ERP have been given. projects. In this study, we present experiences of company-specific risk analysis method (RAM) and Index Terms—Enterprise resource planning, risk analysis characteristics analysis method (CAM) through the case method, characteristics analysis method, small and medium study of three manufacturing SMEs. First, by using RAM, the sized enterprise. critical risks of the ERP projects are identified and assessed. Second, by using CAM, the recommendations of how to I. INTRODUCTION divide the ERP projects into manageable sub projects are Enterprise resource planning (ERP) systems, when given. successfully implemented, links all functions of an organisation including order management, manufacturing, II. RISK ASSESSMENT human resources, financial systems, and distribution with external suppliers and customers into a tight integrated A. ERP project risks system with shared data and visibility. The primary Several research studies have investigated the ERP risks motive for ERP implementation is the potential for enhancing and have attempted to classify them in various ways. Six the firm’s competitiveness. ERP systems provide significant main dimensions of risk in ERP implementation have been benefits, and companies adopted them with the goal of identified by , namely, 1) organizational, 2) replacing inefficient stand-alone legacy systems, increasing business-related, 3) technological, 4) entrepreneurial, 5) communications between business functions, increasing contractual and 6) financial risks. Organizational risk derives information processing efficiencies, improving customer from the environment in which the system is adopted. relations, and improving overall decision making. Business-related risk derives from the enterprise’s Despite the significant benefits that ERP systems provide, post-implementation models, artifacts, and processes with the Statistics show that under 30 % of ERP implementations respect to their internal and external consistency. are successful , which means that projects are completed Technological risk is related to the information processing on time and on budget, with all features and functions technologies required to operate the ERP system – for originally specified. ERP projects are major and risky example the operating system, database management system, exercises for any size of company. The average client/server technology and network. Entrepreneurial or implementation time of ERP system is between 6 months and managerial risk is related to the attitude of the 2 years and the average cost is between US$1,3M and owner-manager or management team, while contractual risk US$70M , and they require disruptive organisational derives from relations with partners and financial risk from change. ERP implementation requires the allocation of cash-flow difficulties, resulting in an inability to pay license special competences, and a number of financial and human fees or upgrading costs, for example. In the research of resources. Also, the implementation is usually carried out , following six risk categories have been presented: 1) concurrently with the daily business, which already ties up organizational fit, i.e. failure to redesign business processes, the available resources. Especially in small and medium 2) skill mix, i.e. insufficient training and reskilling, 3) size enterprises (SMEs), which employ less than 250 persons management structure and strategy, i.e. lack of top and an annual turnover is not exceeding 50 M€, and/or an management support, 4) software systems design, i.e. lack of annual balance sheet total is not exceeding 43 M€, scarce integration, 5) user involvement and training, i.e. ineffective communication, and 6) technology planning/integration, i.e. Manuscript received March 2, 2009. inability to avoid technological bottlenecks. Later, P. Iskanius is with the Raahe Unit, University of Oulu, Oulu, Finland. develop the risk identification list based on the category of (phone: +358 44; fax: + 358; e-mail: paivi,[email protected]).. ISBN: 978-988-17012-5-1 WCE 2009 Proceedings of the World Congress on Engineering 2009 Vol I WCE 2009, July 1 - 3, 2009, London, U.K. The following ERP risk factors are summarised by : 1) manageable and consistent by its different goals content and inadequate ERP selection, 2) poor project team skills, 3) low development approaches. The result of the CAM is a top management involvement, 4) ineffective communication recommendation of how to split the large and complex ICT system, 5) low key user involvement, 6) inadequate training project into manageable sub projects. Further, the inputs of and instruction, 7) complex architecture and high numbers of the CAM are the project proposition document, the modules, 8) inadequate business processes, 9) bad knowledge and experience from prior development projects, managerial conduction, 10) ineffective project management and the requirements of the of the project portfolio. techniques, 11) inadequate change management, 12) In this paper, the CAM analysis is formed out of 90 inadequate legacy system management, 13) ineffective questions dealing with the ICT project. The basic aim is to consulting services experiences, 14) poor leadership, 15) find out the manageable size of the ERP project of the case inadequate ICT system issues, 16) inadequate ICT system company. Also, CAM provides recommendations what manutenibility, 17) inadequate ICT supplier stability and management aspects should be put more attention to performances, 18) ineffective strategic thinking and successfully manage ERP project (management of a project planning, 19) inadequate financial management. as a whole, management of integration, project scope Instead of using abovementioned ready-made risk lists, a management, time management, cost management, quality company might consider identifying their own, management, human resource management, management of company-specific ERP implementation risk list. These risks communication, risk management, management of could be complemented by common risk lists. purchase). The questions are either positive or negative To minimize the risk of the ERP project, have statements for which their applicability to the project will be recommended the application of a risk management plan at evaluated (0 = fault, not true, 5 = exactly right; N/A = don’t different ERP implementation project stages; selection, know). The tool has been implemented as an MS Excel implementation, and usage. A planned and systematically worksheet with automatic tabulation based on decision rule adopted risk management procedure throughout the ERP sets. The result can also be illustrated graphically (see figures project reduces the possibility to risks occurring. 