Operations Management Module 1: Process Analysis PDF
Document Details
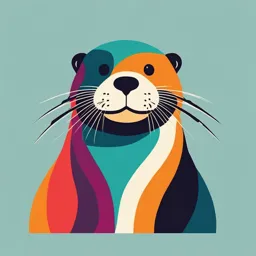
Uploaded by WellKnownFlashback9878
Indian Institute of Management Indore
Dr. Neelkanth Chandrakant Dhone
Tags
Summary
This document is a presentation on operations management, focusing on module 1: process analysis. It covers process strategies, including process focus, repetitive focus, product focus, and mass customization. Various examples and diagrams illustrate these strategies. The document also delves into process analysis and design, production technology, and their impacts on services.
Full Transcript
# Operations Management ## Module 1: Process Analysis ### Sessions: 3rd – 4th Dr. Neelkanth Chandrakant Dhone - Fellow of National Institute of Industrial Engineering (NITIE).Mumbai. - B.E (Mechanical), M.B.A(Marketing/Operations) - UGC.NET-2010 (Management) - Faculty(Productions & Operations Ma...
# Operations Management ## Module 1: Process Analysis ### Sessions: 3rd – 4th Dr. Neelkanth Chandrakant Dhone - Fellow of National Institute of Industrial Engineering (NITIE).Mumbai. - B.E (Mechanical), M.B.A(Marketing/Operations) - UGC.NET-2010 (Management) - Faculty(Productions & Operations Management) - Indian Institute of Management-Nagpur Strictly for the internal circulations only ## Session Plan - Process Strategies - Crossover Chart Example - Focused Processes - Selection of Equipment - Process Analysis and Design - Special Conditions for Service Process Design - Production Technology - Technology in Services - Process Redesign ## 1. Process Strategies > 'The objective is to create a process to produce offerings that meet customer requirements within cost and other managerial constraints' - **How to produce a product or provide a service that:** - Meets or exceeds customer requirements - Meets cost & managerial goals - **Has long term effects on:** - Efficiency & production flexibility - Costs & quality ## 1.2 Process Strategies Four basic strategies: 1. Process Focus 2. Repetitive Focus 3. Product Focus 4. Mass Customization > Within these basic strategies, there are many ways they may be implemented ## 1.2.1 Process Focus - Facilities are organized around specific activities or processes - General purpose equipment & skilled personnel - High degree of product flexibility - Typically, high costs & low equipment utilization - Product flows may vary considerably, making planning & scheduling a challenge. - **Image:** An image of a hospital operating room with three doctors operating on a patient. - **Diagram:** An image diagram that shows many inputs at the top, a square in the middle with multiple black circles. The circles are connected by lines representing the workflow. There are also many outputs at the bottom. - **Summary:** The image shows many inputs, many departments and many routings to create a uniquely treated patient as an output. ## 1.2.2 Repetitive Focus - Facilities often organized as 'assembly lines' - Characterized by modules with parts and assemblies made previously - Modules may be combined for many output options - Less flexibility than process-focused facilities but more efficient - **Diagram:** An image diagram that has many inputs at the top, a funnel that merges the inputs to a few modules, and the modules are then merged to many outputs. - **Summary:** The diagram presents a process with multiple raw materials and module inputs. It simplifies them into few modules and then combines them into many output options. ## 1.2.3 Product Focus - Facilities are organized by product - High volume but low variety of products - Long, continuous production runs enable efficient processes - Typically, high fixed cost but low variable cost - Generally, less skilled labor - Also, called as 'Continuous Processes' (non-stop production) - Example: Paper manufacturing, Sugar Manufacturing, Oil processing units - **Diagram:** An image diagram that has many inputs at the top, a large column with many branching lines to many outputs at the bottom. - **Summary:** The diagram presents a process with multiple inputs that are merged to a single column then are branched into various outputs. The outputs have variants in size, shape, and packaging. ## 1.2.4 Mass Customization - Each customer is different - The rapid production of goods & services to satisfy increasingly unique customer desires - Combines the flexibility of a process focus with the efficiency of a product focus. - **Image:** A woman holding a clear, rigid, customized acrylic teeth aligner in her hand. - **Diagram:** An image diagram that has many inputs at the top, a funnel that merges the inputs into many modules, and the modules are branched into many outputs. - **Summary:** The diagram presents a process with many inputs and many modules that are merged into many output versions. ## 1.2.4 Mass Customization - **Table:** A table compares the 1970s and the 21st century choices for customer demand - | Item | Number of Choices | Number of Choices | - |---|---|---| - | Vehicle Styles | 18 | 1,212 | - | Bicycle Types | 8 | 211,000 | - | iPhone Mobile Game Apps | 0 | 1,200,000 | - | Web Sites | 0 | 634,000,000 | - | Movie Releases per Year | 267 | 1551 | - | New Book Titles | 40,530 | 300,000+ | - | TV Channels | 5 | 185 | - | High-Definition TVs | 0 | 102 | ## 1.3 Comparison of Processes - **Table:** A comparison of the Characteristics of Four Types of Processes - | Process Focus | Repetitive Focus | Product Focus | Mass