1 and 2). Consequently, suggest that major mistakes are made in the early stages of the ERP project, even prior to the III. CASE STUDY implementation process. , however, emphasizes the efficiency of risk management when it is introduced at the A. Case 1: Company A earliest possible opportunity in the life cycle of the system in Company A develops blast cleaning technology and question, when planning issues are most important and the manufactures automated blast cleaning machines and robots criteria for system selection are determined. (turnover about 1,2 M€ and number of personnel This research has been carried out as a case study of three approximately 20). Company A has not an ERP system, but is manufacturing SMEs. The case SMEs are in different phases contemplating the ERP implementation in near future. The of the ERP project. Company A is still contemplating the ERP need for the new ERP system has grown internally because of implementation, Company B is in the selection phase, and the problems in the current ICT system. Today, the company Company C is already in the usage phase. In practice, this is using an excel-based ICT system, which includes e.g. the study has been carried out during 1.1.–30.12.2008. following ERP functions: customer relationship management B. Risk analysis method (CRM), product data management (PDM), purchase and order management, and product lifespan management. The Risk analysis method (RAM) identifies the most essential problem of the current system is how to manage over 100 risks and their probability in the company context. The risk different versions and variations of Excel, Word, and list for the case study has been formed based on the risk list of AutoCAD documents. Main problems occur in the tendering. In this paper, the risk list is formed out of 63 questions or and purchase processes, and in the production capacity statements dealing with the ERP selection, implementation, planning. The purpose of company A is to adopt an ERP and usage. The basic aim is to identify the ERP risks arising system, which helps production capacity planning and from the company’s reality and therefore the employees from control so that the scheduling and resource allocation for various levels of organisation have been interviewed and different projects can be planned in detail before the project observed. The company-specific risk list has been filled in is started. Furthermore, the new system should include close interaction with company personnel. Risk assessment warehouse and stock management functions, and it have to for the risk list is done by evaluating each risk’s probability support purchase process. and effect in a scale from one to five. The number one means The risk list has been filled with company personnel and very small probability and effect, and number five means the effect and probability of risks have been assessed. In the high probability and catastrophic effect. Then, the risk ERP selection phase, the most critical risks which may be multiplication as an indicator of risk significance has been realised in company A are: misunderstanding between buyer used. It is calculated as multiplying the value of the and customer (12), system not flexible enough under probability by the value of the effect. Range of this value is processes’ exceptional circumstances (12), and special needs from one to twenty-one. of a company not defined (10). In the ERP installation phase, C. Characteristics analysis method the most critical risks are: company’s project manager is not a Characteristics analysis method (CAM) is a tool to ensure full time PM (20), data transfers from old to new system is that the information and technology (ICT) project is difficult (16), connecting system to other systems creates ISBN: 978-988-17012-5-1 WCE 2009 Proceedings of the World Congress on Engineering 2009 Vol I WCE 2009, July 1 - 3, 2009, London, U.K. problems (16), and supplier is not committed enough to 1974, currently employs ca. 150 people. system implementation (15). In the ERP usage phase, the Company B is in the selection phase of the ERP project. most critical risks are: system not felt as helping the business The company has interviewed several ERP suppliers. The (12) and the system supplier does not develop the system in company has already gone through more detailed discussions the future (10). with two potential suppliers. The company has made a Company A is just contemplating to acquire an ERP preliminary requirement specification, a type of demand list, system. In the RAM results, in every phase (selection, through which they are able to limit their ERP suppliers to implementation, usage), the crucial factors are depended on two options. Also, some consultants have worked for the the decision of the ERP system itself and the ERP supplier. company. Company B is very aware that the existing ICT The technical and functional factors related to the system, systems are already in the end of their life cycle, and they had and the factors related the chosen system supplier, are to invest in a new ERP system. considered the most critical. Even a company A has very few The risk list has been filled with company personnel and employees (under 20), the lack of resource, skills and the effect and probability of risks have been assessed. In the expertise, and other factors related personnel have - ERP selection phase, the most critical risks which may be surprisingly – not aroused as a potential risk in this analysis. realised in company B are: system is poor compromise for all The results analysed by CAM is presented in Figure 1. parties (12), choosing poor project manager or project group, and misunderstandings between buyer and customer (10), Management of the ERP project as a whole choosing improper ERP system (10). In the ERP installation 5,0 phase, the most critical risks are: normal business disturbs Purchase 4,0 Integration ERP project activities (20), ERP project disturbs normal Management Management business (16), timetable falls behind schedule (16), Software 3,0 2,0 configuration and testing don’t function swiftly (16), Risk Project Scope disciplined use of the system (data entry is not achieved) Management 1,0 Management (16). 0,0 In the ERP usage phase, the most critical risks are: ERP Communication Time system not used in a disciplined manner (12), and only part of Management Management the system used and benefits realized (12). Company B is in the selection phase of the ERP project. In Cost Management the RAM results, the crucial factors are mostly depended on Human Resource Management the personnel (including project manager/team and top Quality Management MA management level) behavior, skills, and experience. AVERAG CRITICAL LEVEL Company B is also worried of the changes what the new ERP system will affect to the company’s normal business, and in Figure 1. CAM diagram of the company A opposite, how the normal business hinders the ERP project progress. According to CAM, Human Resource Management is the The results analysed by CAM; is presented in the figure 2. management/leadership field that clearly exceeds the critical level. Company A should direct special attention to this Management of the ERP project as a whole factor in ERP project management. In addition, several other Purchase 5,0 management/leadership fields, such as ‘Communications Management Integration 4,0 Management’, ‘Purchase Management’, ‘The project as a Management 3,0 whole’, ‘Integration Management’, ‘Project Scope Risk 2,0 Project Scope Management’ and ‘Quality Management’ are right at the Management Management critical level. Only ‘Cost Management’ and ‘Time 1,0 Management’ and ‘Risk Management’ are clearly under 0,0 critical level. According to CAM, factors connected with Communication Time personnel training and increasing personnel skills and Management Management knowledge require more from managing the ERP project, although they are not considered to be amongst the most Human Resource Cost Management potential risk factors according to RAM. On the basis of the Management Quality Management MA CAM, it can be deduct that Company A has a clear view of AVERAG the costs caused by the ERP project, the time spent for it, as CRITICAL LEVEL well as the technical and operational risks involved. B. Case 2: Company B Company B provides demanding sheet metal work, Figue 2. CAM diagram of the company B welding, and heavy metal works, specialising in steel, paper, chemistry, and ship manufacturing related machinery and According to RAM, Communications Management is the equipment. In addition, the company manufactures offshore management/leadership field that clearly exceeds the critical equipment and ship propellers. The company, founded in level. Company B should direct special attention to the factor considered people skills, knowledge and expertise. In ISBN: 978-988-17012-5-1 WCE 2009 Proceedings of the World Congress on Engineering 2009 Vol I WCE 2009, July 1 - 3, 2009, London, U.K. addition, ‘Human Resource Management’ and ‘Quality torn apart and rewritten to work with the newer version. Management’ are right at the critical level. To manage ERP Conversely, it implies less organizational changes, because it project successfully, the company should pay attention to does not require dramatically changing the company best these three management/leadership factors. practices, and therefore the way people work. SME companies usually have great difficulties in their C. Case 3: Company C ERP through. The most common risk that may entail project Company C has implemented an ERP system a few years failure is the ubiquitous lack of resources and IT skills or the ago but only part of the system was functioned complete. company personnel. ERP systems are typically designed Company C is going to continue the ERP project and adopt for large companies, and the ERP suppliers do not necessarily several new functions of the ERP system in use. The risk list understand the special characteristics and operational has been filled with company personnel and the effect and processes of small companies. The success of an ERP probability of risks have been assessed. The risk analysis has project also largely depends on how well SMEs can manage been done focusing on the main risks considered the new changes in their business and how well personnel can adopt modules adoption. Also, because the company C already has new way of operations. This change process is best to start the ERP system in use, the selection phase was skipped. already in the early phase of the ERP project, because many In the ERP installation phase, the most critical risks which risks can be eliminated before the ERP project system starts. may be realised in company C are: normal business disturbs The SMEs can e.g. hire temporary staff to perform the routine ERP project activities (25), cost rise compared to initial operations so the key persons get more time to concentrate on