Customization | ---|:---:|:---:|:---:|:---:| - | Small Quantity & Large Variety of Products | Long Runs, a Standardized Product from Modules | Large Quantity & Small Variety of Products | Large Quantity & Large Variety of Products | - | Broadly Skilled Operators | Moderately Trained Employees | Less Broadly Skilled Operators | Flexible Operators | - | Fixed Costs Low & Variable Costs High | Fixed Costs Depend on Flexibility of Facility | Fixed Costs High & Variable Costs Low | Fixed Costs Tend to Be High & Variable Costs Low | - | High Inventory | Low Inventory | Low Inventory | Low Inventory Relative to the Value of the Product | - | Finished Goods Made to Order & Not Stored | Finished Goods Made from Frequent Forecasts | Finished Goods Made to a Forecast & Stored | Finished Goods are Build-to-Order (BTO) | - | Scheduling is Complex | Scheduling is Routine | Scheduling is Routine | Sophisticated Scheduling Accommodates Custom Orders | ## 2. Crossover Chart Example > 'A chart of cost at the possible volume for more than one process' - Evaluate three different accounting software products - Calculate crossover points between Software A & B, and between B & C | Software | Total Fixed Cost | Dollars Required Per Accounting Report | |:---:|:---:|:---:| | A | $200,000 | $60 | | B | $300,000 | $25 | | C | $400,000 | $10 | ## 3. Focused Processes - Focus brings efficiency - Focus on the depth of the product line - Focus can be: - Customers - Products - Service - Technology ## 4. Selection of Equipment - Decisions can be complex as alternate methods may be available - Important factors may be: - Cost - Quality - Cash flow - Capacity - Market stability - Flexibility - **Illustration:** An image of a high-quality MRI machine. ## 5. Process Analysis & Design - Is the process designed to achieve a competitive advantage? - Does the process eliminate steps that do not add value? - Does the process maximize customer value? - Will the process win orders? ## 5.1 Process Analysis & Design Tools - **Flowchart:** - Shows the movement of materials - Harley-Davidson flowchart - **Time-Function Mapping:** - Shows flows & time frame - Baseline/Target time - **Diagram:** An image of a Harley-Davidson motorcycle assembly line. - **Diagram:** A time-function mapping diagram that shows customer order, sales order, production, control, plant A, warehouse, and transport stages of a production process. ## 5.2(A) "Baseline" Time-Function Map - **Diagram:** An image diagram shows the stages and time for a production process. - **Summary:** The diagram shows a baseline process with various activities and their corresponding time. ## 5.2(B) "Target" Time-Function Map - **Diagram:** An image diagram shows the stages and time for a production process. - **Summary:** The diagram presents a target process with a shorter time frame for various production activities. It shows "print," "extrude," and "wait" activities with estimated time frames. ## 5.3 Process Chart - **Table:** A process chart that shows the stages and their time for a hamburger assembly process. - **Summary:** The table presents a Process Chart with a value-added time of 85.7%. The symbol key is provided for the table. ## 5.4 Service Blueprinting - Defines three levels of interaction - Focuses on the customer & provider interaction - Each level, has different management issues - Identifies potential failure points ## 5.4 Service Blueprint - **Diagram:** An image diagram that shows a service blueprint with different stages and their corresponding time for customer interaction. - **Summary:** The diagram depicts a service blueprint with three levels of interaction that includes Personal Greeting, Service Diagnosis, Perform Service, and Friendly Close, each with its associated time. ## 6. Special Considerations for Service Process Design - Good interaction with customers is necessary - The better these interactions are accommodated in the process design, the more efficient and effective the process. - Find the right combination of cost & customer interaction ## 6.1 Service Process Matrix - **Diagram:** An image diagram that shows a service process matrix. - **Summary:** The diagram depicts a service process matrix with the categories: Service Factory, Service Shop, Mass Service and Professional Service. ## 6.2 Service Process Matrix - **Diagram:** An image diagram that shows a service process matrix. - **Summary:** The diagram presents a service process matrix with the categories: Service Factory, Service Shop, Mass Service, and Professional Service. ## 6.2 Service Process Matrix - **Diagram:** An image diagram that shows a service process matrix. - **Summary:** The diagram provides a service process matrix with the categories: Service Factory, Service Shop, Mass Service and Professional Service. ## 6.3 Improving Service Productivity - **Table:** A table that presents various techniques for service productivity enhancement. - | Strategy | Technique | Example | - |---|---|---| - | Separation | Structuring Service So Customers Must Go Where the Service Is Offered | Bank Customers Go to a Manager to Open a New Account, to Loan Officers for Loans, and to Tellers for Deposits | - | Self-Service | Self-Service So Customers Examine, Compare, and Evaluate at Their Own Pace | Supermarkets & Department Stores, Internet Ordering | - | Postponement | Customizing at Delivery | Customizing Vans at Delivery Rather Than at Production | - | Focus | Restricting the Offerings| Limited-Menu