estimations (25), supplier is not committed enough to system the ERP system characteristics and new work practices. implementation (25), software configuration and testing The most potential risks can be divided in the following don’t function swiftly (25), company is not important categories: the ERP supplier, the ERP system, and the customer for supplier and don’t get the best effort (25), and customer company. The most potential risk related to the supplier don’t understood the customer needs (25). In the ERP supplier, is simple to choose the wrong supplier, which ERP usage phase, the most critical risks are: all needed doesn’t understand the company’s special demands, or are information is not entered into the system (15), only part of not interested enough to committed to the ERP project of the system used and benefits realized (12), and system not small customer. Also, the high potential risk is that the ERP felt as helping the business (12). supplier chosen ends the development and/or support of the Company B estimates several risks and their probability system. Most potential risks related to the ERP system are with maximum rates. This estimate is possibly coloured by depended on its technical and functional performance and the partial failure of their old ERP project, and the features; how well the system can be implemented, communication difficulties they experienced with their ERP configured, parameterised, and integrated. supplier. Company B also has few employees (under 20), and Most potential risks related to the company are connected when the contact person of the system supplier disappeared with the factors of company personnel and company top in the middle of the project, the risks came true. management; their skills, knowledge, and experience. Also, The CAM was not carried out in the company B, since they resistance to change is a typical potential risk factor. were already at the usage phase of their ERP project. Main Personnel may not see the benefits of the system in their own usage phase problems occur because of the poor work and, thus, are not committed to the new business model, requirements specification phase, and lack of and don’t use the system in a disciplined manner. Normal documentations in the implementation phase related to business also disturbs the ERP implementation, and configuration and parameterisation. Also, the key person of personnel may be unwilling to put time or effort to the the ERP vendor shifted to another company middle of the development work. Top management support to the project is project. the most important success factor for the ERP project. The second success factor is the proper project manager. IV. DISCUSSION According to the CAM, the biggest investments in terms of The ERP project should not be viewed merely as a project bringing the ERP project to the finish line should be directed of acquiring and implementing a new ICT system but as a at Human Resource Management and Communications framework project for the company’s all business processes. Management. In such a large change project the challenge is According to , twofold approaches should be taken for to make the employees stand behind the change. The ERP projects: 1) Change the business processes to fit the acquisition of an ERP system includes within it changes for software with minimal customisation. On one hand, fewer the company modes of operation and processes. For this modifications to the software application should reduce reason the commitment of staff should be strong, so that new errors and help to take advantage of newer versions and operational models are taken into use and the system can releases On the other hand, this choice could mean changes in therefore be exploited to its full potential. The risk of sticking long-established ways of doing business (that often provide to old ways of doing things after system implementation is competitive advantage), and could shake up important people often high. People are experts at finding reasons why there is roles and responsibilities; and 2) modify the software to fit no need to change things or why it is better to stick to the old the processes. This choice would slow down the project, way of doing things, when they do not fully understand the could affect the stability and correctness of the software purpose for the change. The change process is as a ground application and could increase the difficulty of managing rule condemned to failure if people do not understand the future releases, because the customizations could need to be need for change. For this reason it is important to create a ISBN: 978-988-17012-5-1 WCE 2009 Proceedings of the World Congress on Engineering 2009 Vol I WCE 2009, July 1 - 3, 2009, London, U.K. clear vision of the desired change and to communicate this integrator/provider and commenced the change requirement really actively to the people involved in the change. In a long specification phase of adjusting their system. Company C ERP project it is also important to obtain short-term made their decision on which ERP system they will choose at successes so that people do not lose interest in the change the end stage of this research. Implementation will process and the final aims are reached. Hence, it is good to commence in 2009. divide the project into smaller part projects. It is typical for change processes that a process is declared a success too REFERENCES soon, at a stage when the first goals of the process are I.J. Chen, “Planning for ERP systems: analysis and future trend,” reached. For example, in the case of ERP projects it is Business Process Management Journal, vol. 7, no. 5, pp. 1463-7154, 2001. erroneous to proclaim the project a success at the stage when S.J. Cereola, The performance effects of latent factors on assimilation the system they have has managed to run the system of commercial open-source ERP software on small-medium successfully and they have just started using it. Only when enterprises, Virginia Commonwealth University, Richmond, Virginia, the system can be fully exploited and the original goals have September 2006. Standish Group International, Inc., 2004, The Quarter Research Report been achieved can you consider the project to have D. Aloini, R. Dulmin, V. Mininno, ”Risk management in ERP project succeeded. It is possible to enhance staff commitment to the introduction: Review of a literature, Information & Management, vol. process and the new operational model by communicating 44, pp.547-567, 2007. I. Vilpola, Applying use-centered design in ERP implementation the change and by training staff. It is very typical that the requirements analysis, Tampere University of Technology, Publication need for communication and training is underestimated. The 739, Tampere, 2008. importance of communication can also be seen in the fact that J Muscatello, M. Small, I Chen, “Implementing enterprise resource planning (ERP) systems in small and midsize manufacturing firms,” communications enhance the commitment of the Internationa Journal of Operations and Production Management, vol. management level in the process. It also pays off to 23, no. 7/8, pp. 850-871, 2003. communicate issues during the project that are not being P. Poba-Nzaou, L Raymond, B. Fabi, “Adoption and risk of ERP systems in manufacturing SMEs. a positivist case study,” Business done. In this way you can diminish the potential of Process Management Journal, vol. 14, no. 4, pp. 530-550, 2008. misunderstandings and to be in control of expectations. At M. Sumner, “Risk Factors in enterprise-Wide/ERP Projects,” Journal the beginning of the ERP process it is recommended that a of Information Technology, vol. 15, pp. 317-327, 2000. communications plan be drawn up, in which target groups, S.M. Huang, I.C. Chang, S.H. Li, M.T. Lin, “Assessing risk in ERP projects: identify and prioritize the factors,” Industrial Management means and timing are outlined. In the case that everything and Data Systems, vol. 108, no. 8, pp. 681-688, 2004. possible in the project is outsourced the company staff will M.L. Markus, C. Tanis, “The enterprise systems experience—From not consider the operational model to be their own. adoption to success”, in: R.W. Zmud, (Ed.), Framing the domains of IT management: Glimpsing the future through the past, Pinnaflex, Cincinnati, OH, 2000, pp. 173–207. V. CONCLUSION E.W.N. Bernroider, M.J. Leseure, “Enterprise resource planning (ERP) diffusion and characteristics according to the system's lifecycle: A This study presents experiences that are obtained in case comparative view of small-to-medium sized and large enterprises,” studies in which three SME companies were drawn an ERP Working Papers on Information Processing and Information project risk analysis and characteristics analysis. The case Management, no. 01, 2005. Wirtschaftsuniversität Wien, Vienna. R.L. Kliem, “Risk management for business process reengineering companies considered both of the methods as good tools; project,” Information Systems Management, vol. 17, no. 4, pp.71-73, they forced the company to think of the potential risks that 2000 might go off at the different stages of the ERP project, P. Forselius, “Software development program characteristics,” 2008, whether these risks had to do with the technical and http://citeseerx.ist.psu.edu/viewdoc/summary?doi=10.1.1.131.1516, read in 2/2009 functional characteristics of the system itself, or with the R. McAdam, A. Galloway, “Enterprise resource planning and expertise and commitment of the staff, top management or organisational innovation: a management perspective,” Industrial ERP system vendor. The RAM presents risks in a form and Management and Data Systems, vol. 105, no. 3, pp.280-290, 2005. S.F. King, T.F. Burgess, “Beyond critical success factors: A dynamic language that is understandable, because the analysis have model of enterprise system innovation,” International Journal of been done in the company context. As negative aspect of this Information Management, vol. 26, pp. 59-69, 2006 RAM is that it requires a significant amount of work, and also G. Buonanno, P. Faverio, F. Pigni, A. Ravarini, D. Sciuto, M. Tagliavini,, “Factors affecting ERP system adoption. A comparative help from external experts. The CAM helped the case analysis between SMEs and large companies,” Journal of Enterprise companies in dividing their ERP project into manageable Information Management, vol. 18, no. 4, pp. 384-426, 2005 entities and provided them with recommendations on what leadership/management aspects they should devote special Päivi Iskanius, (Doctor of Technology) works as a Postdoctoral Research Fellow at the University of Oulu. She has received her Master’ in Mechanical attention to. The CAM also showed inadequacies in the fields Engineering in 1988, eMBA in 2002, Licentiate’s degree in Mechanical of management and leadership that the implementation of an Engineering in 2004 and Doctoral degree in Industrial Engineering and ERP system causes in companies. Management in 2006. All of these degrees are from the University of Oulu. Her research interests are logistics, supply chain management and e-business Cooperation with the research group provided the applications in the SME business networks. At present, she has over 70 companies with new skills and the drive to continue in their research publications in these areas. own ERP project. Company A will take the next step in their ERP project and is faced with an extensive requirement specification process with the objective of mapping out the suitable ERP solutions for their company and to choose their ERP in 2009. Company B aims at enhancing the system they already have in use and to adopt new modules in 2009. Company B has initiated new contacts with their system ISBN: 978-988-17012-5-1 WCE 2009