Restaurant | - | Modules | Modular Selection of Service | Investment & Insurance Selection | - | Automation | Separating Services That May Lend Themselves to Some Type of Automation | Automatic Teller Machines | - | Scheduling | Precise Personnel Scheduling | Scheduling Ticket Counter Personnel at 15-Minute Intervals at Airlines | - | Training | Explaining How to Avoid Problems | After-Sale Maintenance Personnel| ## 7. Production Technology - Machine Technology - Automatic Identification Systems (AISs) - Process Control - Vision Systems - Robots - Automated Storage & Retrieval Systems (ASRSs) - Automated Guided Vehicles (AGVs) - Flexible Manufacturing Systems (FMSs) - Computer-Integrated Manufacturing (CIM) ## 7.1 Machine Technology - Increased productivity, & flexibility - Computer numerical control (CNC) - Reduced environmental impact - Additive manufacturing produces products by adding material, not removing it. - Supports innovative product design, minimal custom tooling required, minimal assembly time, low inventory & reduced time to market ## 7.2 Automatic Identification Systems (AISs) & RFID - Improved data acquisition - Reduced data entry errors - Increased speed - Increased scope of process automation - **Image:** An image that shows two people standing by a checkout counter. One person is reading a barcode on a shopping cart. - **Summary:** The image depicts a scenario of using barcodes and RFID in the context of checkout operations. ## 7.3 Process Control - Real-time monitoring & control of processes - Sensors collect data - Devices read data on a periodic basis - Measurements translated into digital signals then sent to a computer - Computer programs analyze the data - Resulting output may take numerous forms ## 7.4 Vision Systems - Particular aid to inspection - Consistently accurate - Modest cost - Superior to individuals performing the same tasks - **Image:** An image of ophthalmologic examination with a machine and a doctor. - **Summary:** The image showcases the use of vision systems in the context of ophthalmologic examination. ## 7.5 Robots - Perform monotonous or dangerous tasks - Perform tasks requiring significant strength or endurance - Generally, enhanced consistency & accuracy - **Image:** An image of an orange colored robot arm in an industrial setting. - **Summary:** The image showcases a robot arm involved in an industrial context, highlighting its role in repetitive tasks. ## 7.6 Automated Storage & Retrieval Systems (ASRSs) - Automated placement & withdrawal of parts & products - Reduced errors & labor - Particularly useful in inventory and test areas of manufacturing firms ## 7.7 Automated Guided Vehicle (AGVs) - Electronically guided & controlled carts - Used for the movement of products and/or individuals - **Image:** An image of a person operating a moving cart in a hospital setting. - **Summary:** The image showcases the use of Automated Guided Vehicles (AGVs) in a transportation context. ## 7.8 Flexible Manufacturing Systems (FMS) - Computer controls both the workstation & the material handling equipment - Enhance flexibility & reduced waste - Can economically produce low volume but wide variety - Reduced changeover time & increased utilization - Stringent communication requirement between components ## 7.9 Computer-Integrated Manufacturing (CIM) - Extend flexible manufacturing - Backward to engineering & inventory control - Forward into warehousing & shipping - Can also include financial & customer service areas - Reducing the distinction between low-volume/high-variety & high-volume/low-variety production. - **Diagram:** An image diagram shows computer-integrated manufacturing (CIM) systems. - **Summary:** The diagram presents a model of CIM systems with different stages like Computer-Aided Design (CAD), Order Management (OM), and Computer-Aided Manufacturing (CAM) involved in producing a product. ## 8. Technology in Services - **Table:** Examples of Technology's Impact on Services - | Service Industry | Example | - |---|---| - | Financial Services | Debit Cards, Electronic Funds Transfer, ATMs, Internet Stock Trading, Online Banking via Cell Phone | - | Education | Online Newspapers & Journals, Interactive Assignments via WebCT, Blackboard, and Smartphones | - | Utilities & Government | Automated One-Person Garbage Trucks, Flood-Warning Systems, Meters That Allow Homeowners To Control Energy Usage & Costs | - | Restaurants & Foods | Wireless Orders From Waiters To Kitchen, Transponders on Cars That Track Sales at Drive-Throughs | - | Communications | Interactive TV, E-books via Kindle | - | Hotels | Electronic Check-In/Check-Out, Electronic Key/Lock Systems, Mobile Web Bookings | - | Wholesale/Retail Trade | Electronic Communication Between Store & Supplier, Bar-Coded Data, RFID | - | Transportation | Automatic Toll Booths, Satellite-Directed Navigation Systems, Wi-Fi in Automobiles | - | Health Care | Online Patient-Monitoring Systems, Online Medical Information Systems, Robotic Surgery | - | Airlines | Ticketless Travel, Scheduling, Internet Purchases, Boarding Passes | ## 9. Process Redesign > 'The fundamental rethinking of business processes to bring about dramatic improvements in performance. - Relies on re-evaluating the purpose of the process & questioning both the purpose and the underlying assumptions - Requires re-examination of the basic process & its objectives - Focuses on activities that cross-functional lines - **Image:** A Thank You message.